
Mechanical and dielectric properties of Ni/Al2O3 composites
LUO Fa(罗 发), XUE Hui(薛 晖), ZHU Dong-mei(朱冬梅), ZHOU Wan-cheng(周万城)
State Key Laboratory of Solidification Processing, Northwestern Polytechnical University, Xi’an 710072, China
Received 15 July 2007; accepted 10 September 2007
Abstract: Ni/Al2O3 composites were prepared by hot pressing approach. The relationship between their microstructure, mechanical, dielectric and magnetic properties with Ni particle content was studied. By increasing the amount of metal in the composite, the relative density and the bending strength decrease gradually. The possible reason is that non-wetting between Ni and alumina in the preparation results in weak adhesion of the Ni/Al interface. For the composites, the maximum fracture toughness is 6.4 MPa? m1/2, which is about 25% higher than that of pure alumina ceramic. The increase in toughness of the Ni/Al2O3 composites is due to the deformation of nickel particles. The complex dielectric constant measurements indicate that the real part and the imaginary part increase greatly with the Ni content in the frequency range of 8.2-12.4 GHz. The real part and the imaginary part of complex permeability of the composites also increase with increasing Ni content.
Key words: Al2O3/Ni composites; dielectric property; magnetic property; mechanical property
1 Introduction
The ceramics used as structural materials are often limited by their brittleness nature, much effort has been focused on producing tougher ceramics. The fracture toughness of the matrix materials can be improved by incorporating various energy-dissipating components into the microstructure to create ceramic matrix composites[1-2]. The addition of ductile materials for reinforcing the matrix have been one much studied approach to overcome such a drawback. The ductile materials are potentially very effective in toughening with minimal matrix cracking[3]. The first metallic dispersions used in alumina were chromium particles[4]. Then several other metals such as Ni, Ni-Co, Cr and Mo etc have also been used to tough ceramic matrix. Among the metal/ceramic composites, alumina is the most common matrix material to be studied. The potential of using alumina for engineering applications is high for its availability, high electrical resistance and chemical inertness. Nickel is a prime candidate for the ductile inforcement of alumina. One of the reasons is that the mechanical properties of alumina are indeed improved by adding nickel[5]. It is very resistant to oxidation and has generally excellent high temperature properties as utilized in nimonic series of alloys used widely at elevated temperatures in critical applications[3]. Another interesting point for this composite is that nickel is a ferromagnetic material. Its high Curie temperatures (>1 000℃) is compatible with Ni/Al2O3 hot applications[6-7]. But the data related to dielectric properties of the composites were limited. Therefore, Ni powders were selected to tougher alumina ceramic in the present paper. The mechanical, dielectric and magnetic properties of Ni/Al2O3 composites prepared by hot- pressing route were investigated.
2 Experimental
The Ni powder of 20 mm and a-Al2O3 powder of 5 mm were used as starting materials. The compositions of the blends are shown in Table 1. The mixtures of the two powders were put into a graphite die and sintered at 1 550 ℃ for 30 min under a pressure of 20 MPa in N2 atmosphere. The hot-pressed billets were cut into specimens with dimensions of 3 mm×5 mm×40 mm for three-point bending strength tests. The cross-head speed was 0.5 mm/min.
The bulk density the sintered samples were measured by the Archimedes displacement method.
The microstructures were conducted on OLYMPUS PM-G3. The phase identification of the samples was performed by conventional X-ray diffraction (XRD).
The permittivity and permeability of the specimens in 8.2-12.4 GHz were measured by wave guard method in E8362B PNA series network analyzer.
3 Results and discussion
3.1 Microstructures
The Ni/Al2O3 composites were sintered at 1 550 ℃ for 30 min under a pressure of 22 MPa. Figs.1 and 2 show the microphotographs of Ni/Al2O3 composites with 10%(volume fraction) and 20% Ni. It can be found from the Fig.1 that the Ni particles are inhomogeneously distributed in the Al2O3 matrixes and the Ni particles are obviously elongated in the perpendicularity direction of the pressure due to Ni particles’ plastic deform under the sintering pressure at the high temperature.
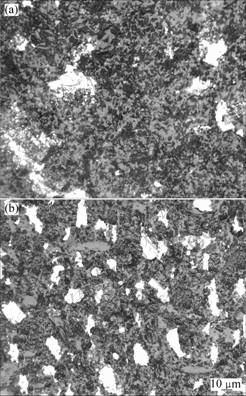
Fig.1 Microphotographs of Ni/Al2O3 composites with 10% Ni(a) and 20% Ni(b)
3.2 Strength and toughness
Fig.2 shows that the strength of the Ni/Al2O3 reduces with increasing Ni content. The strength of the monolithic alumina is 364 MPa. The strength of the Ni/Al2O3 composites decreases from 342 MPa to 245 MPa when the Ni content increases from 10% to 30%. On the other hand, the fracture toughness of the Ni/Al2O3 composites rises apparently with increasing Ni content. The fracture toughness of the Ni/Al2O3 ceramic among all the samples is the lowest. It is only 5.1 MPa×m1/2. The increase in fracture toughness of the Ni/Al2O3 composites from 5.3 to 6.4 MPa×m1/2 is considerable with the Ni content rise in the composites.
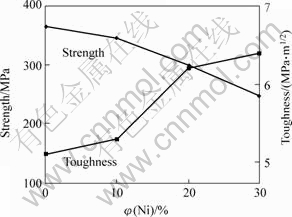
Fig.2 Variation of strength and toughness of Ni/Al2O3 composites with Ni content
3.3 Dielectric properties
The Ni/Al2O3 composites were sintered in highest grade N2 atmosphere. Ni-Al2O3 is non-reaction system in no oxygen condition. In such a case, non-wetting between Ni and alumina was observed. Therefore adhesion of the Ni/alumina interface is weak[8]. The contact area between Ni and alumina extends with the increase of the Ni content. It implies that the weak adhesion in the composites intensifies. On the other hand, the strong bond between Ni and Al can be obtained when intimate contact between the two materials is effective depending on plastic deformation of Nickel that varies with the applied pressure[9]. The fact that the relative density of the Ni/Al2O3 composites reduces with the increase of Ni content reflects that the applied pressure is not enough. The intimate contact does not yield. The two reasons above results in the strength fall of the Ni/Al2O3 composites.
Figs.3 and 4 show the dielectric and magnetic properties of the composites. It can be seen from Fig.3 that the real and imaginary parts of permittivity of the Ni/Al2O3 composites increase greatly with Ni content. The real and imaginary parts of permittivity of the pure Al2O3 ceramic are very close to reported data and keep almost constant in the tested frequency range. The real part of the Ni/Al2O3 composites presents an obvious rise from 30 to 54 when Ni content increases from 10% to 20% at 9.375 GHz. The imaginary part of the Ni/Al2O3 composites also exhibits an increase from 22 to 54 while Ni content increases from 10% to 20% at 9.375 GHz. A slight drop of the real parts of the Ni/Al2O3 composites is seen while the imaginary part shows a different variation pattern in the frequency range.
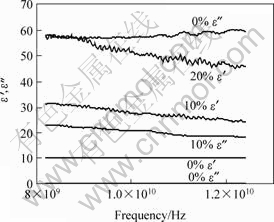
Fig.3 Real and imaginary parts of permeability of Ni/Al2O3 composites vs. Ni content
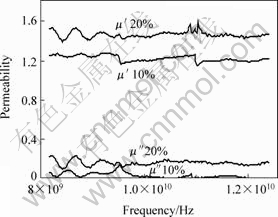
Fig.4 Real and imaginary parts of permeability of Ni/Al2O3 composites vs. Ni content
Fig.4 shows the variation of real and imaginary parts of permeability of the Ni/Al2O3 composites depending on Ni content. The real and imaginary parts of permeability increase with increasing Ni content.
There are many mixture rules to calculate the permittivity and permeability of mixtures. For example, Maxwell Garnett mixture equation could be used to predict the permittivity and permeability of mixtures for solid spherical particles. In the usual composites composed of particles and binder, the particles are isolated from one another by the binder materials. For the composites consisting of Ni particles and alumina particles, alumina particles surface was already contaminated with Ni during mixing by long time dry milling. On the other hand, when the volume fraction of Ni particles becomes large, the magnetic attraction between Ni particles forces them agglomeration where local semicontinuous geometry forms. These reasons make it difficult to predict the permittivity and permeability of the composites.
The conductivity of the composites increases when more Ni powder is incorporated into the composites. Due to the big difference in conductivity of Ni particles and Al2O3 particles, it is believed that a large number of space charges remain in their grain boundaries. The responses of the space charges to foreign electromagnetic field increase the dielectric constant. The imaginary part (ε″) of permittivity is given by the following equation as:
ε? = δdc/(ωεo)+ε?ac
where δdc is dc conductivity, ω is the angular frequency, εo is the permittivity of free space and ε?ac is the loss contribution at high frequency. Therefore, addition of Ni particles also enhances the imaginary part of the composites.
The rise of real part μ?of permeability of the composites with increase of the Ni powder accords to the mixture formula of magnetic composite in low content. The rise of imaginary part μ? of permeability of the composites results from the hysteresis loss and eddy current loss of the added Ni particles.
Because both the dielectric and magnetic loss contribute the loss tanδ of the Ni/Al2O3 composites to electromagnetic wave, compared with sole is given as following formula due to the addition of magnetic Ni particles:
Tan δ = tan(δe) +tan(δm)=ε?/ε?+μ?/μ?
where tan(δe), tan(δm) are dielectric and magnetic loss, respectively. Therefore, high dissipation to electromagnetic wave is expected, especially at high temperatures because of high Curie temperature of Ni.
4 Conclusions
1) The strength of the hot-pressed Ni/Al2O3 composites reduces with increase of Ni content.
2) The fracture toughness of the Ni/Al2O3 composites rises apparently with the Ni content increases due to the deformation of nickel particles.
3) The increase of conductivity from addition of Ni particles leads to the rise of real and imaginary parts of the permittivity of the composites. The big μ?, hysteresis loss and eddy current loss of the incorporated Ni particles make the composites’ μ? and μ? high.
References
[1] JI Y, YEOMANS J A. Microstructure and mechanical properties of chromium and chromium/nickel particulate reinforced alumina ceramics[J]. Journal of Materials Science, 2002, 37(24): 5229–5236.
[2] VEKINIS G, SOFIANOPOULOS E, TOMLINSON W J. Alumina toughened with short nickel fibers[J]. Acta Materialia, 1997, 45(11): 4651-4661.
[3] GUICHARD J L, TILLEMENT O, MOCELLIN A. Alumina- chromium cermets by hot-pressing of nanocomposite powders[J]. Journal of the European Ceramic Society, 1998,18(12): 1743-1752.
[4] WANG T C, CHEN R Z, TUAN W H. Oxidation resistance of Ni-toughened Al2O3[J]. Journal of the European Ceramic Society, 2003, 23(6): 927–934.
[5] SEKINO T, NAKAJIMA T, NIIHARA K. Mechanical and magnetic properties of nickel dispersed alumina-based nanocomposite[J]. Materials Letters, 1996,29(1/3): 165-169.
[6] VENDANGE V, TRONC E, COLOMBAN P H. Towards microwave absorbing metal-oxide nanocomposites: The problem of metal/matrix reaction [J]. Journal of Sol-Gel Science and Technology, 1998, 11(3): 299–307.
[7] WAN C, KRITSALIS P, DREVIT B, ENSTATHOULOS N. Optimization of wettability and adhesion in reactive nickel-based alloys/alumina systems by a thermodynamic approach[J]. Mater Sci Eng A, 1996, 207(2): 181-187.
[8] LOURDIN P, JUVK D, TRKHEUX D. Nickel-alumina bonds: Mechanical properties related to interfacial chemistry[J]. Journal of the European Ceramic Society, 1996,16(7): 745-752.
(Edited by YANG Hua)
Foundation item: Projects(50572090) supported by the National Natural Science Foundation of China
Corresponding author: LUO Fa; Tel: +86-29-88494574; E-mail: gslfa@126.com