Trans. Nonferrous Met. Soc. China 22(2012) s422-s427
Microstructure and properties of AZ80 alloy semisolid billets fabricated by new strain induced melt activated method
JIANG Ju-fu1,2, WANG Ying3, DU Zhi-ming1, LUO Shou-jing1
1. School of Materials Science and Engineering, Harbin Institute of Technology, Harbin 150001, China;
2. National Key Laboratory for Precision Hot Processing of Metals, Harbin Institute of Technology, Harbin 150001, China;
3. School of Mechatronics Engineering, Harbin Institute of Technology, Harbin 150001, China
Received 28 August 2012; accepted 25 October 2012
Abstract: AZ80 alloy semisolid billets were fabricated by a new strain induced melt activated method (SIMA), which involved the predeformation of as-cast AZ81 alloy via equal channel angular extrusion (ECAE) and the following semisolid isothermal treatment of ECAE-processed AZ80 alloys. The results show that highly strain-induced effect is successfully achieved by ECAE due to refined microstructure and the mechanical properties are enhanced. High-quality AZ80 semisolid billets with fine and spherical grains are fabricated by new SIMA method. The results of thixoforged experiment confirm that enhanced mechanical properties including yield strength of 216.9 MPa, ultimate tensile strength of 312.4 MPa and elongation of 26% are successfully achieved. It also confirms that new SIMA method is a very desirable method for fabricating AZ80 alloy semisolid billets.
Key words: AZ80 alloy; semisolid billets; new strain induced melt activated method; thixoforge
1 Introduction
Magnesium alloy has been widely used in automobile, motorcycle and 3C fields due to low density, high specific strength and stiffness and excellent damping capacity [1,2]. Thixoforming is a net-shape method for forming complex Mg alloy components with high properties. ZHANG et al [3] reported mechanical properties of thixomolded AZ91D magnesium alloy and found that mechanical properties of thixomolded AZ91D mainly depended on porosity level, the size and volume fraction of primary solid phase. PATEL et al [4] examined microstructure and tensile properties of thixomolded magnesium alloys and concluded that the microstructure of AZ91D and AM60B thixomolded alloys consisted mainly of globular primary α-Mg phase surrounded by network-like eutectic structure containing intermetallic β-Mg17Al12 phase. ZHAO et al [5] studied microstructural evolution and tensile mechanical properties of AM60B magnesium alloy prepared by the SIMA (strain induced melt activated) route and thought that the SIMA route (four-pass CCDF and partial remelting) produced ideal, fine semi-solid microstructure.
Three essential procedures including fabrication of semisolid billets, reheating and forming are involved in the thixoforming process [6-8]. High-quality semisolid billet has an important influence on the filling process, microstructure and properties of the thixoformed parts. Various routes had been developed for fabricating the non-dendritic or spheroidal microstructure, e.g. semisolid isothermal treatment (SSIT) [9], mechanical stirring [10], electromagnetic stirring [11], SIMA [12], two-screw stirring [13] and continuous semisolid extrusion process (CSEP) [14,15]. A novel method so-called new SIMA was firstly developed by JIANG et al [16,17], in which equal channel angular extrusion (ECAE) was used as predeformation of as-cast magnesium alloy and a semisolid isothermal treatment (SSIT) of the ECAE- processed billets was followed.
ECAE is a desirable predeformed method of magnesium alloy, by which a refined and homogeneous microstructure could be prepared [18-20]. New SIMA, i.e. combination of ECAE and SSIT, has a good potential technology to fabricate semisolid billets with fine and highly spherical grains. Research on new SIMA method has been done in AZ91D [21] and AM60 [22]. However, reports on fabricating AZ80 alloy semisolid billets by means of new SIMA are very few. Therefore, the present research is aiming to employ new SIMA to fabricate AZ80 alloy semisolid billets and investigate microstructure and mechanical properties of the AZ80 alloy semisolid billets.
2 Experimental
AZ80 magnesium alloy was used as experiment materials. It contains 8.5%Al, 0.5%Zn, 0.12%Mn, 0.003%Fe, 0.02%Cu, 0.001%Ni (mass fraction) and Mg as balance. New SIMA method was employed to fabricate the semisolid billet of AZ80 magnesium alloy. Firstly, as-cast AZ80 magnesium alloys with diameter of 57 mm and height of 120 mm were processed for 4 passes at 300 °C under route Bc by an equal channel die [22]. The route Bc refers to the rotations of 90° in the same sense between consecutive passes in the cylindrical specimens. Sixteen AZ80 alloy billets were extruded by EACE. Four tensile specimens were cut from each ECAE-processed billet along the direction of extrusion. Eight ECAE-processed billets were used as tensile and microstructural specimens. At the same time, room temperature tensile test and microstructural observation were done in the eight as-cast ingots. The mechanical properties of the tensile specimen were measured at room temperature by a universal testing machine (INSTRON 5569) at a crosshead speed of 0.5 mm/min. Microstructural samples were fabricated by the standard metallurgical technique, followed by etching in a solution of 4.2 g picronitric acid, 10 mL ethanediol, 70 mL ethanol and 10 mL distilled water. The microstructure was observed by using an Olympus G50 optical microscope. The other eight billets were used as semisolid isothermal treatment (SSIT). These eight ECAE-processed billets were isothermally treated for 10 min at various semisolid temperatures in an electrical furnace. The various semisolid temperatures involved 530, 540, 550 and 560 °C. The AZ80 magnesium alloy was prevented from oxidation or burning by argon gas. The average particle size and shape factor of the solid phases were measured using a digital image analysis system. Average particle size and shape factor (SF) of solid particles are calculated in each case [23].
In addition, the thixoforging experiments were carried out on the 2000 kN universal hydraulic presser. Ten components were achieved by thixoforging under the same process parameters. The same process parameters involved preheating temperature of 400 °C, punch speed of 30 mm/s, isothermal temperature of 540 °C and holding time of 10 min. Two tensile specimens were cut from each thixoforged component. Tensile test and microstructural observation were done.
3 Results and discussion
3.1 Comparison of microstructure and properties between as-cast and ECAE-processed AZ80 alloys
Figure 1 shows the macrographs of as-cast and ECAE-processed AZ80 alloys. As-cast AZ80 alloys were machined into cylindrical billets and then were extruded by ECAE. As shown in Fig. 1, after as-cast machined cylindrical billets were processed 4 passes by ECAE at 300 °C using route Bc, the longitudinal shape (i.e. extrusion direction) was changed due to different friction forces between billets and surface of the die’s cavity. The friction between the billets and the upper surface of the die is less than that between the billets and the lower surface of the die, leading to low flowing velocity of the upper extruded billet. As a result, the longitudinal shape is changed during the ECAE process, which has no effect on its application because it can be changed into cylindrical shape by a followed upsetting [22]. Cross-sectional shape is not changed due to constrain of the equal channel die.
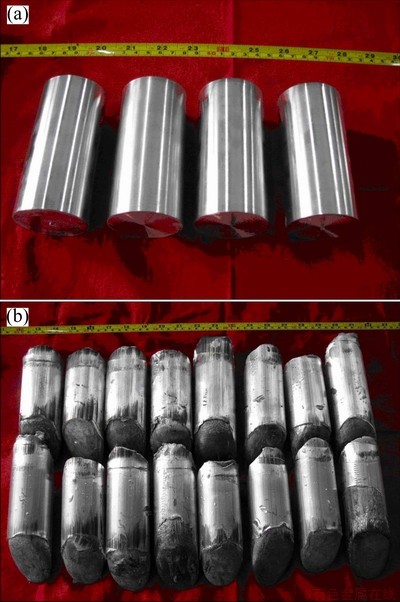
Fig. 1 Macrographs of as-cast (a) and ECAE-processed (b) AZ80 alloys
Figure 2 shows the microstructure of as-cast and ECAE-processed AZ80 alloys. As indicated in Fig. 2, the microstructure of the as-cast AZ80 alloy consists of coarse dendrites. Some dendrites’ size is more than 150 μm. In addition, the microstructure of the as-cast AZ80 alloy is not homogeneous. The difference of the grain size is easily found in the microstructure.
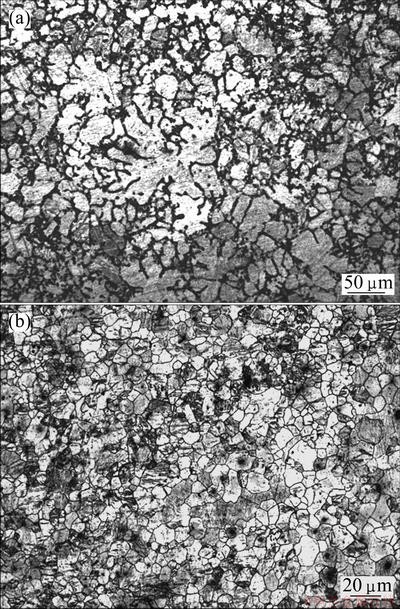
Fig. 2 Microstructure of as-cast (a) and ECAE-processed (b) AZ80 alloys
However, the microstructure of the ECAE-processed AZ80 alloy consists of fine equiaxed grains. The average grain size is about 12.5 μm. Furthermore, the microstructure is characterized by uniform distribution of equiaxed grains. Severe plastic deformation (SPD) can be successfully achieved by ECAE [18-20], which accelerates the dynamic recrystallization occurred in the ECAE-processed AZ80 alloys. The dynamic recrystallization occurred in the ECAE process leads to the refinement of the microstructure of the magnesium alloys [22,24,25]. Consequently, the refined and uniform equiaxed grains are obtained in the microstructure of the ECAE- processed AZ80 alloys.
Figure 3 shows the mechanical properties of the as-cast and ECAE –processed AZ80 alloys. As shown in Fig. 3(a), the yield strength of the as-cast AZ80 alloys ranges from 118.6 MPa to 126.3 MPa. The average yield strength is 122.1 MPa. The average ultimate tensile strength and elongation are 184.8 MPa and 8.5%, respectively. As shown in Fig. 3(b), the yield strength, ultimate tensile strength and elongation of the ECAE- processed AZ80 alloys are 217.7 MPa, 310.8 MPa and 22.9%, respectively. The yield strength of the ECAE- processed AZ80 alloys is increased by 77.8% compared with as-cast AZ80 alloy.
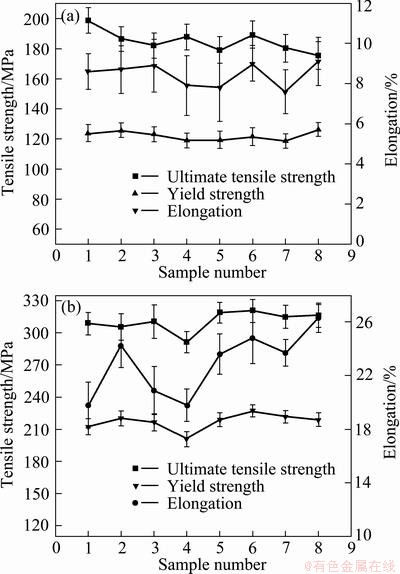
Fig. 3 Mechanical properties of as-cast (a) and ECAE-processed (b) AZ80 alloys
The ultimate tensile strength and elongation of the ECAE-processed AZ80 alloy increase by 68.2% and 169%, respectively, as compared with the as-cast AZ80 alloy. The refined and uniform microstructure of the ECAE-processed AZ80 alloy leads to the enhanced mechanical properties. The fine-grained structure is beneficial to improve the yield strength due to the Hall-Petch effect [26]. Furthermore, the refined and homogeneous microstructure is beneficial to fabricate high-quality semisolid billets in the following SSIT process.
3.2 Microstructure of semisolid billets fabricated by new SIMA
Figure 4 shows the microstructure of AZ80 alloy semisolid billets fabricated by new SIMA. As shown in Fig. 4, the microstructure is characterized by three characteristics. The first is that equiaxed grains in the microstructure are very fine. A large number of fine solid grains can be found in the microstructure. Refinement of microstructure caused by ECAE leads to the fine solid grains in the semisolid microstructure [27]. The solid grains’ size can be measured by image analysis system, as shown in Fig. 5. When the isothermal temperatures are 530, 540, 550 and 560 °C, the average grain sizes are 18.6, 22.6, 28.4 and 25.3 μm, respectively. When isothermal temperature is elevated, the average grain size firstly increases and followed by a decrease.
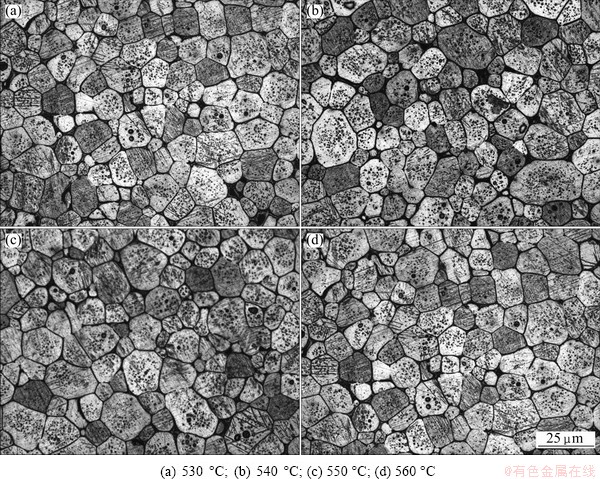
Fig. 4 Microstructure of AZ80 alloy semisolid billet fabricated by new SIMA at different temperatures
The reason for this is that two trends including coarsening and melting occur in the microstructure when the temperature is elevated [16]. The second characteristic which is high spheroidization is obtained in the semisolid microstructure. It is confirmed by the shape factor as shown in Fig. 5. The shape factor ranges from 0.89 to 0.92, which is close to 1 (sphere shape). High- spherical grains can be found in the microstructure of semisolid billets fabricated by new SIMA. The last characteristic is that the microstructure is very uniform. The size difference in the microstructure is small. The fine, spherical and uniform microstructure will contribute to the enhanced mechanical properties of the thixoforged components.
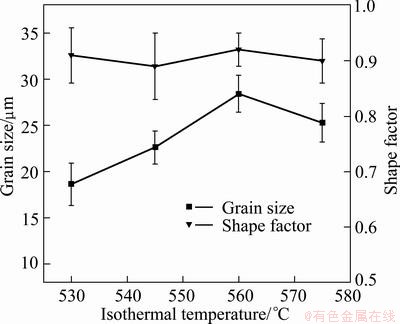
Fig. 5 Grain size and shape factor of AZ80 alloy semisolid billet fabricated by new SIMA
3.3 Mechanical properties of semisolid billets fabricated by new SIMA
Figure 6 shows the macrograph and microstructure of the thixoforged component. As shown in Fig. 6(a), good surface quality was obtained in the thixoforged components. It confirms that complex shape of component can be successfully achieved by thixoforging technology. The microstructural specimen is cut from the sampling location B. As shown in Fig. 6(b), fine and homogeneous microstructure was found in the thixoforged component. The fine and uniform microstructure is beneficial to improve the mechanical properties of the thixoforged components [17].
Figure 7 shows the mechanical properties of the thixoforged components. The tensile specimen is cut from the sampling locations A and B. The average yield strength, ultimate tensile strength and elongation are 216.9 MPa, 312.4 MPa and 26%, respectively. The fine and uniform microstructure of AZ80 alloys semisolid billets leads to enhanced mechanical properties of the thixoforged components. It confirms that new SIMA is a very desirable fabricating method for AZ80 alloy semisolid billets.
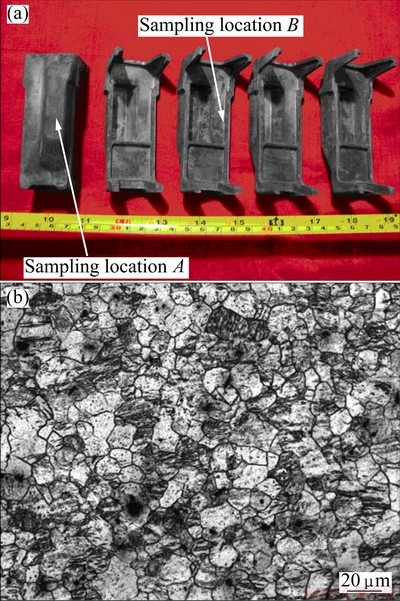
Fig. 6 Macrograph (a) and microstructure (b) of thixoforged component
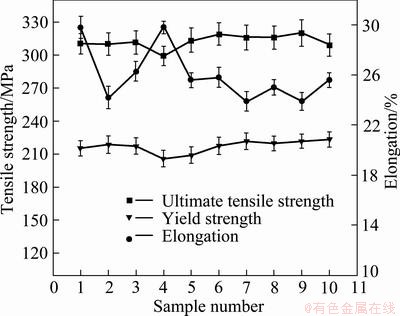
Fig. 7 Mechanical properties of thixoforged component
4 Conclusions
1) Highly strain-induced effect is successfully achieved by equal channel angular extrusion due to refined microstructure and enhanced mechanical properties. The microstructure of the ECAE-processed AZ80 alloy consists of fine equiaxed grains with average grain size of 12.5 μm. The yield strength, ultimate tensile strength and elongation of the ECAE-processed AZ80 alloys are 217.7 MPa, 310.8 MPa and 22.9%, respectively.
2) High-quality AZ80 semisolid billets can be fabricated by new SIMA. The average grain size of the high-quality semisolid billets varies in a range of from 18.6 μm to 25.3 μm. High-spherical and uniform solid grains are obtained and the microstructure of AZ80 alloys semisolid billets is prepared by new SIMA.
3) The results of thixoforged experiment confirm that enhanced mechanical properties such as yield strength of 216.9 MPa, ultimate tensile strength of 312.4 MPa and elongation of 26% are successfully achieved in the thixoforged components. It confirms that new SIMA is a very desirable method for fabricating AZ80 alloy semisolid billets.
References
[1] MORDIKE B L, EBERT T. Magnesium: Properties-applications –potential [J].Materials Science and Engineering A, 2001, 302(1): 37-45.
[2] FRIEDRICH H, SCHUMAN S. Research for a “new age of magnesium” in automotive industry [J]. Journal of Materials Processing Technology, 2001, 117(3): 276-281.
[3] ZHANG Y F, LIU Y B, CAO Z Y, ZHANG Q Q, ZHANG L. Mechanical properties of thixomolded AZ91D magnesium alloy [J]. Journal of Materials Processing Technology, 2009, 209(3): 1375-1384.
[4] PATEL H A, CHEN D L, BHOLE S D, SADAYAPPAN K. Microstructure and tensile properties of thixomolded magnesium alloys [J]. Journal of Alloys and Compounds, 2010, 496(1-2): 140-148.
[5] ZHAO Z D, CHEN Q, TANG Z J, HU C K. Microstructural evolution and tensile mechanical properties of AM60B magnesium alloy prepared by the SIMA route [J]. Journal of Alloys and Compounds, 2010, 497(1-2): 402-411.
[6] FLEMINGS M C. Behavior of metal alloys in the semisolid state [J]. Metallurgical and Materials Transactions A, 1991, 22(5): 957-981.
[7] CHAYONG S, ATKINSON H V, KAPRANOS P. Thixoforming 7075 aluminum alloys [J]. Materials Science and Engineering A, 2005, 390(1-2): 3-12.
[8] KOPP R, NEUDENBERGER D, WIMMER M, WINNING G. Thixoforging basic experiment and optimized tool design [C]// Proceeding of the Fifth International Conference on Semi-Solid Processing of Alloys and Composites. Colorado, USA: Colorado School of Mines, 1998: 336-341.
[9] YANG M B, PAN F S, CHENG R J, BAI L. Effect of semi-solid isothermal heat treatment on the microstructure of Mg–6A1–1Zn– 0.7Si alloy [J]. Journal of Materials Processing Technology, 2008, 206(1-3): 374-381.
[10] SUKUMARAN K, PAI B C, CHAKRABORTY M. The effect of isothermal mechanical stirring on an Al–Si alloy in the semisolid condition [J]. Materials Science and Engineering A, 2004, 369(1-2): 275-283.
[11] KANG C G, BAE J W, KIM B M. The grain size control of A356 aluminum alloy by horizontal electromagnetic stirring for rheology forging [J]. Journal of Materials Processing Technology, 2007, 187-188: 344-348.
[12] ZHANG L, LIU Y B, CAO Z Y, ZHANG Y F, ZHANG Q Q. Effects of isothermal process parameters on the microstructure of semisolid AZ91D alloy produced by SIMA [J]. Journal of Materials Processing Technology, 2009, 209(2): 792-797.
[13] JI S, ROBERS K, FAN Z. Isothermal coarsening of fine and spherical particles in semisolid slurry of Mg–9Al–1Zn alloy under low shear [J]. Scripta Materialia, 2006, 55(11): 971-974.
[14] GUAN R G, CHEN L Q, LI J P, WANG F X. Dynamical solidification behaviors and metal flow during continuous semisolid extrusion process of AZ31 alloy [J]. Journal of Materials Science and Technology, 2009, 25(3): 395-400.
[15] GUAN Ren-guo, ZHAO Zhan-yong, SUN Xiao-ping, HUANG Hong-qian, DAI Chun-guang, ZHANG Qiu-sheng. Fabrication of AZ31 alloy wire by continuous semisolid extrusion process [J]. Transactions of Nonferrous Metals Society of China, 2010, 20(s3): 729-733.
[16] JIANG Ju-fu, LUO Shou-jing. Reheating microstructure of refined AZ91D magnesium alloy in semi-solid state [J]. Transactions of Nonferrous Metals Society of China, 2004, 14(6): 1074-1078.
[17] JIANG J F, WANG Y, LUO S J. Application of equal channel angular extrusion to semi-solid processing of magnesium alloy [J]. Materials Characterization, 2007, 58(2): 190-196.
[18] YING T, ZHENG M Y, HU X S, WU K. Recycling of AZ91 Mg alloy through consolidation of machined chips by extrusion and ECAP [J]. Transactions of Nonferrous Metals Society of China, 2010, 20(s2): s604-s607.
[19] HU H J, ZHANG D F, YANG M B, DENG M. Grain refinement in AZ31 magnesium alloy rod fabricated by extrusion-shearing severe plastic deformation process [J]. Transactions of Nonferrous Metals Society of China, 2011, 21(2): 243-249.
[20] YING T, HUANG J P, ZHENG M Y, WU K. Influence of secondary extrusion on microstructures and mechanical properties of ZK60 Mg alloy processed by extrusion and ECAP [J]. Transactions of Nonferrous Metals Society of China, 2012, 22(8): 1896-1901.
[21] JIANG J F, WANG Y, DU Z M, QU J J, SUN Y, LUO S J. Enhancing room temperature mechanical properties of Mg-9Al-Zn alloy by multi-pass equal channel angular extrusion [J]. Journal of Materials Processing Technology, 2010, 210(5): 751-758.
[22] JIANG J F, WANG Y, QU J J, DU Z M, SUN Yi, LUO Shou-jing. Microstructure evolution of AM60 magnesium alloy semisolid slurry prepared by new SIMA [J]. Journal of Alloys and Compounds, 2010, 497(1-2): 62-67.
[23] SEO P K, KANG C G. The effect of raw material fabrication process on microstructural characteristics in reheating process for semi-solid forming [J]. Journal of Materials Processing Technology, 2005, 162-163: 402-409.
[24] HORITA Z, FUJINAMI T, LANGDON T G. The potential for scaling ECAP: Effect of sample size on grain refinement and mechanical properties [J]. Materials Science and Engineering A, 2001, 318 (1-2): 34-41.
[25] FIGUEIREDO R B, CETLIN P R, LANDON T G. The processing of difficult-to-work alloys by ECAP with an emphasis on magnesium alloys [J]. Acta Materilia, 2007, 55(14): 4769-4779.
[26] KUBOTAK K, MABUCHI M, HIGASHI K. Review processing and mechanical properties of fine-grained magnesium alloys [J]. Journal of Materials Science, 1999, 34(10): 2255-2262.
新SIMA法制备AZ80合金半固态坯料的组织与性能
姜巨福1,王 迎2,杜之明1,罗守靖1
1. 哈尔滨工业大学 材料科学与工程学院,哈尔滨 150001;
2. 哈尔滨工业大学 金属精密热加工国家级重点实验室,哈尔滨 150001;
3. 哈尔滨工业大学 机电工程学院,哈尔滨 150001
摘 要:借助新应变诱导熔化激活方法制备AZ80合金半固态坯料。在新应变诱导熔化激活方法中,首先利用等通道角挤压对铸态AZ80镁合金进行预变形,然后将预变形的AZ80镁合金进行半固态等温处理。结果表明:利用等通道角挤压能够使AZ80合金获得很好的应变诱导效果。这是由于等通道角挤压能够使AZ80合金微观组织细化,力学性能提高。新应变诱导熔化激活方法能够制备晶粒细小且球化程度高的半固态坯料。利用新应变诱导熔化激活方法制备的半固态坯料触变锻造的零件具有高的力学性能,其屈服强度达到216.9 MPa,抗拉强度达到312.4 MPa,伸长率达到26%。触变成形实验结果也证明,新应变诱导熔化激活方法是一种非常理想的AZ80半固态坯料制备方法。
关键词:AZ80镁合金;半固态坯料;新应变诱导熔化激活法;触变锻造
(Edited by HE Yun-bin)
Foundation item: Project (51075099) supported by the National Natural Science Foundation of China; Project (E201038) supported by the Natural Science Foundation of the Heilongjiang Province, China; Project (HIT.NSRIF.2013007) supported by the Fundamental Research Funds for the Central Universities, China; Project (2011RFQXG010) supported by the Harbin City Young Scientists Foundation, China; Project (LBH-T1102) supported by Specially Postdoctoral Science Foundation of Heilongjiang Province, China
Corresponding author: JIANG Ju-fu; Tel: +86-451-86415464; E-mail: jiangjufu@hit.edu.cn
DOI: 10.1016/S1003-6326(12)61741-5