
Microstructures and properties of reciprocating extruded
as-cast ZK60 magnesium alloy
JIANG Ting(姜婷) 1, 2, GUO Xue-feng(郭学锋)2, MA Guang(马光)1
1. Northwest Institute For Non-ferrous Metal Research, Xi’an 710016, China;
2. School of Materials Science and Engineering, Xi’an University of Technology, Xi’an 710048, China
Received 15 July 2007; accepted 10 September 2007
Abstract: As-cast d 50 mm ZK60 magnesium alloys were reciprocating extruded for different passes under (335±5)℃. The microstructures and properties of the alloys were studied under different reciprocating extrusion passes. The results show that, reciprocating extruded microstructures were refined and uniformed effectively, in compared with as-cast condition. For 2 passes, the grain size is about 7 μm. After 4 passes, the grain size is about 6 μm. During reciprocating extrusion, refined as-cast eutectic and reinforcement phases in dispersed particles are uniformly distributed on matrix, and their size is less than 50 nm. The tensile strength, yield strength and the elongation of 4 passes reciprocating extruded as-cast ZK60 magnesium alloy are 311 MPa, 214 MPa and 17.93%, respectively. The thermal expansion coefficient of RE-4-EX-ZK60-CT magnesium alloy is the lowest. More or less extrusion passes can not decrease the value of the thermal expansion coefficient.
Key words: reciprocating extrusion; magnesium alloys; ZK60; dynamic recrystallization
1 Introduction
Magnesium alloys have low density, high specific strength, low elastic modulus, good stiffness, strong power of shock-resistant, better shielding properties, ease to recycle and so on. Therefore, magnesium alloys are available in electron, communication and astronavigation fields[1]. ZK60, as the highest strength of transformation magnesium alloys, attracts special attention. However it exhibits low ductility under room temperature, and its elongation of extrusion sectional bar after artificial aging treatment is only 10%[2]. Poor ductility limits its application and development. How to improve plasticity of magnesium alloys in a rather large grade is a focal field. Major methods are alloying and plastic deformation[3-4]. Alloying increases reinforcement phases by adding elements such as Y, Nd, Ce, La, promotes heterogeneous nucleation and suppresses grain growing during solidification, and advances properties. Plastic deformation makes alloys occur dynamic recovery and dynamic recrystallization, improving structures, decreasing interior defects, breaking second- phase and non-metal inclusion while improving their distribution on matrix, reducing segregation, advances properties[5-6]. During casting process, non-equilibrium crystallization generates any segregation, intermetallic compound on grain boundary and tree-like network, leading to non-uniform chemical constituent and structure, decreasing hot plasticity[7]. Reciprocating extrusion (RE) is able to erase segregation, raise uniformity of constituent and structure, amend structure, increase its combination property[8]. Most researchers studied on strength and structures by conventional deformation[9-11]. We will use RE to improve properties and structures of ZK60. During the RE process, the die which was designed by ourselves is employed.
In this study, ZK60-CT was reciprocating extruded. Microstructures and properties of ZK60 alloys were investigated by different passes, and elongation was emphasized.
2 Experimental
The material used in the study was ZK60 magnesium alloy, and the chemical composition was Mg- (5.0%-6.0%)Zn-(0.3%-0.9%)Zr. As-cast d 50 mm ZK60 magnesium alloy ingots were made by casting firstly, while molting was protected by RJ-2 flux. Then the as cast ingots were machined to remove oxide skin and were reciprocating extruded on an YJ32-315 adjustable varying-speed four-column hydraulic press. The reciprocating extrusion passes were counted with the material passing through the die which has a 14 mm diameter. The processing parameters of the reciprocating extrusion are as follows: extrusion ratio of 12.75, maximal extrusion pressure of 512 MPa, extrusion temperature of 335 ℃, extrusion passes of 2, 4 and 8. The principle diagram of the reciprocating extrusion is shown in Fig.1. After reciprocating extrusion, the magnesium alloy was direct extruded to d12 mm bars for analysis.
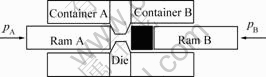
Fig. 1 Principle diagram of RE
For the convenience of description, use ZK60-CT to express as-cast ZK60 magnesium alloy, RE-n-EX- ZK60-CT express reciprocating extruded as-cast ZK60 magnesium alloy. Here, RE represents reciprocating extrusion, n represents reciprocating extrusion pass, EX represents forward extrusion, and CT represents as-cast.
Metallographic specimens were sampled from extruded bars, ground with waterproof abrasive paper, polished with a Al2O3 water solution, and etched in a solution with 4% nitric acid in alcohol. Microstructures were analyzed by OLMPUS BX51-TRF metallographic microscope. Differential thermal analysis (DTA) was used to determine the transforming temperatures of the phases. A sample having a mass of about 5 mg was placed in a CRY-2P calorimeter with an Al2O3 standard and then heated in an argon atmosphere at a heating rate of 10 ℃/min between 300 ℃ and 700 ℃. Thermo-mechanical analyzer (TMA) was used to determine thermal expansion coefficients. The samples were machined to d 4 mm×6 mm by an EDS machine with axis of sample along the extrusion direction. A sample was placed in a RJY-1P with an argon atmosphere at a heating rate of 10 ℃/min between 50 ℃ and 400 ℃. Hardness was measured at a load of 50 N and hold time of 30 s. Tensile test samples were machined along the direction of extrusion with a diameter of d 6 mm and gauge length of 30 mm. Tensile test was conducted on a WDW-200 electronic universal- testing machine with a 1 mm/min tensile rate.
3 Results and discussion
3.1 Microstructure
Microstructure of ZK60-CT is shown in Fig.2. It consists of α-Mg matrix, (α-Mg+MgZn) eutectic along grain boundary and MgZn compound.
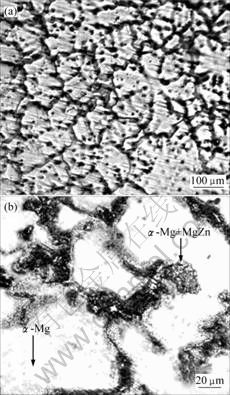
Fig.2 Microstructures of ZK60-CT magnesium alloy
Microstructures of RE-n-EX-ZK60-CT magnesium alloy are given in Fig.3. RE-2-EX-ZK60-CT with equiaxed grains has an average grain size of 7 μm, as shown in Fig.3(a), (b) and (c). After 4 passes, the grain size of RE-4-EX-ZK60-CT was about 6 μm. Refined and dispersed particle phases with an average size of 50 nm exist within grain and at grain boundary, as shown in Fig.3(d). 8 or more passes have no significant grain refinement effect.
DTA curve of ZK60 magnesium alloy is shown in Fig.4. There are two sharp endothermic peaks at 343.1 ℃ and 648.6 ℃ respectively and a weaker endothermic peak at 550.7 ℃ for ZK60-CT magnesium alloy. According to Mg-Zn binary phase diagram, peak 343.1 ℃ is Mg-Zn eutectic temperature, peak 648.6 ℃ is the melting point. Based on Mg-Zn and Mg-Zr phase diagram, there is no Mg-Zn phase transformation around 550.7 ℃, and Mg-Zr doesn’t form compounds. Therefore the endothermic peak at 550.7 ℃ is probably from a phase transformation peak of some non- equilibrium solidified products.
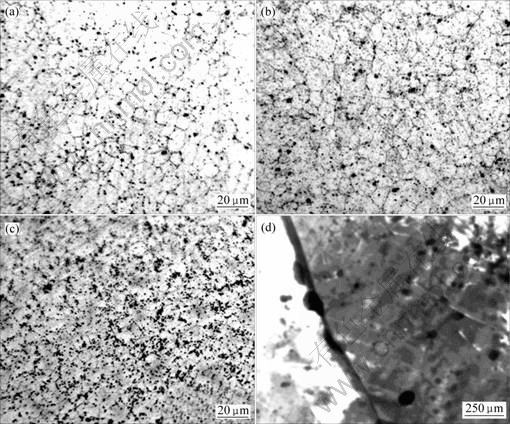
Fig.3 Microstructures of RE-n-EX-ZK60-CT magnesium: (a) RE-2-EX-ZK60-CT; (b)RE-4-EX-ZK60-CT; (c) RE-8-EX-ZK60-CT; (d) RE-n-EX-ZK60-CT (TEM)

Fig.4 DTA curves of ZK60 magnesium alloys: (a) ZK60-CT; (b) RE-n-EX-ZK60-CT
From Fig.4(b), DTA curves of RE-2-EX-ZK60-CT, RE-4-EX-ZK60-CT and RE-8-EX-ZK60-CT magnesium alloys are uniformly diffused and soluted, and matrix α-Mg and eutectic (α-Mg+MgZn) were broken. Dynamic recrystallization occurred. MgZn phase was redistributed within α-Mg equiaxed grains and at grain boundary in isolated dispersed particles, as shown in Fig.3. Therefore, 343.1 ℃ (α-Mg+MgZn) eutectic peak of ZK60-CT vanished after reciprocating extrusion.
3.2 Mechanical property
Fig.5 shows the mechanical properties of RE-n-EX-ZK60-CT magnesium alloy. The mechanical properties of RE-2-EX-ZK60-CT magnesium alloy are the lowest. With 4 passes the mechanical properties become uniform. There are no distinct mechanical properties differences between RE-4-EX-ZK60-CT and RE-8-EX-ZK60-CT. RE-4-EX-ZK60-CT magnesium alloy has σb and σ0.2 of 301 MPa and 214.2 MPa, respectively.
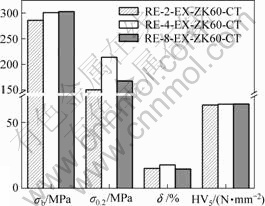
Fig.5 Mechanical properties of RE-n-EX-ZK60-CT magnesium alloys
According to Hall-Patch principle, the finer the grain, the higher the tensile strength and ductility are. During reciprocating extrusion, softening resulted form dynamic recovery and dynamic recrystallization. The softening counteracts the work hardening during hot extrusion. Therefore, solid solution strengthening, grain refinement strengthening and precipitation strengthening contribute to the strength increasing.
3.3 Thermal expansion property
Fig.6 shows thermal expansion property of ZK60 magnesium alloy. The thermal expansion coefficient of RE-4-EX-ZK60-CT magnesium alloy is the lowest. More or less extrusion passes can not decrease the value of the thermal expansion coefficient.
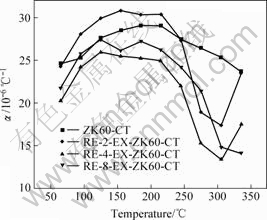
Fig.6 TMA curves of ZK60 magnesium alloys
4 Conclusions
1) Reciprocating extrusion could refine structures of ZK60 magnesium alloys, make structures uniform and the reinforced phase disperse in matrix.
2) RE-4-EX-ZK60-CT magnesium alloy has ultimate tensile strength of 301 MPa, yield tensile strength of 214.2 MPa and elongation of 17.93%.
3) Reciprocating extrusion can effectively accelerate welding of cast defects, decrease thermal expansion coefficients, and improve the stability of dimensions.
References
[1] YU Kun, LI Wen-xian, WANG Ri-chu, MA Zheng-qing. Research, development and application of wrought magnesium alloys[J]. The Chinese Journal of Nonferrous Metals, 2003, 13(2): 277-288.
[2] MA Chun-jiang, LIU Man-ping, WU Guo-hua, DING Wen-jiang, ZHU Yan-ping. Tensile properties of extruded ZK60-RE alloys[J]. Mater Sci Eng A, 2003, A(349): 207-212.
[3] CHEN Zhen-hua, XIA Wei-jun, CHEN Yong-qi, FU Ding-fa. Texture and anisotropy in magnesium alloys[J]. The Chinese Journal of Nonferrous Metals, 2005, 15(1): 1-11.
[4] WANG Bin, YI Dan-qing, ZHOU Ling-ling, FANG Xi-ya, LUO Wen-hai, YANG Jie. Influence of Y and Nd on microstructure and properties of Mg2Zn2Zr alloys[J]. Heat Treatment of Metals, 2005, 30(7): 9-13.
[5] HORITA Z, MATSUBARA K, MAKII K, LANGDON T G. A two-step processing route for achieving a superplastic forming capability in dilute magnesium alloys[J]. Scripta Materialia, 2002(47): 255-260.
[6] WATANABE H, MUKAI T, ISHIKAWA K, HIGASHI K. Low temperature superplasticity of a fine-grained ZK60 magnesium alloy processed by equal-channel-angular extrusion[J]. Scripta Materialia, 2002(46): 851-856.
[7] PENG Jian, ZHANG Ding-fei, YANG Chun-mei, DING Pei-dao. Homogenizing research on ZK60 magnesium alloy ingot[J]. Material Engineering, 2004, 8: 32-35.
[8] LEE S W, WANG H Y, CHEN Y L, YEH J W, YANG C F. An Mg-Al-Zn alloy with very high specific strength and superior high strain rate superplasticity processed by reciprocating extrusion[J]. Advanced Engineering Materials, 2004, 6(12): 948-952.
[9] EISENMEIER G, HOLZWARTH B, HO¨PPEL H W, MUGHRABI H. Cyclic deformation and fatigue behaviour of the magnesium alloy AZ91[J]. Mater Sci Eng A, 2001, A319-321: 578-582.
[10] MA?THIS K, TROJANOVA? Z, LUKA?C P. Hardening and softening in deformed magnesium alloys[J].Mater Sci Eng A, 2002, A324: 141–144.
[11] STYCZYNSKI A, HARTIG CH, BOHLEN J, LETZIG D. Cold rolling textures in AZ31 wrought magnesium alloy[J]. Scripta Materialia, 2004(50): 943-947.
Foundation item: Project (50271054) supported by the National Natural Science Foundation of China; Project (2002E110) supported by the Natural Scientific Research program of Shaanxi Province China; Projected supported by the Scientific Research Foundation for the Returned Overseas Chinese Scholars, State Education Ministry of China
Corresponding author: JIANG Ting; Tel: +86-29-86224473; E-mail: jiangtingyf1106@163.com
(Edited by CHEN Ai-hua)