J. Cent. South Univ. (2017) 24: 1619-1626
DOI: 10.1007/s11771-017-3567-9

Investigation on jointed rock strength based on fractal theory
YANG Lan-lan(杨兰兰)1, 2, XU Wei-ya(徐卫亚)1, 2, MENG Qing-xiang(孟庆祥)1, 2, 3, WANG Ru-bin(王如宾)1, 2
1. Research Institute of Geotechnical Engineering, Hohai University, Nanjing 210098, China;
2. Key Laboratory of Ministry of Education for Geomechanics and Embankment Engineering, Hohai University, Nanjing 210098, China;
3. Department of Civil & Environmental Engineering, University of Waterloo, Waterloo N2L 3G1, Canada
Central South University Press and Springer-Verlag Berlin Heidelberg 2017
Abstract: Strength of discontinuities with complex structure is an important topic in rock engineering. A large number of studies have shown that fractal is applicable in the description of this discontinuity. Using fractal interpolation method for the generation of rock joints, numerical experiments of shear tests of the jointed rock mass model were carried out using FLAC3D. The test results show that the real rock joints can be simulated by fractal curves obtained by fractal interpolation. The fractal dimension is an important factor for the characterization of jointed rock mass; test results show that the fractal dimension of rock joints can be related to the equivalent cohesion strength and shear strength of the rock mass. When the fractal dimension of the joint surface is less than critical dimension Dc 1.404, the cohesion strength and shear strength of the rock mass increase as the fractal dimension increases; for larger fractal dimensions, all mechanical parameters decrease as the fractal dimension increases. Joint surfaces with different degrees of roughness were obtained by the fractal interpolation method. Three types of failure modes were observed in the tests: climbing slip failure, climbing gnawing fracture, and non-climbing gnawing fracture.
Key words: rock joints; fractal dimension; shear strength; numerical simulation
1 Introduction
Rock mass is rarely a uniform and continuous medium and usually contains many natural discontinuities, such as faults, joints, and weak planes. As a kind of typical heterogeneous material, the engineering properties of rock mass, such as strength, deformability, and fluid flow behaviors, are influenced by these inhomogeneities [1]. For a better understanding of the rock properties, an accurate description of this heterogeneity is an essential and challenging task.
In fact, the geometry of rock mass is extremely complex and the traditional Euclidean model cannot give an accurate description [2, 3]. The concept of fractals was introduced by MANDELBROT [4] in a geological context and then became a powerful tool in the description of natural phenomena. Existing research results have shown that fracturing in rock materials has a fractal structure and several researchers have suggested that the fractal can be used to quantify the roughness of rock joint [5-8]. Fractal dimension is applied to represent the rock joint surface roughness [9] and classify the rock mass quality [10, 11]. As for the estimation of fractal parameters, boxing fractal dimension and Hurst Index are widely used in the calculation [12, 13]. KULATILAKE et al [14, 15] suggested that at least two parameters should be used to study two-dimensional roughness variability and anisotropy.
Taking a step further, extensive investigations studied the relationship between the fractal parameters and mechanical behavior [16]. LEE et al [17] pointed out that high fractal dimension of joint profiles results in high shear strength. XIE et al [18, 19] studied the fractal effects of surface roughness on the mechanical behavior of rock joints as well as the fractal property of spatial distribution of acoustic emissions during the failure process. These studies conclude that joints fractal features play a dominant role in the mechanical behavior of rock joints.
However, the in-situ and laboratory tests have limitations that the roughness has a certain value and each experiment consumes a lot of human and material resources. Using numerical method, the relationship between fractal dimension and rock strength parameters is analyzed. Taking rock masses with different roughness of joints as example, a series of strength parameters of rock mass were obtained through numerical shear tests. Based on the numerical results, a quantitative analysis combining fractal dimension and mechanical properties is carried out.
2 Fractal fracture surface
Accurate description and characterization of the geometrical characteristics of rock mass are the basis of the studying on the mechanical properties of the jointed rock mass. In geological studies, discontinuous shapes such as joints are generally described as “jagged”, “stepped”, or “wavelike”. This is a generalization of the overall shape using traditional geometric terminology [20]. However, the structure of the actual rock mass cannot be described by traditional geometric language because of the complexity and irregular nature of the rock structure. Fractal interpolation can overcome this shortcoming by reflecting the local characteristics of two adjacent known related points. Higher accuracy of the simulating the natural geologic forms can be achieved by using fractal interpolation method than traditional methods [21]. In this work, the fractal interpolation function was used to describe a rock joint surface.
2.1 Fractal interpolation theory and method
For a data set of N points shaped like
(1)
the corresponding interpolation function is a continuous function
so that
i=0, 1, 2, …, N (2)
These points
are the interpolation points and the curve of function f passes through these points.
The fractal interpolation principle is shown in Fig. 1, with three different iterations from Figs. 1(b) to (d). The fractal interpolation is a fractal curve, and the curve is self-similar.
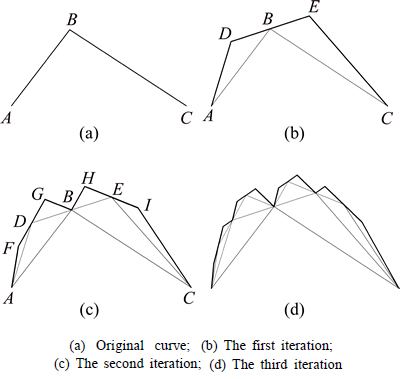
Fig. 1 Fractal interpolation diagram
Consider an iterated function system (IFS)
where Wn is an affine transformation in the form of
(3)
and
(4)
In Eq. (3), the constant value of 0 ensures that the functions do not overlap between sections. The parameter dn is the vertical scaling factor of the transformation Wn and |dn|<1 (otherwise, this IFS does not converge [22]). Although dn is a free parameter, it has a great influence on the fractal interpolation results. The effect of dn on the roughness of the fractal curve is shown in Fig. 2.
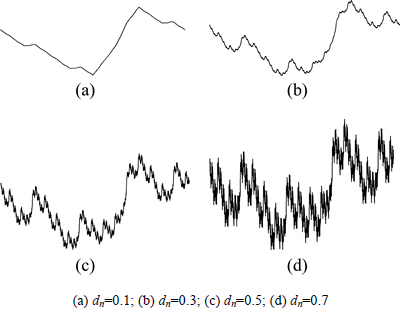
Fig. 2 Influence of vertical scaling factor dn on fractal curve
2.2 Fractal dimension of fractal interpolation curve
For a given dataset and IFS, G represents the attractor of the IFS, which yields the graphic image of the fractal interpolation function for the given dataset. If
(5)
and the interpolation point is not collinear, then the fractal dimension D of G will be the only real solution of the following equation:
(6)
Otherwise, the fractal dimension D of G is 1.
When the interpolation data
is equidistant, let
and then, substituting
into Eq. (6) leads to
(7)
Thus, the fractal dimension of the fractal interpolation function is directly dependent on the vertical scaling factor dn, so that dn will be the dominant factor that determines the complexity and the fractal dimension of the curve [20].
2.3 Construction of fractal curve of a rock mass joint surface
Because the actual shape of the rock joint is too irregular to be described by a common function, only one type of typical joint shape is studied in this work. An IFS
was used, in which Wn is the affine transformation in R2 and the attractor is the fractal graphics with interpolation points [(0,2), (1,1.8), (2,2), (3,2.2), (4,2)]. Based on the principle and method of fractal interpolation mentioned above, the software MATLAB was used to obtain the fractal curves with different vertical scaling factors (Fig. 3).
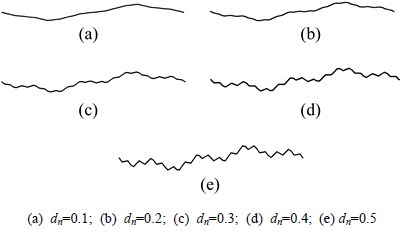
Fig. 3 Rock mass joints formed by IFS with different vertical ratio factors
Using Eq. (7), the fractal dimension D of the joint surface corresponding to the different vertical scale factors can be calculated (Table 1).
Table 1 Fractal dimension of rock joint surface for various dn

3 Numerical shear test of jointed rock mass
To study the influence of different rock mass joint surface morphologies on the joint strength and deformation characteristics, numerical simulation shear tests of jointed rock mass were carried out based on the finite difference method using the FLAC3D software.
3.1 Numerical modeling
The fractal curves obtained in the previous section are used as the shape of the joint surface cutting through the rock mass in the three-dimensional (3D) models of 4 m×0.2 m×4 m (Fig. 4). Fractal curves with different vertical scaling factors were generated. To minimize the difference between the numerical results generated by the grid partition, these models are meshed by the finite element grid generator GMSH, which can be easily adapted to our model and has adjustable grid density. The specific steps are as follows:
1) The coordinates of the points in the fractal curve obtained from Section 2.3 are rewritten into new file in the GEO format (Fig. 4(a)), which can be read by GMSH.
2) After importing the .geo file into GMSH, the 2D model is generated with a grid length of lc=0.1 m for the fractal curve points of the model, and lc=0.3 m for the boundary points of the model. The grid is exported (see Fig. 4(b)).
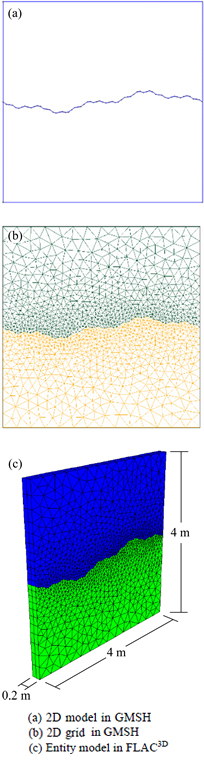
Fig. 4 Jointed rock mass model (taking jointed rock mass with D=1.566 as an example)
3) The interface program between GMSH and FLAC3D is written by using MATLAB. Then the .msh file can be rewritten into a .flac3d file easily by using the interface program. All the 2D models can be expanded to 3D models (see Fig. 4(c)) in this program.
3.2 Mechanical parameters of model materials
In the numerical test models, the Mohr–Coulomb plastic criterion [23, 24] is used to describe the failure behavior of the rock mass. The rock mass and rock joint material’s mechanical parameters used in the numerical test are listed in Table 2.
3.3 Boundary conditions
The bottom surface of the lower part of the model is fixed in all directions, and the side faces are fixed in normal direction. The analysis was carried out in two steps. In the first step, only normal stress was applied on the top surface of the model, and in the second step, normal and shear stresses were both applied. All of the
analyses were performed using normal stresses ranging from 0.1 to 1.1 MPa, and shear stress was applied by displacement of the upper model with a loading rate of v=4.0×10-3 mm/step [25, 26].
4 Results and analysis of numerical tests
4.1 Analysis of shear stress-displacement relations of joint surface
The relationship between the shear stress and displacement of the rock specimens with the same fractal dimension at different normal stress conditions is shown in Fig. 6. In the shear test, the shear stress of the joint surface increases gradually, then decreases with fluctuations, and finally stabilizes with slight fluctuations. As the normal stress increases, the peak shear stress increases gradually, so as to the value of the corresponding displacement. This indicates that the joint surface model based on the fractal theory is in line with the basic shear characteristics of the actual rock mass joint surface.
Fig. 5 Numerical models of rock mass joint with various fractal dimensions
Table 2 Material parameters of rock mass and joint surface

Fig. 6 Relationship between shear stress and displacement under different normal stress conditions
4.2 Equivalent strength parameters of fractal fracture surface
In order to get the valuable macro equivalent mechanical parameters like equivalent cohesion and friction angle, the values of peak shear strength of each rock mass under different normal stress were obtained, and the relationship between the normal stress σn and peak shear strength τc with different fractal dimensions was analyzed. As shown in Fig. 7, the peak shear strength τc has an almost linear relationship with the normal stress σn. Based on the numerical simulation data, an empirical equation between peak shear strength τc of the rock joint and normal stress σn can be obtained by numerical fitting. The fitting equation is in the form of
(8)
where τc is the peak shear strength of the rock joint (MPa); σn is the normal stress (MPa); and a1 and a2 are fitting parameters.
The fitting parameters and correlation coefficients for the five values of fractal dimension used in the model are shown in Table 3. The data show that the relationship between the normal stress and peak shear strength of the fractal surface can be described by a linear equation.
The corresponding equivalent cohesion and friction angle were obtained based on the Mohr–Coulomb
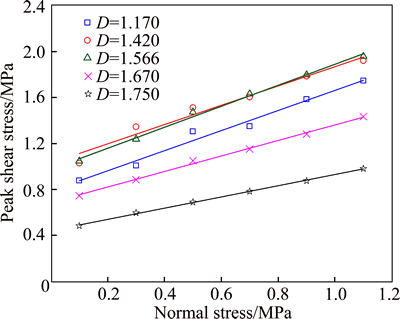
Fig. 7 Measured values and fitting curves (solid line) of peak shear strength vs normal stress
Table 3 Fitting of normal stress and peak shear strength
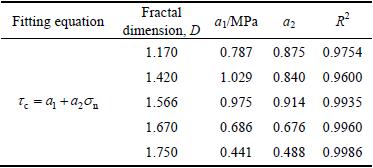
principle (Table 4) when the relationship between the normal stress and peak shear strength of the fractal surface can be described by a linear equation. The equivalent cohesion and friction angle have greatly improved compared with the initial values used in the model of the joint surface (cohesion c=0.1 MPa and friction angle φ=24.2°). That is, the strength parameters are influenced easily by fractal dimension of jointed rock masses.
Table 4 Calculation results of equivalent cohesion and friction angle of joint plane
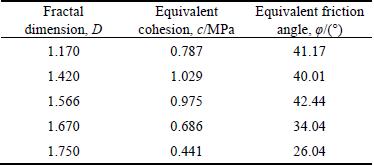
Based on the data in Table 4, the relationship between the fractal dimension and the equivalent cohesion is shown in Fig. 8. The fitted curves for the relationship between the fractal dimension and the two parameters can be described by quadratic functions.
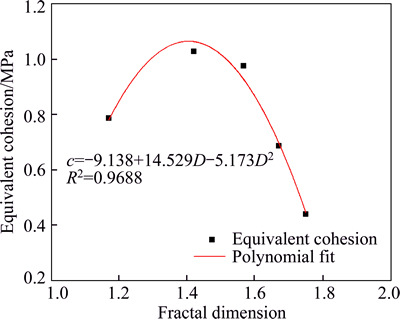
Fig. 8 Calculation and fitting curve of equivalent bond force and fractal dimension
Using the numerical simulation data, the empirical equation of the fractal dimension vs equivalent cohesion through numerical fitting was obtained. The fitting equation is in the form of
(9)
where y represents the equivalent cohesion c; D is the fractal dimension; and b1, b2, and b3 are fitting parameters.
Based on the quadratic fitting equation, a critical fractal dimension, Dc=1.404, of the peak equivalent is obtained. The equivalent cohesion increases as the fractal dimension increases when the fractal dimension is less than Dc, and decrease as the fractal dimension increases when the fractal dimension is greater than Dc.
4.3 Failure mode of rock joint under shear test
A clean serrated joint surface can fail by three basic processes: climbing sliding failure, climbing sliding gnawing fracture, or non-slip gnawing fracture [27]. In a climbing sliding failure, the peak intensity of the shear stress displacement curve is not obvious; this is characteristic of plastic failure. Non-slip gnawing fracture failure has the characteristic of brittle failure. To model the joint surfaces with different degrees of roughness, the fractal interpolation method was used. The numerical simulation of the joint surface shows that the failure mode of the joint fractal has similar characteristics to those of the jagged joint surface.
Figure 9 shows the max shear strain rate of the rock mass with different fractal dimensions at the normal stress of 0.3 MPa. As shown in Fig. 9(a), when the joint surface is smooth, relative sliding mainly happened between the jointed rock masses on both sides, and almost no significant shear deformation.
When the joint surface is a little ragged, as shown in Fig. 9(b) and (c), relative sliding is still the main behavior, besides, shear deformation occurred in protruding parts of the rock masses on both sides. But the whole damage failure did not happen.
Fig. 9 Max shear strain rate (step-1) with different fractal dimensions at normal stress of 0.3 MPa
When the joint surface is ragged enough, as shown in Figs. 9(d) and (e), a connected shear failure zone appears around the fractal joint surface.
5 Conclusions
1) During the simulated shear test, the shear stress of the joint surface gradually increases, then decreases with fluctuations, and finally stabilizes with slight fluctuations. The growth rate of the shear stress decreases with time during the shear test. The normal stress and shear strength were positively correlated under different fractal dimension values, and both can be fitted by a linear function.
2) The relationship between the fractal dimension and the equivalent cohesion can be fitted well with a quadratic function.
3) Based on the quadratic fitting equation, a critical fractal dimension, Dc=1.404, of the peak equivalent is obtained. The equivalent cohesion increases as the fractal dimension increases when the fractal dimension is less than Dc, and decrease as the fractal dimension increases when the fractal dimension is greater than Dc.
4) Joint surfaces with different degrees of roughness were obtained by the fractal interpolation method. Numerical shear tests of the joint surface show that the failure mode of the joint fractal has similar characteristics to those of the jagged joint surface. Three types of failure modes were observed in the tests: climbing slip failure, climbing gnawing fracture, and non-climbing gnawing fracture.
References
[1] ZHOU Yu, WU Shun-chuan, GAO Yong-tao, MISRA A. Macro and meso analysis of jointed rock mass triaxial compression test by using equivalent rock mass (ERM) technique [J]. Journal of Central South University, 2014, 21(3): 1125-1135.
[2] POWER W L, TULLIS T E. Euclidean and fractal models for the description of rock surface roughness [J]. Journal of Geophysical Research: Solid Earth (1978–2012), 1991, 96(B1): 415-424.
[3]
,
, AGAMALIAN M, WIGNALL G D, LINDNER P, RANDL O G. Fractal geometry of rocks [J]. Physical Review Letters, 1999, 82(15): 3078-3081.
[4] MANDELBROT B B. How long is the coast of Britain [J]. Science, 1967, 156(3775): 636-638.
[5] XIE He-ping, CHEN Zhi-da. Fractal geometry and fracture of rock [J]. Acta Mech Sinica, 1988, 4(3): 255-264.
[6] MILLER S M, MCWILLIAMS P C, KERKERING J C. Ambiguities in estimating fractal dimensions of rock fracture surfaces [C]// Proc 31st US Symp on Rock Mech. The Netherlands: AA Balkema Rotterdam, 1990.
[7] DEN OUTER A, KAASHOEK J F, HACK H R. Difficulties with using continuous fractal theory for discontinuity surfaces [J]. International Journal of Rock Mechanics and Mining Sciences & Geomechanics Abstracts, 1995, 32(1): 3-9.
[8] KEWEN L. Characterization of rock heterogeneity using fractal geometry [C]// SPE International Thermal Operations and Heavy Oil Symposium and Western Regional Meeting. Society of Petroleum Engineers, 2004.
[9] TURK N, GREIG M J, DEARMAN W R, AMIN F F. Characterization of rock joint surfaces by fractal dimension [C]// The 28th US Symposium on Rock Mechanics (USRMS). American Rock Mechanics Association, 1987.
[10] BOADU F K, LONG L T. The fractal character of fracture spacing and RQD [J]. International Journal of Rock Mechanics and Mining Sciences & Geomechanics Abstracts, 1994, 31(2): 127-134.
[11] CARR J R, WARDNER J B. Rock mass classification using fractal dimension [C]// The 28th US Symposium on Rock Mechanics (USRMS). American Rock Mechanics Association, 1987.
[12] AI T, ZHANG R, ZHOU H W, PEI J L. Box-counting methods to directly estimate the fractal dimension of a rock surface [J]. Applied Surface Science, 2014, 314: 610-621.
[13] YANG Z Y, DI C C, LO S C. Two-dimensional Hurst index of joint surfaces [J]. Rock Mechanics and Rock Engineering, 2001, 34(4): 323-345.
[14] KULATILAKE P H S W, BALASINGAM P, PARK J, MORGAN R. Natural rock joint roughness quantification through fractal techniques [J]. Geotechnical & Geological Engineering, 2006, 24(5): 1181-1202.
[15] KULATILAKE P H S W, FIEDLER R, PANDA B B. Box fractal dimension as a measure of statistical homogeneity of jointed rock masses [J]. Engineering Geology, 1997, 48(3): 217-229.
[16] XI Yue, CHEN Jin-jian, XU Yong-fu, CHU Fei-fei, LIU Chuan-xin. Yield stress of fractal aggregates [J]. Fractals, 2015, 23(03): 1550028.
[17] LEE Y H, CARR J R, BARR D J, HAAS C J. The fractal dimension as a measure of the roughness of rock discontinuity profiles [J]. International Journal of Rock Mechanics and Mining Sciences & Geomechanics Abstracts, 1990, 27(6): 453-464.
[18] XIE He-ping, WANG Jin-an, XIE Wei-hong. Fractal effects of surface roughness on the mechanical behavior of rock joints [J]. Chaos, Solitons & Fractals, 1997, 8(2): 221-252.
[19] XIE H P, LIU J F, JU Y, LI J, XIE L. Z. Fractal property of spatial distribution of acoustic emissions during the failure process of bedded rock salt [J]. International Journal of Rock Mechanics and Mining Sciences, 2011, 48(8): 1344-1351.
[20] YANG Lu-jun, ZOU Yan-ping, QIAN Jian-long. Application of fractal geometry in research of jointed rock mass [J]. China Water Transport, 2007, 5(8): 60-62. (in Chinese)
[21] YANG Jie. Study on fractal interpolated and its fractal dimension [J]. Journal of Wuhan Polytechnic University, 2006, 25(1): 9-11. (in Chinese).
[22] LI Shui-gen. Fractal [M]. Beijing: Higher Education Press, 2004: 236. (in Chinese)
[23] WANG Wei, LI Liang-quan, XU Wei-ya, MENG Qing-xiang, LI Jun. Creep failure mode and criterion of Xiangjiaba sandstone [J]. Journal of Central South University, 2012, 19(12): 3572-3581.
[24] NIKADAT N, FATEHI M, ABDOLLAHIPOUR A. Numerical modelling of stress analysis around rectangular tunnels with large discontinuities (fault) by a hybridized indirect BEM [J]. Journal of Central South University, 2015, 22(11): 4291-4299.
[25] SUN Shu-wei, REN Hang, REN Lian-wei. Application of FLAC3D in geotechnical engineering [M]. Beijing: China Water & Power Press, 2011. (in Chinese)
[26] LI Hai-bo, FENG Hai-peng, LIU Bo. Study on strength behaviors of rock joints under different shearing deformation velocities [J]. Chinese Journal of Rock Mechanics and Engineering, 2006, 25(12): 2435-2440. (in Chinese)
[27] ZHOU Rui-guang. Mechanical effect of structural plane of rock mass [J]. Geotechnical Investigation & Surveying, 1981(1): 46-51. (in Chinese)
(Edited by YANG Hua)
Cite this article as: YANG Lan-lan, XU Wei-ya, MENG Qing-xiang, WANG Ru-bin. Investigation on jointed rock strength based on fractal theory [J]. Journal of Central South University, 2017, 24(7): 1619-1626. DOI: 10.1007/s11771-017-3567-9.
Foundation item: Projects(51479049, 51209075) supported by the National Natural Science Foundation of China
Received date: 2015-12-16; Accepted date: 2016-05-11
Corresponding author: YANG Lan-lan, PhD Candidate; Tel: +86-15251771611; E-mail: yanglanlan_hhu@163.com