文章编号:1004-0609(2016)02-0392-10
设计与制备具有放射状介孔壳层的PS/MSiO2复合磨料及其抛光氧化硅片效果
陈爱莲1,汪亚运2,陈 杨2
(1. 常州大学 机械工程学院,常州 213164;
2. 常州大学 材料科学与工程学院,常州 213164)
摘 要:以阳离子表面活性剂CTAB为牺牲模板、TEOS为硅源、硝酸铵/乙醇混合溶液为选择性溶剂,合成以表面经PVP修饰的聚苯乙烯(Polystyrene, PS)微球为内核、表面包覆介孔氧化硅(Mesoporous-silica, MSiO2)壳层的新型PS/MSiO2复合磨料。采用场发射扫描电镜(FESEM)、透射电镜(TEM)和原子力显微镜(AFM)测试,研究PS/MSiO2复合磨料的核壳结构以及经复合磨料抛光后的表面粗糙度均方根值和抛光速率。结果表明:PS/MSiO2复合磨料具有包覆完整的核壳结构,其PS内核尺寸为200~210 nm,介孔氧化硅壳层厚度约为30 nm,包覆层中存在大量放射状介孔孔道。氮气吸附/脱附测试表明:复合磨料的比表面积为612 m2/g,介孔孔径为2~3 nm;经复合磨料抛光后衬底表面粗糙度均方根值(RMS)和抛光速率(MRR)分别为0.252 nm和141 nm/min,明显优于粒径相当的常规SiO2磨料(0.317 nm, 68 nm/min)。复合磨料中有机内核及壳层中的介孔孔道结构有利于降低颗粒的弹性模量和表面硬度,从而有助于减小磨料在衬底表面的压痕深度并降低抛光表面粗糙度。此外,复合磨料可借助其高比表面积提高对抛光液中有效化学组分的吸附能力,从而增强接触微区内的化学反应活性以提高抛光速率。
关键词:聚苯乙烯;介孔氧化硅;核壳结构;复合磨料;化学机械抛光
中图分类号:TB383 文献标志码:A
根据国际半导体技术发展路线图(International technology roadmap for semiconductors, ITRS)2014版的预测,超大规模集成电路还将延续Moore定律迅速发展。伴随集成度的提高、特征尺寸的减小以及各种新材料、新工艺的不断涌现,对化学机械抛光/平坦化(Chemical mechanical polishing/planarization, CMP)技术[1-2]提出了更加严苛的要求。以强度低、脆性大的低介电常数(Low-k)薄膜材料[3-4]为例,通常在CMP过程易产生剥落、破碎和划痕,导致成品率下降和制造成本的提高[5]。为此,Semiconductor Insights的专家也将Low-k薄膜等易碎、易损伤材料的加工列为22 nm以下节点的十五大技术挑战之一。
磨料的功能化和复合化结构设计为实现高效无损伤抛光提供了有益思路。其中,在聚合物微球内核表面包覆无机纳米颗粒的有机/无机复合磨料,具有区别于常规无机颗粒的非刚性力学特性,在减少抛光表面缺陷方面发挥了积极作用。比利时微电子中心和鲁汶大学的ARMINI等[6-7]曾通过硅烷偶联剂表面改性的方法得到了聚甲基丙烯酸甲酯(PMMA)/SiO2和PMMA/CeO2复合磨料,明显改善对二氧化硅薄膜及铜布线的抛光表面质量。遗憾的是,这种方法无法有效获得具有完整核壳结构的复合磨料,无机纳米颗粒不能在有机内核表面均匀包覆,且壳层厚度也无法准确控制。为了解决这一问题,本文作者课题组[8-9]利用化学原位包覆技术,合成了结构完整、包覆均匀,且具有可控壳厚的聚苯乙烯(PS)/CeO2和PS/SiO2复合磨料。然而,上述草莓状复合磨料的壳层均由纳米无机颗粒组成,在抛光过程中结构稳定性不够理想,从壳层脱落的纳米颗粒易附着在抛光表面造成二次污染,不利于CMP后清洗。为此,本文作者课题组[10]和中科院上海微系统所[11]进一步分别利用正硅酸乙酯在酸性条件下的水解过程,在PS内核表面包覆连续网状氧化硅壳层,得到了具有连续壳层的PS/SiO2复合磨料,明显提高磨料在抛光接触过程中壳层的结构稳定性。而不足之处在于该类型磨料的抛光速率仍有待进一步提高。
上述核壳结构有机/无机复合磨料的核心设计思想在于利用弹性有机内核与刚性无机壳层耦合产生的非刚性力学特性[12],从调控磨料与衬底之间界面物理接触状态的层面对机械磨损过程进行优化,从而降低抛光衬底的机械损伤。然而,该类型复合磨料则无法有效改善受限区域内的化学环境,对增强局部真实接触区域内化学反应活性、提高材料去除率无明显促进作用,在同时满足高效抛光和无损伤抛光方面的作用不能完全令人满意。
为了进一步研究核壳结构PS/SiO2复合磨料,本文作者尝试对其常规的合成条件进行改进,在制备过程引入CTAB作为介孔结构导向模板剂,利用正硅酸乙酯的溶胶凝胶过程在具有不同表面性质的PS内核表面包覆SiO2/CTAB前驱物;进一步通过硝酸铵乙醇混合溶液选择性去除CTAB模板后,得到以PS微球为内核、介孔氧化硅(Mesoporous MSiO2)为壳层的PS/MSiO2复合磨料,并利用红外光谱、扫描电镜、透射电镜以及N2吸附/脱附等手段对样品的结构进行表征。在相同抛光试验参数条件下,对比常规实体SiO2磨料与PS/MSiO2复合磨料对热氧化硅片的平坦化特性差异,采用原子力显微镜测定抛光前后衬底表面形貌、粗糙度及轮廓曲线,利用表面粗糙度和抛光速率两个指标去评价抛光效果。
1 实验
1.1 化学试剂
苯乙烯单体(St),化学纯,购自国药集团上海化学试剂有限公司。使用前采用浓度为5%(质量分数)的NaOH溶液反复洗涤除去阻聚剂,用无水CaCl2干燥,再经减压蒸馏处理后置于低温保存,备用。
其他试剂包括:丙烯酸、碳酸氢氨、碳酸氢钠、过硫酸钾(KPS)、聚乙烯吡咯烷酮(PVP)、无水乙醇、氨水、正硅酸乙酯(TEOS)和氢氧化钠,均购自国药集团上海化学试剂有限公司;十六烷基三甲基溴化铵(CTAB)购自常州新华活性材料研究所,偶氮二异丁基脒盐酸盐(AIBA)购自美国Aladdin Chemistry公司,上述试剂未经处理直接使用。硝酸铵为自制。
1.2 PS/MSiO2复合磨料的合成与表征
经PVP表面修饰PS微球[13]的制备:将St(8.5 g)、PVP(1.0 g)和去离子水(150 g)依次加入带有冷凝管、氮气导管的四口烧瓶中,搅拌均匀后通氮气驱氧30 min。将体系温度缓慢升至70 ℃,恒温5 min后加入AIBA (0.18 g,溶于30 g去离子水中)引发聚合,反应持续持续时间为24 h。所得样品标记为PS-1。表面显电负性PS微球[14]的制备:依次向配有冷凝管和氮气导管的四口圆底烧瓶中加入St (7.6 g)、丙烯酸(0.4 g)和去离子水(25 g),搅拌均匀后加入含有碳酸氢氨(0.2 g)、碳酸氢钠(0.4 g)和去离子水(50 g)的混合溶液,搅拌均匀后通入氮气驱氧30 min。随后用油浴缓慢升温至70 ℃,恒温5 min后加入KPS(0.32 g,溶于25 g去离子水中)引发聚合,7 h后停止反应。所得样品标记为PS-2。上述聚合反应均在磁力搅拌(330 r/min)和氮气保护条件下完成。
分别量取含有PS-1和PS-2微球的乳胶液2.5 mL分散在体积比为3:1 的去离子水(112.5 mL)/乙醇(37.5 mL)混合溶液中,超声强化分散10 min后加入CTAB(0.3 g)和氨水(1.0 g)。将所配制的溶液置于30 ℃恒温水槽中持续搅拌(搅拌速度为250 r/min)30 min,再逐滴加入TEOS (0.4 g),持续反应2 h后将沉淀物离心分离、洗涤。在60 ℃条件下,将烘干后的白色粉末用浓度为10 mg/mL的硝酸铵/乙醇混合溶液[15]反复洗涤以选择性去除 CTAB模板剂,再将颗粒物离心分离、反复水洗醇洗,烘干后备用。以PS-1和PS-2微球为内核制备的复合磨料依次标记为PS/MSiO2-1和PS/MSiO2-2。另外进行了一组不加PS乳胶液的空白实验,其他条件同上。
采用美国Thermo公司生产的Nicolet 6700型傅里叶红外光谱仪(FTIR)定性分析样品表面基团;小角衍射(XRD)分析在日本理学生产的D/max 2500 PC型X 射线粉末衍射仪上完成;样品的形貌和结构通过日本电子公司生产的JEM-2100型透射电镜(TEM)和德国蔡司公司生产的SUPRA 55型场发射扫描电镜(FESEM)进行表征;利用TEM所配备的OXFORD INCA 型能谱仪对样品表面进行元素分析;样品的比表面积和孔结构用N2物理吸附法在美国Micromeritics公司生产的ASAP 2010C型孔径分析仪上测定,分别通过BET和BJH模型计算样品的比表面积和孔径尺寸及分布。
1.3 抛光试验及评价
分别将一定质量的复合磨料PS/MSiO2-1及实心SiO2磨料(约300 nm,常州大学江苏省太阳能电池及储能材料与技术重点实验室提供)分散在去离子水中,配制成质量浓度为1%的悬浮液,用浓度为0.1 mol/L的NaOH溶液将浆料的pH值调至8,抛光试验前超声分散10 min。
将4英寸热氧化硅片(购自常州华诚常半微电子有限公司)作为抛光衬底,其表面氧化层(SiO2薄膜)厚度约为1200 nm。将其切割成约2 cm×2 cm的试件,用丹麦Struers公司生产的TegraForce-1/TrgraPol-15型抛光平台进行抛光试验,选用多孔聚氨酯抛光垫的型号为MD-Chem(Struers公司生产)。具体工艺参数如下:抛光压力为28 kPa,上盘转速为120 r/min,下盘转速为90 r/min,抛光液流量为100 mL/min,抛光时间为1 min。
抛光前后衬底表面形貌测试在美国DI公司生产,配备Dimention V控制器的NanoScope Ⅲa 型原子力显微镜(AFM)上完成,利用AFM自带NanoScope Analysis软件计算并分析样品的表面粗糙度值(Root-mean-square roughness, RMS)及微观轮廓曲线,扫描范围为5 μm×5 μm。根据文献[8]中给出的方法,计算抛光速率(Material removal rate, MRR),用单位时间内衬底厚度变化(nm/min)来表示。文中粗糙度数值及抛光速率均为3次测量平均值。
2 结果与讨论
2.1 样品的结构表征
无皂乳液聚合工艺制备的单分散PS微球样品(见图1)表面光滑,尺寸均一,利用图1中的标尺可估算出PS-1和PS-2微球的粒径分别约为200~210 nm和240~250 nm。

图1 所制备PS-1和PS-2微球样品的TEM像
Fig. 1 TEM images of obtained PS-1(a) and PS-2(b) samples
从样品的红外光图谱(见图2)可知,所得复合磨料样品在1636、1493和1452 cm-1附近处出现的吸收峰对应于苯环骨架振动的特征吸收;在758和698 cm-1 附近的吸收峰归属于单取代苯环的特征吸收[16],表明样品中存在聚苯乙烯。此外,图谱中1083、790 和462 cm-1附近的吸收峰分别对应Si—O—Si键的反对称伸缩、对称伸缩和弯曲振动峰[16-17],以上分析表明样品中又存在氧化硅。进一步可知,红外图谱中均未出现CTAB的特征吸收峰[15](在1476 cm-1处,对应C—N键的伸缩振动峰)。这表明前驱物经硝酸铵/乙醇混合溶液反复洗涤后,已成功将CTAB模板去除,最终产物为聚苯乙烯与氧化硅的复合物。
图3所示为复合磨料PS/MSiO2-1样品的SEM像。由图3可知,包覆后复合颗粒均呈单分散规整球形,其粒径为270~280 nm。此外,样品中存在极个别壳层破损的复合微球(如图3中箭头所示),可以清楚地观察到裸露出的内核及周围壳层,说明样品具有核壳包覆结构。
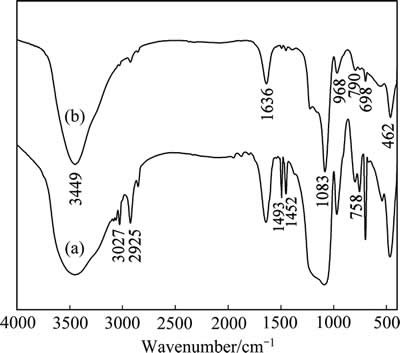
图2 所得PS/MSiO2-1和PS/MSiO2-2复合磨料样品的红外光谱
Fig. 2 FTIR spectra of as-prepared PS/MSiO2-1(a) and PS/MSiO2-2(b) composites

图3 复合磨料PS/MSiO2-1的FESEM像
Fig. 3 FESEM image of PS/MSiO2-1 composites
利用TEM进一步分析了PS/MSiO2复合磨料样品的结构特征,其结果如图4所示。由图4可以看出,经氧化硅包覆后得到的复合微球均保持了原PS内核良好的单分散性和球形度。从图4(a)中可以清晰地观察到PS/MSiO2-1样品边缘和中部存在明显的衬度差,氧化硅壳层均匀连续地包覆在内核表面,表明样品具有包覆完整的核壳结构。由PS/MSiO2-1样品的高倍电镜照片(见图4(b))可知,氧化硅壳层厚度约为30 nm,且壳层中存在较为明显的放射状介孔,其孔道均基本垂直于有机内核表面。从相应的EDS谱(见图4(f))中可以看出,样品表面存在Si、O、C和Cu元素,而且C元素的峰较强。分析可知,Cu元素可能来自于铜网,C元素一方面可能来自于铜网上的支撑碳膜,另一方面有可能是由于电子束穿过包覆层后直接作用到聚苯乙烯内核上,激发出C元素所致。以表面显负电性的PS-2微球为内核,包覆后所得PS/MSiO2-2复合微球(见图4(c))的粒径由240~250 nm增大至300~310 nm,表明其氧化硅壳层厚度同样约为30 nm;进一步能够观察到个别复合微球的壳层出现破损(如图4(c)中箭头所示),同样说明样品具有核壳包覆结构。将其高倍TEM像(见图4(b)与4(d))对比可知,复合磨料PS/MSiO2-2样品壳层中的放射状介孔结构并不明显,这表明PS内核的表面性质对包覆后氧化硅壳层结构具有明显影响。空白实验所得产物的TEM像如图4(e)所示,可以直观地观察到具有放射状孔道的介孔SiO2微球,其粒径为140~160 nm。
由样品的XRD谱(见图5)可知,所得PS/MSiO2-1样品在2θ=2.4°附近出现了一个尖锐衍射峰,对应六方介孔结构材料的(100)晶面[18],这也是六方介孔材料最主要的特征峰。此外,该处衍射峰的相对强度较高,表明材料的介孔结构长程有序性较好。对比可知,PS/MSiO2-2样品衍射谱线中没有出现高的有序衍射峰,说明该样品壳层中氧化硅不具备有序介孔结构,上述XRD分析与TEM的观察结果(见图4)相吻合。可能的原因如下:当聚合体系中加入PVP作为稳定剂时,所得PS-1微球经PVP表面修饰。在后续的包覆过程中,PVP与阳离子表面活性剂CTAB组成了高聚物与表面活性剂的超分子模板体系,在PVP与CTAB之间通过弱的离子偶极作用和疏水作用力的驱动下,自组装形成有序超分子结构的棒状胶束软模板,吸附于微球内核表面呈放射状有序排列[19]。硅源TEOS在体系中水解之后带负电,在阳离子表面活性剂CTAB的引导下聚集到模板周围,从而形成含有棒状胶束模板剂的有序介观结构;利用硝酸铵/乙醇混合溶液选择性去除CTAB后,最后在内核表面形成具有介孔结构的氧化硅壳层。
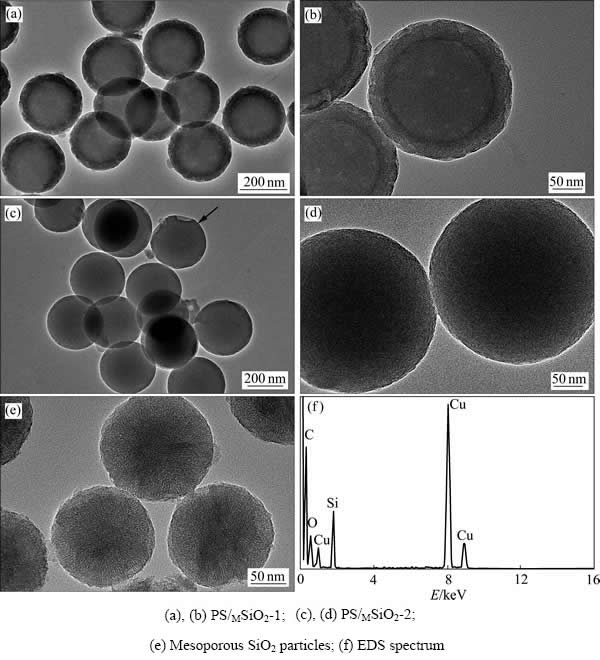
图4 复合磨料PS/MSiO2-1、PS/MSiO2-2以及介孔SiO2微球的TEM像及EDS谱
Fig. 4 TEM images((a)-(e)) and EDS spectrum(f) of PS/MSiO2-1, PS/MSiO2-2 and mesoporous SiO2 particles
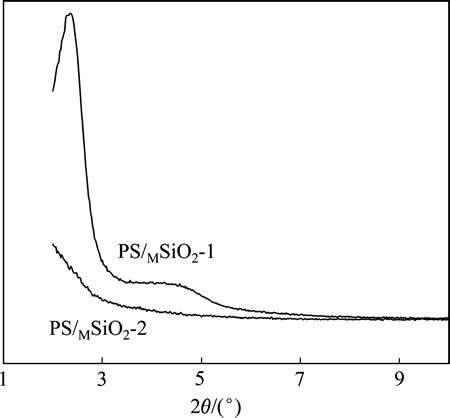
图5 样品的XRD谱
Fig. 5 XRD patterns of as-synthesized samples
图6所示为复合磨料PS/MSiO2-1样品的N2吸附/脱附等温线以及由脱附支得到的孔径分布曲线。由图6可知,该吸脱附等温线呈现Langmuir IV 型,表现出介孔材料的吸脱附特征。在相对压力为0.2~0.4时出现一个较为明显的突跃,可能是由于毛细管效应引起氮气在介孔中凝聚所致[20]。此外,显现出的H1 型回滞环说明样品具有圆筒形细长孔道,且孔径大小均一、分布较窄[21]。样品的BET比表面积为612 m2/g,远高于粒径相当的常规实体氧化硅微球的(16.7 m2/g)。从插入的孔径分布曲线可以看出,样品的孔径集中在2~3 nm,最可几孔径约为2.4 nm。

图6 复合磨料PS/MSiO2-1样品的N2吸附/脱附等温线及孔径分布曲线
Fig. 6 N2 adsorption/desorption isotherms and pore size distribution curves of PS/MSiO2-1composites
2.2 复合磨料的抛光特性评价
用AFM分析抛光前衬底的原始形貌,以及经常规实体SiO2磨料和PS/MSiO2-1复合磨料抛光后衬底表面典型的二维和三维形貌。为了更加直观地显示出抛光前后表面形貌特征的细微变化差异,将AFM二维形貌高度图的单位垂直高度设定在2 nm。对于AFM高度图而言,颜色较浅的区域代表该位置较高,反之则代表位置较低,二维形貌图中的颜色柱则表示了色差与相对高度之间的对应关系,其结果如图7(a1)所示,抛光前衬底表面较为粗糙,存在明显的高低起伏,在5 μm×5 μm范围的粗糙度RMS平均值为0.791 nm(见图7(a2))。经实体SiO2磨料抛光后,衬底表面(见图7(b1)和(b2))的平坦化程度得到较为明显的改善,从二维和三维形貌图中均可以看出表面趋于平整,粗糙度RMS值降至0.317 nm。经测定,实体SiO2磨料的抛光速率MRR为68 nm/min。由图7(c1)和(c2)可知,在本研究抛光试验条件下,经PS/MSiO2-1复合磨料抛光后的衬底表面AFM高度图中各区域的颜色最为均匀,表明衬底最为光洁平坦,没有出现明显的高度差。经测定,经复合磨料抛光后工件表面的粗糙度(RMS)值为0.252 nm,MRR达到141 nm/min,为常规SiO2磨料(68 nm/min)的两倍。

图7 抛光前以及经实体SiO2磨料和PS/MSiO2-1复合磨料抛光后衬底表面的典型AFM像
Fig. 7 Typical AFM images of substrate surfaces before and after CMP with solid SiO2 and PS/MSiO2-1 composite abrasives
为了更加直接地反映出抛光前后衬底表面的平整程度,相应地进行了微观轮廓分析,均选择AFM二维形貌图的一条对角线(如图7二维形貌图中白线所示)作为测量位置。由图8可知,抛光前原始晶片表面的轮廓起伏主要集中在±1.8 nm范围内波动,经常规SiO2磨料及PS/MSiO2-1复合磨料抛光后晶片表面的轮廓波动则分别集中在± 0.9和± 0.6 nm范围内。AFM形貌观察与表面轮廓分析结果均显示,在磨料尺寸相当以及相同的试验参数条件下,所制备以介孔氧化硅为壳层的有机/无机复合磨料能够有效改善抛光后晶片表面平坦化程度,以降低表面粗糙度。更重要的是,所设计合成的复合磨料还能够明显地提高对氧化硅片的抛光速率,这表明该类型新型结构有机/无机复合磨料有望在实现高效无损伤抛光方面发挥重要作用。

图8 抛光前后衬底表面的微观轮廓曲线
Fig. 8 AFM profilograms of substrate surfaces before and after CMP
化学机械抛光作为一种基于化学和机械协同作用的超光滑表面加工技术,其材料去除过程的实质在于化学腐蚀作用下的机械摩擦磨损过程[1-2],表面质量(形貌、粗糙度和平整度等)和抛光速率是评价抛光效果的两个重要指标。理论分析结果表明[22-23],改善CMP效果的关键在于调控磨料微粒与加工衬底表面之间的接触状态以及微观摩擦磨损行为,优化局部真实接触微区内物理和/或化学环境。因此,磨料的力学特性(如弹性模量和硬度等)以及表面(吸附)特性都将对材料的去除过程产生影响,影响最终抛光表面质量及抛光速率。
本课题组[12]在前期工作中,利用AFM力曲线技术测定了核壳结构PS/SiO2复合微球(内核尺寸约200 nm,壳厚为10~20 nm,壳层由氧化硅纳米颗粒组成)的力-位移曲线,进一步利用Hertz接触模型计算样品的弹性模量。结果显示,复合微球的弹性模量(为2~10 GPa)随壳厚的增加而增大,明显低于纯氧化硅的弹性模量(72 GPa),且更接近于其PS内核的(2.2 GPa),表现出非刚性力学特性。由此可知,本实验所制备以介孔氧化硅为壳层的核壳结构PS/MSiO2复合磨料也将表现出类似的力学性质。
在机械作用方面,CHEN等[24]在充分考虑到磨料自身变形的基础上,以弹塑性力学、微观接触力学以及磨粒磨损机理为指导,构建了用于描述压痕深度和抛光速率的数学模型。
根据弹性接触力学,磨料粒子与抛光垫之间的弹性接触应力(Fa/p)为
(1)
式中:D为磨料的直径;
为磨料压入抛光垫表面的深度;Ea/p为磨料与抛光垫之间的等效弹性模量,可由式(2)表示:
(2)
式中:
和Ea分别为磨料的泊松比和弹性模量;
和Ep分别为抛光垫的泊松比和弹性模量。
同理,磨料粒子与抛光衬底之间的弹性接触应力Fa/w为
(3)
式中:
为磨料的自身变形量,可由式(4)表示;Ea/w为磨料与晶片之间的等效弹性模量,可由式(5)表示。
(4)
(5)
式中:
和Ew分别为晶片的泊松比和弹性模量。
根据力平衡原理,Fa/w=Fa/p,结合式(1)和(3)可进一步得到式(6):
(6)
根据磨料直径(D)、磨料的自身变形量(
)、磨料压入抛光垫的深度(
)以及磨料压入晶片的深度(
)之间的关系:
,带入后可得式(7):
(7)
根据以上分析可知,随着磨料弹性模量Ea的降低,磨料在晶片表面的压痕深度
也随之减小,这将有利于降低抛光表面粗糙度、改善加工表面质量。因此,在粒径相当以及相同的抛光试验工艺参数条件下,与常规实体SiO2磨料相比,经PS/MSiO2-1复合磨料抛光后的衬底表面具有相对较低的粗糙度。此外,由于低密度聚苯乙烯内核的存在,使得复合磨料的密度降低,在相同固含量条件下,抛光液中磨料的总数量增多。在抛光过程中,可能使得抛光垫与衬底接触界面之间的有效磨料数量增多,这也将有助于降低磨料与衬底之间的接触应力Fa/w,最终降低压痕深度
及表面粗糙度。
陈志刚等[25]曾考察Al2O3、SiO2和CeO2 3种纳米磨料对单晶硅片的抛光效果,讨论纳米磨料的硬度对抛光后表面粗糙度的影响,认为磨料硬度的降低有利于减小压痕深度,从而改善抛光表面质量。姚素薇等[26]的研究表明,多孔材料相对于常规实体材料通常表现出相对较低的硬度。由于实验所合成的复合磨料具有介孔氧化硅壳层,同样可推测其具有相对较低的表面硬度,这也将有利于降低压痕深度及抛光表面粗糙度。
氮气吸附/脱附结果显示,所得PS/MSiO2-1复合磨料的比表面积(612 m2/g)远高于常规实体SiO2磨粒的(16.7 m2/g)。由此可知,在化学作用方面,复合磨料的介孔氧化硅壳层可借助其丰富的孔结构以及高比表面增强对抛光液中有效化学组分的吸附能力,强化磨料与衬底之间真实接触区域内的化学反应活性,有利于热氧化片表面腐蚀软质层的形成与去除,这将有助于提高抛光速率。
通过上述结果与讨论可知,以介孔氧化硅为连续壳层的核壳结构有机/无机复合磨料能够在有效降低抛光表面粗糙度的基础上明显提高抛光速率,有望在实现高效无损伤抛光方面发挥积极作用。然而,该类型复合磨料的微观结构与其力学特性、化学吸附特性和抛光效果之间的关系尚不明确,其确切抛光机制与模型尚未构建,仍有待深入探索。
3 结论
1) 以AIBA为阳离子引发剂、PVP为稳定剂,采用无皂乳液聚合的方法合成单分散、表面经PVP修饰的PS微球。
2) 再以阳离子表面活性剂CTAB为模板剂,利用TEOS的溶胶-凝胶过程,在PS内核表面原位包覆含有棒状胶束模板剂氧化硅壳层。
3) 利用硝酸铵/乙醇混合溶液选择性去除CTAB模板之后,得到了以PS微球为内核(200~210 nm)、介孔氧化硅为壳层(约30 nm)的核壳结构PS/MSiO2复合磨料。
4) 复合磨料的比表面积为612 m2/g,介孔孔径在2~3 nm。
5) 经PS/MSiO2复合磨料抛光后衬底表面粗糙度RMS值为0.252 nm,抛光速率可达141 nm/min,明显优于相当粒径的常规SiO2实体磨料的(0.317 nm, 68 nm/min)。
6) 抛光效果的提高可能来自于通过利用复合磨料的特殊结构(弹性有机内核及介孔壳层),对磨料与衬底之间真实接触区域内物理和/或化学环境的优化。
REFERENCES
[1] KRISHNAN M, NALASKOWSKI J W, COOK L M. Chemical mechanical planarization: slurry chemistry, materials, and mechanisms[J]. Chemical Reviews, 2010, 110 (1): 178-204.
[2] ZHAO De-wen, LU Xin-chun. Chemical mechanical polishing: theory and experiment[J]. Friction, 2013, 1(4): 306-326.
[3] DUBOIS C, SYLVESTRE A, CHAABOUNI H, FARCY A. Impact of the CMP process on the electrical properties of ultra low k porous SiOCH[J]. Microelectronic Engineering, 2010, 87: 333-336.
[4] LOMONOSOV A M, AYOUCH A, RUELLO P, VAUDEL G, BAKLANOV M R, VERDONCK P, ZHAO L, GUSEV V E. Nanoscale noncontact subsurface investigations of mechanical and optical properties of nanoporous low-k material thin film[J]. ACS Nano, 2012, 6: 1410-1415.
[5] GATES S, RAO S P, ANANDAN V, KRISHNAN M, COHEN S, OSTROVSKI Y, KLYMKO N, CHACE M, CANAPERI D. Effects of chemical mechanical polishing on a porous SiCOH dielectric[J]. Microelectronic Engineering, 2012, 91: 82-88.
[6] ARMINI S, WHELAN C M, MAEX K, HERNANDEZ J L, MOINPOUR A M. Composite polymer-core silica-shell abrasive particles during oxide CMP[J]. Journal of the Electrochemical Society, 2007, 154(8): 667-671.
[7] ARMINI S, de MESSEMAEKER J, WHELAN C M, MOINPOUR M, MAEX K. Composite polymer core-ceria shell abrasive particles during oxide CMP: A defectivity study[J]. Journal of the Electrochemical Society, 2008, 155(9): H653-H660.
[8] CHAN Yang, LU Jin-xia, CHEN Zhi-gang. Preparation, characterization and oxide CMP performance of composite polystyrene-core ceria-shell abrasives[J]. Microelectronic Engineering, 2011, 88(2): 200-205.
[9] 陈 杨, 穆为彬, 陈志刚. 草莓状PS/SiO2复合磨料的可控合成及其抛光性能[J]. 中国有色金属学报, 2013, 23(10): 2962-2969.
CHEN Yang, MU Wei-bin, CHEN Zhi-gang. Controlled synthesis of strawberry-like PS/SiO2 composite abrasives and their polishing behavior[J]. The Chinese Journal of Nonferrous Metals, 2013, 23(10): 2962-2969.
[10] CHEN Ai-lian, MU Wei-bin, CHEN Yang. Compressive elastic moduli and polishing performance of non-rigid core/shell structured PS/SiO2 composite abrasives evaluated by AFM[J]. Applied Surface Science, 2014, 290: 433-439.
[11] ZHANG Lei, WANG Hai-bo, ZHANG Ze-fang, QIN Fei, LIU Wei-li, SONG Zhi-tang. Preparation of monodisperse polystyrene/silica core-shell nano-composite abrasive with controllable size and its chemical mechanical polishing performance on copper[J]. Applied Surface Science, 2011, 258: 1217-1224.
[12] CHEN Yang, QIAN Cheng, MIAO Nai-ming. Atomic force microscopy indentation to determine mechanical property for polystyrene-silica core-shell hybrid particles with controlled shell thickness[J]. Thin Solid Films, 2015, 579: 57-63.
[13] LEE J, JUN Y, KIM D, LEE Y, OH S. Effects of PVP on the formation of silver-polystyrene heterogeneous nanocomposite particles in novel preparation route involving polyol process: Molecular weight and concentration of PVP[J]. Materials Chemistry and Physics, 2009, 114(2/3): 549-555.
[14] SHIBUYA K, NAGAO D, ISHII H, KONNO M. Advanced soap-free emulsion polymerization for highly pure, micron-sized, monodisperse polymer particles[J]. Polymer, 2014, 55(2): 535-539.
[15] RAN Zhi-peng, SUN Yang, CHANG Bai-song, REN Qing-guang, YANG Wu-li. Silica composite nanoparticles containing fluorescent solid core and mesoporous shell with different thickness as drug carrier[J]. Journal of Colloid and Interface Science, 2013, 410: 94-101.
[16] SERTCHOOK H, AVNIR D. Submicron silica/polystyrene composite particles prepared by a one-step sol-gel process[J]. Chemistry of Materials, 2003, 15(8): 1690-1694.
[17] KUMAR K, NANDAN B, LUCHNIKOV V, SIMON F, VYALIKH A, SCHELER U, STAMM U. A novel approach for the fabrication of silica and silica/metal hybrid microtubes[J]. Chemistry of Materials, 2009, 21(18): 4282-4287.
[18] FU Wen-hua, GUAN Ye-jun, WANG Yi-meng, HE Ming-yuan. A facile synthesis of monodispersed mesoporous silica nanospheres with Pm3n structure[J]. Microporous and Mesoporous Materials, 2016, 220(15): 168-174.
[19] 丁红霞, 尹晓爽, 杨文忠, 唐永明.PVP 与表面活性剂混合模板对CaCO3结晶的调控作用[J]. 南京工业大学学报, 2011, 33(4): 68-72.
DING Hong-xia, YIN Xiao-shuang, YANG Wen-zhong, TANG Yong-ming. Crystallization of CaCO3 induced by mixed template of PVP and surfactant[J]. Journal of Nanjing University of Technology, 2011, 33(4): 68-72.
[20] 潘旭晨, 汤 静, 薛海荣, 郭 虎, 范晓莉, 朱泽涛, 何建平. 氮掺杂有序介孔碳-Ni纳米复合材料的制备及电化学性能[J]. 无机化学学报, 2015, 31(2): 282-290.
PAN Xu-chen, TANG Jing, XUE Hai-rong, GUO Hu, FAN Xiao-li, ZHU Ze-tao, HE Jian-ping. Synthesis and electrocatalytic performance of N-doped ordered mesoporous carbon-Ni nanocomposite[J]. Chinese Journal of Inorganic Chemistry, 2015, 31(2): 282-290.
[21] 杨 俊, 唐 波, 戴卫理, 李兰冬, 武光军, 关乃佳. 介孔分子筛MCM-48的氮化与表面胺化及其碱催化反应性能[J]. 中国科学: 化学, 2015, 45(4): 396-404.
YANG Jun, TANG Bo, DAI Wei-li, LI Lan-dong, WU Guang-jun, GUAN Nai-jia. Nitridation and surface amino-functionalization of mesoporous molecular sieve MCM-48 as solid base material and its basic catalytic performance[J]. Scientia Sinica: Chimica, 2015, 45(4): 396-404.
[22] ILIE F. Models of nanoparticles movement, collision, and friction in chemical mechanical polishing (CMP)[J]. Journal of Nanoparticle Research, 2012, 14: 752-761.
[23] GUO Dan, XIE Guo-xin, LUO Jian-bing. Mechanical properties of nanoparticles: Basics and applications[J]. Journal of Physics D: Applied Physics, 2014, 47: 013001.
[24] CHEN Xiao-chun, ZHAO Yong-wu, WANG Yong-guang. Modeling the effects of particle deformation in chemical mechanical polishing[J]. Applied Surface Science, 2012, 258: 8469-8474.
[25] 陈志刚, 陈 杨. 纳米磨料硬度对超光滑表面抛光粗糙度的影响研究[J]. 中国有色金属学报, 2005, 15(7): 1075-1080.
CHEN Zhi-gang, CHEN Yang. Effect of hardness of nano-sized abrasives on roughness of polished super-smooth surface[J]. The Chinese Journal of Nonferrous Metals, 2005, 15(7): 1075-1080.
[26] 姚素薇, 张 璐, 张卫国, 张振宇, 李鸿琦. 多孔氧化铝膜的纳米力学性能研究[J]. 无机材料学报, 2006, 21(3): 736-740.
YAO Su-wei, ZHANG Lu, ZHANG Wei-guo, ZHANG Zhen-yu, LI Hong-qi. Nanomechanics properties research of anodic aluminium oxide film[J]. Journal of Inorganic Materials, 2006, 21(3): 736-740.
Design and fabrication of PS/MSiO2 composite abrasives with radial mesoporous shells and their polishing behavior for oxidized silicon wafer
CHEN Ai-lian1, WANG Ya-yun2, CHEN Yang2
(1. School of Mechanical Engineering, Changzhou University, Changzhou 213164, China;
2. School of Materials Science and Engineering, Changzhou University, Changzhou 213164, China)
Abstract: The novel composite abrasives containing polyvinylpyrrolidone modified polystyrene (PS) cores and mesoporous silica (MSiO2) shells were synthesized using cetyltrimethylammonium bromide as sacrificial template, tetraethoxysilane as Si source and ammonium nitrate/alcohol mixed solution as selective solvent. The core-shell structure of PS/MSiO2 composites and the root-mean-square and polishing rate were investigated by field emission scanning electron microscopy (FESEM), transmission electron microscopy (TEM) and atomic force microscopy. The results show that the obtained PS/MSiO2 composites exhibit a well-defined core-shell structure, and the PS cores with size of 200-210 nm are coated by mesoporous silica shells with thickness of 30 nm with radial meso-channels. As confirmed by N2 adsorption-desorption measurement, the specific surface area and pore size of the composites are 612 m2/g and 2-3 nm, respectively. The oxidized silicon wafer after polishing with PS/MSiO2 composite abrasives presents a lower root-mean-square surface roughness (0.252 nm) and much higher material remvoal rate (141 nm/min) than those of conventional solid SiO2 abrasives with comparable partilce size (0.317 nm, 68 nm/min). The reduced indentation depth and surface roughness might be contributed to the low elastic modulus and surface hardness coming from polymer cores and MSiO2 shells. Meanwhile, the material removal rate is improved due to the mesoporous silica shells of the PS/MSiO2 composites, which might be help to adsorb more active chemical constituents in slurry and enhance chemical reactivity.
Key words: polystyrene; mesoporous silica; core-shell structure; composite abrasive; chemical mechanical polishing
Foundation item: Projects(51205032, 51405038, 51575058) supported by the National Natural Science Foundation of China
Received date: 2015-06-17; Accepted date: 2015-12-02
Corresponding author: CHEN Yang; Tel: +86-519-86330066; E-mail: cy.jpu@126.com
(编辑 李艳红)
基金项目:国家自然科学基金资助项目(51205032,51405038,51575058)
收稿日期:2015-06-17;修订日期:2015-12-02
通信作者:陈 杨,副教授,博士;电话:0519-86330066;E-mail: cy.jpu@126.com