Trans. Nonferrous Met. Soc. China 27(2017) 1411-1416
Impurity distribution in distillate of terbium metal during vacuum distillation purification
Xiao-wei ZHANG, Rui-ying MIAO, Dao-gao WU, Qiong ZHU, Zhi-qiang WANG, De-hong CHEN, Shi-hong YAN
National Engineering Research Center for Rare Earth Materials, General Research Institute for Nonferrous Metals, Grirem Advanced Materials Co., Ltd., Beijing 100088, China
Received 17 June 2016; accepted 12 December 2016
Abstract: The distribution rules of impurities in distilled terbium metal were investigated by vacuum distillation purification experiment and theoretical analysis. It is found that Ti impurity in distilled terbium is 220 mg/kg in the initial stage of the distillation purification, increases slowly in the middle stage, and increases rapidly in the last stage, reaching 2260 mg/kg, and the modified separation coefficient of Ti is 1/19.02. The diffusion of the impurity Ti in liquid metal can reach a quasi-equilibrium state in the initial stage of distillation purification and the calculated results agree well with experimental results; the distribution profile of impurity Cu is opposite to Ti, being 380 mg/kg in the initial stage, decreasing linearly to 290 mg/kg in the last stage, and the modified separation coefficient is 17.99, and the theoretical calculated results are inconsistent with the experimental result.
Key words: vacuum distillation purification; modified separation coefficient; terbium metal; impurity distribution; liquid metal
1 Introduction
High purity metallic terbium is a key raw material for the preparation of higher-performance magnetostrictive material [1]. In general, vacuum distillation purification is an effective method to obtain high purity terbium metal. In this process, metallic terbium atoms evaporate and condense on the cooled collector, and the impurities, with lower saturated vapor pressure, can be separated and the matrix metal can be purified.
In the vacuum distillation purification field, most previous studies discussed the preparation of high purity rare earth metals [2,3], measurement of distillation velocity [4], and influence of experimental conditions on purification effect [5]. A few reports used the separation coefficient to estimate whether impurities can be separated from the matrix metal. XI and YU [6] found that impurities with a separation coefficient βi>1 (defined as βi=γi
/(γm
), where γi and γm are activity coefficients of the impurity and matrix metal, and
and
are saturated vapor pressures of impurity and matrix metal, respectively) can be evaporated preferentially, the impurities with βi<1 will be remained mostly in the crucible, and the impurities with βi≈1 cannot be separated. LI and LIU [7,8] considered that βi cannot be calculated accurately using the defined formula due to the lack of a value for the activity coefficient of the impurity, but it can be obtained by experimental measurements that Al, Cu, Cr, and Co impurities presented a negative deviation in liquid scandium, and Ni and Si presented a positive deviation. PANG et al [9] calculated the volatile quantity of impurities in metallic neodymium theoretically; the calculated result agreed with experimental results for the impurities with βi<1, but there was a large error for impurities with βi>1. ZAIOUR et al [10] discussed the behaviour of impurities in the distillation process and noted that the removal efficiency of submicron major impurities in tellurium can be characterized by studying the effective separation coefficient α, which is affected by both the evaporation rate and particle size. KONG et al [11-14] used molecular interaction volume model to calculate the activities of components of Pb-Sn-Sb ternary alloy system, Sn-based binary system and Sn-Zn system in vacuum distillation. The above research works are all focused on the separation coefficient to evaluate whether impurities can be removed, however, the removal rate of the impurities and the distribution of impurities in distilled metal have not been studied.
In the present study, a vacuum distillation purification experiment using terbium metal was carried out. The mass fractions of impurities were measured by inductively coupled plasma atomic emission spectrometry (ICP-AES), and the impurities distribution in distilled metal was studied. A modified separation coefficient was proposed, and a theoretical analysis of impurity distribution based on the solute redistribution at solid/liquid interface during solidification was discussed.
2 Experimental
The self-preparation metallic terbium was used in the present experiment. The total amount of metal was about 5 kg, and the purity of terbium was above 99.6% with detailed assays as shown in Table 1.
Table 1 Mass fraction of impurities in metallic terbium (mg/kg)
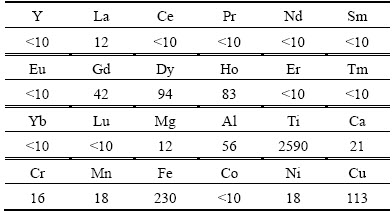
The schematic of distillation equipment is shown in Fig. 1. The metallic terbium was placed into a tungsten crucible (115 mm in external diameter, 95 mm in inner diameter and 225 mm in height), and a soaking temperature of 1850 °C was maintained for 30 h under a pressure of 10-5 Pa, and the temperature of crucible was measured by an infrared radiation thermometer (RATMR1SBSF, Reytek, USA) through the sight hole in the furnace, as seen in Fig. 1(a). Metallic vapor condenses on the inner surface of a cooled collector (tantalum sheet, with thickness of 0.1 mm), leaving high melting point and low vapour pressure impurities at the bottom of the crucible, where H is the thickness of the distilled metal (equal to 55 mm in the present experiment), while r and z are the cylindrical coordinates.
3 Results
When the distillation experiment was finished, five samples were taken successively along the axial line in the distilled metal and the mass fractions of impurities determined are plotted in Fig. 2. For Ti, in the initial stage of the distillation experiment (Sample 1 in Fig. 1(b)), the mass fraction of Ti in the distilled metal is 220 mg/kg. As the distillation process continues, the mass fraction of Ti increases to 336, 560, 1245 mg/kg, and in the last stage of distillation, the mass fraction of Ti increases to 2260 mg/kg. It was found that in the initial stage, the impurity mass fraction is low, increases slowly, and in the last stage of the experiment, the impurity mass fraction increases rapidly, and the mass fraction of Ti in distilled metal increases exponentialy. For Cu impurity, the mass fraction profile is quite different from Ti, as it decreases linearly during the distillation process. In the initial distillation stage, the mass fraction of Cu is 380 mg/kg, gradually decreasing to 350 mg/kg, 330 mg/kg, 314 mg/kg, and in the last stage of distillation, the mass fraction of Cu decreases to 290 mg/kg, as seen in Fig. 2(b).
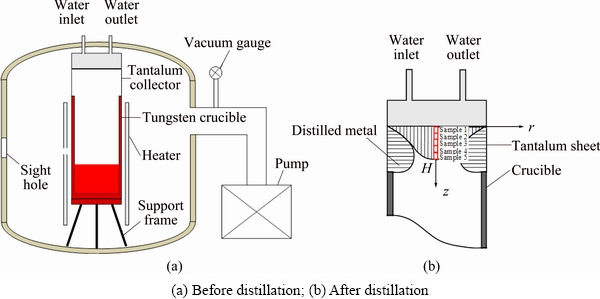
Fig. 1 Schematic of distillation equipment for metallic terbium
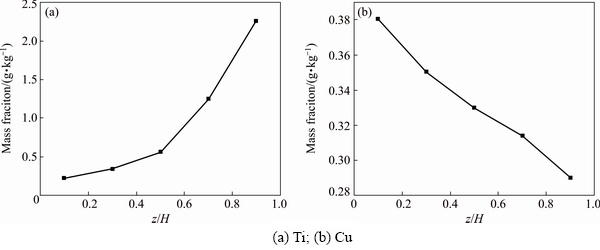
Fig. 2 Mass fractions of impurities in distilled terbium
4 Theoretical analysis and discussion
During the solidification process, metal is transformed from liquid to solid state, and in distillation purification process, metal is transformed from liquid via gas to solid state. There is no mass accumulation or loss in metallic vapor. The metallic vapor transforms to solid metal completely, so that the distillation purification process is coincident with that of the solidification. In the solidification process, the solute with an equilibrium partition coefficient (represented by k) of <1 will have a mass fraction in the solid metal that will be less than that in the liquid metal [15]. In the distillation purification process, if the distillation velocity of an impurity is smaller than that of the matrix metal, the impurity mass fraction in the distilled metal will be less than that in the liquid metal, so the impurity will be separated from the matrix metal, which will be purified. Therefore, the solidification theory can be used in a distillation purification field to discuss the behaviour of the impurity.
In order to describe the separation degree of an impurity to the matrix metal, a modified separation coefficient is introduced, which is the dimensionless ratio of distillation velocity of the impurity element (pure metal) to the matrix metal, and is defined as
(1)
where
and
are vapor pressures of impurity and matrix metal respectively (Pa) and Mi and Mm are the atomic mass of impurity and matrix metal, respectively. In Eq. (1), Ei and Em are the distillation velocities of impurity and matrix metals respectively (g/(cm2·s)) defined as
(2)
where p is vapor pressure (Pa), M is atomic mass, and T is temperature (K). In the present experiment, the modified separation coefficients of impurities of Ti and Cu in metallic terbium are 1/19.02 and 17.99, respectively [16].
If the modified separation coefficient β′<1, then the distillation velocity of matrix metal is greater than the impurity element and the mass fraction of impurity in the distilled metal will be less than that on the evaporating surface and equal to β′C0, where C0 is the mass fraction of the impurity on the evaporating surface. The remaining impurity atoms can accumulate on the evaporating surface so that the mass fraction of such impurity will increase gradually throughout the whole purification run. At the same time, a mass fraction gradient is formed on the evaporating surface and impurity atoms will tend to diffuse into the liquid metal. If the solute in the liquid metal is homogeneous, the mass fraction in the distilled metal can be described as follows:
(3)
The mass fraction of impurity in the distilled metal calculated by Eq. (3) is shown in Fig. 3 for various values of β′<1. In the initial stage of the distillation, the mass fraction of impurity in the distilled metal is lower and increases slowly, but in the later stages of the distillation, the mass fraction of the impurity increases rapidly and the matrix metal is purified. With the modified separation coefficient increasing, the mass fraction of impurity in the distilled metal increases gradually, and the mass fraction curve slope also presents an increasing tendency; it means that the impurity can be separated effectively in distillation purification operations, and the impurity mass fraction is much lower in the distilled metal condensed in the initial and middle stages of distillation purification. Compared with Ti in distilled terbium, as seen in Fig. 2(a), the mass fraction curves present a similar tendency.
Figure 4 compares the dimensionless mass fraction of Ti in distilled metal between experimental and calculated result. As seen in Fig. 4, the calculated mass fraction agrees well with experimental results in the early stage of the distillation experiment, but in the latter stage the calculated result is lower than the experimental result.
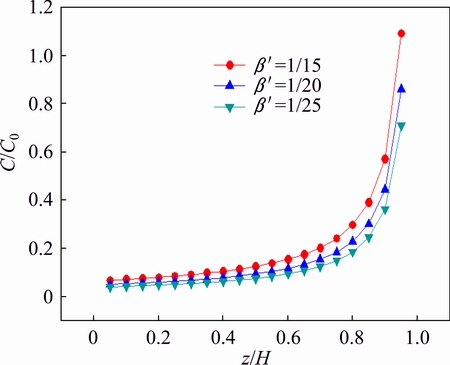
Fig. 3 Distribution of impurity in distilled metal with β′<1
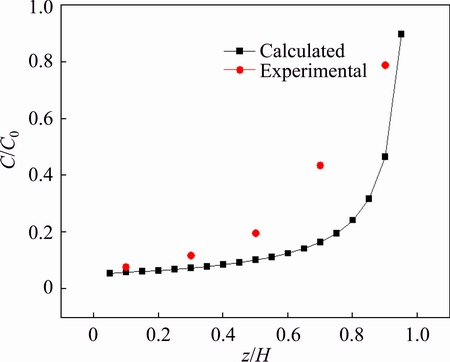
Fig. 4 Comparison of dimensionless mass fraction of Ti between experimental and calculated values
Vacuum distillation purification is a high temperature and multi-phase process in which an influential factor on the impurity distribution in the distilled metal is temperature. In our experiments, the crucible holding the distilling sample is placed on a tripod and part of the heat energy is dissipated to the inner wall of the furnace and the temperature of the liquid metal can drop during the experiment. The temperature drop increases gradually as the depth of the liquid metal decreases leading to the following consequences: 1) a decrease in the modified separation coefficient, as seen in Fig. 5, 2) decrease of diffusion coefficient of impurities in the liquid metal, and 3) an increase in viscosity of liquid metal. The decreasing modified separation coefficient is beneficial (improving purification effect) but the other consequences will decrease the diffusion velocity of impurity atoms, and the impurity diffusion cannot reach an equilibrium state or a quasi-equilibrium state. A mass fraction boundary layer can be formed near the evaporating surface, and it results in experimental results larger than the calculated results.
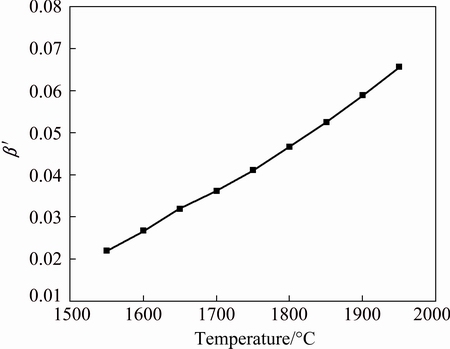
Fig. 5 Modified separation coefficient of Ti with matrix metal of terbium
The other influential factor is the impurity activity coefficient. Because the elemental electro-negativity values of Tb and Ti are equal to 1.2 and 1.5, respectively, there is an inter-atomic force between the impurity atom and matrix metallic atom. The activity coefficient will be less than 1 and so the calculated result will be less than the experimental result.
It is concluded that, in the early stage of the distillation process, impurity diffusion in liquid metal can reach a quasi-equilibrium state, the impurity is almost homogeneous, and the mass fraction of impurity in distilled metal can be described by Eq. (3). In the later stage of the process, the impurity diffusion rate decreases greatly due to the decreasing temperature, and the impurity mass fraction on the evaporating surface is larger than that in the liquid metal. Consequently, the mass fraction in the distilled metal is larger than the calculated result.
When the modified separation coefficient β′>1, the impurity mass fraction in the distilled metal calculated by Eq. (3) is shown in Fig. 6. In the initial stage of the distillation purification process, the mass fraction of impurity in the distilled metal is very high but decreases sharply and when z/H is about 0.4, the impurity mass fraction decreases to zero.
Figure 7 compares the experimental and calculated dimensionless impurity mass fractions of Cu in distilled metal. The calculated result indicates that the impurity mass fraction decreases sharply in the initial stage, and then decreases to about zero. The experimental result shows that the impurity mass fraction has a simple linear relation to the dimensionless height of z/H, quite different from the calculated result.
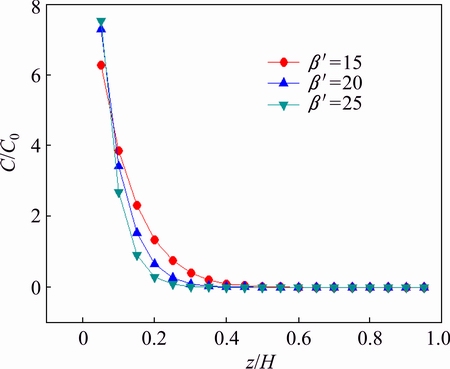
Fig. 6 Distribution of impurity in distilled metal with β′>1

Fig. 7 Comparison of dimensionless mass fraction of impurity Cu between experimental and calculated results
In the theoretical calculation of the impurity mass fraction, the impurity mass fraction in the evaporating surface is calculated by C0/k, meaning that the content of impurity Cu is 18.0C0 in the initial distillation stage and a large mass fraction boundary is needed in the vicinity of the evaporating surface. Obviously, the above mass fraction boundary is not formed spontaneously; consequently, the solidification theory cannot describe the mass fraction distribution in the distilled metal when the modified separation coefficient is larger than 1.
The main reason Cu distributes in distilled terbium is that the saturated vapor pressure of Cu is higher than that of terbium. As such, Cu will have a preference to evaporate, which is equivalent to the condition of a relative increase in the Cu mass fraction in the metallic vapor, and terbium atoms will accumulate on the evaporating surface. However, metallic terbium is the solute (>99%), and the mass fraction of terbium increases only slightly, so that the mass fraction of Cu in distilled metal is only slightly higher than that in the liquid metal. After the volatilization of a Cu atom on the evaporating surface, a mass fraction boundary is formed, and Cu atoms in the liquid metal will diffuse to the evaporating surface. As the experiment proceeds, Cu atoms are continuously consumed and the mass fraction of Cu on the evaporating surface decreases gradually, so that the mass fraction of Cu in distilled metal also presents a gradually decreasing trend.
5 Conclusions
1) During the distillation purification of metallic terbium, the mass fraction of impurity Ti in the distilled metal is lower in the initial stage, increases slowly in the middle stage, and increases rapidly in the last stage.
2) A modified separation coefficient has been proposed. The modified separation coefficient of impurity Ti is 1/19.02, and impurities with modified separation coefficients less than 1 can be removed during distillation purification. In the early stages of distillation purification, the impurity diffusion in the liquid metal can reach a quasi-equilibrium state, and the calculated result of impurity mass fraction in the distilled metal agrees well with experimental data. In the later stages, the impurity diffusion rate in the liquid metal decreases, and the impurity mass fraction in the distilled metal is larger than the calculated result.
3) Impurity Cu in the distilled metal decreases linearly in experiments. As such, the theoretical calculated results for impurities with modified separation coefficients larger than 1 are inconsistent with the experimental results.
References
[1] WANG Bo-wen, LI Shu-ying, YAN Rong-ge, CAO Shu-ying, WENG Ling. Magnetostrictive properties of epoxy bonded Tb-Dy-Fe composites [J]. Journal of the Chinese Rare Earths Society, 2003, 21(6): 729-732. (in Chinese)
[2] LI Zong-an, ZHANG Wei, XU Jing, ZHAO Bin, XIAO Feng, ZHANG Yao. Study on the preparing process of high purity terbium metal [J]. Chinese Rare Earths, 2002, 23(6): 36-39. (in Chinese).
[3] ZHANG Zhi-qi, WANG Zhi-qiang, CHEN De-hong, MIAO Rui-ying, ZHU Qiong, ZHANG Xiao-wei, ZHOU Lin, LI Zong-an. Purification of praseodymium to 4N5+ purity [J]. Vacuum, 2014, 102: 67-71.
[4] JIANG Yin-ju, HAO Zhan-zhong, DAI Qing, YANG Jia-yong, ZHANG Xiao-qin, QIU Dong-mei. Measurement and theoretical computation of the distillation rate of metallic terbium [J]. Chinese Rare Earths, 1999, 20(6): 11-13. (in Chinese).
[5] JIANG Yin-ju, HAO Zhan-zhong, ZHANG Xiao-qin, DAI Qing. Discussion on the factors affecting purification of rare earth metals by vacuum distillation [J]. Chinese Rare Earths, 2003, 24(4): 60-63. (in Chinese).
[6] XI Bin, YU Li-ping. The impure behavior of terbium in the distillation process [J]. Jiangxi Metallurgy, 2001, 21(1): 27-28. (in Chinese).
[7] LI Guo-dong, LIU Yong-lin. The study on the new technology and purification mechanism in the preparation high purity scandium metal [J]. Acta Scientiarum Naturalium Universitatis Neimongol, 1997, 28(5): 614-618. (in Chinese).
[8] LI Guo-dong, LIU Yong-lin. Study on technology and optimization of purifying scandium metal by vacuum distillation method [J]. Journal of the Chinese Rare Earths Society, 2000, 18(2): 183-186. (in Chinese).
[9] PANG Si-ming, CHEN De-hong, LI Zong-an, YAN Shi-hong, ZHOU Lin, XU Li-hai, WANG Zhi-qiang, XU Jian-lin. Theory and technology of vacuum distillation method for preparing high-purity metal neodymium [J]. Journal of the Chinese Society of Rare Earths, 2013, 31(1): 14-19. (in Chinese).
[10] ZAIOUR A, ZAHRAMAN K, ROUMIE M, CHARARA J, FAWAZ A, LMAI F, HAGE-ALI M. Purification of tellurium to nearly 7N purity [J]. Materials Science and Engineering B, 2006, 131(1-3): 54-61.
[11] KONG Ling-xin, YANG Bin, XU Bao-qiang, LI Yi-fu, LIU Da-chun, DAI Yong-nian. Application of MIVM for Pb-Sn-Sb ternary system in vacuum distillation [J]. Vacuum, 2014, 101: 324-327.
[12] KONG Ling-xin, YANG Bin, XU Bao-qiang, LI Yi-fu. Application of molecular interaction volume model for phase equilibrium of Sn-based binary system in vacuum distillation [J]. Metallurgical and Materials Transactions A: Physical Metallurgy and Materials Science, 2014, 45(10): 4405-4410.
[13] YANG Bin, KONG Ling-xin, XU Bao-qiang, LIU Da-chun, DAI Yong-nian. Recycling of metals from waste Sn-based alloys by vacuum separation [J]. Transactions of Nonferrous Metals Society of China, 2015, 25(4): 1315-1324.
[14] KONG Ling-xin, YANG Bin, XU Bao-qiang, Li Yi-fu, HU Yuan-shou, LIU Da-chun. Application of MIVM for Sn-Zn system in vacuum distillation[J]. Metallurgical and Materials Transactions A: Physical Metallurgy and Materials Science, 2014, 46(3): 1205-1213.
[15] GLICKSMAN M E. Principles of Solidification [M]. New York: Springer, 2011.
[16] LIDE D R. CRC handbook of chemistry and physics [M]. 90th ed. Florida, Boca Raton: CRC Press, 2010.
杂质在真空蒸馏产物铽中的分布
张小伟,苗睿瑛,吴道高,朱 琼,王志强,陈德宏,颜世宏
北京有色金属研究总院 稀土材料国家工程研究中心,有研稀土新材料股份有限公司,北京 100088
摘 要:通过真空蒸馏实验和理论分析研究了杂质在蒸馏产物金属铽中的分布规律。研究结果表明:在蒸馏产物中,钛杂质在蒸馏初期的含量为220 mg/kg,在蒸馏中期杂质含量缓慢增加,到了蒸馏提纯末期,杂质含量高达2260 mg/kg,钛的修正分离系数为1/19.02,在蒸馏初始阶段,钛原子在液态金属中的扩散达到准稳态,且理论计算结果与实验结束相吻合;铜杂质的在蒸馏产物中的分布与钛相反,在蒸馏初始阶段铜含量为380 mg/kg,到了蒸馏提纯末期,铜含量线性降至290 mg/kg,其修正分离系数为17.99,理论计算结果与实验结果不一致。
关键词:真空蒸馏提纯;修正分配系数;金属铽;杂质;液态金属
(Edited by Yun-bin HE)
Foundation item: Project (51504036) supported by the National Natural Science Foundation of China; Project (2012CBA01207) supported by the National Basic Research Program of China; Project (2011AA03A409) supported by the National High-Tech Research and Development Program of China
Corresponding author: Xiao-wei ZHANG; Tel: +86-10-89583403; Fax: +86-10-89583401; E-mail: 04202095@163.com
DOI: 10.1016/S1003-6326(17)60162-6