DOI: 10.11817/j.ysxb.1004.0609.2020-35729
停放时间对6061铝合金性能及微观组织的影响
寇琳媛1, 2,王 冠1, 2,马 超1,卞东伟1
(1. 宁夏大学 机械工程学院,银川 750021;
2. 宁夏大学 宁夏智能装备CAE重点实验室,银川 750021)
摘 要:采用宏观检测与显微分析相结合的手段,研究不同停放时间下6061铝合金的力学性能与微观组织的变化规律。结果表明:停放时间对6061铝合金的晶粒尺寸有较大影响,晶粒尺寸呈先增大后减小的趋势;停放时间对6061铝合金弹塑性变形过渡阶段有较大影响,但对弹性及塑性阶段变形的影响很小。6061铝合金在停放为0~2 h时,力学性能无明显变化,变形后试样表面光滑,变形协调性较好;停放时间为12 h时,材料的抗拉强度和屈服强度降至最低,但伸长率提高,试样表面呈橘皮形貌,变形均匀性较差;停放时间为24 h~15 d时,合金的强度回升并逐渐趋于稳定。结果表明:随着停放时间的增长,6061铝合金断口的韧窝直径和深度不断增加,第二相粒子的尺寸也不断增大,形状由球状、带状逐渐转变为板状、块状。通过研究得到6061铝合金满足汽车结构强韧化需求,综合性能最优需求的停放时间为12~24 h。此研究结果能够为6061铝合金加工工艺优化提供理论指导。
关键词:6061铝合金;停放时间;力学性能;微观组织
文章编号:1004-0609(2020)-04-0750-13 中图分类号:TG146.21 文献标志码:A
可进行热处理强化的铝合金在热处理过程中存在“停放效应”,即合金经过固溶淬火到进行人工时效处理的过程中,几乎不可避免的需要一段停放时间,这段时间对合金综合力学性能、耐腐蚀性能等的影响称为“停放效应”。7050-T6铝合金在0~250 s淬火转移时间内其抗剥落腐蚀性能随着淬火转移时间的延长而减小[1]。无锆7055合金,其强度随停放时间的延长在20 s时达到最大值,然后略有下降;而含锆7055合金的伸长率在20s内随停放时间的增加而缓慢下降,在20 s后快速下降[2]。ROBINSON等[3]指出停放会对7050铝合金在压缩变形中的加工硬化行为产生影响,随着停放时间的减少材料冷变形后的残余应力水平降低。祝伟忠等[4]通过对比不同停放时间下A6N01-T5铝合金的强度和伸长率,确定了型材力学性能与停放时间的关系曲线,发现淬火后立即进行人工时效时合金强度最高,停放时间8~30 h内强度最低,停放时间超过30 h后,强度逐渐稳定。张洪辉 等[5]指出6061铝合金的停放时间为8~20 h时,经人工时效处理后,合金的强度下降较大,但伸长率得到提升。很多学者关注停放过程中合金微观组织的变化,CESCHINI等[6]研究了停放时间为0~96 h时A356铝合金的性能变化,指出预时效中形成的团簇成分影响了最终材料的力学性能。1933合金在5~90 s的短停放时间内,随着停放时间的增加,晶粒内产生η平衡相,材料的力学性能逐渐及耐腐蚀性能降低;为了保证合金具有较高的力学性能,在进行淬火转移时,温度应高于366 ℃[7]。2024铝合金在短时间停放时会形成圆形的Al-Cu-Mg沉淀相以及形状不规则的Al-Cu-Mn- Si-Fe沉淀相[8],但随着停放时间的增加,材料的内部及表面会形成壳状的颗粒,使合金的腐蚀性能降低。国内学者伊琳娜等[9]、宋伟苑等[10]、杜君[11]采用宏观力学性能实验与显微组织检测相结合的手段对7xxx系铝合金开展研究。结果表明,停放效应对7xxx系铝合金的强度、抗腐蚀性及电导率会造成显著影响,并建议停放时间不超过14 d。王雪玲等[12]研究了停放时间、人工时效时间对6082-T651铝合金板材力学性能和显微组织的影响,提出6082-T651铝合金板材最佳停放时间为不超过4 h。刘星兴等[13]、李翔等[14]认为停放过程中发生自然时效,会消耗淬火空位,弱化6061铝合金烤漆时效的硬化能力,温变形可降低停放效应对烤漆硬化的影响。
综上所述,现有研究虽然在合金停放效应上获得了一些成果,但其研究工作主要集中在停放效应对材料宏观力学性能的影响规律,缺少针对停放导致的微观组织演化与宏观力学特性关系的系统研究,因此,立足于汽车行业对高强高韧铝合金薄板的需求,本文作者系统开展停放时间对6061铝合金的宏微观特性及变形行为影响的研究,为车身用铝合金的生产加工提供理论指导和实验参考。
1 实验
实验采用的坯料是由西南铝业生产的6061轧制铝合金板,其合金成分见表1。
表1 6061铝合金的化学成分
Table 1 Chemical composition of 6061 aluminum alloy (mass fraction, %)

热处理选用的是SX2-10-12N箱式电阻炉和DHG-9145A鼓风干燥箱,热处理工艺路线为:固溶处理(560 ℃, 50 min)→水淬→停放→人工时效(180 ℃, 8 h),如图1所示。6061铝合金停放时间分别为0 h、2 h、4 h、6 h、12 h、24 h、3 d、7 d、15 d、30 d、60 d。
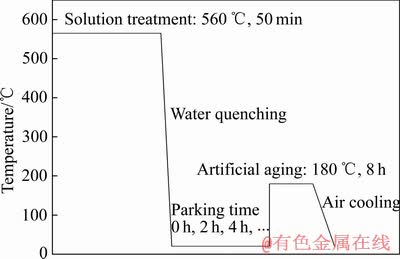
图1 停放效应实验流程图
Fig. 1 Heat treatment flow of 6061 aluminum alloy with parking effect
热处理后的材料沿垂直轧制方向取样,在磨抛机上依次用600#、800#、1000#水磨砂纸研磨后,使用抛光布配合水与研磨膏进行精细研磨,并达到无划痕的镜面效果;随后用体积比1:9的高氯酸与无水乙醇溶液电解抛光,时间10 s,电压25 V;阳极覆膜采用体积比1:20的氟硼酸和水,时间3 min,电压25 V,酒精清洗后吹干,在蔡司金相显微镜上观察其微观组织。
硬度检测采用310HVS-5维氏硬度计测试,载荷为49.04 N,保荷时间为20 s;为了保证硬度值的精确性,预先对试样进行机械抛光与电解抛光,避免表面氧化层对硬度值的影响。在每个试样上选取5个点进行硬度测试,将得到的数据去掉最大值和最小值后求平均数作为最终结果。
拉伸试样按照GB/T 228—2002《金属材料室温拉伸实验方法》中的规定加工而成,厚度2.0 mm,其中轧制方向与试样轴向垂直。采用MTS E45型万能实验机进行准静态拉伸实验。拉伸速率为2 mm/min,力学性能取3组稳定实验的平均值。采用扫描电子显微镜观察拉伸后试样断口的形貌,并进行能谱分析。
2 结果与讨论
2.1 停放时间对微观组织的影响
图2所示为6061铝合金停放0 h、6 h、12 h、24 h、7 d、30 d再经过人工时效的金相图。通过对比其中的微观组织可以看出:停放0 h时,6061铝合金晶粒尺寸均匀性较好,晶粒形状为不规则的多边形;停放6~12 h时,部分晶粒的尺寸显著增大,晶粒尺寸的均匀性降低;停放时间大于24 h时,晶粒尺寸的又有所减小,晶粒尺寸的一致性提高,并逐渐趋于稳定。
晶粒尺寸会影响合金的强度,晶粒的均匀程度决定着合金伸长率的大小。为研究不同停放时间下铝合金晶粒的差异,以GB/T 6394—2002《金属平均晶粒度测定方法》为标准,基于200倍的金相图像进行晶粒尺寸的测量,其结果如图3所示。
由图3可知,原始轧制态试样未经过固溶和人工时效处理,晶粒尺寸较小,约为45 μm;热处理过后的6061铝合金晶粒尺寸发生明显变化,停放时间为0 h时晶粒尺寸约为63 μm。随着停放时间的增加,晶粒尺寸的变化大致呈现两个阶段;停放0~12 h晶粒的尺寸逐渐长大;停放时间为12 h时,平均晶粒尺寸达到最大,约为74.5 μm。随着停放时间的继续增长,晶粒的尺寸开始变小,停放时间超过24 h后,晶粒尺寸进入到平台期,此时,平均晶粒尺寸约为59 μm,与停放12 h的晶粒尺寸相比较,减小约26.3%,并随时间的推移有持续减小的趋势。
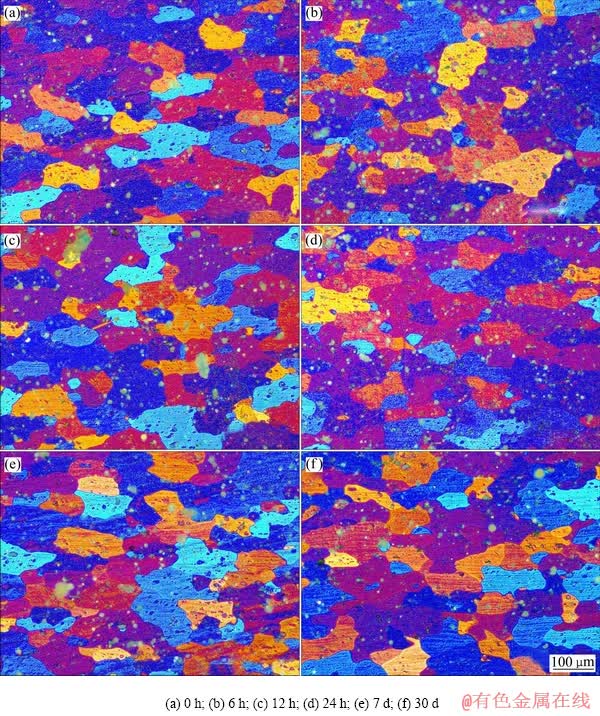
图2 不同停放时间下6061铝合金的微观组织
Fig. 2 Microstructures of 6061 Al alloy under different quench delay time
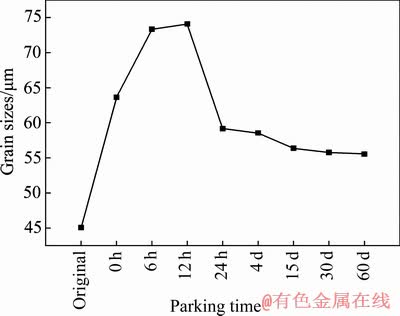
图3 不同停放时间6061铝合金的晶粒尺寸
Fig. 3 Grain size of 6061 Al alloy under different quench delay time
2.2 停放时间对材料性能与变形的影响
图4所示为停放时间与6061铝合金硬度的关系曲线。由图4可知,停放时间为0~2 h时,合金的硬度变化不大;但当停放时间为2~12 h时,合金的硬度快速下降,并在停放12 h时,达到最小值73.2HV,较停放0h时下降了10%;停放12 h~7 d时,合金的硬度开始快速增长,并在停放15 d后,达到稳定状态,约为81HV,较初始值降低了0.7%左右。
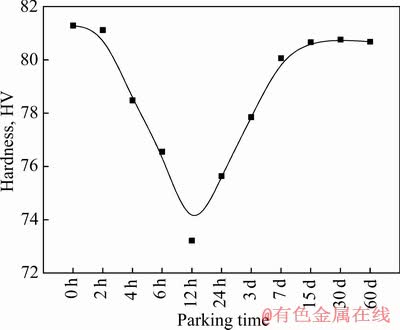
图4 停放时间对6061铝合金硬度的影响
Fig. 4 Effect of quench delay time on 6061 Al alloy hardness
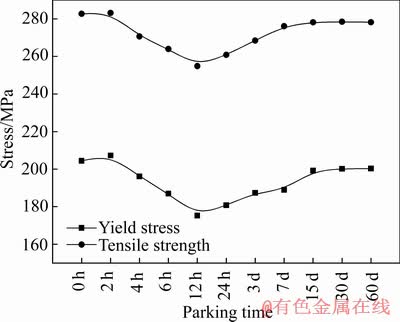
图5 停放时间与6061铝合金的屈服强度、抗拉强度的关系
Fig. 5 Relationship of quench delay time with yield strength and tensile strength of 6061 Al alloy
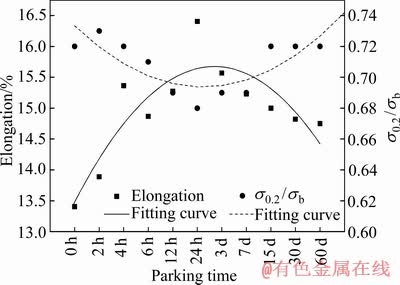
图6 停放时间与6061铝合金的伸长率、屈强比的关系
Fig. 6 Relationship of quench delay time with elongation and yield ratio of 6061 Al alloy
将实验得到的应力-应变曲线数据进行分析计算,得到停放时间与6061铝合金屈服强度、抗拉强度、伸长率、屈强比的关系,如图5和6所示。由图5和6可知,6061铝合金在停放前2 h内力学性能变化不大,抗拉强度约为283.17 MPa,屈服强度约为207.26 MPa,伸长率约为13.89%;但当停放时间为2~12 h时,6061铝合金的力学性能出现了明显的下降,并在停放12 h时达到最低值,抗拉强度降低至254.87 MPa,屈服强度降低至175.25 MPa,但伸长率提高至15.25%;停放时间为12 h~7 d时,合金的性能有所提高,但幅度不大;最终合金的性能在停放时间15 d后趋于稳定,在此区间内,抗拉强度约为280.00 MPa,屈服强度约为200.00 MPa,伸长率约为14.75%。抗拉强度与屈服强度所受影响的趋势几乎保持一致,而伸长率则恰好相反。
屈强比是指材料的屈服强度
与抗拉强度
的比值。屈强比低的合金材料延伸性能佳、结构可靠度高,过高的屈强比意味着材料的屈服强度与抗拉强度相近,这会影响材料的可靠性;但由于屈强比过低又会导致材料的屈服点与抗拉强度差距过大,性能得不到充分发挥,因此,需要结合实际要求来判断材料屈强比高低的好坏。结合图6可知,屈强比的趋势与强度趋势相似,在停放0~1 h时,屈强比稳定在0.72左右;并在停放时间为1~24 h时,呈明显下降趋势,屈强比最低达到0.68;停放24 h后,屈强比开始上升;直到15 d后,屈强比稳定在0.72。通过屈强比与衍生率变化曲线可知,面向汽车行业的强韧化需求,6061铝合金综合性能最优的停放时间为12~24 h。
图7所示为典型停放时间0 h、12 h、15 d条件下材料的工程应力-应变曲线。由图7可见,6061铝合金在不同停放时间下的应力-应变曲线的弹性段几乎完全一致;通过计算测量,得出其斜率约为68 GPa,说明停放对材料的弹性模量没有影响。
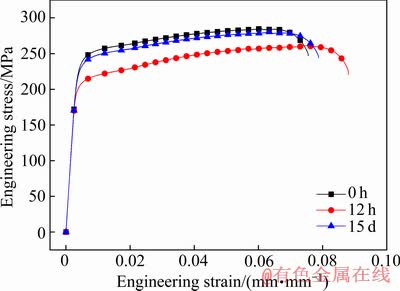
图7 不同停放时间下6061铝合金的真实应力-应变曲线
Fig. 7 True stress-strain curves of 6061 Al alloy under different quench delay time
为准确获得弹塑性变形的临界点,对应力-应变曲线进行微分,并结合Langevin Mod非线性拟合,获得应力的变化率曲线,如图8所示。由图8可知,曲线由3个典型阶段组成,在变形初期,应力-应变曲线保持稳定的斜率,其斜率值即为6061铝合金的弹性模量,三组试样曲线基本重合,说明停放时间对弹性变形线性阶段的影响较小。当应变超过材料的比例极限σp后斜率开始下降,其中停放时间为12 h试样应力1阶倒数曲线最先开始发生下降,且下降速度明显高于停放0 h与15 d试样。当应变超过0.006时,材料完全进入塑性变形,三组试样的曲线再次重合,应力1阶倒数曲线的下降速度减慢并最终达到稳定。说明停放时间对塑性变形阶段的影响较小。
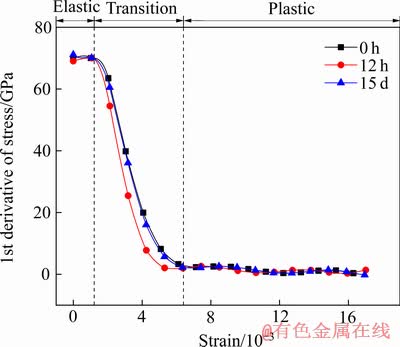
图8 合金的应力-应变曲线一阶微分
Fig. 8 First-order differential of stress and strain curves of alloy
对图8再次微分能够获得试样应力斜率的变化率曲线,其结果如图9所示。曲线的最低点为应力-应变曲线的突变点,即为发生塑性变形的临界应变εcr。由图9可知,停放0 h与15 d试样应力二阶倒数曲线基本重合,临界应变约为0.0032;而停放12 h试样的临界应变出现较早,约为0.0026,且曲线的谷值更低。说明停放时间会对6061铝合金的弹塑性变形过渡阶段产生显著影响。
由图7可知,停放0 h、12 h、15 d的6061铝合金颈缩与失效断裂的临界应变量为0.078、0.086、0.079。图10所示为铝合金轴向拉伸实验后试样的宏观形貌。对比拉伸后试样表面形貌特征可知,停放0 h试样拉伸变形后表面光滑;而停放12 h试样的表面较为粗糙,其断口附近呈现出类似于橘皮的凹凸。橘皮现象的主要原因是合金内晶粒的粗大不均匀。当粗大的晶粒受到外力作用时,晶粒沿受力方向拉长,并发生畸变;由于晶粒发生变形的方向不一致,其滑移方向上的剪应力在方向、大小上存在的差异,使得合金内各个晶粒产生不同的变形。这种由应力与变形导致的不均匀性,使合金表面产生了凹凸不平的变形。由图3可知,停放12 h的6061铝合金材料内部晶粒粗大且尺寸不均,是导致试样表面出现橘皮现象的主要原因。

图9 合金的应力-应变曲线二阶微分
Fig. 9 Second-order differential of stress and strain curves of alloy
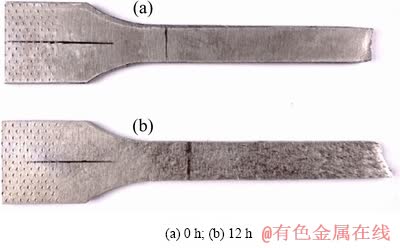
图10 不同停放时间下拉伸试样的宏观表面
Fig. 10 Macroscopic surfaces of tensile specimens under different quench delay time
2.3 SEM分析
采用扫描电镜观察铝合金的拉伸断口,分析不同停放时间下拉伸试样断口韧窝大小、深浅以及第二相的大小和分布。图11(a)所示为停放2 h时拉伸试样的断口SED像,由图11(a)可知,试样断口表面分布着大量的韧窝,韧窝的深度较浅,韧窝多呈圆形且直径较小,部分尺寸较大的韧窝中包含尺寸更小的韧窝,形成“韧窝中的韧窝”。在尺寸较大的韧窝边缘及部分韧窝中能够观察到明显的微孔,其成因是由于第二相粒子受力后脱出基体所致。除韧窝外,断口表面还存在一定的台阶状区域,因此停放2 h时的6061铝合金塑性较差,韧性断裂中包含着脆性断裂。图11(b)所示为停放2 h时合金的BSD像,清晰反映了合金的第二相分布及形貌。由图11(b)可知,第二相粒子的形貌主要为球状及板条状,尺寸约为5 μm,且分布较为均匀,主要集中在韧窝的内部,部分较小的第二相也出现在韧窝边缘。
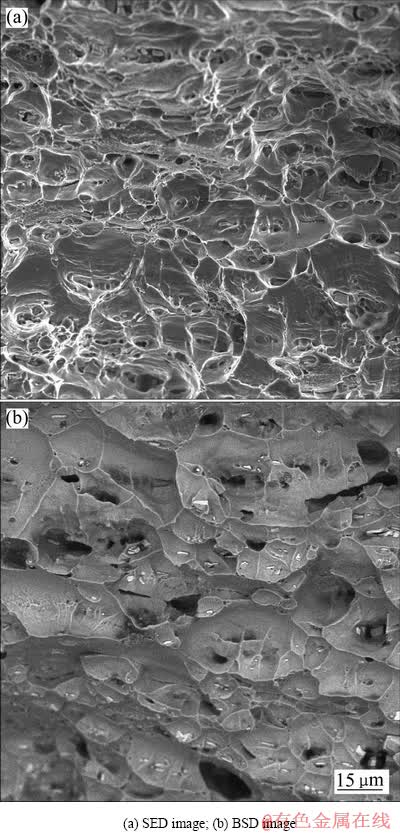
图11 停放2 h时铝合金的SEM像
Fig. 11 SEM images of aluminum alloy parked for 2 h
图12(a)所示为停放12 h时拉伸实验断口的SED像。由图12(a)可以看出,与停放2 h相比,断口的显微形貌出现了明显变化:断口表面台阶状花纹彻底消失,并出现了更多的韧窝,韧窝分布较密集,这些韧窝直径变化不大但形状更圆,大韧窝中包含小韧窝的情况减少,但韧窝边界的微孔仍然大量存在。除此之外,还可以看到部分韧窝的深度明显增加,难以直接观察到韧窝中的第二相粒子。图12(b)所示为停放12 h时合金的BSD像。在此停放时间下,第二相出现明显变化,原先较为均匀且分散的第二相粒子变得更加集中,一个较小的韧窝中可能聚集了多个第二相粒子。第二相粒子多分布在韧窝之中,几乎每个韧窝中都能观察到第二相粒子。此停放时间下的第二相中长条状粒子的厚度有所增加,且数量明显减少,取而代之的是多边形状的粒子。

图12 停放12 h时铝合金的SEM像
Fig. 12 SEM images of aluminum alloy parked for 12 h
图13(a)所示为停放24 h时拉伸实验断口的SED像,与之前相比,最显著的变化是韧窝直径明显增大,形状不一且伴有被拉长的畸变现象。大韧窝中包含小韧窝的情况进一步减少,韧窝边界的微孔也出现减少的迹象。韧窝的深度较深,但能够直接观察到尺寸较大的第二相粒子。图13(b)所示为停放24 h时合金的BSD像。由图13(b)可以发现,停放24 h时,试样中小尺寸的第二相粒子出现聚集现象,某些韧窝中的二次相粒子甚至超过10颗以上;与之前不同的是,一些较大尺寸的第二相粒子也有聚集,部分韧窝中甚至出现了约10 μm的第二相,其周围分布着一些较小的第二相。
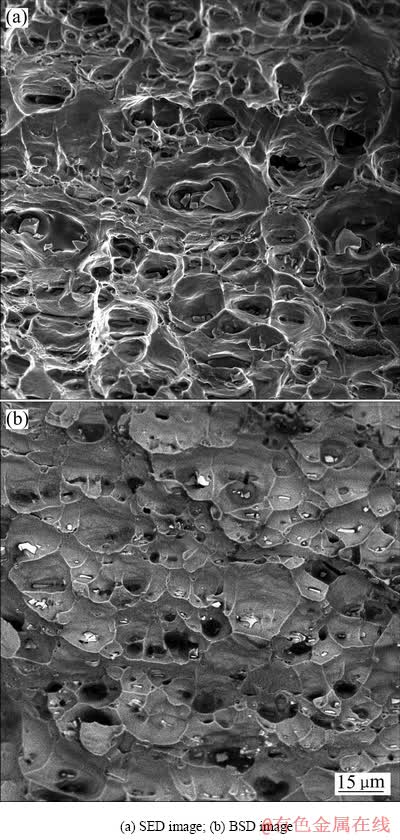
图13 停放24 h时铝合金的SEM像
Fig. 13 SEM images of aluminum alloy parked for 24 h
图14(a)所示为停放15 d时拉伸实验断口的SED像。与停放24 h相比,可以发现此时的韧窝数量变少且直径明显变小,多为较小的圆形韧窝或较大的椭圆韧窝,此时大韧窝中包含小韧窝的情况基本消失。部分断口处出现了一些脆性断裂的痕迹,表现为台阶状花纹。图14(b)所示为停放15 d时合金的BSD像,可看出此时的断口内第二相粒子明显长大且分布较不均匀,小尺寸粒子聚集现象不再出现。此时的第二相粒子多为厚板状或块状,长条状的第二相粒子较少。第二相粒子多分布在韧窝内,微孔中鲜见第二相粒子。
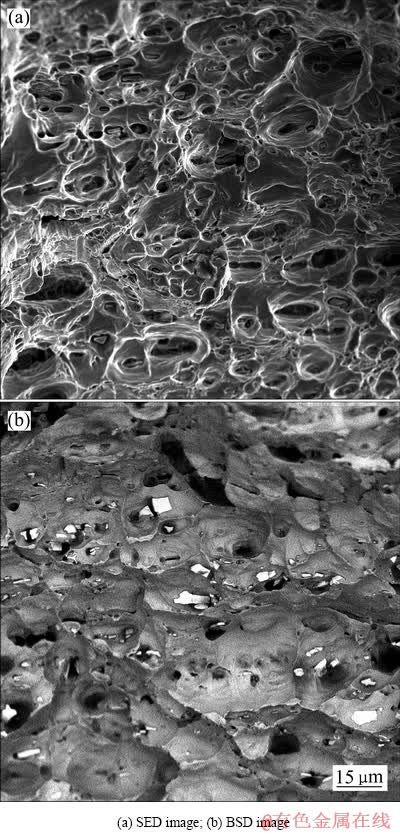
图14 停放15 d时铝合金的SEM像
Fig. 14 SEM images of aluminum alloy parked for 15 d
图15(a)所示为停放30 d时拉伸实验断口的SED像,可明显看出,此时韧窝形貌与停放15 d时的已经区别不大,此时韧窝直径进一步减小,且椭圆形韧窝数量减少,韧窝形状多为圆形,韧窝深度变浅;部分断口较为平整并呈现台阶状,这是脆性断裂的特征。图15(b)所示为停放30 d时合金的BSD像,与停放 15 d相比,部分第二相粒子尺寸变大,但分布规律基本相同,粒子形状多为多边形块状,散布在韧窝中。
总之,停放2 h时的断口表面较为平整,韧窝的数量较少,直径小且浅,韧窝边缘有微孔,且出现韧窝中包含韧窝的现象;第二相粒子多为圆球状和长条状多边形,分布在韧窝和微孔中,大小相对均匀。停放12 h时,韧窝的数量明显增加,且直径变大、深度变深,韧窝周围微孔仍大量存在且明显变大,第二相粒子开始出现聚集,一个韧窝中可能出现几个第二相粒子。停放24 h时,韧窝直径进一步增大且深度较深,韧窝周边的微孔数量减少但尺寸变大,第二相尺寸变大,部分甚至达到10 μm,部分大尺寸的第二相粒子参与到粒子聚集。停放15 d时,小尺寸第二相粒子不再聚集,出现尺寸较大的第二相粒子,此时断口韧窝直径较小,深度较浅,部分区域出现台阶状断口,停放30 d的断口形貌与停放15 d时的相近。
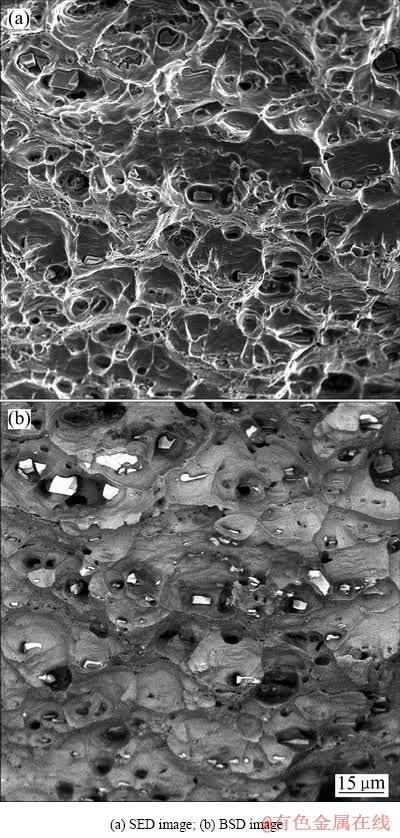
图15 停放30 d时铝合金的SEM像
Fig. 15 SEM images of aluminum alloy parked for 30 d
2.4 EDS分析
6000系铝合金中的富铁相主要分为α-AlFeSi和β-AlFeSi两类。α-AlFeSi主要有立方晶体和六方晶体两种结构,按形状分主要有汉字状、粒状和多边形 状[15]。α-AlFeSi按化学计量大致分为Al12Fe3Si2、Al8Fe2Si与Al12Fe3Si,其中Fe与Si的摩尔比约为1.38~2.75。β-AlFeSi为单斜晶体结构,多为长条板状,主要有Al5FeSi和Al9Fe2Si2两种,Fe与Si的摩尔比约为0.8~1.13[16]。由于试样已经过热处理,因此,合金中的β-AlFeSi相应较少,可通过计算Fe与Si的原子比来判断第二相种类[17]。
图16所示为停放2h时合金的微观组织和元素分布,表2所列为各点元素的摩尔分数。结合图16 表2可以看出,除Al基体外,Mg元素分布也较为广泛,Fe与Si元素分布情况较为相似,因此,可以判断图中第二相中包含富铁相。通过计算可以看出,点1和点5位置的主要成分是Al基体,含有少量的Mg化合物且不含Fe;点2、3、4的Fe与Si摩尔比分别为1.67、1.67、1.64,因此,可推断该点为α-AlFeSi。
图17所示为停放12 h时合金的微观组织和元素分布,表3所列为各点元素的摩尔分数。结合图17和表3可以看出,点5、点6与点8的Fe与Si摩尔比为1.86、2.49及2.00,推测为α-AlFeSi相;同时,点2、点3与点4出现了一种Fe浓度很高的第二相,其中Si不足以与如此高浓度的Fe形成化合物,该第二相呈现出多边形或板状形貌。
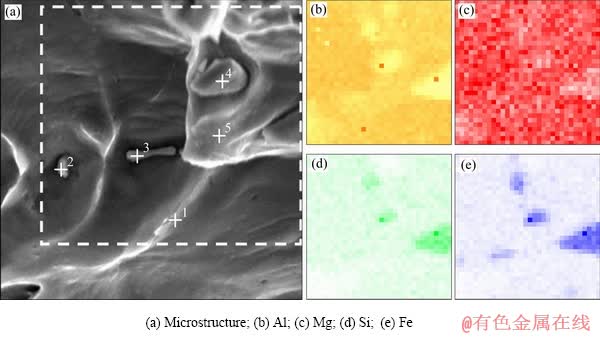
图16 停放2 h时6061铝合金显微组织与元素分布
Fig. 16 Microstructures and elements distributions of 6061 aluminum alloy parked for 2 h
表2 停放2 h时6061铝合金元素的浓度
Table 2 Elements concentration of 6061 aluminum alloy parked for 2 h
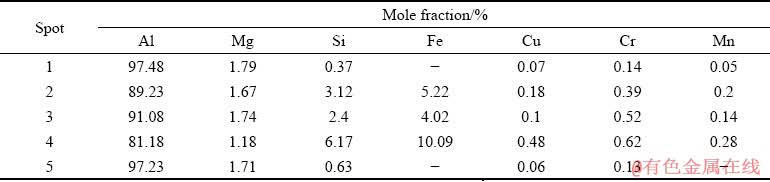
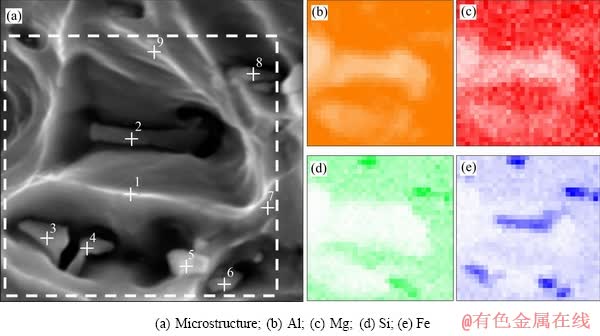
图17 停放12 h时6061铝合金显微组织与元素分布
Fig. 17 Microstructures and elements distributions of 6061 aluminum alloy parked for 12 h
表3 停放12 h时6061铝合金元素的浓度
Table 3 Element concentration of 6061 aluminum alloy parked for 12 h
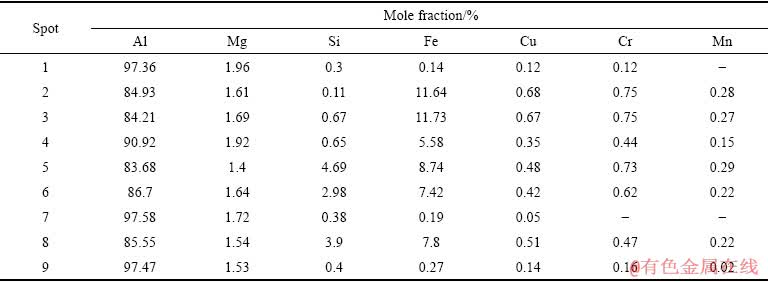
图18所示为停放24 h时合金的微观组织和元素分布,表4所列为各点元素的摩尔分数。结合图18和表4可以看出,点1、2、3、4中含高浓度Fe的第二相进一步增多,且Fe浓度进一步提高,第二相较粗大且形状呈多边形,各点Al与Fe摩尔比分别为2.87、4.74、3.20、2.78,该第二相可能为Al3Fe。此外,点5、点6为α-AlFeSi相。
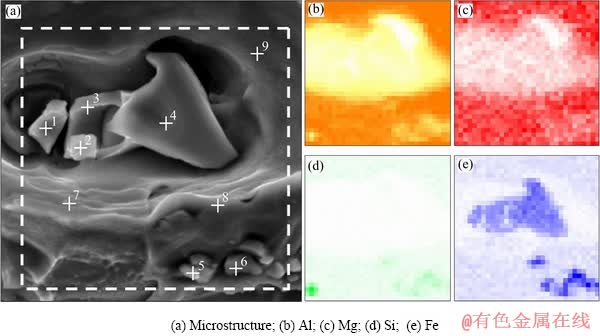
图18 停放24 h时6061铝合金显微组织与元素分布
Fig. 18 Microstructure and elements distribution of 6061 aluminum alloy parked for 24 h
表4 停放24 h时6061铝合金元素浓度
Table 4 Element concentration of 6061 aluminum alloy parked for 24 h
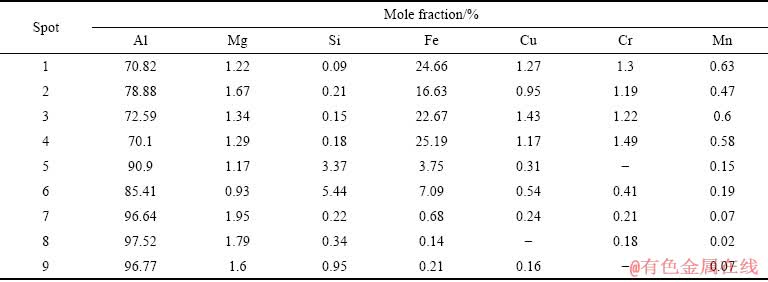
时效过程中的析出序列和形貌演变过程已确定为过饱和固溶体→原子团簇→GP区→β″相→ β′/U1/U2/B′/Q′相→β/Q/相+Si。针状β″相和棒状β′/U1/U2/B/Q′相等被认为是亚稳相,片状β相为最终平衡相[18-19]。停放过程中,过饱和的溶质原子将逐渐形成GP区。当GP区的尺寸小于临界尺寸时,已形成的GP区将会在人工时效时重新溶入固溶体,而停放时间延长,GP区尺寸逐渐长大,在12 h时,GP尺寸相当;进行人工时效时,产生部分回归,部分溶质原子再次溶入基体,但仍保留了足够的GP区,在人工时效时达到稳定,形核率高。人工时效时,Mg和Si原子继续向形成的GP区偏聚长大,利于强化相弥散析出。停放24 h后,第二相仍能均匀弥散析出,表现出强度的回升[12, 20]。
根据[21]文献,富含Fe的第二相粒子在铸造初期即存在,通过均匀化难以消除。在停放过程中,偏聚长大;Si在机体的溶解度小于Mg,固溶处理后,最先析出,与Fe形成α-AlFeSi,造成后期人工时效影响Mg2Si相析出的数量,降低了时效析出强化效果,使强化相数量减少;强化相强化效果弥补不了杂质相对强度的影响,最终使该条件下强化效果减小。因此,合金在停放12~24 h时,6061合金的强度有所下降。合金中的析出强化相具有很高的稳定性[22]。结合SED和EDS结果可见,随着停放时间的延长,富含Fe的第二相粒子(主要为α-AlFeSi)长大程度较高;当停放时间超过12 h时,富Fe的第二相粒子随着停放时间的延长,其大小和形态都发生了变化,从多边形变为粗大的板条状,对材料的拉伸性能产生了影响,导致其伸长率下降。
3 结论
1) 停放时间对6061铝合金的晶粒尺寸有较大影响,呈先增大后减小的趋势;停放时间为6~12 h时,晶粒尺寸最大为74.5 μm;停放时间超过24 h后,晶粒尺寸逐步减小至59 μm。
2) 6061铝合金在停放2 h内力学性能变化较小;当停放时间增加至12~24 h时,抗拉强度和屈服强度降至最低,但伸长率提高,屈强比降低,材料综合性能最优;继续增加停放时间,合金强度回升,停放15 d后,合金的性能趋于稳定。
3) 停放时间对6061铝合金弹性及塑性阶段变形的影响很小,但对弹塑性变形过渡阶段有较大影响。停放0h试样表面光滑,厚度均匀减薄,颈缩变形区较长;停放12 h试样表面呈橘皮形貌,变形均匀性较低,颈缩主要集中在断口1~2 mm处。
4) 随着停放时间的增长,6061铝合金断口的韧窝直径和深度不断增加,第二相粒子的尺寸也不断增大,形状由球状、带状逐渐转变为板状、块状。
REFERENCES
[1] SONG F X, ZHANG X M, LIU S D, TAN Q, LI D F. The effect of quench transfer time on microstructure and localized corrosion behavior of 7050-T6 Al alloy[J]. Materials and Corrosion, 2014, 65(10): 1007-1016.
[2] YOU J H, LIU S D, ZHANG X M, ZHANG X Y. Influence of quench transfer time on microstructure and mechanical properties of 7055 aluminum alloy[J]. Journal of Central South University of Technology, 2008, 15(2): 153-158.
[3] ROBINSON J S, TIERNAN P J, KELLEHER J F. Effect of post-quench delay on stress relieving by cold compression for the aluminium alloy 7050[J]. Materials Science and Technology, 2015, 31(4): 409-417.
[4] 祝伟忠, 王虎臣, 王 煜. A6N01-T5铝合金型材力学性能与停放时间的关系[J]. 轻合金加工技术, 2007, 35(9): 27-29.
ZHU Zhong-wei, WANG Hu-chen, WANG Yu. Relation between mechanical properties and placed time for A6N01-T5 aluminium alloy profiles[J]. Light alloy fabrication technology, 2007, 35(9): 27-29.
[5] 张洪辉, 王 坤, 刘景胜. 6061合金时效及停放效应的工艺探讨[J]. 材料研究与应用, 2011, 5(3): 233-235.
ZHANG Hong-hui, WANG Kun, LIU Jing-sheng. Technology discussion on the aging and stay time effect of 6061 alloy[J]. Materials Research and Application, 2011, 5(3): 233-235.
[6] CESCHINI L, MORRI A, MORRI A. Effects of the delay between quenching and aging on hardness and tensile properties of A356 aluminum alloy[J]. Journal of Materials Engineering and Performance, 2013, 22(1): 200-205.
[7] 刘文军, 刘胜胆, 张新明, 陈 慧, 钟奇鸣. 淬火转移时间对1933铝合金拉伸性能、腐蚀性能及微观组织的影 响[J]. 中南大学学报(自然科学版), 2012, 43(4): 1276-1280.
LIU Wen-jun, LIU Sheng-dan, ZHANG Xin-min, CHEN Hui, ZHONG Qi-ming. Influence of quench transfer time on tensile properties, corrosion properties and microstructure of 1933 aluminum alloy[J]. Journal of Central South University (Science and Technology), 2012, 43(4): 1276-1280.
[8] CAMPESTRINI P, ROOIJEN H W V, WESTING E P M V, WIT J H W D. Influence of quench delay time on the corrosion behavior of aluminium alloy 2024[J]. Materials & Corrosion, 2000, 51(9): 616-627.
[9] 伊琳娜, 汝继刚. 停放时间对7B04铝合金性能的影响[J]. 稀有金属, 2004, 28(1): 179-181.
YI Lin-na, RU Ji-gang. Effect of delay time on properties of 7B04 aluminum alloy[J]. Chinese Journal of Rare Metals, 2004, 28(1): 179-181.
[10] 宋伟苑, 林高用, 李 琪. 人工时效前停放时间对7055铝合金挤压管显微组织与性能的影响[J]. 有色金属科学与工程, 2018, 9(5): 41-46.
SONG Wei-yuan, LIN Gao-yong, LI Qi. Influence of conditioning time before artificial aging on the microstructure and properties of 7055 aluminium alloy extruded tube[J]. Nonferrous Metals Science and Engineering, 2018, 9(5): 41-46.
[11] 杜 君. 7020铝合金挤压产品停放时间对力学性能的影响[J]. 铝加工, 2018(2): 15-16.
DU Jun. Effect of storage period on mechanical property of 7020 aluminum alloy extrusions[J]. Aluminium Fabrication, 2018(2): 15-16.
[12] 王雪玲, 于莉莉, 赵永军, 谢延翠, 石广福, 王春辉, 张淑艳. 时效前停放时间和时效保温时间对6082-T651铝合金板材组织和性能的影响[J]. 轻合金加工技术, 2011, 39(2): 25-28.
WANG Xue-ling, YU Li-li, ZHAO Yong-jun, XIE Yan-cui, SHI Guang-fu, WANG Chun-hui, ZHANG Shu-yan. Influence of holding time both before and during aging on structure and properties of 6083-T651 plate[J]. Light Alloy Fabrication Technology, 2011, 39(2): 25-28.
[13] 刘星兴, 唐建国, 张新明, 谈 琦, 王莹莹, 邓运来. 双级淬火对车身板用6016铝合金烤漆硬化效应的影响[J]. 中国有色金属学报, 2014, 24(5): 1186-1193.
LIU Xing-xing, TANG Jian-guo, ZHANG Xin-ming, WANG Ying-ying, DENG Yun-lai. Influence of interrupted quenching on paint-bake response of AA6016 Al alloy sheet[J]. The Chinese Journal of Nonferrous Metals, 2014, 24(5): 1186-1193.
[14] 李 翔, 唐建国, 张新明, 凌利月, 刘文辉, 廖志宇, 杨 涛, 邓运来. 温变形对汽车车身用6061铝合金自然时效及力学性能的影响[J]. 中国有色金属学报, 2016, 26(1): 1-6.
LI Xiang, TANG Jian-guo, ZHANG Xin-ming, LING Li-yue, LIU Wen-hui, LIAO Zhi-yu, YANG Tao, DENG Yun-lai. Effect of warm deformation on natural ageing and mechanical property of aluminum alloy 6061 sheets for automotive body[J]. The Chinese Journal of Nonferrous Metals, 2016, 26(1): 1-6.
[15] 张 静, 彭 建, 潘复生. 工业纯铝中的化合物相[J]. 轻合金加工技术, 2000, 28(5): 1-6.
ZHANG Jing, PENG Jian, PAN Fu-sheng. Intermetallic compounds in commercial-purity aluminium[J]. Light Alloy Fabrication Technology, 2000, 28(5): 1-6.
[16] VERMA A, KUMAR S, GRANT P S, O'REILLY K A Q. Influence of cooling rate on the Fe intermetallic formation in an AA6063 Al alloy[J]. Journal of Alloys & Compounds, 2013, 555(13): 274-282.
[17] 张 静, 潘复生, 左汝林, 王文高. AA1235铝箔坯料的中温相转变[J]. 中国有色金属学报, 2006, 16(8): 1394-1399.
ZHANG Jing, PAN Fu-sheng, ZUO Ru-lin, WANG Wen-gao. Medium temperature phase transformation in AA1235 aluminium sheets for foils[J]. The Chinese Journal of Nonferrous Metals, 2006, 16(8): 1394-1399.
[18] EDWARDS G A, STILLER K, DUNLOP G L, COUPER M J. The precipitation sequence in Al-Mg-Si alloys[J]. Acta Materialia, 1998,46(11): 3893-3904.
[19] 贾志宏, 丁立鹏, 吴赛楠, 王雪丽, 刘 庆, 陈昌云. 汽车车身用6000系铝合金板材微观组织与热处理工艺的研究进展[J]. 材料工程, 2014, 42(12): 104-113.
JIA Zhi-hong, DING Li-peng, WU Sai-nan, WANG Xue-li, LIU Qing, CHEN Chang-yun. Research progress on microstructure and heat treatment of 6000 series aluminum alloys sheet for automotive body[J]. Journal of Materials Engineering, 2014, 42(12): 104-113.
[20] 凡晓波. 6A02铝合金板材热成形淬火一体化工艺强化机理研究[D]. 哈尔滨: 哈尔滨工业大学, 2012.
FAN Xiao-bo. Research on strengthening mechanism of integrated process of quenching-hot forming for aluminium 6A02 sheet[D]. Harbin: Harbin Institute of Technology, 2012.
[21] 杜 鹏, 闫晓东, 李彦利, 沈 健. 6061铝合金中富铁相在均匀化过程中的相变机理[J]. 中国有色金属学报, 2011, 21(5): 981-986.
DU Peng, YAN Xiao-dong, LI Yan-li, SHEN Jian. Transformation mechanism of iron-rich phase in 6061 aluminum alloy during homogenization[J]. The Chinese Journal of Nonferrous Metals, 2011, 21(5): 981-986.
[22] 冯银成, 李落星, 刘 杰, 刘 波, 刘扬胜. 自然时效对6061铝合金显微组织和力学性能的影响[J]. 机械工程材料, 2011, 35(5): 18-21.
FENG Yin-cheng, LI Luo-xing, LIU Jie, LIU Bo, LIU Sheng-yang. Effect of natural aging on microstructure and mechanical properties of 6061 aluminium alloy[J]. Materials for Mechanical Engineering, 2011, 35(5): 18-21.
Influence of quench delay time on mechanical properties and microstructure of 6061 aluminum alloy
KOU Lin-yuan1, 2, WANG Guan1, 2, MA Chao1, BIAN Dong-wei1
(1. School of Mechanical Engineering, Ningxia University, Yinchuan 750021, China
2. Ningxia Key Laboratory of computer Aided Engineering Technology for Intelligent Equipment, Ningxia University, Yinchuan 750021, China)
Abstract: The dependence of the mechanical properties and microstructure of 6061 aluminum alloy under different quench delay time were investigated by the combination of macro-detection and micro-analysis. The results show that the quench delay time has a great influence on the grain size of 6061 aluminum alloy, and the grain size increases first and then decreases. The quench delay time has a great influence on the elastic-plastic transition deformation of 6061 aluminum alloy, but has little effect on the elastic deformation. The 6061 aluminum alloy has no obvious change in mechanical properties during quench delay time of 0-2 h. After deformation, the surface of the specimens is smooth and the deformation coordination is better. When the quench delay time is 12 h, the tensile strength and yield strength of the material are minimized, but the elongation increases. Meanwhile, the surfaces of the specimens show the appearance of orange peel and the deformation uniformity is poor. When the quench delay time is 12 h-15 d, the strength of the alloy rises and gradually stabilizes. The results of microscopic analysis show that, with the increase of quench delay time, the diameter and depth of the dimples of the 6061 aluminum alloy fracture increase, and the sizes of the second phase particles also increase. The shapes gradually change from spheres and ribbons to plates and blocks. The optimal quench delay time of 6061 aluminum alloy is 12-24 h. The research results can provide theoretical guidance for the optimization of 6061 aluminum alloy processing technology.
Key words: 6061aluminum alloy; quench delay time; mechanical properties; microstructure
Foundation item: Project(2018AAC03061) supported by the Natural Science Foundation of Ningxia Province, China; Project(51605234) supported by the National Natural Science Foundation of China; Project(2017, Western Light) supported by Key Research and development Program of Ningxia Province, China; Project(ZKZD2017010) supported by the Major Innovation Projects for Building First-Class Universities in China’s Western Region
Received date: 2019-04-02; Accepted date: 2019-10-09
Corresponding author: WANG Guan; Tel: +86-13895189949; E-mail: belonging@163.com
(编辑 李艳红)
基金项目:宁夏自然科学基金资助项目(2018AAC03061);国家自然科学基金资助项目(51605234);宁夏重点研发计划资助项目(2017,西部之光);西部一流重大创新项目(ZKZD2017010)
收稿日期:2019-04-02;修订日期:2019-10-09
通信作者:王 冠,副教授,博士;电话;13895189949;E-mail:belonging@163.com