铜电解过程在线多尺度能效分析
高东波1,彭小奇1, 2,宋彦坡1,王晓娜1
(1. 中南大学 能源科学与工程学院,湖南 长沙,410083;
2. 湖南第一师范学院 信息科学与工程学院,湖南 长沙,410205)
摘要:为了对铜电解过程的能效进行精确分析,运用支持向量机、软测量等方法构造一种在线多尺度能效分析方法并开发相应的软件系统。研究结果表明:该方法较好地解决了阴极铜产量实时预测、作业阶段在线识别等技术问题,实现了电解过程能效分析的在线化与自动化;多种时间尺度下的能效分析结果更加清晰,能系统地描述过程的能效状况,为相关操作与决策人员提供了从宏观到细节的更多层面的辅助信息;能效计算结果精度高,系统级能效计算误差低于2%。
关键词:铜电解;能效分析;综合能耗;节能;多尺度分析
中图分类号:TK01 文献标志码:A
文章编号:1672-7207(2021)06-1934-10
On-line multi-scale analysis of energy efficiency in copper electrolysis process
GAO Dongbo1, PENG Xiaoqi1, 2, SONG Yanpo1, WANG Xiaona1
(1. School of Energy Science and Engineering, Central South University, Changsha 410083, China;
2. School of Information Science and Engineering, Hunan First Normal University, Changsha 410205, China)
Abstract: In order to precisely analyse the energy efficiency in the copper electrolysis process, a multi-scale analysis method was proposed and the corresponding software system was developed by combining the support vector machine and the soft-measuring technique. The results show that with the method proposed in this paper, the technical difficulties including the real-time prediction of cathode copper output and the online identification of operation stage are solved, and the online energy efficiency analysis is realized. At the meantime, by making the analysis at the multiple time scales, the energy efficiency of the electrolysis process can be described more clearly and systematically, and thus auxiliary information covering macro to micro levels can be provided for the process operation and decision-makings. The energy efficiency calculated by the method is accurate, and the error of the indexes at the system level is less than 2%.
Key words: copper electrolysis; energy efficiency analysis; comprehensive energy consumption; energy saving; multi-scale analysis
节能是工业领域从业人员长期以来不懈追求的重要目标,而要实现这一目标,必须对工业系统能源利用水平进行科学分析。根据热力学原理,现有的能效分析方法可以分为基于热力学第一定理的热分析方法和基于热力学第二定理的火用分析方法两大类。基于热力学第一定理的热分析方法应用广泛[1-2],我国有关能效计算的国家标准[3-4]中规定的方法也多属此类。WOOD等[5]运用这类方法对比分析了几种典型炼铜工艺的单位产品能耗,WANG等[6]分析了我国国内钢铁行业的能源消耗与水资源消耗之间的平衡与协同关系。热分析方法能够定量地描述能量在系统中的传递与转化,但无法反映能源或能量的“品质”变化,而基于热力学第二定理的火用分析方法[7-8]在一定程度上克服了这一不足。火用分析方法能够从“数量”和“品质”2个方面描述系统的耗能特征,在能效分析方面比热分析方法更具优势,该分析方法已广泛应用于蒸馏[9]、地热发电[10]、太阳能发电[11]、氧化铝生产[12]、布雷顿循环发电[13]、牛奶处理[14]、合金熔炼处理[15]等工业过程。为了充分发挥各类方法的优势,很多研究者将这2类方法以及其他分析方法结合使用。彭小奇等[1]综合运用热分析、火用分析这2种方法分析了氧化铝生产蒸发过程的能耗特征,据此提出了优化建议;ANDERSEN等[16]运用热分析方法、最终用途模型和过程步骤模型等,对钢铁行业的物料流和能量流进行了分析;LIU等[17]开发了一个分层的SDA模型,以分析导致钢铁厂能耗变化的关键因素;CHEN等[18]运用生命周期方法对原生铜、再生铜的生产过程能耗结构与影响因素进行了分析;YU等[19]基于能量、物料平衡原理以及协同理论构建了电弧炉中铁矿球团融化过程的物质流与能量流协同模型,据此评估和优化过程用能效率。这些研究工作促进了工业领域的节能优化,然而,目前针对工业过程尤其是复杂冶金过程的能效分析与评估几乎都是离线进行,这些离线分析的结果往往与生产实际结果严重不符,无法对工业过程的控制与决策提供指导信息。就本文的研究对象即铜电解过程而言,考虑到该过程在整个铜冶炼流程中的能耗很大,多数企业定期对能效进行分析与评估,然而,这需消耗大量时间和人力,因此,多数企业对其进行离线能效分析的时间间隔为1~3月[20],这必会遗漏电解过程能耗的诸多“细节”特征(如能耗在不同作业阶段的时间分布特征等),分析结果不仅滞后而且可信度不高。离线分析结果只能从宏观上为企业的管理人员、技术人员提供有关用能优化的指导信息,无法为现场的具体操作提供及时、有效指导。为此,本文作者提出一种在线多尺度能效分析方法,以期及时、全面反馈铜电解过程的能效。
1 问题分析
冶炼企业当前普遍使用的铜电解过程能效分析方法存在如下2个共性问题。
1) 能耗分析所使用的时间过长,分析结果仅能反映1个作业周期(约200 h)甚至更长时间的整体能耗,无法反映能耗小时间尺度的时间分布特征。
2) 能耗分析大多是离线进行,耗时费力,而且结果往往严重滞后,难以为现场操控提供及时、有效信息。
问题1)主要是能耗分析所需要的关键参数即阴极铜产量获得频率过低所致。从反应机理看,尽管电解是连续式生产,产品(阴极铜)持续产出并沉积在阴极板上,但从作业制度看,该过程又是一个间歇式生产过程,“装入极板、开始电解”与“取出极板、终止电解”反复交替,每经过1个作业周期会有一批产品(阴极板)从电解槽取出。相应地,只有经历1个作业周期,现场才能产生1个阴极铜产量。显然,解决问题1)的关键在于获取更小时间尺度(如1.0 h或0.5 h)内的阴极铜产量。在现有工艺及检测技术条件下,阴极铜产量不可能通过直接测量获得。尽管如此,多数电解工艺已实现对电流、电解液温度等多个过程变量的实时监测,探索这些变量与阴极铜产量之间的关系,理论上可望构建出测量阴极铜产量的模型。
问题2)的产生与铜电解过程的作业制度及现有检测水平有关,体现在:① 现场对阴极铜产量的测量是离线的、滞后的;② 铜电解过程的作业周期不固定,使得电耗、蒸汽消耗等参数与实际作业周期之间的对应关系复杂,往往需要人工记录各个作业周期的起止时间并据此确认各个作业周期内的能耗。对于问题①,理论上可以通过前述阴极铜产量软测量模型解决。解决问题②的一个思路是,分析铜电解过程中关键监测变量的变化规律,据此建立基于过程监测的作业周期在线自动识别模型。
2 方法与模型
2.1 基于支持向量机的阴极铜产量软测量模型
在铜电解过程中,阴极铜的实时生成速率可表示为
(1)
式中:
为阴极铜的产生速率,t/h;
为铜的电化当量,1.185×10-6 t/(A·h);
为电解槽的电流效率;
为电流,A。相应地,在统计期t1~t2中,阴极铜的产量可表示为
(2)
式中:
和
分别为统计期中电流效率与电流的时均值。
式(1)和(2)中的
在生产现场已实现在线测量,
的诸多影响因素如电解液进/出口温度、净液入槽流量、电流、极间电压等也大多实现在线测量,而且现场工人也会在每个阴极周期之后计算该周期的平均电流效率。每经历1个阴极周期,可从现场获取如下1组数据:
(3)
式中:下标i为标识阴极周期的编号;Tin和To分别为电解液的进、出口温度,℃;qL为净液的入槽流量,m3/h;
为槽电压,V;等号右侧括号内变量均是相应变量在该阴极周期内的时均值。
理论上,现场积累的这些数据中蕴含有电流效率与其影响因素之间的“关系”信息,因此,本文提出运用不敏感支持向量机(ε-SVM)从数据中探索这种“关系”,从而建立电流效率的软测量模型。模型基本结构如图1所示。
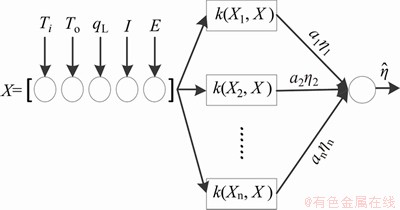
图1 基于支持向量机的电流效率软测量模型
Fig.1 Soft-measuring model of electricity efficiency based on support vector machine
支持向量机的输入变量均采用下式进行自标准化处理:
(4)
式中:xi为模型的任一输入变量的原始值;
为xi自标准化处理后的结果;
为训练数据中各阴极周期变量x的算术平均值;
为训练数据中各阴极周期变量x的标准偏差。
图1所示模型也可描述为
(5)
式中:
为核函数,本文选用高斯核函数,即
;
为经训练确定的模型参数,
只对部分训练样本成立(这部分样本被称为支持向量)。
本文提出的铜电解电流效率软测量模型的具体建模过程如下。
Step 1 将可用数据划分为训练集
和检验集
,记为:
(6)
(7)
式中:N和M分别为训练集和检验集内的数据总数。
Step 2 对训练集SL和检验集ST中的输入变量根据式(4)进行标准化处理,式中的
和
均是基于训练数据SL的统计变量。标准化处理后的训练集和检验集分别记为:
(8)
(9)
Step 3 基于标准化处理后的训练集
,运用文献[21]中方法确定ε-SVM模型的3个元参数(即高斯核函数参数p、不敏感参数ε和正则化参数C)并训练ε-SVM模型。
Step 4 利用标准化处理后的检验集
对模型进行检验。
经检验合格的ε-SVM模型可用于估算任一统计期t1~t2内的平均电流效率,并进而估算相应阴极铜产量,具体方法如下:1) 根据式(4)对输入变量(统计期内的
,
,
,
和
)进行标准化处理(
和
仍是基于训练数据
的统计结果);2) 根据式(2)计算统计期内的阴极铜产量m。
2.2 基于极间电压监测的电解过程作业阶段的在线识别模型
本文所研究的具体铜电解系统的1个实际作业周期包括第一阴极周期(记为P1)、第一出铜期(记为S1)、第二阴极周期(记为P2)和第二出铜期(记为S2)共4个阶段。在不同作业阶段,极间电压存在显著区别,如图2所示。从图2可见:极间电压在阴极周期(P1和P2)为4.5~7.5 V,而在出铜期(S1和S2)显著低于3 V。针对极间电压的这一变化规律,本文根据极间电压监测值在线判断电解周期所处作业阶段。
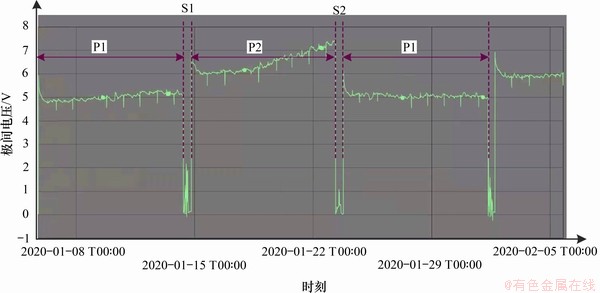
图2 电解槽极间电压与作业阶段示意图
Fig. 2 Schematic diagram of voltages between electrodes in operation stages in electrolytic cell
为了方便描述本文提出的识别模型,定义2个判断条件:
且
(10)
且
(11)
本文模型的识别规则如下。
1) 当前一个采样时刻所处的工作阶段为S2(或S1)时,若条件(10)成立,则将当前采样时刻所处的工作阶段识别为P1(或P2);否则,保持当前识别结果不变。
2) 当前一个采样时刻所处的工作阶段为P1(或P2)时,若条件(11)成立,则将当前采样时刻所处的工作阶段识别为S1(或S2),保持当前识别结果不变。
由于模型在识别作业阶段时需用到前一采样时刻所处的作业阶段信息,因此,模型初次运行时需人工设定系统当前所处的工作阶段。之后,模型即可自行识别,不再需要人工干预。
本文在设置条件(10)和(11)中综合考虑了极间电压的2个连续采样值,其目的在于避免采样噪声可能导致的误判。若现场电压采样值准确度更高,则前述2个条件也可以分别简化为:
(12)
(13)
需要说明的是,本文的识别规则式(10),(11),(12)和(13)是针对国内某企业铜电解系统的实际情况设计的,由于作业制度、工况条件不同,它们可能并不能直接应用于其他企业的铜电解过程。但在目前工艺技术下,铜电解工艺在不同作业阶段极间电压均存在显著差异,因此,在对前述条件中的阈值进行合理修正后,可以适用于其他企业的铜电解过程。
2.3 铜电解过程综合能耗的在线多尺度分析方法
铜电解现场实现了对蒸汽、电等能源消耗量的在线计量,因此,在解决阴极铜产量软测量、作业阶段在线识别等关键问题之后,可以以任意时间尺度对该过程能耗进行分析。考虑到实际工程需要以及现有数据采集制度,本文对电流、极间电压、蒸汽流量等过程变量的采样周期设为1 min,而关键能耗指标的计算周期则主要采用小时(h)、日(d)、作业周期共3个时间尺度,具体步骤如下。
Step 1 将训练好的阴极铜产量软测量模型(模型的训练需离线进行)、电解过程作业阶段在线识别模型以及相关数据采集系统上线运行。
Step 2 整点时刻进行小时级能耗分析,即分析前1 h内系统的能耗。
Step 2(a) 若电解槽在前1 h处于第一阴极周期(P1)或第二阴极周期(P2),则求前1 h内电解液的进出口温度等监测变量平均值即
,启动阴极铜产量软测量模型估算前1 h内的阴极铜产量,计算、输出并存储各类能源消耗量、单位产品能耗等指标。
Step 2(b) 若电解槽在前1 h处于第一出铜期(S1)或第二出铜期(S2),考虑到该阶段没有电解反应发生,仅计算各类能源消耗量,不计算单位产品能耗。
Step 2(c) 若电解槽在前1 h内经历多个作业阶段(如既有阴极周期P1又有出铜期S1),则计算单位产品能耗时仅考虑阴极周期的能耗,各类能耗量的计算方法与步骤2(a)和2(b)的相同。
Step 3 每日0:00进行日级能耗分析,即分析前1 d(前日0:00至当日0:00)内系统的能耗,分析的主要依据是前1 d内存储的小时级能耗。当前1 d包含多个作业阶段时,也需要分作业阶段分析,具体方法与小时级能耗分析方法类似。
Step 4 当“电解过程作业阶段在线识别模型”识别到某个作业阶段结束时,计算并存储该作业阶段的能效。若刚刚结束的是第二出铜期S2,则另需计算和存储该完整作业周期(包含P1,S1,P2和S2)的各项能效指标。
3 方法验证与应用效果
3.1 阴极铜产量软测量模型的验证
本文建立的阴极铜产量软测量模型的核心是电流效率软测量模型。由式(1)和(2)可知,阴极铜产量的软测量误差与电流效率的软测量误差成正比,因此,本节先验证电流效率软测量模型。训练与验证模型的数据均取自国内某铜冶炼厂2019年下半年电解车间的生产记录,在剔除少量变量残缺及存在明显谬误的记录后,共构成312组数据。将其中的260个归入训练集、52个归入检验集,按照2.1节中方法建立和训练基于支持向量机的电流效率软测量模型,3个元参数(p,ε和C)优化结果分别为1.16,0.005和1.1。训练后,模型对训练集、检验集中电流效率的估算效果如图3所示,模型误差的部分统计结果如表1所示。表1中:K为训练集或检验集中数据样本个数;
和
分别为数据集中第i个样本的电流效率真实值和模型计算值。

图3 电流效率软测量模型计算结果示意图
Fig. 3 Calculation result of current efficiency by soft-measuring model
表1 模型误差的部分统计量
Table 1 Partial statistics of model errors
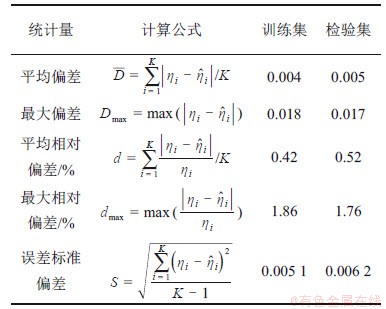
由图3及表1可知:模型的训练集误差与检验集误差相差不大,这在一定程度上说明模型不存在“过拟合”问题,因而具有较强的泛化性能;模型的各项评价指标较好,精度较高,能较准确地估算电解过程的电流效率。由于阴极铜产量的软测量误差与电流效率的软测量误差成正比,因此,图3与表1也能说明本文所建立的阴极铜产量软测量模型具有较强的泛化性能和较高的准确度。
3.2 在线多尺度能效分析方法验证
基于本文开发的“在线多尺度能效分析系统”(简称“分析系统”)在国内某冶炼厂试运行约1月,用于监测和分析其中72个电解槽的整体能耗。试运行期间,电解槽极间电压的监测值如图2所示。现场对这72个电解槽的各项操作(如操作参数的调整、作业阶段的控制等)几乎完全同步,因此,可用本文方法进行统一分析。按照2.3节,“分析系统”分别在整点、每日0:00以及各作业阶段结束时刻分别对小时级、日级以及作业周期级3个时间尺度下的能效进行分析。3种尺度下的能效分析均未涉及复杂运算,计算量较小,因而,从“分析系统”的实际运行速度看,计算耗时均可以忽略不计。
某日(图2所示的2020-01-15之前的24 h)“分析系统”计算获取的小时级数据如图4和图5所示。由图2可知:在分析当日的8:10和19:40,电解过程的作业阶段发生了变迁,“分析系统”准确识别到这2个作业变迁时刻,并按照2.3节中step2(c)的方法计算这2个时刻点所在的小时级周期的相关能效指标。以8:00—9:00这个分析周期为例(图4和5中横坐标为9 h),各类能源消耗量(见图4)为该分析周期的实际消耗量,而单位产品能耗(见图5)为该分析周期中的P1阶段(8:00—8:10)的单位产品能耗。由图4和图5可以看出:铜电解过程消耗的主要能源是电能,包括电解反应消耗的直流电能、行车等传动装置消耗的动力电以及其他辅助设备消耗的电能(图4中的“其他电耗”)。直流电主要消耗于阴极周期(P1或P2),动力电主要消耗于出铜期(S1或S2),因此,这两类电耗在不同作业阶段相差很大。而其他辅助设备的电耗相对稳定,在不同作业阶段相差不大,这主要是因为多数辅助设备不会跟随电解作业阶段的变迁而同步启停。蒸汽消耗量与“其他电耗”的变化规律类似,在不同作业阶段亦无显著区别,原因在于:为了使电解液温度相对稳定,无论是在阴极周期还是在出铜期均需要通入蒸汽,由于电解槽在出铜期内无阴极铜产生,因此,图5中横坐标10~19 h(对应于9:00—19:00)的区域内阴极铜产量为0 t且无单位产品能耗。此外,分析系统计算获取的P1和P2阶段单位阴极铜综合能耗分别为1 267.4 MJ/t和1 270.0 MJ/t,P2阶段的单位产品综合能耗比P1阶段高约1.5%,这与P2阶段极间电压较高等多种因素有关。
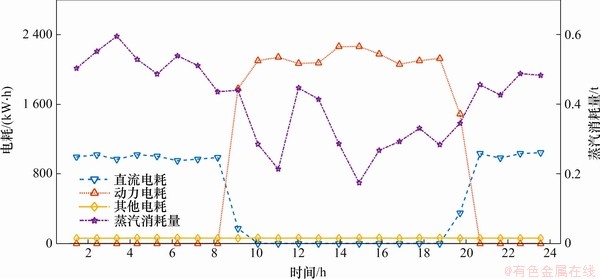
图4 某日各类能源消耗量的小时级电能
Fig. 4 Hourly electric energy of various energy consumptions on a certain day
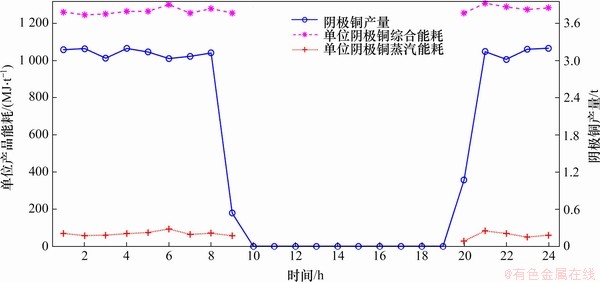
图5 某日阴极铜产量及单位产品能耗的小时级能耗
Fig. 5 Hourly energy consumption of cathode copper production and energy consumption per unit product on a certain day
连续2周(图2所示的2020-01-08T00:00—2020-01-22T00:00),“分析系统”的计算获取的日级能效如图6和图7所示。图中第7日包含了P1,S1和P2共3个作业阶段。对于这种情况,“分析系统”按照2.3节介绍的方法分阶段计算其阴极铜产量以及单位产品能耗,因而,图7中第7日对应的阴极铜产量、单位阴极铜综合能耗、单位阴极铜蒸汽消耗等数据均有2套,分别是基于第7日的P1期数据和P2期数据计算获得的。图6也展示了电解过程中各类能源消耗量在不同作业阶段的分布与变化规律,与图4所示结果以及实际结果一致。从图7可以看出:P2阶段的单位产品综合能耗(1 279.1 MJ/t)比P1(1 267.4 MJ/t)的略高,P2阶段的单位产品蒸汽消耗(58.5 MJ/t)比P1(70.2 MJ/t)的略低。产生这一现象的部分原因在于,P2阶段极间电压较高,致使更多的电能以热的形式耗散,从而增加了直流电耗,但另一方面也降低了电解系统的热需求,蒸汽消耗量的降低量低于直流电耗的增加量。
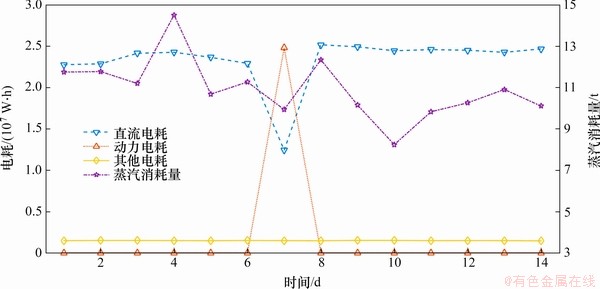
图6 连续2周各类日馺能源消耗量
Fig. 6 Daily energy consumption in two consecutive weeks
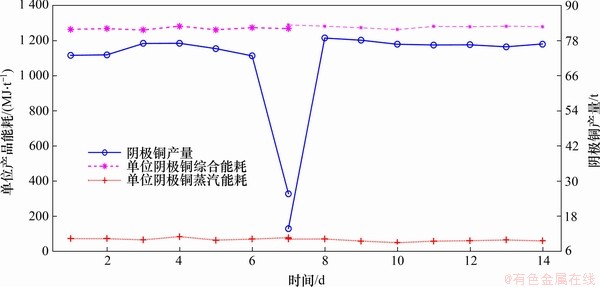
图7 连续2周日级阴极铜产量及单位产品能耗
Fig. 7 Daily copper cathode output and energy consumption per unit product in two consecutive weeks
“分析系统”针对1个完整阳极周期的计算获取的部分周期级能效如表2所示,其中,W代表整个阳极周期。表2中阴极铜产量计算值是本文阴极铜产量软测量模型的计算结果,实测值是现场工人对阴极铜板总质量离线称量所得结果,两者相差不大,这一定程度上说明本文模型的准确性。按照行业习惯,人们在计算单位阴极铜产品综合能耗时通常将阴极周期及其对应的出铜期合并考虑,即用P1和S1(或P2和S2)这2个阶段的总能耗除以P1(或P2)阶段的阴极铜产量作为P1(或P2)阶段的单位产品综合能耗。据此,本文基于阴极铜产量估算值、实测值计算得到P1阶段综合能耗分别为1.413 7 MJ/t和1.390 3 MJ/t,计算得到的P1阶段综合能耗分别为1.443 0 MJ/t和1.457 6 MJ/t。这2组数据的对比结果一方面说明了本文方法的正确性,另一方面也表明电解过程在P2阶段的单位产品综合能耗比P1的高。需指出的是,表2中单位产品综合能耗显著大于日级、小时级的综合能耗,其原因在于周期级能效分析考虑了出铜期消耗的动力电能,而日级、小时级能效分析未将这部分电能计入其中。本文在对处于P1或P2阶段的电解过程进行日级、小时级能效分析时,未考虑出铜期消耗的动力电,其原因是分析时不可能获得动力电消耗(出铜期尚未开始),此外,电解过程的阴极周期和出铜期相对独立,在较小的时间尺度上(如1 h和1 d),分别解析这2类作业阶段的能耗状况对过程的操作优化更具指导意义。
表2 周期级能效分析部分结果
Table 2 Partial results of energy efficiency analysis at cycle-level
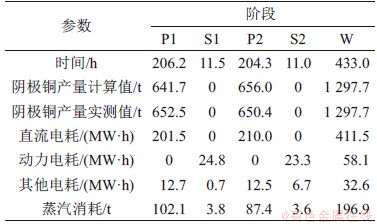
由图4~7以及表2可知不同时间尺度的能效分析具有不同的“精细度”,对电解过程节能优化的作用与意义也有所不同。小时间尺度(如小时级)能效分析结果能够及时反映电解过程“当前”的能耗细节(如某种能源的消耗量是否正常等),可用于指导过程的动态优化控制;大时间尺度(如周期级)能效分析结果主要反映过程能耗的宏观规律与特征(如能耗在不同作业阶段的分布),可用于指导过程调度及作业制度优化等。因而,本文提出的多尺度能效分析方法能够更系统、更全面地反映电解过程,而且采用本文方法无需增加测量仪表等硬件。
4 结论
1) 为了解决铜电解过程能效分析结果相对粗糙且滞后严重等问题,提出了一种基于阴极铜产量软测量的在线多尺度能效分析方法,并开发了相应的软件系统。系统现场试运行结果证明了本文方法的有效性和准确性:
2) 实现了能效分析过程的精细化和在线化,分析的时间尺度细化至小时级,分析结果的时间滞后在分钟级,因而能够及时地向现场的操作人员与决策人员反馈电解过程的能耗。
3) 小时间尺度(如小时级)、大时间尺度(如周期级)分别从细节和宏观层面反映了电解过程能效状态的变化规律,因而多尺度能效分析能更系统而全面地描述过程的能效。
4) 本文的能效计算方法准确,准确度满足现场工程需要。
参考文献:
[1] 彭小奇, 伍雁鹏, 李时民, 等. 氧化铝生产蒸发工序能耗分析[J]. 中南大学学报(自然科学版), 2013, 44(1): 362-366.
PENG Xiaoqi, WU Yanpeng, LI Shimin, et al. Energy consumption analysis for evaporation process in alumina refinery[J]. Journal of Central South University(Science and Technology), 2013, 44(1): 362-366.
[2] 黄健, 赵众. 延迟焦化加热炉热效率的机理建模与实时估计应用[J]. 化工学报, 2020, 71(7): 3140-3150.
HUANG Jian, ZHAO Zhong. Mechanism modeling and real-time estimation application of thermal efficiency for delayed coking furnace[J]. CIESC Journal, 2020, 71(7): 3140-3150.
[3] GBT 2589—2020. 能耗计算通则[S].
GBT 2589—2020. General rules for calculation of the comprehensive energy consumption[S].
[4] GB 21248—2014. 铜冶炼企业单位产品能源消耗限额[S].
GB 21248—2014. The norm of energy consumption per unit product of copper metallurgical enterprise[S].
[5] WOOD J, HOANG J, HUGHES S. Energy efficiency of the Outotec Ausmelt process for primary copper smelting[J]. JOM, 2017, 69(6): 1013-1020.
[6] WANG Can, ZHENG Xinzhu, CAI Wenjia, et al. Unexpected water impacts of energy-saving measures in the iron and steel sector: tradeoffs or synergies?[J]. Applied Energy, 2017, 205: 1119-1127.
[7] MOROSUK T, TSATSARONIS G. Splitting physical exergy: theory and application[J]. Energy, 2019, 167: 698-707.
[8] MOROSUK T, TSATSARONIS G. Advanced exergy-based methods used to understand and improve energy-conversion systems[J]. Energy, 2019, 169: 238-246.
[9] ARAUJO A B, BRITO R P, VASCONCELOS L S. Exergetic analysis of distillation processes:a case study[J]. Energy, 2007, 32(7): 1185-1193.
[10] YARI M. Exergetic analysis of various types of geothermal power plants[J]. Renewable Energy, 2010, 35(1): 112-121.
[11] SINGH N, KAUSHIK S C, MISRA R D. Exergetic analysis of a solar thermal power system[J]. Renewable Energy, 2000, 19(1/2): 135-143.
[12] 彭小奇, 宋国辉, 宋彦坡, 等. 氧化铝生产蒸发工序的(火用)分析[J]. 中南大学学报(自然科学版), 2011, 42(3): 829-834.
PENG Xiaoqi, SONG Guohui, SONG Yanpo, et al. Exergy analysis of evaporation process in an alumina refinery[J]. Journal of Central South University(Science and Technology), 2011, 42(3): 829-834.
[13] MOHAMMADI Z, FALLAH M, MAHMOUDI S M S. Advanced exergy analysis of recompression supercritical CO2 cycle[J]. Energy, 2019, 178: 631-643.
[14] BUHLER F, NGUYEN T V, JENSEN J K, et al. Energy, exergy and advanced exergy analysis of a milk processing factory[J]. Energy, 2018, 162: 576-592.
[15] RONG W, LI B, LIU P, et al. Exergy assessment of a rotary kiln-electric furnace smelting of ferronickel alloy[J]. Energy, 2017, 138: 942-953.
[16] ANDERSEN J P, HYMAN B. Energy and material flow models for the US steel industry[J]. Energy, 2001, 26(2): 137-159.
[17] LIU Xiaojun, LIAO Shengming, RAO Zhenghua, et al. A process-level hierarchical structural decomposition analysis (SDA) of energy consumption in an integrated steel plant[J]. Journal of Central South University, 2017, 24(2): 402-412.
[18] CHEN Jingjing, WANG Zhaohui, WU Yufeng, et al. Environmental benefits of secondary copper from primary copper based on life cycle assessment in China[J]. Resources, Conservation & Recycling, 2019, 146: 35-44.
[19] YU Yang, LI Baokuan, WANG Changjun, et al. Evaluation and synergy of material and energy in the smelting process of ferrochrome pellets in steel belt sintering-submerged arc furnace[J]. Energy, 2019, 179: 792-804.
[20] 刘宇锋, 董博, 柯新安, 等. 降低铜电解电耗的生产实践[J]. 中国有色冶金, 2017(2): 23-25.
LIU Yufeng, DONG Bo, KE Xinan, LIU Jianxin, et al. Production practice of power consumption reduction in copper electrolysis[J]. China Nonferrous Metallurgy, 2017, 46(2): 23-25.
[21] 宋彦坡, 彭小奇, 胡志坤. 支持向量回归机元参数优化方法[J]. 系统工程与电子技术, 2010, 32(10): 2238-2242.
SONG Yanpo, PENG Xiaoqi, HU Zhikun. Meta-parameters optimization method for support vector regression[J]. Systems Engineering and Electronics, 2010, 32(10): 2238-2242.
(编辑 陈灿华)
收稿日期: 2020-12 -10; 修回日期: 2021 -04 -10
基金项目(Foundation item):国家自然科学基金资助项目(51634010,51676211) (Projects(51634010, 51676211) supported by the National Natural Science Foundation of China)
通信作者:宋彦坡,博士,副教授,从事工业过程节能与优化决策研究;E-mail:songyanpo@csu.edu.cn
DOI: 10.11817/j.issn.1672-7207.2021.06.023
引用格式:高东波, 彭小奇, 宋彦坡, 等. 铜电解过程在线多尺度能效分析[J].中南大学学报(自然科学版), 2021, 52(6):1934-1943.
Citation:GAO Dongbo, PENG Xiaoqi, SONG Yanpo, et al. On-line multi-scale analysis of energy efficiency in copper electrolysis process[J]. Journal of Central South University(Science and Technology), 2021, 52(6): 1934-1943.