J. Cent. South Univ. (2016) 23: 975-982
DOI: 10.1007/s11771-016-3145-6

Numerical investigations on effects of bluff body in flat plate micro thermo photovoltaic combustor with sudden expansion
E Jia-qiang(鄂加强)1, 2, HUANG Hai-jiao(黄海蛟)1, ZHAO Xiao-huan(赵晓欢)2
1. College of Mechanical and Vehicle Engineering, Hunan University, Changsha 410082, China;
2. Institute of New Energy and Energy-saving & Emission-reduction Technology, Hunan University,
Changsha 410082, China
Central South University Press and Springer-Verlag Berlin Heidelberg 2016
Abstract: In order to reveal combustion characteristics of H2/air mixture in a micro-combustor with and without bluff body, the effects of inlet velocities, equivalence ratios and bluff body’s blockage ratios on the temperature field, pressure of the combustor wall, combustion efficiency and blow-off limit were investigated. The numerical results indicate that the sudden expansion plate micro combustor with bluff body could enhance the turbulent disturbance of the mixed gas in the combustion chamber and the combustion condition is improved. Moreover, a low-speed and high temperature recirculation region was formed between the sudden expansion step and the bluff body so that the high and uniform wall temperature (>1000 K) could be gotten. As a result, it could strengthen the mixing process, prolong the residence time of gas, control the flame position effectively and widen the operation range by the synergistic effect of the bluff body and steps. When the blockage ratio ranged from 0.3 to 0.6, it could be found that the bluff body could play a stabilizing effect and expand combustion blow burning limit, and combustion efficiency firstly was increased with the inlet velocity and equivalence ratio, and then was decreased.
Key words: micro combustor; bluff body; sudden expansion; numerical investigations
1 Introduction
Recently, the theoretical and experimental works of the micro energy system based on hydrogen combustion (micro power generation systems) have been fully developed [1-4]. It is well known that micro scale combustion means that the fuel is burned in the chamber whose volume was usually less than 1 cm3 and characteristic scale was usually less than or close to the fuel’s quenching diameter or quenching distance. Micro combustors were of many merits, including high energy density, small volume and long working time. Besides, the voltage of the output is stable and the environmental pollution is low. Power MEMS based on the micro power system could not only supply power for the portable civil electronic devices, but also could be applied in the field of national defense, such as micro air vehicles, micro satellites and Single Soldier Combat System. Therefore, the research on micro scale combustion is of great significance [5-8].
Micro thermophotovoltaicc system (micro-TPV) is one of the emerging micro power systems which uses solar cells and can convert the radiation energy of the high-temperature micro combustion chamber into electrical energy directly [9-12]. It is quite important that the micro combustor in the micro-TPV system should keep high combustion stability. At present, the stabilized combustion technology of bluff body has been applied in the aviation and industrial boiler burner combustion in turbulent diffusion [13] and its principle was using the bluff body to make a recirculation region of low speed, high temperature, high concentration, etc, which formed the so-called “flame on duty” and achieved the goal of igniting around fuel. Besides, the existed researches showed that in conventional scale, the sudden expansion structure could produce recirculation region near the wall and be able to strengthen the mixing in combustion process to achieve complete and stable combustion. The source of flame instabilities in premixed combustion of narrow channels was investigated by S
NCHEZ-SANZ et al [14]. It was revealed that the blow-off limit was extended in the presence of the bluff body and higher equivalence ratios. Indeed, higher mixture velocities will be applicable when the bluff body was installed [15]. ZARVANDI et al [16] found that adding hydrogen to methane in a micro- stepped tube could play a pivotal role in modification processes of combustion phenomena in a micro combustor. Also, they found that adding hydrogen to CH4 could assure that the flame existed in certain conditions in comparison to the simple backward facing step method. HOSSEINI et al [17] had studied that in the premixed conventional micro-combustion, the stability of the flame was increased when a triangular bluff-body was applied. Moreover, micro-flameless combustion was more stable when a bluff-body was used. BAGHERI et al [18] had studied the blow-off limit, combustion efficiency, wall temperature and exhaust gas temperature of micro- combustors with different bluff bodies (circle, ellipse, diamond, semicircular, half ellipse, triangle, crescent, arrowhead and wall-blade).
In order to improve and optimize the combustion chamber of the photoelectric system, the bluff body and the sudden expansion step were applied and then the sudden expansion flat plate micro combustor with a bluff body was designed. The combustion characteristics of H2/air based on temperature and pressure distribution, blow-off limit, and combustion efficiency were investigated and the effects of equivalence ratios and the blockage ratios and other factors were discussed.
2 Mathematical model and boundary conditions
2.1 Calculation model
The structures of the micro combustor with and without the bluff body are shown in Fig. 1.
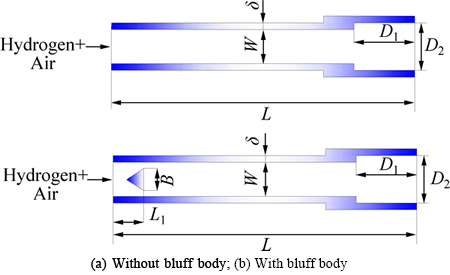
Fig. 1 Structure of micro combustors:
The bluff body’s blockage ratio was defined as B/W and the dimensions of the micro combustor were listed in Table 1.
According to Fig. 1, premixed hydrogen/air mixture flowed into the combustor from the inlet (on the left). After being fully burned, the exhaust gas expelled from the outlet (on the right). Physical property parameters of quartz glass were displayed in Table 2 [19].
Table 1 Dimensions of micro combustor
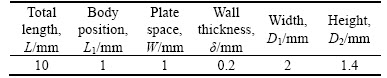
Table 2 Physical property parameters of quartz glass

2.2 Governing equations
In the calculation, the effects of volume force, flow dissipation and gas radiation in the combustor were ignored. Based on the assumption, the governing equations were as follows.
Continuity equation:
(1)
where ρ was the fluid density, kg/m3; u was the velocity of fluid in x direction, m/s; v was the velocity of fluid in y direction, m/s.
Momentum conservation equation:
(2)
where p was the absolute pressure of the fluid, Pa; τ was the viscous stress produced by molecular viscosity.
Energy conservation equation:


(3)
where h was the enthalpy of the fluid, J/kg; λ was the thermal conductivity of the fluid, W/(m·K); T was the absolute temperature of fluid, K; Di was the diffusion coefficient of specie i, m2/s, Yi was the mass fraction of specie i; hi was the enthalpy of specie i, J/kg.
Wall energy conservation equation:
(4)
where λw was the wall thermal conductivity, W/(m·K).
Species conservation equation:

(5)
where Ri was the generation or consumption rate of specie i, kmol/(m3·s).
Hydrogen-air one step reaction rate equation:
(6)
where A was the pre-exponential factor, m1.5·(kmol)-0.5·s-1; E was the reaction activation energy of hydrogen combustion, J/mol; [H2] was the molar concentration of hydrogen, kmol/m3; [O2] was the molar concentration of oxygen, kmol/m3.
2.3 Boundary conditions
Due to the fact that the characteristic diameter of micro combustor was 1 mm and the Kn number of the air was 7×10-5, which was less than 10-3, it could be considered as a continuous fluid and the N-S equation was applicable. In the calculation conditions, although the bluff body wake might appear unstable flow such as the vortex generation and shedding, the maximum Reynolds number was about 600 under cold state.
In the case of combustion, the gas flow rate and the kinematical viscosity were proportional to temperature. The effective Reynolds number of the flow field was smaller than that in the cold condition and the vortex generation and the shedding was obviously inhibited. That is to say, the wake region behind the bluff body was basically the laminar flow in this combustion condition. In addition, the k-turbulence model was calculated and compared with low Reynolds number, and it was proved that the laminar flow model was appropriate. So, a two- dimensional double precision steady-state solver in FLUENT was employed. Meanwhile, the surface reaction was ignored. The boundary conditions were listed in Table 3.
3 Numerical calculation and analysis
3.1 Temperature field distribution
In this section, the temperature field in the combustor without bluff body was compared with the temperature field in the combustor with bluff body. As the distance was 1 mm, the blocking ratio of the combustor with bluff body was 0.3, and the equivalenceratio of simulation under working conditions was 0.5, the temperature distribution in micro combustor and bluff body at different inlet velocities was shown in Figs. 2 and 3, respectively.
Figure 2 presented the temperature field of the sudden expansion micro combustor without a bluff body at various inlet velocities. When the inlet velocity was 0.4 m/s, the high temperature region of the non-bluff body combustor was located at the exit of inlet vicinity with the shape of the flat, which indicated that the flame shape should be flat. Other inlet velocities were compared, and it could be found that the maximum temperature was obtained when the equivalent ratio was 0.5 through calculation under this condition. The front flame and high temperature region in the combustion chamber went to expand when the inlet velocity increased to 5 m/s and 10 m/s. The front flame was narrower and the high temperature region was increased faster. The flame structure went to be narrow when the speed was increased to 15 m/s. it was found that it was a random phenomenon through several calculations. If the inlet velocity was further increased, the flame would be blown out of the combustion chamber. This indicated that the blowout limit of the combustor was about 15 m/s when the equivalent ratio was 0.5.
When the blockage ratio of the combustor with bluff body was 0.3, the plate combustor temperature field distribution with sudden expansion was shown in Fig. 3. Compared with the situation without a bluff body, when the inlet velocity was 0.4, the high temperature region was still located at the exit of inlet vicinity with the shape of the flat, which indicated that the flame shape should be flat. As shown in Fig. 3(c), when the inlet velocity was increased, the high temperature region was located behind the bluff body, which indicated that stable flame behind the bluff body existed at this point. When the inlet velocity was increased to 15 m/s, high temperature zone in the combustion chamber went to be wider, and a long strip at the sudden expansion of the combustion chamber was represented. And the front flame was close to the outlet of the combustion chamber. The flame was moved downstream due to the sudden expansion steps that strengthened the mixing process and prolonged the residence time of gas and controlled the position of the flame to broaden the range of operation effectively.
Table 3 Boundary conditions of the simulation

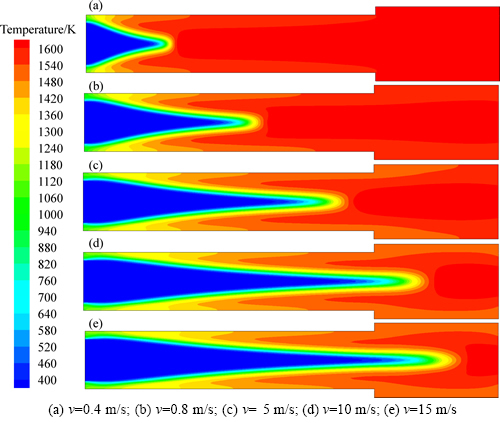
Fig. 2 Temperature field distributions of sudden expansion plate combustor without bluff body:
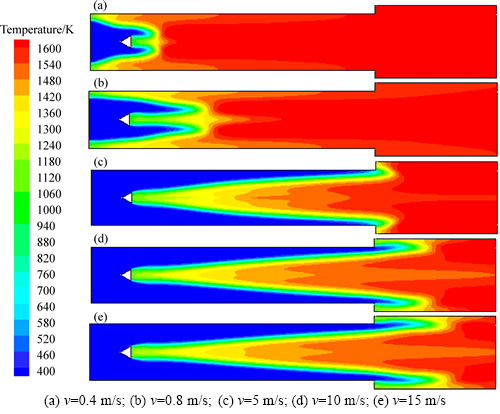
Fig. 3 Temperature field of sudden expansion plate combustor with bluff body at blockage ratio of 0.3:
Therefore, even in the case near the blow-off limit, it could be seen that the temperature field was still in symmetrical distribution, which indicated the existence of symmetric flame distribution in the combustion. When the velocity of import gas was continuous to increase, the flame would be blown out of the combustion chamber. It was indicated that when the equivalent ratio was 0.5, the blow-off limit of the micro combustor with a bluff body was about15 m/s. It could be seen from Fig. 3 that in the case of low velocity, the wall temperature distribution of micro combustor without a bluff body was basically the same as the one with it. This was because at this time flame was in front of the bluff body and the bluff body did not play a role in stabilizing combustion. When the speed was increased, the flame moved to the rear of the bluff body. Because of the expansion of the blow-off limit, it could be brought out that a very uniform temperature distributed on the wall, which illustrated that the bluff body could not only improve blow-off limit but also improve the wall temperature distribution at the same time.
In addition, at different velocities, the temperature field and wall temperature distribution of the flat sudden expansion micro-combustor with the bluff body were verified when the equivalence ratio was 1.0 and the blockage ratio was 0.3. Similar phenomenon happened to non-bluff body combustor since higher temperature distribution was brought by high equivalence ratio. And because of the expansion of the blow-off limit, uniform temperature distribution in most cases could be kept on the wall.
3.2 Pressure distribution
The outer wall pressure profiles of the micro- combustor with and without a bluff body were presented in Fig. 4. Figure 4(a) illustrated the case without bluff body while Fig. 4(b) showed the results with a bluff body. It was seen from Fig. 4 that the trend of pressures decreased under different velocities in the combustor. The reason for this phenomenon was that there was a much more efficient combustion at the back (right) of the combustor and in this zone of high temperature, the outer wall pressure was small because the balance of the flow pressure and explosion pressure produced by combustion. This effect could protect the combustor wall from the high pressure shock, which can reduce the pressure requirements of combustion chamber material. At the sudden expansion of the combustion combustor, the overall pressure fluctuated partly, just as shown in the region of A and B in Fig. 4(a). According to the principle of Bernoulli in fluid mechanics: p+1/2ρv2+ρgh=C (where p is the pressure of the fluid, v is the flow rate of the fluid, ρ is the fluid density, g is the gravity, h is the altitude, and C is a constant). It could be seen that the gravitational potential energy of working medium decreased as a whole at the position of the sudden expansion, and as a result, the pressure altered with the change of velocity and there was fluctuation. By the way, the reason was also suitable to the case of the micro-combustor with a bluff body in the region of A in Fig. 4(b).
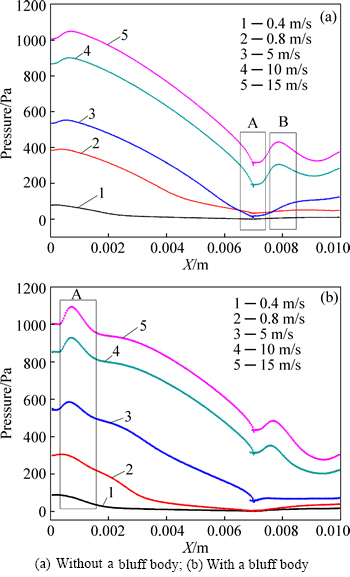
Fig. 4 Pressure field distributions of combustor:
From Figs. 4(a) and (b), it could be found that there was the same trend of pressure distribution at the position of X=0.007-0.008 m and both of them appeared the crest value which was caused by the design of sudden expansion. Obviously, the separation and attachment of the fluid to the step could strengthen the mixing process. Even with the reaction proceeding, the total pressure decreased gradually along the direction from entrance to export. This made a backflow region near wall and prolonged the residence time of the hydrogen/air mixture due to the function of the sudden enlargement stage, which could make the pressure on the combustor wall rise suddenly. Moreover, it was more obvious in the situation of flow velocity or high equivalence ratio. Now, we could draw a conclusion that it could be divided into two stages in the inner of the micro combustor with the sudden enlargement steps: in preliminary stage, combustion happened close to wall area due to the function of the steps; and then, combustion occurred in the center of the burner exit areas, which was caused by the high temperature near the wall produced by the previous phase. Therefore, for a given equivalent ratio and flow rate, high pressure still existed. This meant that it was very effective for the high demand of high wall heat flux density/temperature direct energy conversion model of micro power systems using this sudden enlargement type micro combustor.
3.3 Combustion efficiency
The combustion efficiency in the combustor with and without a bluff body was compared. For the micro combustor, the combustion efficiency was defined as follows:
(7)
where
was the mass flow rate of air,
was the mass flow rate of fuel, h1 was the specific enthalpy of air, h2 was the specific enthalpy of mixture, hf was the specific enthalpy of fuel, and Qloss was the total heat loss.
As the fuel in this work was hydrogen, the combustion efficiency was rewritten as follows:
(8)
where mfuel,in was the mean mass fraction of inlet fuel, and mfuel,out was the mean mass fraction of outlet fuel.
Figures 5 and 6 show the combustion efficiencies of the combustor with and without a bluff body at various inlet velocities when the equivalence ratio was 0.5 and 1, respectively. It could be seen from Fig. 5 that, the combustion efficiency of the two combustors increased firstly with the inlet velocity, then decreased. When the inlet velocity was low, the total mass of fuel flowing into the combustion chamber per unit time was very small. Although the low fuel mass flow rate could increase the fuel’s residence time in the combustion chamber, it would weaken chemical reaction rate and decrease combustion efficiency. Although the chemical reaction rate increased with the inlet velocity, it needed a longer time to completely combust the mixing gas. Meanwhile, the increase of inlet gas velocity caused the flame to move towards the outlet of the combustion chamber and shortened the residence time of fuel in the combustion chamber. Both effects could cause combustion efficiency to decrease with the inlet velocity. Even so, the combustion efficiency in the whole range still maintained at a high level. In addition, it also could be seen that, at low inlet velocity, the combustion efficiency of the micro combustors with and without a bluff body had a good agreement. This was because when the inlet velocity was 0.5-2 m/s, for the micro combustor with a bluff body, the flame was in front of the bluff body and the bluff body had little effect on flame stability. So, the combustion efficiency of the two micro combustors was very close and low. When the inlet velocity exceeded 2.0 m/s, the flame was located behind the bluff body. Compare with the combustor without a bluff body, the combustor with a bluff body had a higher combustion efficiency at the same inlet velocity. This was due to the existed low speed and high temperature recirculation zone behind the bluff body which increased the residence time of gas and strengthened the chemical reaction rate.
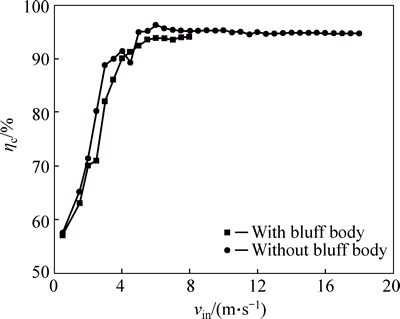
Fig. 5 Comparison of combustion efficiency of combustors with and without a bluff body at various inlet velocities with equivalent ratio of 0.5
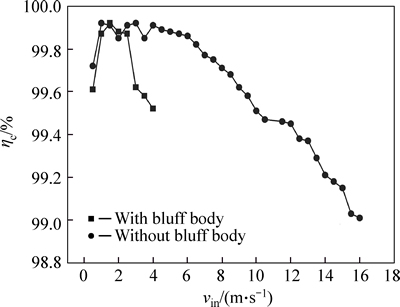
Fig. 6 Comparison of combustion efficiency of combustors with and without a bluff body at various inlet velocities with equivalent ratio of 1.0
Figure 6 showed the comparison of combustion efficiency of combustors with and without a bluff body at various inlet velocities when the equivalence ratio was 1. It could be seen from Figs. 5 and 6, the changing trend of the combustion efficiency at the equivalence ratio of 1 was similar to that at the equivalence ratio of 0.5. A slight difference was that the reaction zone was close to the bluff body at the inlet velocity of 2 m/s when the equivalence ratio was 0.5. The flame structure in the local flow field changed because of the interference of the bluff body. The combustion efficiency of the combustor with bluff body was slightly lower than the one without bluff body.
In addition, by comparing Figs. 5 with 6, it could still be seen that at the same velocity, the combustion efficiency at an equivalence ratio of 1 was less than that at an equivalence ratio of 0.5 and the difference was especially obvious at low flow rates. Besides, it could also be seen that the combustion efficiency was less than that with equivalence ratio of 0.5 at the same velocity. It was especially different at low flow rates. It was because when the hydrogen content was higher, it could not be fully conversed in a short period. Therefore, the combustion efficiency decreased. When the inlet flow velocity was smaller, due to the less heat with reaction released, the decrease of the combustion efficiency was more obvious.
3.4 Blow-off limit
The blow-off limit of the combustor with and without bluff body is discussed. Figure 7 presented the blow-off limit of the combustors with and without a bluff body at the blockage ratio of 0.3. As shown in the figure, the blow-off limit of the combustor with a bluff body increased by 2-4 times than the one without a bluff body. The blow-off limit of the combustor without a bluff body was significantly lower than the combustor with a bluff body. Moreover, when the equivalence ratio was in the range of 0.5-0.8, the blow-off limit of the micro combustor with a bluff body could be kept at 16 m/s in a wide range, which would be conducive to the practical application of the micro combustor.
Figure 8 presented the effects of the blockage ratio on the blow-off limit. From this figure, the following conclusions could be drawn.
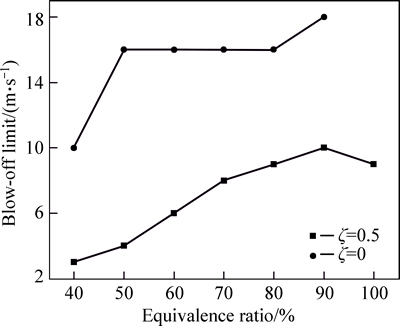
Fig. 7 Comparison of blow-off limit in a sudden expansion flat combustor with and without a bluff body
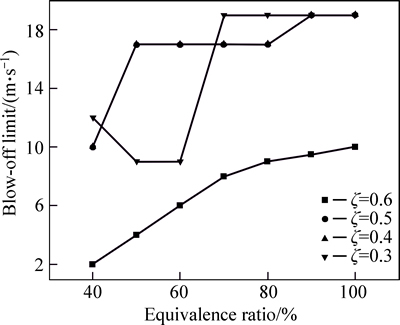
Fig. 8 Effects of blockage ratio on blow-off limit
Firstly, it reached the optimal effectiveness to stabilize combustion when the blockage ratio of the sudden expansion micro-combustor with a bluff body was 0.5. It could keep the blow-out limit at 19 m/s when the equivalent ratio ranged from 0.4 to 0.9. Compared with the sudden expansion micro-combustor without a bluff body, the blow-off limit was nearly increased twice. And when the equivalence ratio was 0.4, the increase ratio of the combustion chamber wall abstracted heat to the heat exothermic reaction, which could weaken the effects of the bluff body on expanding blow-off limit.
Secondly, when the blockage ratio was 0.6 and 0.4, respectively, in the same equivalence ratio, the two combustors nearly had the same blow-off limit. When the equivalent ratio ranged from 0.5 to 0.8, the blow-off limit kept a constant of 16 m/s.
Thirdly, when the blockage ratio was 0.3, it could be seen that the blow-off limit was nearly linearly increased with the equivalence ratio and did not exist a steady blow-off limit. This was due to the fact that the bluff body was too small and the steady-flow region behind the bluff body was too small. Under this condition, the bluff body didn’t work. When the inlet velocity was 6 m/s, the stable flame did not exist behind the bluff body. However, at some distance behind the bluff body, there was a deflective flame. Meanwhile, due to the existence of bluff body, it disturbed the fluid velocity distribution and made the flame move to the downstream of the combustion chamber. So, under the blockage ratio of 0.3, it actually reduced the reaction time in the combustion chamber, decreasing the combustion efficiency.
4 Conclusions
1) The temperature in the flat micro-combustor with a bluff body was increased with the increase of the inlet velocity. Behind the bluff body, a low speed and high temperature recirculation region were formed. Besides, high (>1000 K) and uniform wall temperature could be obtained in the combustor because of the sudden expansion.
2) Compared with the micro-combustor without bluff body, the micro-combustor with a bluff body could make full use of bluff body and the step for strengthening the mixing, prolonging the residence time of gas, controlling the flame position and broadening the operation range. The combustion efficiency firstly was increased with the inlet velocity and equivalence ratio, and then was decreased.
3) At various equivalence ratios, it was found that the bluff body could stabilize flame and expand blow-off limits with the blockage ratio ranging from 0.3 to 0.6. When the blockage ratio was equal to 0.3, the bluff body would lose the role of stabilizing combustion.
4) The numerical results showed that the combustor with sudden expansion and bluff body was much more suitable for micro thermal photovoltaic system.
References
[1] KAISARE N S, VLACHOS D G. A review on microcombustion: Fundamentals, devices and applications [J]. Progress in Energy and Combustion Science, 2012, 38(3): 321-359.
[2] KHANDELWAL B, KUMAR S. Experimental investigations on flame stabilization behavior in a diverging micro channel with premixed methane–air mixtures [J]. Applied Thermal Engineering, 2010, 30(17): 2718-2723.
[3] JU Y, MARUTA K. Microscale combustion: Technology development and fundamental research [J]. Progress in Energy and Combustion Science, 2011, 37(6): 669-715.
[4] CHOU S K, YANG W M, CHUA K J, LI J, ZHANG K L. Development of micro power generators–A review [J]. Applied Energy, 2011, 88(1): 1-16.
[5] LI J, HUANG J, YAN M, ZHAO D, ZHAO J, WEI Z, WANG N. Experimental study of n-heptane/air combustion in meso-scale burners with porous media [J]. Experimental Thermal and Fluid Science, 2014, 52: 47-58.
[6] YANG W M, CHOU S K, SHU C, LI Z W, XUE H. Development of microthermophotovoltaic system [J]. Applied Physics Letters, 2002, 81(27): 5255-5257.
[7] LI J, HUANG J, ZHAO D, ZHAO J, YAN M, WANG N. Diffusion combustion of liquid heptane in a small tube with and without heat recirculating [J]. Combustion Science and Technology, 2012, 184(10/11): 1591-1607.
[8] JI C, ZHAO D, LI X, LI S, LI J. Nonorthogonality analysis of a thermoacoustic system with a premixed V-shaped flame [J]. Energy Conversion and Management, 2014, 85: 102-111.
[9] VEERARAGAVAN A, CADOU C. Theoretical study of conjugate heat transfer effects on temperature profiles in parallel flow with embedded heat sources [J]. International Journal of Heat and Mass Transfer, 2010, 53(9): 1699-1711.
[10] HOSSEINI S E, BAGHERI G, WAHID M A. Numerical investigation of biogas flameless combustion [J]. Energy Conversion and Management, 2014, 81: 41-50.
[11] E Jia-qiang, ZUO Wei, LIU Hao-jie, PENG Qing-guo. Field synergy analysis of the micro-cylindrical combustor with a step [J]. Applied Thermal Engineering, 2016, 93: 83-89.
[12] TANG A, PAN J, YANG W, XU Y, HOU Z. Numerical study of premixed hydrogen/air combustion in a micro planar combustor with parallel separating plates [J]. International Journal of Hydrogen Energy, 2015, 40(5): 2396-2403.
[13] SMITH A G, MENON S, LOVETT J A. Large eddy simulation of a bluff-body–stabilized flame with close-coupled liquid fuel injection [J]. Journal of Engineering for Gas Turbines and Power, 2014, 136(3): 031505.
[14] S
NCHEZ-SANZ M. Premixed flame extinction in narrow channels with and without heat recirculation [J]. Combustion and Flame, 2012, 159(10): 3158-3167.
[15] FAN Ai-wu, WAN Jian-long, MARUTA K. Interactions between heat transfer, flow field and flame stabilization in a micro-combustor with a bluff body [J]. International Journal of Heat and Mass Transfer, 2013, 66: 72-79.
[16] ZARVANDI J, TABEJAMAAT S, BAIGMOHAMMADI M. Numerical study of the effects of heat transfer methods on CH4/(CH4+ H2)-Air pre-mixed flames in a micro-stepped tube [J]. Energy, 2012, 44(1): 396-409.
[17] HOSSEINI S E, WAHID M A. Investigation of bluff-body micro-flameless combustion [J]. Energy Conversion and Management, 2014, 88: 120-128.
[18] BAGHERI G, HOSSEINI S E, WAHID M A. Effects of bluff body shape on the flame stability in premixed micro-combustion of hydrogen–air mixture [J]. Applied Thermal Engineering, 2014, 67(1): 266-272.
[19] REBOLA A, COELHO P J, COSTA M. Assessment of the performance of several turbulence and combustion models in the numerical simulation of a flameless combustor [J]. Combustion Science and Technology, 2013, 185(4): 600-626.
(Edited by YANG Bing)
Foundation item: Project(51176045) supported by the National Natural Science Foundation of China; Project(201208430262) supported by the National Studying Abroad Foundation of China
Received date: 2015-01-30; Accepted date: 2015-05-30
Corresponding author: E Jia-qiang, Professor, PhD; Tel: +86-13187041842; E-mail: ejiaqiang@126.com