Trans. Nonferrous Met. Soc. China 24(2014) 861-867
Reductive leaching of manganese oxide ores using waste tea as reductant in sulfuric acid solution
Qing TANG1,2, Hong ZHONG1,2, Shuai WANG1,2, Jin-zhong LI1,2, Guang-yi LIU1,2
1. School of Chemistry and Chemical Engineering, Central South University, Changsha 410083, China;
2. Key Laboratory of Resources Chemistry of Nonferrous Metals, Ministry of Education, Changsha 410083, China
Received 5 March 2013; accepted 29 June 2013
Abstract: Manganese oxide ores from Gabon and Xiangxi were leached with waste tea as reductant in dilute sulfuric acid solution. The effects of waste tea dosage, concentration of sulfuric acid, liquid-to-solid ratio, leaching temperature and reaction time on leaching process were explored. The leaching efficiency of Gabonese manganese oxide ore reached almost 100% under the optimal condition which was determined as follows: manganese oxide ore to waste tea mass ratio of 10:1, sulfuric acid concentration of 2.5 mol/L, liquid-to-solid ratio of 7.5:1, leaching temperature of 368 K, time of 8 h. The leaching efficiency of Xiangxi manganese oxide ore reached 99.8% under the optimal condition which was determined as follows: manganese oxide ore to waste tea mass ratio of 10:1, sulfuric acid concentration of 1.7 mol/L, liquid-to-solid ratio of 7.5:1, leaching temperature of 368 K, time of 8 h. The leaching process followed the internal diffusion controlled kinetic model, and the apparent activation energies of Gabonese manganese oxide ore and Xiangxi manganese oxide ore were calculated to be 38.2 kJ/mol and 20.4 kJ/mol, respectively. The morphological changes and mineralogical forms of the ore before and after the chemical treatment were discussed with the support of XRD analysis and SEM analysis.
Key words: manganese oxide ore; waste tea; reductant; leaching
1 Introduction
Manganese is an important industrial raw material, especially for the growing requirement of smelting steel. Manganese oxide ore is stable in acid or alkaline conditions so the extraction of manganese must be carried out under reducing conditions [1-3]. Recently, reductive leaching technology of manganese oxide ore develops rapidly. There are some advantages for hydrometallurgy of pyrolusite compared with pyrometallurgy, such as low power consumption, simple equipment requirement, and less environment pollution.
Many reductants have been applied to developing efficient and economical processes to recover manganese from manganese oxide ores, which include aqueous sulfur oxide [4], pyrite [5], iron(II) sulphate [6], iron metal [7], oxalic acid [8] and hydrogen peroxide [9]. There are a lot of reports about using biomass as reductant to leach manganese oxide ores, such as sawdust [10], cane molasses [11,12], molasses alcohol wastewater [13], cornstalk [14] and corncob [15]. It has been demonstrated that biomass is non-hazardous, and has good reactivity, availability and low cost and is used under mild conditions.
As we know, waste tea is a rich resource in China, and can be a renewable and non-hazardous biomass reductant. There are many reducing components in waste tea, such as polysaccharide, tea polyphenols, cellulose and organic acids, which could be hydrolyzed into release glucose in acid condition. Hence, the extraction rate of manganese should be improved significantly. Making use of waste tea to reduce manganese oxide ores can not only widen the channels of reductant, but also comply with the requirement of green economy.
The aim of this work is to develop a new leaching process for manganese oxide ore in the presence of waste tea as reductant in sulfuric acid solution. The effects of reductant concentration, concentration of sulfuric acid, liquid-to-solid(L/S) ratio, leaching temperature and reaction time on the processes are discussed [16-19]. The dynamics of the leaching process is also investigated [20,21].
2 Experimental
2.1 Materials
2.1.1 Manganese oxide ores
Two manganese oxide ores samples were obtained from Gabon and Xiangxi, respectively. The ores were crushed, ground and screened to provide raw material with particle size of 100% from 50 μm to 200 μm. The Gabonese ores sample used in the experiment contained 45.62% Mn, 2.75% Fe, 10.78% SiO2, 9.65% Al2O3. And the Chinese ores sample contained 20.34% Mn, 10.46% Fe, 37.22% SiO2, 8.38% Al2O3.
2.1.2 Waste tea
Waste tea obtained from Hunan province, China contained 4.0% polyphenols, 7.9% polysaccharide, 17.2% cellulose, 6.3% hemicellulose, 19.8% lignin and 22.2% moisture. Prior to the experiments, it was processed to be powder-like with a particle size of 80-150 μm.
2.2 Experimental procedure
Leaching experiments were carried out in a 250 mL three-neck flask fitted with a reflux condenser and kept over a mechanical stirring system and immersed in a thermostatically controlled water bath. In a typical experiment, the liquid-to-solid(L/S) ratio was fixed as 5:1 (mL/g). A sample of 10 g Gabonese manganese oxide ore and 4 g sieved (100mesh) waste tea were added to 50 mL aqueous sulfuric acid solution (2.5 mol/L) under stirring (400 r/min) at constant temperature for a certain period of time. The sample of 10 g Chinese manganese oxide ores and 1 g waste tea were added to 50 mL aqueous sulfuric acid solution (1.7 mol/L) under the same conditions. At the end of each leaching experiment, the slurry was filtered and manganese in the filtrate (leach liquor) was measured by spectrophotometry which was performed at 526 nm. As a result, the leaching recovery of manganese could be calculated.
3 Results and discussion
3.1 Effect of mass ratio of manganese oxide ores to waste tea on leaching process
A series of leaching experiments for Gabonese manganese oxide ore were carried out by varying the mass ratio of the ore to waste tea. The mass ratio of the ore to waste tea was varied from 10:1 to 10:5 while keeping the leaching condition: the initial H2SO4 concentration fixed at 2.5 mol/L, the L/S ratio of 5:1, the leaching temperature of 368 K and the extraction time of 8 h. The leaching experiments of Xiangxi manganese oxide ore were performed by varying the mass ratio of the ore to waste tea from 10:0.8 to 10:5 with H2SO4 concentration of 1.7 mol/L, L/S ratio of 5:1, leaching temperature of 368 K, time of 8 h. From the obtained data shown in Fig. 1, it is evident that as the waste tea amount increased, the leaching efficiency of manganese sharply increased, but it became slow with further increase to 10:4 at which above 97% recovery of manganese was obtained for Gabonese manganese oxide ore, while over 90% manganese was leached with further increase to 10:1 for Xiangxi manganese oxide ore, and the leaching efficiency reached over 99% when the mass ratio of manganese oxide ore to waste tea was 10:1.5. The amount of waste tea was dependent on the manganese content of ore, and it decreased with the decrease of Mn content.
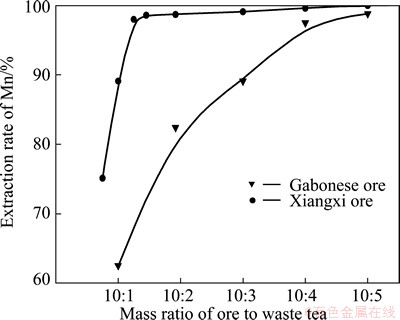
Fig. 1 Effect of mass ratio of ore to waste tea on extraction rate of Mn
3.2 Effect of sulfuric acid concentration on leaching process
The effect of sulfuric acid concentration was studied by varying sulfuric acid concentration from 1.0 mol/L to 3.0 mol/L while the other conditions were fixed at 368 K for 8 h and L/S ratio of 5:1 in the presence of 10:4 of mass ratio for Gabonese manganese oxide ore to waste tea and 10:1 for Chinese.
From the obtained results, it is shown that recovery of manganese sharply increased with an increase in the sulfuric acid concentration from 1.0 to 2.0 mol/L, but the leaching efficiency of manganese was slightly improved when the concentration was over 2.0 mol/L, as shown in Fig. 2. Increasing the sulfuric acid concentration from 1.0 to 2.0 mol/L, the leaching efficiency of Gabonese manganese oxide ore varies from 60.2% to 96.0% and that of Chinese manganese oxide ore from 86.5% to 98.7%. The reason could be concluded that the hydrolyzing degrees of polysaccharide and cellulose were improved rapidly with increasing the sulfuric acid concentration when the concentration was below 2.0 mol/L.

Fig. 2 Effect of sulfuric acid concentration on extraction rate of Mn
3.3 Effect of L/S ratio on leaching process
A series of experiments were conducted at different initial L/S ratios, ranging from 3:1 to 10:1 while keeping other conditions as the waste tea amount of 0.4 g/g (mass ratio of waste tea to ore) and sulfuric acid of 2.5 mol/L for Gabonese manganese oxide ore, the waste tea amount of 0.1 g/g and sulfuric acid of 1.7 mol/L for Xiangxi ore, stirring speed of 400 r/min, temperature of 368 K and leaching time of 8 h. The results demonstrated that the recovery efficiencies of manganese in the two manganese oxide ores were increased sharply with the increase of L/S ratio, and the extraction rate was almost 100% when the mass ratio was over 7.5, which indicated that leaching reaction nearly reached equilibrium, as shown in Fig. 3. The increase of L/S ratio could reduce the pulp viscosity so that the diffusion of leaching conditions would be modified and the leaching efficiency was improved. Therefore, the L/S ratio of 7.5:1 is sufficient for almost complete recovery of manganese.
3.4 Effect of leaching temperature and time on leaching process
The experiments were carried out at different temperatures ranging from 333 K to 368 K for different time ranging from 0 to 8 h under the conditions of waste tea 0.4 g/g, 2.5 mol/L sulfuric acid, 5:1 L/S ratio and 400 r/min stirring speed for Gabonese ore, while the conditions of Chinese were waste tea 0.1 g/g, 1.7 mol/L sulfuric acid, 7.5:1 L/S ratio and stirring speed 400 r/min. With the increase of leaching temperature and time, the leaching efficiencies of the two kinds of ores were improved, especially in the initial period of 0-5 h. With the leaching time of 8 h and the temperature of 368 K, the extraction rate of Gabonese ore reached 97.4% as presented in Fig. 4(a), and the extraction rate of Chinese ore reached 99.8% as presented in Fig. 4(b).
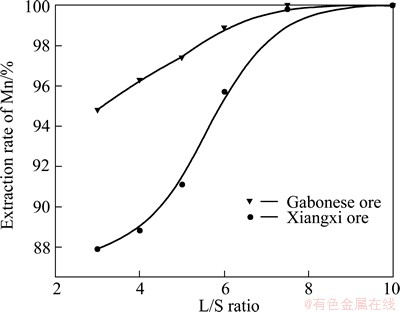
Fig. 3 Effect of L/S ratio on extraction rate of Mn

Fig. 4 Effect of temperature and time on extraction rate of Gabonese (a) and Xiangxi (b) manganese oxide ores
In order to obtain the kinetic equation and apparent activation energy of manganese dissolution in the presence of cellulose, the shrinking core models with internal diffusion controlled model and surface chemical reaction controlled model are correlated to rationalize these experiment data.
Surface chemical reaction controlled kinetic model can be expressed as follows:
1-(1-x)1/3=kt (1)
and internal diffusion controlled kinetic model can be expressed as follows:
1-2/3x-(1-x)2/3=kt (2)
where k is the apparent reaction rate constant (h-1), t is leaching time (h) and x is the leaching efficiency.
Surface chemical reaction controlled kinetic model was examined but did not fit the data well. However, internal diffusion controlled model is found to fit the data best with both the R2 over 0.96, as shown in Fig. 5.
The apparent activation energy is determined based on the Arrhenius equation:
(3)
where A is the frequency factor, Ea is the apparent activation energy and R is the mole gas constant.
A plot of ln k versus 1/T for the five temperatures is linear as shown in Fig. 6. The regression analysis indicates that liner relationships are all significant with R2 of 0.99 and 0.95. The apparent activation energy (Ea) of Gabonese ores is determined from the slope to be 38.2 kJ/mol and the other is 20.4 kJ/mol, which indicates that the leaching processes are controlled by diffusion through the insoluble layer of the associated minerals. This value clearly confirms that this process is controlled by internal diffusion.
In order to investigate the ore particle transformation during the leaching process, SEM and XRD studies were carried out. The results of XRD analysis (Fig. 7, Fig. 8) show that the sample of manganese oxide ores are mainly silicon oxide, Mn-complexes and some aluminosilicate, and Mn-complexes disappear after the leaching attack. The morphological changes of the ore particle before and after the chemical leaching by SEM (Fig. 9, Fig. 10) show that the surface of the unreacted manganese oxide ores is a little rough and porous, which can increase diffusion resistance of reactant and reduce reaction speed.
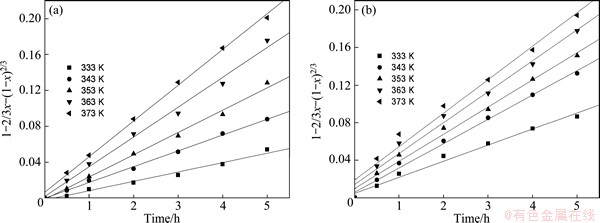
Fig. 5 Relationship between [1-2/3x-(1-x)2/3] and leaching time for manganese leaching at various temperatures for Gabonese (a) and Xiangxi (b) manganese oxide ores
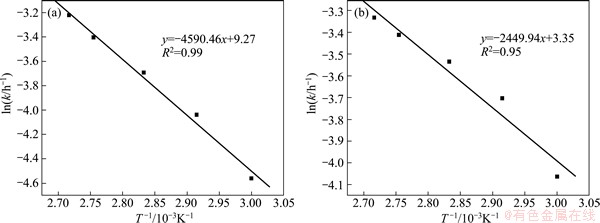
Fig. 6 Arrhenius plot for manganese leaching of Gabonese (a) and Chinese (b) manganese oxide ores
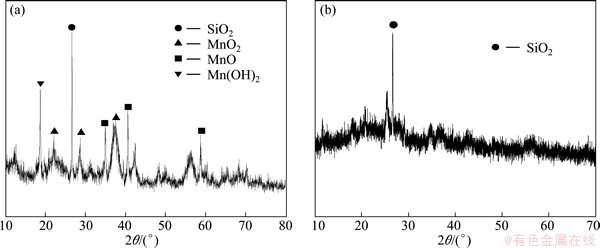
Fig. 7 XRD analysis of Gabonese manganese oxide ores before (a) and after (b) reductive leaching

Fig. 8 XRD analysis of Xiangxi manganese oxide ores before (a) and after (b) reductive leaching

Fig. 9 SEM images of Gabonese manganese oxide ore (a) and mineral slag (b)
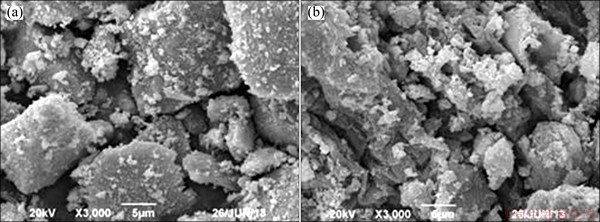
Fig. 10 SEM images of Xiangxi manganese oxide ore (a) and mineral slag (b)
4 Conclusions
1) The studied relevant leaching factors of Gabonese manganese oxide ore were optimized as the mass ratio of 10:4(ore to waste tea), 2.5 mol/L sulfuric acid, 368 K in a liquid-to-solid ratio of 7.5:1 for 8 h. Under these optimal conditions, the leaching efficiency of manganese can reach 100%. The optimum leaching conditions of Xiangxi manganese oxide ore are the mass ratio of 10:1(ore to waste tea), 1.7 mol/L sulfuric acid and liquid-to-solid ratio of 7.5:1 at 368 K for 8 h. Under these optimal conditions, the leaching efficiency of manganese can reach 99.8%.
2) The leaching processes are controlled by internal diffusion. The activation energies of Gabonese manganese oxide ore and Xiangxi manganese oxide ore are determined to be 38.2 kJ/mol and 20.4 kJ/mol, respectively.
3) XRD analyses show that waste tea gives significantly manganese extraction. SEM analyses show that the surface of the unreacted manganese oxide ores is a little rough and porous, which can reduce reaction speed.
References
[1] ABBRUZZESE C, DUARTE M Y, PAPONETTI B, TORO L. Biological and chemical processing of low-grade manganese ore [J]. Minerals Engineering, 1990, 3(3-4): 307-318.
[2] DAS S C , SAHOO P K, RAO P K. Extraction of manganese from low grade manganese ores by FeSO4 leaching [J]. Hydrometallurgy, 1982, 8: 35-47.
[3] SAHOO P K, RAO K S. Sulphating-roasting of low grade manganese ore: optimization by factorial design [J]. International Journal of Mineral Processing, 1989, 25(1-2): 147-152.
[4] NAIK P K, SUKLA L B, DAS S C. Aqueous SO2 leaching studies on Nishikhal manganese ore through factorial experiment [J]. Hydrometallurgy, 2000, 54: 217-228.
[5] KANUNGO S B. Rate process of the reduction leaching of manganese nodules in dilute HCl in presence of pyrite, Part I. Dissolution behavior of iron and sulphur species during leaching [J]. Hydrometallurgy, 1999, 52: 313-330.
[6] VU H, JANDOVA J, LISA K, VRANKA F. Leaching of manganese deep ocean nodules in FeSO4-H2SO4-H2O solutions [J]. Hydrometallurgy, 2005, 77: 147-153.
[7] BAFGHI M S, ZAKERI A, GHASEMI Z, ADELI M. Reductive dissolution of manganese ore in sulfuric acid in the presence of iron metal [J]. Hydrometallurgy, 2008, 90: 207-212.
[8] SAHOO R N, NAIK P K, DAS S C. Leaching of manganese from low-grade manganese ore using oxalic acid as reductant in sulphuric acid solution [J]. Hydrometallurgy, 2001, 62: 157-163.
[9] NAYL A A, ISMAIL I M, ALY H F. Recovery of pure MnSO4·H2O by reductive leaching of manganese from pyrolusite ore by sulfuric acid and hydrogen peroxide [J]. International Journal of Mineral Processing, 2011, 14: 116-123.
[10] HARIPRASAD D, DASH B, GHOSH M K, ANAND S. Leaching of manganese ores using sawdust as a reductant [J]. Minerals Engineering, 2007, 14: 1293-1295.
[11] SU H F, WEN Y X, WANG F, SUN Y Y, TONG Z F. Reductive leaching of manganese from low-grade manganese ore in H2SO4 using cane molasses as reductant [J]. Hydrometallurgy, 2008, 93: 136-139.
[12] LASHEEN T A, EL-HAZEK M N, HEIAL A S, EL-NAGAR W. Recovery of manganese using molasses as reductant in nitric acid solution [J]. International Journal of Mineral Processing, 2009, 92: 109-114.
[13] SU H F, WEN Y X, WANG F, SUN Y Y, TONG Z F. Leaching of pyrolusite using molasses agreen teaohol wastewater as a reductant [J]. Minerals Engineering, 2009, 22: 207-209.
[14] CHENG Z, ZHU G C, ZHAO Y. Study in reduction-roast leaching manganese from low-grade manganese oxide ores using cornstalk as reductant [J]. Hydrometallurgy, 2009, 96: 176-179.
[15] TIAN X K, WEN X X, YANG C, LIANG Y J, PI Z B, WANG Y X. Reductive leaching of manganese from low-grade manganese oxide ores using corncob as reductant in sulfuric acid solution [J]. Hydrometallurgy, 2010, 100: 157-160.
[16] GUO Xue-yi, SHI Wen-tang, LI Dong, TIAN Qing-hua. Leaching behavior of metals from limonitic laterite ore by high pressure acid leaching [J]. Transactions of Nonferrous Metals Society of China, 2011, 21: 191-195.
[17] TIAN Guo-cai, LI Jian, HUA Yi-xin. Application of ionic liquids in hydrometallurgy of nonferrous metals [J]. Transactions of Nonferrous Metals Society of China, 2010, 20: 513-520.
[18] GUO Zhao-hui, PAN Feng-kai, XIAO Xi-yuan, ZHANG Long, JIANG Kai-qi. Optimization of brine leaching of metals from hydrometallurgical residue [J]. Transactions of Nonferrous Metals Society of China, 2010, 20: 2000-2005.
[19] CHEN Xiang-yang, LAN Xin-zhe, ZHANG Qiu-li, MA Hong-zhou, ZHOU Jun. Leaching vanadium by high concentration sulfuric acid from stone coal [J]. Transactions of Nonferrous Metals Society of China, 2010, 20(s): s123-s126.
[20] XIAO Li, FANG Zheng, QIU Guan-zhou, WANG Shao-fen, WANG Chun-xiong. Mechanism of electro-generative-leaching of chalcopyrite-MnO2 in presence of Acidithiobacillus ferrooxidans [J]. Transactions of Nonferrous Metals Society of China, 2010, 20(s): s15-s20.
[21] BIAN Xue, YIN Shao-hua, LUO Yao, WU Wen-yuan. Leaching kinetics of bastnaesite concentrate in HCl solution [J]. Transactions of Nonferrous Metals Society of China, 2011, 21: 2306-2310.
以废茶叶为还原剂在硫酸溶液中还原浸出氧化锰矿
唐 清1,2,钟 宏1,2,王 帅1,2,李进中1,2,刘广义1,2
1. 中南大学 化学化工学院,长沙 410083;
2. 有色金属资源化学教育部重点实验室,长沙 410083
摘 要:采用废茶叶在硫酸溶液中还原浸出加蓬和湘西氧化锰矿石,探索废茶叶用量、硫酸浓度、固液比、浸出温度和反应时间对浸出过程的影响。对加蓬氧化锰矿,优化的浸出条件为:氧化锰矿与废茶叶的质量比10:4、硫酸浓度2.5 mol/L、固液比7.5:1、浸出温度368 K、浸出时间8 h;在此条件下,加蓬氧化锰矿的浸出率几乎达100%。对于湘西氧化锰矿,优化浸出条件为:氧化锰矿与废茶叶的质量比10:1、硫酸浓度1.7 mol/L、液固比7.5:1、温度368 K、浸出时间8 h;在此条件下,锰的浸出率达到99.8%。氧化锰矿的还原浸出过程符合内扩散控制模型,加蓬和湘西氧化锰矿石的还原浸出反应表观活化能分别为38.2 kJ/mol和20.4 kJ/mol。采用X-射线衍射(XRD)和扫描电子显微镜(SEM)对浸出前、后的锰渣进行表征。
关键词:氧化锰矿;废茶叶;还原剂;浸出
(Edited by Hua YANG)
Foundation item: Project (2010FJ1011) supported by the Major Project of Hunan Science and Technology, China; Project (cstc2012ggB90002) supported by the Chongqing Key Science and Technology Program, China
Corresponding author: Hong ZHONG; Tel/Fax: +86-731-88830654; E-mail: zhongh@csu.edu.cn
DOI: 10.1016/S1003-6326(14)63136-8