
Influence of extrusion temperature on microstructure and mechanical properties of Mg-4Y-4Sm-0.5Zr alloy
LI Da-quan(李大全)1, 2, WANG Qu-dong(王渠东)2, DING Wen-jiang(丁文江)2, J. J. BLANDIN3, M. SU?RY3
1. National Engineering Research Center for Nonferrous Metals Composites,
General Research Institute for Nonferrous Metals, Beijing 100088, China;
2. National Engineering Research Center of Light Alloys Net Forming,
State Key Laboratory of Metal Matrix Composites, School of Materials Science and Engineering,
Shanghai Jiao Tong University, Shanghai 200240, China;
3. Université de Grenoble, Grenoble INP, Science et Ingénieriedes Matériaux et Procédés (SIMAP),
CNRS UMR 5266, UJF, BP 46, 38402 Saint-Martin d’Héres Cedex, France
Received 23 September 2009; accepted 30 January 2010
Abstract: The solution-treated Mg-4Y-4Sm-0.5Zr alloy was extruded at temperatures from 325 ?C to 500 ?C. Dynamic recrystallization (DRX) completely occurs when the alloy is extruded at 350℃ and above. The grains of the extruded alloy are obviously refined by the occurrence of DRX. The average grain size of the extruded alloy increases with increasing the extrusion temperature, leading to a slight decrease of the ultimate tensile strength (UTS) and the yield strength (YS). On the contrary, the UTS and YS of the extruded and aged alloy increase with increasing the extrusion temperature. Values of UTS of 400 MPa, YS larger than 300 MPa and elongation (EL) of 7% are achieved after extrusion at 400 ?C and ageing at 200 ?C for 16 h. Both grain refinement and precipitation are efficient strengthening mechanisms for the Mg-4Y-4Sm-0.5Zr alloy.
Key words: Mg-Y-Sm-Zr alloy; extrusion; heat treatment; ageing; mechanical properties
1 Introduction
There has been a rapidly growing interest in the development of high strength, and high creep-resistant magnesium alloys for the automotive and aerospace industries[1-8]. But, the use of magnesium alloys has been limited in the past owing to their poor mechanical properties and low formability[9-11].
It has been demonstrated that rare earth metals (RE) are the most effective elements to improve the strength of magnesium especially at elevated temperatures [12-13]. A recently developed Mg-4Y-4Sm-0.5Zr alloy was shown to exhibit promising mechanical properties[14]. The microstructural evolution during heat treatments and mechanical properties of the as-cast Mg-4Y-4Sm-0.5Zr alloy were further investigated [15-16].
Generally, wrought magnesium alloys have superior mechanical properties to cast magnesium alloys, due to such mechanisms as the refinement of grains, the elimination of casting defects and the homogenization of the microstructure during the plastic deformation processes[17].
The aim of the present work is to investigate the influence of the extrusion temperature on microstructure evolution and mechanical properties of the Mg-4Y-4Sm-0.5Zr alloy.
2 Experimental
The material used in this investigation was Mg-4Y-4Sm-0.5Zr alloy (mass fraction, %). The alloy was solution-treated at 525 ?C for 8 h before extrusion. Details of the casting and solution treatment procedure were described in an earlier publication[15]. The solution-treated Mg-4Y-4Sm-0.5Zr alloy was extruded at 325, 350, 400, 450 and 500 ?C with an extrusion ratio of 10?1. After extrusion, some of the specimens were isothermally aged at 200 ?C for up to 128 h in an oil-bath.
The room temperature tensile properties were tested by a Zwick/Roell testing machine with the tensile axis parallel to the extrusion direction. The ageing responses of the alloy were checked by hardness measurement. Hardness was measured with a Vickers-hardness tester under a load of 300 N.
The microstructures of the alloy were examined using a LEICA MEF4M optical microscope and the average grain size was measured by the linear intercept method. The specimens were mechanically polished and etched with a dilute solution of 4% nitric acid in alcohol.
3 Results and discussion
3.1 Microstructure evolution
The microstructure of the solution-treated Mg-4Y-4Sm-0.5Zr alloy is shown in Fig.1. Almost all the eutectic phases are dissolved into the Mg matrix, and the average grain size is 60 μm.
Fig.2 shows optical micrographs of the Mg-4Y- 4Sm-0.5Zr alloy extruded at different temperatures in the transverse section. It is clearly confirmed that dynamic
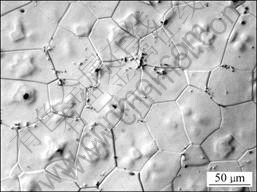
Fig.1 Optical micrograph of solution-treated Mg-4Y-4Sm-0.5Zr alloy
Fig.2 Microstructures of Mg-4Y-4Sm-0.5Zr alloy extruded at different temperatures: (a) 325 ?C; (b) 350 ?C; (c) 400 ?C; (d) 450 ?C; (e) 500 ?C
recrystallization (DRX) partially occurs during extrusion at 325 ?C. Some very fine recrystallized grains coexist with the un-recrystallized matrix. DRX completely occurs when the alloy is extruded at 350 ?C and above. The grains of the extruded alloy are evidently refined by the occurrence of DRX. The average grain size of the extruded alloy increases with increasing the extrusion temperature.
3.2 Tensile properties
The mechanical properties of the Mg-4Y-4Sm-0.5Zr alloy after extrusion at different temperatures from 325 ?C to 500 ?C are shown in Fig.3. The ultimate tensile strength (UTS) and more evidently the yield strength (YS) of the alloy extruded at 325 ?C are larger than those of the alloy extruded at 350 ?C and above. It is attributed to the partially recrystallized microstructure of the material at this temperature. Indeed, when the alloy is extruded at 325 ?C, DRX just partially occurs so that the other part of the microstructure is still strain hardened. As a result, the YS and UTS are larger. However, the elongation to fracture (EL) is small accordingly. When the alloy is extruded at 350 ?C and above, DRX has completely occurred; the recrystallized grains are fine and homogeneously distributed. As a result, the EL increases evidently. The ELs of the alloy extruded at 350 ?C and above are all larger than 20%. The UTS and the YS of the alloy extruded at 350 ?C and above decrease slightly with increasing the extrusion temperature owing to the increase of the grain size with increasing the extrusion temperature.
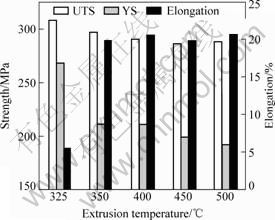
Fig.3 Mechanical properties of Mg-4Y-4Sm-0.5Zr alloy after extrusion at different temperatures
The hardness curves of the Mg-4Y-4Sm-0.5Zr alloy extruded at different temperatures and then aged at 200 ?C for different times are shown in Fig.4. The hardness of the alloy extruded at 325 ?C is evidently larger, in agreement with the results of the tensile experiments. When the alloy is extruded at 350 ?C and above, DRX
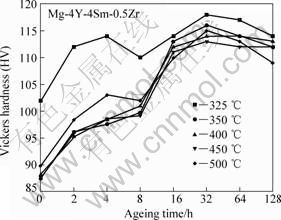
Fig.4 Hardness curves of Mg-4Y-4Sm-0.5Zr alloy extruded at different temperatures and then aged at 200 ?C for different times
completely occurs. The alloys exhibit very similar microstructures in these conditions. As a result, the alloys exhibit a very similar starting hardness, and also very similar ageing behaviors. The maximum hardness is reached after ageing at 200 ?C for 32 h; and the hardness of the alloy in the peak-aged state is evidently much larger than that in the extrusion state. The precipitation strengthening effect is, therefore, very effective for the extruded alloys. It was reported in the previous publication[18] that, when the extruded Mg-4Y-4Sm- 0.5Zr alloy is aged at 200 ?C for 16 h, numerous fine globular β′ precipitates homogeneously form within the grains, which leads to a very efficient strengthening.
The mechanical properties of the Mg-4Y-4Sm-0.5Zr alloy extruded at different temperatures and then aged at 200 ?C for 16 h are shown in Fig.5. The UTS and YS of the extruded alloy are greatly enhanced after ageing, but the EL of the extruded alloy decreases accordingly. The UTS and YS of the extruded and aged alloy increase with
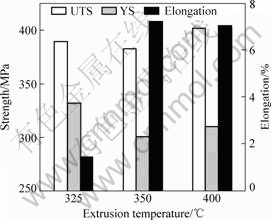
Fig.5 Mechanical properties of Mg-4Y-4Sm-0.5Zr alloy extruded at different temperatures and then aged at 200 ?C for 16 h
increasing the extrusion temperature when the alloy is extruded at 350 ?C and above. When the alloy is extruded at higher temperature, more Y and Sm elements are present in solid solution in the extruded alloy. Therefore, it is reasonable to assume that the precipitation hardening effect of the extruded alloy is larger, which results in a higher UTS and YS.
The tensile properties of the Mg-4Y-4Sm-0.5Zr alloy in different states are shown in Fig.6. It is shown that the UTS and YS of the alloy are greatly enhanced after the extrusion and aging treatment. After extrusion at 400 ?C, the increment of UTS is more than 50 MPa, and the increment of YS is nearly 100 MPa. These increases are mainly due to the grain refinement strengthening. After ageing at 200 ?C for 16 h, both the increment of UTS and YS are more than 100 MPa. This is mainly due to the precipitation strengthening of the alloying elements Y and Sm. A UTS of 400 MPa, a YS of more than 300 MPa and an EL of 7% are achieved after extrusion at 400 ?C and ageing at 200 ?C for 16 h. It is thus concluded that both grain refinement and precipitation are very efficient strengthening mechanisms for the Mg-4Y-4Sm-0.5Zr alloy.
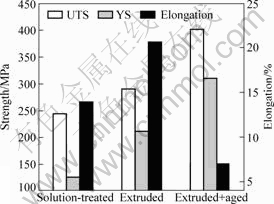
Fig.6 Tensile properties of Mg-4Y-4Sm-0.5Zr alloy in different states (extruded at 400 ?C; aged at 200 ?C for 16 h)
4 Conclusions
1) When the Mg-4Y-4Sm-0.5Zr alloy is extruded at 350 ℃ or above, DRX completely occurs. The grains of the extruded alloys are evidently refined by the occurrence of DRX. The average grain size of the extruded alloys increases with increasing the extrusion temperature.
2) The UTS and YS of the extruded Mg-4Y-4Sm-0.5Zr alloy decrease slightly with increasing the extrusion temperature owing to the increase of the grain size. On the contrary, the UTS and YS of the extruded alloy increase with increasing the extrusion temperature after ageing and this is due to the precipitation strengthening.
3) A UTS of 400 MPa, a YS of more than 300 MPa and an elongation of 7% are achieved after extrusion at 400 ?C and ageing at 200 ?C for 16 h. Both grain refinement and precipitation are, therefore, very efficient strengthening mechanisms for the Mg-4Y-4Sm-0.5Zr alloy.
Acknowledgements
The authors acknowledges the financial support of the French Ministry of Foreign Affairs and of the Rhone-Alpes Regional Council through the ARCUS Programme, and of the visiting study programme for doctoral students abroad from Shanghai Jiao Tong University.
References
[1] LI Zhi-cheng, ZHANG Hong, LIU Lu, XU Yong-bo. Growth and morphology of β phase in an Mg-Y-Nd alloy [J]. Mater Lett, 2004, 58(24): 3021-3024.
[2] ZHENG Kai-yun, DONG Jie, ZENG Xiao-qin, DING Wen-jiang. Effect of pre-deformation on aging characteristics and mechanical properties of Mg-Gd-Nd-Zr alloy [J]. Trans Nonferrous Met Soc China, 2007, 17: 1164-1168.
[3] CHANG Jian-wei, GUO Xing-wu, FU Peng-huai, PENG Li-ming, DING Wen-jiang. Relationship between heat treatment and corrosion behaviour of Mg-3.0%Nd-0.4%Zr magnesium alloy [J]. Trans Nonferrous Met Soc China, 2007, 17: 1152-1157.
[4] ZOU Hong-hui. Effects of microstructure on creep behavior of Mg-5%Zn-2%Al(-2%Y) alloy [J]. Trans Nonferrous Met Soc China, 2008, 18: 580-587.
[5] SALMAN S A, ICHINO R, OKIDO M. Improvement of corrosion resistance of AZ31 Mg alloy by anodizing with co-precipitation of cerium oxide [J]. Trans Nonferrous Met Soc China, 2009, 19: 883-886.
[6] ZHANG Jing, LI Zhong-sheng, GUO Zheng-xiao, PAN Fu-sheng. Solidification microstructural constituent and its crystallographic morphology of permanent mould cast Mg-Zn-Al alloys [J]. Trans Nonferrous Met Soc China, 2006, 16: 452-458.
[7] YIN Dong-song, ZHANG Er-lin, ZENG Song-yan. Effect of Zn on mechanical property and corrosion property of extruded Mg-Zn-Mn alloy [J]. Trans Nonferrous Met Soc China, 2008, 18: 763-768.
[8] QIAN Jian-gang, WANG Chun, LI Di, GUO Bao-lan, SONG Guang-ling. Formation mechanism of pulse current anodized film on AZ91D Mg alloy [J]. Trans Nonferrous Met Soc China, 2008, 18: 19-23.
[9] BARBAGALLO S, CAVALIERE P, CERRI E. Compressive plastic deformation of an AS21X magnesium alloy produced by high pressure die casting at elevated temperatures [J]. Mater Sci Eng A, 2004, 367(1/2): 9-16.
[10] MENG Fan-gui, LIU Hua-shan, LIU Li-bin, JIN Zhan-peng. Thermodynamic optimization of Mg-Nd system [J]. Trans Nonferrous Met Soc China, 2007, 17: 77-81.
[11] FENG Xiao-ming, AI Tao-tao. Microstructure evolution and mechanical behavior of AZ31 Mg alloy processed by equal-channel angular pressing [J]. Trans Nonferrous Met Soc China, 2009, 19: 293-298.
[12] ROKHLIN L L, DOBATKINA T V, NIKITINA N I. Constitution and properties of the ternary magnesium alloys containing two rare-earth metals of different subgroups [J]. Mater Sci Forum, 2003, 419/422: 291-296.
[13] MOHRI T, MABUCHI M, SATIO N, NAKAMURA M. Microstructure and mechanical properties of a Mg-4Y-3RE alloy processed by thermo-mechanical treatment [J]. Mater Sci Eng A, 1998, 257: 287-294.
[14] LI Da-quan, WANG Qu-dong, DING Wen-jiang. Characterization of phases in Mg-4Y-4Sm-0.5Zr alloy processed by heat treatment [J]. Mater Sci Eng A, 2006, 428: 295-300.
[15] LI Da-quan, WANG Qu-dong, DING Wen-jiang. Effects of heat treatments on microstructure and mechanical properties of Mg-4Y-4Sm-0.5Zr alloy [J]. Mater Sci Eng A, 2007, 448: 165-170.
[16] LI Da-quan, WANG Qu-dong, DING Wen-jiang. Precipitate phases in the Mg-4Y-4Sm-0.5Zr alloy [J]. J Alloy Compd, 2008, 465: 119-126.
[17] DING H L, LIU L F, KAMADO S, DING W J, KOJIMA Y. Study of the microstructure, texture and tensile properties of as-extruded AZ91 magnesium alloy [J]. J Alloy Compd, 2008, 456: 400-406.
[18] WANG Q D, LI D Q, BLANDIN J J, SU?RY M, DONNADIEU P, DING W J. Microstructure and creep behavior of the extruded Mg-4Y-4Sm-0.5Zr alloy [J]. Mater Sci Eng A, 2009, 516: 189-192.
(Edited by YANG Bing)
Foundation item: Project(2009AA033501) supported by the National Hi-tech Research and Development Program of China; Project(2006BAE04B01-2) supported by the National Key Technology Research & Development Program of China; Project(06SR07104) supported by the International Cooperation Fund of Shanghai Science and Technology Committee, Shanghai/Rhone-Alpes Science and Technology
Corresponding author: WANG Qu-dong; Tel: +86-21-54742715; Fax: +86-21-34202794; E-mail: wangqudong@sjtu.edu.cn
DOI: 10.1016/S1003-6326(09)60296-X