
Preparation of highly dispersed antimony-doped tin oxide nanopowders by azeotropic drying with isoamyl acetate
YANG Fen (杨 芬)1, 2, ZHANG Xue-jun(张学俊)3, WU Xu(吴 旭)1,
TIAN Fang(田 芳)1, GAN Fu-xing(甘复兴)1, 4
1. Department of Environmental Engineering, School of Resources and Environmental Science, Wuhan University, Wuhan 430079, China;
2. Department of Chemistry, Qujing Normal University, Qujing 655011,China;
3. Guizhou Province Key Laboratory of Ferment Engineering and Biological Pharmacy, Guizhou University,
Guiyang 550003, China;
4. State Key Laboratory of Metal Corrosion and Protection, Institute of Metals Research,
Chinese Academy of Sciences, Shenyang 110016, China
Received 19 September 2006; accepted 19 March 2007
Abstract: Antimony-doped tin hydroxide colloid precipitates were prepared by hydrolysis of SnCl4?5H2O and SbCl3 ethanol solutions. Isoamyl acetate was selected as azeotropic drying solvent and was compared with the most commonly used n-butanol solvent on treating precipitate for low hard agglomeration precursor powders. The FT-IR, BET, XRD, and TEM results of the precursor powders and calcinated antimony-doped tin oxide powders were recorded. The results demonstrate that isoamyl acetate is an excellent azeotropic drying solvent that can effectively prevent the agglomeration of particles and greatly improve the fluffiness of the obtained dried powders. After these precursor powders are calcined, antimony-doped tin oxide nanopowders with tetragonal rutile structure and high dispersivity can be obtained.
Key words: antimony-doped tin oxide; nanopowder; dispersivity; azeotropic drying; isoamyl acetate
1 Introduction
Nanocrystalline antimony-doped tin oxide(ATO) is of good optical property, chemical and mechanical stabilities, high conductivity[1]. Most of these special characterizations benefit from the uniform doping of antimony and the nanometer dimension of antimony-doped tin oxide crystals. Solution chemistry method is a significant process to synthesize precursors of many nano scale metal oxides. But during the processes of deposition, drying, calcinations and agglomeration take place to some degree, and the specific surface area decreases, thus leading to negative effect on the performance and application of powders[2]. More and more researchers have been aware of the importance of the drying methods and the disadvantages of the absorbed water to the dispersivity of powder[3]. Therefore, many drying methods, such as supercritical drying[4-5], freeze drying[6-7], microwave drying [8] and azeotropic distillation[9-10], were developed to remove the water adsorbed on the surface of colloid particles in order to prevent or reduce aggregation caused by shrinkage of water films between precipitated particles. The water film is formed by the surface adsorbed water when colloid particles make contact at the drying stage. Supercritical drying, freeze drying and microwave drying methods reduce hard agglomerates by eliminating or diminishing the surface tension of the water films between colloids. Azeotropic distillation, however, removes surface adsorbed water when colloids disperse in azeotropic mixture solution, which radically prevents the formation of water films between colloids and the aggregation of particles. It has been reported that when azeotropic drying is adopted in the coprecipitation method, hard agglomeration can be prevented and nano ultrafine powders with uniform dispersion can be obtained[11-12].
In this paper, a synthetic method with a non- aqueous ion-exchange hydrolysis for removal of chlorine ions was adopted, and an antimony-doped tin hydroxide precipitate free from chlorine ions was obtained according to Refs.[13-14]. According to a great amount of experiments, isoamyl acetate was developed to be the optimized azeotropic drying solvent. Isoamyl acetate was compared with the most commonly used n-butanol solvent on treating precipitate for very low agglomeration precursor powders. The sizes and dispersivity of the final particles dried by isoamyl acetate were characterized with FT-IR, BET, XRD and TEM. And grain growth processes during the calcinations were investigated.
2 Experimental
2.1 Experimental methods
2.1.1 Preparation of antimony-doped tin hydroxide
Antimony-doped tin hydroxide was obtained according to Ref.[13].
2.1.2 Azeotropic drying
The lower-density precipitate slurry was divided into three equal parts for the tests of azeotropic drying. One part of lower-density precipitate was directly dried at 100℃ as a reference sample; the other two parts were added respectively with n-butanol and isoamyl acetate. After shaking on the shaker for 2 h, the mixtures of precipitate and organic solvents were distilled to drive off solvent in a water-bath at about 95 ℃ and the hydrolysis product remained. The dried powder was placed in an oven to continue drying at 100-110 ℃ for 4-8 h.
2.1.3 Firing and crystallization
The dehydrated powders dried by isoamyl acetate were spread (about 1 mm thick) on corundum plate and fired in a muffle furnace separately at 550, 650, 750 and 850 ℃ for 2.5 h in air. The fired powders were light-blue crystals.
2.2 Characterization of powders
The FT-IR analysis of the precursor powders for the remainder of organic solvent was performed on a Nicolet (USA) 5700 FTIR spectrometer with the KBr pellets method. The analysis of specific surface area of the dried powders was done with a specific surface area analyzer, ASAP 2020 (Micromeritics, USA). The BET nitrogen surface area, SBET, was obtained by applying the BET (Brunauer, Emmett and Teller) equation to a relative pressure range of 0.05-0.30 on the adsorption isotherm. The crystalline form and size were characterized with the transmission electron microscope(TEM), JEM-2010(HT) (JEOL, Japan) and the D8 advance X-ray diffractometer (XRD) (Bruker, Germany). The patterns of samples were scanned at step of 0.02?(2θ) in the 2θ range from 15? to 75? with a fixed scanning rate of 4 (?)/min. The average crystal size of the powders was calculated from diffraction peak full width at half maximum(FWHM) by using the Scherrer equation.
3 Results and discussion
3.1 Photograph of antimony-doped tin hydroxide
Fig.1 shows the results of antimony-doped tin hydroxide with azeotropic distillation drying by n-butanol (Fig.1(b)), isoamyl acetate (Fig.1(c)) and a direct distillation without azeotropic agent(absolute alcohol). The colourities, agglomerates and hardness of dried products were studied. Dehydrating ability order is: absolute alcohol<n-butanol<isoamyl acetate.
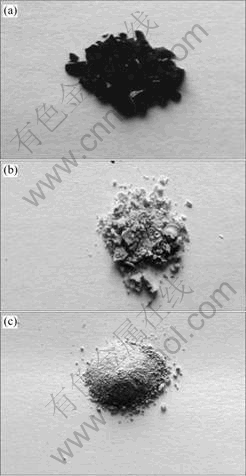
Fig.1 Photographs of antimony-doped tin hydroxide dried by: (a) Direct distillation drying; (b) Azeotropic distillation drying of n-butanol; (c) Azeotropic distillation drying of isoamyl acetate
The surface hydrated layers of particles make the polymer precipitate with a steady dispersibility in the ethanol solvent. However, during evaporation, the ethanol with lower boiling point is evaporated first and water molecules are left on the surface of precipitate particles. As the volume of solution containing polymer precipitate lessens, colloid particles close up and surface hydrated water combines to form water film between the particles. The film water, like capillary one, has capillary force that can cause particles to shrink up and eventually contact others to form hard brown agglomerates. Although the majority of H2O molecules on the surface of colloid precipitate can be removed by azeotropic distillation with n-butanol, water is partly miscible with n-butanol up to 20.1% (volume fraction) [15]. At the end of the dehydrating process, a little amount of H2O molecules still remain in the system, which leads to the crystallite growing and forming hard agglomeration to some extent. The isoamyl acetate organic solvent was selected from a series of solvents with groups containing oxygen in azeotropic distillation experiments. Water is almost un-miscible with isoamyl acetate, with a miscibility of 1.6% (volume fraction). Isoamyl acetate has a higher boiling point (143 ℃) because it consists of an oxygen-contained group to replace surface water molecule of colloid particle by forming a hydrogen bond between the group and the surface —OH of polymer particle. Furthermore, the group is located in the middle of the alkane instead of at the ends in that the alkane will stretch out and cover more surface area to achieve a lower degree of agglomeration. Consequently, a well dispersed and loosely dried product can be obtained[16].
3.2 FT-IR spectra
The surface state of the dried antimony-doped tin hydroxide powders dried by azeotropic distillation of n-butanol and isoamyl acetate is shown in Fig.2.
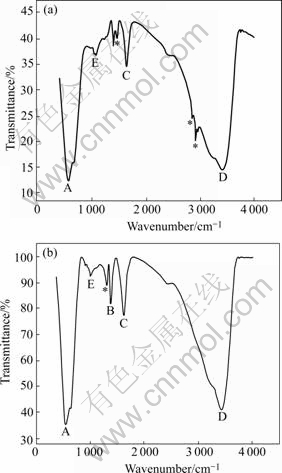
Fig.2 IR spectra of antimony-doped tin hydroxide dried powder (A: Sn(Sb)—O; B: Ammonia water; C: Water; D: —OH; E: C—O; *: Organic substance): (a) n-butanol; (b) Isoamyl acetate
As shown in Fig.2, the broad band D at 3 420 cm-1 indicates a large amount of surface —OH groups of antimony-doped tin hydroxide, while the band A at 565 cm-1 indicates Sn(Sb)—OH. Band B is caused by NH3, the catalyst added in the hydrolysis process, appeared at 1 400 cm-1. The bands at 2 792, 2 840, 2 930 and 1 440 cm-1, the sign *, and 1040 cm-1, the sign E, are all indicative of the presence of organic compounds, or the azeotropic agents, whereas among them, the band at 1 040 cm-1 indicates C—O groups. The band C at 1 635 cm-1 is indicative of the presence of water molecule. But the height of the absorption peak cannot suggest the dehydration capacities of azeotropic agents, because the higher peak is probably caused by water adsorbed from air when the sample tablets were prepared. The higher the dispersivity of the powder, the more the water molecules it adsorbs in the air[16-17]. As shown in Fig.2(a), n-butanol forms numerous strong hydrogen bonds with polymer particles, and the residual quantity of organic solvent is more than isoamyl acetate (Fig.2(b)). Thus, isoamyl acetate is a more effective azeotropic drying solvent than n-butanol.
3.3 BET analysis
The specific surface area of powders relates to the particle size, shape and aggregation state. Smaller size and irregular surface lead to high specific surface area, while aggregation of particles will lower specific surface area. To further investigate the effects of isoamyl acetate on the dispersivity of the dried product, the analysis of specific surface area was conducted on the powders. The adsorption isotherms for the dried powder obtained using isoamyl acetate and n-butanol as azeotropic solvents are shown in Fig.3. The BET nitrogen surface areas are obtained by applying the BET equation to a relative pressure range of 0.05-0.30 on the adsorption isotherm. When the most often used n-butanol is substituted by isoamyl acetate, the BET surface area increases from 234.750 0 to 284.440 0 m2/g, and the dispersivity of the dried powder increases by 22%. Before the adsorption measurement, the dried product obtained with n-butanol was ground since pieces of dried agglomerates were present in large amounts. However, the dried product derived from the same azeotropic conditions with isoamyl acetate was a highly dispersed powder that did not require grinding. So the isoamyl acetate azeotropic solvent was further studied.
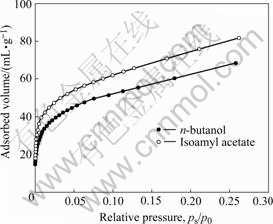
Fig.3 Nitrogen adsorption isotherms for dried powder
The SBET, VBJH, dXRD and DBET values of precursor powders dried with isoamyl acetate and powders that calcined at different temperatures are listed in Table 1. Generally, dXRD is considered as the original crystallite size; the average grain size is calculated using the equation DBET=6/(ρSBET), where DBET is the average diameter of spherical particle, SBET is the surface area of the powder and ρ is the theoretical density of tin oxide. dXRD is deduced from the full width at half maximum (FWHM) of (110) crystal face by applying Scherrer equation. It can be seen from Table 1 that the BET specific surface area of precursor powders is much larger than that of the calcined powders of antimony-doped tin oxide. And both the BET specific surface area and BJH adsorption cumulative volume of pores show a sharp decrease when the calcination temperature increases. The reason is that the grain size of precursor powders is smaller than that of the calcined powders, therefore after the calcination the grain size of the powder becomes bigger, leading to the increase of pore width. As calcina- tion temperature rises, the spacing between primary particles becomes smaller, and even disappears[18], and the density of particles increases. Therefore, both the BET specific surface area and BJH adsorption cumulative volume of pores decrease. Furthermore, the adjacent bond Sn—OH will condensate to Sn—O—Sn during the calcination. Therefore, the occurrence of hard agglomeration also results in the decrease of the BET specific surface area. Table 1 indicates that the precursor powders dried with isoamyl acetate have less hard agglomeration. When the calcination temperature increases, the hard agglomerate degree increases. This illuminates that the surface hydroxyl groups are apt to condense and hydrate when the temperature rises. Furthermore, as the grains contact compactly, hard agglomerate that is difficult to disperse, generates.
Table 1 Characteristics of antimony-doped tin oxide nanopowders calcinated at different temperatures

3.4 XRD analysis
Fig.4 shows the XRD patterns of the precursor that is azeotropically dried with isoamyl acetate at 100 ℃ and the powders in air calcined at 550, 650, 750 and 850 ℃ for 2.5 h. It is obvious that in all cases, the peak positions match well with the reflections of tetragonal rutile structure of pure SnO2 (JCPDS card No.88 2348). The broaden diffraction peaks attributed to (110), (101), (211) of SnO2 were detected, which indicates that all antimony ions come into the crystal lattice of rutile SnO2 to substitute for tin ions[19]. It can also be observed that in the same calcination time, as the calcining temperature increases, the diffraction peaks become sharper. The result indicates that the crystal characters become distinct and the crystal structure becomes perfect.
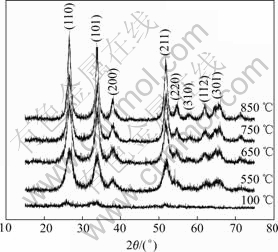
Fig.4 XRD patterns of precursor azeotropically dried with isoamyl acetate at 100 ℃ and of antimony-doped tin oxide powder calcined at different temperatures
Table 2 lists the crystallite size determined by the Scherrer equation (Dhkl=kλ/(βcosθ)). It is observed in Table 2 that the crystallite size increases as the calcination temperature rises. When the temperature is below 650 ℃, the crystallite size increases slowly, but when the temperature is above 650 ℃, the crystallite size increases rapidly as the calcination temperature rises.
Table 2 Crystallite size (nm) calculated using Scherrer equation
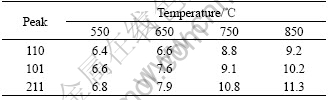
The lattice distortion rates of nano antimony-doped tin oxide crystal grains at different calcination temperatures can be obtained by Eqm.(1) [20-21]:
(2ω)2cos2θ=4λ2/(π2D2)+32<ε2>sin2θ (1)
where 2ω is the half-width (obtained after correction for the instrumental broadening), θ is the angle of diffraction, D is the average crystallite size, and <ε2>1/2 is the lattice distortion rate.
Fig.5 shows the calcination temperature dependence on (110) crystal face lattice distortion rate. It is observed in Fig.5 that the lattice distortion rate gradually decreases when the calcination temperature increases.
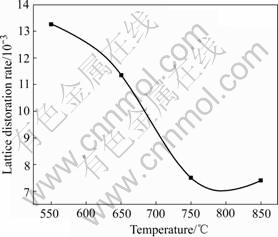
Fig.5 Relationship between lattice distortion rate and calcination temperature
The reason is that the crystalline field of the surface atom is different from that of bulk atom. The smaller the crystal size, the higher the ratio of surface atom, the more the defect and the higher the lattice distortion rate. With the high calcination temperature, the crystallite size increases, the crystal structure tends to get perfect, and the lattice distortion rate decreases correspondingly. When the temperature is up to 750 ℃, lattice distortion rate remains stable.
Table 3 lists the lattice constants for the a-axis and c-axis of SnO2 crystal and cell volume V=a2c[20-21] with the lattice constants formula determined from the (110) and (101) planes.
Table 3 Relation between lattice constants and cell volume of Sb-doped tin oxide calcinated at different temperatures
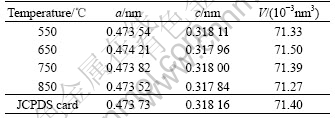
It can be seen from Table 3 that the lattice parameters a and c calculated at different calcined temperatures are in agreement with tetragona SnO2 of standard pattern (JCPDS card No.88 2348). It further approves the obtained powder with rutile structure SnO2. The Sb ions are incorporated into SnO2, and as a consequence, the cell parameters are changed. The ionic radii of Sn4+, Sb5+ and Sb3+ are 0.069, 0.060 and 0.090 nm, respectively. If antimony is incorporated into the lattice of tin oxide to substitute Sn4+ in the form of Sb5+, the crystal cell of SnO2 nanoparticles will shrink for the ionic radius of Sb5+ is smaller than that of Sn4+. It will expand when antimony enters into the lattice of tin oxide in the form of Sb3+ for the ionic radius of Sb3+ is larger than that of Sn4+. The lattice constants and the cell volume have a decreasing tendency with the increase of the calcination temperature. The initial increase of lattice constants is due to the dissolution of Sb3+ into the SnO2 lattice.
3.5 TEM analysis
Fig.6 shows the TEM images and electron diffraction pattern of precursor powder and antimony- doped tin oxide nanocrystallites calcined in air at 550 ℃ and 850 ℃ for 2.5 h from the dried powder by isoamyl acetate at 550 ℃. It can be seen from Fig.6 that the dried powder of precursor shows low agglomeration, high dispersivity and uniform crystal size. The precursor is poor crystalline or noncrystalline. With the increase of calcined temperature the crystallite size increases, the morphology of nanocrystalline antimony-doped tin oxide particle is irregular axiolite and the crystalline shape becomes perfect.
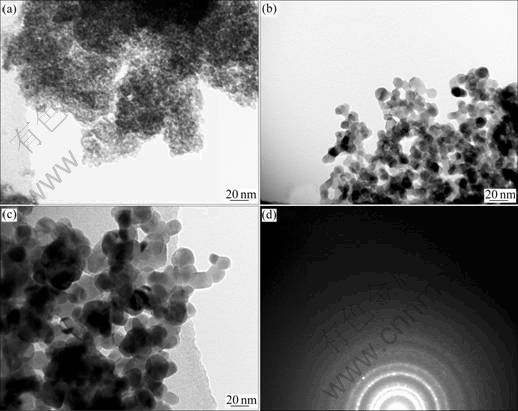
Fig.6 TEM images of precursor powder at 100 ℃ (a) and antimony-doped tin oxide powder calcined at 550 ℃ (b) and 850 ℃ (c) for 2.5 h and electron diffraction image at 550 ℃ (d)
4 Conclusions
1) Antimony-doped tin hydroxide colloid pre- cipitates were synthesized with an anion exchange resin hydrolysis method by removing chlorine. The isoamyl acetate was selected as azeotropic drying solvent and was compared with the most commonly used n-butanol solvent on treating precipitate for low hard agglomeration precursor powders.
2) Isoamyl acetate is more effective than the most commonly used n-butanol. Compared with n-butanol, isoamyl acetate greatly improves the dispersivity and fluffiness of the obtained dried powder. Based on the results from the FT-IR, BET, XRD and TEM measurements, high dispersivity and very low hard agglomeration precursor powders can be obtained with isoamyl acetate azeotropic drying.
3) The precursor powders dried with isoamyl acetate are calcined, and antimony-doped tin oxide nanopowders with tetragonal rutile structure and high dispersivity are obtained.
Acknowledgments
The authors give their special thanks to Kevin Yang of California State University, Fullerton, USA for his critical reading and editing.
References
[1] WU Xiang-wei, CHEN Zhen-hua, HUANG Pei-yun. Influence of dehydrating process on properties of ATO nano-powders [J]. Trans Nonferrous Met Soc China, 2004, 14(6): 1123-1127.
[2] ZHANG Jian-rong, GAO Lian. Synthesis and characterization of antimony-doped tin oxide (ATO) nanoparticles [J]. Inorganic Chemistry Communications, 2004, 7(1): 91-93.
[3] BOUJDAY S, WüNCH F, Portes P, JEAN-FranCois J F, Bocquet, Colbeau-Justin C. Photocatalytic and electronic properties of TiO2 powder elaborated by sol-gel route and supercritical drying [J]. Solar Energy Materials & Solar Cells, 2004, 83(4): 421-433.
[4] Park C H, Bell A T, Tilley T T D. Oxidative dehydrogenation of propane over vanadia-magnesia catalysts prepared by thermolysis of OV(OtBu)3 in the presence of nanocrystalline MgO [J]. Journal of Catalysis, 2002, 206(1): 49-59.
[5] Vidal K, Lezama L, Arriortua M I, Rojo T, Gutiérrez J, Barandiarán J M. Magnetic characterization of Nd0.8Sr0.2(Mn1-xCox)O3 perovskites [J]. J Magnetism and Magnetic Mater, 2005, 290/291(4): 914-916.
[6] Shlyakhtin O A, Oh Y J, Tretyakov Y D. Preparation of dense La0.7Ca0.3MnO3 ceramics from freeze-dried precursors [J]. Journal of Europe Ceramic Society, 2000, 20(12): 2047-2054.
[7] Hwang K T, Auh K H, KIM C S, Cheong D S, Niihara K. Influence of SiC particle size and drying method on mechanical properties and microstructure of Si3N4/SiC nanocomposite [J]. Material Letters, 1997, 32(4): 251-257.
[8] Hu Z S, Dong J X, Chen G X. Replacing solvent drying technique for nanometer particle preparation [J]. Journal of Colloid and Interface Science, 1998, 208(2): 367-372.
[9] Frazee J W, Harris T M. Processing of alumina low-density xerogels by ambient pressure drying [J]. J Non-Cry Sol, 2001, 285(1/3): 84-89.
[10] Luan Wei-ling, Gao Lian, Guo Jing-Kun. Study on drying stage of nanoscale powder preparation [J]. Nanostructured Materials, 1998, 10(7): 1119-1125.
[11] Li Ji-guang, Ikegami T, Wang Ya-rong, Mori T. Nanocrystalline Ce1-xYxO2 (0≤x≤0.35) oxides via carbonate precipitation: Synthesis and characterization [J]. Journal of Solid State Chemistry, 2002, 168(1): 52-59.
[12] HE Qiu-xing, TU Wei-ping, HU Jian-qing. Synthesis and characterization of bismuth-doped tin dioxide nanometer powders [J]. Journal of Central South University of Technology, 2006, 13(5): 519-524.
[13] ZHANG Xue-jun, LIANG Hong-bo, GAN Fu-xing. Novel anion exchange method for exact antimony doping control of stannic oxide nanocrystal powder [J]. Am Ceram Soc, 2006, 89(3): 792-798.
[14] ZHANG Xue-jun, GAN Fu-xing. A Preparation Method of Antimony-Doped Stannic Oxide Nanocrystal [P]. CN 1594099A, 2005-03-16. (in Chinese)
[15] CHENG Neng-lin. Solvents Handbook [M]. Beijing: Chemical Industry Press, 2002. (in Chinese)
[16] ZHANG Xue-jun, YANG Fen, GAN Fu-xing. Preparation of High Dispersivity Antimony-Doped Tin Oxide Nanopowders [P]. CN 1736877. 2006-02-26. (in Chinese)
[17] ZHANG Xue-jun. The Preparation and Electrochemical Properties of Sb-Doped Stannic Oxide Nanocrystal [D]. Wuhan: Wuhan University, 2005. (in Chinese)
[18] GAO Lian, CHEN Jin-yuan, HUANG Jun-hua, Yan Dong-sheng. Preparation of superfine titania powder by the hydrolysis of titanium alkoxide [J]. Journal of Inorganic Materials, 1995, 10(4): 423-427.
[19] ZHANG Jian-rong, GAO Lian. Antimony-doped tin oxide nanocrystallites prepared by a combustion process [J]. Materials Letters, 2004, 58(22/23): 2730-2734.
[20] JIANG Ming-xi, YANG Tian-zu, GU Ying-ying, DU Zuo-juan, LIU Jian-ling. Preparation of antimony-doped nanoparticles by hydrothermal method [J]. Trans Nonferrous Met Soc China, 2005, 15(3): 702-705.
[21] JIANG Ming-xi, YANG Tian-zu, CHU Guang, GU Ying-yin, DU Zuo-jian. Synthesis of antimony-doped tin oxide nanoparticles by complexing-hydrothermal oxidation method [J]. Journal of Central South University, 2006, 37(2): 247-251. (in Chiense)
Foundation item: Project(50471027) supported by the National Natural Science Foundation of China
Corresponding author: GAN Fu-xing; Tel: +86-27-68775799; E-mail: fxgan@public.wh.hb.cn
(Edited by CHEN Wei-ping)