
Preparation of ultrafine nickel powder by wet chemical process
CHEN Rui-ying(陈瑞英), ZHOU Kang-gen(周康根)
School of Metallurgical Science and Engineering, Central South University, Changsha 410083, China
Received 11 October 2005; accepted 23 February 2006
Abstract: The main technical problems of nickel powder for multiplayer ceramic capacitors are particle size controlling, the agglomeration and tap density. Ultrafine nickel powders with submicron size and spherical shape were synthesized by the hydrazine reduction of nickel sulfate in ethanol-water solvent. The effects of reaction temperature, nucleator and flow rate of nickel sulfate solution on nickel powders properties were investigated. The nickel particles synthesized were characterized by SEM and TGA. The results show that the average particle size changes from 0.1 to 0.7 ?m by adjusting reaction temperature (53-73 ℃) and flow rate of nickel sulfate solution (50-100 mL/min). Moreover, temperature below 60 ℃ and appropriate flow rate of nickel sulfate solution (85 mL/min) are in favor of obtaining particles with high tap density (>3.0 g/cm3). In addition, the introduction of nucleator is useful to obtaining particles with narrow size distribution.
Key words: ultrafine nickel powder; chemical reduction; tap density; multiplayer ceramic capacitor
1 Introduction
Driven towards smaller size, higher capacitance and lower cost, the manufacturing techniques of multilayer ceramic capacitors(MLCCs) are now undergoing a revolution characterized by the development of MLCCs with base metal internal electrode(BME) and thinner dielectric layers[1]. Nickel powders are seen as a more economical alternative to the conventional precious metal powders for MLCC internal electrode, owing to their good electrical conductivity, high melting point and low cost[2-4]. Preparation of nickel powders with small average particle size, narrow particle size distribution, spherical particle morphology, reduced agglomeration of particles and high tap density has been one of the key technologies for the manufacture of MLCCs.
Preparation of ultrafine nickel powders has attracted a great deal of attention over the past decades due to their broad applications in conductive paste, battery materials, catalysis materials, magnetic materials, etc[5-8]. Up to now, various methods have been reported to synthesize ultrafine nickel powders, such as ball milling, electrodeposition, decomposition of Ni(CO)4, chemical vapor deposition(CVD) and wet chemical process[9-14]. However, it is difficult to obtain the ultrafine nickel
powders with the properties suitable for MLCCs by most of these methods. Among them, wet chemical process is considered one of the most suitable methods to obtain nickel powders for MLCCs because it is easy to operate and to control the shape, the size distribution and morphology of powders. However, though many researchers have studied the preparation of nickel powders for MLCC by wet chemical processes, problems like particle size controlling, the agglomeration and tap density are still not dissolved.
In this work, the preparation of nickel was investigated by the hydrazine reduction of nickel sulfate in ethanol-water solvent. It has been found that the combination of a nucleator and a complexing agent is very effective for settling the problem of agglomeration and for obtaining nickel particles with high tap density and narrow size distribution. The effects of reaction temperature, amount of the nucleator and flow rate of nickel sulfate solution on the particle size, size distribution and morphology of nickel powders are investigated.
2 Experimental
2.1 Materials
All agents including NiSO4·6H2O, N2H4·H2O, NaOH, ethanol and acetone were analytically pure. The nucleator A is a metallic ions with a reduction potential more positive than nickel. The complexing agent B is an organic acid having suitable stability constant with nickel.
2.2 Experiment
2.2.1 Powder preparation
In all experiments, the solvent was ethanol-water mixture prepared by diluting 400 mL ethanol to 1 000 mL with water. The nickel sulfate solution was prepared by adding NiSO4·6H2O, the complexing agent B and nucleator A into the ethanol-water solvent. The reducing agent solution was prepared by adding N2H4·H2O and NaOH to ethanol- water solvent. In all experiments, the concentrations of agents in the nickel sulfate solution were fixed at NiSO4 0.4 mol/L and the complexing agent B 0.12 mol/L. The concentrations of agents in the reduc- ing agent solution were fixed at N2H4·H2O 0.64 mol/L and NaOH 1.5 mol/L.
The experimental procedure is as follows: 500 mL of the nickel sulfate solution and 500 mL of the reducing agent solution were heated respectively to a given temperature in a water bath. Whereafter, the nickel sulfate solution was added with a given flow rate to the reducing agent solution under agitating condition (the stirring rate 300 r/min). After nickel ion was completely reduced, the nickel powder was separated from the solution by centrifugal separation, and washed with distilled water followed by ethanol and acetone. The powder was finally dried in a vacuum dry oven at 40 ℃. Gray-black nickel powder was obtained.
2.2.2 Powder characterization
The powder morphology was characterized by a scanning electron microscopy(SEM). And the particle size distribution was measured by an image analysis software (Smile View). The thermal and oxidation behaviors of the powder were characterized by the thermogravimetry analysis(TGA) in atmosphere at a heating rate of 10 ℃/min. Tap density was determined by pouring the powder into a graduated cylinder (about 5 cm3), weighing, and then vibrating to obtain the maximum volume change and hence, the highest apparent density.
3 Results and discussion
3.1 Effect of reaction temperature
To find the effect of reaction temperature for the preparation of nickel powders, the chemical reduction was performed at various temperatures including 53, 58, 63, 68 and 73 ℃ under the following conditions: the flow rate of the NiSO4 solution 73 mL/min and the molar ratio of A-to-Ni 0.002.
Fig.1 shows SEM micrographs of samples obtained at 53, 58, 63, 68 and 73 ℃. From the SEM results, the particles in all of samples are spherical in shape and not agglomerated. In the sample of 53 ℃, the particle size distribution is broad and surfaces are rough. While in the samples of higher temperature (58, 63, 68 ℃), the particle size distributions are more narrow and the surfaces are smoother. But when reaction temperature reaches 73 ℃, the particle size distribution turns broad again.
Fig.2 shows the average particle size and tap density of the samples obtained at different reaction temperatures. The average particle size of the samples is about 0.57 ?m at 53 ℃, 0.24 ?m at 58 ℃, 0.20 ?m at 63 ℃, 0.12 ?m at 68 ℃ and 0.22 ?m at 73 ℃. It is indicated that the average particle size decreases first and then increases with increasing temperature. Tap density is affected by size, size distribution and morphology of particles[15, 16]. Samples of 58 ℃ and 73 ℃ have similar average particle size, but the sample obtained at 58 ℃ has relatively high tap density. The reason is considered to be that the surface morphology of sample obtained at a lower temperature is much smoother and more regular as shown in Fig.1.
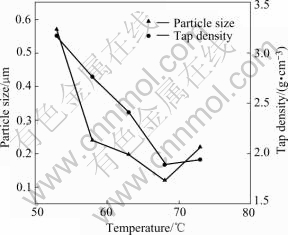
Fig.2 Average particle size and tap density of samples obtained at different reaction temperatures
3.2 Effects of nucleator A
The effects of nucleator are investigated in the range of molar ratio of A-to-Ni from 0 to 0.004 under the following conditions: the flow rate of the NiSO4 solution 70 mL/min and the temperature 63 ℃. The addition of nucleator A is very important to the acceleration of the reaction rate. When there is no nucleator in the NiSO4 solution, the reduction of nickel ion is quite slow and only a few black particles are deposited on the wall of the reactor in the initial stage of reaction. After nucleator A is added into the NiSO4 solution, a large amount of nuclei can be rapidly formed since nucleator A can be reduced more easily than that with nickel ion as nuclei.
Table 1 lists the effects of the molar ratio of A-to-Ni on the size of nickel particles. It is indicated that the molar ratio affects the size of nickel particles, but the effect is not obvious. Fig.3 shows the particle size distributions of the nickel particles obtained at the condition with and without the addition of nucleator A. It is found that the addition of nucleator A is in favor of obtaining particles with more narrow size distribution.
Table 1 Effect of nucleator A on size of nickel particles
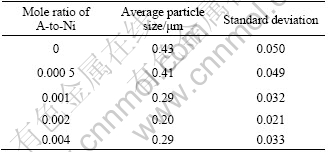
3.3 Effects of flow rate of nickel sulfate solution
The effects of the flow rate of nickel sulfate solution are investigated in the range of the flow rate of 50-100 mL/min under the following conditions: the molar ratio of A-to-Ni 0.002 and the temperature 53 ℃. The effects of the flow rate of nickel sulfate solution on particle size may start at lower nickel ion concentration and fewer nuclei are formed in the early period of the reduction. Along the reaction, the nickel is reduced and grows on the surface of nuclei, however the total amount of solute in the system is the same, and fewer nuclei may form larger nickel particles. While, with increasing the flow rate of nickel sulfate solution, the tap density increases first and then decreases when the flow rate is higher than 85 mL/min.
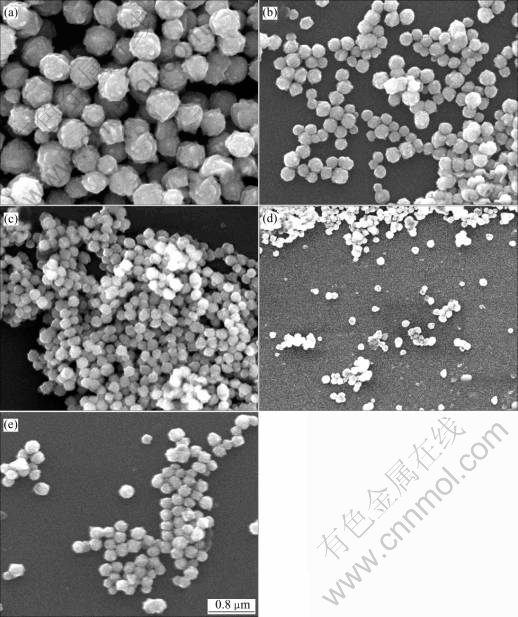
Fig.1 SEM micrographs of nickel powders obtained at different temperatures: (a) 53 ℃; (b) 58 ℃; (c) 63 ℃; (d) 68 ℃; (e) 73 ℃
and tap density are illustrated in Fig.4. It is found that, with increasing flow rate of nickel sulfate solution, the average particle size of nickel particles decreases. This phenomenon can be explained by the influence of reduction rate on the nucleation. At a low flow rate of nickel sulfate solution, the generation of nickel nuclei
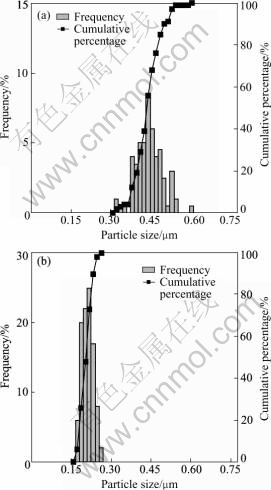
Fig.3 Particle size distribution of ultrafine nickel powders: (a) Without nucleator A; (b) With nucleator A (molar ratio of A-to-Ni=0.002)
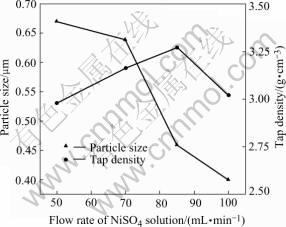
Fig.4 Average particle size and tap density of samples obtained at different flow rates of nickel sulfate solution
3.4 Oxidation resistance of nickel powders
The oxidation resistance of nickel powders in the atmosphere is demonstrated in Fig.5. From Fig.5 we can see that the temperature at which mass gain starts at about 305 ℃ and then stops at about 810 ℃. This means that the nickel powders begin to oxidize thermally at above 305 ℃. Therefore, nickel powders prepared by this method have excellent oxidation resistance properties, and it is appropriate for MLCC internal electrode.
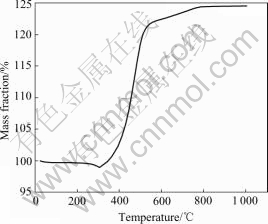
Fig.5 TGA curve of nickel powders
4 Conclusions
Ultrafine nickel powders with spherical shape and narrow size distribution have been prepared by the reduction of nickel sulfate with hydrazine hydrate in ethanol-water solvent. The reaction temperature, amount of nucleator A added and flow rate of nickel sulfate solution affect the preparation of nickel powders. The following conclusions are obtained.
1) With increasing reaction temperature, average particle size decreases first and then increases when reaction temperature is over 70 ℃. And lower temperature is in favor of obtaining smooth and regular particles.
2) The sample obtained with addition of nucleator A has much narrower size distribution than that obtained without addition of nucleator A.
3) The flow rate of nickel sulfate solution is an important factor to the reduction. With increasing flow rate of nickel sulfate solution, the particle size decreases, while the tap density increases first and then decreases.
4) It is found that the optimum conditions are: NiSO4 0.4 mol/L, the complexing agent B 0.12 mol/L and the molar ratio of A-to-Ni of 0.002 in the nickel sulfate solution; N2H4·H2O 0.64 mol/L and NaOH 1.5 mol/L in the reducing agent solution; the reaction temperature 53 ℃ and the flow rate of the NiSO4 solution 85 mL/min. Nickel powders obtained under the optimum conditions are 0.46 ?m in average particle size and 3.27 g/cm3 in tap density.
References
[1] HIROSHI K, YOUICHI M, HIROKAZU C. Base-metal electrode- multilayer ceramic capacitors: past, present and future perspectives [J]. Japanese Society of Applied Physics, 2003, 8: 4-19.
[2] HENNINGS D F K. Dielectric materials for sintering in reducing atmospheres [J]. Journal of the European Ceramic Society, 2001, 21: 1637-1642.
[3] YUKIO S. Multilayer ceramic capacitors [J]. Current Opinion in Solid State and Materials Science, 1997, 2(5): 584-587.
[4] YAMAMATSU J, KAWANO N, ARASHI T, SATO A, NAKANO Y. Reliability of multilayer ceramic capacitors with nickel electrodes [J]. Journal of Power Sources, 1996, 60(2): 199-203.
[5] WEI Zhi-qiang, WEN Xian-lun, WANG Jun, WANG Zhi-guo, XU Jiang-wei. Preparation of Ni nanopowders by anodic arc plasma [J]. The Chinese Journal of Nonferrous Metals, 2003, 13(5): 1136-1140. (in Chinese)
[6] GAO Jin-zhang, GUAN Fei, ZHAO Yan-chun, WANG Yang, MA Yong-jun, LU Xiao-quan. Preparation of ultrafine nickel powder and its catalytic dehydrogenation activity [J]. Materials Chemistry and Physics, 2001, 71(2): 215-219.
[7] YOSHINAGA H, ARAMI Y, KAJITA O, SAKAI T. Highly densed-MH electrode using flaky nickel powder and gas-atomized hydrogen storage alloy powder [J]. Journal of Alloys and Compounds, 2002, 330-332: 846-850.
[8] BAE D S, KIM W H, KIM S W, HAN K S, ADAIR J H. Synthesis of fine nickel powders by glycothermal process [J]. Journal of Materials Science Letters, 2001, 20(21): 1969-1970.
[9] YU Shui, YU Hong-ying, WANG Ying, XIAN Chai-jun, MENG Hui-ming. Preparation of nanostructured nickel-phosphorous powders using ultrasonic chemistry reduction in aqueous solution [J]. The Chinese Journal of Nonferrous Metals, 2003, 13(6): 1387-1391. (in Chinese)
[10] CHAI Li-yuan, ZHONG Hai-yun. Preparation of ultrafine nickel powder [J]. Transa Nonferrous Met Soc China, 1996, 6(2): 22-25.
[11] QIN Zhen-ping, GUO Hong-xia, LI Dong-sheng, SHI Xue-ping. Preparation and characterization of nickel nanopowders in diethyleneglycol by liquid-phase reduction [J]. Journal of Functional Materials and Devices, 2004, 10(1): 95-97.
[12] JIANG Yu, LAI Qing-gui, YANG Yan-ming, GUO Deng-gao, CHEN Jia-zhao, TU Meng-jing. Preparation of nano nickel powder for MLCs by non-confined arc with fusible hydrogen [J]. Electronic Components and Materials, 2003, 22(12): 13-15.
[13] QU Zi-mei. Production of nano meter nickel powder by carbony lation [J]. Powder Metallurgy Industry, 2003, 13(5): 16-19.
[14] KIM K H, PARK H C, LEE S D, HWA W J, HONG S S, LEE G D. Preparation of submicron nickel powders by microwave-assisted hydrothermal method [J]. Materials Chemistry and Physics, 2005, 92(1): 234-239.
[15] SUZUKI M, SATO H, HASEKAWA M, HIROTA M. Effect of size distribution on tapping properties of fine powder [J]. Powder Technology, 2001, 118(1-2): 53-57.
[16] BALASUBRAMANIAN V, SINGH P N, RAMAKRISHNAN P. Effect of some particle characteristics on the bulk properties of powders [J]. Powder Metallurgy International, 1984, 16(2): 56-59.
Foundation item: Project(50474047) supported by the National Natural Science Foundation of China
Corresponding author: ZHOU Kang-gen; Tel: +86-731-8836442; E-mail: zhoukg63@mail.csu.edu.cn
(Edited by YANG Bing)