DOI:10.19476/j.ysxb.1004.0609.2018.09.14
从废旧LiFePO4电池极片中原子经济回收Li、Fe和集流体-Al箔
王 轩1, 2,王先友1, 2,张 蕊1, 2,张媛媛1, 2
(1. 湘潭大学 化学学院 电化学能源储存与转换湖南省重点实验室,湘潭 411105
2. 湘潭大学 化学学院 新能源装备及储能材料与器件国家国际科技合作基地,湘潭 411105)
摘 要:根据废旧LiFePO4正极片中各元素物理化学性质差异,通过高温焙烧、酸浸并选择不同沉淀剂分离等手段,回收废旧LiFePO4电池极片中Li、Fe元素和集流体-Al箔。Li首先以Li3PO4的形式回收,Fe以FePO4形式回收。结果表明:废旧LiFePO4电池极片经过600 ℃高温煅烧后,当溶解混合物的HCl浓度为5 mol/L时,在60 ℃加热搅拌4 h,混合粉料的溶解率达到了98%,未溶解的是残留的少量导电碳和PVDF。向滤液中加入3% SDS,调节滤液pH值至2,在80 ℃得到无定形FePO4可作为新制备LiFePO4的前驱体。继续向滤液中加入Na3PO4至饱和,可以最大程度地回收锂元素,Li以梭形形貌的Li3PO4形式沉淀。Fe的回收率为97%,Li的回收率可以达到96%。
关键词:废旧LiFePO4电池;元素回收;原子经济;磷酸锂;磷酸铁
文章编号:1004-0609(2018)-09-1824-08 中图分类号:TM912 文献标志码:A
随着全球经济的快速发展,能源短缺和生态环境恶化日益突出,新能源的发展受到越来越多的重视。锂离子电池(LIB)由于其高的工作电压,高的能量密度,自放电小,循环寿命长,使用方便,无记忆效应等优点被广泛应用于便携式电子设备、通讯机站备用电源、电动汽车和大规模电网储能等领域,具有广阔的发展前景[1-3]。
近年来,全球3C锂电池市场日趋成熟,动力锂电池市场已经成为全球锂电池市场的最大引擎。从长远发展看,未来十年,全球动力锂电池市场将继续迅猛增长,预计至2022年,总需求量和市场规模将分别达到54.9 GW·h和267亿美元,未来10年年均复合增长率分别为37.0%和31.6%,市场规模占比将迅速提升至63%左右[4-6]。混合电动汽车和纯电动汽车的迅速扩张是动力锂电池快速增长主要原因[7-8]。2016年,全年新能源汽车总计销量为51.7万辆,锂电池市场规模约为1115亿元,动力锂电池需求605亿元,同比增长65.8%。预计到2020年全球电动汽车将达到800万辆,2030年更是将达到9500万辆[9]。在选择电动汽车动力电池时,能量密度,功率密度,循环寿命,安全性和成本是考虑的首要因素[10]。LiFePO4电池因具有安全、环保、稳定性好、比容量高、价格便宜等优点,被认为是动力电池和储能电池中重要的一类电池体系[11]。2016年新能源汽车搭载电池总量达28 GW·h,与2015年相比增长79%,其中LiFePO4电池占比高达73%,搭载量高达20 GW·h。
随着动力电池市场需求不断攀升,受限于动力电池的使用寿命,未来报废的动力电池数量也将会极为庞大。据专业机构预计,到2020年我国动力电池市场需求将达125 GW·h,报废量将达32.2 GW·h,约50万t;到2030年,动力电池报废量将达101 GW·h,约116万t,可以预见未来LiFePO4动力电池的报废量将会是巨大的[12]。如果这些废旧LiFePO4正极片被废弃而没有回收利用,不仅浪费了宝贵的资源,而且会造成环境污染。尤其是随着新能源汽车对锂电池的需求越来越大,导致各种锂盐的价格迅速上涨,并且越来越多LiFePO4电池生产厂家使用FePO4作为合成LiFePO4的前驱体,也一定程度导致了电池级FePO4价格的提高。因此,回收LiFePO4电池正极废片中Li、Fe及集流体-Al箔的意义是非常巨大,不仅仅可以解决LiFePO4电池报废后的资源回收问题,消除环境污染,而且回收得到的产物还可以产生一定的经济效益。同时,通过回收得到的锂盐、铁盐可以作为重新合成LiFePO4的原料,进一步降低生产成本,实现原子经济。
目前国内外废旧锂电池回收研究,大部分是关于LiCoO2及三元体系等使用的锂离子电池,因为其Co、Ni等价格昂贵,而LiFePO4电池回收的报道则较少[13-15]。大部分报道只是由于锂资源短缺、价格上涨,而简单的回收Li2CO3,并没有对Fe元素进行回收,更谈不上对回收的FePO4的晶形及形貌进行论述。此外,考虑到溶液中PO43-的存在,要完全优先将纯的Li2CO3沉淀下来并不是很容易,由于Ksp(Li3PO4)<<Ksp(Li2CO3),Li2CO3溶解度为13.3 g/L,Li3PO4溶解度为0.3821 g/L。Li2CO3相对于FePO4在水溶液中的溶解度还是较大的,所以回收得到的Li2CO3最后还是会有少量的溶解在水溶液中。鉴于此,本文作者采用湿法冶金原理将LiFePO4正极废片中的Fe2+以无定形的FePO4形式回收,通过高温煅烧得到六方晶系FePO4,回收得到的FePO4可以作为重新合成LiFePO4的前驱体[16-17]。Li以Li3PO4的形式回收,可以确保最大程度的回收废旧LiFePO4正极片中的Li元素,同时Li3PO4也可作为制备Li2CO3或LiOH的锂源[18]。而且,Li3PO4具有高的离子电导率,回收得到的Li3PO4还可以作为固体电解质使用或用于锂离子电池三元正极材料的表面修饰[19]。
1 实验
1.1 实验过程
废旧LiFePO4极片回收的工艺流程如图1所示。将回收得到的20 g废旧LiFePO4片整理好后浸入一定浓度NaOH溶液中,机械搅拌0.5 h。待LiFePO4等完全从Al箔上脱离后,Al箔通过清洗后可直接回收。将碱液中LiFePO4混合材料过滤分离,在80 ℃干燥12 h,球磨过筛得到LiFePO4混合粉体。
LiFePO4混合粉体在空气气氛下煅烧6 h,取10 g煅烧后的混合材料在一定浓度的HCl溶液中加热溶解。对得到的溶液进行过滤,除掉微量的滤渣。取出100 mL滤液,加入6 mol/L NH3·H2O调节pH=4,过滤干燥,标记为LF-UD。取2g滤饼重新分散在500 mL 6 mol/L H3PO4溶液中,调节溶液pH至2和3,80 ℃加热搅拌5 h后过滤、洗涤可得到FePO4。将pH=3的样品标记为LF-3,pH=2的样品标记为LF-2。另取2 g滤饼重新分散在500 mL去离子水中,加入3%的SDS(十二烷基硫酸钠),调节溶液pH=2,80 ℃加热搅拌5 h后过滤、洗涤可得到电池级FePO4,标记为LF-SDS。
向上述处理得到的滤液中,加入6 mol/L NH3·H2O,调节pH至中性,在滤液中加入一定量的Na3PO4,搅拌,溶液中逐步出现白色沉淀,直至白色沉淀不再出现后,过滤、洗涤,得到Li3PO4沉淀。
1.2 材料与仪器
废旧LiFePO4正极材料为LiFePO4正极材料厂产生的废料,以及电池厂切片过程中产生的LiFePO4边角余料,采用的化学药品均为分析纯试剂。
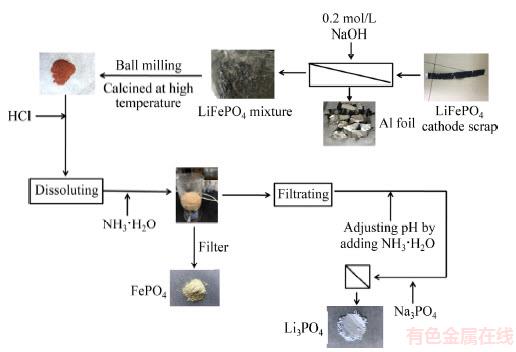
图1 回收LiFePO4正极废片工艺流程图
Fig. 1 Recycling process diagram of spent LiFePO4 scraps
采用日本Rigaku公司生产的D/Max-3C型的X射线自动衍射仪进行物相分析,以Cu Kα1为射线源,扫描范围为10°~80°,扫描速率为4 (°)/min,管电压为40 kV,管电流为40 mA。用S-4800型扫描电子显微镜(SEM)在20 kV下进行表面形貌分析。用美国TA公司生产的SDTQ600型热分析仪对样品进行TG-DTG测试,用N2作保护气体,温度范围为25~500 ℃,升温速率为5 ℃/min。采用梅特勒-托利多仪精密酸度计(FE20)测量溶液pH值。用日本岛津生产的原子吸收分光光度计(AA7000)测量溶液中Li+、Fe3+和Al3+含量。用德国元素分析系统公司的元素分析仪(Vario EL III)测量煅烧后样品的C的含量。
2 结果与讨论
2.1 预处理及煅烧条件的优化
LiFePO4正极片的组成中,Al的质量分数约为15.99%[7]。集流体Al箔为两性金属,使用较低浓度的NaOH溶液腐蚀铝箔边缘,同时进行搅拌,正极材料随着搅拌的进行而逐渐从铝箔上脱落,从而达到物理分离铝箔的目的。NaOH溶液浓度对正极片和Al箔分离效果的影响如表1所示。由表1可见,随着NaOH溶液浓度的增大,溶液中Al3+的浓度也越来越大。当NaOH的浓度为0.2 mol/L,正极材料与Al箔能完全分离,并未见Al箔有明显腐蚀;继续增加NaOH溶液浓度至0.3 mol/L时,溶液中Al3+的浓度达到了0.12 mo/L,表明一部分Al箔被溶解了。因此,为了确保LiFePO4材料的完全分离和Al箔尽量少的溶解,NaOH溶液浓度为0.2 mol/L较合适。
表1 NaOH溶液浓度对正极片和Al箔分离效果的影响
Table 1 Effect of NaOH concentration on separation of cathode material from Al foil
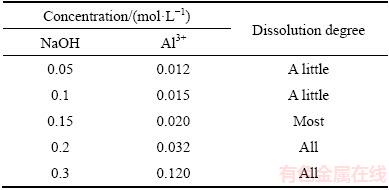
分离后的LiFePO4混合材料在空气气氛下进一步煅烧,基于反应方程式(1)可以看出,空气气氛下煅烧既可以使Fe2+氧化为Fe3+,避免后续酸浸过程中氧化剂的加入,还可以通过煅烧除去LiFePO4混合材料中残留的导电碳和PVDF,且被氧化后的红棕色疏松混合物在HCl溶液中的更易溶解。为了保证导电碳和PVDF尽可能通过煅烧除去,同时又尽可能减少煅烧过程中Li的损失,试验选择500、600和700℃温度阶段进行煅烧,结果见表2所示。从表2可以看出,随着煅烧温度的升高,煅烧后混合物中C和Li的含量都在下降,实验中选择600 ℃为煅烧温度既可以确保大部分的PVDF及导电碳被除去,还可以尽量降低Li元素在高温煅烧中的损失。
12LiFePO4+3O2→4Li3Fe(PO4)3+2Fe2O3 (1)
表2 煅烧温度对C和Li含量的影响
Table 2 Effect of calcination temperature on C and Li content
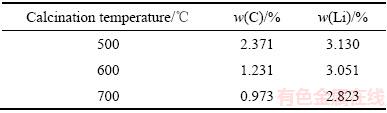
2.2 浸出工艺条件的优化
LiFePO4混合材料被完全氧化后可以更加容易溶解在HCl中。图2所示为HCl溶液浓度、温度、液固比等工艺条件对氧化物溶解的影响。从图2(a)中见,HCl浓度为5 mol/L时,4 h内混合物溶解程度为98%,其中未溶解的物质应该是煅烧后导电碳或者PVDF的残留物,并且继续提高HCl浓度对材料的溶解没有明显影响。从图2(b)中可以看出,适当提高温度可以加速混合物的溶解,当HCl浓度为5 mol/L、温度为60 ℃时,氧化物的溶解达到极大值。从图2(c)中可见,当HCl的浓度为5 mol/L、温度为60 ℃时,当液固比大于12.5后,溶解量不再随时间而变化,因此选择液固比12.5比较合适。
2.3 Fe元素的浸出和沉淀
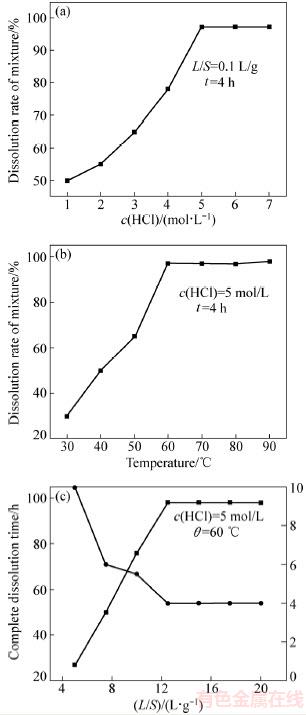
图2 不同条件对混合物溶解程度和完全溶解所需时间的影响
Fig. 2 Effects of different conditions on dissolution rate of mixture and complete dissolution time
浸出后的溶液中包含有Fe3+、Li+、PO43-、SO42-、H+,溶液中HPO42-和H2PO4-浓度极低,对Fe3+的沉淀过程没有影响。由于FePO4只有在强酸溶液中才能溶解,根据这一性质,加入NH3·H2O调节溶液pH值,使溶液中的Fe3+和PO43+发生沉淀反应,从而回收废旧磷酸铁锂正极材料中的Fe元素,反应方程如式(2)所示:
Fe3++PO43-→FePO4↓ (2)
图3(a)所示为调节不同pH值时溶液中剩余Fe3+和Li+的含量。从图3(a)中可以看出,约80%的Fe3+在pH=2.0时沉淀了下来,当pH=4.0时,溶液中的Fe3+已经沉淀完全,可以看出Fe的沉淀率为97%;而且从图3(a)可以看出,在此过程中溶液中的Li+含量几乎没有变化,表示Li+没有沉淀。图3(b)所示为浸出时间与滤液中Fe3+含量的关系图。从图3(b)中可以看出,在pH值为4的时候,Fe3+在25 min内就可以沉淀完全。在Fe3+的沉淀过程中,pH值对Fe3+的沉淀起决定性作用。当pH值低于2时,将导致生成的FePO4沉淀在强酸性溶液中再次溶解,而pH值大于2时可保证浸出液中的Fe3+大部分沉淀。
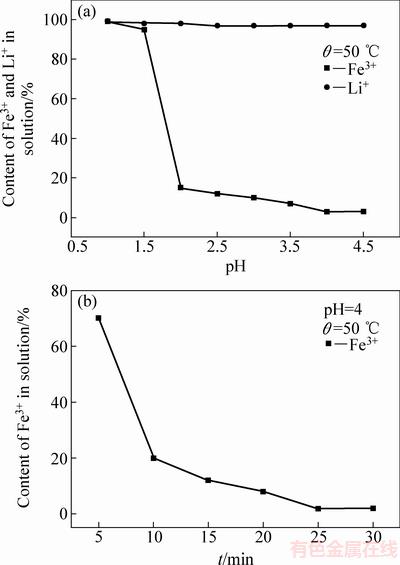
图3 pH值和浸出时间对滤液中离子含量的影响
Fig. 3 Effects of pH and leaching time on content of ions in solution
CAI等[20]提出溶液pH值在2.5以下的时候,沉淀大部分是FePO4(Ksp=9.91×10-16),但随着pH的进一步升高,沉淀中Fe(OH)3(Ksp=4×10-26)的含量将会增大。根据沉淀溶解平衡原理,随着pH值的增大,溶液中c(OH-)变大,使生成的FePO4向Fe(OH)3转化。因此为了使Fe3+尽可能多的沉淀,且大部分以FePO4的形式沉淀,所以选择先调节溶液的pH=4,接着将过滤得到的滤饼重新分散在去离子水中,再加入H3PO4重新调节溶液的pH值,80 ℃的温度下搅拌5 h,得到纯FePO4。由于生成的FePO4不溶解在H3PO4中,且H3PO4可以将沉淀中少量的Fe(OH)3重新转变为FePO4,反应方程如式(3)所示:
Fe(OH)3+H3PO4→FePO4+H2O (3)
图4(a)所示为得到的FePO4的XRD谱,从图4(a)中可以看出,在2θ=25°左右出现一个宽的馒头峰,且峰形较宽,未见其他衍射峰,说明回收得到的首先是无定形的FePO4·xH2O。随着目前一些含锂负极(如含锂合金负极材料)的开发与应用,一些无锂正极材料正逐渐成为研究热点,最近的研究表明,无定形FePO4也具有成为优秀正极材料的潜力[21],并且目前FePO4已经成为工业上生产LiFePO4最为经济有效的前驱体。图4(b)所示为FePO4·xH2O的TG-DTG图,从DTG曲线在140 ℃处可以看到有一个明显的吸热峰,这是由于脱去结晶水所造成的。从TG曲线中可以看出,从初始温度30 ℃到300 ℃之间,存在一个明显的质量损失,在这段温度区间内质量损失率约为25.2%,经计算可以判断得到的FePO4应为FePO4·3H2O。图4(c)所示为LF-3、LF-2和LF-SDS在600 ℃煅烧5 h后得到的FePO4 XRD谱,可见在600 ℃煅烧可以确保产物失去结晶水,磷酸铁在高温煅烧下发生的晶形转变,3个样品与FePO4的标准卡片PDF#77-0094的特征峰均完全吻合,且衍射峰的强度较高,峰形尖锐。比较标准卡片可见,600 ℃煅烧后的3个样品均属于六方晶系,且晶体充分发育,结晶完整。
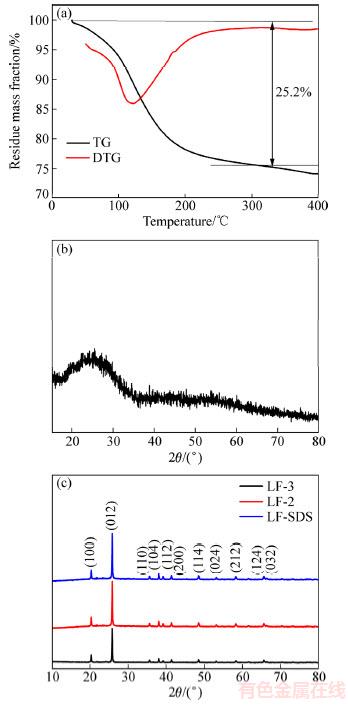
图4 FePO4·xH2O的TG-DTG曲线和XRD谱以及LF-3、LF-2和LF-SDS的XRD谱
Fig. 4 TG-DTG curves (a) and XRD patterns (b) of FePO4·xH2O and XRD patterns of LF-3, LF-2 and LF-SDS (c)
图5所示为不同条件下回收得到的FePO4的扫面电镜图。图5(a)所示为没有经过再次调节pH值回收得到的FePO4,可以看出图中颗粒大且团聚现象明显,可以推断出在pH=4条件下回收得到的不是纯的FePO4,可能存在少量的Fe(OH)3[20]。由图5(b)可以看出,经过再次调节pH=3,颗粒结晶度明显提高,形貌逐渐规则,但还是存在粒径大小不一和少量团聚现象。图5(c)则是调节pH=2,此时样品中存在的少量的Fe(OH)3应该是完全转变为FePO4,粒径较样品LF-3明显减小,但图中可以看出颗粒团聚更加明显。图5(d)所示为加入3% SDS后的扫描电镜照片,发现加入表面活性剂SDS后,粒径分布比较均匀、规则。可以认为,在回收废旧FePO4的过程中加入少量的表面活性剂,有利于得到粒径分布均匀的FePO4。因为SDS(阴离子表面活性剂)对固液界面产生吸附作用,形成一层很薄的界面膜,可起到一定的空间位阻作用,使FePO4微粒相互隔离;同时可降低微粒的表面能,减少粒子间的吸附作用。因此,在回收废旧FePO4的过程中加入少量的表面活性剂,可以减少或避免微粒发生团聚,有利于得到粒径分布均匀的FePO4。
2.4 Li元素的浸出和沉淀
在Fe3+沉淀的过程中,Li+并没有与其他离子结合沉淀,因此分离出FePO4后的溶液中主要包含Li+、SO42-、H+、NH4+,其中NH4+、SO42-对Li+的沉淀是没有影响的。由于Li3PO4(Ksp=2.37×10-14)在溶液中的溶解度是非常小,因此可以向浸出液中加入可溶的磷酸盐,使PO43-与Li+结合形成Li3PO4沉淀,从而达到回收废旧磷酸铁锂正极材料中Li元素的目的,反应方程如式(4)所示。
Na3PO4+3Li+→Li3PO4↓+3Na+ (4)
由于Li3PO4能溶解在弱酸性溶液中,而分离出FePO4后的滤液仍然为酸性。在工作过程中为了防止Li3PO4的溶解并提高Li的回收率,先向浸出液中加入NH3·H2O,调节滤液的pH值至接近中性,然后再加入Na3PO4使Li以Li3PO4的形式沉淀。从图6(a)中可以看出,Li的沉淀量随Na3PO4加入量的增加而增加,当Na3PO4的加入量在接近饱和,即120 g/L时,Li的沉淀率可以达到96%。图6(b)所示为Na3PO4加入量为120 g/mL时,溶液中Li+含量与pH值的关系,由于Li3PO4是会溶于稀酸的,从图6(b)中可以看出当pH=4的时候,还是有接近20%的Li+没有沉淀。当pH调节至5.5时,溶液中Li几乎可以完全沉淀,因此调节pH=5.5,可确保Li充分沉淀。
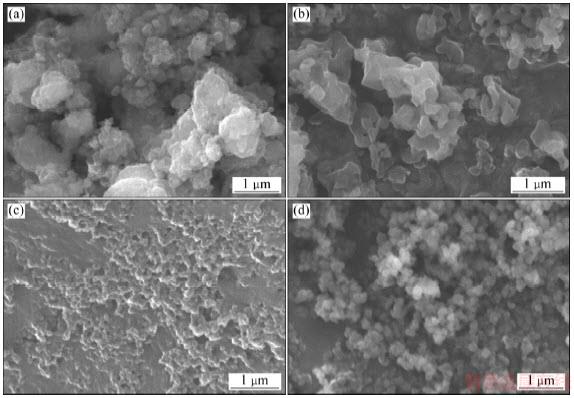
图5 回收得到的LF-UN、LF-3、LF-2和LF-SDS的SEM像
Fig. 5 SEM images of LF-UN (a), LF-3 (b), LF-2 (c) and LF-SDS (d) samples
图7(a)所示为回收得到的Li3PO4的XRD谱,各个衍射峰形状规则且尖锐,说明获得的Li3PO4结晶度高,并且图中未见杂质衍射峰,证明回收得到了纯相的Li3PO4。图7(b)和(c)所示为Li3PO4在不同放大倍数下SEM像,可以看出,Li3PO4颗粒有轻微的团聚现象,Li3PO4粒子呈梭形,粒径分布比较均一。
3 结论
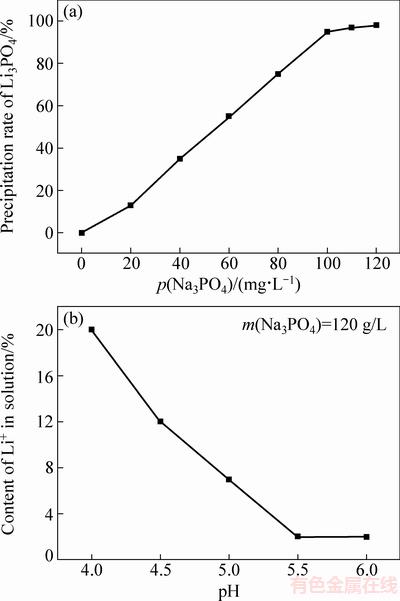
图6 Li沉淀率与Na3PO4加入量的关系以及pH值对溶液中Li+含量的影响
Fig. 6 Precipitation rate of lithium with amount of Na3PO4 (a) and effect of pH on content of Li+ in solution (b)
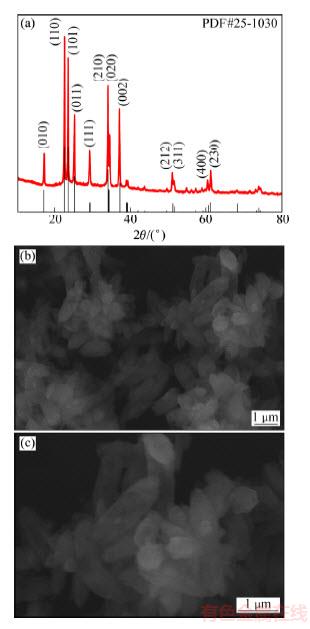
图7 Li3PO4的XRD谱以及Li3PO4的SEM像
Fig. 7 XRD patterns of Li3PO4 (a) and SEM images of Li3PO4 ((b), (c))
1) 通过高温焙烧→酸浸→调节pH值→加不同沉淀剂回收废旧LiFePO4电池极片中Li、Fe和集流体-Al箔的方法为废旧LiFePO4电池中有价金属的回收提供了一条原子经济的新途径。
2) 采用高温煅烧和HCl浸出,高温煅烧可以减少后续过程中氧化剂的加入且可以除去LiFePO4正极片中的导电碳材料和粘结剂PVDF。HCl浸出方法简单,回收率较高,当HCl的浓度为5 mol/L时,液固比为12.5,在60 ℃加热搅拌4 h后,混合材料的溶解率达到了98%。
3) 通过调节浸出液pH=2及加入3% SDS可以首先得到无定形结构的FePO4,600℃高温煅烧后可以转变为具有六方晶系的电池级FePO4,Fe的回收率为97%。进一步向滤液中加入饱和Na3PO4可以沉淀出Li3PO4,Li3PO4呈梭形形貌,Li的回收率可以达到96%。
REFERENCES
[1] ZHENG Ru-juan, ZHAO Li, WANG Wen-hui, LIU Yuan-long, MA Quan-xin, MU De-ying, LIA Ru-hong, DAI Chang-song. Optimized Li and Fe recovery from spent lithium ion batteries via a solution-precipitation method[J]. RSC Advances, 2016, 6(49): 43613-43625.
[2] CHAGNES A, POSPIECH B. A brief review on hydrometallurgical technologies for recycling spent lithium-ion batteries[J]. Journal of Chemical Technology and Biotechnology, 2013, 88: 1191-1199.
[3] CHEN Jiang-ping, Li Qing-wen, SONG Ji-shun, SONG Da-wei, ZHANG Lian-qi, SHI Xian-xing. Environmentally friendly recycling and effective repairing of cathode powders from spent LiFePO4 batteries[J]. Green Chem, 2016, 18: 2500-2506.
[4] ZENG Xian-lai, LI Jin-hui, NARENDRA N. Recycling of spent lithium-ion battery: A critical review[J]. Critical Reviews in Environmental Science and Technology, 2013, 44(10): 1129-1165.
[5] CAI Guo-qiang, FUNG K Y, NG K M. Process Development for the Recycle of Spent Lithium-Ion Batteries by Chemical Precipitation[J]. Ind Eng Chem Res, 2014, 53(7): 18245-18259.
[6] DUNN J B, GAINES L, KELLY J C, JAMES C, GALLAGHER K G. The significance of li-ion batteries in electric vehicle life-cycle energy and emissions and recycling’s role in its reduction[J]. Energ Environ Sci, 2015, 8(1): 158-168.
[7] 吴 越, 裴 锋, 贾簬路, 田 旭. 从废旧LiFePO4电池中回收铝、铁和锂[J]. 电源技术, 2014, 38(4): 629-631.
WU Yue, PEI Feng, JIA Lu-lu, TIAN Xu. Recovering aluminum iron and lithium from waste LiFePO4 bacillary[J]. Power Technology, 2014, 38(4): 629-631.
[8] XU Jin-qiu, THOMAS H R, FRANCIS R W, LUM K R, WANG Jin-wei, LIANG Bo. A review of processes and technologies for the recycling of lithium-ion secondary batteries[J]. Journal of Power Sources, 2008, 177(2): 512-527.
[9] 潘小勇, 彭 玲, 陈伟华, 韦泽平, 卢 萧, 陈 正, 王 婕. 废旧锂离子电池中钴和锂的回收及综合利用[J]. 中国有色金属学报, 2013, 23(7): 2047-2054.
PAN Xiao-yong, PENG Ling, CHEN Wei-hua, WEI Ze-ping, LU Xiao, CHEN Zheng, WANG Jie. Recovery and comprehensive utilization of cobalt and lithium in waste lithium ion batteries[J]. The Chinese Journal of Noneferrous Metals, 2013, 23(7): 2047-2054.
[10] PARK O K, CHO Y H, LEE S H, YOO H C, SONG H K, CHO J. Who will drive electric vehicles, olivine or spinel[J]. Energ Environ Sci, 2011, 4: 1621-1633.
[11] LEI Xing-ling, ZHANG Hai-yan, CHEN Yi-ming, WANG Wen-guang, YE Yi-peng, ZHENG Chu-chun, DENG Peng, SHI Zhi-chong. A three-dimensional LiFePO4/carbon nanotubes/ graphene composite as a cathode material for lithium-ion batteries with superior high-rate performance[J]. J Alloy Compd, 2015, 626: 280-286.
[12] PALACIN M R, GUIBERT A. Why do batteries fail?[J]. Science, 2016, 351: 1253292.
[13] 郭丽萍, 黄志良, 方 伟, 杜小弟, 雷 家. 化学沉淀法回收LiCoO2中的Co和Li[J]. 电池, 2005, 35(4): 266-267.
[14] NIE He-he, XU Long, SONG Da-wei, SONG Ji-sun, SHI Xi-xi, WANG Xiao-qin, ZHANG Lian-qi, YUAN Zhi-hao. LiCoO2: Recycling from spent batteries and regeneration with solid state synthesis[J]. Green Chem, 2015, 17: 1276-1280.
[15] SONG Da-wei, WANG Xiao-qi, NIE He-he, SHI Hua, WANG Dong-ge, GUO Fen-xia, SHI Xi-xi, ZHANG Lian-qi. Heat treatment of LiCoO2 recovered from cathode scraps with solvent method[J]. J Power Sources, 2014, 249: 137-141.
[16] KIM H S, SHIN E J. Re-synthesis and electrochemical characteristics of LiFePO4 cathode materials recycled from scrap electrodes[J]. Bulletin of the Korean Chemical Society, 2013, 34(3): 851.
[17] BIAN Dou-chen, SUN Yong-hui, LI Sheng, TIAN Yuan, YANG Ze-heng, FAN Xiao-ming, ZHANG Wei-xin. A novel process to recycle spent LiFePO4 for synthesizing LiFePO4/C hierarchical microflowers[J]. Electrochimica Acta, 2016, 190: 134-140.
[18] LIANG Hong-yu, ZHANG Lian-hong. Nanoscaled LiFePO4 synthesized solvothermally by wettish precursor[J]. Russian Journal of Electrochemistry, 2014, 50(2): 198-200.
[19] AYU I P, KARTINI E, PRAYOGI L D, FAISAL M, SUPARDI. Crystal structure analysis of Li3PO4 powder prepared by wet chemical reaction and solid-state reaction by using X-ray diffraction (XRD)[J]. Ionics, 2016, 22(7): 1051-1057.
[20] CAI Guo-qiang, FUNG K Y, NG K M. Process development for the recycle of spent lithium ion batteries by chemical precipitation[J]. Ind Eng Chem Res, 2014, 53(47): 18245-18259.
[21] GANDRUD K B, NILSEN O, FJELLVAG H. Ultra-high power capabilities in amorphous FePO4 thin films[J]. J Power Sources, 2016, 306: 454-458.
Atomic-economic recovery of aluminum, iron and lithium from spent LiFePO4 battery
WANG Xuan1, 2, WANG Xian-you1, 2, ZHANG Rui1, 2, ZHANG Yuan-yuan1, 2
(1. Hunan Province Key Laboratory of Electrochemical Energy Storage and Conversion, School of Chemistry, Xiangtan University, Xiangtan 411105, China;
2. National Base for International Science and Technology Cooperation, School of Chemistry, Xiangtan University, Xiangtan 411105, China)
Abstract: According to the differences of the physical and chemical properties for each element in the spent LiFePO4 battery, Li, Fe and current collector-Al foil were atomic-economically recovered by high temperature sintering, acid leaching and adding different precipitating reagents. Lithium was first recovered in the form of Li3PO4, and iron was recovered in the form of FePO4. The results show that when the concentration of HCl is 5 mol/L, the dissolution rate of the mixed material reaches 98% when being heated at 60 ℃ for 4 h. The pH of the filtrate is adjusted to 2 after adding SDS to recover FePO4. Followed by adding of Na3PO4, when the concentration of Na3PO4 is close to saturation, lithium precipitates in the form of Li3PO4. The precipitation rate of iron can reach 97%, the precipitation rate of lithium can reach 96%.
Key words: spent LiFePO4 battery; element recycling; atomic economy; Li3PO4; FePO4
Foundation item: Project(51472211) supported by the National Natural Science Foundation of China
Received date: 2017-08-24; Accepted date: 2018-01-02
Corresponding author: WANG Xian-you; Tel: +86-731-58293377; E-mail: wxianyou@yahoo.com
(编辑 李艳红)
基金项目:国家自然科学基金资助项目(51472211)
收稿日期:2017-08-24;修订日期:2018-01-02
通信作者:王先友,教授,博士;电话:0731-58293377;E-mail:wxianyou@yahoo.com