文章编号:1004-0609(2011)03-0546-08
时效制度对2A97铝锂合金强韧性的影响
钟 申, 郑子樵, 廖忠全, 蔡 彪
(中南大学 材料科学与工程学院,长沙 410083)
摘 要: 通过拉伸试验及平面应变断裂韧性测试,研究不同时效制度对2A97合金强韧性的影响,并利用透射电镜和扫描电镜对合金的微观组织及断口形貌进行观察。结果表明:2A97合金在135 ℃单级时效时断裂韧性较好,但强度偏低;双级时效可促进强度的提高,但第二级时效温度过高时(175 ℃),断裂韧性迅速下降,经过(135 ℃, 36 h)+(150 ℃, 18 h)时效,可得到较好的强韧性匹配,其σb、σ0.2和KIC 分别为547 MPa、489 MPa和28.9 MPa·m1/2。2A97合金中的主要强化相为δ ′相和T1相。δ ′相易共面滑移而引起应力集中,对合金韧性不利;T1相能有效地阻止位错滑移,对合金强度有显著提高。2A97合金在时效初期以穿晶和沿晶混合型断裂为主,断口表现出明显的分层特征,具有较好的韧性;随时效时间的延长,析出相的体积分数、尺寸以及临界分切应力增大,所造成的应力集中更明显,同时晶界平衡相增多,晶界无沉淀带加宽,沿晶断裂比例增多,合金韧性急剧下降。
关键字: 2A97铝锂合金;微观组织;时效制度;断裂韧性
中图分类号: TG14612 ; TG113 文献标志码:A
Effects of aging treatment on strength and fracture toughness of 2A97 aluminum-lithium alloy
ZHONG Shen, ZHENG Zi-qiao, LIAO Zhong-quan, CAI Biao
(School of Materials Science and Engineering, Central South University, Changsha 410083, China)
Abstract: The effect of ageing treatment on the strength and fracture toughness of 2A97 alloy was investigated by tensile test and plane-strain fracture toughness experiments. The microstructures and fracture morphologies were observed and analyzed by TEM and SEM. The results indicate that the 2A97 alloy obtains a preferable fracture toughness of in single aging at 135 ℃,but its strength is relatively low. The duplex aging enhances the strength, while the fracture toughness deteriorates at an excessive temperature as 175 ℃. The 2A97 alloy can obtain the superior combination of the strength and toughness after (135 ℃, 36 h)+(150 ℃, 18 h) aging treatment, with the σb, σ0.2and KIC of 547 MPa, 489 MPa and 28.9 MPa·m1/2, respectively. The δ′ and T1 phases are the major precipitates in the 2A97 alloy. The δ′ phase may induce the stress localization and thus deteriorate the toughness, while the T1 phase can resist the slip of dislocation effectively and significantly enhance the strength. At the early stage, it primarily presents a hybrid of transgranular and intergranular fractures with obvious delamination crackings at the fracture surfaces, which indicates a high level of toughness. The volume fraction, size and critical resolved shear stress of precipitations increase with prolonging the aging time, and lead to more severe stress localizations. In additions, the more equilibrium phases at grain boundaries, the wider PFZs together with the greater proportional of intergranular fractures result in a sharply reduce of fracture toughness.
Key words:2A97 Al-Li alloy; microstructure; aging treatment; fracture toughness
铝锂合金具有低密度、高比强度和比刚度等优点,已成为航空航天领域最具应用潜力的结构材料之 一[1-3]。2A97铝锂合金是作者课题组与国内相关单位合作自主研发的新型第三代铝锂合金,具有比强度高、可焊性好及耐疲劳损伤性能优异等特点,有望用于飞机框梁结构及机翼下壁板和燃料贮箱等航空航天结构件,具有广泛的应用前景[4]。
对航空航天承力结构件来说,强度和断裂韧性是极其重要的性能指标要求。众所周知,材料的强度和断裂韧性与其微观组织结构密切相关,合理的时效制度可以改善析出相的尺寸和分布,是调控合金微观组织的重要方法之一。因此,了解时效过程中显微组织的变化及其对该合金性能的影响,优化其时效工艺,从而改善其强韧性匹配,对推动2A97合金在航空和航天工程中的应用有重要意义。由于2A97是我国自主研发的一个新合金,有关时效制度对该合金断裂韧性的影响尚未开展系统研究[5-9]。本文作者研究不同时效制度对2A97合金的常规力学性能、断裂韧性及微观组织的影响,讨论微观组织与合金强度和韧性之间的关系,并期望通过优化时效工艺以获得最佳强韧性能匹配,为该合金在航天航空领域的应用奠定基础。
1 实验
试验用料为半工业化生产的25 mm厚2A97铝锂合金热轧板材。板材在铝加工厂的辊底式喷淋淬火炉中进行固溶和淬火,淬火后立即进行2.5%的预拉伸变形,并在135 ℃预时效36 h。预时效后的板材经剪切后,按表1所示的时效制度进行后续时效处理。沿厚板L方向截取圆棒状试样在CSS-44100万能电子拉伸机上进行拉伸性能测试。从T-L方向取紧凑拉伸(CT)试样测定其断裂韧性,试样尺寸按ASTM E399-08标准制定(W/B=2,B=20 mm)。在MTS 810材料试验机上进行平面应变断裂韧性KIC测定,每测试点取3个有效数据,试验结果取平均值。TEM观察在TecnaiG220透射电子显微镜上进行,加速电压为200 kV;SEM断口观察在FEI Quanta 200环境扫描电镜上进行,加速电压为15 kV。
2 结果
2.1 拉伸性能及断裂韧性
2A97合金预拉伸板经(135 ℃, 36 h)预时效后,分别在135、150和175 ℃进一步时效不同时间后,拉伸性能及断裂韧性如图1和表2所示。由此可知,预时效后2A97合金具有较好的塑性和断裂韧性(δ5=13.7 %,KIC=33.1 MPa·m1/2),但强度偏低,其抗拉强度和屈服强度分别为522和435 MPa。后续时效处理使合金强度得到进一步的提高,在135 ℃继续时效时,随时效时间增加,合金强度缓慢上升,经96 h后达到峰值,对应抗拉强度和屈服强度分别为567和514 MPa;而在双级时效处理时,合金时效响应速率加快,强度提高,合金在150与175 ℃进行第二级时效时,分别经72和24 h达到峰值,对应的抗拉强度分别为588 和597 MPa,屈服强度分别为568和562 MPa。由此可见,双级时效与单级时效相比,时效响应速率更快,合金峰值强度更高。
由表2可知,随着时效的进行,合金的断裂韧性逐渐降低。合金在135 ℃继续时效时,随着时效时间的延长,断裂韧性下降不大,时效96 h后,其KIC为24 MPa·m1/2);在双级时效制度下,随第二级时效温度的提高,合金的断裂韧性下降更快。第二级时效温度
表1 2A97合金后续时效制度
Table 1 Subsequent heat treatment schedule of 2A97 alloys

表2 不同时效制度下2A97合金断裂韧性
Table 2 Fracture toughness of 2A97 alloy under different aging conditions

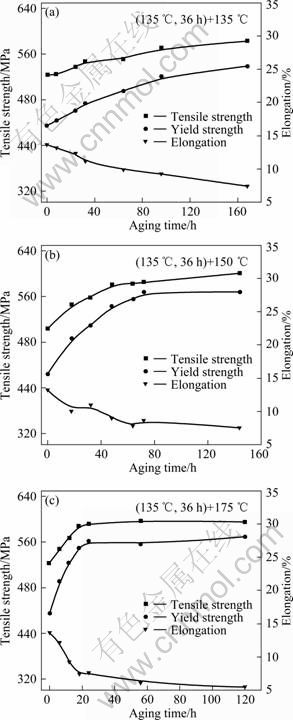
图1 2A97合金常规力学性能随时效时间变化曲线
Fig.1 Tensile properties of 2A97 alloy vs. ageing time curves under different conditions: (a) (135 ℃, 36 h)+135 ℃; (b) (135 ℃, 36 h)+150 ℃; (c) (135 ℃, 36 h)+175 ℃
为150 ℃时,时效64 h后,其KIC为16.2 MPa·m1/2;而第二级时效温度为175 ℃时,仅时效18 h后,其KIC下降为15 MPa·m1/2。在本研究中,比较3种时效制度的性能结果可知,经(135 ℃, 36 h)+(150 ℃, 18 h)时效后,合金拉伸强度、屈服强度和KIC分别为547 MPa、489 MPa和28.9 MPa·m1/2,可以达到较理想的强度和韧性匹配。
2.2 KIC断口形貌观察
图2为所示不同时效制度下的KIC试样的断口形貌。从图2中可以看出,2A97合金断口形貌主要表现为穿晶断裂和沿晶断裂的混合型断口。从图2(a)~(c)可以看出,时效初期,2A97合金断口以穿晶断裂为主,并表现出明显的分层特征,且垂直于主裂纹前进方向,此时在高倍下可见层间分布着大量细小的韧窝,这种断口特征表明此时合金具有较好的韧性。随着时效时间的延长以及时效温度的提高,合金断口逐渐转变为以沿晶界/亚晶界断裂为主,断口分层趋势减弱,如图2(d)~(f)所示,此时合金断口在高倍下,可观察到韧窝数量明显减少,并表现出冰糖状形貌特征,这种断口形貌对应较低的断裂韧性。
2.3 微观组织观察
2A97合金不同时效状态的á001?α、á112?α暗场TEM图像及相应衍射花样如图3和4所示,从图3和4中可以看出,随时效制度的改变,2A97合金中析出δ′相、T1相、S′相以及δ′/β′、δ′/θ′复合相粒子等不同第二相。由图3(a)可见,在(135 ℃, 36 h)预时效条件下,2A97合金中的主要强化相为大量细小弥散的球状δ′相和少量鱼眼状δ′/β′复合相粒子,从衍射斑和TEM像上未能观察到T1相及S′相。在135 ℃进一步时效32 h后,δ′相形貌和体积分数与预时效后相差不大,但有细小而稀疏的T1相析出(见图4(a));预时效后在150和175 ℃分别时效18和6 h时,2A97合金析出相形貌如图4(b)和(c)所示。由图4可见,双级时效时,由于第二级时效温度提高,溶质原子扩散速度增加,时效响应速度加快。与135 ℃单级时效时相比,双级时效时δ′相尺寸略有长大,而T1相体积分数明显增加,且第二级时效温度为175 ℃时的T1相体积分数大于第二级时效温度为150 ℃时的。此外,合金中还有少量S′相,在(135 ℃, 96 h)条件下还可见到δ′包覆θ′和β′形成的δ′/θ′和δ′/β′复合相粒子(见图3(b)箭头所示),在(175 ℃, 18 h)条件下还可以观察到T1相沿亚晶界连续析出(见图4(f))。进一步延长时效时间,从图4(d)~(f)可见,双级时效后期T1相的尺寸和密度大于单级时效时的,同时,δ′相尺寸明显增大,第二级时效温度对双级时效时的合金析出相形貌有很大影响,时效温度越高,T1相的尺寸和体积分数增长越快,δ′相的体积分数就越小。
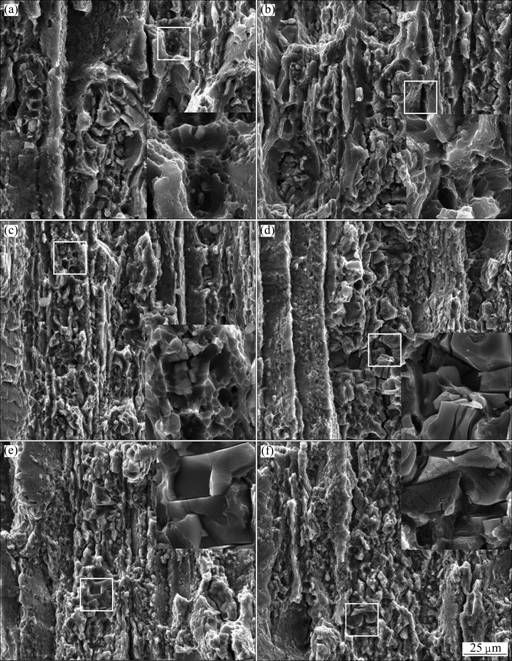
图2 2A97合金在不同时效制度下试样断口形貌
Fig.2 Fractographs of 2A97 alloy under different aging conditions: (a) (135 ℃, 32 h); (b) (135 ℃, 36 h)+(150 ℃, 18 h); (c) (135 ℃, 36 h)+(175 ℃, 6 h); (d) (135 ℃, 96 h); (e) (135 ℃, 36 h)+(150 ℃, 64 h); (f) (135 ℃, 36 h)+(175 ℃, 18 h)
图5所示为2A97合金预时效态和时效后期晶界析出相的形貌。由图5(a)可见,在预时效状态时,2A97合金晶界干净而平直,没有明显的无沉淀析出区(PFZ);图5(b)~(d)所示分别为对应(135 ℃, 36 h)+(135 ℃, 96 h)、(135 ℃, 36 h)+(150 ℃, 64 h)、(135 ℃, 36 h)+(175 ℃, 18 h)时效后合金晶界附近析出相的形貌。与预时效态相比,此时合金中晶界附近可观察到无沉淀带(如图中箭头所示),随着时效时间的延长,无沉淀区宽度增加。
3 分析与讨论
时效制度对2A97合金强韧化的作用主要表现为对合金中析出相的影响。2A97合金中影响强韧化的晶内析出相主要是与基体共格、球状的δ′相和在基体{111}
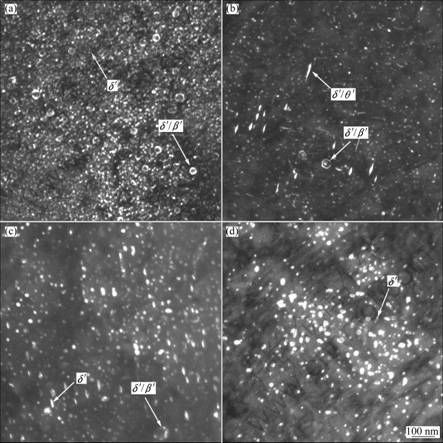
图3 在不同时效制度下2A97合金在á001?α方向的TEM像
Fig.3 TEM images of 2A97 alloy from á001?α under different conditions: (a) (135 ℃, 36 h); (b) (135 ℃, 36 h)+(135 ℃, 96 h); (c) (135 ℃, 36 h)+(150 ℃, 64 h); (d) (135 ℃36, h)+(175 ℃, 18 h)
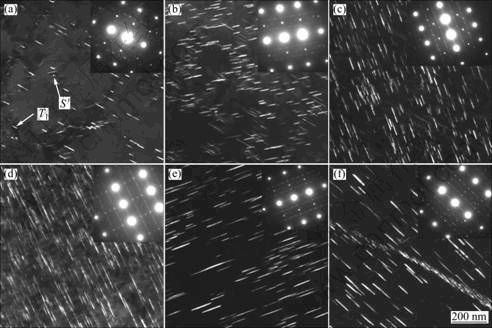
图4 不同时效制度下2A97合金T1相在á112?α方向的TEM像及衍射斑点
Fig.4 TEM images and corresponding SAD patterns of T1 phase of 2A97 alloy from á112?α under different aging conditions: (a) (135 ℃, 36 h)+(135 ℃, 32 h); (b) (135 ℃, 36 h)+(150 ℃, 18 h); (c) (135 ℃, 36 h)+(175 ℃, 6 h); (d) (135 ℃, 36 h)+(135 ℃, 96 h); (e) (135 ℃, 36 h)+(150 ℃, 64 h); (f) (135 ℃, 36 h)+(175 ℃, 18 h)
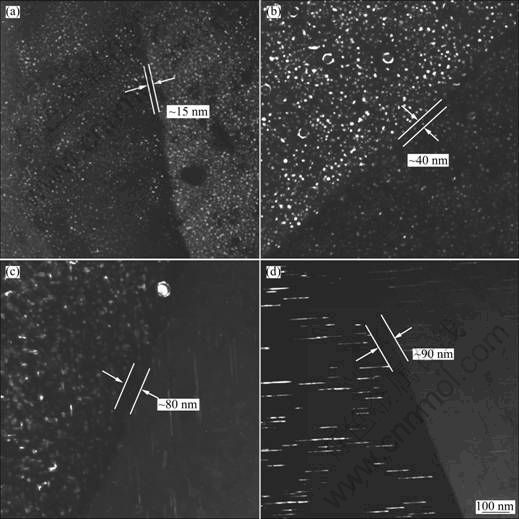
图5 2A97合金预时效态与时效后期晶界析出相的形貌
Fig.5 Morphologies of precipitations at grain boundary in 2A97 alloy at pre-aged and further aged stages: (a) 135 ℃, 36 h; (b) (135 ℃, 36 h)+(135 ℃, 96 h); (c) (135 ℃, 36 h)+(150 ℃, 64 h); (d) (135 ℃, 36 h)+(175 ℃, 18 h)
面析出的片状T1相。δ′相有一定的强化作用,但由于这种与基体共格的有序相在应力作用下,易被位错成对切割而引起长程共面滑移[2, 10],导致大位错塞积,并引发强剪切带,强剪切带冲击晶界而引起局部应力集中,诱发裂纹萌生并使裂纹沿晶界或滑移面迅速扩展,使合金的韧性恶化[10-11]。T1相是{111}面上不可切割的脆性片状析出相,与位错的交互作用服从Orawan机制,其临界分切应力大于δ′相,因此强化作用大于δ′相 [12]。合金中细小弥散的T1相对共面滑移有一定的抑制作用,但时效后期,粗大T1相不规则边缘也容易导致局部应力集中而使韧性降低。
研究表明,析出相对铝锂合金断裂韧性的影响主要归因于其尺寸、分布、体积分数以及由晶内析出相所导致的局部应力集中。析出相引起的应力集中可用下式表示[9, 13]:
(1)
式中:dp为析出相的有效尺寸;τc为剪切带冲击晶界造成的应力集中;τrss为临界分切应力;fv为析出相的体积分数;L为位错滑移的平均距离;Cp是与反相畴界能有关的常量;b为柏格斯矢量;CB=G/[π(1-μ)]。
由此可知,晶内析出相的体积分数、尺寸、间距及临界分切应力越大(fv、dp、τrss),所造成的应力集中越明显,对合金韧性的影响越大。本研究中,时效早期,合金中主要强化相为δ′相,且尺寸和体积分数相差不大;而T1相的体积分数则有很明显的差异。从图4(a)~(c)中可明显地看出,随时效温度的升高,T1相的体积分数依次增大,析出相的间距减小。析出相的体积分数和尺寸越大,所造成的局部应力集中越明显,合金韧性越低,这也是(175 ℃, 6 h)时效后合金断裂韧性较低的原因之一。随着时效的进行,T1相进一步析出长大,析出相的总体积分数继续增加,尺寸变大而间距逐渐减小,粗大的析出相使得应力集中更为明显。除此之外,由于T1相极易在位错等缺陷处形核,而亚晶界的位错缠结给T1提供了大量优先形核位置,因此,时效后期,可观察到大量T1相沿着亚晶界连续析出,如图4(e)所示。亚晶界上连续析出的T1相将加剧局部应力集中,导致微裂纹的萌生,从而降低合金的韧性。
时效制度不同导致晶界和晶内强度的差异也是影响合金断裂韧性的因素之一。铝锂合金晶界强度较低,在拉应力作用下易沿轧制方向的扁平状拉长晶界开裂,形成分层断口[14]。时效初期,晶界脆性平衡相和晶内强化相析出较少,两者强度相差不大,因此,合金表现为穿晶和沿晶混合的断裂机制。此时断口沿短横向分层明显,层间分布着大量细小的韧窝。这种分层具有裂纹分解(Crake divider)效应,阻碍了位错的滑移,对裂纹尖端的塑性区有一定的限制作用,并使得裂纹尖端处的三向拉应力减小,使得裂纹尖端由平面应变状态转变为平面应力状态,宏观上表现为断裂韧性的提高[15-16]。而时效后期,晶界附近无沉淀析出带(PFZ)宽化,使得晶界强度下降,晶界/晶内强度差异增大,同时较软的PFZ使得晶界处的应力集中更为明显,沿晶开裂趋势增强;此外,由于时效后期晶界上析出的脆性平衡相(主要为Al2Cu、Al2CuMg及富Mn相)极易导致裂纹的萌生,使得晶界强度急剧下降,因此断口表现出明显的沿晶断裂趋势,合金的韧性明显下降。
4 结论
1) 随时效时间延长和时效温度升高,2A97合金强度上升而断裂韧性逐渐下降;135 ℃单级时效时断裂韧性下降较慢,但强度偏低;双级时效可提高合金强度,缩短时效时间,但第二级时效温度过高将使断裂韧性迅速下降。(135 ℃, 36 h)+(150 ℃, 18 h)双级时效条件下,2A97合金的σb、σ0.2和KIC分别为547 MPa、489 MPa和28. 9 MPa·m1/2,可得到较好的强韧性匹配。
2) 2A97合金中的主要强化相为δ′相和T1相。δ′相易共面滑移而引起应力集中,对合金韧性不利;T1相能有效阻止位错滑移,对合金强度有显著提高。2A97合金在时效初期,晶界和晶内强度相差不大,以穿晶和沿晶混合型断裂为主,断口表现出明显的分层特征,具有较好的韧性,随着时效时间的延长,析出相的体积分数、尺寸以及临界分切应力逐渐增大,所造成的应力集中越明显,晶界平衡相增多,晶界无沉淀带加宽,晶界强度急剧下降,沿晶断裂比例增多,合金韧性降低。
REFERENCES
[1] GRIMES R, CORNISH A J, MILLER W S, REYNOLDS M A. Aluminum-lithium based alloys for aerospace application[J]. Metals and Materials, 1985, 1(6): 357-366.
[2] LAVERNIA E J, GRAND N J. Aluminum-lithium alloys[J]. Journal of Materials Science, 1987, 22(5): 1521-1529.
[3] NOBLE B, THOMPSON G E. T1(Al2CuLi) precipitation in aluminum-copper-lithium alloys[J]. Metal Science Journal, 1972, 6: 167-174.
[4] 袁志山, 陆 政, 谢优华, 戴圣龙, 刘常升. 时效制度对2A97铝锂合金组织和性能的影响[J]. 中国有色金属学报, 2006, 16(12): 2027-2033.
YUAN Zhi-shan, LU Zheng, XIE You-hua, DAI Sheng-long, LIU Chang-sheng. Effects of aging treatment on microstructure and properties of 2A97 aluminum-lithium alloy[J]. The Chinese Journal of Nonferrous Metals, 2006, 16(12): 2027-2033.
[5] 袁志山, 陆 政, 谢优华, 戴圣龙, 刘常升. 新型高强2A97铝锂合金组织和性能研究[J]. 材料热处理学报, 2008, 29(5): 44-48.
YUAN Zhi-shan, LU Zheng, XIE You-hua, DAI Sheng-long, LIU Chang-sheng. Study on microstructure and properties of a novel high strength aluminum lithium alloy 2A97[J]. Transactions of Materials and Heat Treatment. 2008, 29(5): 44-48.
[6] 袁志山, 陆 政, 谢优华, 戴圣龙, 刘常升. 预变形对高强Al-Cu-Li-X铝锂合金组织和性能的影响[J]. 稀有金属材料与工程. 2007, 36(3): 493-495.
YUAN Zhi-shan, LU Zheng, XIE You-hua, DAI Sheng-long, LIU Chang-sheng. Effect of plastic deformation on microstructure and properties of high strength Al-Cu-Li-X aluminum-lithium alloy[J]. Rare Metal Materials and Engineering, 2007, 36(3): 493-495.
[7] 魏修宇, 郑子樵, 潘峥嵘. 预变形对2197铝锂合金显微组织和力学性能的影响[J]. 稀有金属材料与工程, 2008, 37(11): 1996-1999.
WEI Xiu-yu, ZHENG Zi-qiao, PAN Zheng-rong. The role of plastic deformation on microstructure and mechanical properties of 2197 Al-Li alloy[J]. Rare Metal Materials and Engineering, 2008, 37(11): 1996-1999.
[8] 袁志山, 陆 政, 戴圣龙, 刘常升. 预时效对高强铝锂合金2A97组织和性能的影响[J]. 东北大学学报, 2007, 28(1): 53-56.
YUAN Zhi-shan, LU Zheng, DAI Sheng-long, LIU Chang-sheng. Effect of pre-aging on microstructure and properties of high strength 2A97 Al-Cu-Li-X alloy[J]. Journal of Northeastern University, 2007, 28(1): 53-56.
[9] GABLE B M, ZHU A W, CSONTOS A A, STARKE E A. The role of plastic deformation on the competitive microstructural evolution and mechanical properties of a novel Al-Li-Cu-X alloy[J]. Journal of Light Metals, 2001, 1(1): 1-14.
[10] CSONTOS A A, STARKE E A. The effect of inhomogeneous plastic deformation on the ductility and fracture behavior of age hardenalbe aluminum alloys[J]. International Journal of Plasticity, 2005, 21: 1097-1118.
[11] KALYANAM S, BEAUDOIN A J, DODDS R H, BARLAT F. Delamination cracking in advanced aluminum-lithium alloys-experimental and computational studies[J]. Engineering Fracture Mechanics, 2009, 76: 2174-2191.
[12] LAVERNIA E J, SRIVATSAN T S, MOHAMED F A. Strength, deformation, fracture behavior and ductility of aluminum-lithium alloys[J]. Journal of Materials Science, 1990, 25: 1137-1158.
[13] VENKATESWARA RAO K T, RITCHIE R O. Mechanical properties of Al-Li alloys Part 1: Fracture toughness and microstructure[J]. Materials Science and Technology, 1989, 5(9): 882-895.
[14] VENKATESWARA RAO K T, YU W K, RITCHIE R O. Cryogenic toughness of commercial aluminum-lithium alloys: Role of delamination toughening[J]. Metallurgical Transactions A, 1989, 20: 485-497.
[15] CUI Jiang-guo, FU, Yong-hui, LI Nian, SUN Jun, HE Jia-wen, DAI Yao. Study on fatigue crack propagation and extrinsic toughening of an Al-Li Alloy[J]. Materials Science and Engineering A, 2000, 281: 126-131
[16] CSONTOS A A, STARKE E A. The effect of processing and microstructure development on the slip and fracture behavior of the 2.1wt pct Li AF/C-489 and 1.8wt pct Li AF/C-458 Al-Li-Cu-X alloys[J]. Metallurgical and Materials Transactions A, 2000, 31(A): 1965-1976.
(编辑 何学锋)
收稿日期:2010-04-06;修订日期:2010-04-28
通信作者:郑子樵; 教授; 电话: 0731-88830270;E-mail: s-maloy@mail.csu.edu.cn