J. Cent. South Univ. Technol. (2007)05-0647-04
DOI: 10.1007/s11771-007-0124-y 
Effect of cooling modes on microstructure and
electrochemical performance of LiFePO4
HU Guo-rong(胡国荣), GAO Xu-guang(高旭光), PENG Zhong-dong(彭忠东),
TAN Xian-yan(谭显艳), DU Ke(杜 柯), DENG Xin-rong(邓新荣), LIU Ye-xiang(刘业翔)
(School of Metallurgical Science and Engineering, Central South University, Changsha 410083, China)
Abstract: LiFePO4 was prepared by heating the pre-decomposed precursor mixtures sealed in vacuum quartz-tube. Three kinds of cooling modes including nature cooling, air quenching, and water quenching were applied to comparing the effects of cooling modes on the microstructure and electrochemical characteristics of the material. The results indicate that the water quenching mode can control overgrowth of the grain size of final product and improve its electrochemical performance compared with nature cooling mode and air quenching mode. The sample synthesized by using water quenching mode is of the highest reversible discharge specific capacity and the best cyclic electrochemical performance, demonstrating the first discharge capacity of 138.1 mA?h/g at 0.1C rate and the total loss of capacity of 3.11% after 20 cycles.
Key words: Li-ion battery; cathode material; LiFePO4; cooling mode; microstructure; electrochemical performance
1 Introduction
Lithium-ion batteries with the characteristics of high voltage, long cycling life, high energy density, non-memory effect and pollution-free, introduced in the early 1990s, are widely applied in the field of personal electronic devices, such as cell phones, laptops and digital cameras[1]. Furthermore, the latent crisis of energy and environment requires the batteries with the basic requirements of good thermal stability, low raw materials cost and environmental friendliness for making large-size cells used in power tools, electric bikes(E-bikes) and even hybrid electric vehicle(HEVs) or electric vehicle(Evs). Among the cathode materials, the key parts in the Li-ion batteries, LiFePO4 cathode material with a structure of olivine-type might meet the requirements above[2-6]. For LiFePO4, the key barriers limiting its application are extremely low electronic conductivity and low ion diffusive rate[2]. Although the problems have been solved to some extent by coating carbon[7-9] or suitable preparation procedures to minimize the particle of the sample[10-12] or doping supervalent metals ions to Li+ sites[13-14] or Fe2+ sites[15-16], the controversies of which is the nature in improving the electrochemical performance still exist [17-18]. CHUNG et al[13] believed that electron conductivity can be improved by crystal lattice doping to decrease the forbidden band width[13]. RAVET et al[17] and SUBRAMANYA et al[18] found that the electronic conductivity can be improved by carbon or residual carbon in final products or some compounds such as Fe2P etc with high electronic conductivity. Although the method of coating carbon is the most effective, it will not only lower the content of active material in samples but also decrease their tap density greatly. Meanwhile, the routes by doping supervalent metals ions cannot effectively avoid the overgrowth of single crystal in the calcining process, which makes the material with poor electrochemical performance. According to the mechanism of diffusion limit in this material, only the sample with uniform and fine particle size can obtain a higher availability ratio of active material and decrease electrode polarization. It is believed that choosing of cooling mode is also very important in controlling the crystallization process and avoiding the overgrowth of the final product. In this study, the cooling processes, including nature cooling(NC), air quenching(AQ), and water quenching(WQ) and their effects on the microstructure and electrochemical behaviors of pure LiFePO4 were investigated.
2 Experimental
LiFePO4 was prepared by the solid-state reaction using stoichiometric Li2CO3 (99.95%), FeC2O4·H2O (99%) and NH4H2PO4 (98%) as raw materials. The synthesis was performed in four consecutive steps. The starting materials were first fired at 400 ℃ for 6 h in flowing ultra-pure Ar2 atmosphere to pre-decompose the oxalate and phosphate. After cooling down, the pre-decomposed precursor mixtures were pressed into pellets (d20 mm×10 mm) at a load of 10 kN and transferred to a quartz-tube and sealed in vacuum. Then the vacuum-tight samples were finally calcined at 650 ℃ for 8 h in muffle furnace. Finally, the samples treated with different cooling modes were available by taking the quartz-tube out of the furnace and putting them in air or in water or in the furnace with cutting off the power at the calcining temperature. The final products were obtained by breaking the quartz-tube into pieces and separating the sample with the fragile quartz piece after the temperature cooled down.
The process of sealing samples was as follows. The pellets of pre-decomposed mixture were transferred into a piece of quartz-tube (d20 mm×150 mm) with one edge sealed by oxyacetylene welding flame. The air in the quartz-tube was expelled by flowing ultra-pure argon for 30 min, then the other edge was sealed by oxyacetylene welding flame while the vacuum pump was used to pump the ultra-pure argon. The schematic diagram of vacuum-tight sample is shown in Fig.1.
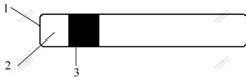
Fig.1 Schematic diagram of reactive system
1—Quartz-tube; 2—Vacuum state; 3—Pre-decomposed mixture
The phases and cell parameters of all samples were determined by X-ray diffraction (XRD, D/max-r A type Cu Kα,40 kV,300 mA,10?-70?, Japan).
Scanning electron microscope (SEM) was used to examine the microstructures of the cathode material (SEM, KYKY 2800, Japan).
The electrochemical characterization of the cathode powders was evaluated at 23 ℃. LiFePO4 electrodes for electrochemical testing were prepared by slurrying LiFePO4 powder (80%) with 10% acetylene black (AB) and 10% polyvinylidene difluoride (PVDF, in N-methyl pyrolidinone (NMP)), and then casting the mixture onto a aluminum foil. After being vacuum dried at 120 ℃ for 8 h, the electrode disks with diameter of 12 mm were punched and weighed. The cathodes were incorporated into laboratory-scale 2025 coin-type cells. A micro-porous polypropylene film (Celgard2400) was used as a separator and 1 mol/L LiPF6 solution with the volume ratio of EC to DEC of 1:1 was used as electrolyte solution. Lithium metal foil was used as counter electrode. All cells were assembled inside a glove box filled with ultra-pure argon. Charge/discharge characteristics of the active material were recorded at 0.1 C (15mA/g) rate over a voltage range of 2.5-4.1 V using a battery test system (LAND CT2001A).
An EG&G PAR potentiostat/galvanostat model 273A, operated by model 270 software EG&G was used to scan the potential at 0.5 mV/s by using the powder microelectrode assembled in argon in dry box as the working electrode, lithium metal foils as the counter electrode and 1mol/L LiPF6/EC+DMC (1:1, in volume ratio) as the electrolyte solution. The potential window was from 2.5 to 4.2 V.
3 Results and discussion
Fig.2 displays the powder X-ray diffraction patterns of LiFePO4 sintered at 650 ℃ for 8 h, followed by three different cooling processes at 650 ℃. All the patterns fit the olivine structure (PDF#83-2092) well with the relatively high intensity ratio of (I311/I111>1.2) (Table 1). This result indicates that the olivine phase LiFePO4 can be obtained by heating the pre-decomposed precursor mixtures sealed in vacuum quartz-tube under various cooling conditions. Besides, compared with the diffraction peak position of powder under NC, those of other samples shift to the left observed from the part-zooming patterns, which shows the slightly increase of unit cell with increasing cooling speed.
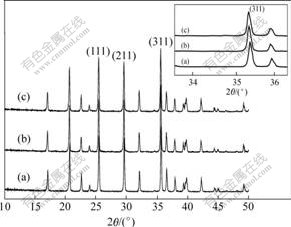
Fig.2 XRD patterns for samples prepared under various cooling conditions
(a) NC; (b) AQ; (c) WQ
Table 1 XRD data for various LiFePO4 phases
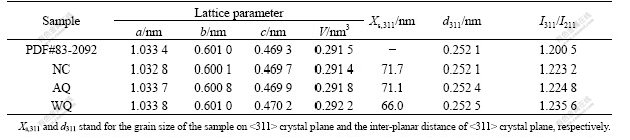
The XRD data in Table 1 can also reflect the same information. The grain size of sample under WQ at (311) crystal plane is 66.0 nm, which is smaller than those of the sample under NC (71.7 nm) and sample under AQ (71.1 nm). The sample WQ has larger peak intensity ratio (I311/I211) of 1.235 6. The lattice parameters are a=1.033 4 nm, b=0.601 2 nm, c=0.470 2 nm and V=0.292 2 nm3, which are larger than the corresponding parameters of samples under NC and AQ.
The SEM images of LiFePO4 prepared in three different cooling ways are shown in Fig.3. In Fig.3(a), there is many sub-micrometer grains aggregated to regular particles within a diameter range of 1-4 μm, in which the grains have no obvious interface. More fine grains are observed in Fig.3(b) and the particle size range is 0.5-2.0 μm with irregular and rough shape. The particle distribution of sample under WQ is the most uniform. Meanwhile the particle becomes round and smoother, with a diameter down to 0.2-1.0 μm. In addition, with the increase in particle size and uneven particle distribution, the electrochemical activity and the polarization of the larger particles will decrease greatly. The SEM micrograph of the sample synthesized by a water quenching method shows that this method is beneficial to improving the electrochemical performance and diminish the polarization when the material prepared under WQ is used as an electrode for lithium ion battery. So, choosing more rapid cooling speed and shortening cooling time can effectively control the overgrowth of pure LiFePO4.
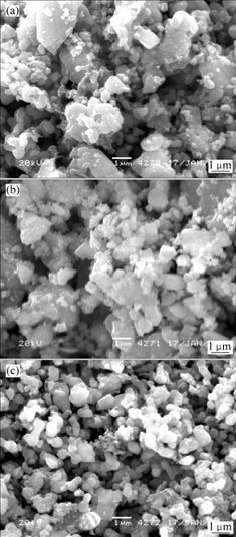
Fig.3 SEM images of LiFePO4 prepared under different conditions
(a) NC; (b) AQ; (c) WQ
Fig.4(a) shows the first charge-discharge cyclic curves for LiFePO4 with three different falling temperature method. The charge-discharge current density is 0.1C rate (15 mA/g) with cut-off voltage of 2.5-4.1 V at room temperature. The sample prepared by water quenching (sample WQ) has the highest discharge specific capacity of 138.1 mA?h/g, while the samples NC and AQ display the reversible specific capacity of 117.3 and 133.8 mA?h/g, respectively, and the separate distance between charge plateau and discharge plateau of WQ is also the shortest, which means the lowest electrode polarization. The cycling stability of samples NC, AQ and WQ is shown in Fig.4(b). The discharge capacity losses of samples NC, AQ and WQ are 38.2%, 24.4% and only 3.11%, respectively after 15 times cycles. The sample WQ processes the highest discharge capacity and the most excellent cycling performance.
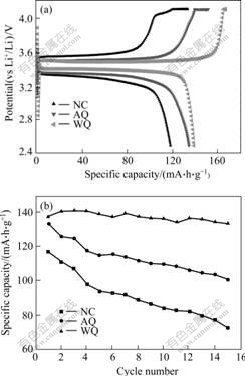
Fig.4 First-cycle voltammograms(a) and electrochemical cycling stability(b) for LiFePO4 cycled at 0.1C rate
Fig.5 shows the cyclic voltammogram curves of samples NC, AQ and WQ in the first cycle at the scan rate of 0.5 mV/s between 2.5 and 4.2 V. All curves have a pair of peaks, consisting of an anodic and a cathodic peak, observed around 3.45 V (vs Li+/Li), corresponding to the two-phase charge-discharge reaction of the Fe2+/Fe3+ redox couple. The oxidation and reduction peak positions for samples NC, AQ and WQ occurred at 4.09 and 2.97, 4.01 and 2.92, 3.78 and 3.18 V(vs Li+/Li), respectively. The sample WQ has the narrowest peak separation, indicating excellent kinetic reversibility of the two-phase transformation.
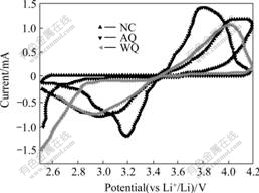
Fig.5 CVs of LiFePO4 cathode material in electrolyte of 1 mol/L LiPF6 in 1:1 EC:DEC solvent at sweep rate of 0.5 mV/s
4 Conclusions
1) The grain size of the sample has great effect on its electrochemical capability. The cooling processes including nature cooling, air quenching and water quenching were applied to preparing pure LiFePO4 and studying their effects on microstructure and electrochemical capability.
2) LiFePO4 with perfect olivine phase can be obtained by heating the pre-decomposed precursor mixtures sealed in vacuum quartz-tube under various cooling conditions.
3) Rapid cooling speed and short cooling time can effectively control the overgrowth of pure LiFePO4 and improve its electrochemical performance. Sample WQ (prepared by water quenching) has uniform and fine grain size and good electrochemical performance. The grain size of sample WQ on (311) crystal plane is 66 nm, and its grain size is smaller than those of sample NC (71.7 nm) and sample AQ (71.1 nm). Meanwhile, sample WQ has higher crystalline degree.
4) Cooling mode is also a key factor in controlling the overgrowth of pure LiFePO4 and improving its electrochemical performance in synthesizing process. The method can avoid the loss of bulk density in contrast to others.
References
[1] NISHI Y. Lithium ion batteries: Past 10 years and the future[J]. J Power Sources, 2001, 100(1/2): 101-106.
[2] PADHI A K, NAJUNDASWAMY K S, GOODENOUGH J B. Phospho-olivines as positive-electrode materials for rechargeable lithium batteries[J]. J Electrochem Soc, 1997, 144(4): 1188–1194.
[3] BAUER E M, BELLITTO C, PASQUALI M, et al. Versatile synthesis of carbon-rich LiFePO4 enhancing its electrochemical properties[J]. Electrochem Solid-State Lett, 2004, 7(4): A85-A90.
[4] ZAGHIB K, STRIEBEL K, GUERFI A, et al. LiFePO4/polymer/natural graphite: Low cost Li-ion batteries[J]. Electrochimica Acta, 2004, 50(2/3): 263-270.
[5] HUANG H, YIN S C, NAZAR L F. Approaching theoretical capacity of LiFePO4 at room temperature at high rates[J]. Electrochem Solid- State Lett, 2001, 4(10): A170-A172.
[6] GUERFI A, KANEKO M, PETITCLERC M, et al. LiFePO4 water-soluble binder electrode for Li-ion batteries[J]. J Power Sources, 2007, 163(2): 1047-1052.
[7] HU Guo-rong, GAO Xu-guang, PENG Zhong-dong, et al. Synthesis of LiFePO4/C composite electrode with enhanced electrochemical performance[J]. Trans Nonferrous Met Soc China, 2005, 15(4): 795-798.
[8] MYUNG S T, KOMABA S, HIROSAKI N, et al. Emulsion drying synthesis of olivine LiFePO4/C composite and its electrochemical properties as lithium intercalation material[J]. Electrochimica Acta, 2004, 49(24): 4213-4222.
[9] HO C S, WON C, HO J. Electrochemical properties of carbon-coated LiFePO4 cathode using graphite, carbon black, and acetylene black[J]. Electrochimica Acta, 2006, 52(4): 1472-1476.
[10] YANG Shou-feng, ZAVALIJ P Y, WHITTINGGHAM M S. Hydrothermal synthesis of lithium iron phosphate cathodes[J]. Electrochemistry Commun, 2001, 3(9): 505-508.
[11] PARK K S, KANG K T, LEE S B, et al. Synthesis of LiFePO4 with fine particle by co-precipitation method[J]. Materials Research Bulletin, 2004, 39(12): 1803-1810.
[12] YAMADA A, CHUNG S C, HINOKUMA K. Optimized LiFePO4 for lithium battery cathodes[J]. J Electrochem Soc, 2001, 148(3): A224–A229.
[13] CHUNG S Y, BLOCKING J T, CHIANG Y M. Electronically conductive phospho-olivines as lithium storage electrodes[J]. Nature Mater, 2002, 2: 123-128.
[14] HU Guo-rong, GAO Xu-guang, PENG Zhong-dong, et al. Influence of Ti ion doping on electrochemical properties of LiFePO4/C cathode material for lithium-ion batteries[J]. Trans Nonferrous Met Soc China, 2007, 17(2): 296-300.
[15] HONG Jian, WANG Chun-sheng, KASAVAJJULA U. Kinetic behavior of LiFeMgPO4 cathode material for Li-ion batteries[J]. J Power Sources, 2006, 162(2): 1289-1296
[16] WANG De-yu, LI Hong, SHI Si-qi, et al. Improving the rate performance of LiFePO4 by Fe-site doping[J]. Electrochimica Acta, 2005, 50(14): 2955-2958
[17] RAVET N, ABOUIMRANE A, ARMAND M, et al. On the electronic conductivity of phospho-olivines as lithium storage electrodes[J]. Nature Mater, 2003, 2: 702-720.
[18] SUBRAMANYA H P, ELLIS B, COOMBS N, et al. Nano-network electronic conduction in iron and nickel olivine phosphates[J]. Nature Mater, 2004, 3: 147-152.
Foundation item: Project(50604018) supported by the National Natural Science Foundation of China
Received date: 2007-03-20; Accepted date: 2007-05-18
Corresponding author: HU Guo-rong, Professor; Tel:+86-731-8830474; E-mail: hgrhsj@263.net
(Edited by CHEN Wei-ping)