
Correlation of recalescence with grain refinement of magnesium alloys
GAO Lei(高 磊)1, 2, LIANG Song-mao(梁松茂)1, 2, CHEN Rong-shi(陈荣石)1, HAN En-hou(韩恩厚)1
1. State Key Laboratory for Corrosion and Protection, Institute of Metal Research, Chinese Academy of Sciences, Shenyang 110016, China;
2. Graduate School of Chinese Academy of Sciences, Beijing 100039, China
Received 12 June 2008; accepted 5 September 2008
Abstract: The grain refinement of Mg-Al based alloys with carbon inoculation was investigated by a computer-aided cooling curve analysis (CA-CCA) system. The results show that carbon inoculation decreases the main parameters of the recalescence regime during the initial stage of solidification. These parameters include the recalescence undercooling (Δθrec), duration of recalescence (trec), and liquid peak parameter (LPP) which is firstly introduced into magnesium alloys. The resultant grain size decreases with increasing nucleation temperature (θn) and decreasing values of Δθrec, trec and LPP.
Key words: magnesium alloys; grain refinement; recalescence; thermal analysis
1 Introduction
Grain refinement is an important practice in the magnesium industry which can be used to improve the mechanical properties of magnesium alloys. Many grain-refining methods have been developed, including melt superheating, Elfinal process, melt agitation, carbon inoculation, and Zr addition[1-2]. Among these methods, adding carbon-containing agents, such as C2Cl6, to the melt is known to be the most effective way to refine the grains of Mg-Al based alloys, as they offer several practical advantages, such as low operating temperature and less fading with long holding times, for applications in mass production[2-3].
Currently, the most popular method to investigate the grain refinement is to check the cast microstructure which however cannot provide complete information about primary crystal nucleation as ROHATGI and ASTHANA[4] suggested. On the other hand, cooling curve thermal analysis is a useful technique to study solidification and can provide some supplementary information about the nucleation behavior. This technique, which has been well applied in our laboratory[5-6], involves the monitoring of the temperature changes in a melt during its cooling and solidification[7]. During solidification the latent heat released by the solidifying microconstituents causes changes in the cooling curve and its derivative which are linked with the development and characteristics of the microstructure observed in the cast product[5-6]. The precise shape of the curve is directly related to various microstructural features and is as significant and individual as the human thumbprint[8].
However, cooling curve thermal analysis has not been well applied to magnesium alloys while it has been widely used in the studies of grain refinement for aluminium alloys[9-11]. For clarity of the definitions used for thermal data, the basic cooling curve parameters are defined and illustrated on an actual cooling curve (T curve) in Fig.1[4, 9-12]. Where θn is the initial temperature start of primary α-Mg dendrites nucleation; θmin is unsteady state growth temperature, beyond which the newly nucleated crystals grow to such extend that the latent heat liberated surpasses the heat extracted from the sample; θg is recalescence of steady state growth due to release of latent heat of primary α-Mg dendrites; ?θrec is the recalescence undercooling, the temperature difference between unsteady (θmin) and steady (θg) state growth temperatures of primary α-Mg dendrites; trec is duration
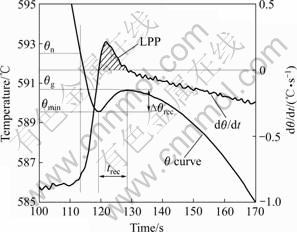
Fig.1 Segment of cooling curve with illustration of critical points
of recalescence[4, 10-11]; LPP is liquidus peak parameter, the area below the positive segment (dθ/dt>0) of the first derivative curve.
θn provides information about the first nucleation events while Δθrec, trec, and LPP characterize the degree of recalescence. LPP is associated with Δθrec and trec[9].
In the present study, the grain refinement of AZ31 and AZ91 magnesium alloys was analyzed and related to the solidification thermal parameters such as recalescence undercooling (Δθrec), duration of recalescence (trec), and liquid peak parameter (LPP) which were determined from the temperature versus time curves.
2 Experimental
Commercial purity magnesium, aluminium and zinc ingots were used as the raw material to prepare AZ31 and AZ91 melts. Smelting process was carried out in an electrical resistance furnace with capacity of 15 kg under a protective cover gas (1.0%SF6 in 49% dry air and 50% CO2). The magnesite particles, with a size of about 0.5 mm and wrapped up with aluminum foil, were introduced in a bell jar to the melt at 720 ℃ after the refining procedure. The content of MgCO3 in magnesite particles was more than 98% (mass fraction) and the addition of magnesite particles to the melt accounted for 1.5% (mass fraction) of the total mass of raw materials.
The samples for thermal analysis studies were taken from the top of the melt using a boron nitride coated steel mould, and then cooled in air. The mould was a cone cup with a diameter of 50 mm at the bottom and 60 mm at the top and 80 mm in height. Cups were held in the melt for approximately 1 min before sampling to ensure uniform temperature distribution across the steel cups at the beginning of solidification. A K-type thermocouple was immersed into the melt sample approximately at the center of the melt to record the changes in melt temperature. The thermocouple was connected to a National Instrument data acquisition system with 20 readings per second sampling rate. Three duplicate runs for each melt sample were carried out to ensure the accuracy and consistency of the analytical data. For these series of experiments, cooling rates were around 1 ℃/s above liquid temperature.
The macrostructure/microstructure was developed on the transversely sectioned surface 35 mm from the bottom. AZ91 sample for grain size measurement was taken solid solution treatment at 420 ℃ for 2 h and then quenched in water. The grain size of each cone sample was measured from the central region of a polished section in accordance with the intercept linear method described in the ASTM standard E112-96.
3 Results and discussion
Fig.2 shows the typical cooling curves of AZ31 alloys before and after carbon inoculation. It can be seen that the additions of magnesite shift the cooling curves up to the left with increasing nucleation temperature and decreasing recalescence undercooling. The nucleation takes places at higher temperatures and maintains shorter time after pouring. The detected thermal parameters are listed in Table 1. It can be seen that AZ31 alloy cooling from this experimental condition exhibits a nucleation temperature of 627.5 ℃ for α-Mg without carbon inoculation. However, with the influence of carbon inoculation, the nucleation temperature was raised to 631.9 ℃. Additionally, after carbon inoculation 0.2 ℃ of recalescence undercooling was observed while 0.6 ℃ of recalescence undercooling prior to carbon inoculation.
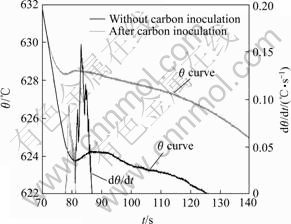
Fig.2 Curves of temperature vs time for AZ31 ingots before and after carbon inoculation
The effect of carbon inoculation on the solidification of AZ91 alloy is illustrated in Fig.3(a). Two peaks are observed from both of the derivative curves, namely, solidification of α-Mg for the first one and eutectic reaction for the second. Closer inspection for the solidification of α-Mg is enlarged in Fig.3(b). The effect of carbon inoculation on the thermal analysis temperature parameters for AZ91 alloys (see Fig.3) is similar to those observed previously for AZ31 alloys (see Fig.2) with nucleation temperature increasing from 598.9 to 605.1 ℃ and recalescence undercooling decreasing from 0.4 ℃ to 0-0.1 ℃ (see Table 1).
Figs.4(a) and 4(b) show the typical grain structures for AZ31 before and after carbon inoculation, respectively.
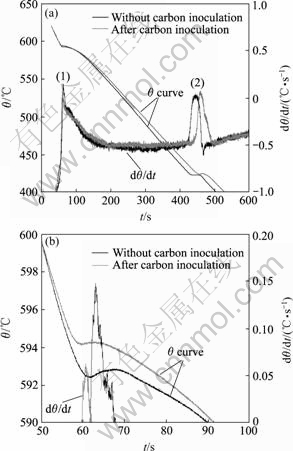
Fig.3 Typical temperature—time curves and their derivatives for AZ91 alloy(a) and magnification of curve limited to recalescence regime(b)
It can be seen that significant grain refinement is obtained by the addition of magnesite particles as carbon inoculation agent. The grain refinement mechanism of magnesite particles should be attributed to the Al2CO nucleus which are formed by a reaction between aluminium and CO2 released by decomposition of magnesite[3]. The corresponding average grain size of AZ31 and AZ91 alloys before and after carbon inoculation are also listed in Table 1.
It can be seen from Table 1 that the increase in θn and decrease in Δθrec under the effect of carbon inoculation correspond to the resultant grain size, which is in good agreement with those reported by ACHENBACH et al[13], TINER[14], and CAO[4] for Mg-9%Al alloys. However, liquidus peak parameter (LPP), related to the recalescence is not studied by these researchers. From analyzing the derivative curves, LPP is observed in the current research. It can be observed from Fig.2 and Table 1 that the value of LPP for AZ31 decreases from 0.47 without carbon inoculation to 0.16
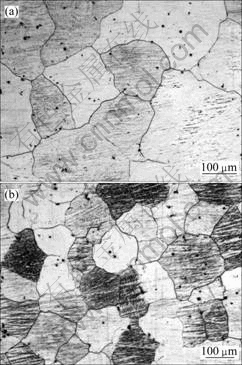
Fig.4 Typical grain structures for AZ31 alloys before(a) and after(b) carbon inoculation
Table 1 Correlation of parameters related to recalescence with grain refinement for AZ31 and AZ91 alloys

1) Carbon inoculation.
after carbon inoculation. Similar results can be gained from Fig.3(b) and Table 1 that the value of LPP for AZ91 decreases from 0.39 to 0.06. It should be noticed that obvious decrease in LPP can be observed for Mg-9%Al alloy before and after superheating in Ref.[4] which has been ignored by the authors. The detected changes in LPP shown in Figs.2 and 3(b) are similar to those recorded for aluminium alloys before and after the addition of Ti and B containing refiner[9]. The results suggest that the grain size decreases with increasing nucleation temperature (θn) and decreasing values of Δθrec, trec and LPP.
The preceding content can be understood if one considers that thermal analysis cooling curves, corresponding to the cooling process of melt in the mold or test cup, mainly include two factors: solidification latent heat and elimination of heat [11, 15-16]. For grain refinement, the latent heats mainly relate to the nucleation and growth of primary crystal α-Mg. The grain size decrease with increasing nucleation temperature can be ascribed to the easier nucleation: a larger number density of nucleation events at smaller undercooling. Additionally, the decrease of grain size with decreasing values of Δθrec, trec, and LPP can be ascribed to the reduction of recalescence, because it was suggested [11, 17] that with the increase of recalescence the nucleation potential of the melt decreases, which means the solidification structure would be coarse grain. Recalescence limits the refinement of grain size by allowing growth of existing grains but preventing further nucleation [9-10].
However, it is worth noting that detecting the recalescence of magnesium alloys is difficult due to the relatively low value of latent heat of fusion (8.48 kJ/mol) to aluminium alloys (10.71 kJ/mol) and iron alloys (13.81 kJ/mol)[18]. Further investigations are needed and in progress to understand the recalescence.
4 Conclusions
1) Carbon inoculation increases the nucleation temperature while it decreases the recalescence undercooling, duration of recalescence, and liquid peak parameter.
2) The resultant grain size in the casting corresponds to these changes in θn, Δθrec, trec, and LPP caused by carbon inoculation.
References
[1] LU L, DAHLE A K, STJOHN D H. Grain refinement efficiency and mechanism of aluminium carbide in Mg-Al alloys[J]. Scripta Materialia, 2005, 53: 517-522.
[2] KIM Y M, YIM C D, YOU B S. Grain refining mechanism in Mg-Al base alloys with carbon addition[J]. Scripta Materialia, 2007, 55: 691-694.
[3] MA Yue-qun, CHEN Rong-shi, HAN En-hou. Keys to improving the strength and ductility of the AZ64 magnesium alloy[J]. Materials Letters, 2007, 61: 2527-2530.
[4] CAO P, QIAN M, STJOHN D H. Grain refinement of commercial purity Mg-9%Al alloys by superheating[C]// NEELAMEGGHAM N R, KAPLAN H I, POWELL B R. Magnesium Technology 2005. TMS, Warrendale, 2005: 297-302.
[5] HUANG Z H, LIANG S M, CHEN R S, HAN E H. Solidification pathways and constituent phases of Mg-Zn-Y-Zr alloys[J]. Journal of Alloys and Compounds, 2008, doi:10.1016/j.jallcom.2008.01.034.
[6] LIANG S M, CHEN R S, BLANDIN J J, SUERY M, HAN E H. Thermal analysis and solidification pathways of Mg-Al-Ca system alloys[J]. Mater Sci Eng A, 2008, 480:365-372.
[7] CRUZ H, GONZALEZ C, JUAREZ A, HERRERA M, JUAREZ J. Quantification of the microconstituents formed during solidification by the Newton thermal analysis method[J]. Journal of Materials Processing Technology, 2006, 178: 128-134.
[8] KROHN B R. Thermal analysis: metallurgical thumbprinting[J]. Modern Casting, 1985, 75(3): 21-25.
[9] YEN C M, EVANS W J, NOWICKI R M, COLE G S. Measuring the quality of aluminum casting alloys with microprocessor-aided thermal analysis[J]. AFS Transactions, 1985, 93: 199-204.
[10] NAFISI S, GHOMASHCHI R. Grain refining of conventional and semi-solid A356 Al-Si alloy[J]. Journal of Materials Processing Technology, 2006, 174: 371-383.
[11] WANG Q, LI Y X, LI X C. Grain refinement of Al-7Si alloys and the efficiency assessment by recognition of cooling curves[J]. Metall Mater Trans A, 2003, 34:1175-1182.
[12] IBARRA D G. Control of grain refinement of Al-Si alloys by thermal analysis[D]. McGill University, 1999.
[13] ACHENBACH K, NIPPER H A, PIWOWARSKY E. Contribution to the question of melting practice for cast magnesium alloys[J]. Die Giesserei, 1939, 26: 621-623.
[14] TINER N. Superheating of magnesium alloys[J]. AIME, Tech Pub, 1945, 12: 1-19.
[15] KUMAR G, HEGDE S, PRABHU K N. Heat transfer and solidification behaviour of modified A357 alloy[J]. Journal of Materials Processing Technology, 2007, 182: 152-156.
[16] CHAVEZ M R, AMARO A, FLORES C, JUAREZ A, GONZALEZ R C. Newton thermal analysis of gray and nodular eutectic cast iron[J]. Materials Science Forum, 2006, 509: 153-158.
[17] GOWRI S. Comparison of thermal analysis parameters of 356 and 359 alloys[J]. AFS Trans, 1994, 102: 503-512.
[18] The free encyclopedia (2001) US Wikipedia. http://en.wikipedia. org/wiki.
(Edited by LONG Huai-zhong)
Foundation item: Project(2007CB613704) supported by the National Basic Research Program of China; Project(50574086) supported by the National Natural Science Foundation of China
Corresponding author: CHEN Rong-shi; Tel: +86-24-23926646; E-mail: rschen@imr.ac.cn