Article ID: 1003-6326(2005)03-0691-06
Preparation and characterization of La0.8Cu0.2MnO(3±δ) perovskite-type catalyst for methane combustion
HE Fang(何 方), WANG Hua(王 华), DAI Yong-nian(戴永年)
(Faculty of Materials and Metallurgical Engineering,
Kunming University of Science and Technology, Kunming 650093, China)
Abstract: La0.8Cu0.2MnO(3±δ) perovskite-type catalyst for methane combustion prepared through sol-gel process was characterized by X-ray Diffractometry(XRD), X-ray Photoelectron Spectroscopy(XPS) and Scanning Electron Microscopy(SEM). XPS analyses reveal that the surface characteristics of the catalyst are changed. The lattice defects and oxygen vacancies on the catalyst surface are enhanced due to a part of La3+ being substituted by Cu2+. Temperature-programmed-desorption(TPD) and temperature-programmed-reduction(TPR) analyses were carried out to study the catalytic behavior. It is found that there are two O2-desorption peaks at 350℃ and 650℃ in the TPD pattern, and two CH4-consumption peaks at 420℃ and 750℃ in the TPR patterns respectively, which indicates that the two kinds of oxygen species, so-called α and β oxygen, can react with the methane during catalytic combustion process. The catalytic activity tests were performed in a fixed-bed reactor, and the results show that the T1/2 at which the conversion of methane attains 50% of La0.8Cu0.2MnO(3±δ) is lower by 55℃ than that of LaMnO3. This indicates that the catalytic activity of La0.8Cu0.2MnO(3±δ) is increased with partial substitution of Cu2+ for La3+.
Key words: perovskite-type catalyst; methane catalytic combustion; sol-gel; TPD-TPR-MS characterization CLC
number: O643 Document code: A
1 INTRODUCTION
Catalytic combustion is an environmentally-friendly process without pollutant emissions. Typically, NOx emission can be reduced dramatically, since the combustion temperature is maintained below 1673K[1, 2]. Thus, the catalytic combustion technology has been considered one of the promising technologies for reducing hazardous exhaust gases emissions[3]. Catalytic combustion of methane has gained wide attention in recent years in order to limit environment pollution. Perovskites are mixed oxides of general formula ABO(3±δ), where A is usually a lanthanide ion and B is a transition metal ion. Both A and B can be partially substituted, leading to a wide variety of compositions of general formula A1-xA′xB1-yB′yO(3±δ), characterized by structural and electronic defects owing to their non-stoichiometry[4, 5]. The metal ion B is considered to be responsible for the catalytic activity in the complete oxidation reactions, while the ion A, especially when being partially substituted with ion A′ of different valences, determines the formation of crystal lattice vacancies and can stabilize unusual oxidation states for B, leading to different catalytic performance[6]. Perovskite-like samples of formula La1-xCuxMnO(3±δ) have been reported to be catalytically active for the complete oxidation of CO, HC and NH3[7]. Also, it is believed that mixed oxides of the perovskite structure are promising methane combustion catalysts substituting noble metal catalysts[8, 9]. In the present work, La0.8Cu0.2MnO(3±δ) (designated as LCMO below) perovskite-like catalyst for methane catalytic combustion was prepared through sol-gel process, and characterized by XRD, XPS and SEM. Furthermore, the catalytic properties of LCMO for methane combustion were investigated by means of TPD and TPR techniques.
2 EXPERIMENTAL
2.1 Catalyst preparation
The active phase, LCMO, was prepared through the so-called sol-gel method by dissolving La(NO3)3·6H2O, Cu(NO3)2 and Mn(NO3)2 in the desired ratios, in distilled water, and adding the nitrates solutions into a mixed solution of EDTA and ethylene glycol. If it was necessary, some ammonia was added in the solution in order to control the pH value. The solvent was evaporated at 70℃ until a very viscous gel was formed, then the gel was dried at 120℃ in an oven. The dried gel was heated at 300℃ for 6h and calcined at 850℃ for 20h in air.
2.2 Catalyst characterization
XRD analysis of the catalyst was carried out by using a Rigaku-3105 X-ray diffractometer with CuKα radiation. The scanning rate was 8(°)/min with scanning scope from 4° to 80°. XPS measurements were conducted using a Perkin Elmer PHI-550 multifunctional electron spectrometer with MgKα radiation. The C1s peak at 285.00eV due to adventitious carbon was used as an internal reference. Morphology and particle size were determined by means of a Philip XL30 Scanning Electron Microscope(SEM).
2.3 TPD-TPR-MS analysis
The temperature programmed desorption(TPD) of the catalyst was carried out on a Quantachrome Instruments. The experiments were performed in flowing He from room temperature to 1273K with a heating rate of 15K/min and a flow rate of 20cm3/min. The composition of the outlet gas was monitored by means of a quadrupolar mass spectrometer. The temperature programmed reduction(TPR) of the catalyst was tested in the same apparatus. 5.0%CH4(volume fraction) in He was fed to the reactor. Other experimental conditions were the same as those of TPD tests.
[BJ(,,,][BJ)] Vol.15 №.3 Preparation and characterization of La0.8Cu0.2MnO(3±δ) perovskite-type catalyst 2.4 Catalytic activity tests
The catalytic oxidation of methane was carried out in a fixed-bed quartz tubular reactor at atmospheric pressure. Briefly, a quartz tubular reactor with 600mm in length and 18mm in inside diameter, was put into a tubular furnace. 100mg of the catalyst was placed in the middle part of the reactor between two flocks of quartz wool. The void part of the reactor tube was filled with quartz beads. The temperature of the catalyst bed was monitored by a thermocouple placed in the centre of the catalyst bed. The temperature of the reactor was maintained by an electronic controller. Prior to catalytic tests, the catalyst was activated in flowing air, such as increasing temperature by 10℃/min up to 600℃, then keeping for 1h. The activity tests were performed by feeding a mixture composed of 1%CH4, 5%O2, and 94%N2(volume fraction), and increasing temperature by 5℃/min form 200 to 900℃. The product analysis was conducted using an on-line gas chromatograph provided with a TC detector, using Helium as carrier gas. The conversion was calculated by using the concentration of methane and confirmed by the yields of CO2 and CO. In order to examine the effect of the partial substitution of Cu2+ in A site on the catalytic activity, the catalytic activity of Cu2+ substituted catalyst was compared with that of the non-substituted one.
3 RESULTS AND DISCUSSION
3.1 XRD analysis
The XRD pattern of LCMO is shown in Fig.1. The XRD analysis shows the presence of a perfectly pure crystalline perovskitic phase of LCMO. It is worth to point out that, in some cases, the XRD diffraction patterns obtained for LCMO show a couple of additional weak peaks, probably because of the tendency of Cu or Mn to remain stable in different oxidation states. However, high phase purity of perovskite-type catalyst is achieved for LCMO in most cases.
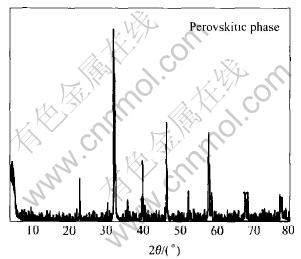
Fig.1 XRD pattern of La0.8Cu0.2MnO(3±δ) catalyst
3.2 XPS characterization
The XPS spectrum of La3d5/2 of LCMO is shown in Fig.2(a). It can be seen that the spectrum is composed of two peaks of La3d5/2 binding energy in the catalyst, being at 837.58 and 833.72eV respectively. Moreover, a satellite peak around each main peak usually can be found during measuring process, which is assigned to the shakeup in the La3d electrons. It is believed that the shakeup satellite results from the transition of a 3d electron to an empty 4f orbital[10]. The spectrum also indicates that lanthanum ion is the trivalent ion in LCMO. Fig.2(b) shows the Mn2p XPS spectrum. The binding energy of Mn2p is at 653.35 and 642.13eV. From the results, it seems to be difficult to discern the valence state of manganese ions in LCMO. It is widely believed that the manganese ions co-exist as tri- and quadrivalent in LCMO at the same time, and the amount of Mn4+ increases with Cu2+ partially substituting B site ions. A typical measure of the skewness is the asymme- try index β used by X-ray spectroscopy. The asym-
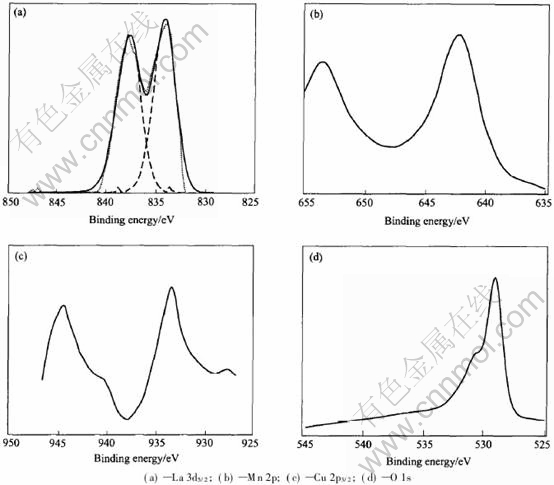
Fig.2 XPS spectra of La0.8Cu0.2MnO(3±δ) catalyst
metry index β=a/b has been defined by Kowalczyk et al[11], in which a is the half-width at half-maximum on the high binding energy side and b is the half-width at half-maximum on the low binding energy side. The value of β increases with the increase of x(the molar fraction of Cu) in LCMO, and the Mn4+ molar fraction rises with the value of x going up. When x is 0.2 in LCMO, β is measured to be over 1.0, and the shift of peak position shows the change of valence state from Mn3+ to Mn4+. Fig.2(c) shows the spectrum for Cu2p3/2 in the LCMO. There is a weak satellite peak accompanying the main high binding energy peak, which is believed to be the result of the shakeup of Cu2p in Cu2+ because the main peak of Cu+ does not have satellite peaks[12]. So, the copper ions in LCMO are mainly composed of Cu2+. Since partial substitution of La3+ by Cu2+, according to the condition of electroneutrality condition, the excess negative charge introduced by Cu2+-doping to LCMO is probably compensated either by formation of holes or creation of oxygen vacancies. The oxygen vacancy concentration increases with increasing Cu-doping content. This is beneficial to enhancing the oxygen ionic conductivity, and subsequently improving the catalytic performance of the catalyst. The O1s XPS spectrum is shown in Fig.2(d). It can be seen that the spectrum consists of two peaks, which indicates that there are two types of oxygen in LCMO. One type of oxygen with lower binding energy(528.80eV) is believed as the lattice oxygen. The other type of oxygen with higher binding energy(531.15eV) corresponds to the absorbed oxygen.
3.3 SEM analysis
SEM micrograph of the LCMO catalysts is presented in Fig.3. The particle size is about 10μm. It is noted that the catalyst particles have irregular shape with large porous structure, which, to some extent, increases the surface area of the catalyst.
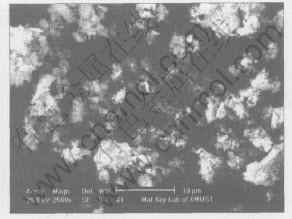
Fig.3 SEM micrograph of La0.8Cu0.2MnO(3±δ) catalyst
3.4 O2-TPD and CH4-TPR results
Temperature-programmed desorption(TPD) of oxygen is a powerful technique for the evaluation of catalyst affinity towards oxygen. During the TPD analysis of pre-adsorbed oxygen, two desorption peaks, called α and β, can be observed, which are relative to the release of oxygen, adsorbed on the surface or migrating from the bulk, respectively[13]. It is well-known that, when a perovskite is heated in inert atmosphere at high temperature, usually around 800℃, oxygen vacancies can form. By cooling in air, these vacancies are filled with adsorbed oxygen and the charge compensation is provided by partial oxidation of the metal B ion. As mentioned above, a TPD analysis of a perovskite-type materials reveals two possible desorption peaks, called α and β, widely reported in Refs.[14, 15]. The α peak, usually observed at lower temperature, represents the desorption of oxygen adsorbed on the catalyst surface and it is not always observable, depending on the concentration of filled oxygen vacancies on the catalyst surface. In particular, its onset temperature and intensity depend partially on the nature of metal B, but mainly on the substitution degree of the A ion with a cation of different valence. The β peak corresponds to the lattice oxygen desorption process. It, characterized by higher onset temperature, strictly depends on the nature of the B ion, and is correlated to its partial reduction to a lower oxidation state. The onset temperature of the β peak is usually very near that of thermal decomposition of the pure B metal oxide. For instance, the onset temperature of the LCMO β peak is near the decomposition temperature of pure Mn2O3.
Fig.4 illustrates the Oxygen TPD-MS pattern for LCMO catalyst. As shown in Fig.4, there are two peaks in the TPD spectrum of the catalyst which correspond to the above mentioned α and β peaks respectively. LCMO shows an intense α peak around 350℃, while the onset temperature of the β peak is approximately 650℃, and the maximum of the β desorption peak reaches at around 750℃. The appearance of an intense α peak indicates a high concentration oxygen vacancies and defects on the surface of the catalyst. Thus, it may be concluded that La0.8Cu0.2MnO(3±δ) possesses a high concentration of oxygen vacancies and defects. In comparison, according to the Ref.[13], LaMnO(3±δ) does not show any α desorption peak. This means that it is possible to introduce different defective sites through partially substituting La ion by Cu. Indeed, the partial substitution of Cu for La leads to a change of the intensity and the onset temperature of α peak. The β peak is assigned to the release of the lattice oxygen in the catalyst. The existence of the β peak and its onset temperature can be adopted as a qualitative index to describe the reducibility and oxygen mobility of the catalyst. This peak has been attributed to Mn4+ reduction to Mn3+ or lower valence state during the oxygen desorption process, where Mn4+ is formed by the substitution of Cu2+ for La3+. So, Cu-doping can increase the amount of Mn4+ in the catalyst, in consequence increasing the area of β peak. As a result, the performance of the catalyst is enhanced to some extent.
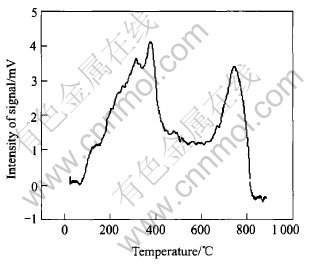
Fig.4 Oxygen TPD-MS pattern of La0.8Cu0.2MnO(3±δ) catalyst
The temperature programmed reduction of the catalyst was performed with 5% CH4 in He from room temperature to 1000℃ with a heating rate of 15℃/min and a flow rate of 20cm3/min. Fig.5 shows the CH4-TPR pattern of La0.8Cu0.2MnO(3±δ) catalyst. Two reduction peaks positioned at approximately 420 and 750℃, respectively, are observed for the catalyst. As mentioned above, there are two kinds of oxygen species on the surface of the catalyst, so called α- and β-oxygen respectively. According to the O2-TPD analysis, α-oxygen is desorbed at relatively lower temperature. So in the TPR pattern, the reduction peak at lower temperature is attributed to the α-oxygen. By contrast, the reduction peak at about 750℃ may be assigned to the reduction of B site ion to lower valences. In this case, the later peak assigned to the reduction of Mn4+ to Mn3+ or Mn2+. With partially Cu-doping in the A site, there are Cu2+ ions in the lattice of the catalyst, which may be interacted with the Mn ions and reacted with CH4 during the temperature programmed reduction process[16]. Compared with the TPR profiles of La-Mn-O mixed oxide without Cu-doping, the reduction peaks of LCMO appear at lower temperature. It is probable that Cu-doping in the catalyst can decrease the reaction activation energy between catalyst and CH4 and enhance oxidation activity.
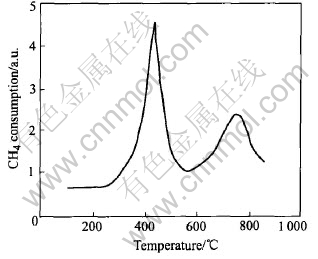
Fig.5 CH4-TPR pattern of La0.8Cu0.2MnO(3±δ) catalyst
3.5 Catalytic activity
The combustion of methane was studied on the La0.8Cu0.2MnO(3±δ) and LaMnO3 catalyst series over a wide temperature range from 473K to 1173K. Activity data expressed as CH4 conversion ratio are given in Fig.6 as a function of temperature. Since the CH4 conversion data depicted in Fig.6 are obtained with the same catalyst mass and specific area varying in a narrow range, it appears more appropriate to reveal the catalyst performance in terms of intrinsic activity. We can see that con-
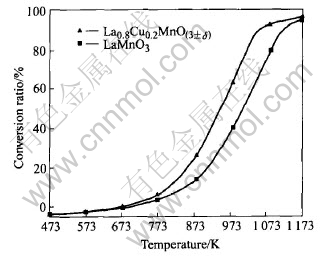
Fig.6 Methane conversion ratio vs temperature of two kinds of catalyst
version starts at 573K for La0.8Cu0.2MnO(3±δ) and LaMnO3. La0.8Cu0.2MnO(3±δ) shows a higher catalytic activity than LaMnO3. La0.8Cu0.2MnO(3±δ) and LaMnO3 show the value of T1/2 at about 948K and 1003K respectively(T1/2, being the temperature at which the conversion of methane attains 50%, is an important parameter characterizing the activity of catalysts[17]). The temperatures of CH4 full conversion of these two kinds of catalysts are very close. But in general, the Cu2+ partially substituted perovskite is more active than LaMnO3.
4 CONCLUSIONS
The LCMO catalyst prepared by sol-gel method is proved to be thermally stable material of high surface area and highly perovskitic crystalline, hence, of high catalytic activity. The XPS analysis results show that with the substitution of Cu for La in the catalyst, Mn4+ and the oxygen vacancy concentration increase significantly, meanwhile the catalytic activity for methane combustion increases. The catalytic activity tests confirm these results. There are two kinds of oxygen species, α and β oxygen, on LCMO surface, corresponding to adsorption oxygen with high electron binding energy and lattice oxygen with low electron binding energy. The oxygen species and redox performance of the LCMO oxide were investigated by means of TPD and TPR techniques. There are two peaks both in O2-TPD and CH4-TPR patterns, which means that the two kinds of oxygen species can be involved into the methane combustion reaction. It is possible that in redox mode the lattice oxygen from the LCMO catalyst instead of molecular O2 reacts with methane to the partial or complete oxidation production. The results of catalytic activity tests show that La0.8Cu0.2MnO(3±δ) exhibits a better catalytic activity for methane combustion than LaMnO3.
REFERENCES
[1]Cho S J, Song K S, Ryu I S, et al. Characteristics of methane combustion over La-Cr-O catalysts [J]. Catalysis Letters, 1999, 58: 63-66.
[2]XU Xiu-feng, PAN Yan-fei, LIU Yan-xia, et al. Catalytic combustion of methane over MnOx/ZrO2-Al2O3 catalysts [J]. Journal of Natural Gas Chemistry, 2003, 12(4): 228-232.
[3]Terribile D, Trovarelli A, de Leitenburg C, et al. Catalytic combustion of hydrocarbons with Mn and Cu-doped ceria±zirconia solid solutions [J]. Catalysis Today, 1999. 47: 133-140.
[4]MA Wen-hui, XIE Gang, CHEN Shu-rong, et al. Solid-state synthesis of Sr- and Co-doped LaMnO3 [J]. Trans Nonferrous Met Soc China, 2001, 11(6): 904-907.
[5]Leanza R, Rossetti I, Fabbrini L, et al. Perovskite catalysits for the catalytic flameless combustion of methane preparation by flame-hydrolysis and characterization by TPD-TPR-MS and EPR [J]. Applied Catalysis (B): Environmental, 2000, 28: 55-64.
[6]Rossetti I, Forni L. Catalytic flameless combustion of methane over perovskites prepared by flame-hydrolysis [J]. Applied Catalysis(B): Environmental, 2001, 33: 345-352.
[7]Dai H X, He B H, Li W, et al. Perovskite-type oxide ACo0.8Bi0.2O2.87(A=La0.8Ba0.2): a catalyst for low-temperature CO oxidation [J]. Catalysis Letters, 2001, 73(2-4): 149-156.
[8]Spinicci R A, Tofanari A A, Faticanti M, et al. Hexane total oxidation on LaMO3(M=Mn, Co, Fe) perovskite-type oxides [J]. Journal of Molecular Catalysis A: Chemical, 2001, 176: 247-252.
[9]Saracco G, Geobaldo F, Baldi G. Methane combustion on Mg-doped LaMnO3 perovskite catalysts [J]. Applied Catalysis (B): Environmental, 1999, 20: 277-288.
[10]DING Tie-zhu, LI Jian, QI Qi-ge, et al. XPS studies on rare earth oxide LSCO/YSZ electrodes [J]. Journal of Rare Earths, 2003, 21(4): 453-457.(in Chinese)
[11]Kowalczyk S P, Ley L, Mcfeely F R, et al. Multiple splitting of the manganese 2p and 3d levels in MnF2 single crystals [J]. Physics Reviews(B), 1975, 11: 1721.
[12]LAN Cui-ling, MENG Yan-qiang, ZHAO Lin-yuan, et al. Surface characterization of La-Cu-Mn perovskite-type mixed oxides [J]. Guangxi Sciences, 2002, 9(4): 284-288.(in Chinese)
[13]Rossetti I, Forni L. Catalytic flameless combustion of methane over perovskites prepared by flame-hydrolysis [J]. Applied Catalysis(B): Environmental, 2001, 33: 345-352.
[14]Leanza R, Rossetti I, Fabbrini L, et al. Perovskite catalysts for the catalytic flameless combustion of methane preparation by flame-hydrolysis and characterization by TPD-TPR-MS and EPR [J]. Applied Catalysis (B): Environmental, 2000, 28: 55-64.
[15]PAN Zhi-yong, ZHANG Chang-bin, YU Chang-chun, et al. Study on catalytic combustion of methane over the supported La-Mn perovskite catalysts [J]. Journal of Molecular Catalysis, 2003, 17(4): 274-278.(in Chinese)
[16]LIANG Zhen-cheng, QIN Yong-ning, LIAO Qiao-li, et al. Properties of perovskite-type La1-xCuxMnO3 catalysts [J]. Chinese Journal of Applied Chemistry, 1997, 14(1): 11-15.
[17]Fabbrini L, Rossetti I, Forni L. Effect of primer on honeycomb-supported La0.9Ce0.1CoO(3±δ) perovskite for methane catalytic flameless combustion [J]. Applied Catalysis (B): Environmental, 2003, 44: 107-116.
(Edited by YANG Bing)
Foundation item: Project(50164002) supported by the National Natural Science Foundation of China; Project(2004E0058Q) supported by the Natural Science Foundation of Yunnan Province, China; Project supported by Baoshan Iron & Steel(Group) Co. Ltd, China
Received date: 2004-11-5; Accepted date: 2005-03-21
Correspondence: HE Fang, PhD candidate; Tel: +86-871-5153405; E-mail: hefangmj@hotmail.com