Influences of fine pitch solder joint shape parameters on fatigue life under thermal cycle
HUANG Chun-yue(黄春跃)1, 2, WU Zhao-hua(吴兆华)2,HUANG Hong-yan(黄红艳)2, ZHOU De-jian(周德俭)2
(1. School of Electro-Mechanical Engineering, Xidian University, Xian 710071, China;
2. Department of Electronic Machinery and Transportation Engineering, Guilin University of Electronic Technology, Guilin 541004, China)
Abstract: The solder joint reliability of a 0.5mm lead pitch, 240-pin quad flat package(QFP) was studied by nonlinear finite element analysis(FEA). The stress/strain distributions within the solder joints and the maximum plastic strain range of the solder joints were determined. Based on the calculated maximum plastic strain range the thermal fatigue life of the solder joints was calculated using Coffin-Manson equation. The influences of shape parameters including volume of solder joint, pad size and stand-off on the thermal fatigue life of the solder joints were also studied. The results show that the stress and strain distribution in the solder joint are not uniform; the interface between the lead and the solder joint is the high stress and strain region; the maximum stress and stain occur at the topmost point where the solder joint intersects with the inner side of the lead. The solder joint cracks should occur firstly at this point and propagate along the interface between the solder and the lead. The solder joint with the pad size of 1.25mm×0.35mm, the stand-off of 0.02mm and the solder volume of 0.026mm3 has longer fatigue life than that of any others. These optimal parameters have been applied in practice to assemble the 240-pin, 0.5mm pitch QFP.
Key words: fine pitch; solder joint shape; nonlinear finite element analysis; thermal fatigue life CLC number: TG405
Document code: A
1 INTRODUCTION
The electronicer industry is driven mainly by the demand for “smaller, faster, higher complexity, lower power consumption and cheaper”[1]. To meet these needs, the demand for smaller size, higher density and higher heat dissipation integrated circuit(IC) chips is on the rise. With the requirements of high performance and small package size, the design of IC chips is headed toward higher pin count, smaller pad size and fine pitch; consequently, the fine pitch technology is a key to electronic industry. When the lead pitch of a surface mount component is equal to or less than 0.65mm, then it is called a fine-pitch surface mount component(SMC)[2]. As a typical model of fine-pitch SMC, the lead pitch of quad flat package(QFP) has been developed from early 0.8mm pitch to 0.65mm and 0.5mm pitch in dominant as yet, the 376-pin, 0.35mm pitch QFP has also been applied[3], but 0.2mm pitch QFP is very rare[4]. With the same size of 32mm×32mm, 0.8mm pitch QFP contains 120pins, and 0.5mm pitch, 0.3mm pitch QFP contains 208pins, 328pins, respectively. The increase in number of leads results in the difficulty of assembling, and some problems, such as bridge, occur during the reflow process[5]. QFP solder joints provide both a mechanical support and an electrical connection between the package and PCB. The reliability of solder joints is directly affected by the shape parameter[6, 7], therefore, the design of parameters for the solder joints shape before assembling will be very important for the quality of solder joints[8,9]. In this work, a 240pins, 0.5mm pitch QFP, whose type is XC4028EXHQ240, will be considered. The ultimate goal of the present study was to perform a QPF solder joint reliability analysis under thermal cycling, which consisted of three different steps: 1) finite element analysis modeling of QFP; 2) nonlinear finite element analysis of QFP solder joint to determine the stress/stain distribution within the joint and failure life of QFP solder joint predicting under thermal cycling condition; 3) influence of some shape parameters on the thermal fatigue life of QFP solder joints analysis.
2 FINITE ELEMENT ANALYSIS AND FATIGUE LIFE PREDICTION OF SOLDER JOINT OF QFP UNDER THERMAL CYCLING CONDITION
2.1 Finite element analysis model of QFP
The 240-pin QFP is made of plastic, which is shown in Fig.1. It has gull-wing shaped leads that are spaced on 0.5mm pitch with 0.6mm foot in length. For the QFP solder joints under temperature cycle, a mismatch of the coefficients of thermal expansion(CTE) between the plastic package, solder joints and the FR-4 PCB can induce repeated straining, which will result in fatigue damage accumulation in the solders[10, 11]. In the present study, by means of nonlinear finite element method, the thermal stress/strain analysis of QFP solder joints was performed, and the key solder joint that was subjected to the most thermal stresses/strains could be determined and the maximal plastic strain was calculated. Based on the Coffin-Manson equation and plastic strain calculated, the fatigue life of the QFP solder was also estimated.
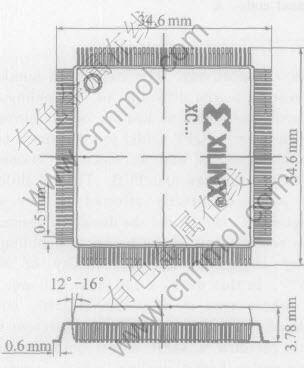
Fig.1 Schematic of 240pin QFP
The two-dimensional finite element method(FEM) analysis model is given in Fig.2, where the size of pad is 1.6mm×0.35mm and the volume of the 63%Sn-37%Pb solder joint is 0.02mm3. The stand-off is 0.0127mm. The finite element model consists of 745 elements with 2490 nodes. The solder joint was modeled as visco-plastic material whereas all other materials were modeled as linear elastic material. Material properties of the QFP package are listed in Table 1. The temperature cycling profile is shown in Fig.3. The imposed dis-placement boundary conditions are: 1) at the bottom of PCB all points cannot move in the x direction and y direction; 2) at the upper end of chip all points cannot move in the x direction.
Table 1 Material properties of QFP package
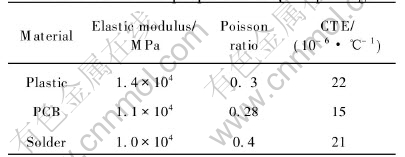
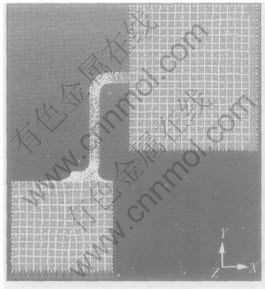
Fig.2 Finite element model of QFP
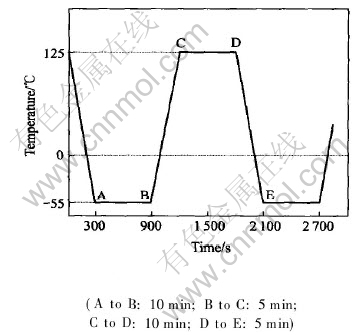
Fig.3 Temperature cycling profile
2.2 Finite element analysis and results
The FEM analysis result of the typical QFP solder joint is shown in Fig.4, which shows the stress distribution within the whole QFP assembly at the third cycle. Fig.5 shows the stress distribution just within the solder joint and Fig.6 shows the strain distribution within the same solder joint at the same cycle. Some stress/strain data on several nodes of the solder joint are given as examples in Tables 2-5.
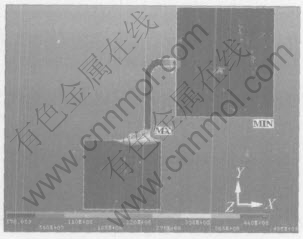
Fig.4 QFP finite element analysis result
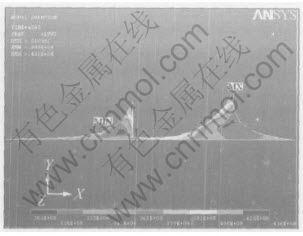
Fig.5 Stress distribution just within QFP solder joint

Fig.6 Strain distribution just within QFP solder joint
Table 2 Stress on nodes of QFP solder joint
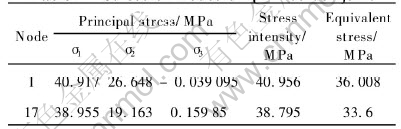
As indicated in Fig.4, the maximum stresses of the whole QFP assembly occur mainly at the interface between the pin foot and the solder joint. And it also can be seen from Figs.5 and 6 that: 1) the stress and strain distribution in the solder joint
Table 3 Maximum stress on nodes of QFP solder joint
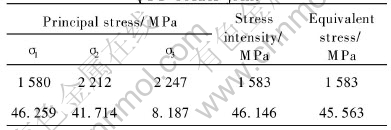
Table 4 Strain on nodes of QFP solder joint
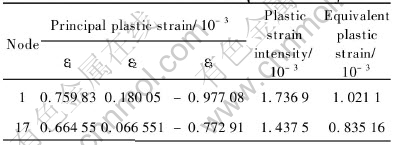
Table 5 Maximum plastic strain on nodes of QFP solder joint
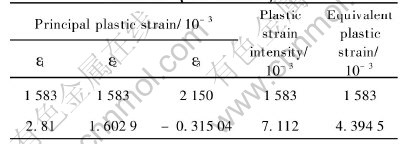
are not uniform; 2) the interface between the pin foot and solder is the high stress/strain region, the maximum stress/stain occurs at the topmost point that the solder joint intersects with the inner side of the lead. The maximum stress/stain are 43.563MPa and 4.3945×10-3 respectively according to Table 3 and Table 5. Thus, the solder joint cracks should occur firstly at the topmost point of the solder joint and propagate along the interface between the solder and the lead and through the whole interface finally, as a result, the solder joint is disabled.
2.3 Thermal fatigue life of QFP solder joint
The thermal fatigue life of the QFP solder joint can be estimated based on the calculated maximum plastic strain and Coffin-Manson equation[12, 13]:
Nf=θ(Δγp)(η)(1)
where Nf is mean cycles to failure, Δγp is maximum plastic strain which can be calculated by FEA, θ and η are material constants. For 63%Sn-37%Pb solder joints, the values of θ and η are 1.2928 and -1.96 respectively[14, 15]. In this case, the maximum plastic strain of 0.0043945 can be obtained from Fig.6, consequently the solder joint of QFP should have the fatigue life of 53880 cycles according to Eqn.1. Following Ref.[13], a safe factor of 4 was used, as the result, it is safely predicted that the solder joint will have the life of 13470 cycles.
3 INFLUENCE OF SHAPE PARAMETERS ON FATIGUE LIFE OF QFP SOLDER JOINT
3.1 Influence of volume of solder joint
The influence of the variation of volume on the distribution of stress within the solder joint is shown in Figs.7 and 8, in which the volumes are 0.024mm3 and 0.032mm3 respectively, but the pad size is fixed at 1.25mm in length and 0.35mm in width, and the stand-off is 0.0127mm.
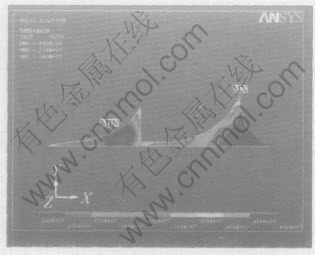
Fig.7 Stress distribution just within QFP solder joint(V=0.024mm3)
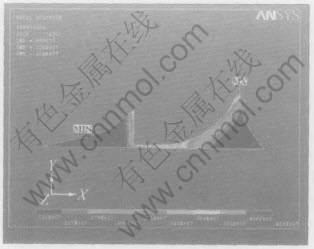
Fig.8 Stress distribution just within QFP solder joint(V=0.032mm3)
Figs.7 and 8 show that: 1) the distribution of stress within the solder joint varies with the volume, and different volumes have different stress distributions within the solder joint; 2) although the stress distribution within the solder joint is influenced by the volume, the high stress/strain region is still fixed at the interface between the pin foot and solder, and the maximum stress/stain also occurs at the topmost point of the solder joint intersected with the inner side of the lead. When other conditions keep constant, the fatigue life of solder joint with different volumes was calculated, shown in Table 6. It can be seen from Table 6 that the fatigue life varies with the solder volume, compared with the others, the longer fatigue life is found in the volume of 0.026mm3.
Table 6 Variation of fatigue life with volume
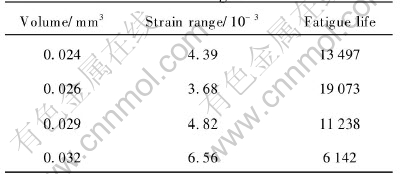
3.2 Influence of pad length
The influence of the variation of pad length on the distribution of stress within the solder joint is shown in Figs.9 and 10, in which the pad length is 1.0mm and 1.6mm respectively, but the pad width, the stand-off and the volume are fixed at 0.35mm, 0.02mm and 0.026mm3, respectively.
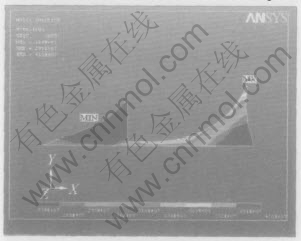
Fig.9 Stress distribution just within QFP solder joint(L=1.0mm)
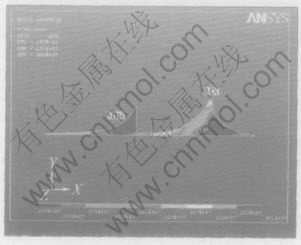
Fig.10 Stress distribution just within QFP solder joint(L=1.6mm)
Figs.9 and 10 show that: 1) the distribution of stress within the solder joint varies with the pad length, and different pad lengths have different stress distributions within the solder joint; 2) although the stress distribution within the solder joint is influenced by the pad length, the high stress/strain region is still fixed at the interface between the pin foot and solder, and the maximum stress/stain also occurs at the topmost point of the solder joint intersected with the inner side of the lead.
When other conditions keep constant, the fatigue life of solder joint with different pad lengths was calculated, shown in Table 7. It can be seen that the fatigue life varies with the pad length, and the pad length of 1.25mm has longer fatigue life than those of the others.
Table 7 Variation of fatigue life with pad length
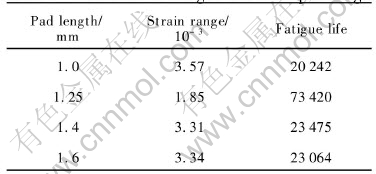
3.3 Influence of stand-off
The stand-off is defined as the height measured from the lowest point on the lead of QFP to PCB. The influence of the variation of stand-off on the distribution of stress within the solder joint is shown in Figs.11 and 12, in which the stand-off is 0.0203mm and 0.0254mm,respectively, but the pad length, the width and the volume are fixed at 1.6mm, 0.35mm and 0.02mm3, respectively.
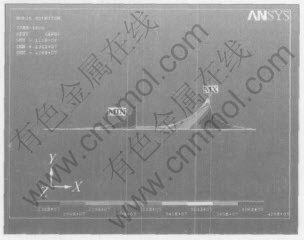
Fig.11 Stress distribution just within QFP solder joint(H=0.0203nm)
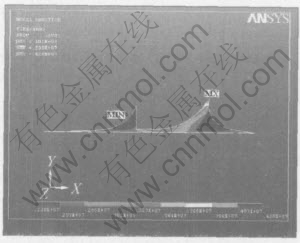
Fig.12 Stress distribution just within QFP solder joint(H=0.0254nm)
Figs.11 and 12 show that the distribution of stress within the solder joint varies with the stand-off, however the high stress/strain region is still fixed at the interface between the pin foot and the solder, and the maximum stress/stain also occurs at the topmost point of the solder joint intersected with the inner side of the lead.
When the other conditions keep constant, the fatigue life of solder joint with different stand-offs was calculated, shown in Table 8. It can be seen that the fatigue life varies with the stand-off; while at the stand-off of 0.0051mm the solder joint has longer fatigue life than in any other cases.
Table 8 Variation of fatigue life with stand-off
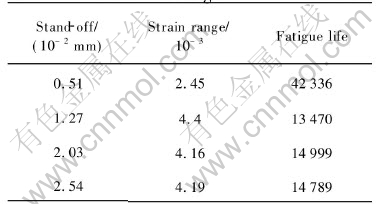
By comparing Tables 6-8, it can be seen that the solder joint with the pad size of 1.25×0.35mm, the stand-off of 0.02mm and the solder volume of 0.026mm3 has the longest fatigue life than any other cases. These optimal parameters have been applied in practice to assemble the 240-pin, 0.5mm pitch QFP, whose type is XC4028EXHQ240.
4 CONCLUSIONS
1) The stress/strain distribution in the solder joint is not uniform, and the interface between the lead and the solder is the high stress/strain region. The maximum stress/stain occurs at the topmost point where the solder joint intersects with the inner side of the lead. The solder joint cracks should occur firstly at this point and propagate along the interface between the solder and the lead and through the whole interface finally.
2) The plastic strain in the solder joint was calculated. Based on the calculated plastic strain and Coffin-Mansons equation, the thermal fatigue life of the 0.5mm pitch, 240-pin QFP solder joint was estimated. In the case of the pad size of 1.6mm×0.35mm, the solder volume of 0.02mm3 and the stand-off of 0.0127mm the fatigue life was estimated to be 13470 cycles.
3) The fatigue life is sensitive to the shape parameters. Although the stress distribution within the solder joint is influenced by the shape parameters, the high stress/strain region is still fixed at the interface between the pin foot and the solder, and the maximum stress/stain also occurs at the topmost point of the solder joint intersected with the inner side of the lead. The solder joint with the pad size of 1.25mm×0.35mm, the stand-off of 0.02mm and the solder volume of 0.026mm3 has the longest fatigue life than other cases. These optimal parameters have been applied in practice to assemble the 240-pin, 0.5mm pitch QFP.
REFERENCES
[1]LEE Ning-cheng. Reflow Soldering Processes and Troubleshooting: SMT, BGA, CSP and Flip Chip Technology [M]. Boston: Newnes, 2001.
[2]Lau J H, Pao Y H. Soler Joint Reliability of BGA, CSP, Flip Chip, and Fine Pitch SMT Assemblies [M]. New York: McGraw-Hill, 2000.
[3]Makoto T, Yasuhiro T, Nobutaka I, et al. Design of 0.35mm pitch QFP lead and its assembly technology [J]. IEEE Transactions on Components Packaging and Manufacturing Technology Part B, 1995, 18(3): 456-461.
[4]Reinard J, Klein W, Martin M F V. Manufacturing Techniques for Surface Mounted Assemblies [M]. Isle of Man: Electrochemical Publications Ltd, 1995.
[5]YANG Jian-sheng. Comparison between ultra-fine pitch QFPs and BGAs and their future [J]. Microelectronic Technology, 2003, 31(2): 61-65.( in Chinese)
[6]ZHOU De-jian, PAN Kai-lin, WU Zhao-hua, et al. Predicting three-dimensional solder joint shapes of SMT based on minimal energy principle [J]. Acta Electronics Sinica, 1999, 29(5): 66-68.( in Chinese)
[7]ZHOU De-jian. Study on SMT Solder Joint Shape Theory and CAD Technology [D]. Hangzhou: Zhejiang University, 1998.
[8]ZHOU De-jian, PAN Kai-lin, LIU Chang-kang. The CAD study on the shpe-evlving and the thermal reliability of PBGA solder joint [J]. Journal of Guilin Institute of Electronic Technology, 1999, 19(1): 69-74.
[9]ZHOU De-jian, PAN Kai-lin, LIU Chang-kang. Solder joint shape evolving and reliability CAD of SMT solder joint [J]. Chinese Journal of Semiconductors, 2000, 21(2): 204-208.(in Chinese)
[10]Wong T E, Kachatorian L A, Tierney B D. Gull-wing solder joint fatigue life sensitivity evaluation [J]. ASME Journal of Electronic Packaging, 1997, 119: 171-176.
[11]Gupta V K, Barker D B. Influence of surface mount lead end geometry on fatigue life [J]. Journal of Electronic Packaging, 1994, 116: 157-160.
[12]Manson S S. Thermal Stress and Low Cycle Fatigue [M]. New York: McGraw-Hill, 1966.
[13]Solomon H D. Fatigue of 60/40 solder [J]. IEEE Transaction on Components, Hybrids, and Manufacturing Technology, 1986, 4(9): 423-432.
[14]John L, Steve E. Reliability of fine pitch plastic quad flat pack leads and solder joints under bending, twisting, and thermal conditions [J]. ASME Journal of Electronic Packaging, 1993, 115: 322-328.
[15]John L, Suresh G, Paul B, et al. Solder joint reliability of a thin small outline package(TSOP) [A]. Proceedings of 42nd Electronic Components and Technology Conference [C]. San Diego: IEEE, 1992. 519-532.
(Edited by LI Xiang-qun)
Foundation item: Project(02336060) supported by the Natural Science Foundation of Guangxi Province, China
Received date: 2005-01-07; Accepted date:2005-03-28
Correspondence: HUANG Chun-yue, PhD Candidate; Tel: +86-773-5601304; E-mail: hcymail@163.com