J. Cent. South Univ. Technol. (2008) 15: 309-312
DOI: 10.1007/s11771-008-0058-z

Spray deposition for making large size billet with swing atomizer
LI Jian-ping(李建平), LIU Tao(刘 涛), TANG Qing-yun(唐青云),
HAN Lei(韩 雷), ZHONG Jue(钟 掘)
(School of Mechanical and Electrical Engineering, Central South University, Changsha 410083, China)
Abstract: The movement mode of the atomizer is a very important parameter during spray deposition process, which has direct influence on the size and surface texture of the billets. To resolve the problem of manufacturing large size billets, a method of spray deposition by the atomizer with off-center swing was put forward. The atomizer was driven by the alternating current servomotor to swing within 7? at varying speed. The influence of the atomizer parameters, such as translation of the atomizer, swing angle of the atomizer, substrate falling speed and spraying pressure, on the spray deposition was studied. The optimized parameters of the spray deposition process were obtained. The results show that the large size billets with uniform surface quality can be made through adjusting swing frequency and angle of the atomizer, offset distance of the atomizer and inclined angle of the substrate; the valid spray area will decrease and the dimension of top surface will reduce when pressure is less than 0.4 MPa within certain spray distance; meantime, the moving time and cooling time of the droplets are extended, which will lead to loose structure and bad densification. When the pressure, the swing angle and the eccentric offset of the atomization equal 0.5 MPa, 7? and 60 mm, respectively, large size billets with fine texture and diameter of 500 mm can be produced.
Key words: spray deposition; large size billet; atomizer; swing angle; eccentric offset
1 Introduction
The spray deposition with swing atomizer is a fast growing metal forming technology, by which the stocks or semi-product of the metal material can be produced with the rapid solidification method. The technology can be used to produce strips, tubes and billets by adopting depositor with different shapes and movement modes[1-2]. For production of the billets with the diameter less than 400 mm, the technology of spray deposition is mature at present[3-4]. But for the large size billets’ making, especially for billet with diameter larger than 500 mm, the spray technology is still under study. The design of the atomizer’s structure and the optimization of the process parameters are the key factors during the large size billets’ making.
The spray deposition technology can be divided into two types. One is the current technology in which the atomizer is fixed at one place or swings in a given angle[5-6]. Due to the limit of the swing angle, the area of the spray deposition cannot be very large. Additionally, the spindle of the substrate is installed vertically, so the maximum diameter of the billet can only reach 400 mm. The other is the technology in which the atomizer keeps reciprocating scanning in horizontal direction[7-9]. The main difference between the two types is that the movement of the atomizer is changed from swing to reciprocating-movement in horizontal direction. The larger size billets can be produced through adjusting the amplitudes of the swing angle or the reciprocating- movement. But the adjustable range of the reciprocating- movement is much greater than that of the swing movement, so large size billets can be fabricated by applying the reciprocating scanning atomizer. The problem is that the process of the reciprocating- movement can hardly be finished in a closed deposition chamber, and the device is difficult to be sealed tightly. So there must be some heavy metal spilling out, which will contaminate the environment and threaten the people’s health. Moreover, the control of the billets’ shape is not easy[10-11].
In order to overcome these problems, the eccentric-type swing atomizer was presented in this work. The kernel of spray deposition with eccentric- type swing atomizer was the determination of cross- section curve of the spray tube, the structure of the atomizer, the installed mode of the spindle of the depositor, and the optimized parameters. A new spray deposition technology was proposed, which has many advantages: the whole deposition process can be finished in a closed chamber without contamination; there is an offset between the spraying center and the inclined substrate center; the movement of the swing atomizer with variable velocity can be realized. Through experiments on optimizing the spray process parameters,the large size billets with good shape and dense contexture were made.
2 Principle of spray deposition with eccentric-type atomizer
There is little difference in principle between the spray deposition with eccentric-type atomizer and the traditional spray deposition[12-14] (see Fig.1). To obtain large size billets with dense contexture, the scan velocity, the swing frequency, the offset distance and the inclined angle should be set appropriately.
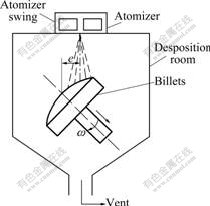
Fig.1 Schematic diagram of spray deposition with swing atomizer
The reciprocating-movement of the swing atomizer is realized by an alternating current servomotor. The atomizer scans within a given range and the velocity is adjustable, and the quantity of the spray in unit time is invariable. The smaller the diameter of the billet is, the less the deposition quantity is needed, and the faster the scanning velocity should be. Contrarily, the more the deposition quantity is needed, the slower the scanning velocity should be. To guarantee the uniformity of the surface quality, the swing frequency and swing angle of the atomizer should be changed. And to enlarge the deposition area, the offset distance should be adjusted. When the falling velocity of the spindle is well coordinated with the growing velocity of the deposition volume, a reasonable billet can be made at a constant spraying height.
The flow velocity of the atomizing gas is greatly influenced by the distribution and the cross-section shape of the atomizer muzzles. And the density of the deposition billets is justly determined by the atomizing pressure and the flow. Therefore, the structure design of the atomizer’s muzzle is very important. The atomizer muzzles consist of round holes with equal distance (see Fig.2). The outlet is composed of several Laval type tubes (see Fig.3)[15-16]. The state of the flowing in the tube is determined by the outlet pressure and Mach

Fig.2 Schematic diagram of atomizer with evenly distributed holes
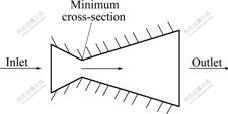
Fig.3 Schematic diagram of cross-section of atomizer’s muzzle
number in the minimum cross-sections area[17-18].
To get the supersonic flow in the divergent cone of the Laval type tube, an appropriate expansion angle should be chosen. After the repeated tests with different angles, the half-apex angle in the divergent cone was determined to be about 5?. If the expansion angle is too large, the jet flow will diffuse very fast. And when the expansion angle is too small, the length of the supersonic flow passage will become much longer and the boundary layer will get thicker, resulting in the decrease of the pressure. Therefore, the transition section from the throat section to divergent cone should be smooth. In practice, a curve with a certain curvature is applied. A smaller radius of curvature should be applied in the intersection between the divergent cone and jet’s end surface because a large curvature will cause an unsteady and weak penetrating flow. Based on the above analyses, a new type of the atomizer with evenly distributed distance holes, which is suitable for the acceleration of the higher pressure gas, was designed.
3 Deposition experiments for eccentric-type atomizer with annular hole
3.1 Design of experiments
To further study the influence of the process parameters, such as swing angle, swing frequency, falling velocity of the substrate, offset distance, and spraying pressure, two experiment projects, groups A and B, were presented.
In experiments of group A, the atomizer was fixed without movement, the pressure of the atomizing gas was lower and the offset distance between the spraying center and the substrate center was shorter. Compared with those in group A, for the atomizer scanning in horizontal direction, the pressure was higher and the offset distance was longer in experiments of group B. The whole process was controlled by the modifiable PLC program, and the deposition shape was shown in the infrared ray monitor. The primary and the secondary atomizers were both made with evenly distributed holes. The detailed parameters are listed in Table 1.
3.2 Analysis about experiment of group A
The atomizer was fixed in horizontal direction, and the online control was introduced during the spray process. After spraying for 5 min, the concaves appeared in the upper deposition surface. During the process of the deposition, the concaves still existed. And the grain of the atomizing metal droplet became coarser but distributed uniformly. To get smooth surface, the falling speed of the substrate was adjusted to 0.23 mm/s after depositing for 8 min. The whole process lasted for 32 min. The diameter of the billet is 300 mm for the upper surface, that for the lower surface is 450 mm, and the height of the billet is 250 mm. The billet is of loose structure and bad densification. Fig.4 shows that there exist large metal grain and cavity on the outer surface.
For the phenomena above, there are several reasons: the lower pressure of the atomizing gas changes the function of the injection density; and the varied gas-liquid
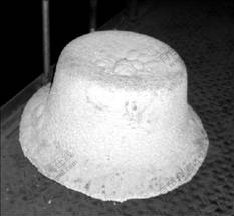
Fig.4 Photo of billet from experiment of group A
ratio affects the size of the metal droplet.
The pressure of the atomizing gas is an important parameter for the state of the melted metal droplet, and it also has an influence on the injection density function and the speed of the droplet. During the atomizing process, the convective heat exchange between the high-pressure gas and the melted metal disperses the melted metal into droplet, and some of the droplets’ state is changed to be semi-solid or semi-liquid.
When the pressure of the atomizing gas is less than 0.4 MPa, two cases will take place. One is that the valid spray area reduces, and the diameter of the upper surface decreases. The other is that the velocity of the droplets is slower and the cooling time increases. Thus the ratio of the liquid phase declines, which results in loose structure and low density.
3.3 Analysis about experiment of group B
At the eccentric offset of 60 mm, the swing angle of ±7?, the swing frequency of 8 Hz and the atomizing pressure of 0.5 MPa, the atomizing gas supply system began to spray when the crucible prepared with material was inserted into the atomizer. The experimental parameters are listed in Table 1. During the first 5 min of the spraying, the melted metal droplet was a finer grain. The distribution of the droplet grain was uniform and the deposition surface was flat. 12 min after the process started, the center of deposition surface was a little higher than the edge, which means the ejecting distance became shorter. And the rotating speed of the spindle was adjusted to 0.15 mm/s until the material was completely consumed. The whole process lasted for 25 min. Finally the billet with good shape was obtained (see Fig.5). The diameter of the billet is 480 mm for the upper surface, that for the lower surface is 500 mm, and the height of the billet is 250 mm. From Fig.5, it can be seen that the billet is of a fine density and smooth cylindrical surface although the particle of the lower part is coarse,
Table 1 Experimental conditions of atomizer with annular holes
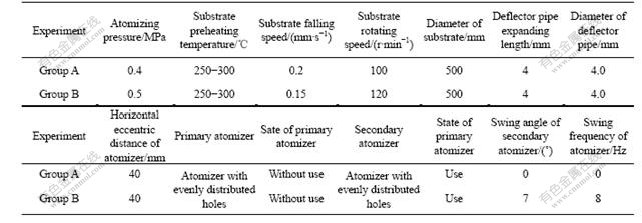
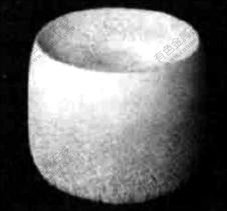
Fig.5 Photo of billet from experiment of group B
which results from the splash of the melted droplet at the deposition edge.
From the comparison of the two groups, the billet with finer shape and tight density can be made at the eccentric offset of 60 mm, the swing angle of ±7? and the swing frequency of 8 Hz. The experiment results are helpful for the process of the spray deposition during the making process of large size billets. They also offer practical guidance for the industrial production.
4 Conclusions
1) A new eccentric-type atomizer with equal distance holes is designed. The spray of the sonic or ultrasonic flow in the outlet of the atomizer can be achieved.
2) For the eccentric-type swing atomizer, the nominal pressure of the atomizing gas is 0.5 MPa. When the operating pressure is less than 0.4 MPa, it is difficult to guarantee the forming of the billet, which maybe results in loose structure and the reduction of density.
3) There exists an offset distance between the spray center of the atomizer and the center of the substrate. The eccentric-type atomizer can enlarge the valid atomizing area. At the swing angle of 7?, the atomizing pressure of 0.5 MPa, and the eccentric distance of 60 mm, the billets with diameter of 500 mm can be made.
4) For the large diameter billets’ making, the advantages of the spray deposition with swing atomizer and the reciprocating movement should be considered totally, which can make the process of the deposition easier and more convenient.
References
[1] GRANT P S. Solidification in spray forming [J]. Metallurgical and Materials Transactions A: Physical Metallurgy and Materials Science, 2007, A38(7): 1520-1529.
[2] ZHOU Yi-zhang, WU Yue, LAVERNIA E J. Process modeling in spray deposition: A review [J]. International Journal of Non-Equilibrium Processing, 1997, 10(2): 95-183.
[3] XIAO Yu-de, LI Min, ZHONG Jue, LI Wen-xian, MA Zheng-qing. Devitrification behaviour of rapidly solidified Al87Ni7Cu3Nd3 amorphous alloy prepared by melt spinning method [J]. Journal of Central South University of Technology, 2007, 14(3): 285-290.
[4] TAN Dun-qiang, LI Wen-xian, XIAO Yu-de, WANG Chong. Precipitated phases and thermodynamic analysis during solidification of Al-Fe-X system at slow cooling rate [J]. Transactions of Nonferrous Metals Society of China, 2003, 13(5): 1133-1136.
[5] YUAN Wu-hua, CHEN Zhen-hua, XU Hai-yang, ZHANG Fu-quan, FU Ding-fa. Properties and microstructure of 7075/SiCp composites prepared by spray deposition [J]. Transactions of Nonferrous Metals Society of China, 2003, 13(5): 1160-1163.
[6] ZHAN Xiao-jun, LI Wen-xian, TAN Dun-qiang, WANG Ri-chu, DING Rong-hui. Preparation technology of 6066/SiCp billet by spray co-deposition with scanning atomizer to and fro [J]. Light Alloy Fabrication Technology, 2004, 32(6): 43-46, 51. (in Chinese)
[7] BAI Zhen-hai, LI Wen-xian, WANG Ri-chu. Study on the extrusion process of spray-deposition SiCP/Al composite and 6066 Al alloy [J]. Aluminum Fabrication, 2003, 150(3): 27-33. (in Chinese)
[8] SRIVASTAVA A K, OJHA S N, RANGANATHAN S. Microstructure feature and heat flow analysis of atomized and spray-formed Al-Fe-V-Si alloy [J]. Metallurgical and Materials Transactions A: Physical Metallurgy and Materials Science, 1998, A29(8): 2205- 2218.
[9] ELLENDT N, SCHMIDT R, KNABE J, HENEIN H, UHLENWINKEL V. Spray deposition using impulse atomization technique [J]. Materials Science and Engineering A, 2004, A383(1): 107-113.
[10] TAN Dun-qiang, LI Wen-xian, XIAO Yu-de, WANG Ri-chu, MA Zheng-qing, XIONG Bai-qing, ZHU Bao-hong, ZHANG Yong-an. Phase transition of Al-Fe-V-Si heat resistant alloy by spray deposition [J]. Transactions of Nonferrous Metals Society of China, 2003, 13(3): 568-573.
[11] YANG Zheng-wen. Perturbation analysis of extrusion of porous metal materials [J]. Applied Mathematical Modelling, 1995, 19(10): 601-612.
[12] GRANT P S, CANTOR B, KATGERMAN L. Modelling of droplet dynamic and thermal histories during spray forming (II): Effect of process parameters [J]. Acta Metallurgica et Materialia, 1993, 41(11): 3109-3118.
[13] PRYDS N H, HATTEL J H, PEDERSEN T B, THORBORG J. An integrated numerical model of the spray forming process [J]. Acta Materialia, 2002, 50(16): 4075-4091.
[14] GRANT P S. Spray forming [J]. Progress in Materials Science, 1995, 39(4): 497-545.
[15] CUI C S, FRITSCHING U, SCHULZ A, LI Q C. Mathematical modeling of spray forming process of tubular performs (Part 1): Shape evolution [J]. Acta Materialia, 2005, 53(9): 2765-2774.
[16] PRYDS N H, HATTEL J H. Spray forming: A numerical investigation of the influence of the gas to melt ratio on the billet surface temperature [J]. International Journal of Thermal Sciences, 2005, 44(6): 587-597.
[17] HATTEL J H, PRYDS N H. A unified spray forming model for the prediction of billet shape geometry [J]. Acta Materialia, 2004, 52(18): 5275-5288.
[18] SAHU S N, HARIKISHORE S, KORIA S C. Solidification behaviour of droplets in spray deposition [J]. Powder Metallurgy, 2005, 48(3): 270-276.
(Edited by CHEN Wei-ping)
Foundation item: Project(G1999064900) supported by the National Key Fundamental Research and Development Program of China
Received date: 2007-09-22; Accepted date: 2007-11-20
Corresponding author: LI Jian-pin, PhD; Tel: +86-731-8830293; E-mail: rikennpei102@hotmail.com