DOI:10.19476/j.ysxb.1004.0609.2017.10.13
原位自生TiC-M7C3粒柱混杂结构及其干滑动摩擦学特性
袁有录1,张 屹2,李铸国3
(1. 三峡大学 机械与动力学院 水电机械设备设计与维护湖北省重点实验室,宜昌 443002;
2. 常州大学 机械工程学院,常州 213164;
3. 上海交通大学 材料科学与工程学院 上海市激光制造与材料改性重点实验室,上海 200240)
摘 要:以Fe-Ni-Cr-Ti-C粉末为原料,采用等离子束原位冶金技术在低碳钢表面合成颗粒柱体混杂增强TiC-M7C3/Fe复合涂层。利用光学显微镜、扫描电镜、电子能谱、X射线衍射仪、同步热分析仪及热力学计算,分析TiC与M7C3混杂生长特征,考察干滑动摩擦条件下粒柱混杂结构的摩擦学特性。结果表明:原位合成时初生相TiC可作为次生相M7C3的形核基底促进M7C3形核;TiC-M7C3粒柱混杂与单一M7C3增强相比耐磨性提高了31.5%;其干滑动摩擦温升与滑动距离之间符合指数渐近稳定关系y=a-b×cx;混杂增强时,M7C3磨损面裂纹率和脆性剥落坑增加,涂层的干滑动磨损机理主要为磨粒磨损和氧化磨损。
关键词:原位冶金;TiC-M7C3;混杂结构;干滑动;摩擦学
文章编号:1004-0609(2017)-10-2062-10 中图分类号:TG115;TH117.3 文献标志码:A
磨损是机械设备失效的主要原因。常用耐磨材料主要为高铬铸铁,其增强相为复合碳化物M7C3。全世界铬资源有限,我国又是贫铬国家,近10年因铬资源大量消耗,其价格也增长了4~5倍,从而制约了高铬耐磨材料的应用。
原位自生TiC-M7C3多元混杂增强涂层近来备受关注。首先,原位自生的碳化物具有内部缺陷少、分布均匀、表面无污染、与金属基体润湿性好、结合强度高等优点;其次,多元碳化物可以克服单一碳化物使用上的局限性,多元增强体之间可以“取长补短”,对基体的增强产生“协同作用”[1-2];最后,表面涂层技术可节省贵重材料的使用、改善材料表面性能、提高材料表面耐磨性、拓宽材料应用领域。苏允海等[3-4]以钛铁(Ti-Fe)、铬铁(Cr-Fe)、还原铁粉(Fe)及石墨(C)为原料,配置了Fe-Cr-C和Fe-Cr-Ti-C系合金粉末,采用等离子堆焊设备在20 g钢板表面制备了TiC-M7C3/Fe涂层,研究了涂层的组织及其协同抗磨性能,得出Fe-Cr-Ti-C系合金比相同Cr含量的Fe-Cr-C系合金硬度更高,抗磨损性能更好的结论。但有关原位自生TiC与M7C3混杂生长特征及其干滑动摩擦磨损机理方面的研究仍然较少。
因此,本文作者分别以Fe-30Ni、Cr粉、Ti粉及石墨为原料,配制Fe-Ni-Cr-Ti-C混合粉末;采用等离子束原位冶金工艺,在Q235基板上通过原位反应制备TiC-M7C3混杂增强Fe基复合涂层;分析TiC颗粒与M7C3柱体在涂层中的混杂生长特征,并考察TiC-M7C3粒柱混杂结构的干滑动摩擦学特性。
1 实验
制备涂层的基板为普通结构钢Q235A,尺寸 100 mm×50 mm×5 mm,对表面进行喷砂处理以去除板材轧制过程中所形成的斑迹、结疤、氧化皮等。制备TiC-M7C3/Fe复合涂层的原料为Fe-30Ni、Cr粉、Ti粉及石墨(成分见表1)。为了与原位自生的TiC混杂M7C3增强Fe基涂层进行对比分析,同时制备了不加Ti粉的M7C3/Fe涂层。制备TiC-M7C3/Fe涂层时粉末的混合比例(质量分数)为24% Cr、1% Ti、4.89% C、其余为Fe-30Ni。为了与TiC-M7C3混杂增强铁基涂层的性能进行对比分析,本文作者同时又制备了不含TiC的单一柱状碳化物M7C3增强铁基涂层M7C3/Fe,制备该涂层的粉末混合比例为24% Cr、4.87% C、其余为Fe-30Ni。
表1 粉末化学成分
Table 1 Chemical compositions of deposited powders
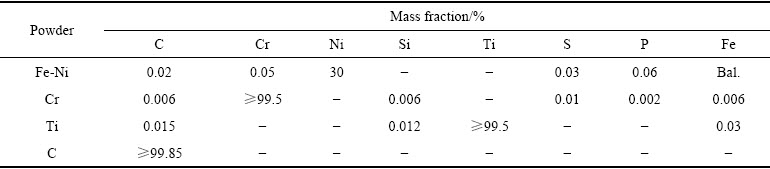
本研究采用等离子弧原位合成法用来制备涂层。制备前,先把各粉末进行干燥处理(120 ℃,1 h),然后依混合比例称取粉末并混合。待粉末混合均匀后装入粘结在基板上的保温套(刚玉)并压实。工艺中使用保温套的目的:一是防止较轻混合粉末在等离子弧加热过程中被气体及等离子弧产生的离子流力、斑点压力等驱散;二是降低涂层的冷却速度,延长熔池中元素原位反应时间,使碳化物晶体得到生长。等离子弧原位冶金时,先用非弧对保温套中表层粉末进行预熔化(因非弧的等离子流力较低,可避免粉末溅出),然后再切换至转弧加热,因其温度较高(10000~15000 ℃),会迅速熔化粉末并与基体达到冶金结合。
涂层制备后用线切割切下试样,经制样抛光后,用腐蚀剂(V(HCL):V(C2H5OH)=1:1)对试样进行腐蚀。用MDJ200型光学金相显微镜观察金相组织。用JSM-6510LA型扫描电镜分析磨损面及磨损磨粒的微观结构。用Inca X-Max 能谱仪分析组织与磨粒元素组成及含量。用DX-2700X型X射线衍射仪分析涂层物相组成。用HV1000型显微硬度计测量显微硬度,载荷质量为300 g,加载时间10 s。
干滑动摩擦磨损试验在M-2000型试验机上进行。摩擦条件为:载荷200 N,滑动速度0.836 m/s,滑动距离500 m。涂层为上试样,尺寸30 mm×7 mm×5 mm,表面粗糙度Ra≤0.6 μm。下试样(偶件)为T10钢轮,内外径分别为d 40 mm和d 16 mm,厚度为10 mm,经调质处理后洛氏硬度为(60±1) HRC,表面粗糙度Ra≤0.8 μm。摩擦因数由试验机自动采集,采集频率为100次/s。摩擦温升由试验机自带的红外测温仪自动测量并记录(测温范围0~500 ℃)。
材料的耐磨性能一般用磨损率来表征,且对于不同的研究对象需用不同的磨损率,如对于固定距离的磨损,需采用单位距离磨损率;对于连续摩擦,需采用单位时间内的磨损率;对于密度不同材料间的磨损常采用体积磨损率。由于原位自生碳化物TiC与M7C3以及Fe基体之间的密度相差较大。因此,本研究采用体积磨损率表征涂层的耐磨性,计算式为[5]:
(mm3/(N·m)) (1)
式中:Δm是摩擦过程中的质量损失,磨损前后的质量用MettlerAG204型电子分析天平称量(精度0.1 mg),结果取3次测量平均值;
是涂层的密度,gm/cm3,先由浸水法测量体积V,再由MettlerAG204称取质量m,最后由
=m/V计算密度;Fn是外加载荷,N;L是摩擦距离,m。涂层磨损面的形貌及成分用SEM和EDS分析。
2 结果与讨论
2.1 合金体系相图分析
本研究首先采用热力学相图计算软件Thermo- Calc对Fe-Ni-Cr-C与Fe-Ni-Cr-Ti-C多元合金体系的平衡相图进行了计算,结果如图1所示。可以看到:1) Fe-Ni-Cr-C合金体系共晶点的碳含量约为5.3%。这表明碳含量为 4.87%的涂层为亚共晶组织。当温度沿着4.87% C降低时,先从液相中析出复合碳化物M7C3。当温度降到1363 K时,发生L→γ转变。温度下降到1344 K时,液相中析出过剩石墨,最后涂层主要组织为α、γ、M7C3、过剩石墨(见图1(a));2) Fe-Ni-Cr-Ti-C合金体系共晶点碳含量约为5.2%。这表明碳含量为 4.89%的涂层为亚共晶组织。当温度沿4.89% C下降时,先从液相中析出TiC。当温度降到1520 K时,再从液相中析出M7C3。温度下降到1356 K时,发生L→γ转变。温度下降到1314 K时,液相中析出过剩石墨,最后涂层主要组织为γ、TiC、M7C3、过剩石墨(见图1(b))。计算结果表明,依设计比例制备的涂层中可以获得多元碳化物TiC和M7C3。
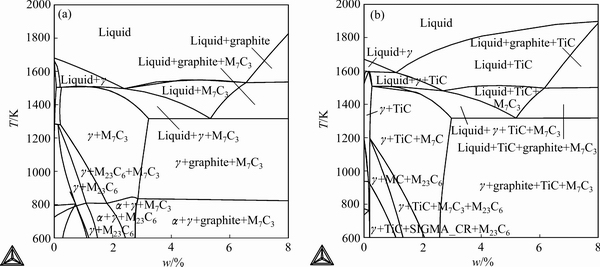
图1 Fe-Ni-Cr-C与Fe-Ni-Cr-Ti-C系垂直截面相图
Fig. 1 Calculated vertical section diagrams of Fe-Ni-Cr-C(a) and Fe-Ni-Cr-Ti-C(b) systems
2.2 涂层组织结构
图2所示为Fe-Ni-Cr-C与Fe-Ni-Cr-Ti-C系合金粉末经等离子原位冶金工艺制备涂层的XRD谱。可以看到:1) 由Fe-Ni-Cr-C混合粉末制备涂层的主要组织为奥氏体γ[Fe,Ni]和碳化物M7C3;2) 由Fe-Ni-Cr-Ti-C混合粉末制备涂层的主要组织为奥氏体γ[Fe,Ni]、TiC、M7C3。这表明在Fe-Ni-Cr-C系粉末中添加1%Ti后,涂层中合成出了TiC和M7C3两种碳化物。

图2 Fe-Ni-Cr-C系与Fe-Ni-Cr-Ti-C系的XRD谱
Fig. 2 XRD patterns of Fe-Ni-Cr-C(a) and Fe-Ni-Cr-Ti-C(b) systems
图3所示为Fe-Ni-Cr-C系粉末制备涂层组织。可以看到涂层宏观厚度接近3 mm,涂层与基体发生熔合,二者之间为冶金结合,涂层内部显微组织由分布较均匀的基体、块状及板条状组织组成(见图3(a)),将组织放大后可以看到块状组织为六边形结构(见图3(b))。为了观察块状组织的三维生长特征,对周围基体进行了深腐蚀处理,可以看到六边形块状组织的三维结构为六棱柱状(见图3(c))。EDS结果表明,该组织的元素组成为29Fe-3Ni-64Cr-4C(见表2),结合XRD分析结果可知,六棱柱体为复合碳化物M7C3(M=Fe, Ni, Cr),与其他文献结果相符[6-7]。为了方便,由Fe-Ni-Cr-C系粉末制备涂层简称为M7C3/Fe涂层。
图4所示为Fe-Ni-Cr-Ti-C系粉末制备涂层组织。可以看到涂层宏观厚度接近3 mm,涂层与基体发生熔合,二者之间为冶金结合,涂层内部显微组织由分布较均匀的亮色块状、深色细颗粒及基体组成(见图4(a))。放大后可以发现,基体与亮色块体中均分布有许多细小颗粒组织(见图4(b))。同样对涂层基体进行了深腐蚀处理,可以看到柱体表面及内部均生长有颗粒(见图4(c))。结合EDS(表2)与XRD分析结果可知,柱体组织为复合碳化物M7C3,颗粒组织为TiC,其三维生长特征为八面体,尺寸在10~20 μm之间,远小于M7C3。这表明相同条件下,TiC的生长速度远小于M7C3的。为了方便,由Fe-Ni-Cr-Ti-C系粉末制备涂层简称为TiC-M7C3/Fe涂层。
对比图3(a)与图4(a)可以发现:在Fe-Ni-Cr-C系粉末基础上添加1%Ti后,涂层中生成M7C3的量增加了,而尺寸减小了。表明添加的Ti对原位合成的M7C3有细化尺寸和促进形核的作用。
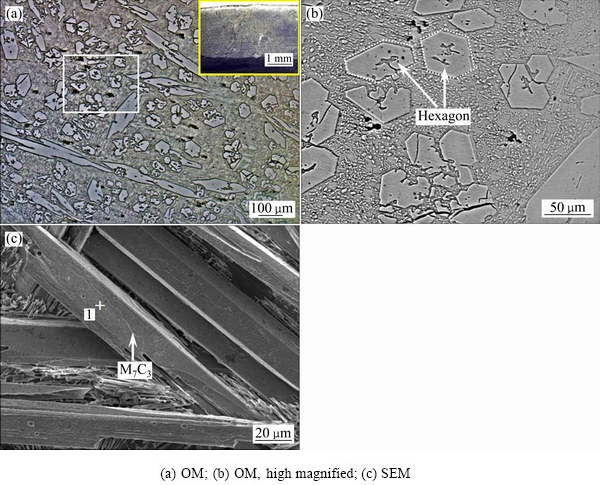
图3 Fe-Ni-Cr-C系涂层组织
Fig. 3 Microstructures of coating of Fe-Ni-Cr-C system
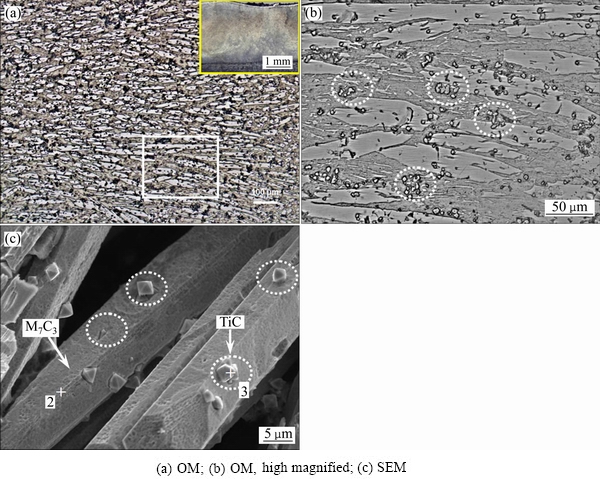
图4 Fe-Ni-Cr-Ti-C系涂层组织
Fig. 4 Microstructures of coating of Fe-Ni-Cr-Ti-C system
表2 能谱分析结果
Table 2 Results of EDS analysis
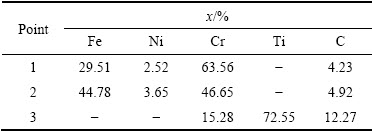
2.3 TiC-M7C3混杂生长的晶体学结构关系
由Fe-Ni-Cr-Ti-C体系相图(见图1(b))可知:涂层冷却过程中,首先发生L→TiC转变,然后为L→ TiC+M7C3,即液相中先析出TiC,其次为M7C3。TiC-M7C3/Fe涂层组织结果(见图4)表明:在M7C3的内部生成有TiC颗粒,说明TiC应先于M7C3生成。结果表明:涂层中的Ti对M7C3柱体有细化尺寸和促进形核的作用。这表明初生相TiC(s) 可作为次生相M7C3的形核剂,从而促进M7C3在涂层中的形核和细化尺寸。
这种次生相M7C3以初生相TiC(s)为基底进行形核的能力可通过二者之间的晶体结构关系分析。由晶体界面共格理论可知[8]:当次生相表面原子排列和间距与初生相TiC(s)衬底相近时,两相间的界面自由能降低。此时,初生相TiC(s)具有促进次生相M7C3形核的作用。因为原子处于点阵平衡位置时,其势能较低,偏离该位置就会引起势能的升高。当液相原子向固相基底堆砌新相时,需降低两相界面自由能,即减少两相间的点阵错配度。异质形核时,两相间点阵错配度为零的情况很少,这称为绝对匹配。多数情况下,只要两相间点阵错配度处于一个较小的范围,就可以实现两相界面共格对应。此时,次生相基底与初生相晶核之间具有较低的界面自由能,有利于次生相形核。BRAMFITT[9]对TURNBUL等[10]的点阵错配度公式改进后,通过计算次生相低指数晶面与初生相低指数晶面重合度来计算它们之间的点阵错配度,其公式为
(2)
式中:(hkl)s是外加固相基底的低指数晶面;[uvw]s是(hkl)s晶面上的低指数晶向;(hkl)n是晶核的低指数晶面;[uvw]n是(hkl)n晶面上的低指数晶向;d[uvw]n是沿[uvw]n晶向的点阵间距;d[uvw]s是沿[uvw]s晶向的点阵间距;
是[uvw]s和[uvw]n之间的夹角(
≤90°)。研究表明:当点阵错配度
<6%时,初生固相基底对促进次生相形核非常有效;6%≤
≤12%时,初生固相基底对促进次生相形核为有效;而
>12%时,初生固相基底对促进次生相形核为无效。
由XRD分析可知,添加Ti粉后涂层中次生相M7C3的晶格结构为正交系,晶格常数为a=0.701 nm,b=1.214 nm,c=0.453 nm。初生相TiC为面心立方结构,晶格常数为a=0.432 nm。把TiC与M7C3的晶格常数分别代入式(2)计算得出低指数晶面(110)TiC与(001)M7C3之间的错配度为
=9.3% (见表3),属于6%≤
≤12%范围。表明TiC可有效促进柱状碳化物M7C3的形核。计算结果与实验结果相吻合(见图4),TiC与M7C3的晶格错配关系见图5。
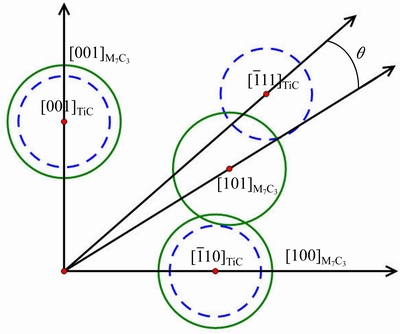
图5 初生相TiC与次生相M7C3晶格错配度关系
Fig. 5 Relationship of lattice misfits between TiC and M7C3
2.4 TiC-M7C3原位反应热力学
由XRD分析结果可知(见图2),当Fe-Ni-Cr-C中添加Ti粉后,涂层中合成了M7C3和TiC两种碳化物。组织结果显示(见图4),在M7C3柱体内部和表面均有TiC颗粒。晶体学计算结果表明,M7C3柱体可以TiC为基底进行非匀质形核。所以当Ti比例增加时,生成TiC的量增加,M7C3形核增多,使M7C3柱体得到了细化。接下来本文作者采用热力学计算对此加以分析。
表3 TiC与M7C3低指数面上的错配度计算结果
Table 3 Calculation results of two-dimensional lattice misfits between planes of TiC and M7C3

由于Fe-Ni-Cr-Ti-C体系涂层中没有检测出其他碳化物(如:Fe3C、Cr4C、Cr23C6、Cr3C2等),因此仅需比较体系生成M7C3和TiC两种碳化物的难易。另外,复合碳化物M7C3 (M=Fe, Ni, Cr)是由Fe、Ni取代Cr7C3中部分Cr而成。因此,可简化为体系生成Cr7C3和TiC两种碳化物的难易。这两种碳化物的反应式为
Ti+C→TiC (3)
7Cr+3C→Cr7C3 (4)
两种化学式不同温度下的反应热和自由能采用下式计算:
(5)
(6)
(7)
式中:
和
分别为温度T时某物质i的反应热效应和反应熵差;
为反应的Gibbs自由能;物质的摩尔定压热容
,J/(mol·K);
和
为物质发生相变的相变热和相变熵,若发生相变的物质在反应中是生成物,则为“+”,是反应物则为“-”。计算所用的热力学数据见表4,计算结果见图6。
如图6(a)所示,反应式(3)和(4)的Gibbs自由能△G都为负值。说明在热力学上,两个反应都能发生。但反应式(3)的△G远低于式(4)的,所以反应式Ti+C=TiC更容易发生,即在热力学上更易生成碳化物TiC。同时图6(b)显示,反应式(3)和(4)的反应生成焓△H的绝对值都比较大,说明反应过程中放热较多。
图7所示为Fe-Ni-Cr-C和Fe-Ni-Cr-Ti-C体系的DSC分析。可以看到,没有添加Ti粉时,Fe-Ni-Cr-C体系冷却过程只有一个放热峰,其温度为1537 K,与图6(a)热力学计算的放热温度1500 K接近。当加入1% 的Ti后,Fe-Ni-Cr-Ti-C体系中有两个放热峰:其中一个较大的放热峰温度为1532 K,接近1537 K,可知该放热峰应为式(4)反应放热;另一个较小的放热峰温度为1579 K,该温度大于1532 K,可知该放热峰应为式(3)的反应放热。同时,图7显示7Cr+3C=Cr7C3的反应放热远大于Ti+C=TiC,表明复合涂层中原位合成的柱状碳化物Cr7C3远多于TiC。这与涂层组织结果相吻合(见图4)。
2.5 TiC-M7C3粒柱混杂结构干滑动摩擦学特性
图8所示为涂层M7C3/Fe和TiC-M7C3的干滑动摩擦因数与摩擦温升随滑动距离的变化。可以看到,摩擦起始阶段(即“跑合阶段”)涂层的摩擦因数在一个较小范围内波动升上,然后增大至一个较大范围的波动期后,进入一个相对稳定状态(即“稳定阶段”),形成一个“S”形曲线。单一柱状M7C3增强涂层在“跑合阶段”的摩擦因数波动范围相比TiC-M7C3复合涂层的大。“跑合阶段”摩擦因数的波动现象是由新接触的两个对摩样微观表面上凹凸不平引起[1]。因为开始摩擦时,高的微凸区域因摩擦而发生剥落,摩擦受力不均。之后,两对摩样表面之间逐渐趋于匹配,最初的表面被磨掉,新的表面形成,两对摩样表面结构发生变化。由此造成摩擦因数在滑动过程中增大或减小的波动。
干滑动摩擦的一个显著特点是摩擦过程中伴随有较大的热量产生和传递。润滑摩擦时,润滑剂可以把摩擦所产生的热迅速带走,降低温度。而干摩擦条件下,摩擦副之间不但产生热量多(因其摩擦系数较大),且产生的热量不能被及时带走,只有通过热传导被链接设备或空气带走[12]。两个摩擦副发生干摩擦时,其接触表面实为微凸体接触,这些微凸体在一定压力下接触并发生相对滑动会在微凸体上出现很高的瞬间温度(简称“闪温”)。闪温出现在几个微米的表面上,其温度高达几百摄氏度,持续的时间为几纳秒到几微秒,并在滑动过程中时刻变化。由于摩擦热仅释放在那些微凸点上,所以微凸体的温升很高,当达到一定值后,会使摩擦副的磨损机理发生转变,如发生氧化磨损。
表4 计算所用的热力学数据[11]
Table 4 Thermodynamic parameters


图6 式(3)和(4)的Gibbs自由能△G和反应生成焓△H随温度变化
Fig. 6 △G-T(a) and △H-T(b) curves of reactions (3) and (4)
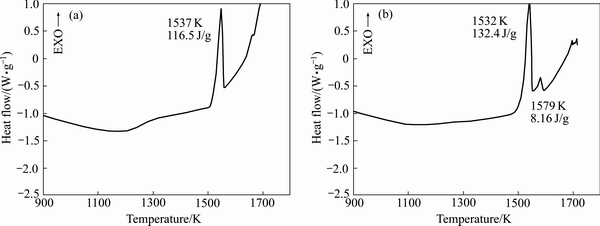
图7 Fe-Ni-Cr-C和Fe-Ni-Cr-Ti-C体系的DSC曲线
Fig. 7 DSC curves of Fe-Ni-Cr-C(a) and Fe-Ni-Cr-Ti-C(b) systems
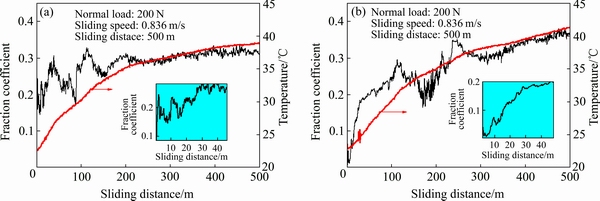
图8 M7C3/Fe和TiC-M7C3/Fe涂层摩擦因数变化
Fig. 8 Variation of friction coefficient of M7C3/Fe(a) and TiC-M7C3/Fe(b) coatings
图9所示为采用最小二乘法对干滑动摩擦温升和滑动距离之间关系进行了拟合,结果见表5。可以看到,二者符合指数渐近稳定模型:y=a-b×cx。涂层M7C3/Fe和TiC-M7C3拟合方程的调整决定系数R2分别为0.998和0.997,接近1,表明涂层摩擦温升y与滑动距离x之间为强相关。涂层M7C3/Fe和TiC-M7C3拟合方程的导数y′分别为0.169×0.99x和0.204× 0.99x(表4)。y′随x的增加而减小。表明两种结构涂层的摩擦温升在摩擦起始阶段升上较快,而后逐渐减慢。TiC-M7C3涂层的y′大于M7C3/Fe涂层,表明TiC-M7C3涂层温升速率较大,所以TiC-M7C3涂层的摩擦温度(41.4 ℃)高于M7C3/Fe涂层(39℃)。
图10所示为M7C3/Fe和TiC-M7C3/Fe两种结构涂层表面碳化物增强相磨损特征对比。可以看到:1) 单一M7C3增强涂层中,M7C3柱体磨损表面出现较多裂纹及脆性剥落坑,柱体周围基体出现凹坑,并有显微犁沟出现;2) 在TiC-M7C3混杂增强涂层中,M7C3柱体磨损表面同样出现较多裂纹和脆性剥落坑,与单一M7C3增强涂层相比,裂纹率增加,说明M7C3柱体内部生长的TiC颗粒使其脆性增加,但柱体周围基体没有发现凹坑,表明基体内部原位合成的TiC颗粒增加了基体的耐磨性[13-14]。
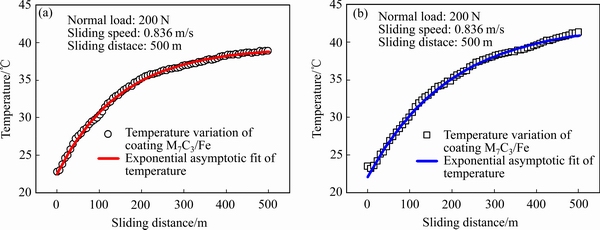
图9 M7C3/Fe和TiC-M7C3/Fe涂层摩擦温度变化
Fig. 9 Variation of temperature of M7C3/Fe(a) and TiC-M7C3/Fe(b) coatings
表5 涂层摩擦温升与滑动距离非线性拟合结果
Table 5 Nonlinearity fitting results of temperature and sliding distance

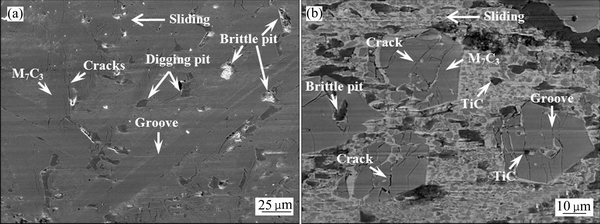
图10 M7C3/Fe和TiC-M7C3/Fe涂层表面碳化物磨损特征
Fig. 10 Characteristic of worn surface of carbide in M7C3/Fe(a) and TiC-M7C3/Fe(b) coatings
图11所示为M7C3/Fe和TiC-M7C3/Fe两种结构涂层的磨损面,为方便观察,对涂层磨损面倾斜了一定角度。可以看到,两个涂层表面均出现了犁沟和磨粒,表明两个涂层表面均发生犁削。但两涂层的磨损程度不同,如:1) TiC-M7C3混杂增强涂层表面的犁沟尺寸与单一M7C3增强涂层相比较小,这是因为TiC-M7C3/Fe涂层表面平均显微硬度(578 HV0.3)大于M7C3/Fe涂层(550 HV0.3),所以其磨损量(1.0 mg)相比M7C3/Fe涂层(1.4 mg)较小,涂层的磨损率(13×10-7 mm3/Nm)相比M7C3/Fe涂层(19×10-7 mm3/Nm)较低,TiC-M7C3混杂增强Fe基涂层的耐磨性提高了31.5%;2) TiC-M7C3/Fe涂层表面的磨粒磨屑相比M7C3/Fe涂层多(虚线区域),EDS结果显示,TiC-M7C3/Fe涂层表面磨粒主要元素组成(摩尔分数,%)为26.74 Fe、 2.12 Ni、4.78 Cr、0.16 Ti、64.99 O、1.21 C,M7C3/Fe涂层表面磨粒主要元素组成(摩尔分数,%)为28.34 Fe、1.82 Ni、2.48 Cr、65.21O、2.15 C。两种涂层表面磨粒中氧含量(摩尔分数,%)均较高(>30.29%[15]),说明均发生了氧化磨损。同时,磨粒中Ni与Cr的含量与涂层元素含量相比均较低,而Fe的含量却较高,表明涂层磨损面上的磨粒主要来之对磨轮(T10钢)而不是涂层。
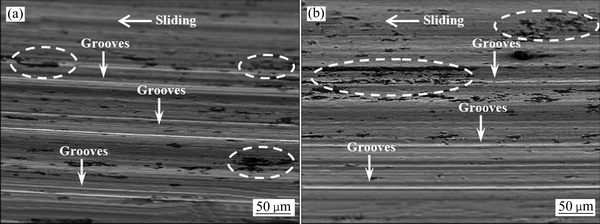
图11 M7C3/Fe和TiC-M7C3/Fe涂层表面磨损特征
Fig. 11 Characteristic of worn surface of M7C3/Fe(a) and TiC-M7C3/Fe(b) coatings
3 结论
1) 实验结果与热力学计算结果表明,在TiC-M7C3混杂结构中,原位自生的初生相TiC颗粒可以作为次生相柱状碳化物M7C3的非匀质形核基底,可以促进M7C3在涂层中形核,提高M7C3的生成量。
2) TiC-M7C3原位混杂生长时,TiC与M7C3的混杂生长特征如下:在柱状碳化物M7C3的内部及表面均生长有TiC颗粒,大部分TiC颗粒单独生长,但有部分TiC颗粒发生团聚生长,所以由八面体结构生长为多面体结构。
3) 干滑动摩擦条件下,TiC-M7C3混杂增强的摩擦温升及温升速率均较单一M7C3增强涂层高,且干滑动摩擦温升与滑动距离之间符合指数渐近稳定关系y=a-b×cx。TiC-M7C3/Fe涂层的磨损率较M7C3/Fe涂层的低,耐磨性高。与单一M7C3增强涂层相比,TiC-M7C3混杂增强时,M7C3内部生长的TiC颗粒使其脆性增加,磨损面裂纹率增加,而生长于涂层基体中的TiC使基体的耐磨性增加。两种结构涂层的干滑动磨损机理主要为犁削、磨粒磨损及氧化磨损。
REFERENCES
[1] 殷 婷, 田保红, 张 毅, 刘 勇, 宋克兴. 放电等离子烧结Cu-W-TiC复合材料的制备及其热变形特性[J]. 中国有色金属学报, 2015, 26(9): 2445-2452.
YIN Ting, TIAN Bao-hong, ZHANG Yi, LIU Yong, SONG Ke-xing. Preparation of Cu-W-TiC composites and its hot deformation characteristics[J]. The Chinese Journal of Nonferrous Metals, 2015, 26(9): 2445-2452.
[2] 孙志雨, 范景莲, 李鹏飞, 成会朝, 田家敏. 添加微量TiC对钨的性能与显微组织的影响[J]. 中国有色金属学报, 2015, 25(1): 80-85.
SUN Zhi-yu, FAN Jing-lian, LI Peng-fei, CHENG Hui-chao, TIAN Jia-min. Effect of microscale TiC on performance and microstructure of tungsten[J]. The Chinese Journal of Nonferrous Metals, 2015, 25(1): 80-85.
[3] 刘政军, 李乐成, 宗琳, 苏允海. 原位合成TiC-M7C3陶瓷硬质相显微组织的分析[J]. 焊接学报, 2012, 33(3): 65-68.
LIU Zheng-jun, LI Le-cheng, ZONG Lin, SU Yun-hai, Analysis on microstructure of in-situ synthesis TiC-M7C3 ceramic hard phase[J]. Transaction of the China Welding Institution, 2012, 33(3): 65-68.
[4] 苏允海,秦昊,吴德广, 刘政军. 原位合成TiC和M7C3陶瓷硬质相的生长习性[J]. 焊接学报, 2012, 33(11): 59-62.
SU Yun-hai, QIN Hao, WU De-guang, LIU Zheng-jun. Growth habit of TiC and M7C3 ceramic hard phase in situ synthesized[J]. Transaction of the China Welding Institution, 2012, 33(11): 59-62.
[5] SARMADI H, KOKABI A H, SEYED REIHANI S M. Friction and wear performance of copper–graphite surface composites fabricated by friction stir processing (FSP)[J]. Wear, 2013, 304(1): 1-12.
[6] 袁有录, 李铸国. 柱状碳化物(Cr,Fe)7C3增强Fe基涂层的摩擦磨损性能[J]. 材料研究学报, 2013: 27(6): 622-630.
YUAN You-lu, LI Zhu-guo. Friction and wear performance of carbide (Cr,Fe)7C3 reinforced Fe-based composite coating[J]. Chinese Journal of Materials Research, 2013, 27(6): 622-630.
[7] WU Xiao-jun, XING Jian-dong, FU Han-guang, ZHI Xiao-hui. Effect of titanium on the morphology of primary M7C3 carbides in hypereutectic high chromium white iron[J]. Materials Science and Engineering A, 2007, 457(1/2): 180-185.
[8] 介万奇. 晶体生长原理与技术[M]. 北京: 科学出版社, 2001: 149-159.
JIE Wan-qi. Principle and Technology of Crystal Growth[M]. Beijing: Science Press, 2010: 149-159.
[9] BRAMFITT B L. The effect of carbide and nitride additions on the heterogeneous nucleation behavior of liquid iron[J]. Metallurgical and Materials Transactions B, 1970, 1(7): 1987-1995.
[10] TURNBULL D, VONNEGUT B. Nucleation catalysis[J]. Industrial & Engineering Chemistry, 1952, 44(6): 1292-1298.
[11] 梁英教, 车荫昌. 无机物热力学数据手册[M]. 沈阳: 东北大学出版社, 1993: 372.
LIANG Ying-jiao, CHE Yinchang. Thermodynamic datebook of inorganic[M]. Shenyang: Northeastern University Press, 1993: 372.
[12] PIRSO J, VILJUS M, LETUNOVITS S. Friction and dry sliding wear behaviour of cermets[J]. Wear, 2006, 260(7): 815-824.
[13] TAN Ye-fa, HE Long, WANG Xiao-long, HONG Xiang, WANG Wei-gang. Tribological properties and wear prediction model of TiC particles reinforced Ni-base alloy composite coatings[J]. Transactions of Nonferrous Metals Society of China, 2014, 24(8): 2566-2573.
[14] CAI Bin, TAN Ye-fa, HE Long, TAN Hua, GAO Li. Tribological properties of TiC particles reinforced Ni-based alloy composite coatings[J]. Transactions of Nonferrous Metals Society of China, 2013, 23(6): 1681-1688.
[15] MA Guo-zheng, XU Bin-shi, WANG Hai-dou, SI Hong-juan, YANG Da-xiang. Effect of surface nanocrystallization on the tribological properties of 1Cr18Ni9Ti stainless steel[J]. Materials Letters, 2011, 65 (9): 1268-1271.
Hybrid structure and dry sliding tribological characteristics of in-situ synthesizing TiC-M7C3
YUAN You-lu1, ZHANG Yi2, LI Zhu-guo3
(1. Hubei Key Laboratory of Hydroelectric Machinery Design & Maintenance, College of Mechanical and Power Engineering, China Three Gorges University, Yichang 443002, China;
2. School of Mechanical Engineering, Changzhou University, Changzhou 213164, China;
3. Shanghai key Laboratory of Materials Laser Processing and Modification, School of Material Science and Engineering, Shanghai Jiaotong University, Shanghai 200240, China)
Abstract: The TiC-M7C3 hybrid reinforced Fe-based coating was fabricated by in-situ reaction method on low carbon steel plate by plasma in-situ metallurgy process with Fe-Ni-Cr-Ti-C powders. Microstructure and hybrid growth character of TiC-M7C3 in the coating were analyzed by OM, SEM, XRD, EDS, simultaneous DSC-TGA, and thermodynamic analysis. Dry sliding wear behavior of TiC-M7C3/Fe coating was tested and compared with single rod carbide M7C3 reinforced Fe-based coating M7C3/Fe. The results show that the primary phase TiC can effectively act as the substrate for the nucleation of M7C3, thus can promote the formation of M7C3 in the TiC-M7C3/Fe coating. The dry sliding wear resistance, frictional temperature, surface crack rate and brittle peeling pit of M7C3 rod of coating TiC-M7C3/Fe are higher than that of M7C3/Fe. The relationship between temperature and sliding distance fits the exponential asymptotic stability model y=a-b×cx. The main dry sliding wear mechanism of coating TiC-M7C3/Fe are abrasive wear and oxidation wear.
Key words: in-situ metallurgy process; TiC-M7C3; hybrid structure; dry sliding; tribology
Foundation item: Project(2016KJX05) supported by the Research Foundation of Hubei Key Laboratory of Hydroelectric Machinery Design & Maintenance, China Three Gorges University, Hubei Province, China; Project(20161212) supported by the Doctoral Starting up Foundation of China Three Gorges University, Hubei Province, China
Received date: 2016-07-21; Accepted date: 2017-01-20
Corresponding author: YUAN You-lu; Tel: +86-717-6397560; E-mail: yylu@ctgu.edu.cn
(编辑 何学锋)
基金项目:水电机械设备设计与维护湖北省重点实验室(三峡大学)(2016KJX05);三峡大学博士科研基金(20161212)
收稿日期:2016-07-21;修订日期:2017-01-20
通信作者:袁有录,副教授,博士;电话:0717-6397560;E-mail: yylu@ctgu.edu.cn