网络首发时间: 2017-07-28 18:53
稀有金属 2018,42(08),864-868 DOI:10.13373/j.cnki.cjrm.xy17060016
无坩埚熔炼气雾化技术制备高纯球形锆粉
宰雄飞 陈仕奇 吴宏 刘咏
中南大学粉末冶金国家重点实验室
摘 要:
以锆棒为原料, 采用自主设计的无坩埚熔炼气雾化设备成功制备出高纯球形锆粉。优化气雾化工艺参数, 并探究进料速度与雾化压力对雾化过程的影响机制。通过氧氮氢化学成分分析仪分析粉末的氧氮氢含量, 激光粒度分析仪和标准筛测定粉末粒径分布, 扫描电子显微镜 (SEM) 观察粉末的球形度及表面形貌, 霍尔流速计测定粉末的流动性和松装密度。试验结果表明, 在本试验采用的工艺参数范围内, 细粉 (粒径<45μm) 收得率与雾化压力和进料速度呈正比。控制进料速度为45 mm·min-1, 雾化压力为5.0 MPa时, 雾化过程稳定, 且细粉的产出率可达40.50%。采用该技术制备的高纯球形锆粉, 氧氮含量均可控制在较低的范围内, 制备的粉末氧含量为870 ppm, 氮含量仅为10 ppm。且制备的粉末粒径可控, 表面光洁, 形状为球形或近球形, 卫星粉较少, 具有良好的流动性和松装密度, 可用于注射成型、粉末冶金、金属增材制造及核工业等领域。
关键词:
锆粉;气雾化;球形;高纯;
中图分类号: TF123.24
作者简介:宰雄飞 (1992-) , 男, 山西临汾人, 硕士, 研究方向:气雾化;E-mail:zxf735@163.com;;*陈仕奇, 副教授;电话:0731-8830464;E-mail:chenpm450@163.com;
收稿日期:2017-06-04
基金:国家科技部重点研发计划项目 (2016YFB1100103);湖南省重点研发计划项目 (2016JC2003) 资助;
Preparation of Spherical High-Purity Zr Powders by Gas Atomization without Crucible
Zai Xiongfei Chen Shiqi Wu Hong Liu Yong
State Key Laboratory of Powder Metallurgy, Central South University
Abstract:
Spherical high-purity Zr powders were prepared by gas atomization equipment without crucible, which was designed independently. The steady atomization processes were achieved by optimum technology conditions. The influences of feed rates and gas pressure on atomization process were studied. Element contents of gas atomization Zr powders were analyzed with O, N and H analyzer.Particle size distribution was measured by laser particle size analyzer and standard sieves. The surface appearance of powders was observed by scanning electron microscope ( SEM) . Flow ability and apparent density of the powders were characterized by Hall flowmeter. The results showed that the yields of fine powder ( particle size < 45 μm) were improved with the increase of feed rate and gas pressure. And the yield of fine powder could reach 40. 50%, when the feed rate was 45 mm·min-1 and gas pressure was 5. 0 MPa.With this gas atomization technique, oxygen content of powders was 870 × 10-6 and nitrogen content was 10 × 10-6. The particle size distribution could be adjusted in the atomization process. The powder had outstanding flow ability and apparent density due to the nearly spherical shape and smooth powder surface. The powder prepared by the gas atomization without crucible could be applied to injection molding, powder metallurgy, metal additive manufacturing and nuclear industry etc.
Keyword:
Zr powder; gas atomization; spherical powder; high purity;
Received: 2017-06-04
锆作为21世纪最具有发展前景的材料之一, 以其独特的性能被广泛应用于现代工业。在冶金领域, 以锆为添加剂可细化合金晶粒, 提高和改善合金性能;在核工业中, 锆可作为核反应堆燃料元件的结构材料和慢化剂;且锆以其独特的机械性能和良好的生物相容性, 被用于医用材料[1,2,3,4,5]。锆粉则由于具有较大的表面积和优异的吸气能力, 被用于电真空行业;其着火点低, 燃烧速度快, 被用于制造烟花、照明弹和引爆剂;核纯级锆粉其中子截面系数小、耐热性好, 被用于燃料元件的基体填充材料[6,7,8]。
在核燃料元件中, 锆粉的流动性直接影响混合粉体的填充性能, 进而影响燃料元件中铀的均匀分布;在粉末冶金领域, 锆粉的流动性会影响粉体的填充性能与压制性能;且近年来, 随着金属增材制造的快速发展, 对于具有良好流动性的锆粉需求也在不断增加。目前用于制备锆粉的方法主要有氢化脱氢法、金属热还原法和熔盐电解法, 制备的锆粉均为不规则状和树枝状, 粉末之间的摩擦与搭接严重, 流动性差[9,10,11,12,13,14]。陈建刚等[15]通过表面氧化和去除细粉的方式提高氢化脱氢法制备的核纯级锆粉流动性, 将流动性提高至10.5 s/50 g。
气雾化技术制备的粉末为球形或近球形, 具有良好的流动性, 但锆会与熔炼坩埚和中间包的材质 (Al2O3或石墨) 发生反应, 无法采用常规坩埚熔炼气雾化法制备锆粉[15,16,17]。本文采用自主设计研发的无坩埚熔炼气雾化技术首次成功制备锆粉, 以满足现代工业对高纯球形锆粉的需求。并探究了雾化工艺对雾化过程的影响机制, 对粉末性能进行表征。
1实验
试验设备为自主设计研发的无坩埚熔炼气雾化设备, 其原理如图1所示。该设备主要由真空系统、进料系统、熔炼系统、雾化系统和智能控制系统组成, 可实现锆粉的高效智能生产。实验原料为纯度99.99%的氩气与直径50 mm的锆棒, 并将锆棒的一端加工为70°的锥角。
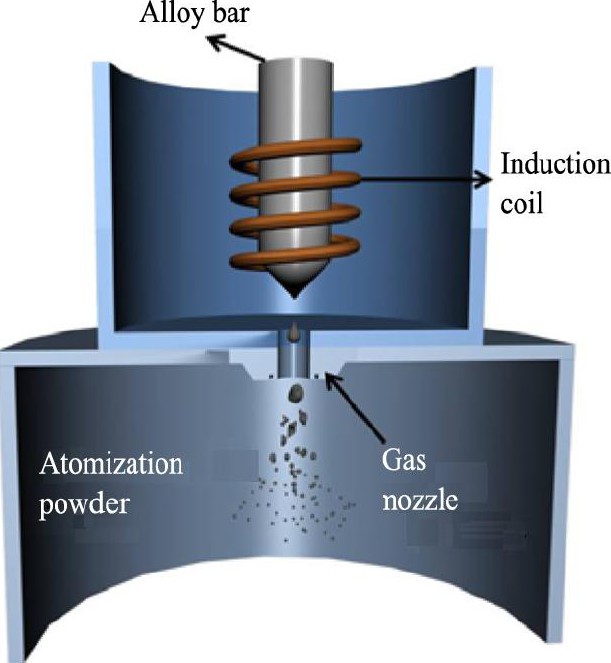
图1 无坩埚熔炼气雾化设备原理Fig.1 Schematic sketch of an gas atomization without crucible process
采用真空系统将熔炼室与雾化室抽真空至1×10-1Pa, 并充入氩气作为保护气体, 保护气体压强应与大气压保持一致或略大于大气压。启动供料装置和熔炼设备, 设定进料速度, 锆棒以一定的速度旋转进入感应线圈。启动雾化系统, 设定雾化压力, 当金属锆棒熔为液滴后, 金属液滴在自身重力和气流的拽拉作用下落入雾化室, 经由喷枪喷出的高速氩气破碎, 最终雾化为细小的金属粉末, 通过旋风分离器, 锆粉最终落入收粉罐。粉末完全冷却后, 打开收粉罐, 用塑料药勺转移锆粉。在锆粉的转移与处理过程中, 应尽量避免金属工具间的摩擦, 防止锆粉发生自燃和爆炸。
采用TCH-600氮氢氧分析仪检测粉末氮氢氧含量;Micro-plus激光衍射粒度分析仪分析粉末的粒径组成;Novatm Nano扫描电镜 (SEM) 观察粉末的球形度和表面形貌。在充有氩气保护气氛的手套箱中, 用标准筛网筛取25~74μm范围内的粉末。根据ISO-4490 (2014) 标准, 采用霍尔流速计测量粉末的流动性, 选用底部漏孔直径为5 mm的标准漏斗, 流动性以50 g粉末从标准漏斗流下的时间来表征。
2结果与讨论
2.1雾化机制
无坩埚熔炼气雾化过程与常规坩埚熔炼气雾化略有不同, 其在雾化过程中, 熔炼室与雾化室相连通, 易在导液孔附件形成紊流, 造成堵塞。因此在雾化过程中, 需不断向熔炼室充入适量氩气, 确保自熔炼室向雾化室的导向气流, 使得金属液滴顺利落入雾化室。
根据雾化过程的不同阶段, 可将无坩埚熔炼气雾化区域分为负压紊流区、雾化区和冷却凝固区, 其雾化机理如图2所示[18]。在导液孔的下方, 由于高速氩气的抽气作用, 形成负压紊流区。第一阶段, 在负压紊流区内, 金属液流在气流的波动下形成圆锥形液面, 并落入雾化区域。雾化第二阶段为在高速氩气的剪切力和气流振动的剧烈作用下, 液面被破碎为带状或不规则的颗粒状。第三阶段为冷却凝固, 带状液滴高速飞行的过程中, 在气流的波动和表面张力的共同作用下, 逐渐分裂为尺寸较小的棒状或哑铃状, 并进一步分裂为球形或近球形粉末。不规则小液滴在表面张力的作用下逐渐球化, 并冷凝为球形或近球形粉末。
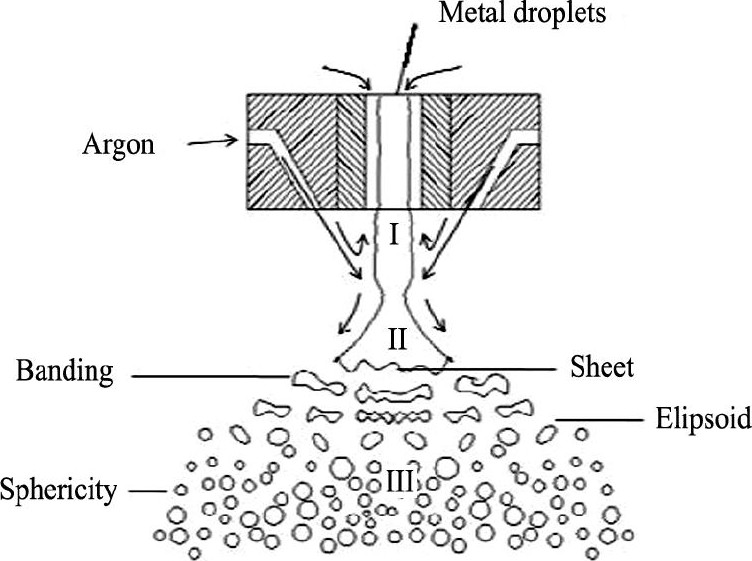
图2 无坩埚熔炼气雾化机制Fig.2 Process of gas atomization without crucible
I-Subatmospheric pressure zone;II-Atomization zone;III-Solidification cooling zone
2.2雾化工艺
影响雾化过程稳定性与粉末粒径分布的主要工艺参数为进料速度与雾化压力, 表1为不同工艺参数下细粉 (-325目) 收得率。随着进料速度和雾化压力的增加, 细粉收得率逐渐提高。在进料速度为45 mm·min-1, 雾化压力为5.0 MPa时, 细粉的收得率最高, 达到40.50%。
2.2.1进料速度对粉末粒径的影响
液滴熔化后从锆棒落入雾化区的时间t (s) 可由下式计算:

式中v为下落初速度 (mm·min-1) , 即等效于进料速度;a为下落加速度 (mm·min-2) ;H为从锆棒尖端到雾化区的距离 (mm) 。当增加进料速度v时, 可减少金属液滴的下落时间t, 液滴的热量损失减小, 提高了液滴雾化时的过热度。金属液滴的粘度会随着其温度的升高而减小, 在较高的过热度下粘度较小, 利于液滴的充分雾化, 细粉收得率提高。
表1 不同工艺下细粉的收得率Table 1 Yield of fine powder with different process parameters 下载原图
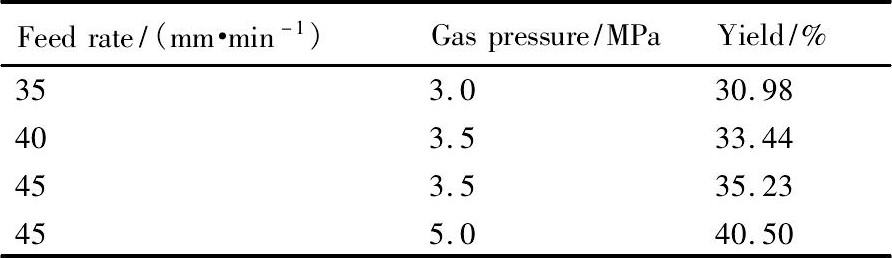
表1 不同工艺下细粉的收得率Table 1 Yield of fine powder with different process parameters
2.2.2雾化压力对粉末粒径的影响
在雾化过程中, 粉末粒径 (dm) 的经验公式[19]如下:

式中, K为常数, F为气体的消耗量 (m3·kg-1) 。当增大雾化压力时, 气体的耗量增加, 由经验公式可判断减小, 粉末粒径变细。
从能量的角度分析, 雾化过程中气体的动能一部分转化为粉末的表面能, 气体的动能 (E) 计算公式为:

式中, M为气体的质量 (kg) , Vg为雾化气体的速度 (m·s-1) 。提高雾化气体压力可提高喷枪出口处的气体速度, 增加气体动量, 更多的能量将转化为粉末的表面能, 从而减小粉末粒径。
2.3粉末表征
2.3.1氧氮氢含量
气雾化制备的锆粉与康建刚等[20]采用氢化还原法制备的锆粉氧氮氢含量如表2所示。气雾化锆粉的氧氮含量均明显低于采用氢化脱氢法制备的锆粉, 氧含量仅为氢化还原锆粉的1/11, 满足核纯级锆粉氧含量的要求 (氧含量<2500×10-6) 。氮含量为10×10-6, 仅为氢化还原锆粉的1/91。这是由于无坩埚熔炼气雾化过程简单, 无需球磨干燥等工艺, 可有效减少粉末与外界大气的接触, 因此其氧氮含量较低。且无坩埚熔炼气雾化过程中, 可避免常规坩埚熔炼气雾化过程中原料与坩埚和中间包的接触, 无其他杂质的引入, 采用该技术制备的粉末可与原料的纯度保持基本一致。
2.3.2粒度分布
在进料速度为45 mm·min-1, 雾化压力为5 MPa的最优工艺下制备的锆粉激光粒度分析结果如图3所示, 粉末粒径分布窄, 呈单峰分布。中位径Dv (50) 为60.7μm, Dv (10) 为22.2μm, Dv (90) 为121.0μm。粒径在10~53μm范围内的粉末, 可用于激光铺粉增材制造[21], 其收得率约为45%。可用于送粉增材制造的粉末 (粒径45~150μm) [22,23]占58%;符合核纯级锆粉粒径技术指标 (粒径<74μm) 的粉末占73%。
表2 锆粉氧氮氢含量Table 2 Element contents of Zr powder 下载原图

表2 锆粉氧氮氢含量Table 2 Element contents of Zr powder
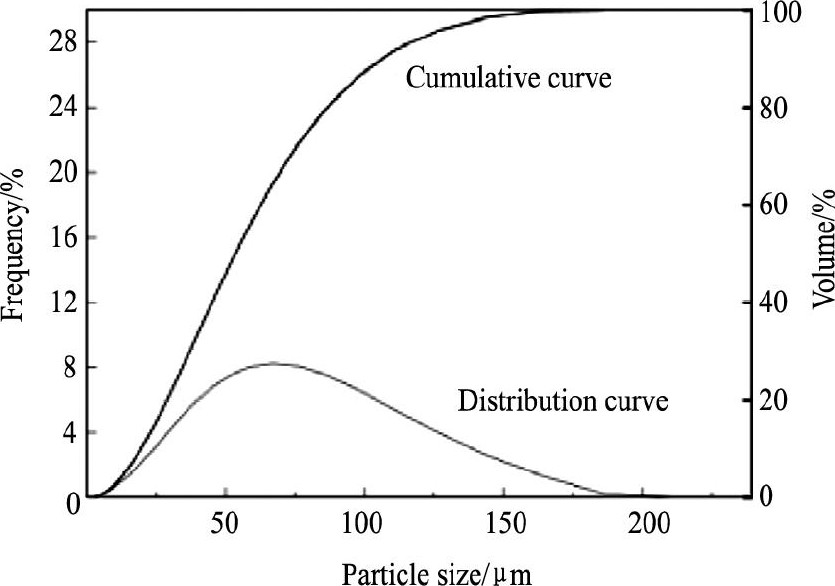
图3 气雾化锆粉粒径分布Fig.3Particle size distribution of Zr powder prepared by gas atomization
2.3.3粉末形貌
无坩埚熔炼气雾化技术制备的锆粉形貌如图4所示, 粉末多为球形或近球形, 表面光洁, 卫星粉数量较少。卫星粉是气雾化过程中普遍存在的现象, 是粉末在飞行过程中与尚未完全凝固的金属液滴相碰撞, 发生焊合, 形成卫星粉。在无坩埚熔炼气雾化过程中, 进料方式为间隔的金属液滴, 单位时间内雾化室的粉尘量较少, 因此采用该技术制备的锆粉卫星粉含量较低。图4 (d) 所示为哑铃状与棒状的不规则粉末, 是在雾化第三阶段时, 棒状或哑铃状液滴在表面张力的作用下球化速度低于其凝固速度造成。
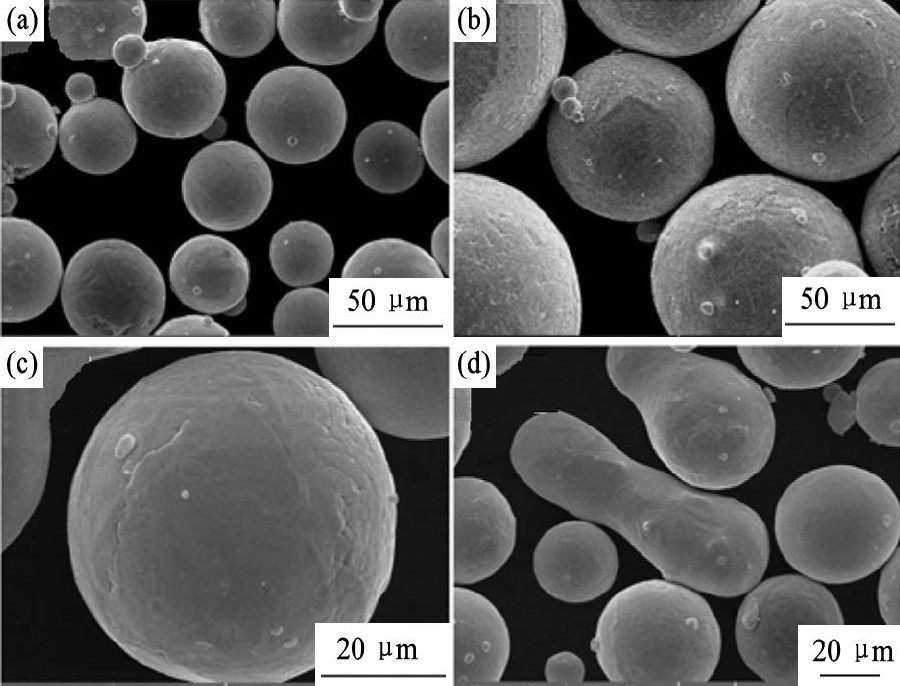
图4 气雾化锆粉形SEM图Fig.4 SEM images of Zr powder prepared by gas atomization (a) ~ (d) being different magnification
2.3.4流动性与松装密度
根据核纯级锆粉技术指标, 筛取74μm以下的粉末, 其无法自漏孔直径为5 mm的漏斗自由留下。为提高粉末流动性, 去除25μm以下的粉末, 其流动性与松装密度分别为3.89 s/50 g和3.36 g·cm-3, 流动性优于氢化还原法制备的粒径在44~74μm核纯级锆粉的流动性 (12.3 s/50 g) , 且优于氢化脱氢核锆粉的最优流动性 (10.5 s/50 g) [15]。这是由于氢化还原法制备的锆粉多棱角, 为不规则形状, 粉末间的搭接与摩擦严重。而采用无坩埚熔炼气雾化技术制备的锆粉为球形或近球形, 表面光洁, 粉末间搭接较少, 接触面积与摩擦力小, 具有优异的流动性。
3结论
1.本单位采用自主设计研发的无坩埚熔炼气雾化设备成功制备出高纯球形锆粉, 可实现粉末的高效智能生产。
2.锆粉的细粉收得率与雾化压力和进料速度成正比。在进料速度为45 mm·min-1, 雾化压力为5 MPa时, 细粉收得率可达40.50%。
3.采用无坩埚熔炼气雾化技术制备的锆粉氧氮含量低, 纯度高, 粒径分布窄, 具有优异的流动性和松装密度。
参考文献
[1] Yang F, Wei B L, Wang X F.Research advance and future direction of nuclear graded zirconium alloy[J].Metal World, 2016, (3) :24. (杨锋, 尉北玲, 王旭峰.核级锆合金研究现状及我国核级锆材发展方向[J].金属世界, 2016, (3) :24.)
[2] Lin Z H.Application of zirconium and its compounds[J].World Nonferrous Metal, 2011, (7) :68. (林振汉.锆及其化合物的应用[J].世界有色金属, 2011, (7) :68.)
[3] Xiong B K.The nuclear properties of zirconium and its application in the nuclear power industry[J].Rare Metals Letters, 2005, 24 (3) :43. (熊炳昆.锆的核性能及其在核电工业中的应用[J].稀有金属快报, 2005, 24 (3) :43.)
[4] Xiong B K.The application of metal zirconium in the field of ferrous metallurgy[J].Rare Metals Letters, 2005, 24 (7) :46. (熊炳昆.金属锆在黑色冶金领域中的应用[J].稀有金属快报, 2005, 24 (7) :46.)
[5] Sehra J C, Vijay P L, Gupta C K.Preparation of zirconium and hafnium metal powders using fused salt electrolysis[J].High Temperature Materials and Processes, 1995, 14:115.
[6] Doolan K R, Narang P P, Pope J M.Nuclear magnetic resonance study of hydrogen diffusion in zirconium and some of its alloys[J].Journal of Physics F:Metal Physics, 1980, 10 (9) :207.
[7] Xiong B K.Preparation and application of zirconium powder[J].Rare Metals Letters, 2005, 24 (10) :45. (熊炳昆.锆粉的制备与应用[J].稀有金属快报, 2005, 24 (10) :45.)
[8] Guo C F, Dong Y H.Progress in the preparation of metal zirconium[J].Rare Metals and Cemented Carbides, 2008, 36 (2) :63. (郭春芳, 董云会.金属锆制备方法的研究进展[J].稀有金属与硬质合金, 2008, 36 (2) :63.)
[9] Becker A J, Careatti D R.Continuous production of finely pided zirconium powder[P].US Patent:4285724, 1981.
[10] Wu Y K, Chen S, Xu Z G, Wang L J.Zirconiun powder prepared by fused salt electrolysis[J].Chinese Journal of Rare Metals, 2009, 33 (1) :62. (吴延科, 陈松, 徐志高, 王力军.熔盐电解法制备锆粉的研究[J].稀有金属, 2009, 33 (1) :62.)
[11] Zhang H, Shen H S, Che X K, Wang L J.Zirconium powder production through hydrogenation and dehydr ogenation process[J].Chinese Journal of Rare Metals, 2011, 35 (3) :417. (张恒, 沈化森, 车小奎, 王力军.氢化-脱氢法制备锆粉工艺研究[J].稀有金属, 2011, 35 (3) :417.)
[12] Sharma R A.Molten salt process for producing titanium or zirconium powder[P].US Patent:6117208, 2000.
[13] Inman D, White S H.The production of refractory metals by the electrolysis of molten salts;design factors and limitations[J].Journal of Applied Electrochemistry, 1978, 8 (5) :375.
[14] Mohandas K S, Fray D J.FFC Cambridge process and removal of oxygen from metal-oxygen systems by molten salt electrolysis:an overview[J].Trans.Indian Inst.Met., 2004, 57 (6) :579.
[15] Chen J G, Li C F, Sun C L, Liu L J, Wang L Q.Research on the improvement of the flow performance of the pure grade zirconium powder[A].2013 Meeting of Powder Metallurge in Chuan-Yu-Rong[C].Zigong, 2013.31. (陈建刚, 李传峰, 孙长龙, 刘利剑, 王录全.核纯级锆粉流动性能改进研究[A].2013年川渝蓉粉末冶金学术交流会论文集[C].自贡, 2013.31.)
[16] Antony L V M., Reddy R G.Processes for production of high-purity metal powders[J].JOM, 2003, 55 (3) :14.
[17] Hohmann M, Diemar W, Ludwig N, Zenker W R.Modern systems for ceramic-free powder production[J].Advances in Powder Metallurgy&Particulate Materials, 1992, 1:27.
[18] Huang P Y.Principle of Powder Metallurgy[M].Beijing:Metallurgical Industry Press, 1997.61. (黄培云.粉末冶金原理[M].北京:冶金工业出版社, 1997.61.)
[19] Alan Lawley.Atomization (the Production of Metal Powders) [M].New Jersey:Metal Powder Industries Federation, 1992.86.
[20] Kang J G, Jiang Y, He Y H, Gao H Y.Fabrication and properties characterization of Zr powder by hydrogenation dehydrogenation combined method[J].Materials Science and Engineering of Powder Metallurgy, 2015, 20 (4) :655. (康建刚, 江壵, 贺跃辉, 高海燕.氢化-脱氢法制备锆粉及其性能表征[J].粉末冶金材料科学与工程, 2015, 20 (4) :655.)
[21] Bremen S, Meiners W, Diatlov A.Selective laser melting[J].Laser Technik Journal, 2012, 9 (2) :33.
[22] Frazier W E.Metal additive manufacturing:a review[J].Journal of Materials Engineering and Performance, 2014, 23 (6) :1917.
[23] Santos E C, Shiomi M, Osakada K, Laoui T.Rapid manufacturing of metal components by laser forming[J].International Journal of Machine Tools and Manufacture, 2006, 46 (12) :1459.