文章编号:1004-0609(2008)S1-0080-04
石煤湿法强化提钒新工艺
魏 昶,李存兄,樊 刚,李旻廷,邓志敢
(昆明理工大学 材料与冶金工程学院,昆明 650093)
摘 要:分别考察石煤常压氧化酸浸和加压氧化酸浸过程中的钒浸取率。结果表明:采用石煤加压氧化酸浸强化提钒新工艺钒浸出率接近90%,比传统工艺提高15%以上,比现有常压浸出工艺的钒浸出率提高20%,特别是当加入催化剂R时,加压氧化酸浸工艺的优势更为突出。提出石煤加压氧化酸浸新工艺的较佳工艺条件:硫酸酸度约为250 g/L,时间约为4 h,加压釜内压强约为1.2 MPa, 浸出温度为100~120 ℃,催化剂R的用量约为石煤矿量的2.5%。
关键词:石煤;钒;氧化酸浸;催化剂;浸取率
中图分类号:TF 841.3 文献标识码:A
New process of vanadium extraction from black shale by strengthening hydrometallurgy
WEI Chang, LI Cun-xiong, FAN Gang , LI Min-ting, DENG Zhi-gan
(Faculty of Materials and Metallurgical Engineering, Kunming University of Science and Technology,Kunming 650093, China)
Abstract: The leaching rates of vanadium of oxidizing acid leaching at atmospheric pressure and oxidizing acid pressure leaching were studied separately by contrasting conclusion. The results show that the leaching rate of vanadium of oxidizing acid pressure leaching is almost 90%, which is 15% higher than traditional technology and enhanced by 20% than the present acid leaching at atmospheric. When using catalyst R, the advantages of oxidizing acid pressure leaching is more prominent. The better technological conditions are that the acid concentration is 250 g/L, the leaching time is 4 h, the oxygen pressure is about 1.2 MPa, the temperature is 100~120 ℃ and the dosage of catalyst is 2.5% of the stone- coal.
Key words: stone-coal; vanadium; oxidizing acid leaching; catalyst; leaching rate
我国含钒石煤资源储备非常丰富,主要蕴藏在煤炭资源贫乏的我国南方诸省及西北地区,遍布于湘、鄂、川、黔、桂、浙、皖、赣、陕、甘、晋和豫等20余省,石煤中钒的总储量为我国钒钛磁铁矿中钒总储量的7倍,是我国独特的一种钒矿资源。
国内石煤提钒的传统工艺是钠化焙烧—水浸—酸沉粗钒—碱溶铵盐沉钒—热解铵制精钒,该工艺设备要求不高、技术简单、投资不大,但V2O5的转浸率和回收率较低(总回收率约为45%),石煤耗量大,资源浪费严重,该法从水浸液到取得精钒工艺流程较长,生产过程复杂,不能连续生产,机械化程度差,劳动强度大,且消耗材料多,生产成本高,特别是该工艺选用食盐作为钠盐氧化焙烧,实际食盐用量为理论用量的20至40倍,且焙烧过程中产生大量烟尘、氯气和氯化氢气体,对周围环境污染严重[1-3]。随着全球对环境保护和提高资源有效利用的重视,寻找新的低污染、高效率的提钒工艺已成为钒冶炼工业中一个急待解决的问题。
近年来,采用全湿法从石煤中提钒得到大量研究,也有一定的工业应用。但这些方法都是采用常压浸出的方法,在酸性介质条件下,浸出过程加入一定量的氧化剂,使矿物中不溶于酸的三价钒氧化转化至可溶于酸的四价或五价钒,再从溶液中提取V2O5 [4-9]。但常压下,由于反应强度不够,存在浸出效率低、硫酸耗量大、钒浸出率偏低及资源浪费严重等问题,且因浸出液酸度过高增加了下一步萃取提钒工序的难度和投资成本。
本文作者分别进行常压和加压下的石煤氧化酸浸实验,通过研究发现,采用石煤加压酸浸强化提钒新工艺钒浸出率接近90%,比传统工艺提高15%以上,比现有常压浸出工艺浸出率提高20%,极大降低了能耗和原材料的消耗。
1 实验
1.1 原料及成分分析
实验用石煤矿样采自贵州某地,其化学成分如表1所列。
表1 石煤矿主要化学成分
Table 1 Main chemical composition of stone-coal (mass fraction, %)
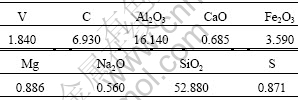
1.2 实验条件及流程
实验主体设备为2 L加压釜,容量为500 mL带冷凝管的三口烧瓶,常压和加压浸出用氧化气体为瓶装工业氧气或空气,浸出剂是浓度为98%的浓硫酸,催化剂R为化学分析纯。
影响石煤浸出过程的因素很多,本研究选择浸出始酸度、时间和催化剂R作为考察因子。为研究方便,对其它因素作如下设定:1) 常压浸出和加压浸出用石煤矿粒度均为74 μm;2) 液固比为1.5 mL?1 g;3) 搅拌强度为650 r/min。
在上述条件下分别向加压釜和三口反应器内加入矿料和硫酸溶液后,通入氧气,在反应温度下进行酸氧化浸取。浸取一定时间后,开始降温并停止通氧气,取出浆料进行液固分离。计量滤液的体积、洗涤后滤液的总体积以及滤渣和烘干后渣的质量。
2 结果及分析
2.1 酸度对钒浸出率的影响
向加压釜和三口烧瓶内各加100 g石煤矿料,时间为4 h,控制加压釜内反应温度150 ℃,三口烧瓶内反应温度为93 ℃(昆明当地沸点),加压釜内压力为1.2 MPa,不断向三口烧瓶和加压釜鼓入工业氧气的条件下进行酸度对钒浸出率的影响实验,结果如图1所示。由图1可看出,在常压氧化浸出和加压氧化浸出条件下,钒浸出率均随硫酸酸度的增加而增大;在加压氧化浸出过程中,当酸度大于250 g/L时,钒浸出率略有下降;在常压氧化浸出过程中,当酸度大于300 g/L时,钒浸出率增幅不大。由此可见,在其它条件相同的条件下,加压氧化酸浸的钒浸取率比常压氧化酸浸的高出20%以上。
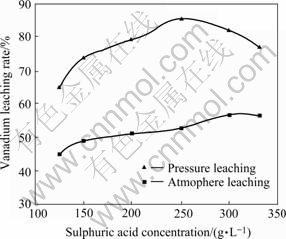
图1 酸度对钒浸出率的影响
Fig.1 Effect of sulfuric acid concentration on vanadium leaching rate
2.2 浸出时间对钒浸出率的影响
将石煤矿粉和酸度为250 g/L的硫酸溶液按液固比为1.5 mL?1 g分别加入到加压釜和三口反应器,并不断通入氧气,维持加压釜内压力为1.2 MPa,控制加压釜内反应温度120 ℃和三口烧瓶内反应温度93 ℃(昆明当地沸点)的条件下进行了时间对钒浸出率的影响实验,结果如图2所示。由图2可知,随浸出时间的延长,常压和加压下钒浸出率都提高,当浸出时间超过4 h时,继续延长时间,钒浸出率提高幅度不大。在该组实验条件下,加压氧化酸浸的钒浸取率比常压氧化酸浸的高出25%以上。
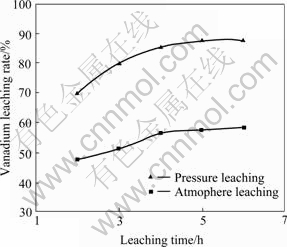
图2 浸出时间对钒浸出率的影响
Fig.2 Effect of leaching time on vanadium leaching rate
2.3 氧化剂用量对钒浸出率的影响
将石煤矿粉和酸度为250 g/L的硫酸溶液按液固比1.5 mL?1 g分别加入到加压釜和三口反应器,并不断通入工业空气,维持加压釜内压力1.2 MPa,控制加压釜内反应温度120 ℃和三口烧瓶内反应温度 93 ℃(昆明当地沸点),浸出4 h,在加压和常压条件下考察了催化剂R的用量对钒浸出率的影响。实验结果如图3所示。
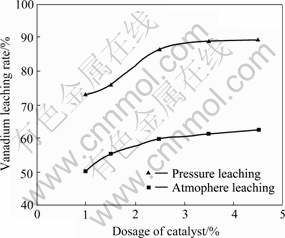
图3 催化剂R用量对钒浸出率的影响
Fig.3 Effect of dosage of catalyst on vanadium leaching rate
由图3 可知,在石煤常压和加压氧化酸浸过程中加入催化剂R所得钒浸出率比同条件下无催化剂时钒浸出率分别提高5%和6%以上。在该组实验条件下,加压氧化酸浸的钒浸取率比常压氧化酸浸的高出23%以上。
3 结论
1) 采用石煤加压酸浸强化提钒新工艺钒浸出率接近90%,比传统工艺的钒浸取率提高15%以上,比现有常压氧化酸浸工艺浸出率提高20%,特别是当加入催化剂R时,石煤加压酸浸强化提钒新工艺的优势尤为突出。
2) 石煤矿直接加压氧化酸浸的较佳技术条件为:硫酸酸度约为250 g/L,时间约为4 h,加压釜内压力约为1.2 MPa, 浸出温度为100~120 ℃,催化剂R的用量约为石煤矿量的2.5%,并在此最佳条件下钒的浸取率可接近90%。
3) 在较佳工艺条件的基础上可采用两段浸出,能大幅度提高钒浸取率的同时降低浸出液的酸度,从而降低浸出过程酸耗和浸出液后续中和处理的碱耗,避免引入新的杂质。
4) 采用石煤加压氧化酸浸新工艺强化了浸出过程,极大提高钒浸出率,避免了现存石煤提钒主导工艺带来的环境污染和资源浪费等问题,具有广阔的发展前景。
REFERENCES
[1] 舒型武.石煤提钒工艺及废物治理综述[J]. 钢铁技术, 2007(1): 47-48.
SHU Xing-wu. Vanadium extraction technology from stone coal and waste treatment [J]. Iron Steel Technology, 2007(1): 47-48.
[2] 潘 勇, 于吉顺, 吴红丹. 石煤提钒的工艺评价[J]. 矿业快报, 2006, 4(4): 10-12.
PAN Yong, YU Ji-shun, WU Hong-dan. Process evaluation of vanadium extraction from stone coal [J]. Express Information of Mining Industry, 2007, 4(4): 10-12.
[3] 邓志敢, 魏 昶, 樊 刚, 李旻廷. 石煤提钒传统工艺与氧压酸浸新工艺对比[J]. 稀有金属, 2007, 31(s): 140-145.
DENG Zhi-gan, WEI Chang, FAN Gang, LI Min-ting. Contrast of extracting from stone coal between traditional craft and new craft of oxygen pressure acid leaching [J]. Chinese Journal of Rare Metals, 2007, 31(s): 140-145.
[4] 杨静翎, 金 鑫. 酸浸法提钒新工艺的研究[J]. 北京化工大学学报, 2007, 34(3): 254-257.
YANG Jing-ling, JIN Xin. A new way of recovering vanadium from iron/vanadium slag [J]. Journal of Beijing University of Chemical Technology, 2007, 34(3): 254-257.
[5] 梁建龙, 刘惠娟, 史文革, 胡鄂明, 李熙琪, 彭 军. 湿法冶金提钒浸出新工艺[J]. 中国矿业, 2006, 15(7): 64-66.
LIANG Jian-long, LIU Hui-juan, SHI Wen-ge, HU E-ming, LI Xi-qi, PENG Jun. A study of a new technology leaching of vanadium ores with hydrometallurgy [J]. China Mining Magazine, 2006, 15(7): 64-66.
[6] 常 娜, 顾兆林, 李 云. 石煤提钒浸出工艺研究[J]. 无机盐工业, 2006, 38(7): 57-59.
CHANG Na, GU Zhao-lin, LI Yun. Study on leaching vanadium from stone coal [J]. Inorganic Chemicals Industry, 2006, 38(7): 57-59.
[7] 郑祥明, 田学达, 张小云, 石 华, 邓益强. 湿法提取石煤中钒的新工艺研究[J]. 湘潭大学自然科学学报, 2003, 25(1): 43-45.
ZHENG Xiang-ming, TIAN Xue-da, ZHANG Xiao-yun, SHI Hua, DENG Yi-qiang. Extraction of vanadium pentoxide from stone coal with a wet chemical separation method [J]. Natural Science Journal of Xiangtan University, 2003, 25(1): 43-45.
[8] 鲁兆伶. 用酸法从石煤中提取五氧化二钒的试验研究与工业实践[J]. 湿法冶金, 2002, 21(4): 175-183.
LU Zhao-ling. Investigation and industrial practice on extraction of V2O5 from stone coal containing vanadium by acid process [J]. Hydrometallurgy of China, 2002, 21(4): 175-183.
[9] 向小艳, 王明玉, 肖连生, 高泽斌. 石煤酸浸提钒工艺研究[J]. 稀有金属与硬质合金, 2007, 35(3): 10-13.
XIANG Xiao-yan, WANG Ming-yu. XIAO Lian-sheng, GAO Ze-bin. Study on acid leaching of vanadium from stone coal [J]. Rare Metals and Cemented Carbides, 2007, 35(3): 10-13.
基金项目:国家高技术研究发展计划资助项目(2006AA06Z130);云南省科技厅支持资助项目(2007GA010)
通讯作者:魏 昶,教授,博士;电话:0871-5188819;E-mail: weichang2008@sina.com
(编辑 李艳红)