DOI:10.19476/j.ysxb.1004.0609.2017.11.05
铝合金实心凸起结构板锻造成形工艺
董文正1, 2, 3,张存园1,林启权1,王志刚3
(1. 湘潭大学 机械工程学院,湘潭 411105;
2. 华中科技大学 材料成形与模具技术国家重点实验室,武汉 430074;
3. 日本岐阜大学 机械系统工学科,岐阜 501-1193)
摘 要:以铝合金筒形件底部实心凸起成形为例,提出采用拉深-镦挤板锻造工艺成形中心实心凸起结构,结合有限元模拟技术及工艺实验方法,比较传统反挤压工艺与板锻造工艺成形实心凸起结构的异同。结果表明:当成形同一凸起高度时,板锻造成形载荷比反挤压成形载荷减小一倍左右。板锻造成形过程中,底部分流面位置先内移后趋于稳定;而在反挤压成形过程中,底部分流面位置先趋于稳定后外移。凸模与板料上表面的单面润滑可有效防止底部缩孔缺陷。
关键词:铝合金板材;实心凸起;板锻造;分流面;缩孔机制
文章编号:1004-0609(2017)-11-2221-07 中图分类号:TG386.3 文献标志码:A
凸起结构(Boss structure),根据美国金属手册定义,即锻件表面上相对较短、通常为圆柱形的突起或突出部分[1]。作为一种局部功能结构,凸起扮演着装配定位、固定、铆接、加强结构等角色,在现代汽车、电子电器等轻量化产品生产领域得到了广泛应用。金属板材零件凸起结构常常采用反挤压成形工艺,但存在成形载荷大、工序多、缩孔缺陷等不足,不符合现代绿色、高效制造的发展要求。因此,开展金属板材凸起成形新工艺及其变形机理研究,不仅丰富了现代精密塑性成形理论,而且对轻量化产品设计、降低制造成本与提高结构件的整体综合性能具有重要的现实意义。
板锻造是以板料或其半成品毛坯在冲压成形过程中,通过实施体积成形、控制局部金属材料的非均匀流动,从而获得非等厚、具有三维特征结构的精密塑性成形工艺,也称为流动控制成形、板料体积成形或冲锻成形。目前,板锻造技术在日本、德国等工业发达国家得到了大力推广与支持,已开发了大量适合不同装配产品需求的板锻造成形零件[2-5]。MERKLEIN等[6]基于板锻造成形技术,以厚度2 mm的DC40钢为坯料,提出了圆筒齿轮板锻造一体化成形方案,解决传统机加工方法高成本、低效率的缺点。KO等[7]采用拉深、镦挤板锻造成形工艺成形带两个空心凸起的汽车车门锁扣,大大简化传统成形工艺,并减小了零件的质量。MORI等[8]在对汽车用激光拼焊板进行方盒拉深时辅以局部增厚工序,显著提高了激光拼焊板方盒拉深的成形极限。在国内,王新云等[9-11]对温板锻成形、大厚差板材成形进行了一系列研究,解决了传统加工中空薄壁零件不能满足使用要求和加工难度大等问题,对实际产品生产具有一定的指导作用。杨合等[12-13]对钛合金板T形凸起成形过程进行力学分析,探讨了摩擦、凸起结构、板料几何尺寸对金属塑性分流的影响,并对局部加载成形的微观组织演化进行了深入研究。张士宏等[14-15]对方盒形件底部带凸柱零件的热冲锻成形研究时,将数值模拟与工艺试验相结合,探讨AZ31镁合金热锻温度对不同板厚成形性能的影响,查明缺陷产生的机理,并提出控制的方法。林启权所在课题组[16-18]分别对厚板翻边和薄板凸起的相关板锻复合成形工艺进行了一系列研究,并开发圆筒形齿轮制坯工艺。薛克敏等[19-20]采用冲锻复合成形技术对带轮轮毅锥度凸台冲锻增厚和双向厚差小圆角带轮成形工艺进行优化,有效避免金属流动成形过程中存在的失稳折叠和断裂等缺陷,显著降低加工载荷。
以往研究表明,板锻造技术与某些传统的加工方法相比具有生产效率高、生产成本低等优点,具有广阔的应用前景与实践价值。本文作者基于板锻造成形技术,针对底部带有实心凸起结构的铝合金筒形零件,采用拉深-墩挤板锻造成形工艺成形底部中心实心凸起结构,如图1所示,并结合有限元数值模拟及工艺试验,揭示凸起板锻造成形过程中的变形机理,探明凸起底部缩孔形成机制。
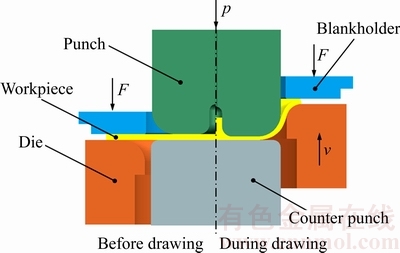
图1 实心凸起板锻造成形原理示意图
Fig. 1 Schematic diagram of solid boss forming principle during plate forging process
1 实心凸起成形过程的有限元解析
由于实心凸起结构零件变形具有轴对称性,采用DEFORM-2D数值模拟软件,以提高模拟计算效率和精度。分别建立了两种成形工艺的有限元模型:图2(a)为传统反挤压模型,图2(b)为拉深-镦挤板锻造模型。整个有限元模型中除板料为塑性体外,其他均设为刚性体,压边圈和凹模与板料之间的摩擦系数设为0.05,凸模和背压块与板料之间的摩擦系数设为0.1,加工速度均为1 mm/s。板料为A1050-O铝合金,其本构方程σ=168(ε+0.02)0.12。两种方式的成形模具结构尺寸相同,其模具和坯料的相关参数如表1所列。

图2 反挤压和拉深-镦挤工艺有限元模型
Fig. 2 FEM model of backward extrusion and compression-drawing process
2 模拟结果分析与讨论
2.1 加工载荷的比较
板锻造成形背压块加载6.4,压边力0.12,对实心凸起结构的成形过程进行模拟,将两种工艺的成形载荷和凸起高度进行对比,如图3所示。随着底部厚度的减薄,板锻造成形工艺的凸模载荷缓慢增加至稍高于背压力(拉深力的作用),并在其附近波动,而反挤压成形工艺的载荷急剧增加。板锻造成形过程中,靠近中心位置材料受压应力作用,靠近凸模圆角位置的底部板料受径向拉深应力作用,有利于金属的流动,而反挤压成形过程底部板料受压应力作用,径向受挤压应力较大,阻碍金属的流动,当成形3.4 mm的凸起高度时,反挤压所需载荷是板锻造成形的2倍左右。反挤压成形凸起高度的增加速度随底部厚度的减小而增大,板锻造成形凸起高度与底部壁厚始终呈线性关系增加,后趋于稳定。
表1 模具和坯料参数
Table 1 Dimensions of tools and blank
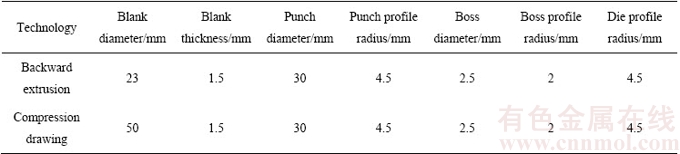
为了方便比较,将同一摩擦因数条件下,两种工艺成形十分接近的凸起高度视为相同高度。通过不同润滑条件下板锻造成形和反挤压成形工艺的加工载荷对比,如图4所示。在相同润滑条件下成形同一凸起高度时,两种工艺所需的成形载荷随摩擦因数的减小而减小,且板锻造工艺成形载荷减小的更快,摩擦因数越小,两种成形载荷的比值越大。因此,在成形实心凸起结构时,可采用板锻造成形工艺,并通过润滑条件的改善,从而更好的降低加工载荷。
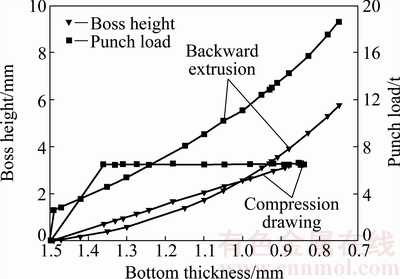
图3 两种工艺加工凸起高度与载荷随板料厚度的变化
Fig. 3 Variation of boss height and punch load with bottom thickness

图4 凸起高度与加工载荷随摩擦因数的变化(t0=1.5 mm,h≈3.4 mm)
Fig. 4 Variation of boss height and forming load with friction coefficient (t0=1.5 mm, h≈3.4 mm)
在实心凸起板锻造成形过程中,凸起底部板料的变形受到压边力和法兰变形抗力的影响较大,因此,保持其他条件不变,只改变压边力的大小,模拟结果如图5所示。随压边力的增加,凸起高度和凸起底部减薄量增大,当压边力大于12.2 kN后,凸模圆角底部发生断裂,由此可知当压边力增大10倍左右,凸起高度增加47%。
2.2 凸起成形过程分流面位置的分析
在实心凸起成形过程中,金属的流动特征影响着材料的流动、模具的填充及缺陷的形成与控制。实际加工凸起过程很难捕捉金属的塑性流动状态,因此,采用成形数值模拟技术,可动态观察金属材料变形过程的塑性流动状态。图6所示为模拟板锻造成形实心凸起结构过程中,底部金属瞬间的流动特征。模拟发现,实心凸起成形过程中离中心一定距离位置存在着塑性流动方向相反的分界面,即分流面,它将底部金属分成沿半径向内和向外两个塑性流动区域,金属材料内流填充而成形实心凸起,外流的金属材料被分配到外部筒壁。
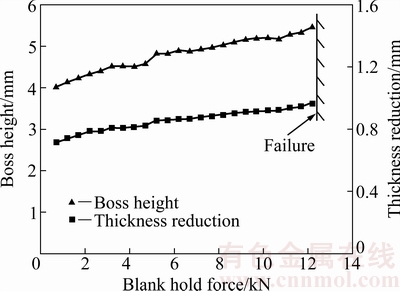
图5 凸起高度与减薄量随压边力的变化(t0=1.5 mm,μ=0.1)
Fig. 5 Variation of boss height and thickness reduction with blank holder force (t0=1.5 mm, μ=0.1)

图6 数值模拟底部材料的分流面特征
Fig. 6 Separation flow surface nature on part bottom by FEM numerical simulation

图7 分流半径随底部减薄量的关系(t0=1.5 mm, μ=0.1)
Fig. 7 Relationship between radii of separation flow surface and bottom thickness reduction (t0=1.5 mm, μ=0.1)
在凸起成形的不同时刻,分别对反挤压和板锻造工艺的分流特征进一步研究分析,如图7所示。对于板锻造成形而言,底部板料开始阶段受较大的径向拉应力,有利于材料外流,当拉深一定高度后受径向拉应力影响较小,分流面位置随底部减薄量的增加,开始内移,之后比较稳定;对于反挤压成形凸起,开始阶段径向为自由边界,受径向压应力的影响较小;随着凹模圆角部位的填充,径向压应力增加而阻碍金属外流,因此,分流面位置随底部减薄量的增加,开始比较稳定,之后逐渐外移。在实心凸起成形初始阶段,板锻造成形的分流半径大于反挤压的;凸起形成后期,板锻造成形的分流半径小于反挤压的。
2.3 板锻造成形实心凸起底部缩孔形成过程及控制
如果模具结构尺寸、毛坯尺寸以及工艺参数不合理,在板锻造成形实心凸起结构过程中,极易在实心凸起底部出现缩孔,如图8所示。本文作者采用易出现缩孔的薄板(t0=1.2 mm),进一步对实心凸起成形过程进行模拟,对缩孔形貌变化情况进行实时跟踪观察。
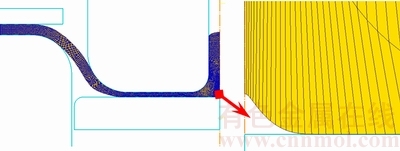
图8 板锻造成形中缩孔缺陷示意图
Fig. 8 Schematic diagram of dimple defect during compression- drawing process
凸模与板料之间的摩擦因数分别设为0、0.03、0.05、0.08、0.1,背压块与板料之间的摩擦因数设为0.2,其他接触摩擦因数均为0.05。 模拟结果如图9所示,缩孔深度随底部厚度的减薄开始增加,之后减小,最后增加,当凸模与板料之间的摩擦因数为0、0.03、0.05时,缩孔深度出现3个演化阶段,分别为一次缩孔阶段、缩孔消失阶段和二次缩孔阶段,并随摩擦因数的减小,缩孔消失阶段所对应的底部减薄量越大;当摩擦因数为0.08、0.1时,缩孔形成后一直存在,深度先增加,后减小,最后一直增加,减小的极小值随摩擦因数增加而增大,即缩孔越难消除。为了便于对缩孔变化规律的后续研究,定义一次缩孔消失时的板厚为最大板厚tmax,二次缩孔出现时的板厚为极限板厚tmin。因此,在板料成形实心凸起时,尽可能的改善凸模与板料之间润滑条件,从而抑制缩孔的形成,若要获得高质量的制件,设计制件的底部厚度尽量在最大板厚和极限板厚之间。
当底部厚度为0.8 mm时,分别对几种摩擦条件下离凸起底部中心同一高度的等效应变速率进行测量,其结果如图10所示。在凸起成形过程中,凸起部位的材料流动速率沿半径方向逐渐减小,即材料越靠近中心流动填充的速度越快,经过一定应变(材料的填充体积)的积累后,如果没有足够内流的材料及时补充时,就形成如图8所示的锥形缩孔。
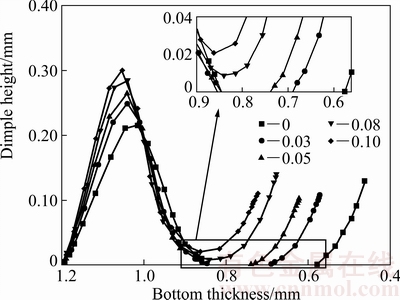
图9 润滑条件对缩孔高度的影响(t0=1.2 mm)
Fig. 9 Variation of dimple height at different frictions (t0=1.2 mm)
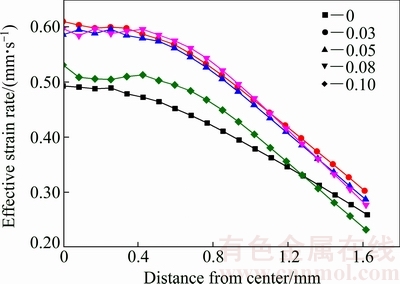
图10 凸起截面速度场的分布
Fig. 10 Distribution of velocity field on boss cross section
对板料两侧采用不同的润滑条件,凸模一侧的摩擦因数为0.03,背压块一侧的为0.2,以不同厚度坯料来成形相同结构的实心凸起。结果发现,当板厚t0≥1.6 mm时,成形实心凸起底部未出现缩孔;而是当底部减薄到一定厚度时,在凸模底部圆角处出现断裂。凸模底部圆角处断裂与二次缩孔出现时的凸起底部厚度一样,都是成形无缺陷实心凸起所对应的极限厚度tmin。为了形象表达成形实心凸起的缺陷与板厚之间的关系,建立板锻造成形实心凸起失效机制图,即表述原始板厚t0、最大板厚tmax和极限板厚tmin之间的关系及失效和安全区域,如图11所示。原始板厚、最大板厚和极限板厚曲线将图11右下方分成3个区域,最大板厚和极限板厚曲线之间为无缺陷的安全区域,其余为失效区域;在失效区域内,极限板厚曲线以下,板厚t0≥1.6 mm为断裂缺陷区域,t0<1.6 mm为二次缩孔缺陷区域。对于成形特定结构的实心凸起时,原始板厚越小,刚度越小,凸起底部越容易屈曲失稳出现缩孔;而原始板厚越大,法兰处的变形抗力越大,凸模圆角底部板料受拉应力增大易出现断裂。因此,随着原始板厚的增加,极限板厚先减小后增大,在t0=1.5 mm附近最小,一次缩孔所对应的变形厚度逐渐减小。通过失效机制图的建立,对板材上凸起结构的设计,加工原始板厚的选择具有一定的参考价值。
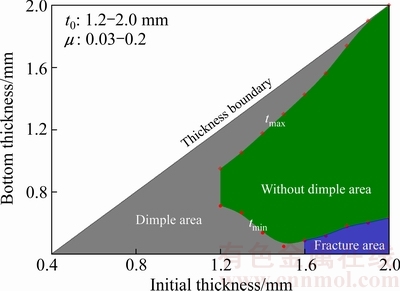
图11 实心凸起成形失效机制图
Fig. 11 Failure mechanism diagram of boss forming process
3 实心凸起成形实验验证
为了对上述模拟结果进行验证,自行设计板锻造成形模具和反挤压模具,在KTP-100伺服压力机上进行实心凸起成形实验。毛坯材料为A1050-O铝合金板材,润滑剂为P460+PTFE5%。
实验后,采用Origin分别对两种工艺不同的载荷及其所对应的凸起高度进行处理后,获得同一凸起高度的载荷大小,最后得到反挤压成形载荷与板锻造成形载荷比值的变化规律,如图12所示。由试验载荷比值曲线可知,相同凸起高度,板锻造成形载荷是反挤压成形的一半左右,与图3模拟所得的结果相一致。
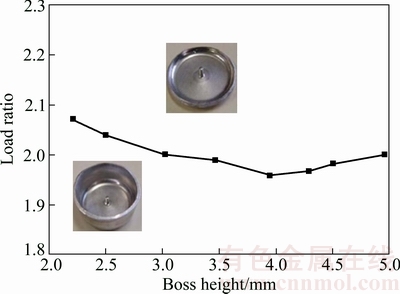
图12 成形载荷比值随凸起高度的关系
Fig. 12 Relationship between load ratio and boss height
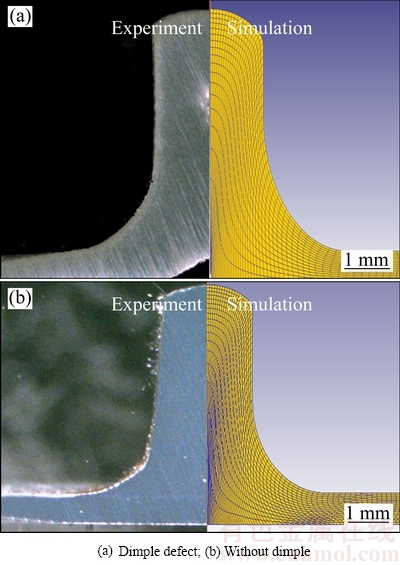
图13 实验与模拟结果对比
Fig. 13 Comparison of experiment and simulation results
对板料两面与凸模、背压块之间采用两种润滑方式:一种是板料两面润滑,另一种是凸模与板料上表面单面润滑。凸起成形实验后,将工件割开与模拟结果对比如图13所示。采取两面都润滑则出现缩孔如图13(a),实验的缩孔与模拟的缩孔几何尺寸相差较大,实验的缩孔锥度较大,而模拟的缩孔锥度较小,但是缩孔形成的规律是一致的。只对凸模一侧润滑则无缩孔出现,与模拟结果一致如图13(b)。由此表明,通过改善凸模与板料之间的润滑条件可以有效防止缩孔缺陷的形成。
4 结论
1) 板锻造成形凸起高度随底部厚度的变化呈线性增加,当成形相同实心凸起高度时,板锻造成形载荷比反挤压成形载荷减小一倍左右。
2) 板锻造成形过程中分流面位置随底部板厚的减薄先内移后趋于稳定,而反挤压成形则是先趋于稳定后外移。
3) 凸模与板料间的润滑条件对缩孔影响较大,采用板料上表面与凸模单面润滑,可以有效防止缩孔缺陷的产生。
REFERENCES
[1] SEMIATIN S L. ASM Handbook (Vol.14)[M]. 9th Edition. New York: John Wiley, 1993.
[2] NAKANO T. Compound technology of sheet metal forming and cold forming[J]. Journal of the Japan Society for Technology of Plasticity, 2001, 42(5): 22-26. (In Japanese)
[3] IMURA T. Forming examples of FCF method and points of utilization[J]. Press Working, 2008, 46(1): 28-33. (In Japanese)
[4] MORI K, NAKANO T. State-of-the-art of plate forging in Japan[J]. Production Engineering, 2016, 10(1): 81-91.
[5] MERKLEIN M, ALLWOOD J M, BEHRENS B A, BROSIUS A, HAGENAH H, KUZMAN K, MORI K, TEKKAYA A E, WECKENMANN A. Bulk forming of sheet metal[J]. CIRP Annals-Manufacturing Technology, 2012, 61(2): 725-745.
[6] MERKLEIN M, KOCH J, SCHNEIDER T. Fundamental investigations on the material flow at combined sheet and bulk metal forming processes[J]. CIRP Annals-Manufacturing Technology, 2011, 60(1): 283-286.
[7] KO D C, CHOI H S, JANG W S, KIM B M. Progressive process design of door lock striker with double bosses by the wall-thickening process[J]. The International Journal of Advanced Manufacturing Technology, 2013, 66(5/8): 1191-1199.
[8] MORI K, ABE Y, OSAKADA K, HIRAMATSU S. Plate forging of tailored blanks having local thickening for deep drawing of square cups[J]. Journal of Materials Processing Technology, 2011, 211(10): 1569-1574.
[9] 王新云, 夏巨谌, 陈志明, 胡国安.板冲锻成形新工艺及其在轿车飞轮盘加工中的应用[J]. 塑性工程学报, 2008, 15(4): 180-184.
WANG Xin-yun, XIA Ju-chen, CHEN Zhi-ming, HU Guo-an. Application of a new sheet stamping-forging hybrid technology in the forming of flying wheel panel of car[J]. Journal of Plasticity Engineering, 2008, 15(4): 180-184.
[10] LUO J C, WANG X Y, GUO M L, XIA J C. Precision research in sheet metal flanging and upset extruding[J]. Materials Research Innovations, 2011, 15(1): 439-442.
[11] WANG X Y, GUO M L, LUO J C, OUYANG K,XIA J C. Stamping-forging hybrid forming of double layer cup with different wall thicknesses[J]. Materials Research Innovations, 2011, 15(1): 435-438.
[12] ZHANG D W, YANG H. Analytical and numerical analyses of local loading forming process of T-shape component by using coulomb, shear and hybrid friction models[J]. Tribology International, 2015, 92: 259-271.
[13] ZHANG Da-wei,YANG He. Development of transition condition for region with variable-thickness in isothermal local loading process[J]. Transactions of Nonferrous Metals Society of China, 2014, 24(4): 1101-1108.
[14] ZHANG S H, CHENG S U N, WANG Z T. Finite element simulation on press forging of magnesium alloy AZ31 sheets[J]. Transactions of Nonferrous Metals Society of China, 2008, 18(S1): s269-s272.
[15] 张士宏, 周丽新, 王忠堂. 板材零件局部体积成形技术研 究[J]. 塑性工程学报, 2008, 15(2): 31-36.
ZHANG Shi-hong, ZHOU Li-xin, WANG Zhong-tang. Research on local bulk forming of sheet metal parts[J]. Journal of Plasticity Engineering, 2008, 15(2): 31-36.
[16] LIN Q Q, DONG W Z, WANG Z G. A new hole-flanging method for thick plate by upsetting process[J]. Transactions of Nonferrous Metals Society of China, 2014, 24(7): 2387-2392.
[17] DONG W Z, LIN Q Q, LI Y T. Analytical and FEM investigations on boss forming process by compression-drawing method[J]. Procedia Engineering, 2014, 81: 383-388.
[18] 林启权, 袁中林, 王振球. 厚板局部镦粗圆孔翻边的数值模拟[J]. 热加工工艺,2011, 40(3): 82-84.
LIN Qi-quan, YUAN Zhong-lin, WANG Zhen-qiu. Numerical simulation on upsetting-burring process for thick sheet[J]. Hot Working Technology, 2011, 40(3): 82-84.
[19] 王伶俐, 瞿 方, 薛克敏. 带轮轮毂锥度凸台冲锻增厚工艺及影响因素研究[J]. 锻压技术, 2014, 39(5): 40-45.
WANG Ling-li, QU Fang, XUE Ke-min. Research on stamping-forging hybrid forming process and influence factors for thickening tapered boss of hub of pulley[J]. Forging & Stamping Technology, 2014, 39(5): 40-45.
[20] 姚彭彭, 杨善文, 张建新, 朱建伟, 李 萍, 薛克敏. 双向厚差小圆角带轮冲锻成形工艺[J]. 塑性工程学报, 2015, 22(1): 1-5.
TAO Peng-peng, YANG Shan-wen, ZHANG Jian-xin, ZHU Jian-wei, LI Ping, XUE Ke-min. Stamping-forging hybrid forming of pulley parts with small fillet and thickness difference in two directions[J]. Journal of Plasticity Engineering, 2015, 22(1): 1-5.
Solid boss forming process of plate forging aluminium alloy
DONG Wen-zheng1, 2, 3, ZHANG Cun-yuan1, LIN Qi-quan1, WANG Zhi-gang3
(1. School of Mechanical Engineering, Xiangtan University, Xiangtan 411105, China;
2. State Key Laboratory of Materials Processing and Die and Mould Technology, Huazhong University of Science and Technology, Wuhan 430074, China;
3. Department of Mechanical and Systems Engineering, Gifu University, Gifu501-1193, Japan)
Abstract: A new solid boss plate forging process named compression-drawing method was proposed to form the aluminum alloy sheet. The finite element method with DEFORM-2D and experiments were used to investigate the solid boss forming process. As a result, the forming load of back-extrusion is about two times higher than that of plate forging when the same height boss is acquired. During the solid boss forming, the location of separation flow surface first moves inner side and then remains stable as for plate forging, while it first remains stable and then moves outer side as for back extrusion. Besides, single lubrication between punch and upper side of workpiece can prevent the dimple defect.
Key words: aluminum alloy sheet; solid boss; plate forging; separation flow surface; dimple defect mechanism
Foundation item: Projects(51575467, 51605408) supported by the National Natural Science Foundation of China; Project(P2018-010) supported by State Key Laboratory of Materials Processing and Die & Mould Technology, Huazhong University of Science and Technology, China
Received date: 2016-09-02; Accepted date: 2017-06-09
Corresponding author: LIN Qi-quan; Tel: +86-731-58292454; E-mail: xtulqq@163.com
(编辑 李艳红)
基金项目:国家自然科学基金资助项目(51575467,51605408);华中科技大学材料成形与模具技术国家重点实验室开放课题研究基金资助项目(P2018-010)
收稿日期:2016-09-02;修订日期:2017-06-09
通信作者:林启权,教授,博士;电话:0731-58292454;E-mail:xtulqq@163.com