Trans. Nonferrous Met. Soc. China 25(2015) 1050-1055
Analysis of bulging process of aluminum alloy by overlapping sheet metal and its formability
Tie-jun GAO1, Yang LIU1, Peng CHEN1, Zhong-jin WANG2
1. Faculty of Aerospace Engineering, Shenyang Aerospace University, Shenyang 110136, China;
2. School of Materials Science and Engineering, Harbin Institute of Technology, Harbin 150001, China
Received 9 May 2014; accepted 13 July 2014
Abstract: The influences of strength coefficient K, work hardening exponent n and thickness t of the overlapping sheet on bulging process are analyzed based on hardening material model. Also, bulging experiments are carried out by taking the aluminum alloy LF21 as formed sheet metal, and selecting overlapping sheet with different thicknesses and material properties, by which accuracy of the above analysis result is verified in the aspects of geometric shape, thickness distribution and limit bulging height. The results show that higher strength coefficient K, larger work hardening exponent n and proper thickness of the overlapping sheet are helpful to improve the formability and forming uniformity of formed sheet metal.
Key words: overlapping sheet; aluminum alloy; bulging; power hardening material; formability
1 Introduction
In order to improve the plasticity of metal materials, on one hand, we can improve the inherent properties such as lattice type, chemical composition and microstructure of materials [1], and on the other hand, we can choose external conditions such as suitable deformation temperature and deformation rate [2-5]. Meanwhile, we can improve the formability of formed sheet metal by controlling or changing the force condition and stress state [6-9].
In overlapping forming process, we overlap the formed sheet metal with another sheet metal (called overlapping sheet) of different or the same kind of material. At the same time, the overlapping sheet takes the shape of the formed sheet metal, so that the formed sheet metal can be constrained and loaded with reverse pressure, so as to improve its formability [10-12]. SEMIATIN and PIEHLER [13] studied the forming limit of the aluminum overlapping sheet with stainless steel without lubrication by experiment, and the results showed that the unstable flow of the overlapping sheet material can lead to interface irregularities which have been associated with the local deformation, and local deformation determines the forming limit of overlapping sheet. MASANORI et al [14] used the rigid die on overlapping sheets of the same material of pure aluminum in bulging test, and proved that the limit bulging height increased with increasing thickness of the overlapping sheet by changing the thickness, and that the stress state of the formed sheet metal and the overlapping sheet can lead to the changes of necking position by changing the contact conditions, and the two measures mutually inhibited the development of necking, and thereby improved the formability of formed sheet metal. TSENG et al [15] obtained the overlapping sheet bulging limit diagram through bulging tests on the Al/Cu overlapping sheet searching its the forming limit in different thicknesses. MASASHI and KAZUYOSHI [16] studied the formability of aluminum sheet metal cemented by the overlapping sheet of copper sheet, and results showed that the formability with overlapping sheet performed better than that of the two sheet metals formed separately. In this work, based on the model of power hardening material, the influences of properties and thickness of overlapping sheet on bulging uniformity and formability of formed sheet metal are analyzed. With the research object of aluminum alloy LF21 (formed sheet metal), overlapping sheets with different thicknesses and properties are selected in bulging test to verify the accuracy of the analysis.
2 Analysis of overlapping bulging
The overlapping bulging and stress state in the process are shown in Fig. 1. The overlapping sheet is formed mainly under tangential tensile stress σρ and circumferential tensile stress σθ. For the formed sheet metal, besides radial tensile stress σ′ρ and circumferential tensile stress σ′θ, it is also affected by the reverse compressive stress σ′b from the overlapping sheet. So, there are two ways to improve the formability of the formed sheet metal by overlapping bulging. One is to take advantage of good property of the overlapping sheet to control the forming process of the formed sheet metal. While the deformation regularity between the formed sheet metal and the overlapping sheet is similar or identical, the deformation uniformity and the formability of the formed sheet metal can be improved correspondingly. The other way is to use the reverse pressure of the overlapping sheet to turn stress state of the formed sheet metal from plane stress state to three-dimensional stress state, which brings compressive stress on both sides of the formed sheet metal. As a result, all kinds of damage caused by plastic deformation can be prevented and, the thinning and fracture of metal can be restricted. Thus, the deformation uniformity and formability of the formed sheet metal can be improved.

Fig. 1 Stress state of overlapping bulging
By either way, the improvement of the formability of the formed sheet metal is associated with mechanical properties of overlapping sheet. Assume that the stress and strain of the overlapping sheet and formed sheet metal satisfy the power hardening material relations:
(1)
(2)
where K1 is the overlapping sheet strength coefficient; n1 is the overlapping sheet hardening exponent; K2 is the formed sheet metal strength coefficient; n2 is the formed sheet metal hardening exponent.
For the first way to improve the formability of formed sheet metal, deformation regularity of overlapping sheet determines the deformation uniformity of formed sheet metal. So, suppose that the overlapping sheet and the formed sheet metal have the same intensity coefficient K1=K2, when n1>n2, strain hardening effect and deformation uniformity of overlapping sheet are better than those of formed sheet metal. Under similar forming conditions, the deformation uniformity and the formability of the formed sheet metal can also be improved correspondingly. When n12, strain hardening effect and deformation uniformity of overlapping sheet are poor. So it can do little help to the formability of the formed sheet metal.
For the second way to improve the formability of formed sheet metal, reverse compressive stress from the overlapping sheet can restrain the development of cracks inside the formed sheet metal and the greater the reverse compressive stress is, the better the sheet metal can be formed. The reverse compressive stress at any point on overlapping sheet is related to the deformation stage of formed sheet metal and overlapping sheet. It can be calculated from the derivation of Eqs. (1) and (2):
(3)
(4)
It is assumed that the work hardening exponents of overlapping sheet and formed sheet metal are equal (n1=n2), deformation regularities are similar (ε1=ε2), then with the constant thickness, the greater the overlapping sheet strength coefficient K is, the more helpful there will be to improve the formability of formed sheet metal. Also, the reverse compressive stress can be improved by increasing the thickness of overlapping sheet.
3 Experimental
In order to verify the accuracy of the analysis results, bulging experiment with different overlapping sheet materials was carried out. Diameter of the bulging die is 100 mm. The formed sheet metal is aluminum alloy LF21. The overlapping sheet includes aluminum alloy LF21, LF2, stainless steel SUS201 and copper alloy H62. Mechanical properties of the materials are shown in Table 1. Sheet blank size is 190 mm × 190 mm. The transmission force is viscous medium with the relative molecular mass of 600 k and the shear viscosity of 25260 Pa·s. The experiments were carried out on the 1000 kN hydraulic press at Shenyang Aerospace University, China.
Table 1 Mechanical properties of formed sheet metal and overlapping sheet
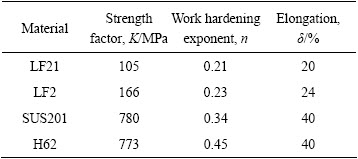
4 Results and analysis
4.1 Influence of material properties of overlapping sheet on formed sheet metal
In order to obtain the influence of overlapping sheet material properties on sheet metal bulging, four kinds of overlapping sheets LF21/LF21, LF2/LF21, SUS201/LF21 and H62/LF21 with thickness t=1.0 mm were chosen in the bulging test. Specimens of LF21 with the bulging height h=23.5 mm are shown in Fig. 2. The bulging pressures are 9.5, 12.5, 16.7 and 17.1 MPa, respectively. Geometrical shapes measured from the center vertex of the specimen are shown in Fig. 3.
Thickness distributions of the specimens are shown in Fig. 4. As shown in Figs. 4 and 5, heights of specimens are similar, but the geometrical shape changes obviously in the area 10-45 mm away from the specimen center. From the comparison of overlapping sheet materials of LF2/LF21 and LF21/LF21, although the work hardening exponents of the two materials are similar, the strength coefficient of LF2 is higher than that of LF21(shown in Table 1), which means that with the same bulging height, LF2 needs bigger bulging pressure and leads to bigger reverse compressive stress. So, the deformation of the formed sheet metal can be more uniform. From the comparison of overlapping sheet materials of SUS201/LF21 and H62/LF21, strength coefficients are similar, but the work hardening exponent of SUS201 is smaller than that of H62 (shown in Table 1). So, the strain strengthening effect and the deformation uniformity of H62 are better than those of SUS201. As a result, H62 overlapping sheet is more helpful to the improvement of formed sheet metal formability. So it can be concluded from Fig. 3 and Fig. 4 that the larger the strength coefficient and work hardening exponent are, the more uniform the formed sheet metal can be.
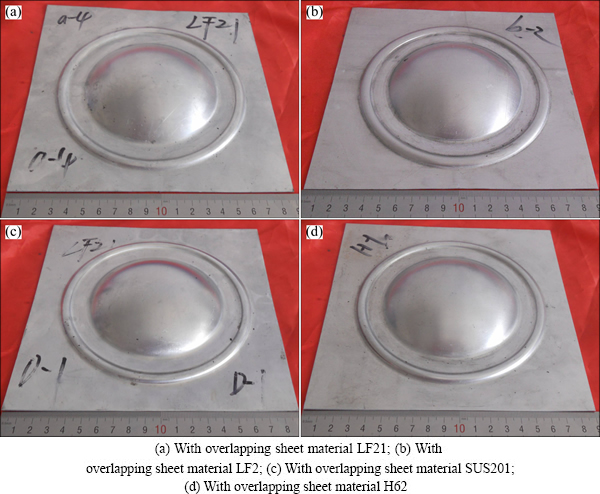
Fig. 2 LF21 specimens with different overlapping sheet materials (h=23.5 mm)
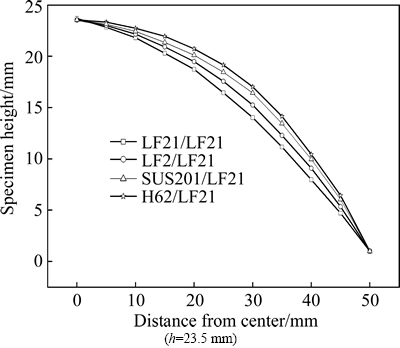
Fig. 3 Geometrical shape of LF21 specimens with different overlapping sheet materials
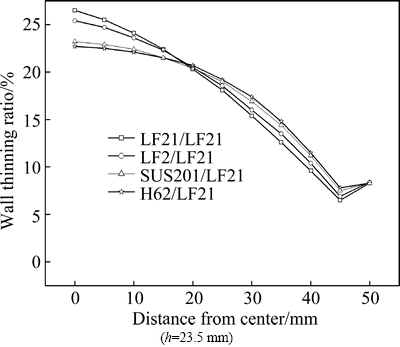
Fig. 4 Wall thinning ratio of LF21 specimens with different overlapping sheet materials
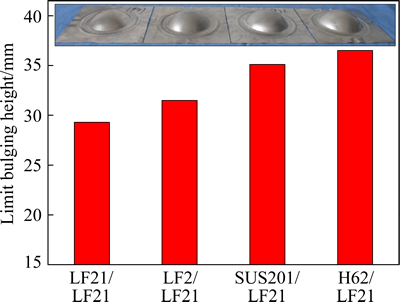
Fig. 5 Limit bulging height of LF21 specimen with different overlapping sheet materials
In order to verify the impact of overlapping sheet material on the formability of LF21 formed sheet metal, four kinds of bulging tests are carried out. Comparison of limit bulging height with different overlapping sheet materials is shown in Fig. 5. The limit bulging heights are 29.3, 31.5, 35.1 and 35.9 mm, respectively. With the overlapping material of H62, the bulging performance of LF21 sheet metal is the best, and with the material of LF21, the bulging performance of LF21 sheet metal is the worst. Again, it indicates that larger strength coefficient and work hardening exponent are good for the improvement of formed sheet metal formability.
4.2 Influence of overlapping sheet thickness on formed sheet metal
SUS201 overlapping sheets with thickness of t=0.5, 0.8, 1.0 and 1.2 mm (the thickness of LF21 specimen is 1.0 mm) are chosen. In the test, bulging height is h= 25.5 mm. The bulging pressures are 13.6, 15.5, 17.5 and 19.1 MPa, respectively. The geometrical shape of LF21 specimen is shown in Fig. 6. The specimen thinning ratio is shown in Fig. 7. As can be seen, the maximum wall thinning ratios of the specimen are 26.4%, 25.8%, 25.1% and 24.8%, respectively. With the increase of thickness of the SUS201 overlapping sheet, the bulging pressure increases correspondingly, so does the reverse compressive stress. So, the maximum wall thinning ratio of the specimen decreases and the thickness distribution becomes more uniform. The comparison of limit bulging height of LF21 specimen with different overlapping sheet thicknesses is shown in Fig. 8. With the SUS201 overlapping sheets with thickness of t=0.5, 0.8, 1.0 and 1.2 mm, the limit bulging heights are 33.1, 34.3, 35.1 and 35.5 mm, respectively. As the increase of thickness of the SUS201 overlapping sheet, the limit bulging height increases and then begins to flatten when the thicknesses of overlapping sheet and the formed sheet metal are similar. Therefore, it is better to choose the overlapping sheet thickness that is similar to the formed sheet metal, which can lower the production cost and forming difficulty.
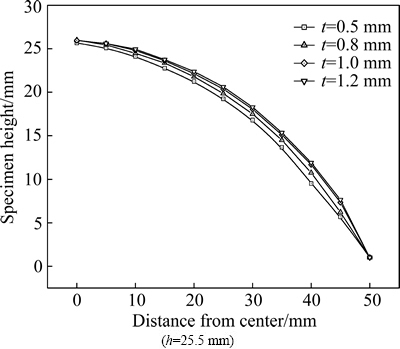
Fig. 6 Geometrical shapes of LF21 specimen with different overlapping sheet thicknesses
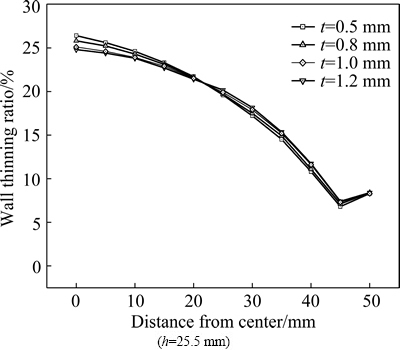
Fig. 7 Wall thinning ratios of LF21 specimen with different overlapping sheet thicknesses
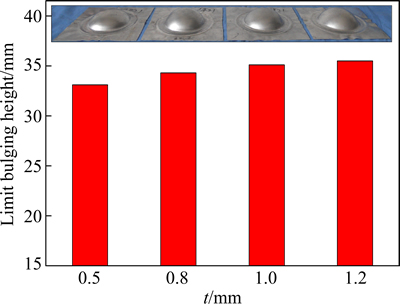
Fig. 8 Comparison of limit bulging height of LF21 specimen with different overlapping sheet thicknesses
5 Conclusions
1) In overlapping sheet bulging, the material and property of overlapping sheet are the main factors that influence the improvement of the formability of formed sheet metal. For the material that meets the power hardening medium model, higher strength coefficient K, larger work hardening exponent n can contribute to the improvement of the formability of formed sheet metal.
2) In overlapping sheet bulging, one main way to improve the formability of formed sheet metal is to uniformize the deformation. Proper choice on the material of overlapping sheet can disperse the large deformation of formed sheet metal, so as to improve the limit deformation of formed sheet metal.
3) In overlapping sheet bulging, increasing the overlapping sheet thickness can also improve the formability of formed sheet metal, but the production cost and process condition should be taken into consideration in practical process.
References
[1] LIU Yan-hui, WANG Gang, WANG Ru-ju, ZHAO De-qian, PAN Ming-xiang, WANG Wei-hua. Super plastic bulk metallic glasses at room temperature [J]. Science, 2007, 315: 1385-1388.
[2] CHEN F K, CHIU K H. Stamping formability of pure titanium sheets [J]. Journal of Materials Processing Technology, 2005, 170(1-2): 181-186.
[3] CHAN L C, LU X Z. Material sensitivity and formability prediction of warm-forming magnesium alloy sheets with experimental verification [J]. International Journal of Advanced Manufacturing Technology, 2014, 71: 253-262.
[4] SONG Hui, WANG Zhong-jin. Microcrack healing and local recrystallization in pre-deformed sheet by high density electro pulsing [J]. Materials Science and Engineering A, 2008, 490(1-2): 1-6.
[5] HU X H, WU P D, LLOYD D J, EMBURY J D. Enhanced formability in sheet metals produced by cladding a high strain-rate sensitive layer [J]. Journal of Applied Mechanics, 2014, 81(2): 021007.
[6] LIU Jian-guang, XUE Wei. Formability of AA5052/ polyethylene/ AA5052 sandwich sheets [J]. Transactions Nonferrous Metals Society of China, 2013, 23(4): 964-969.
[7] XU Yong-chao, LI Feng, LIU Xin, YUAN Shi-jian. Effects of pre-bulging on 2024 aluminum alloy complex-shaped components [J]. Journal of the Minerals, Metals and Materials Society, 2011, 63(5): 39-41.
[8] CUI Xiao-lei, WANG Xiao-song, YUAN Shi-jian. Progress on effects of through-thickness normal stress on sheet metal forming limit [J]. Journal of Plasticity Engineering, 2013, 20(2): 1-9.
[9] TSENG Huang-chi, HUNG Jung-chung, HUNG Ching-hua, LEE Ming-fu. Experimental and numerical analysis of titanium/aluminum clad metal sheets in sheet hydroforming [J]. International Journal of Advanced Manufacturing Technology, 2011, 54(1-4): 93-111.
[10] WANG Zhong-jin,SONG Hui,WANG Zhe. Deformation behavior of TC1 titanium alloy sheet under double-sided pressure [J]. Transactions Nonferrous Metals Society of China, 2008, 18(1): 72-76.
[11] Yilamua K, Hinob R, Hamasakib H, et al. Air bending and springback of stainless steel clad aluminum sheet [J]. Journal of Materials Processing Technology, 2010, 210: 272-278.
[12] LIU J, WANG Z, MENG Q. Loading mode effects on sheet formability in viscous pressure forming (VPF) [J]. Materials Research Innovations, 2011, 15(1): 295-298.
[13] SEMIATIN S L, PIEHLER H R. Forming limits of sandwich sheet materials [J]. Metallurgical Transactions A, 1979, 10: 1107-1118.
[14] MASANORI K, NOBUKAZU H, YASUSHI K. Improvement of pure stretchability by overlapping sheet metals [J]. Journal of the Japan Society for Technology of Plasticity, 2001, 42(4): 328-332.
[15] TSENG Huang-chi, HUNG Ching-hua, HUANG Chin-chuan. An analysis of the formability of aluminum/copper clad metals with different thicknesses by the finite element method and experiment [J]. International journal of Advanced Manufacturing Technologies, 2010, 49: 1029- 1036.
[16] MASASHI H, KAZUYOSHI K. Press forming of clad sheets [J]. Japan Society for Technology of Plasticity, 1985, 26(4): 385-393.
铝合金覆层板胀形过程及成形性能
高铁军1,刘 洋1,陈 鹏1,王忠金2
1. 沈阳航空航天大学 航空航天工程学部,沈阳 110136;
2. 哈尔滨工业大学 材料科学与工程学院,哈尔滨 150001
摘 要:基于幂硬化材料模型,分析覆板材料强度系数K、加工硬化指数n及厚度t对成形板材胀形性能的影响,并以铝合金LF21为研究对象,选择不同厚度及性能的覆板进行了粘性介质压力胀形实验,从覆板材料性能及厚度等方面对板材胀形试件几何形状、壁厚分布规律及极限胀形高度等方面验证了分析结果的准确性。研究结果表明:覆板成形时,选择强度系数K较高、加工硬化指数n值较大及适当厚度的覆板有助于板材成形性能的提高。
关键词:覆板;铝合金;胀形;幂硬化材料;成形性能
(Edited by Yun-bin HE)
Foundation item: Project (51205260) supported by the National Natural Science Foundation of China; Project (L2012046) supported by the Liaoning Provincial Committee of Education, China
Corresponding author: Tie-jun GAO; Tel: +86-24-89723748; E-mail: gtj2572@sina.com
DOI: 10.1016/S1003-6326(15)63697-4