DOI: 10.11817/j.issn.1672-7207.2020.11.007
润滑相粒度对Ag-WS2复合材料摩擦磨损行为的影响
李云,孙阳,康潇,张雷,周科朝
(中南大学 粉末冶金国家重点实验室,湖南 长沙,410083)
摘要:采用放电等离子烧结技术制备WS2粒度分别为80 nm,600 nm和6 μm的Ag-WS2固体润滑复合材料,研究WS2粒度对复合材料摩擦磨损行为的影响,并对Ag-WS2复合材料磨损表面微观形貌进行分析。研究结果表明:随着WS2粒度由6 μm降低至80 nm,Ag-WS2复合材料的摩擦因数从0.21降低到0.09,磨损率由4.68×10-5 mm3/(N·m)降低到3.35×10-5 mm3/(N·m),Ag-WS2复合材料磨损机制由磨粒磨损和疲劳磨损共同作用转变为轻微的磨粒磨损;WS2粒度显著影响界面润滑膜的形成,粒度越小的WS2越容易填充到磨损表面的沟槽或微凸体的间隙结构中,有助于形成连续、平整的润滑膜,从而显著降低Ag-WS2复合材料的摩擦因数和磨损率。
关键词:Ag-WS2复合材料;润滑相粒度;润滑膜;摩擦磨损
中图分类号:TH117.2 文献标志码:A
文章编号:1672-7207(2020)11-3064-08
Effect of lubricating phase size on tribological behavior of Ag-WS2 composites
LI Yun, SUN Yang, KANG Xiao, ZHANG Lei, ZHOU Kechao
(State Key Laboratory of Powder Metallurgy, Central South University, Changsha 410083, China)
Abstract: The Ag-WS2 solid lubricating composites containing WS2 granularity of 80 nm, 600 nm and 6 μm were prepared by spark plasma sintering, and the influence of WS2 granularity on the tribological behavior of the composites was investigated. The wear surface micro-morphology of Ag-WS2 composites was analyzed.The results show that as the WS2 granularity decreases from 6 μm to 80 nm, the friction coefficient of the Ag-WS2 composites decreases from 0.21 to 0.09, and the wear rate of the composites decreases from 4.68×10-5 mm3/(N·m) to 3.35×10-5 m3/(N·m). The wear mechanism of Ag-WS2 composites changes from the combined effect of abrasive wear and fatigue wear to slight abrasive wear.WS2 granularity significantly affects the formation of interfacial lubricating film. The smaller granularity of WS2 makes it easier to fill the grooves or micro-convex gaps on the wear surface, which can form a continuous and smooth lubricating film, and thereby significantly reduce the friction coefficient and wear rate of the Ag-WS2 composites.
Key words: Ag-WS2 composites; lubricating phase size; lubricating film; friction and wear
金属基固体润滑复合材料既具有优异的力学性能和导电、导热性能,又具有良好的润滑和摩擦磨损性能,广泛应用于汽车配件、精密仪器、航空航天、军事装备等领域[1-2]。随着现代工业的快速发展,人们对机械运动部件的摩擦磨损性能提出了更高的要求。研究金属基固体润滑复合材料的摩擦学机理[3-4],设计制造具有更高性能的金属基固体润滑复合材料是国内外学者的重点关注方向。在金属基固体润滑复合材料的摩擦过程中,润滑相通过物质转移在接触表面形成润滑膜,减缓金属与金属直接接触所产生的黏着效应,从而降低材料的摩擦因数与磨损率[5]。已有研究发现,金属基固体润滑复合材料的摩擦磨损性能与其应用条件[6-7]及润滑相的体积分数[8-10]密切相关。WU等[6]研究了环境气氛对WS2体积分数约为30%的AgCu-WS2复合材料摩擦学行为的影响,发现与潮湿空气条件下相比,干燥N2气氛下,复合材料磨损表面更加平整,磨损表面WS2润滑膜覆盖率高达58%,摩擦因数由0.19降低到0.09,磨损率下降43%;XIAO等[10]研究了MoS2体积分数为0~40%的Cu-MoS2复合材料摩擦磨损行为,并基于X线光电子能谱(XPS)分析方法表征了磨损表面MoS2润滑膜的覆盖率,发现当MoS2体积分数由5%提升到40%时,磨损表面润滑膜覆盖率由31%提升到73%,摩擦因数也由0.48降低到0.14,磨损率下降1个数量级。除了应用条件和润滑相体积分数外,润滑相的粒度也会显著影响金属基自润滑复合材料的摩擦学性能。RAJKUMAR等[3]对比了微米石墨与纳米石墨对铜基复合材料摩擦磨损性能的影响,发现在不同载荷下,石墨体积分数同为15%的铜-纳米石墨复合材料的摩擦因数均低于铜-微米石墨复合材料的摩擦因数,磨损率仅为铜-微米石墨复合材料的1/2。RAPOPORT等[11]比较了WS2粒度分别为120 nm和4 μm的Cu-WS2复合材料的摩擦磨损性能,发现当WS2粒度为120 nm时,Cu-WS2复合材料摩擦因数降低40%,磨损率降低了50%。金属基固体润滑复合材料的应用条件[6]或润滑相体积分数发生改变[10]会导致磨损表面形貌特征及表面润滑膜覆盖率发生变化,进而影响其摩擦磨损行为,而低粒度的润滑相颗粒虽也能够显著提高金属基固体润滑复合材料的摩擦磨损性能,但润滑相粒度对金属基固体润滑复合材料摩擦磨损行为的影响规律与机制尚有待进一步探索。银与其他金属材料相比具有良好的电导率和热导率以及耐高温、抗腐蚀等优良性能,在电子元件以及航空航天等领域具有广阔的使用前景[1],但目前有关Ag-WS2固体润滑复合材料摩擦磨损行为的报道很少,研究润滑相粒度对银基固体润滑复合材料的摩擦磨损行为的影响机理,为新型银基固体润滑复合材料的应用提供理论依据具有显著意义。为此,本文作者采用粒度分别为80 nm,600 nm和6 μm的WS2颗粒制备Ag-WS2复合材料并研究WS2粒度对复合材料摩擦磨损性能的影响规律,重点分析复合材料磨损表面组织形貌特征及润滑膜覆盖率,揭示WS2粒度对Ag-WS2复合材料摩擦磨损行为的影响机理。
1 实验
1.1 材料制备
采用粉末冶金技术制备3种粒度(80 nm,600 nm与6 μm)的WS2颗粒增强的Ag-WS2复合材料,分别命名为S-80,S-600和S-6。WS2颗粒形貌如图1所示,粒度为600 nm和6 μm的WS2颗粒为片层状结构,粒度为80 nm的WS2颗粒为颗粒状结构。Ag粉和WS2粉按WS2质量分数为23.4%(体积分数为30%)进行配料,然后将称量好的粉末放入行星球磨机中混合均匀(球磨转速为250 r/min,球料比为10:1,时间为8 h)。随后,将均匀混合的粉末在氢气气氛下(400 ℃,2 h)还原,并将还原后的Ag/WS2复合粉末填充到石墨模具中,采用放电等离子烧结(SPS)技术烧结。烧结参数如下:以100 ℃/min的升温速度从室温升温至750 ℃,于750 ℃保温15 min,然后冷却至室温,整个烧结过程压力保持在45 MPa。
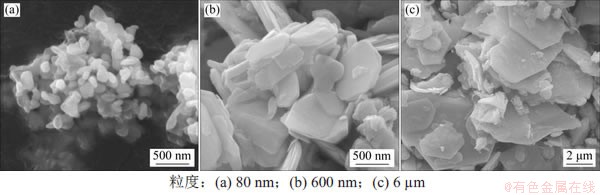
图1 WS2粉末形貌
Fig. 1 WS2 powder morphologies
1.2 摩擦磨损测试
采用瑞士CSM公司生产的销盘式摩擦实验机对Ag-WS2复合材料进行摩擦磨损测试。将Ag-WS2复合材料切割成长×宽×高为3 mm×3 mm×5 mm块体并与AgCu10合金盘对磨,AgCu10合金盘的硬度为120 HB。摩擦磨损测试参数如下:载荷为3.0 N,转速为100 r/min(线速度为0.28 m/s),滑动距离为10.0 km。通过电子分析天平测量磨损前后Ag-WS2复合材料的质量以计算体积磨损率,体积磨损率计算公式为Wvol=△m/(ρpd)[12](其中,Wvol为体积磨损率(mm3 /(N·m)),△m为磨损质量损失(g),ρ为样品密度(g/cm3),p为法向载荷(N),d为滑动距离(m))。
1.3 材料表征
Ag-WS2复合材料的硬度利用维氏硬度计(中国华银,610VS-30)进行测试,测试载荷为100 N,取10次测量结果的平均值作为最终硬度。分别使用德国Leica公司的DM2400M型金相显微镜和日本Rigaku公司的D/Max 2550型X线衍射仪(XRD)对Ag-WS2复合材料的微观组织和物相进行分析。采用美国FEI公司生产的Nova NanoSEM 230型场发射扫描电子显微镜表征Ag-WS2复合材料磨损表面显微形貌,并使用美国Veeco Metrology公司的WYKO NT9100型光学轮廓仪对磨损表面3D轮廓及表面粗糙度进行测量。为了研究Ag-WS2复合材料磨损表面润滑相的迁移行为,采用美国Thermo Scientific公司的K-Alpha 1063型X线光电子能谱仪测定Ag-WS2复合材料磨损表面不同深度的成分。
2 结果与分析
2.1 Ag-WS2复合材料微观组织与XRD分析
粒度分别为80 nm,600 nm和6 μm的WS2颗粒增强的Ag-WS2复合材料X线衍射图谱见图2(a)。从图2(a)可见:这3种不同粒度的Ag-WS2复合材料具有相同的峰位,分别归属于Ag和WS2的衍射峰,表明在烧结过程中Ag和WS2之间没有发生化学反应,WS2晶体结构被完整保留;Ag-WS2复合材料中WS2的衍射峰强度随着WS2粒度减小而降低,这是由于当WS2粒度由6 μm减小到80 nm时,WS2的晶粒随之减小,引起衍射谱带宽化,从而导致衍射峰强度降低。图2(b),(c)和(d)所示分别为3种不同粒度的Ag-WS2复合材料的金相组织结构,图中黑色区域为WS2颗粒,白色区域为银基体。从图2(b),(c)和(d)可见:样品S-80的WS2颗粒为小尺寸聚集体,并均匀分布在银基体中;样品S-600和S-6中WS2为片状结构,3种不同粒度的Ag-WS2复合材料的WS2结构与图1中3种WS2颗粒的微观形貌一致。
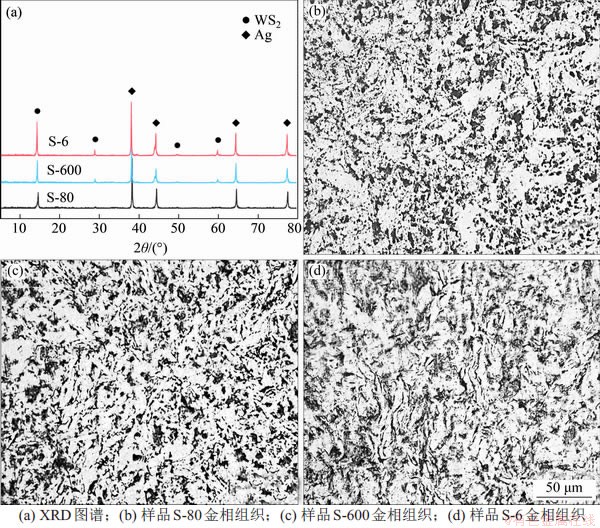
图2 Ag-WS2复合材料XRD图谱及金相组织结构
Fig. 2 XRD pattern and metallographic structures of Ag-WS2 composites
2.2 复合材料机械性能
3种粒度(80 nm,600 nm和6 μm)的WS2颗粒增强的Ag-WS2复合材料密度、致密度和硬度见表1。从表1可见:当WS2粒度由6 μm减小到80 nm时,Ag-WS2复合材料的致密度从96.4%减小到93.6%,维氏硬度(HV10)从53.4增加到64.9;Ag-WS2复合材料的致密度随WS2粒度减小变化不大,但硬度显著增加,这归因于WS2颗粒对银基体的增强作用;随着WS2粒度减小,材料内部晶界迁移和位错运动所受的阻力越大,与样品S-600和S-6相比,样品S-80的力学性能更加优异[14-15]。
表1 Ag-WS2复合材料的密度与硬度
Table 1 Density and hardness of Ag-WS2 composites

2.3 WS2粒度对Ag-WS2复合材料摩擦磨损性能的影响
WS2粒度会显著影响Ag-WS2复合材料的摩擦磨损性能[3]。3种不同粒度的Ag-WS2复合材料在3 N载荷下的摩擦因数与滑动距离的关系见图3。由图3可知:在摩擦初期,3种Ag-WS2复合材料的摩擦因数下降明显,曲线斜率较大;随着摩擦时间延长,样品S-6摩擦因数曲线斜率稳定,摩擦因数缓慢下降;样品S-600摩擦因数曲线趋于稳定;而样品S-80的摩擦因数曲线在达到稳定之前,有一段较长的跑合期,跑合期内样品S-80的摩擦因数不断减小;在跑合过程中,金属基体逐渐被磨损,固体润滑剂从基体中释放出来,黏着在摩擦表面,形成低摩擦因数的润滑膜,从而能持续有效地润滑,降低金属基体材料的磨损。较长的跑合期意味着样品S-80样品形成稳定连续润滑膜的时间更长。图4所示为3种不同粒度的Ag-WS2复合材料的平均摩擦因数与磨损率。从图4可见:随着WS2粒度由6 μm减小至80 nm,Ag-WS2复合材料平均摩擦因数由0.21降低到0.09,磨损率与平均摩擦因数呈现相同的变化趋势,由4.68×10-5 mm3/(N·m)降低到3.35×10-5 mm3/(N·m)。
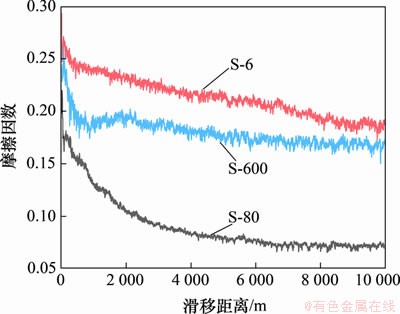
图3 Ag-WS2复合材料摩擦因数曲线
Fig. 3 Friction coefficient curves of Ag-WS2 composites
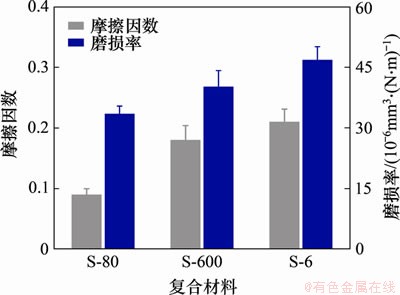
图4 Ag-WS2复合材料平均摩擦因数与磨损率
Fig. 4 Average friction coefficients and wear rate of Ag-WS2 composites
对3种不同粒度的2Ag-WS2复合材料磨损表面的显微形貌及3D轮廓形貌进行检测分析,结果如图5所示。图5(a),(c)和(e)显示3种Ag-WS2复合材料磨损表面均形成了润滑层;样品S-80磨损表面润滑层连续且完整,表面上存在轻微的犁沟,磨损机制以磨粒磨损为主;随着WS2粒度从80 nm增加到600 nm和6 μm,磨损表面除了犁沟还出现明显的裂纹和剥层凹坑,Ag-WS2复合材料磨损机制转变为磨粒磨损与疲劳磨损共同作用。图5(b),(d)和(f)所示为3种不同粒度的Ag-WS2复合材料磨损表面3D轮廓。从图5(b),(d)和(f)可见:随着WS2粒度减小,Ag-WS2复合材料磨损表面粗糙度由3.31 μm降低到1.66 μm。这是由于在Ag-WS2复合材料的摩擦过程中,WS2颗粒在正压力和剪切力的作用下富集在磨损表面,粒度越小的WS2颗粒更容易填充到沟槽或者表面微凸体的间隙结构中,使磨损表面形成完整且连续的润滑层,显著减少磨损表面的犁沟、裂纹和剥层凹坑,降低磨损表面粗糙度。图6所示为Ag-WS2复合材料摩擦过程结束后磨损深度轮廓图。从图6可见:样品S-600和S-6的磨损表面都可观测到明显的沟槽,而样品S-80的磨损表面相对光滑;磨损表面划痕比例越高,WS2颗粒的填充效率越差。统计磨损深度超过1 μm的沟槽长度占总长的比例(取样方式如图6所示),确定WS2颗粒的填充效率。结果表明:样品S-80,S-600和S-6磨损表面上磨损深度超过1 μm的沟槽长度占总长的比例分别为24.19%,18.57%和9.52%;WS2颗粒的填充效率依次升高。摩擦副接触时由磨损表面的粗糙峰先接触,表面越粗糙,接触面积越小,单个接触峰所受的压力越大,接触的尖端部分容易破损导致磨损率增大;粗糙表面的犁削阻力较大,摩擦因数也较高。低粗糙度的磨损表面使材料具有更好的摩擦磨损性能[15]。
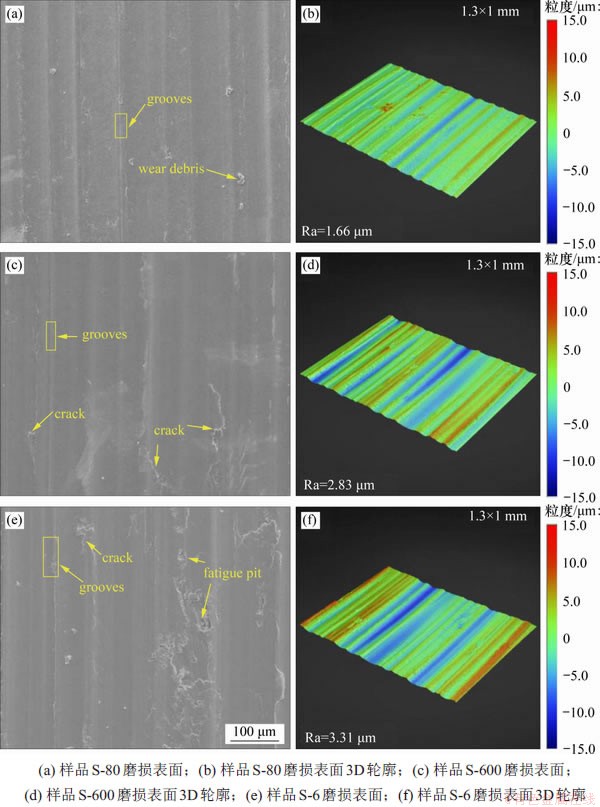
图5 Ag-WS2复合材料磨损表面形貌与3D轮廓形貌
Fig. 5 Worn surface morphologies and 3D profile morphologies of Ag-WS2 composites

图6 Ag-WS2复合材料磨损深度轮廓图
Fig. 6 Wear depth contour map of Ag-WS2 composites
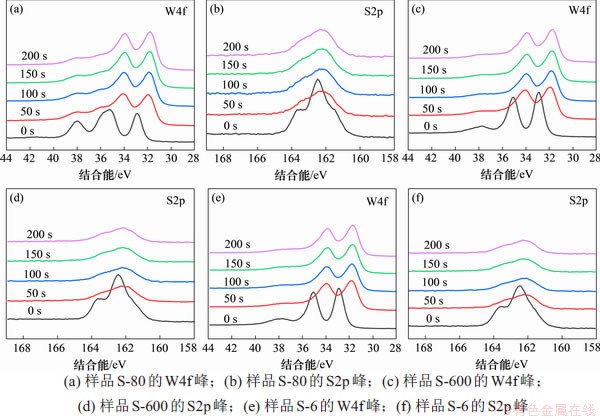
图7 Ag-WS2复合材料磨损表面的XPS刻蚀分析
Fig. 7 XPS etching analysis of Ag-WS2 composites
2.4 磨损面XPS分析
金属基固体润滑复合材料的磨损表面被一层具有润滑特性的润滑层覆盖[5],为研究润滑层的组成,用XPS技术对Ag-WS2复合材料磨损表面元素成分进行逐层分析。图7所示为3种Ag-WS2复合材料磨损表面的XPS刻蚀分析结果。从图7(a)和(b)可见:当刻蚀时间为0 s时,样品S-80磨损表面W4f和S2p峰的强度最高;当刻蚀到50 s时,W4f和S2p峰的强度明显减弱,并且随着刻蚀时间延长,W4f和S2p峰的强度基本保持不变;同时,样品S-600和S-6磨损表面的W4f和S2p峰强度呈现相同的变化趋势,这表明3种不同粒度的Ag-WS2复合材料的磨损表面均富积了WS2颗粒。根据磨损表面的各元素的摩尔分数进行换算得到不同刻蚀深度WS2质量分数如图8所示。从图8可见:3种不同粒度的Ag-WS2复合材料磨损表面WS2质量分数均远比基体的高,当刻蚀时间为0 s时,样品S-80,S-600和S-6磨损表面WS2质量分数分别为51.48%,48.86%和46.83%,均为基体WS2质量分数的2倍多;随着刻蚀时间延长,样品S-80中WS2质量分数一直稳定在35%以上,比另外2组样品的高;样品S-600和S-6中WS2质量分数相近,对应着它们的摩擦因数也相差不大;样品S-80在摩擦过程中,WS2一直向表面聚集并且不易脱落成磨屑,最终导致磨损表面WS2覆盖率显著提高;在摩擦过程中,WS2颗粒从材料内部挤出并在摩擦表面形成润滑层,随着WS2颗粒粒径减小,WS2润滑层的覆盖率增大,摩擦因数显著降低。
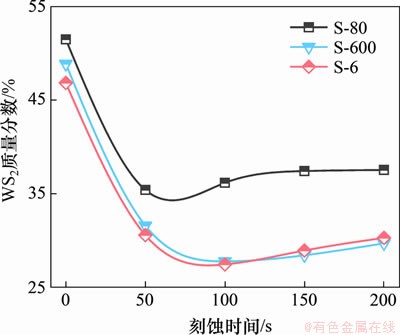
图8 Ag-WS2复合材料WS2质量分数随刻蚀时间的变化曲线
Fig. 8 Evolution curves of WS2 mass fraction of Ag-WS2 composite material with etching time
摩擦力Ff是黏着阻力Fa和犁削阻力Fp共同作用的结果[16],即Ff=Fa+Fp,黏着阻力与接触界面的剪切强度成正比,而犁削阻力与材料表面粗糙度和硬度有关。随着表面粗糙度增大,犁削阻力也会上升。在金属基固体润滑材料的摩擦过程中,接触界面分3部分组成,即金属与金属接触、润滑膜与金属接触、润滑膜与润滑膜接触[10],金属与金属接触的剪切强度显著强于另外2种接触方式的剪切强度。图9所示为WS2粒度对Ag-WS2复合材料润滑机理示意图。样品S-80在摩擦过程中,磨损表面富积的润滑相颗粒会填充到磨损表面的沟槽或微凸体的间隙结构中,这一方面,降低磨损表面粗糙度,减小摩擦力的犁削分量,另一方面,增大Ag-WS2复合材料磨损表面润滑膜覆盖率,减缓金属与金属的直接接触所产生的黏着效应,降低接触界面的剪切力。这2个方面共同促使样品S-80具有低摩擦因数(0.09)和低磨损率(3.35×10-5 mm3/(N·m))。在样品S-6和S-600中,由于WS2颗粒较大,WS2颗粒不能充分地渗入磨损表面的沟槽或微凸体的间隙结构中,在摩擦过程中常以磨屑的形式从磨损面脱落,不利于在磨损面形成连续稳定的润滑膜,因此,其摩擦因数较高(分别为0.21和0.18),磨损率较大(分别为4.68×10-5 mm3/(N·m)和 4.02×10-5 mm3/(N·m))。
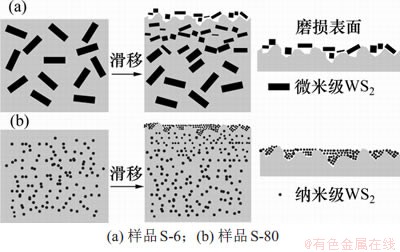
图9 Ag-WS2复合材料润滑机理示意图
Fig. 9 Schematic illustrations for lubrication mechanism of Ag-WS2 composites
3 结论
1) 随着WS2粒度由6 μm降低到80 nm,Ag-WS2复合材料的维氏硬度(HV10)由53.4提高到64.9,摩擦因数从0.21降低到0.09,磨损率由4.68×10-5 mm3/(N·m)降低到3.35×10-5 mm3/(N·m)。
2) 随着WS2粒度减小,Ag-WS2复合材料磨损表面裂纹和剥落区域逐渐消失,表面愈加平滑,磨损面粗糙度由3.31 μm下降到1.66 μm。Ag-WS2复合材料磨损机制由磨粒磨损和疲劳磨损共同作用转变为轻微的磨粒磨损。
3) 随着WS2粒度降低,Ag-WS2复合材料磨损表面WS2质量分数由46.83%增大到51.48%;在WS2质量分数相同时,纳米WS2颗粒可以有效填充到磨损表面的沟槽或微凸体的间隙结构中,增大复合材料磨损表面润滑膜覆盖率,降低Ag-WS2复合材料摩擦因数和磨损率,表现出最优异的摩擦学性能。
参考文献:
[1] 王常川, 王日初, 彭超群, 等. 金属基固体自润滑复合材料的研究进展[J]. 中国有色金属学报, 2012, 22(7): 1945-1955.
WANG Changchuan, WANG Richu, PENG Chaoqun, et al. Research progress of metallic solid self-lubricating composites[J]. The Chinese Journal of Nonferrous Metals, 2012, 22(7): 1945-1955.
[2] YEHIA H M, ABU-OQAIL A, ELMAGHRABY M A, et al. Microstructure, hardness, and tribology properties of the (Cu/MoS2)/graphene nanocomposite via the electroless deposition and powder metallurgy technique[J]. Journal of Composite Materials, 2020, 54(23): 3435-3446.
[3] RAJKUMAR K, ARAVINDAN S. Tribological behavior of microwave processed copper-nanographite composites[J]. Tribology International, 2013, 57(1): 282-296.
[4] 王新平, 肖金坤, 张雷, 等. 银合金粉末粒度对Ag-MoS2复合材料摩擦磨损性能的影响[J]. 中国有色金属学报, 2012, 22(10): 2811-2817.
WANG Xinping, XIAO Jinkun, ZHANG Lei, et al. Effect of silver alloy particle size on friction and wear properties of Ag-MoS2 composites[J]. The Chinese Journal of Nonferrous Metals, 2012, 22(10): 2811-2817.
[5] SCHARF T W, PRASAD S V. Solid lubricants: a review[J]. Journal of Materials Science, 2013, 48(2): 511-531.
[6] WU Jisi, LI Jingfu, ZHANG Lei, et al. Effects of environment on dry sliding wear behavior of silver-copper based composites containing tungsten disulfide[J]. Transactions of Nonferrous Metals Society of China, 2017, 27(10): 2202-2213.
[7] CHEN Fanyan, FENG Yi, SHAO Hao, et al. Friction and wear behaviors of Ag/MoS2/G composite in different atmospheres and at different temperatures[J]. Tribology Letters, 2012, 47(1): 139-148.
[8] XIAO Jinkun, ZHANG Wei, ZHANG Chao. Microstructure evolution and tribological performance of Cu-WS2 self-lubricating composites[J]. Wear, 2018, 412-413(10): 109-119.
[9] ZHAO Lin,YAO Pingping, GONG Taiming, et al. Effect of adding tungsten disulfide to a copper matrix on the formation of tribo-film and on the tribological behavior of copper/tungsten disulfide composites[J]. Tribology Letters, 2019, 67(3): 1-13.
[10] XIAO Jinkun, WU Yuqing, ZHANG Wei, et al. Friction of metal-matrix self-lubricating composites: relationships among lubricant content, lubricating film coverage, and friction coefficient[J]. Friction, 2020, 8(3): 517-530.
[11] RAPOPORT L, FELDMAN Y, HOMYONFER M, et al. Inorganic fullerene-like material as additives to lubricants: structure–function relationship[J]. Wear, 1999, 225-229(4): 975-982.
[12] HUANG Shiyin, FENG Yi, LIU Hongjuan, et al. Electrical sliding friction and wear properties of Cu-MoS2-graphite-WS2 nanotubes composites in air and vacuum conditions[J]. Materials Science and Engineering: A, 2013, 560(2): 685-692.
[13] MOGHANIAN A, SHARIFIANJAZI F, ABACHI P, et al. Production and properties of Cu/TiO2 nano-composites[J]. Journal of Alloys and Compounds, 2017, 698(9): 518-524.
[14] HAN Tielong, LI Jiajun, ZHAO Naiqin, et al. In-situ fabrication of nano-sized TiO2 reinforced Cu matrix composites with well-balanced mechanical properties and electrical conductivity[J]. Powder Technology, 2017, 321(17): 66-73.
[15] CHEN Xiang, HAN Zhong, LI Xiuyan, et al. Lowering coefficient of friction in Cu alloys with stable gradient nanostructures[J]. Science Advances, 2016, 2(12): 1-7.
[16] XIAO Jinkun, ZHANG Lei, ZHOU Kechao, et al. Anisotropic friction behaviour of highly oriented pyrolytic graphite[J]. Carbon, 2013, 65(15): 53-62.
(编辑 陈灿华)
收稿日期: 2020 -08 -28; 修回日期: 2020 -10 -12
基金项目(Foundation item):国家自然科学基金资助项目(51674304) (Project(51674304) supported by the National Natural Science Foundation of China)
通信作者:张雷,博士,研究员,从事金属基复合材料的理论与应用研究;E-mail: zhanglei@csu.edu.cn