
Influence of Cr addition on microstructure of a 5% Re-containing single crystal nickel-based superalloy
TAN Xi-peng1, 2, LIU Jin-lai1, JIN Tao1, SUN Xiao-feng1, HU Zhuang-qi1
1. Institute of Metal Research, Chinese Academy of Sciences, Shenyang 110016, China;
2. Graduate University of Chinese Academy of Sciences, Beijing 100049, China
Received 18 October 2010; accepted 14 January 2011
Abstract: Based on a 5% (mass fraction) Re-containing single crystal nickel-based superalloy with 3% (mass fraction) Cr, the microstructural variation with Cr addition was investigated. The experimental results show that segregation of alloying elements was enhanced in as-cast microstructure with Cr addition; and the volume fraction of eutectic is increased. However, the solidus and liquidus temperatures are remarkably reduced. With the increase of Cr content, the average γ? size and volume fraction are decreased in the fully heat treated microstructure. X-ray diffraction results indicate that γ/γ? lattice misfit becomes more negative. According to the energy dispersive spectroscopy (EDS) results, Cr is mainly distributed in the γ matrix; and more γ-forming elements, such as Re and W, enter the γ matrix, while the γ/γ? partition ratio of Cr is inversely decreased.
Key words: Cr; Re; single crystal superalloy; misfit; microstructure
1 Introduction
Since being successfully introduced in 1980s, single crystal (SC) nickel-based superalloys have become the major materials of turbine blades and vanes for both industrial and aero applications[1-5]. To date the SC superalloys are generally classified into five generations in terms of their composition characteristics, and Cr is always one of the most concerned elements in advanced SC superalloys[6]. It is generally accepted that the temperature capability increases with decreasing Cr content in the alloys[7]. Moreover, Cr is also typically associated with the precipitation of TCP phases due to its electron vacancies in d-shell orbital which provide high potential to form strong TCP phase bonds between Mo and W[8]. Therefore, in view of the composition of the first three-generation SC superalloys, an obvious trend of lowering Cr and increasing Re content was found. However, since Cr plays a key role in promoting the formation of a protective chromium-rich oxide scale at the temperatures where hot corrosion is active, it is of significance for new generation SC superalloys with a certain Cr content added to obtain a satisfactory hot corrosion resistance[9]. Further, previous studies[10-11] have shown that the interaction between Cr and Re or among Cr, Re and Ru is pronounced. Thus, it is meaningful to systematically investigate the influence of Cr on the advanced SC superalloys including microstructure and mechanical properties. The present work aims at elucidating the influence of Cr addition on the as-cast and fully heat treated microstructures of a SC superalloys containing 5% Re (mass fraction).
2 Experimental
2.1 Materials
Based on a SC nickel-based superalloy with a nominal chemical composition of 5Re-3Cr-6W-1Mo- 8Ta-12Co-6Al-Ni (mass fraction, %), additional 2% Cr was added; and these two alloys were designated as 3Cr and 5Cr, respectively. Various Cr additions are the only difference between the two alloys in composition. The master alloys were all melted by vacuum induction technique, and then directionally solidified into [001] oriented cylindrical bars (d16 mm×75 mm) in an investment casting cluster mold in a Bridgman furnace with a withdrawal rate of 6 mm/min. Conventional helical starters were utilized to initiate single crystal growth. The full heat treatment schedules for the two alloys were (1 335 °C, 16 h)+(1 345 °C, 16 h, air cooling)+(1 100 °C, 4 h, air cooling)+(870 °C, 24 h, air cooling) and (1 325 °C, 16 h+1 335 °C, 16 h, air cooling)+(1 100 °C, 4 h, air cooling)+(870 °C, 24 h, air cooling), respectively.
2.2 Microstructural examination and analysis
LEICA optical microscope (OM) and JMS-6301F field-emission scanning electron microscope (SEM) were used to observe the as-cast and fully heat treated microstructures. An EPMA 1610 was used to quantitatively measure the compositions of dendrite cores and eutectics in interdendritic regions and an average value for three parallel data was adopted. In addition, the fully heat treated specimens were cut into d3 mm-discs parallel to (001) plane with 500 μm in thickness and thinned down to 50 μm mechanically. They were then electrochemically polished by the twin-jet method, in a solution of 8% perchloric acid and 92% ethanol at -10 °C and 20-30 mA. A TECNAI 20 transmission electron microscope (TEM) equipped with energy dispersive spectrometer (EDS) was used to examine the partition of alloying elements between γ matrix and γ? precipitates.
2.3 Differential scanning calorimetry (DSC) analysis
The influence of Cr addition on the liquidus and solidus temperature was investigated with a SETERAM SETSYS Evolution 18 integrated thermal analyzer equipped with heat-flow type DSC. The major temperature interval ranged from 1 000 °C to 1 500 °C and a 5 °C/min scanning rate was chosen for heating as it yielded the best combination of temperature accuracy and peak resolution. The cylindrical DSC samples (d3 mm×(1-2) mm) with 90-120 mg were prepared, containing a representative region of the dendritic microstructure.
2.4 X-ray diffraction (XRD) measurement
The XRD patterns were recorded by conventional Rigaku D/MAX 2500 X-ray diffractometer with Cu Kα radiation at 50 kV and 300 mA. This instrument was set up for Bragg-Brentano geometry with a line focus and a graphite monochromator between specimen and detector. The intensity profiles of {004} reflection were collected to measure γ/γ? lattice misfit. The step scans were made at 0.02° per step and the counting time was adjusted to make sure the counts can up to 104. The error of the absolute measurement of the lattice plane spacing in this diffractometer was Δd/d?10-4. With Δ(2θ)=±0.02°, Δδ=±0.02% could be obtained. All the measurements were carried out at room temperature. The detailed diffraction techniques and peak-fitting methods can be seen in Ref.[12].
2.5 EDS measurements
The partitioning behaviors of various alloying elements between γ matrix and γ? precipitate were determined by measuring the local chemical compositions of γ and γ? in fully heat treated specimens using an EDS in TEM and also an average value for three parallel data was adopted. The partition ratio k or k′, which is defined as
or
was widely used. Therefore, it can be known that ki>1 indicates the preferential partition to γ matrix for the alloying element; conversely, ki<1 indicates the preferential partition to γ? precipitate. Further, it also means that the more the deviation from unity for ki, the stronger the partition for the alloying element.
3 Results and discussion
3.1 As-cast microstructure
Both alloys exhibit typical dendritic microstructures. The results of quantitative metallography show that the volume fractions of γ/γ? eutectic are 5.8% and 6.5% for alloy 3Cr and 5Cr, respectively.
In order to clearly show the dendritic segregation of individual alloying element, the segregation ratio K of K′ was defined as Ki=ciD/ciE or K′i=ciE/ciD, where ciD and ciE are concentrations of alloying element in the dendrite core and eutectic in the interdendritic region, respectively. As shown in Fig.1, the segregation behaviors of individual alloying elements in two alloys are basically consistent with the previous reports[13-14]. Al, Ta and Ni partition to the interdendritic eutectic regions, whereas Re, W, Cr, Mo, and Co partition to the dendrite cores. Undoubtedly, Re and Ta are the two elements that segregate more severely. However, it is worth pointing out that 5% Cr addition slightly promotes the segregation of almost all of the alloying elements except Ni. Specially, more γ′-forming elements such as Al and Ta enter the interdendritic region, which results in an increased volume fraction of γ/γ′ eutectic in alloy 5Cr.
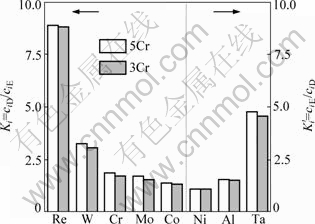
Fig.1 Comparison of segregation ratio for alloying elements in two alloys
Figure 2 shows the heating curves of the two alloys in DSC experiment. It is clearly seen that more Cr addition significantly decreases the solidus and liquidus temperatures (TS and TL) with a gap of over 10 °C. Based on the binary Ni-X phase diagrams, it can be known that adding alloying elements was generally expected to decrease the liquidus temperature of a multicomponent superalloy except Re, W, Ru and Ir[15]. Note that it is to decrease solidus and liquidus temperature to limit the further development of SC superalloys to a higher temperature capability. As known from this work, excess Cr addition must be unfavorable to further enhance the temperature capability of advanced SC superalloys.

Fig.2 Comparison of DSC heating curves of two alloys
3.2 Fully heat treated microstructure
As seen in Fig.3, the fully heat treated microstructures of these two alloys consist of cubical γ′ particles and γ matrix. Figure 4 shows that the γ′ particle size and γ′ volume fraction are decreased with Cr addition. The average γ′ particle sizes are 0.62 μm and 0.5 μm, and the average γ′ volume fractions are 82% and 73%, respectively. It is shown that the distribution of γ′ particle is more uniform for alloy 5Cr than alloy 3Cr.
Figures 5(a) and (b) show fitting results of (004) peaks for the two alloys under full heat treatment. It can be seen that the fitting results of peaks fit well with the experimental data. According to the three-peak fitting model depicted in Ref.[12], the lattice of γ′ phase maintained cubic and the lattice of γ matrix was tetragonally distorted in the fully heat treated microstructure. Therefore, the constrained γ/γ′ lattice misfit dc should be calculated by
, where aγ′ and aγ⊥ are the lattice constants of the γ′ phase and the γ phase in the vertical matrix channels, respectively. Figure 6(a) indicates that both the lattice constants of γ matrix and γ′ precipitate are increased and the increment of the lattice constant of γ matrix is larger. The degree of the tetragonal distortion of γ lattice was evaluated by aγ∥/aγ⊥, where aγ∥ and aγ⊥ are the lattice constants of γ phase in the horizontal and vertical matrix channels, respectively. Thus, it shows that the γ/γ′ lattice misfit becomes more negative and the tetragonal distortion of γ lattice becomes more severely with Cr addition (see Fig.6(b)). As known, a severer distortion of γ lattice would give rise to larger elastic strain energy at the coherent γ/γ′ interfaces. It would be an effective barrier for the growth of γ′ particles, which results in a smaller γ′ size and then a reduced γ′ volume fraction. Moreover, it was reported that a more negative γ/γ′ lattice misfit would be beneficial to the creep properties for SC superalloys[16]. On the other hand, adding Cr improves hot corrosion but degrades microstructural stability associated with precipitation of TCP phases[6]. Therefore, to balance properly the trade-off of these effects of Cr is needed.
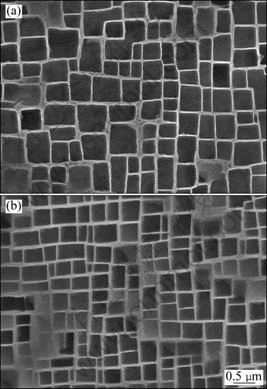
Fig.3 Fully heat treated microstructures of alloy 3Cr (a) and alloy 5Cr (b)
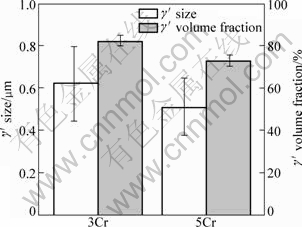
Fig.4 Variations of γ′ particle size and γ′ volume fraction of alloys with Cr addition
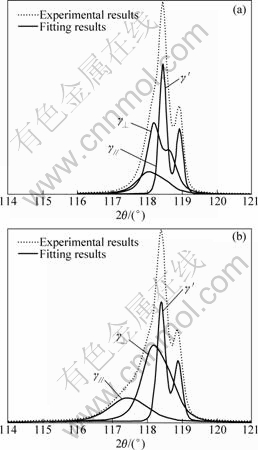
Fig.5 Fitting results of (004) peaks for alloy 3Cr (a) and alloy 5Cr (b) under full heat treatment
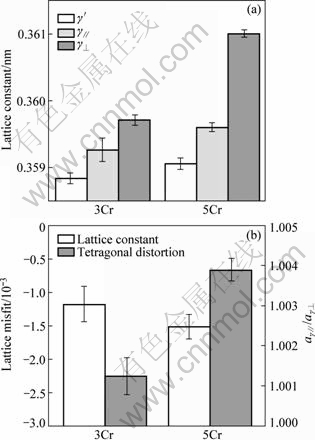
Fig.6 Variations of aγ′, aγ∥ and aγ⊥ (a) and lattice misfit and degree of tetragonal distortion (b) of γ lattice
Figure 7 illustrates the comparison of the partition ratio ki and ki′ for alloying elements in alloy 3Cr and 5Cr. It is clearly seen that Cr was mainly distributed in γ matrix. The most striking feature is that the partition ratio of Re in alloy 5Cr is significantly greater than that in alloy 3Cr. Moreover, the partition ratio of another significant strengthening element W was also increased with 5% Cr addition. Therefore, it is easily considered that more Re and W partitioned to γ matrix would give rise to a more negative lattice misfit between the coherent precipitates and matrix due to their larger atomic radii. This well explains the experimental results mentioned above. Besides, it should be noticed that the γ/γ′ partition ratio of Cr was inversely decreased with Cr addition. It would indirectly elucidate that more Re atoms enter γ phase as a result of substituting for Cr atoms. Thus, it shows strong interaction between Cr and Re. This would also have a great effect on the microstructure and mechanical properties for SC superalloys.
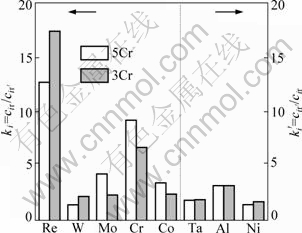
Fig.7 Comparison of partition ratio for alloying elements in two alloys
4 Conclusions
1) With Cr addition, the volume fraction of γ/γ′ eutectic is increased and the segregation of alloying elements is severer. Both the solidus and liquidus temperature are reduced remarkably.
2) The average γ′ size and volume fraction are decreased and the γ/γ′ lattice misfit becomes more negative in the fully heat treated microstructure with increasing Cr content.
3) The γ/γ′ partition ratios of Re and W are significantly increased, while that of Cr is inversely decreased with the increment of Cr content.
References
[1] GELL M, DUHL D N, GIAMEI A F. The development of single crystal superalloy turbine blades superalloys [C]//Superalloys 1980. Warrendale, PA: TMS, 1980: 205-214.
[2] CETEL A D, DUHL D N. Second-generation nickel-base single crystal superalloy [C]//Superalloys 1988. Warrendale, PA: TMS, 1988: 235-244.
[3] HU Zhuang-qi, LIU Li-rong, JIN Tao, SUN Xiao-feng. Development of the Ni-base single crystal superalloys [J]. Aeroengine, 2005,31(3): 1-7.
[4] ERICKSON G L. The development and application of CMSX-10 [C]//Superalloys 1996. Warrendale, PA: TMS, 1996: 35-44.
[5] SATO A, HARADA H, YEH A.C, KAWAGISHI K, KOBAYASHI T, KOIZUMI Y, YOKOKAWA T, ZHANG J X. A 5th generation SC superalloy with balanced high temperature properties and processability [C]//Superalloys 2008. Warrendale, PA: TMS, 2008: 131-138.
[6] REED R C. The superalloys: Fundamentals and applications [M]. Cambridge University Press, 2006: 147-170.
[7] SINGER R. Advanced materials and processes for land-based gas turbines [C]//Materials for Advanced Power Engineering 1994. Liege, 1994: 1707-1729.
[8] BREWER L. Chemical bonding theory applied to metals [C]// ASM International, Alloying 1988. Ohio: Metals Park, 1988: 1-28.
[9] CARON P, KHAN T. Evolution of Ni-based superalloys for single crystal gas turbine blade applications [J]. Aerospace Science and Technology, 1999, 3(8): 513-523.
[10] SMITH J. Effects of Cr and Re additions upon coarsening and deformation behavior of single-crystal Ni-base model superalloys [D]. Urbana-Champaign, University of Illinois, 1987.
[11] CARROLL L, FENG Q, MANSFIELD J, POLLOCK T. High refractory, low misfit Ru-containing single-crystal superalloys [J]. Metallurgical and Materials Transactions A, 2006, 37(10): 2927-2938.
[12] PYCZAK F, NEUMEIER S, G?KEN M. Influence of lattice misfit on the internal stress and strain states before and after creep investigated in nickel-base superalloys containing rhenium and ruthenium [J]. Materials Science and Engineering A, 2009, 510-511: 295-300.
[13] KARUNARATNE M S A, COX D C, CARTER P, REED R C. Modelling of the microsegregation in CMSX-4 superalloy and its homogenisation during heat treatment [C]//Superalloys 2000. Warrendale, PA: TMS, 2000: 263-272.
[14] CALDWELL E C, FELA F J, FUCHS G E. The segregation of elements in high-refractory-content single-crystal nickel-based superalloys [J]. Journal of the Minerals, Metals and Materials Society, 2004, 56(9): 44-48.
[15] FENG Q, NANDY T K, TIN S, POLLOCK T M. Solidification of high-refractory ruthenium-containing superalloys [J]. Acta Materialia, 2003, 51(1): 269-284.
[16] ZHANG J X, WANG J C, HARADA H, KOIZUMI Y. The effect of lattice misfit on the dislocation motion in superalloys during high-temperature low-stress creep [J]. Acta Materialia, 2005, 53(17) 4623-4633.
添加Cr对一种含5%Re镍基单晶高温合金微观组织的影响
谭喜鹏1, 2,刘金来1,金 涛1,孙晓峰1,胡壮麒1
1. 中国科学院 金属研究所,沈阳 110016;
2. 中国科学院 研究生院,北京 100049
摘 要:在一种含5%Re(质量分数)和3%Cr的镍基单晶高温合金基础上,研究再添加Cr后合金组织的变化。实验结果表明:随着Cr含量的增加,合金铸态组织中元素偏析加重,共晶体积分数增加,固相线和液相线温度显著降低。此外,完全热处理态组织中γ′尺寸和体积分数都减小。X射线衍射分析结果表明,Cr的添加使γ/γ′点阵错配度变得更负。从能量色散谱仪的结果可知,Cr主要分布在γ基体中,并且随着Cr含量的增加,更多的γ基体形成元素(如Re和W等)进入γ基体中,但Cr在γ/γ′中的分配比却减小。
关键词:Cr;Re;单晶高温合金;错配度;微观组织
(Edited by YANG Hua)
Foundation item: Projects (2010CB631200, 2010CB631206) supported by the National Basic Research Program of China; Project (50931004) supported by the National Natural Science Foundation of China
Corresponding author: JIN Tao; Tel: +86-24-23971757; E-mail: tjin@imr.ac.cn
DOI: 10.1016/S1003-6326(11)60813-3