控制电位氧化法铅阳极泥脱砷
杨天足,王安,刘伟锋,张杜超,文剑锋,吴江华
(中南大学 冶金科学与工程学院,湖南 长沙,410083)
摘要:采用压缩空气和双氧水作氧化剂,通过控制氢氧化钠体系中的电位来氧化浸出铅阳极泥中的砷。试验中考察电位、NaOH浓度、反应温度、反应时间和液固质量比对脱砷效果的影响,确定碱性浸出过程中预脱砷的最佳工艺条件: NaOH浓度为2 mol/L,温度为80 ℃,液固质量比为5:1,通入0.2 MPa的压缩空气4 h后用双氧水调节体系的电位至-180 mV,反应时间为2 h。在此条件下,砷的浸出率可达98%以上。碱浸液经冷却过滤掉结晶砷酸钠后,返回浸出过程,砷的浸出率达98%以上,实现碱浸液的循环利用以及砷与其他金属的有效分离。
关键词:铅阳极泥;氧化浸出;脱砷;电位控制
中图分类号:TF04 文献标志码:A 文章编号:1672-7207(2012)07-2482-07
Removing arsenic from lead anode slime by oxidation under potential control
YANG Tian-zu, WANG An, LIU Wei-feng, ZHANG Du-chao, WEN Jian-feng, WU Jiang-hua
(School of Metallurgical Science and Engineering, Central South University, Changsha 410083, China)
Abstract: Arsenic was leached from lead anode slime with the oxidants including compressed air and hydrogen peroxide by potential control in sodium hydroxide system. The effects of potential, concentration of sodium hydroxide, reaction temperature, reaction time and solid/liquid ratio on arsenic removal were investigated and the optimum conditions of the arsenic removal in the alkaline leaching process were determined as follows: NaOH concentration of 2 mol/L, reaction temperature at 80 ℃, solid/liquid ratio of 5:1, 0.2 MPa compressed air into reaction system for 4 h, controlling the potential at -180 mV, and reaction time for 2 h. More than 98% of the amount arsenic is removed under these conditions. The alkaline leaching solution is returned to leaching process after the removal of crystal sodium arsenate by cooling and filtration, which achieves the recycling of alkaline solution and the effective separation of arsenic from other metals.
Key words: lead anode slime; oxidative leaching; arsenic removal; potential control
由于铅的需求量增加和炼铅技术的巨大进步,高砷铅精矿在铅冶炼过程中被大量采用,导致了后续电解工序产生的铅阳极泥含砷越来越高。铅阳极泥除含有大量的贱金属外,还含有稀贵金属硒、碲、金和银等[1]。因此,避免砷在后续流程中的污染以及对其他金属提取造成的影响,必须对铅阳极泥进行预脱砷处理。现有预脱砷的工艺主要分为三类:火法工艺、湿法工艺、火法-湿法联合工艺。火法工艺主要有还原焙烧法[2]、挥发焙烧法[3]以及真空脱砷法[4]。火法脱砷工艺成熟、适应性强、流程相对简单、操作简洁,但是也存在其脱砷率较低、环境污染严重等问题。湿法工艺主要有酸浸脱砷法[5-6]、碱浸脱砷法[7-9]以及氯化浸出法[10]等。湿法工艺脱砷率高、污染少,但浸出液的处理流程长、工序比较繁琐、分离困难、回收利用砷等有价金属元素复杂等。火法 -湿法联合工艺[3]主要是指采用苏打烧结-水浸脱砷或纯碱烧结-水浸脱砷的方法,此工艺消耗大量昂贵的添加剂、成本太高,工业上应用很少。 因此,如何解决砷和其他有价金属在冶炼工艺中的回收和环保问题,是当前亟待解决的问题[11-14]。虽然早在20世纪七八十年代,前苏联和日本的学者就进行了对含砷物料的碱性浸出处 理[15-16],但工艺中流程较为复杂,浸出率较低,工业废水处理困难等缺点仍然存在。而本文作者采用碱性浸出工艺,通过控制溶液体系中的氧化电位,开发出了一种新的易于控制的操作流程,既能有效地处理铅阳极泥中的砷,而且处理后的碱液能够得到合理的循环利用。
1 试验部分
1.1 原料
本试验所用铅阳极泥来自于某冶炼厂铅电解车间。新取的铅阳极泥用80~95 ℃热水浆化洗涤,固液分离前用孔径为200~640 μm的筛子筛分以除去铅阳极泥中的大颗粒夹杂物,烘干过程中进行了防氧化处理。原料铅阳极泥的化学成分及砷、锑的物相组成分别见表1和表2。由表1和2可以看出:铅阳极泥中砷含量比较高,且砷主要以化合态存在。在高温氢氧化钠溶液中,高价氧化态的砷会以砷酸盐的形式进入溶液,而其他的金属在控制反应条件的情况下基本上不被浸出,这就为碱性体系选择性浸出砷提供了 条件。
1.2 试验原理
铅阳极泥中的砷,大部分都以低价态形式存在,所以在碱性浸出的过程中需要加入一定的氧化剂来使其氧化到高价[17]。所需氧化剂的加入量则根据体系中砷的氧化还原电位来确定[18-19]。本试验中,溶液电位的测量是在氢氧化钠体系中插入测定电位的铂电极和汞-氧化汞电极,分别作为指示电极和参比电极,以MT320-S pH计为显示仪,所显示的电位是溶液中金属离子的混合电位与汞-氧化汞电极电位之差。由于铅阳极泥成分复杂,实际测得的电位值与理论值会存在一定的偏差。
氢氧化钠浸出铅阳极泥的过程中可能发生的主要反应如下:
As2O3+6NaOH+O2=2Na3AsO4+3H2O (1)
As2O5+6NaOH=2Na3AsO4+3H2O (2)
2Me3(AsO3)x+6xNaOH+xO2=
2xNa3AsO4+3xH2O+3Me2Ox↓ (3)
2Me3(AsO4)x+6xNaOH=
2xNa3AsO4+3xH2O+3Me2Ox↓ (4)
As2O3+6NaOH+2H2O2=2Na3AsO4+5H2O (5)
2Me3(AsO3)x+6xNaOH+2xH2O2=
2xNa3AsO4+5xH2O+3Me2Ox↓ (6)
1.3 试验方法与工艺流程
铅阳极泥经筛分、热水洗涤和烘烤后,在氢氧化钠溶液中通过控制电位进行氧化浸出,分别采用压缩空气和双氧水做氧化剂,使砷被氧化后进入碱性浸出液,而铋、铅、锑和铜等金属则在被氧化后与贵金属一同进入碱性浸出渣。碱性氧化浸出过程结束后趁热过滤,浸出液经过冷却结晶产出结晶砷酸钠,结晶母液再补充一定量的氢氧化钠后返回浸出过程,实现铅阳极泥中砷与其他有价金属的分离与回收。其具体工艺流程如图1所示。
表1 铅阳极泥的化学成分(质量分数)
Table 1 Compositions of lead anode slime %

表2 砷和锑的物相分析结果(质量分数)
Table 2 Phase analysis results of arsenic and antimony %

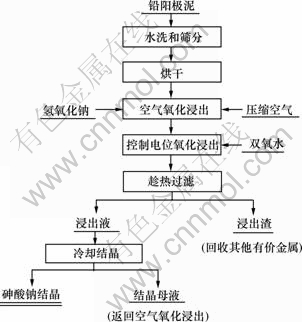
图1 碱性氧化浸出法处理铅阳极泥的工艺流程图
Fig.1 Process flowsheet for alkaline leaching-oxidation of lead anode slime
2 结果与讨论
2.1 电位对浸出率的影响
在NaOH浓度为2 mol/L、液固质量比为5:1、温度为80 ℃、反应时间为2 h、搅拌线速度为135 m/min的条件下,考察了通过双氧水来调节体系中电位对碱性浸出过程主要金属浸出率(质量分数)的影响,结果如图2所示。
由图2可以看出:随着双氧水的加入,体系中电位逐渐升高。铅的浸出率随电位的升高变化不明显,始终维持在5%左右;电位在-380~-180 mV(相对于汞-氧化汞饱和电极,下同)时,砷的浸出率随电位的升高而升高,电位约-180 mV时,其浸出率达到约98%,当电位超过-180 mV后,砷的浸出率基本没有变化,仍然维持在98%左右。所以,为了达到理想的脱砷效果,应该控制体系的电位值不小于-180 mV。
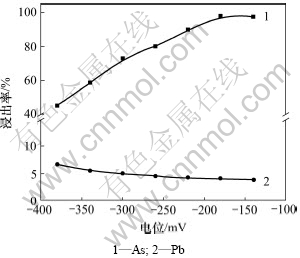
图2 电位对浸出率的影响
Fig.2 Effect of potential on leaching ratio
2.2 空气氧化时间对浸出率的影响
在NaOH浓度为2 mol/L、液固质量比为5:1、温度为80 ℃、压缩空气压力为0.2 MPa、搅拌线速度为135 m/min的条件下,考察了空气氧化时间对碱性浸出过程主要金属浸出率的影响,结果如图3所示。
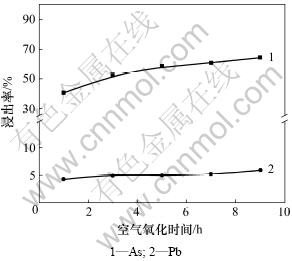
图3 空气氧化时间对浸出率的影响
Fig.3 Effect of oxidative time with air on leaching ratio
由图3可以看出:砷的浸出率随鼓入压缩空气时间的延长而升高。在鼓入空气1 h至3 h这段时间内,砷的浸出率由40.6%上升至52.3%,而之后随着时间的延长,砷的浸出率上升不太明显。由于Pb2+与OH-存在配位关系,所以,在氢氧化钠体系中,部分铅会溶解进入溶液。在该条件下,连续鼓入空气,铅的浸出率维持在4%~6%之间,碱浸液中含铅约1.0~1.3 g/L。表3列出了测得的空气氧化时间与体系中电位的关系。
表3 空气氧化时间与电位的关系
Table 3 Relationship between oxidative time with air and potential

通过表3可以看出:当体系中空气氧化时间大于3 h后,电位值的升高趋势不是很明显,这与图3中砷的浸出率变化相吻合。所以,只通入压缩空气很难达到脱砷的理想效果,这应该与空气自身的氧化能力有关。为了尽可能的提高砷的浸出率,需要再加入更强的氧化剂,同时考虑到氧化剂成本问题,预先通入一定时间的压缩空气是很有必要的。综合以上条件得出最佳空气氧化时间为4 h。
2.3 氢氧化钠浓度对浸出率的影响
在液固质量比为5:1、温度为80 ℃、反应时间为2 h、电位为-180 mV、搅拌线速度为135 m/min的条件下,考察了氢氧化钠浓度对碱性浸出过程主要金属浸出率的影响,结果如图4所示。

图4 氢氧化钠浓度对浸出率的影响
Fig.4 Effect of NaOH concentration on leaching ratio
从图4可以看出:在控制电位碱性氧化浸出的过程中,砷、铅以及铜的浸出率都随着氢氧化钠浓度的升高而升高。当NaOH浓度为2.0 mol/L时,砷的浸出率达到98.2%;当NaOH浓度小于2.0 mol/L时,砷的浸出率增加幅度较大;而当NaOH浓度大于2.0 mol/L时,砷的浸出率基本不变,始终维持在98%左右。然而,随着氢氧化钠浓度的增长,其他金属的溶解也在变化。当NaOH浓度大于2.0 mol/L时,铅的溶解随着氢氧化钠浓度升高明显加剧,当NaOH浓度为4.0 mol/L时,铅的浸出率达到27.33%。随着氢氧化钠浓度的增加,铜的浸出率缓慢增加,NaOH浓度为3 mol/L和4 mol/L的浸出液中带有绿色,说明游离[OH-]增加,与铜离子形成配合物,造成铜的溶解。在整个碱性浸出过程,锑的浸出率在0.7%~2.1%之间,溶液中锑浓度始终保持在0.2~0.5 g/L,说明碱性浸出过程中锑的溶解损失很小。为了有效分离砷,同时尽量防止其他金属的溶解损失,选择NaOH浓度为2.0 mol/L最为适宜。
2.4 反应时间对浸出率的影响
在NaOH浓度为2 mol/L、液固质量比为5:1、温度为80 ℃、电位为-180 mV、搅拌线速度为135 m/min的条件下,考察了反应时间对碱性浸出过程主要金属浸出率的影响,结果如图5所示。
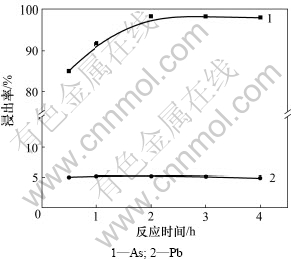
图5 反应时间对浸出率的影响
Fig.5 Effect of aging time on leaching ratio
由图5可知:当反应时间由0.5 h增加到2 h时,砷的浸出率由85%升高至98%以上;反应时间为2 h时,砷的浸出率达到98.2%;而当反应时间由2 h增加到4 h时,砷的浸出率相对于2 h时基本不再变化。反应时间的变化对铅的浸出率没有什么影响。在当前的试验条件下,为了保证砷的高浸出率,最佳反应时间选择2 h。
2.5 反应温度对浸出率的影响
在NaOH浓度为2 mol/L、液固质量比为5:1、反应时间为2 h、电位值为-180 mV、搅拌线速度为135 m/min的条件下,考察了反应温度对碱性浸出过程主要金属浸出率的影响,结果如图6所示。
从图6可以看出:在温度低于80 ℃时,砷的浸出率随着温度的升高而升高;高于80 ℃后,砷的浸出率基本稳定维持在98%左右。当温度为25 ℃时,砷的浸出率不到70%,此时由于溶液中残留的OH-相对于40 ℃时要多,所以铅的溶解也要比40 ℃时多,同时由于温度的升高也会加速铅在碱液中的溶解,所以,铅随温度变化的曲线会呈现先下降、后上升的趋势。但总的来说,铅的浸出率随温度的变化影响不大。综合考虑,选定最佳反应温度为80 ℃。
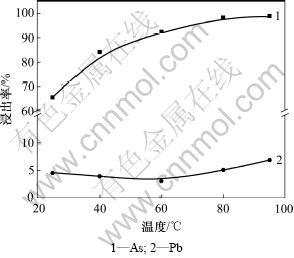
图6 反应温度对浸出率的影响
Fig.6 Effect of temperature on leaching ratio
2.6 液固质量比对浸出率的影响
在NaOH浓度为2 mol/L、温度为80 ℃、反应时间为2 h、电位为-180 mV、搅拌线速度为135 m/min的条件下,考察了液固质量比对碱性浸出过程主要金属浸出率的影响,结果如图7所示。
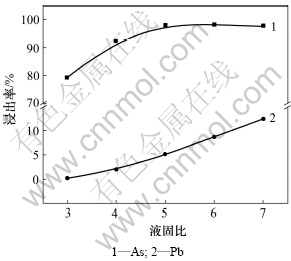
图7 液固质量比对浸出率的影响
Fig.7 Effect of mass ratio of solid to liquid on leaching ratio
从图7可见:随着液固质量比的升高,砷的浸出率由79.3%(液固质量比为3)升高到了98.2%(液固质量比为5)。当液固质量比大于5时,砷的浸出率保持在98%左右。然而,铅的浸出率随着液固质量比的增大逐渐增加。当液固质量比增大时,溶液中总的氢氧化钠量增加,相同质量的铅阳极泥消耗的氢氧化钠量是一定的,那么溶液中游离的氢氧根浓度相应提高,进而造成溶液中铅浓度有所提高,铅的浸出率就会出现如图7中曲线所呈现出来的趋势。为了保证砷的高浸出率,并且其他金属尽量不要进入溶液,同时做到节约成本,液固质量比取5:1较为合适。
2.7 综合条件试验
由上述的条件试验得出铅阳极泥预脱砷的最佳工艺条件为:先通入0.2 MPa的压缩空气4 h,然后通过加入双氧水来调节体系中的电位不小于-180 mV,到达要求电位后反应时间控制为2 h,反应温度为80 ℃,液固质量比为5:1,氢氧化钠浓度为2 mol/L。在该条件下进行了3次综合条件试验,试验结果如表4所示。
表4 综合条件试验结果
Table 4 Experiment results of optimal conditions
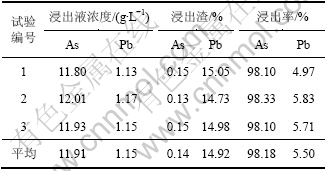
由表4可以看出:在该综合条件下,砷的浸出率达到了98.18%,碱性浸出渣中砷含量降到了0.14%,对后续脱砷铅阳极泥的处理,不管是选择湿法工艺还是火法工艺,都基本上杜绝了砷在流程中的危害;铅的浸出率维持在5.50%左右,碱液中含铅约1.15 g/L。从以上试验结果可以看出:碱性控制电位两段氧化法能有效地分离铅阳极泥中的绝大部分砷,从而实现砷与其他金属有效分离的目的。
2.8 碱浸液的循环利用
在碱性浸出的过程中,阳极泥中的砷进入溶液,而其他金属基本不溶于碱性溶液,从而达到砷与其他金属分离的目的,杜绝了砷在后续其他有价金属的回收中所带来的危害。将趁热过滤后所得到的含砷为11.85 g/L的碱性浸出液冷却至25 ℃后再次过滤,得到大量的白色含砷化合物结晶。此白色结晶在60 ℃下低温烘干,其XRD分析结果如图8所示。
由图8可以看出:结晶析出的含砷化合物为Na3AsO4·10H2O。同时化学分析测得其中砷含量为18.71%,这与Na3AsO4·10H2O中含砷量19.31%非常吻合。结晶过滤后的滤液中含砷量为1.24 g/L,NaOH浓度为1.1 mol/L,补加NaOH至2 mol/L后返回碱性浸出过程。浸出效果如表5所示。
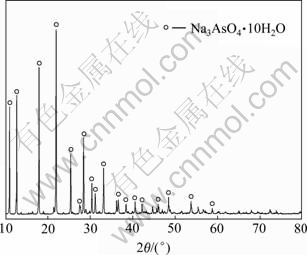
图8 碱浸液结晶物XRD谱
Fig.8 XRD pattern of crystal from alkaline leaching solution
表5 循环浸出试验结果
Table 5 Experiment results of circulated leaching
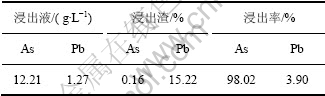
由表5可以看出:利用冷却过滤后的碱浸液返回碱性浸出过程来浸出新的阳极泥,不影响砷的脱除率,脱砷率仍能达到98%左右。同时,铅的浸出率还略有下降,这是由于返浸前的碱液中含有铅离子,根据同离子效应,会起到抑制铅溶解的作用。以上结果表明,碱性控制电位氧化浸出过程结束后趁热过滤,浸出液经过冷却结晶产出砷酸钠结晶,结晶母液补充一定的氢氧化钠后返回空气氧化浸出过程,实现了铅阳极泥中砷与其他有价金属的分离与回收,同时实现了整个预脱砷工艺闭路循环,达到了节能与环保的目的。
3 结论
(1) 通过考察控制电位氧化法处理铅阳极泥中各因素对浸出过程的影响,确定了碱性控制电位氧化浸出铅阳极泥的最佳工艺条件:NaOH浓度为2 mol/L,温度为80 ℃,液固质量比为5:1,通入0.2 MPa的压缩空气4 h,后用双氧水调节体系的电位至-180 mV,反应时间为2 h。在此条件下,砷的浸出率可达98%以上,而铅的浸出率仅有5%左右。
(2) 碱性浸出液中的砷以砷酸钠形式回收,不仅不消耗其他试剂、处理成本低,而且实现了碱性浸出液的循环利用、无废水排放。在返回浸出过程中,砷的浸出率仍可达98%以上,浸出液循环利用对脱砷没有影响。
(3) 通过控制电位氧化法处理铅阳极泥,不仅砷的脱除率高,实现铅阳极泥中砷与其他有价金属的分离,同时进一步富集了其他贵贱金属,杜绝了铅阳极泥处理工艺中砷的二次污染,而且利用控制电位装置实现了浸出过程的有效控制,工艺运行稳定。整个预脱砷工艺闭路循环,达到了节能与环保的目的。
参考文献:
[1] 卢宜源, 宾万达. 贵金属冶金学[M]. 长沙: 中南大学出版社, 2004: 203.
LU Yi-yuan, BING Wang-da. Precious metals metallurgy[M]. Changsha: Central South University Press, 2004: 203.
[2] 傅作健. 高铅砷转炉烟尘中砷的综合利用问题[J]. 有色金属: 冶炼部分, 1978(10): 18-22.
FU Zuo-jian. Comprehensive utilization of arsenic from convertor soot with high content of arsenic and lead[J]. Nonferrous Metals: Extractive Metallurgy, 1978(10): 18-22.
[3] 吴俊升, 陆跃华, 周杨霁, 等. 高砷铅阳极泥水蒸汽焙烧脱砷试验研究[J]. 贵金属, 2003, 24(4): 26-31.
WU Jun-sheng, LU Yue-hua, ZHOU Yang-ji, et al. Experimental study on arsenic removal from arsenic-rich lead anode slime by volatilization roasting in steam condition[J]. Precious Metals, 2003, 24(4): 26-31.
[4] 张国靖, 李敦钫, 吴昆华, 等. 高砷铅阳极泥处理新工艺的研究[J]. 有色金属: 冶炼部分, 1996(2): 10-13.
ZHANG Guo-jing, LI Dun-fang, WU Kun-hua, et al. Study of a new treatment process about arsenic-rich lead anode slime[J]. Nonferrous Metals: Extractive Metallurgy, 1996(2): 10-13.
[5] Jdid E A, Elamari K, Blazy P, et al. Acid and oxidizing leaching of copper refinery anodic slimes in hexaflurosilicic acid and nitric acid media[J]. Separation Science and Technology, 1996, 31(4): 569-577.
[6] Mahramanlioglu M, Gü?lü K. Equilibrium, kinetic and mass transfer studies and column operations for the removal of arsenic(Ⅲ) from aqueous solutions using acid treated spent bleaching earth[J]. Environmental Technology, 2004, 25(9): 1067-1076.
[7] Fermandez M A, Segarra M, Espiell F. Selective leaching of arsenic and antimony contained in the anode slimes from copper refining[J]. Hydrometallurgy, 1996, 41(2/3): 255-267.
[8] Zhu B, Tabatabai M A. An alkaline oxidation method for determination of total arsenic and selenium in sewage sludges[J]. Journal of Environmental Quality, 1995, 24(4): 622-626.
[9] 蔡练兵, 刘维, 柴立元. 高砷铅阳极泥预脱砷研究[J]. 矿冶工程, 2007, 27(6): 44-47.
CAI Lian-bing, LIU Wei, CHAI Li-yuan. Study on pre-treatment process of arsenic removal for arsenic-rich lead anode slime[J]. Mining and Metallurgical Engineering, 2007, 27(6): 44-47.
[10] 胡绪铭, 谢斌. 高砷铅阳极泥湿法处理方法: 中国, CN1079510A[P]. 1993-12-15.
HU Xu-ming, XIE Bin. Hydrometallurgical treatment of arsenic- rich lead anode slime: China, CN1079510A[P]. 1993-12-15.
[11] 张敏. 金精矿固砷固硫焙烧提金工艺设计[J]. 矿冶工程, 2002, 22(4): 58-63.
ZHANG Min. The design of As, S stabilization and roaster smelting of Au concentrate[J]. Mining and Metallurgical Engineering, 2002, 22(4): 58-63.
[12] 陈白珍, 王中溪, 周竹生, 等. 二次砷碱渣清洁化生产技术工业试验[J]. 矿冶工程, 2007, 27(2): 47-49.
CHEN Bai-zhen, WANG Zhong-xi, ZHOU Zhu-sheng, et al. Commercial test of cleanly production technology of second arsenic-alkali residue[J]. Mining and Metallurgical Engineering, 2007, 27(2): 47-49.
[13] Mohan D, Pittman C U Jr. Arsenic removal from water/ wastewater using adsorbents: A critical review[J]. Journal of Hazardous Materials, 2007, 142(1/2): 1-53.
[14] 陈锋, 关中杰, 兰尧中. 含砷废水处理研究现状[J]. 云南冶金, 2010, 39(4): 63-66.
CHEN Feng, GUAN Zhong-jie, LAN Yao-zhong. Research status of arsenic wastewater treatment[J]. Yunnan Metallurgy, 2010, 39(4): 63-66.
[15] 余宝元. 前苏联有色冶金工业应用的脱砷工艺[J]. 有色矿冶, 1992(1): 33-40.
YU Bao-yuan. Arsenic removal process applied in non-ferrous metallurgical industry of the former Soviet Union[J]. Non-Ferrous Mining and Metallurgy, 1992(1): 33-40.
[16] 刘树根, 田学达. 含砷固体废物的处理现状与展望[J]. 湿法冶金, 2005, 24(4): 183-186.
LIU Shu-gen, TIAN Xue-da. Situation and prospect on treating of arsenic-containing solid waste[J]. Hydrometallurgy of China, 2005, 24(4): 183-186.
[17] 蒋学先, 何贵香, 李旭光, 等. 高砷烟尘脱砷试验研究[J]. 湿法冶金, 2010, 29(3): 199-202.
JIANG Xue-xian, HE Gui-xiang, LI Xu-guang, et al. Experimental research on dearsenization of high arsenic fume[J]. Hydrometallurgy of China, 2010, 29(3): 199-202.
[18] Carbonell-barrachina A A, Jugsujinda A, Burlo F, et al. Arsenic chemistry in municipal sewage sludge as affected by redox potential and pH[J]. Water Research, 1999, 34(1): 216-224.
[19] Milazzo G , Caroli S. Table of standard electrode potentials[M]. New York: John Wiley&Sons Ltd, 1978: 345-380.
(编辑 陈爱华)
收稿日期:2011-09-20;修回日期:2011-11-19
基金项目:湖南省重大科技专项资助项目(2009FJ1007)
通信作者:杨天足(1958-),男,广西贺州人,教授,博士生导师,从事贵、重金属冶炼和提纯以及相关化工产品的开发;电话:0731-88836791;E-mail: tianzuyang@163.com