
Microstructure and mechanical properties of Al-Cu-Mg-Ag alloyed with Ce
LI Yun-tao(李云涛), LIU Zhi-yi(刘志义), ZHOU Jie(周杰), XIA Qing-kun(夏卿坤)
School of Materials Science and Engineering, Central South University, Changsha 410083, China
Received 15 July 2007; accepted 10 September 2007
Abstract: The aged characteristics and microstructure of two Al-Cu-Mg-Ag alloys with and without Ce addition are investigated by TEM and mechanical properties test. The results show that trace Ce addition inhibits precipitating process and delays peak aging time. 0.25% Ce additions decrease both tensile strength and ductility. TEM observation shows that the morphology of Ω precipitate can be modified by the small addition of Ce. The trace Ce affects the microstructure by reducing the volume fraction of Ω precipitate. It can be concluded that the intensive interaction between Ce and Cu decreases the Cu atom concentration in alloy matrix and reduces the precipitated kinetics for Ω phase.
Key words: aluminum alloy; aging behavior; microstructure; Ce addition; precipitating kinetics
1 Introduction
As we know, microalloying or trace element added to aluminum alloys can purify the melt and inhibit the deleterious effects of impurity. It also influences the precipitation phenomena strongly and improves the tensile strength[1-3]. These additions alter the precipitation sequence and precipitates morphology[4-5]. The alloying effect depended on the microalloying elements.
Over the past several years, there was an increasing interest in investigating the effects of trace additions with rare earth to aluminum alloys such as Ce , Er[6-7].
Several studies have been concerned with the addition of Er, which forms a thermo-stable L12-type (Cu3Au) Al3Er phase and demonstrates to be coherent and/or semi-coherent with the aluminum matrix. It improved tensile strength significantly. ZHAO et al[8] studied the Al-Zn-Mg-Cu alloy with Er addition. They discovered Er in the alloy mainly formed Al3Er phase and enhanced the mechanical properties. YANG et al[9] and XIAO et al[10] have studied the high pure aluminum and the Al-Mg alloy with addition of Er and found Al3Ce phase present. Whilst, the study carried out by YANG et al discovered the addition of Er in Al-4Cu alloy mainly formed a Al8Cu4Er phase which decreased the ultimate tensile strength and yield strength. Obviously, the alloying behavior was affected by the matrix element in the alloy.
As rare earth, Ce formed Al8CeCu4 intermetallic in Al-Cu class alloy according Al-Ce-Cu ternary phase diagram. However, the study carried out by XIAO et al[6] showed that addition of Ce in Al-Cu-Mg-Ag alloy increased the ultimate tensile strength and yield strength simultaneously. The result was noticeable and discussible.
In this work, we studied the effect of trace addition of Ce on the microstructure and mechanical properties of Al-Cu-Mg-Ag-Mn-Zr alloys, tried to discuss the alloying behavior and the contributing mechanism of Ce in this class alloy.
2 Experimental
The experimental alloys were prepared by melting in electric resistance furnace and iron mold casting. Their normal composition (mass fraction, %) is provided in Table 1. The ingots were homogenized at 510 ℃ for 12 h and hot-rolled into sheets of 1 mm in thickness. After hot rolling, specimens were solution treated at 515 ℃ for 6 h and quenched into cold water, then immediately aged at 165 ℃.
Tensile specimens were machined from sheets in the longitudinal directions, and from the tensile test specimens that aged at 165 ℃ for different time. The tensile test was carried out at room temperature and performed on CSS 44100. Each value represented the mean number of measurements on two specimens. Microstructures of the alloy were observed by using Nephoto-2 optical microscope (OM). Samples for transmission electron microscope (TEM) observation were prepared by mechanical grinding to around 10 ?m, 3 mm in diameter disks were punched out from the sheet, then electropolished using 33% nitric and 67% methanol solution with liquid nitrogen cooling at around -30 ℃ . TEM were performed on Tecnai G220 operated at 200 kV. Scanning electron microscope (SEM) were performed on Philips Sirion200 which assembled with GENESIS 60S energy-dispersive X-ray (EDAX) microanalysis.
Table 1 Normal composition of experiment alloys (mass fraction, %)
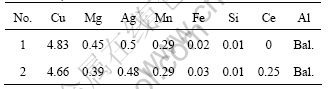
3 Results and discussion
3.1 Mechanical properties
Fig.1 shows mechanical properties of experimental alloys aged at 165 ℃. The tensile strength of both alloys was coincident with the conventional age-strengthening behavior along with aging time increasing. The aging curves present under-aging, peak-aging and over-aging stages. The trend of the ultimate tensile strength(UTS) curve was similar to that of yield strength(YS). Alloy 1 without Ce addition presented higher UTS and YS than alloy 2 with Ce addition. As Al-Cu-Ce ternary phase diagram showed, Ce added to Al-Cu class alloys formed Al8CeCu4 intermetallic and decreased Cu concentration in aluminum matrix.
At the period of under ageing, the strength of alloy 1 increased rapidly and the increment extent is obviously bigger than that of alloy 2. This indicated the precipitation kinetics of alloy 1 is higher than that of alloy 2. The peak-aging of alloy 1 occurred at 4 h and alloy 2 at 8 h. It could be concluded that Ce addition retarded the precipitation of solute.
The elongation of alloy 1 decreased gradually with the aged time increasing. Compared with alloy 2, the elongation at peak ageing of alloy 1 is higher. This showed Ce addition decreased the elongation of Al-Cu-Mg-Ag alloy.
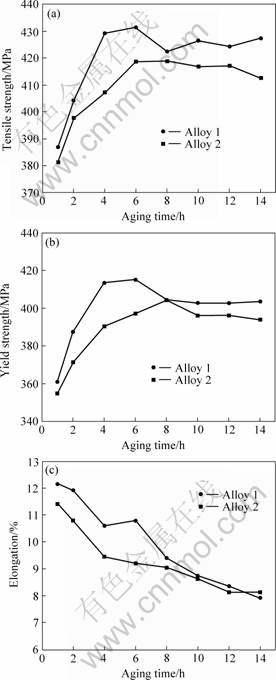
Fig.1 Mechanical properties of alloys aged at 165 ℃
3.2 Fracture microstructure
After hot rolling, fragile Al8Cu4Ce particles were fragmentated along the grain boundary. Usually, it is considered that the undissolved particles was the crack source and decreased the ductility of aluminum alloy. Fig.2 shows the fractographs of alloy 2 which demonstrates a combined consequence of transgranular and intergranular fracture. EDS analyses showed that these particles in dimples are Al8Cu4Ce. It can be concluded that addition of Ce formed Al8Cu4Ce phase and decreased the plasticity. This was coincided with the lower elongation of alloy 2 than alloy 1 without addition of Ce.
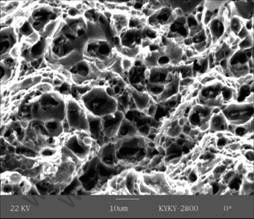
Fig.2 Fractograph for solid solution state of alloy 2
3.3 Casting structure
Fig.3 shows the morphologies of experimental alloys in the as-cast states. The typical grain structure of alloy 1 was shown in Fig.3(a). It consisted of large equiaxed grains with a dendritic substructure. The grain size of the casting was about 1mm. Coarsened dendritic substructure dominated the casting structure.
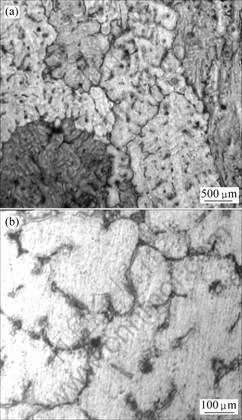
Fig.3 Optical micrographs of alloys in as-cast states: (a) Alloy 1; (b) Alloy 2
For addition of 0.25% Ce, as shown in Fig.3(b), there was slight change in the grain structure in the alloy 2. The grain was refined and grain size was about 250 μm. Coarsened dendritic substructure disappeared partly. Distance between branches of dendritic substructure reduced apparently compared with the alloy 1. Obviously, 0.25%Ce additions refined grain size and grain structure.
3.4 Microstructure
Al-Cu-Mg-Ag alloy was a typical age-hardenable alloy and believed to be promising candidates for future use in high-speed aircraft[11]. As extensively studied before[12-13], it was expected that the precipitates involve massive Ω phase on {111}α plane and a few θ′ phase on {001}α plane in the experimental alloy with a high Cu-to-Mg ratio.
Fig.4 shows the bright field (BF) TEM images of alloy 1 without Ce additions and the electron beam was close to the <011>α zone axis of α(Al) matrix. Fig.4(a) presents the morphology and density of precipitates in alloy 1 aged for 2 h. It is clear that Ω phase precipitated sufficiently in alloy 1 and no θ′ phase was observed. Ω precipitates were fine and uniform.

Fig.4 Precipitates morphologies of alloy 1 aged for different times (Electron beam is close to <011>α: (a) 2 h; (b) 4 h)
After being aged for 8 h, plate-shaped Ω precipitates together with θ′ dominated the microstructure of alloy 1, as shown in Fig.4(b). The densities of the strengthening phases, including Ω and θ′ phases, increased with aging time and the length of the plate-like Ω phase was approximately between 60 and 80 nm.
Fig.5 shows the bright field (BF) TEM images of alloy 2 aged for 8 h and the electron beam was close to the <011>α zone axis of α(Al) matrix. A few precipitates can be observed and precipitate size was about 50 nm. The TEM micrograph showed that the volume fraction of Ω precipitate was obviously lower than that of alloy 1.
The precipitation of Ω phase also included the nucleation and coarsening. The number of nucleation site and coarsening force affected the distribution and the size of Ω precipitate. The metastable precipitate formed on {111}α planes of matrix in Al-Cu-Mg-Ag alloy was found by AULD and POLMEAR in the early 1970s[14-15] and designated Ω phase subsequently. The mechanism of nucleation and coarsening were a matter of speculation. MURAYAMA et al[16-17] investigated the nucleation of Ω phase based on the 3DAP (
three dimensional atom probe) analysis and concluded that Ω phase evolved continuously from co-clusters containing Ag and Mg aligned on {111}α planes of the matrix. In despite of remained controversial about the precursor of Ω precipitates, it is unanimous that the formation of Ag and Mg atoms co-clusters were a critical element of Ω nucleation[18-19].
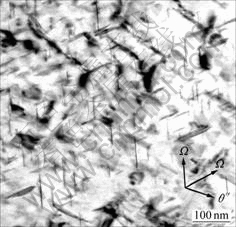
Fig. 5 Precipitates morphology of alloy 2 aged at 165 ℃ for 8 h
The results from TEM observation indicate that trace addition of Ce retard the precipitation of Ω phase. It was concluded that Ce restrained the formation of Ag and Mg atoms co-clusters. As we know, the diffusion of solute in solid solution was realized by vacancy-solute exchanging mechanism and the diffusion rate of solute depended on the movability of vacancy in matrix. As the higher binding of rare earth elements with vacancy than that of other solutes, it was difficult to form the Ag and Mg atoms co-clusters.
As discussed above, addition of Ce in alloy decreased the number of Ag and Mg co-clusters. Simultaneity, Al8Cu4Ce phase formation consumed a part of Cu atom in the solid solution and reduced the solubility of Cu solute. As a result, the volume fraction of Ω precipitate in alloy 2 was lower than that in alloy 1.
4 Conclusions
1) 0.25% Ce addition in Al-Cu-Mg-Ag alloys decreases the mechanical properties.
2) 0.25% Ce addition retards Ω phase precipitation and delays peak-aging time.
3) Al8Cu4Ce phase consumes Cu solubility of aluminum matrix and decreases precipitated kinetics.
References
[1] LI Yun-Tao, LIU Zhi-Yi, XIA Qing-Kun, YU Ri-Cheng, LIU Yan-Bin. Effect of trace addition of Er on microstructure and ageing behavior of Al-Cu-Mg-Ag-Zr alloy[J]. Transactions of Materials and Heat Treatment, 2007, 28(2): 49-53. (in Chinese)
[2] DEL CASTILLO L, LAVERNIA E J. Microstructure and mechanical behavior of spray-deposited Al-Cu-Mg(-Ag-Mn) alloys[J]. Metallurgical and Materials Transactions A: Physical Metallurgy and Materials Science, 2000, 31(9): 2287-2298.
[3] YIN Zhi-Min, JIANG Feng, PAN Qing-Lin, GUO Fei-Yue, ZHU Da-Peng, SONG Lian-Peng, ZENG Yu, TAO Wang. Microstructure and mechanical properties of Al-Mg and Al-Zn-Mg based alloys containing minor scandium and zirconium[J]. Trans Nonferrous Met Soc China, 2003, 13(3): 515-520.
[4] TATSUO S, SHOICHI H, KIYOSHIGE H, TAKAHARU M. Roles of microalloying elements on the cluster formation in the initial stage of phase decomposition of Al-based alloys[J]. Metallurgical and Materials Transactions A: Physical Metallurgy and Materials Science, 2003, 34(12): 2745-2755.
[5] NIE J F, AARONSON H I, MUDDLE B C. The role of microalloying elements in the formation of precipitate plates in aluminium alloys[C]//Kyoto, Japan: Japan Inst Metals, 1999.
[6] XIAO D H, WANG J N, DING D Y. Effect of minor cerium additions on microstructure and mechanical properties of cast Al-Cu-Mg-Ag alloy[J]. Materials Science and Technology, 2004, 20(10): 1237-1240.
[7] NIE Zuo-ren, JIN Tou-nan, ZOU Jing-xia, FU Jing-bo, YANG Jun-jun, ZUO Tie-yong. Development on research of advanced rare-earth aluminum alloy[J]. Trans Nonferrous Met Soc China, 2003, 13(3): 509-514.
[8] ZHAO Zhong-kui, ZHOU Tie-tao, LIU Pei-ying, CHEN Chang-qi. Observation of formed Er phase in Al-Zn-Mg-Cu-Li alloys by TEM[J]. Rare Metal Materials and Engineering, 2004, 33(10): 1108-1111. (in Chinese)
[9] YANG Jun-jun, XU Guo-fu, NIE Zuo-ren, YIN Zhi-min. Effects of trace Er on structures and properties of high strength Al-Zn-Mg alloy[J]. Special Casting and Nonferrous Alloys, 2006, 26(7): 393-396. (in Chinese)
[10] XIAO D H, WANG J N, DING D Y, YANG H L. Effect of rare earth Ce addition on the microstructure and mechanical properties of an Al-Cu-Mg-Ag alloy[J]. Journal of Alloys and Compounds, 2003, 352: 84-88.
[11] POLMEAR I J, PONS G, OCTOR H, SANCHEZ C, MORTON A, BORBIDGE W, ROGERS S. After concorde: Evaluation of an Al-Cu-Mg-Ag alloy for use in the proposed European SST[J]. Materials Science Forum, 1996, 217-222(pt 3): 1759-1764.
[12] AULD J H. Structure of metastable precipitate in some Al-Cu-Mg-Ag alloys[J]. Materials Science and Technology, 1986, 2(8): 784-787.
[13] GABLE B M, SHIFLET G J, STARKE E A Jr. Alloy development for the enhanced stability of Ω precipitates in Al-Cu-Mg-Ag alloys[J]. Metallurgical and Materials Transactions A: Physical Metallurgy and Materials Science, 2006, 37A(4): 1091-1105.
[14] AULD J H. Structure of a metastable precipitate in an Al-Cu-Mg-Ag alloy[J]. Acta Crystallographica, Section A (Crystal Physics, Diffraction, Theoretical and General Crystallography), 1972, A28: S98.
[15] TAYLOR J A, PARKER B A, POLMEAR I J. Precipitation in Al-Cu-Mg-Ag casting alloy[J]. Metal Science, 1978, 12(10): 478-482.
[16] MURAYAMA M, HONO K. Three dimensional atom probe analysis of pre-precipitate clustering in an Al-Cu-Mg-Ag alloy[J]. Scripta Materialia, 1998, 38(8): 1315-1319.
[17] REICH L, MURAYAMA M, HONO K. Evolution of Ω phase in an Al-Cu-Mg-Ag alloy: A three-dimensional atom probe study[J]. Acta Materialia, 1998, 46(17): 6053-6062.
[18] MOORE K T, HOWE J M, VEBLEN D R. High-resolution and energy-filtered TEM imaging of Ag segregation to planar precipitate-matrix interfaces in an Al-Cu-Mg-Ag alloy[J]. Philosophical Magazine B: Physics of Condensed Matter; Statistical Mechanics, Electronic, Optical and Magnetic Properties, 2002, 82(1): 13-33.
[19] TAKAHASHI T, HISAYUKI K, YAMAME T, MINAMINO Y, HINO T. Interdiffusion in α solid solution of the Al-Cu-Mg-Ag system[J]. Materials Transactions, 2003, 44(11): 2252-2257.
Foundation item: Projects (2005CB623705-04) supported by the National Basic Research Program of China
Corresponding author: LIU Zhi-yi; Tel: +86-731-8836011; E-mail: liuzhiyi@mail.csu.edu.cn
(Edited by CHEN Ai-hua)