二次铝灰低温碱性熔炼研究
郭学益1,李菲1,田庆华1, 2,计坤1
(1. 中南大学 冶金科学与工程学院,湖南 长沙,410083;
2. 大冶有色金属股份有限公司博士后科研工作站,湖北 黄石,435005)
摘要:研究利用低温碱性熔炼法提取二次铝灰中铝的过程。探讨碱灰质量比、盐灰质量比、熔炼温度、熔炼时间、不同添加剂和不同混料方式等因素对铝浸出率的影响。研究结果表明:优化条件为:碱灰质量比1.3、盐灰质量比0.7(NaNO3)或0.4(Na2O2)、熔炼温度500 ℃、熔炼时间60 min。湿混料可以提高铝浸出率,以NaNO3为添加剂干混料铝浸出率最高可达87.52 %,以NaNO3为添加剂湿混料铝浸出率最高可达92.71%,以Na2O2为添加剂湿混料铝浸出率最高可达92.76%。
关键词:二次铝灰;低温碱性熔炼;铝;NaOH;资源循环
中图分类号:TF821 文献标志码:A 文章编号:1672-7207(2012)03-0809-06
Recovery of aluminium from secondary aluminum dross using low-temperature alkaline smelting
GUO Xue-yi1, LI Fei1, TIAN Qing-hua1, 2, JI Kun1
(1. School of Metallurgical Science and Engineering, Central South University, Changsha 410083, China;
2. Postdoctoral Workstation of Daye Nonferrous Metals Co., Ltd., Huangshi 435005, China)
Abstract: The process of extracting aluminum from secondary aluminum dross using low-temperature alkaline smelting was studied. The factors, including alkali dross ratio, the addition of different addictive, salt dross ratio, smelting temperature, smelting time, and different mix methods in smelting, were addressed during the transfer of Al into water soluble salt. The results show that the optimum conditions of the process are determined as follows: alkali dross ratio 1.3, salt dross ratio 0.7 (NaNO3) or 0.4 (Na2O2), smelting temperature 500 ℃, smelting time 60 min. Wet mixture of the sample can improve the leaching efficiency of aluminum. 87.52% of Al might be leached in water with dry mixing of the sample, while 92.71% of Al may be leached with wet mixing by using NaNO3 as addictive in smelting process, and 92.76% of Al can be dissolved with Na2O2 as additive.
Key words: secondary aluminum dross; low-temperature alkaline smelting; aluminum; NaOH; resources recycling
铝灰产生于所有铝发生熔融的生产工序,含铝量10%~80%不等,其中的铝约占铝生产使用过程中总损失量的1%~12%[1-2]。随着金属铝及铝合金生产规模不断扩大,铝灰的产生量也将成比例增长。因此,寻找经济有效的方法利用和治理铝灰,对实现铝二次资源的有效循环利用有积极的意义[3]。由于存在来源差异,铝灰可分为2种[4-5]:一种是一次铝灰,在电解原铝及铸造等不添加盐熔剂过程中产生,是一种主要成分为金属铝和铝氧化物的混合物,铝含量可达15%~70%;另一种是二次铝灰,经盐浴处理回收一次铝灰或铝合金精炼产生的NaCl,KCl,氟化物,氧化铝和铝的混合物,铝含量较一次铝灰低。碱法冶金是一种清洁冶金技术,可以实现在碱性介质中,将复杂资源中的部分两性金属转化成可溶性碱式盐,从而实现其与其他元素分离。张懿等[6-14]提出使用碱性亚熔盐体系处理钛、铬、钽、铌原生矿产资源和铝二次资源;徐盛明等[15-16]采用碱性熔炼对银精矿进行了研究。肖剑飞 等[17-18]采用低温碱性熔炼法处理铅、铋、锑硫化精矿,工艺直收率、产品质量等技术指标大大优于传统炼工艺。本文作者通过实验研究了低温碱性熔炼法处理二次铝灰的可行性,旨在探索铝灰高效清洁处理工艺,促进铝二次资源循环利用。
1 实验
1.1 实验原料
实验所用原料为某铝厂A356铝合金熔铸过程中产生的二次铝灰,粒度小于150 μm。实验所用NaOH,NaNO3和Na2O2等试剂均为分析纯,实验用水为去离子水。
对铝灰进行X荧光光谱(XRF)分析,结果如表1所示。铝灰中的主要元素为Al,K,Na,F,Si,Mg和Cl等,另外含有少量V,Ti,Ca,Mn,Fe,Zn,S和P等元素。
XRD分析显示铝灰中的主要物相为:Al,α-Al2O3(刚玉),AlN,Si,SiO2,NaCl,KCl和MgAl2O4等,由于表1中其他元素组成物相的丰度太低,未能检出。
表1 铝灰中主要元素含量(质量分数)
Table 1 Main elements content of aluminum dross %

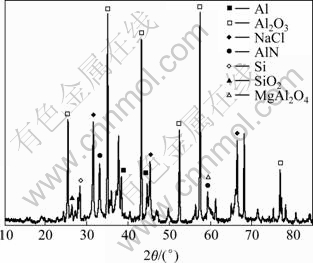
图1 实验用铝灰的XRD谱
Fig.1 XRD pattern of aluminum dross
利用JSM-6360MV型高低真空扫描电子显微镜(含EDAX能谱)对铝灰进行形貌观察和成分测定,显微形貌显示铝灰由大小、形状不一的颗粒组成,各物相形貌各异,为聚集状态,颗粒形貌呈棱片状、细粒状、类球状和长柱状等。图2中各微区元素含量如表2所示。图2(a)中絮状结构为铝与其他元素形成的复合物,图2(b)中较致密组织为NaCl,图2(c)中球状物表面为金属铝与氧化铝的混合物。
1.2 实验原理
本研究是在400~600 ℃下,使铝灰中的金属铝、氧化铝与NaOH,添加剂NaNO3或Na2O2反应生成可溶于水的碱式盐,并用水将其溶出,达到铝与其他杂质分离的过程。其主要反应如下:
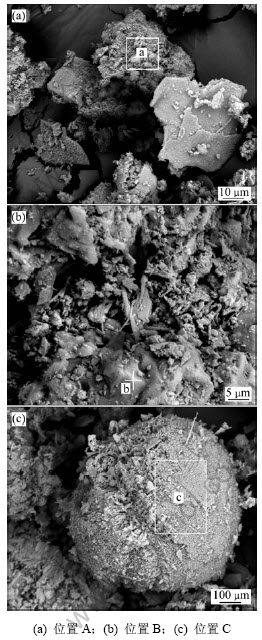
图2 实验用铝灰的SEM像
Fig.2 SEM images of aluminum dross
表2 图2中对应微区元素含量EDAX分析结果(质量分数)
Table 2 EDAX analysis of micro-element content corresponding to Fig.2 %
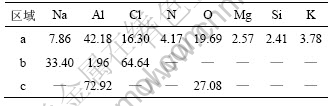
4NaNO3=2Na2O+2N2↑+5O2↑ (1)
2Na2O2=2Na2O+O2↑ (2)
2Na2O2+2H2O=4NaOH+O2↑ (3)
10Al+4NaOH+6NaNO3=10NaAlO2+3N2↑+2H2O (4)
2Al+2NaOH+O2+2Na2O2=2NaAlO2+2Na2O+2H2O (5)
Al2O3+2NaOH=2NaAlO2+H2O (6)
2AlN+2NaOH+2NaNO3+O2=2NaAlO2+2NH3↑+2NaNO2+H2O (7)
2AlN+2NaOH+2Na2O2+O2=2NaAlO2+2NH3↑+2Na2O+H2O (8)
Si+O2+NaNO3+2NaOH=Na2SiO3+NaNO2+H2O (9)
2Si+O2+2Na2O2=2Na2SiO3 (10)
SiO2+2NaNO2=Si+2NaNO3 (11)
Fe2O3+ 2NaNO2=2Fe(NO3)2+Na2O (12)
Fe2O3+2NaOH=2NaFeO2+H2O (13)
FeO+2NaOH=Na2FeO2+H2O (14)
MnO2+2NaOH=Na2MnO3+H2O (15)
2V2O5+4NaNO2=2V2O3+2Na2O+4NO2+O2↑ (16)
V2O3+2NaOH=2NaVO2+H2O (17)
1.3 实验步骤与计算、分析方法
1.3.1 实验步骤
称取10 g铝灰与NaOH、添加剂(NaNO3或Na2O2)按一定比例、一定方式混合均匀(干混料或湿混料),在一定温度下熔炼;用去离子水在一定温度下的恒温水浴中浸出熔炼产物,浸出(浸出温度80 ℃、浸出时间60 min、固液质量与体积比1:8 g/mL)后抽滤、固液分离。对中间产物和最终产物进行XRD物相分析、SEM微观形貌观察和平均粒度分析。
干混料过程:将铝灰、NaOH和NaNO3直接混合搅拌均匀;湿混料过程:先取15 mL水、NaOH和NaNO3配成浓溶液,然后加入铝灰。以Na2O2为添加剂的实验,使用湿混料方式,由于Na2O2极易与水反应,先取15 mL水和NaOH配成浓溶液,加入铝灰后使用冷冻干燥法去除混合物中的水分,最后加入Na2O2并搅拌均匀。
1.3.2 计算方法
根据浸出液中Al和Si等元素的浓度,用下式求得各元素的浸出率:
(18)
式中:R为各元素的浸出率,%;
为浸出液中元素的质量浓度,g/L;m为铝灰的质量,g;
为铝灰中各元素的含量,%。
1.3.3 分析与测试方法
使用原子吸收光谱(AAS)和真空型电感耦合等离子体原子发射光谱分析仪(ICP-AES)分析浸出液中各元素含量。SEM和能谱分析使用日本电子公司生产JSM-6360MV型高低真空扫描电子显微镜(含EDAX能谱)。采用日本理学3014Z型X线衍射分析仪(XRD)测定物相组成,XRD分析在Rigaku衍射仪上进行 (Cu靶Kα射线,λ=0.154 056 nm,管电压为40 kV,管电流为300 mA,石墨单色器,扫描角度为10°~85°,扫描速度为4 (°)/min。使用LS-POP型激光粒度分布仪分析产物的平均粒度(D50)。
2 结果与讨论
2.1 碱灰质量比(m(NaOH)/m(铝灰))的影响
碱灰质量比系指NaOH与铝灰的质量比。在盐灰质量比为0.5、熔炼温度为500 ℃、熔炼时间为60 min的条件下,考察不同碱灰质量比条件下对铝、硅浸出率的影响,结果如图3所示。
由图3可知:在碱灰质量比小于1.3时,铝的浸出率随着碱灰质量比的升高迅速升高,这是由于NaOH的用量加大增加了体系中OH-的活度,有利于NaAlO2的生成。当碱灰质量比大于1.3时,铝的浸出率有所降低,这是由于NaOH的用量增加使体系的黏度不断增大,降低了传质速率。碱灰质量比为1.3时,以Na2O2为添加剂实验的铝浸出率最大,使用NaNO3且湿混料的铝浸出率次之,使用NaNO3干混料的铝浸出率最低,这是由于加水混料可增加铝灰与碱、盐的反应接触面积。在使用NaNO3为氧化助剂的实验中,在碱灰质量比小于1.7时,硅的浸出率随着碱灰质量比的升高,体系中OH-的活度迅速增加。碱灰质量比大于1.7时,随着碱灰质量比增加硅溶出率保持相对稳定。在使用Na2O2为氧化助剂的实验中,硅浸出率随碱灰质量比的增大而迅速升高到85%以上,远远大于其他2组实验的硅浸出率。碱灰质量比为1.3时,铝浸出率最高,硅浸出率较低,碱灰质量比选1.3为宜。
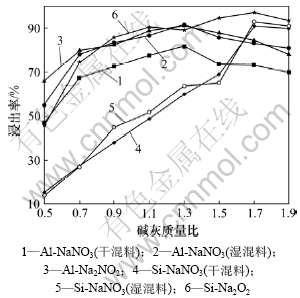
图3 碱灰质量比对铝、硅浸出率的影响
Fig.3 Effects of alkali dross ratio on aluminum, silicon leaching rate
2.2 盐灰质量比(m(NaNO3)/m(铝灰)或m(Na2O2)/m(铝灰))的影响
盐灰质量比指添加剂(NaNO3或Na2O2)与铝灰的质量比。在碱灰质量比为1.3、熔炼温度为500 ℃、熔炼时间为60 min的条件下,考察不同盐灰质量比条件下对铝、硅浸出率的影响,结果如图4所示。
由图4可知:盐灰质量比从0增大到0.7时,3组实验铝回收率均大幅提高,这是因为NaNO3的强氧化作用,Na2O2在反应中放出O2可以增加微反应体系中的氧分压,均有利于铝灰中金属铝的氧化过程,故NaNO3和Na2O2在熔炼过程中起氧化助剂的作用,最终增加了铝回收率。以NaNO3为添加剂的实验中,在盐灰质量比小于0.7时,铝的浸出率随着盐灰质量比的升高而升高,当盐灰质量比大于0.7时,铝的浸出率保持基本不变,故选择盐灰质量比为0.7为宜;以Na2O2为添加剂的实验中,盐灰质量比为0.4时,铝浸出率最大,盐用量继续增大,铝的浸出率也保持稳定,故选择盐灰质量比为0.4为宜。
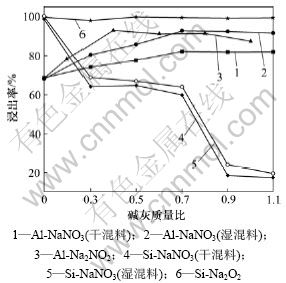
图4 盐灰质量比对铝、硅浸出率的影响
Fig.4 Effects of salt dross ratio on aluminum, silicon leaching rate
以Na2O2为添加剂的实验中,当盐灰质量比由0增加到1.1时,硅浸出率均保持在99%左右。但以NaNO3为添加剂时,随着盐灰质量比的不断增大,硅浸出率迅速降低。当盐灰质量比为1.1时,硅浸出率小于10%。在不同氧化剂条件下,硅浸出率产生差异,这由于体系中存在NaNO3时,体系中的氧化还原反应较为复杂,SiO2可以被反应体系中的产物NaNO2还原,生成了与碱反应活性较低的单质Si,从而降低了硅的浸出率。
2.3 熔炼温度的影响
在碱灰质量比为1.3、盐灰质量比为0.7(NaNO3) 或0.4(Na2O2)、熔炼时间为60 min的条件下,考察不同熔炼温度对铝、硅浸出率的影响。
由图5可以看出:熔炼温度对铝回收率有明显影响。当熔炼温度低于500 ℃时,随温度提高,铝和硅的浸出率均大幅提高。原因在于温度升高,化学反应速率及反应物、产物的扩散速率不断加快,加速了铝和硅向可溶性盐的转化。当熔炼温度高于500 ℃时,铝和硅的浸出率有所降低,以NaNO3为氧化助剂干混料体系降幅最大。这是因为随着反应温度的升高,Al2O3·SiO2对体系黏度增大的作用逐渐增强,反应体系黏度增大,传质速率降低,降低了浸出率Al2O3,SiO2与NaOH的反应效率,从而导致浸出率降低。故反应适宜的熔炼温度应在500 ℃。
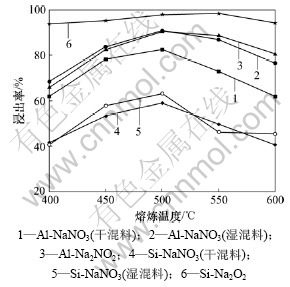
图5 熔炼温度对铝、硅浸出率的影响
Fig.5 Effects of smelting temperature on aluminum, silicon leaching rate
2.4 熔炼时间的影响
在碱灰质量比为1.3、盐灰质量比为0.7(NaNO3)或0.4(Na2O2)、熔炼温度为500 ℃的条件下考察不同熔炼时间对铝和硅浸出率的影响。
由图6可以看出:当熔炼时间少于60 min时,随熔炼时间增长铝和硅的浸出率均提高。当熔炼时间大于60 min时,随熔炼时间继续增长,铝的浸出率保持基本不变,硅的浸出率小幅下降。原因在于熔炼时间过短,化学反应不完全,导致铝和硅浸出率较低。熔炼时间增长,硅氧化物与体系中的其他物质生成难溶于水的复合氧化物(2CaO·SiO2, Na2O·Al2O3·2SiO2),导致硅浸出率降低,故熔炼时间为60 min较为适宜。
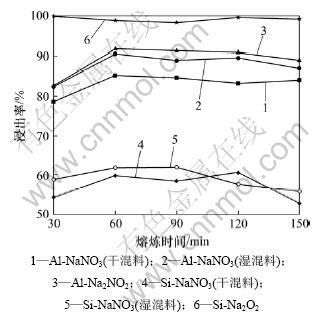
图6 熔炼时间对铝、硅浸出率的影响
Fig.6 Effects of smelting time on aluminum, silicon leaching rate
2.5 熔炼产物XRD分析
分别以优化条件下的熔炼产物进行了XRD物相分析,结果如图7所示。经过低温碱性熔炼,铝灰中的含铝组分转化为了NaAlO2。
2.6 浸出渣XRD分析
分别对优化条件下的浸出渣进行了XRD物相分析,结果如图8所示。经过低温碱性熔炼和浸出,浸出渣中除含有未被反应的刚玉,其他主要物相为Mg,Ca和Al等元素的化合物。

图7 熔炼产物的XRD谱
Fig.7 XRD patterns of smelting products
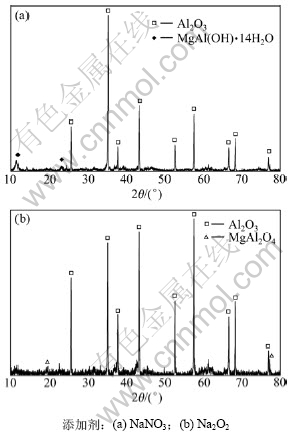
图8 浸出渣的XRD谱
Fig.8 XRD pattern of leaching residue
3 结论
(1) 采用低温碱性熔炼法提取出铝灰中的铝,低温碱性熔炼过程的优化条件如下:碱灰质量比1.3、盐灰质量比0.7(NaNO3)或0.4(Na2O2)、熔炼温度为500 ℃、熔炼时间为60 min。
(2) 湿混料可大幅度地提高铝的浸出率,以NaNO3和Na2O2为添加剂均能高效地提取铝灰中的铝;在优化条件下,以NaNO3为添加剂干混料实验的铝浸出率为87.52%,以NaNO3为添加剂并湿混料实验的铝浸出率为92.71%,以Na2O2为添加剂湿混料实验的铝浸出率为92.76%。
(3) 经XRD分析,熔炼产物和浸出渣中均有未参加反应的刚玉相。其中,熔炼产物中有NaAlO2生成,浸出渣中主要为Mg,Ca和Al等元素的化合物。
参考文献:
[1] 乐颂光, 鲁君乐, 何静, 等. 再生有色金属生产[M]. 修订版. 长沙: 中南大学出版社, 2006: 433-482.
LE Song-guang, LU Jun-le, HE jing, et al. Recycled ferrous metal production[M]. Rev ed. Changsha: Central South University Press, 2006: 433-482.
[2] Tan R B, Khoo H, An H H. LCA study of a primary aluminum supply chain[J]. Journal of Cleaner Production, 2005, 13(6): 607-618.
[3] 郭学益, 田庆华. 有色金属资源循环理论与方法[M]. 长沙: 中南大学出版社, 2008: 16-68.
GUO Xue-yi, TIAN Qing-hua. The resource recycling of nonferrous metal fundamental and approach[M]. Changsha: Central South University Press, 2008: 16-68.
[4] Shinzato M C, Hypolito R. Solid waste from aluminum recycling process: characterization and reuse of its economically valuable constituents[J]. Waste Management, 2005, 25(1): 37-46.
[5] Hazar A B Y, Saridede M N, Cigdem M. A study on the structural analysis of aluminium drosses and processing of industrial aluminium salty slags[J]. Scandinavian Journal of Metallurgy, 2005, 34(5): 213-219.
[6] 陈利斌, 张亦飞, 张懿. 亚熔盐法处理铝土矿工艺的赤泥常压脱碱[J]. 过程工程学报, 2010, 10(3): 470-475.
CHEN Li-bin, ZHANG Yi-fei, ZHANG Yi. Dealkalization of red mud generated in alumina production by sub-molten salt process under atomospheric pressure[J]. The Chinese Journal of Process Engineering, 2010, 10(3): 470-475.
[7] 张洋, 孙峙, 郑诗礼, 等. KOH-KNO3三元亚熔盐分解铬铁矿的试验研究[J]. 化工进展, 2008, 27(7): 1042-1047.
ZHANG Yang, SUN Zhi, ZHENG Shi-li, et al. Experimental study on chromite ore decomposition by KOH-KNO3 binary sub-molten salt[J]. Chemical Industry and Engineering Progress, 2008, 27(7): 1042-1047.
[8] 刘玉民, 齐涛, 张懿. KOH亚熔盐法分解钛铁矿的动力学分析[J]. 中国有色金属学报, 2009, 19(6): 1142-1147.
LIU Yu min, QI Tao, ZHANG Yi. Kinetics analysis of decomposition of ilmenite by KOH sub-molten salt method[J]. The Chinese Journal of Nonferrous Metals, 2009, 19(6): 1142-1147.
[9] 刘玉民, 齐涛, 王丽娜, 等. KOH亚熔盐法分解钛铁矿[J]. 过程工程学报, 2009, 9(2): 319-323.
LIU Yu-min, QI Tao, WANG Li-na, et al. Decomposition of Ilmenite in KOH sub-molten salt[J]. The Chinese Journal of Process Engineering, 2009, 9(2): 319-323.
[10] 周宏明, 郑诗礼, 张懿. KOH亚熔盐浸出低品位难分解钽铌矿的实验[J]. 过程工程学报, 2003, 3(5): 459-463.
ZHOU Hong-ming, ZHENG Shi-li, ZHANG Yi. Leaching of a low-grade refractory tantalum-niobium ore by KOH sub-molten salt[J]. The Chinese Journal of Process Engineering, 2003, 3(5): 459-463.
[11] 钟莉, 张亦飞. 亚熔盐法回收赤泥[J]. 中国有色金属学报, 2008, 18(1): S70-S73.
ZHONG Li, ZHANG Yi-fei. Recovery of Al2O3 and Na2O from red mud by sub-molten salt[J]. The Chinese Journal of Nonferrous Metals, 2008, 18(1): S70-S73.
[12] 孙旺, 郑诗礼, 张亦飞, 等. NaOH亚熔盐法处理拜尔法赤泥的铝硅行为[J]. 过程工程学报, 2008, 8(6): 1148-1152.
SUN Wang, ZHENG Shi-li, ZHANG Yi-fei, et al. Behavior of Al and Si in Bayer red mud processed by NaOH sub-molten salt[J]. The Chinese Journal of Process Engineering, 2008, 8(6): 1148-1152.
[13] 王少娜, 郑诗礼, 张懿. 亚熔盐溶出一水硬铝石型铝土矿过程中赤泥的铝硅行为[J]. 过程工程学报, 2007, 7(5): 965-972.
WANG Shao-na, ZHENG Shi-li, ZHANG Yi. Behavior of Al and Si in red mud from leaching process of diaspore bauxite with NaOH sub-molten salt[J]. The Chinese Journal of Process Engineering, 2007, 7(5): 965-972.
[14] WANG Xiao-hui, ZHENG Shi-li, XU Hong-bin, et al. Leaching of niobium and tantalum from a low-grade ore using a KOH roast-water leach system[J]. Hydrometallurgy, 2009, 98: 219-223.
[15] 徐盛明, 吴延军. 碱性直接炼铅法的应用[J]. 矿产保护与利用, 1997(6): 31-33.
XU Sheng-ming, WU Yan-jun. Application of direct basic lead-smelting process[J]. Conservation and Utilization of Mineral Resource, 1997(6): 31-33.
[16] 徐盛明, 肖克剑, 汤志军, 等. 银精矿碱法熔炼工艺的扩大试验[J]. 中国有色金属学报, 1998(8): 303-308.
XU Sheng-ming, XIAO Jian-ke, TANG Zhi-jun, et al. Treatment of silver concentrate by basic smelting process[J]. The Chinese Journal of Nonferrous Metals, 1998(8): 303-308.
[17] 肖剑飞. 硫化铋精矿低温碱性熔炼新工艺研究[D]. 长沙: 中南大学冶金科学与工程学院, 2009: 55-56.
XIAO Jian-fei. Study on a new process for aikalline smelting bismuth sulfide concentrate at low temperature[D]. Changsha: Central South University. School of Metallurgical Science and Engineering, 2009: 55-56.
[18] 肖剑飞, 唐朝波, 唐谟堂, 等. 硫化铋精矿低温碱性熔炼新工艺研究[J]. 矿冶工程, 2009, 29(5): 82-85.
XIAO Jian-fei, TANG Chao-bo, TANG Mo-tang, et al. Study on a new process for aikalline smelting bismuth sulfide concentrate at low temperature[J]. Mining and Metallurgical Engineering, 2009, 29(5): 82-85.
(编辑 陈爱华)
收稿日期:2011-05-20;修回日期:2011-07-26
基金项目:国家自然科学基金资助项目(51074190);湖南省自然科学基金资助项目(11JJ4048)
通信作者:田庆华(1981-),男,四川宜宾人,博士,讲师,从事有色金属资源循环利用及粉体材料制备研究;电话:0731-88877863;E-mail: qinghua@csu.edu.cn