
Ploughing-extrusion mechanism of V-shaped capillary micro-grooves based on surface of copper strip
CHI Yong(池 勇), TANG Yong(汤 勇), CHEN Jin-chang(陈锦昌),
DENG Xue-xiong(邓学雄), LIU Lin(刘 林), LIU Xiao-kang(刘小康), LIU Xiao-qing(刘晓晴)
College of Mechanical Engineering, South China University of Technology, Guangzhou 510640, China
Received 20 April 2006; accepted 30 June 2006
Abstract: Using ploughing-extrusion process, the V-shaped capillary micro-grooves based on the surface of copper strip with thickness of 0.4 mm were obtained. When the ploughing depth is 0.3 mm and the groove interval is 0.24 mm, the groove width of the obtained structure is about 200 μm, the groove depth is above 400 μm, and the angle of grooves is less than 30?. The formation mechanism of ploughing-extrusion was analyzed using scanning electron microscope (SEM). The results show that the formation process consists of four steps, i.e. splitting-ploughing, extruding, forming and truing. There exist two critical states during the formation process. In the first state, a smooth U-shaped groove appears between two V-shaped grooves, and the compounded structure which comprised of V-shaped grooves and U-shaped grooves is obtained. In the second state, the U-shaped groove is evolved into a narrow crack, and the resulted V-shaped capillary macro-groove structure contains symmetric V-shaped grooves and narrow cracks. These two critical states are restricted by the groove interval (w) and the ploughing depth (ap), and related on the tool parameters simultaneously.
Key words: V-shaped groove; capillary structure; ploughing-extrusion
1 Introduction
Capillary structure is widely applied in chemistry industry and the cooling of micro electronic chip. It provides the power for the phase-change heat-transfer [1-6], and acts as the catalyst carrier to enhance the reaction efficiency[7-12]. There are four kinds of capillary structures, i.e. sintered, silk screen, grooved and foamed.
In this paper, based on ploughing-extrusion technology, the V-shaped capillary micro-grooves are manufactured in the thin copper strip. Some researchers studied the similar structure. XIA et al[13] researched the chopping-extrusion process and divided the formation process into three stages i.e. chopping, extrusion and forming. But this method is based on the thick copper tube aiming to obtain fins not grooves. TANG et al[14] studies the mechanism of pre-roll ploughing on stainless steel and divides this process into three stages, i.e. extrusion-bulging, splitting and fin formation. He analyzed the process and conditions of 3D fin formation. The experiments show that the groove internal and ploughing depth have great effect on the fin height. WARRINGTON et al[15] studied the chipless form tapping process and it is similar to ploughing-extrusion. He established the FEM model for tapping forming and investigated the effects of various tap design parameters and tapping process conditions on the formation of split crests. This process requires the tooth should be 60? and the ratio of depth to width of the groove is small. AZARKHIN et al[16, 17] studies the enhanced model of a plowing asperity by the upper bound method.
Using ploughing-extrusion process, the V-shaped capillary micro-grooves based on the surface of copper strip with thickness of 0.4 mm were obtained. When the ploughing depth is 0.3 mm and the groove interval is 0.24 mm, the groove width of the obtained structure is about 200 μm, the groove depth is above 400 μm, and the groove angle is less than 30?. The ploughing-extrusion mechanism was analyzed by SEM. In the first state a smooth U-shaped groove appears in between two V-shaped grooves, and the compounded structure which comprised of V-shaped grooves and U-shaped grooves are obtained. In the second state, the U-shaped groove is evolved into a narrow crack, and the resulted V-shaped capillary macro-groove structure contains symmetric V-shaped grooves and narrow cracks. These two critical states are restricted by the groove interval (w) and the ploughing depth (ap), and related on the tool parameters simultaneously.
2 Experimental
The experiment was carried out on the planer B6050B. The red copper strip, which was made of T2, was 0.4 mm in depth and is used as the workpiece; the tool was made of W18Cr4V. The schematic diagram of ploughing- extrusion process of V-shaped capillary micro grooves is shown in Fig.1. The workpiece is fixed on the working platform, and the tool ploughs the copper strip along the negative direction of Y, leaving a V-shaped groove behind. Once the tool ploughs the strip a stroke, the work feeds along the negative direction of X axis, then the next ploughing-extrusion process begins. Meanwhile the formed V-shaped micro grooves are modified and the fin gets heightened. In order to avoid the strip bulging due to the ductibility on its X direction, one end of the strip is fixed and the other end can extend and shrink freely along the X axis.
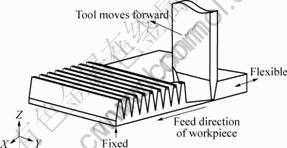
Fig.1 Schematic diagram of ploughing-extrusion process of V-shaped capillary micro grooves
Fig.2 shows the ploughing-extrusion tool grinded by HSS lathe tool (2 mm×10 mm×200 mm). It comprises of a ploughing edge, a main extruding face Aγ, a subsidiary extruding face Aγ′, a main forming face Aβ, a subsidiary forming face Aβ′ and a tool flank Aα. The O-O cross-section of the tool is a wedge, whose front-end is the ploughing edge. It ploughs the metal and makes the metal flow along the main extrusion face and the subsidiary one. The main extruding face Aγ generally extrudes and ploughs the split metal and makes metal flows along the main forming face Aγ. Then the grooves are formed under the function of the main forming face Aγ. The subsidiary extrusion face Aγ′ trims the fins and makes them higher. Owing to the trimming and extruding affect from the adjacent formed groove on the subsidiary forming face, when the next micro-groove is being formed, the ratio of depth to width of the adjacent formed groove is further increased. So the main forming angle β should be bigger than subsidiary forming angle β′ to ensure the symmetry of V-shaped groove.
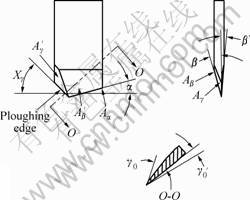
Fig.2 Ploughing-extrusion tool
Since the tool is thin, the component force of tool along the X axis during the ploughing-extrusion process should be small enough to prevent the tool from deforming and creating zigzag interfering on micro-grooves. The component force of X axis mainly divided with the extruding force and the friction force between the workpiece and main/subsidiary extruding face. The extruding force and the friction force from each extruding faces are equal in quantity and are reverse in direction. Then, the relation of the main/subsidiary extruding angle can be obtained as follows:
(1)
where γ0 is the main extruding angle, γ0′ is the subsidiary extruding angle, β is the main forming angle and β′ is the subsidiary forming angle.
3 Results and discussion
3.1 Formation of single V-shaped groove
The ploughing-extrusion process of single V-shaped micro groove comprises of three stages, i.e. splitting-ploughing, extruding and forming.
In the splitting-ploughing stage, the metal is splitted by ploughing edge and flows bilaterally towards the extruding faces.
In the extruding stage, due to the affects from the main/subsidiary extruding faces, the metal at the bottom of V-shaped groove flows upwards and forms bulges. Fig.3 shows the end face of groove when the tool is departing from the workpiece. As shown in Fig.3, the tool moves from inside to outwards and continuous metal streamline can be seen clearly. The metal contacting the extruding face of the tool is extruded and deforms. plastically, so the metal at the bottom of the V-shaped groove flows upwards along the extruding face and forms the continuous streamline. Due to the extrusion between the tool’s extruding face and the un-deformed metal, the metal at the foot and the middle of the groove flows bilaterally and reaches the groove fringe. As the upper face of copper strip is a free surface, the flowing metal accumulates around the fringe and forms bulges where the streamlines are sparse. Fig.4 shows the cross-section of a V-shaped groove, and the bulges are distinct on the two fringes.
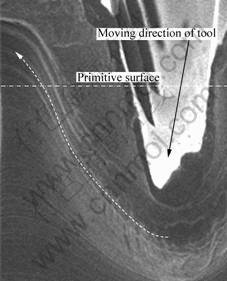
Fig.3 Metal streamlines around V-shaped groove
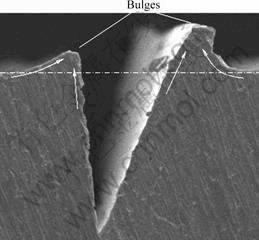
Fig.4 Bulges on fringe of V-shaped groove
In the forming stage, owing to the friction of the extruding/forming face on the groove wall, when the tool moving, the deformed metal is detained at the forming face and moves following the tool. Fig.5 shows the metal streamlines on the two sides of V-shaped groove behind the tool leaving. Under the friction of the tool to the groove, the metal near the fringe of V-shaped groove is the weakest, where the deformation is the largest and the slipping is pretty bigger. More far away from the groove foot and fringe, under the restriction from the un-deformed metal, the deformation is littler. When the tool is departing from the workpiece, due to the friction of the tool on the groove wall, the metal detained on the tool surface goes on plastic deforming till the tool departing away from the V-shaped groove, the end face bulge of groove is shown in Fig.3.
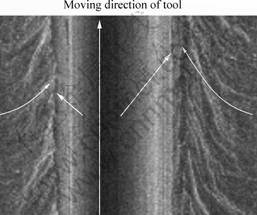
Fig.5 Metal streamlines beside V-shaped groove
3.2 Forming interaction of V-shaped micro-grooves
Based on the above analysis and the theory of metal plastic deformation, the existence of a plastic deforming area is deduced around the V-shaped groove. Only the metal in the deformation area deforms plastically, and there is no plastic deformation appears in the metal outside the plastic deformation area.
When the ploughing depth is small, the deforming area is small, and so is the deformed bulges (shown in Fig.6(a)). With the increase of ploughing- extrusion depth, the deforming area is enlarged, and so is the deformed bulges (shown in Fig.6(b)). Fig.7 shows the SEM image of the formed V-shaped groove when the ploughing depth is 0.1 mm and the groove interval is 0.24 mm. The formed fin (bulge) on the groove fringe is about 40 μm in height. When the ploughing-extrusion depth increases to 0.2 mm, the height of the formed fin is about 100 μm, as shown in Fig.8.
When the groove interval is bigger, the deformation areas don’t affect each other, the structure of the groove and the formation mechanism is the same as that of single micro-groove. In forming process, there is no affect on the last adjacent groove, and the subsidiary extruding face Aγ′ and the subsidiary forming face Aγ′ don’t trim the formed groove. The bulge between the two fringes changes into a low and shallow U-shaped groove (Fig.6(c)), which accords with the SEM image in Fig.7. The forming of new bulge doesn’t affect the adjacent grooves; the bottom of U-shaped groove is a flat and
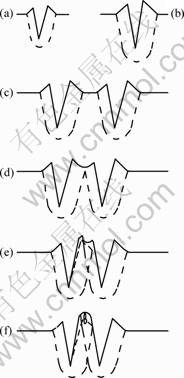
Fig.6 Schematic diagrams of deforming of V-shaped grooves: (a) Single micro-groove; (b) Single deeper micro-groove; (c) Double individual micro-groove; (d) Formation of V-shaped groove; (e) Distorted V-shaped groove and narrower V-shaped groove; (f) Symmetry V-shaped groove and narrow crack
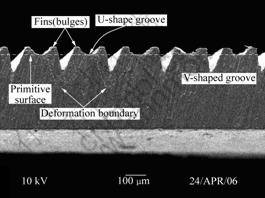
Fig.7 Cross-section SEM image of multi V-shaped groove (Ploughing depth 0.1 mm, groove interval 0.24 mm)
matches together the primitive surface of copper stripe.
When the groove interval is reduced or the ploughing depth increases, the deformation areas contact each other, the newly formed groove interferes on the last adjacent formed groove. The metal between the grooves begins to yield under the extrusion force from the subsidiary extruding face Aγ′ and the trimming from subsidiary forming face Aβ′, and bends along the normal of Aβ′. Because the main forming angle β is bigger than the subsidiary one β′, the inclination angle of groove wall
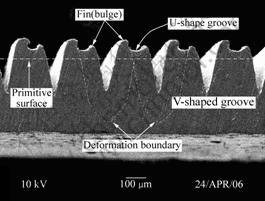
Fig.8 Cross-section SEM image of multi V-shaped groove (Ploughing depth 0.2 mm, groove interval 0.24 mm)
formed by main forming face Aβ is bigger than that formed by subsidiary forming face Aβ′. Due to bending, the inward bend of the inclination angle of the last groove wall formed by main forming face Aβ lessened (in Fig.6(e)). Meanwhile, the U-shaped groove is narrowed under the trimming of the subsidiary forming face Aβ′, the bugle grows higher, and the V-shaped groove becomes deeper and narrower. So the ratio of depth to width of V-shaped groove is increased, which favors the capillarity. The SEM image in Fig.8 shows that under the extrusion from subsidiary extruding face Aβ′ and subsidiary forming face Aγ′, the metal on the bottom of V-shaped groove flows to the groove fringe and makes the bottom of U-shaped groove is higher than the primitive copper stripe, leads to fin (bulge) higher than that in the single groove. At the same time, subsidiary forming face pushes the redundant metal between the grooves to the formed adjacent groove, so the last formed groove is narrowed and becomes symmetric.
When the groove interval is reduced or the ploughing depth increases further, trimming action from the subsidiary extruding face Aβ′ and the subsidiary forming face Aγ′ is greater. The redundant metal between the grooves bends more towards the normal of Aβ′. Due to the extrusion from the two bulges, the U-shaped groove is narrower and nearly forms a crack (in Fig.6(f)). The redundant metal between the grooves becomes long and thin, and then forms the vimineous fins. On the top end of the vimineous fins there are narrow cracks. V-shaped capillary micro groove becomes deeper and narrower, the ratio of depth to width is even larger. Fig.9 shows the even V-shaped micro capillary grooves, whose interval is 200 μm and depth is above 400 μm on the condition that the ploughing depth is 0.3 mm and the groove interval is 0.24 mm.
When the groove interval is narrower or the depth of ploughing-extrusion is deepen further, the subsidiary extruding face Aγ′ and the subsidiary forming face Aγ′ will extrude the last adjacent groove. The angle of V-groove is diminished more, which leads to distort the groove. Simultaneously, the ploughing edge split the last formed bulge, so the volume of the new bulge increases more and more. Finally the chip is appeared, and the groove depth increases no longer. On the contrary, it begins to decrease. So in this state, the V-shaped capillary micro groove isn’t formed steadily due to the chip is generated in the ploughing-extrusion process.
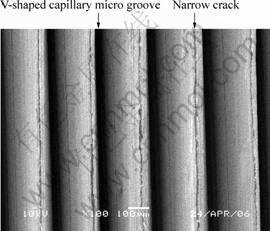
Fig.9 SEM image of V-shaped capillary micro groove (Ploughing depth 0.3 mm, groove interval 0.24 mm)
So the conclusion that there are two critical states in the forming process of V-shaped capillary micro groove is gained. The first critical state is that a U-shaped groove is formed well-timed, and the second critical state is that the U-shaped groove is vanished and evolves a narrow crack. In case the parameters of the tool are fixed, the two critical states is influenced by the spacing interval of grooves, w, and the depth of ploughing-extrusion, ap. But also, the two parameters, w and ap, are restricted each other. If defining wU is the critical value of w and apU is the critical value of ap on the first critical state. wC is the other critical value of w and apC is the other critical value of ap on the second critical state.
For individual distorted V-shaped groove(Figs.6(a), (b), (c))

For distorted V-shaped groove and U-shaped groove(Fig.6(d), (e)):

For symmetry V-shaped groove and narrow crack(Fig.6(f)):

For more distorted V-shaped groove (the chip is appeared)

To different parameters of the tool, the critical values of the spacing interval of grooves and the depth of ploughing-extrusion, wU, wC, apU, apC, will change accordingly. The relation of each critical value and the relation of the critical values and the tool parameters need to investigate by experiments and finite element analysis.
4 Conclusions
Using ploughing-extrusion process, V-shaped capillary micro-grooves based on the surface of copper strip whose thickness is 0.4 mm is obtained. When the ploughing depth is 0.3 mm and the groove interval is 0.24 mm, the groove width of the obtained structure is about 200 μm, and the groove depth is above 400 μm, the groove angle is less than 30?.
The formation mechanism of ploughing-extrusion was analyzed by SEM. The formation process consists of four steps, i.e. splitting-ploughing, extruding, forming and truing.
There exist two critical states during the formation process. In the first state, a smooth U-shaped groove appears in between two V-shaped grooves, and the compounded structure which comprised of V-shaped grooves and U-shaped grooves is obtained. In the second state, the U-shaped groove is evolved into a narrow crack, and the resulted V-shaped capillary macro-groove structure contains symmetric V-shaped grooves and narrow cracks. These two critical states are restricted by the groove interval (w) and the ploughing depth (ap), and related on the tool parameters simultaneously.
References
[1] HAIDER S I, YOGENDRA K J, NAKAYAMA W. A natural circulation model of the closed loop, two-phase thermosyphon for electronics cooling[J]. J Heat Trans-T ASME, 2002, 124(5): 881-890.
[2] PASTUKHOV V G, MAIDANIK Y F, VERSHININ C V, Korukov M A. Miniature loop heat pipes for electronics cooling[J]. Appl Therm Eng, 2003, 23(9): 1125-1135.
[3] CHERNYSHEVA M A, VERSHININ S V, MAIDANIK Y F. Development and tests of miniature loop heat pipe with a flat evaporator[A]. 12th IHPC[C]. Oxford: Pergamonelsevier Science LTD, 2002.
[4] BUGBY D C, KROLICZEK E J, YUN J S. Development and testing of a miniaturized multi-evaporator hybrid loop heat pipe[J]. AIP Conf Proc, 2005, 746: 69-81.
[5] WAJMAN T, WIECEK B, OSTROWSKI B, DANYCH R. Capillary pump for cooling of electronic devices-steady states summary[J]. Kwartalnik Elektroniki i Telekomunikacji, 2005, 51(2): 319-334.(in Polish)
[6] CHEN P C, LIN W K. The application of capillary pumped loop for cooling of electronic components[J]. Appl Therm Eng, 2001, 21(17): 1739-1754.
[7] HOLLADAY J D, WANG Y, JONES E. Review of eevelopments in portable hydrogen production using microreactor technology[J]. Chem Rev, 2004, 104(10): 4767-4789.
[8] HOLLADAY J D, JONES E O, PHELPS M, HU Jian-li. Microfuel processor for use in a miniature power supply[J]. J Power Sources, 2002, 108(1-2): 21-27.
[9] HOLLADAY J D, JONES E O, DAGLE R A, XIA G G, CAO C, WANG Y. High efficiency and low carbon monoxide micro-scale methanol processors[J]. J Power Sources, 2004, 131(1-2): 69-72.
[10] PAN L W, WANG S D. Methanol steam reforming in a compact plate-fin reformer for fuel-cell systems[J]. Int J Hydrogen Energ, 2005, 30(9): 973-979.
[11] TERAZAKI T, NOMURA M, TAKEYAMA K, NAKAMURA O, YAMAMOTO T. Development of multi-layered microreactor with methanol reformer for small PEMFC[J]. J Power Sources, 2005, 145(2): 691-696.
[12] GANLEY J C, SEEBAUER E G, MASEL R I. Development of a microreactor for the production of hydrogen from ammonia[J]. J Power Sources, 2004, 137(1): 53-61.
[13] XIA W, WU B, TANG Y, YE B Y. On chopping–extrusion of integral-fin copper tubes[J]. J Mater Process Tech, 2003, 138(1-3): 385-389.
[14] TANG Y, LIU S D, XIA W, ZENG Z X, YE B Y. The establishment and analysis of fin formation model during ploughing process[J]. J Mater Process Tech, 2003, 138(1-3): 390-393.
[15] WARRINGTON C, KAPOOR S, DEVOR R. Finite Element modeling for tap design improvement in form tapping[J]. J Manuf Sci Eng T ASME, 2006, 128(1): 65-73.
[16] AZARKHIN A, DEVENPECK M L. Enhanced model of a plowing asperity[J]. Wear, 1997, 206(1-2): 147-155.
[17] AZARKHIN A., RICHMOND O, DEVENPECK M. An approximate model of surface ploughing by a rotating disc and other indenters[J]. Wear, 1996, 192(1-2): 157-164.
(Edited by ZHAO Jun)
Foundation item: Projects (50436010, 50375055, 50175028) supported by the National Natural Science Foundation of China; Project (04105942) supported by the Natural Science Foundation of Guangdong Province, China
Correspondence: TANG Yong; Tel: +86-20-87114634; E-mail: ytang@scut.edu.cn