Trans. Nonferrous Met. Soc. China 20(2010) s744-s748

Microstructure of semi-solid ADC12 aluminum alloy adopting new SIMA method
WANG Zhen-yu(王振宇), JI Ze-sheng(吉泽升), SUN Li-xin(孙丽鑫), XU Hong-yu(许红雨)
School of Materials Science and Engineering, Harbin University of Science and Technology, Harbin 150040, China
Received 13 May 2010; accepted 25 June 2010
Abstract: A semi-solid microstructure of ADC12 aluminum alloy containing spherical solid particles was studied. A new strain-induced melt activation (SIMA) process was proposed. In the treatment, chips were cut from ADC12 ingot by lathe machining and the plastic deformation was produced through cutting. The chips were put into a metal mold and compressed into a billet at 473 K. The microstructures of chip and billet were studied. The effect of the isothermal treatment on the semi-solid microstructure evolution of ADC12 aluminum alloy prepared by the new method was analyzed. A series of heating treatments were carried out from 823 to 838 K. The effects of heating temperature on microstructures were studied. The experimental results show the ADC12 aluminum alloy prepared by the new method can reap homogeneous and spherical grains at 828 K. The average grain size is about 82 μm. Also, the grain microstructure obtained by the present process is better than the traditional one. These results prove that the ADC12 aluminum alloy can be applied to semi-solid processing with the new SIMA method.
Key words: ADC12 aluminum alloy; semi-solid; microstructure; strain-induced melt activation
1 Introduction
The semi-solid forming of metals was discovered near 40 years ago by SPENCER et al[1]. The thixocasting and rheocasting were proposed by FLEMINGS et al[2-3]. They are typical cases to process material in the semi-solid state. The strain-induced melt activation (SIMA) is a simple method that does not need expensive equipment for preparing semi-solid billets. SUERY and FLEMINGS[4] used this method to study the behavior of semi-solid Sn-Pb alloy and found a high degree of segregation of the liquid phase at lower rates of deformation. In the SIMA method, the cast materials that are deformed enough are recrystallized to produce fine grained microstructure. After being reheated in the semi-solid range, the grains are well globularized. This processing was developed by KIRKWOOD[5].
SONG and HONG[6] studied the multi-forging technique in SIMA for 6061 aluminum alloy and found that the multi-forging was effective for grain refinement and grain size uniformity. HEIDARY et al[7] compared the effect of unidirectional compression and rolling on final microstructure of A356 aluminum alloy in SIMA. It was found that the ultimate size of spherical dendrites in the rolled billets was smaller than that of compressed ones under the same condition. GU et al[8] used the preparation of ZW61 semi-solid billets through equal channel angular extrusion as strain induced step in SIMA and gained better semi-solid microstructure.
The ADC12 is a die-casting aluminum alloy of the Japanese trademarks and it is close to the eutectic point in the Al-Si binary state diagram. The two-phase region of liquid-solid is narrow. Although many papers have been published in the general area of semi-solid technique for aluminum, little work on ADC12 semi-solid alloy was carried out. ZHUANG and WANG[9] adopted mechanical stirring to produce ADC12 semi-solid aluminum alloy. KIUCHI and SUGIYAMA[10] used shearing-cooling-rolling(SCR) method to produce ADCl2 semi-solid aluminum alloy. But the metallographs did not show the semi-solid spherical particle. WANNASIN and THANABUMRUNGKUL[11] used the gas induced semi-solid (GISS) method to produce ADCl2 semi-solid aluminum alloy. According to the metallograph, it was found the GISS method is not suitable for ADC12. So far, there are not enough convincing evidences that the ADC12 alloy can be produced by semi-solid processing. From literature survey, it appears that none of previous investigations is concerned with the semi-solid ADC12 alloy produced by SIMA method.
However, traditional SIMA method used deformation technique, which easily caused crack and the uneven degree of deformation in billet. To avoid this problem, a new SIMA method for getting uniform and severe plastic deformation was adopted. The objective of the present work is to study the microstructure evolution and component distribution of ADC12 alloy using the new SIMA method.
2 Experimental
The chips were cut from an ingot of commercially available ADC12 aluminum alloy by lathe machining. The chemical composition of commercial ADC12 ingot is listed in Table 1. The chips were in curved shape of about 2.0 mm in width and 0.5 mm in thickness, which were used as the raw material for the experiment. Fig.1 shows the appearance of machined chips. Firstly, the machined chips were filled into a metallic cylindrical mold of 40 mm in diameter and the mass of backfilling chips was 40 g. Secondly, the mold with the chips was heated up to 473 K and held for 20 min. Finally, the mold and chips were quickly removed from the furnace. The chips were compressed by unilateral pressing in the mold. The pressure and holding time were 400 MPa and 10 s, respectively. The shape of compacted billet was 40 mm in diameter and 15 mm in height. The melting temperature of ADC12 alloy started at about 815 K and completed at 858 K by DSC.
Table 1 Chemical composition of ADC12 aluminum alloy (mass fraction, %)

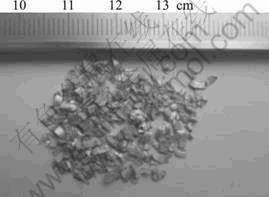
Fig.1 Appearance of machined ADC12 chips
Following the pretreatment, the billets were heated at the predetermined temperature and held for 30 min. Heating rate was 15 K/min. The billets were removed from the furnace and rapidly quenched in water. The holding temperature was controlled to
0.5 K by PID, and the thermocouple embedded at the top center of the billet was used to ensure temperature control. Each test was repeated several times in the same active state to ensure reproducibility. After being etched with 0.5% hydrofluoric acid solution, the section along the vertical axis of billets was observed by OLYMPUS optical microscope (OM).
3 Results and discussion
3.1 Microstructure of chip
DA-SILVA et al[12] found that a (Al) phase is the first to solidify in the Al-Si hypoeutectic alloys. Therefore, in the semi-solid state, the solid particles are essentially a (Al). Eutectic silicon exists in the ADC12 ingot and takes on flakes and acicular grains, as shown in Fig.2(a). Fig.2(b) shows the microstructure of chip. The fine particles of eutectic silicon disperse in the groundmass and align themselves in the cutting direction. The plastic deformation produces a high strain rate in chips. Because of plastic deformation the large eutectic silicon is broken into fine particles that spread along the cutting direction. The chips are compacted to billet after heat treatment at 473 K for 20 min. The middle section of billet’s microstructure is shown in Fig.2(d). The fine particles of eutectic silicon distribute more uniformly in chips. In contrast, no significant differences in size and orientation of eutectic silicon are observed from Figs.2(d) and (c). The silicon phase undergoes a morphological transition from coarse flakes to fine particles, with an obvious directivity after cutting. The large strain induced energy is produced in grain by cutting.
The substructure in plastic deformation can be considered that the critical shear stress leads to new dislocation of a few atoms near the dislocation source through slip plane. In the crystal various barriers retard the movement of dislocations such as second-phase particle, grain boundary, and subboundary. They result in the dislocations interacting on each other and beget the crunodes of dislocation which are not easy to remove. The dislocations lead to the increment of deformation in constant motion. These dislocations in front of barriers will be impeded and subsequently pile up each other, resulting in pile-up of dislocation. The strain energy is stored in metal by the defects which result in unstable thermodynamic state of the metal. It is the immanent reason that the plastic deformation metal is changed by heating.
3.2 Effect of heating temperature on microstructure
Fig.3 shows the microstructures of billets at different temperatures after holding for 30 min. It is seen that, for billets heated at 818 K, Fig.3(a), the a (Al) phase takes on rosette-like shape and the grains merge with one another. Fig.3(b) shows that the a (Al) phase uniformly grow up through the atomic diffusion and the grains take in the spherical shape at 828 K. After heating at 833 K, Fig.3(c), the shape of a (Al) phase becomes smooth and spherical, and the number of spherical grains markedly decreases in matrix. For billets heated at 838 K, the a (Al) phase is molten. The typical dendrites are shown in Fig.3(d).
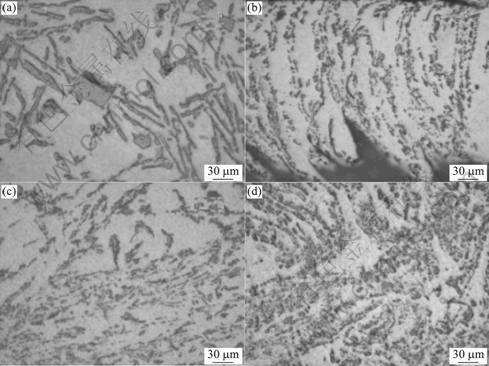
Fig.2 Typical optical micrographs: (a) Cast piece; (b) Chips; (c) Compact chips under 400 MPa at room temperature (middle section); (d) Compact chips under 400 MPa after heat-treatment at 473 K for 20 min (middle section)
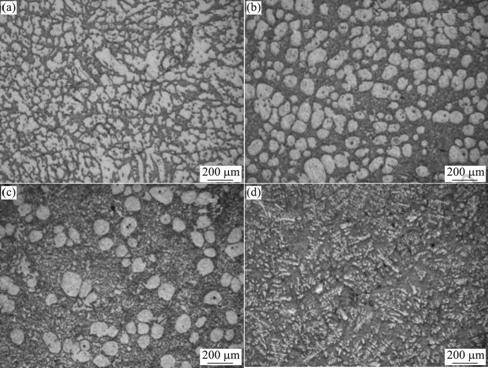
Fig.3 Effect of heating temperature on microstructures (middle section): (a) 823 K; (b) 828 K; (c) 833 K; (d) 838 K
The cold deformations by mechanical work act on the chips, which results in the large strain induced energy and the increase of the number of defects such as dislocation and vacancy. The low-melting metal phases gather around the grain boundary. The low-melting metal phases begin to melt and the interface energy starts to decrease when achieving the melting temperature. The fine grains enter into the larger-size ones and decline the interfacial area. It can be seen that with the increase of temperature, the a (Al) phase gradually changes from rosette-like to spherical, and granular shape and the morphology becomes better by the atomic diffusion. The microstructure of liquid phase increases gradually. In this way, the spherical grains become more and more obvious. With increasing temperature, the growth of a (Al) phase occurs and local areas start to melt.
3.3 Effect of area of billet on microstructure
Only the billets heated at 828 K for 30 min were analyzed, as shown in Figs.4 and 5. The micrographs in Fig.5 show the microstructures at different positions through the diameter. Three positions of billet have the similar roundness and number of grains. The mean diameters of Figs.5(a), (b) and (c) are 83, 80 and 84 mm, respectively. So, the mean diameter of the three positions are close. The degree of cold plastic deformation of chip goes well with others by lathe machining. There is not obvious impact on the cold plastic deformation of chips during the compressing in contrast with Figs.2(b) and (d). As a result, the degree of cold plastic deformation is similar in the billet. The strain energy of grain and degree of grain fragmentation are equal. The billet is even heated under heat conduction. So, each location of billet causes spheroidizing at the same time when the temperature arrives to semi-solid transition range.
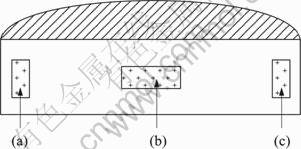
Fig. 4 Schematic drawing of sampling location (vertical section through diameter)
4 Conclusions
1) During cuts ingot, not only the size of eutectic silicon is changed, but also much strain energy is stored in the microstructure, which together offer a driving force for the spheroidizing.
2) The semi-solid billet prepared by the new SIMA method is of even grain distribution. The large size and uniform spheroidizing semi-solid billets can be produced, which has an important significance for industrial production.
3) When increasing the heating temperature, the a (Al) phase changes from rosette-like to spherical and granular shape, and the morphology becomes well. The a (Al) phase occurs and local areas start to melt with a rise in temperature. The ADC12 aluminum alloy prepared by the new method can reap homogeneous and spherical grains at 828 K and the average grain size is about 82 μm.
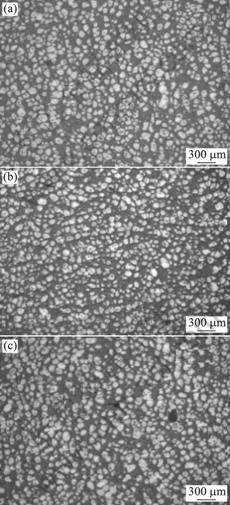
Fig.5 Microstructures of sampling location (vertical section through diameter) at 828 K for 30 min
References
[1] SPENCER D B, MEHRABIAN R, FLEMINGS M C. Rheological behavior of Sn-15 pct Pb in the crystallization range [J]. Metallurgical and Materials Transactions B, 1972, 3(7): 1925-1932.
[2] FLEMINGS M C. Behavior of metal alloys in the semisolid state [J]. Metallurgical and Materials Transactions A, 1991, 22(5): 957- 981.
[3] FLEMINGS M C, RIEK R G, YOUNG K P. Rheocasting [J]. Materials Science and Engineering A, 1976, 25: 103-117.
[4] SUERY M, FLEMINGS M C. Effect of strain rate on deformation behavior of semi-solid dendritic alloys [J]. Metallurgical and Materials Transactions A, 1982, 13(10): 1809-1819.
[5] KIRKWOOD D H. Semisolid metal processing [J]. International Materials Reviews, 1994, 39(5): 173-189.
[6] SONG Y B, HONG C P. Grain refinement of 6061 Al alloy by the modified strain-induced melt-Activated (SIMA) process for semi-solid processing [J]. Solid State Phenomena, 2007, 119: 311-314.
[7] HEIDARY M H, BIGDELI M, MAHDAVI A, KHOMAMIZADEH F. Comparison of microstructural changes in a SIMA processed A356 aluminum alloy after unidirectional compression and rolling: Effect of pressure depth [C]// Procceding of the 10th International Conference on Semi-Solid Processing of Alloys and Composites. Aachen, 2008: 391-396.
[8] GU Zhong-wei, HAN Ya-fang, PAN Fu-sheng, WANG Xi-tao, DUAN Wen, ZHOU Shao-xiong. Preparation of semi-solid billet of ZW61 alloy by equal channel angular extrusion [J]. Materials Science Forum, 2009, 610/613: 806-809.
[9] ZHUANG Wei-wei, WANG Xiao-rong. Formation of ADC12 semi-solid aluminum alloy by mechanical stirring [J]. Acta Agriculturae Universitatis Jiangxiensis, 2006, 28(3): 481-482. (in Chinese)
[10] KIUCH M, SUGIYAMA S. Characterization of semi-solid alloys made by SCR-process [C]// Proccedings of the 4th International Conference on Semi-Solid Processing of Alloys and Composites. England, 1996: 197-201.
[11] WANNASIN J, THANABUMRUNGKUL S. Development of a semi-solid metal processing technique for aluminium casting applications [J]. Songklanakarin Journal of Science and Technology, 2008, 30(2): 215-220.
[12] DA-SILVA M, LEMIEUX A, CHEN X G Characterization of semi-solid slurry using a novel [J]. Journal of Materials Processing Technology, 2009, 209: 5892-5901.
(Edited by CHEN Wei-ping)
Foundation item: Project(GB09A202) supported by the Key Project of Science and Technology of Heilongjiang Province, China
Corresponding author: JI Ze-sheng; Tel: +86-13804517924; E-mail: qinghejin@yahoo.com.cn