J. Cent. South Univ. Technol. (2010) 17: 703-707
DOI: 10.1007/s11771-010-0543-z
Catalytic graphitization of Mo-B-doped apolyacrylonitrile (PAN)-based carbon fibers
XU Shi-hai(徐世海), ZHANG Feng-ying(张凤英), LIU Shao-huan(刘绍欢),
HE Dong-mei(贺冬梅), CAI Qing-yun(蔡青云)
State Key Laboratory of Chemo/Biosensing and Chemometrics, Hunan University, Changsha 410082, China
? Central South University Press and Springer-Verlag Berlin Heidelberg 2010
Abstract: A novel carbon fiber pretreatment was proposed. Polyacrylonitrile (PAN)-based carbon fibers were first anodized in H3PO4 electrolyte to achieve an active surface, and then coated with Mo-B catalysts by immersed the carbon fibers in a uniformly dispersed Mo-B sol. The as-treated carbon fibers were then graphitized at 2 400 ℃ for 2 h. The structural changes were characterized by X-ray diffractometry (XRD), Raman spectroscopy, scanning electron microscopy (SEM) and high-resolution transmission electronic microscopy (HRTEM). The results show that much better graphitization can be achieved in the presence of Mo-B, with an interlayer spacing (d002) of 0.335 8 nm and a crystalline size (Lc) of 28 nm.
Key words: polyacrylonitrile (PAN)-based carbon fibers; anodization; sol; catalytic graphitization; Mo; B
1 Introduction
Graphitization is a transformation of unformed and disordered carbon material into three-dimensional graphite under high heat treatment temperature. Usually, the heat treatment temperature is above 3 000℃. The acceleration of graphitization by stresses in the thermosetting matrix of carbon has been observed and is called stress- graphitization [1]. In addition to stress, the addition of certain inorganic or organic additives is known to accelerate graphitization of carbon materials at lower temperatures and brings about a transformation of a disordered carbon structure into the ordered structure of hexagonal graphite [2-8]. Various additives, such as refractory-metal carbides including TiC, ZrC, VC, and WC [2-4], as well as elemental Fe, Ni, B, Si, Ti, Zr [5-9] were researched. This phenomenon is called catalytic graphitization. The effects of graphitization degree on the mechanical properties of C/C composite were also studied in previous papers and found that the fracture mechanism varies with the graphitization degree [10-11]. Among the inorganic additives tested, boron and its compounds were observed as effective catalysts for the graphitization of carbons. And then, the doped boron was also found to improve the oxidation resistance of graphite [12], carbon fibers [13], C/C composites [14] and other carbon materials [15]. Graphitization by boron occurs through diffusing the boron atom in the carbon lamellar structure. Boron atom could arrange the crystal lattice by replacing carbon atom [16] and the diffusion speed of boron atom is quick in carbon layers, leaving graphitized carbon behind the propagating boron particles. Furthermore, as OYA and OTANI reported [5], molybdenum is also one of efficient catalysts for graphitization of amorphous carbon. To date, there appears to be a dearth of literatures on the catalytic graphitization of polyacrylonitrile (PAN)-based carbon fibers using Mo-B additives. Based on these findings, it can be deduced that a high graphitization of PAN-based carbon fibers can be one way to achieve with the Mo-B mixture.
In this work, the anodized PAN-based carbon fibers were directly immersed in a uniformly dispersed Mo-B sol to obtain Mo-B-coated carbon fibers. The mechanism of Mo-B catalysts induced catalytic graphitization was further discussed in terms of our findings.
2 Experimental
2.1 Raw materials
PAN-based carbon fibers are 12 k fiber tows supplied by Lanzhou Carbon Factory, China. Phosphoric acid, boric acid and ammonium dimolybdate of analytic reagent were purchased from commercial sources and used as supplied. Double distilled water was used throughout the experiments.
2.2 Sample preparation
A novel one-step pre-treatment, anodization, was used to active the PAN-based carbon fibers instead of the routine two-step pretreatment, sensitization with SnCl2 and activation with PdCl2. The PAN-based carbon fibers were activated by anodizing the fibers in 0.5 mol/L H3PO4 electrolyte for 20 min using a two-electrode configuration at a current of 0.2 A (Pt cathode). Mo-B catalysts were directly applied to the anodized PAN-based carbon fibers by immersed the fibers in a uniformly dispersed Mo-B sol for 40 h and allowed to undergo air dry. A Mo-B sol precursor was prepared by dissolving 2.0 g ammonium dimolybdate in 20 mL double distilled water. After stirring for 30 min, 1 g boric acid was added to the solution, resulting in a uniformly dispersed solution. The Mo-B-treated carbon fibers were then graphitized at 2 400 ℃ for 2 h in graphite furnace under helium atmosphere. For comparison, Mo-treated and B-treated PAN-based carbon fibers were prepared by the same method only using boric acid and ammonium dimolybdate sol, respectively.
2.3 Characterization
The surface morphology of carbon fibers was observed by a scanning electron microscope (SEM, JSM6700F, JEOL, Japan). The microstructural features were characterized using high-resolution transmission electronic microscope (HRTEM, JEM3010, JEOL, Japan). Structural changes of the graphitized carbon fibers were characterized using X-ray analysis (XRD, M21X, MAC Science Ltd., Japan) with Cu Kα radiation (l=0.154 178 nm) using silicon as a standard. 2θ values were obtained from (002) diffraction peaks. The values of the interlayer spacing (d002) and crystalline size (Lc) were calculated from (002) diffraction peak according to the method described by Bragg law and Scherrer equation [17]. Raman spectra were obtained on Renishaw system 2000 with He-Ne laser line as the excitation source and the first-order (800-2 000 cm-1) spectra were recorded. The content of element was analyzed by weighing the dried PAN-based carbon fibers before and after loading the additive.
3 Results and discussion
3.1 Surface morphology
Fig.1 shows SEM images of surface morphology of the original PAN-based carbon fibers (Fig.1(a)), anodized carbon fibers (Fig.1(b)), and Mo-B-coated carbon fibers (Fig.1(c)). Comparing Fig.1(a) with Fig.1(b), the anodized carbon fibers generate a lot of fissures and active spots on the surface of carbon fibers. The high surface area of anodized fibers facilitates the Mo-B deposition. As shown in Fig.1(c), the fiber is enwrapped by a layer of Mo-B coating after Mo-B sol immersed. The corresponding EDS spectrum shown in Fig.1(d) indicates the presence of Mo. B is not detected by EDS due to its light relative atomic mass, while the phase composition of XRD analysis shows the presence of B.
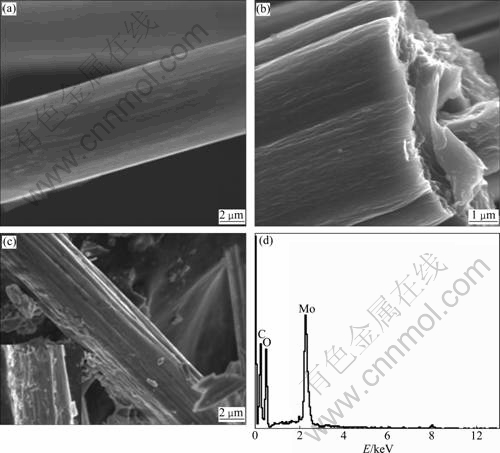
Fig.1 SEM images of PAN-based carbon fiber: (a) Original carbon fibers; (b) Anodized carbon fibers; (c) Mo-B-coated carbon fibers; (d) EDS spectrum of Mo-B-coated carbon fibers
3.2 XRD studies
The changes of the interlayer spacing (d002) and crystalline size (Lc) were analyzed by X-ray diffraction patterns, with the corresponding crystal parameters listed in Table 1. Usually, with increasing the degree of graphitization, the (002) peak shifts right, and the (002) peak profiles become sharper and more symmetrical. The interlayer spacing (d002) decreases with the increase of graphitization. Fig.2 shows XRD patterns of carbon fiber loaded without (sample a) or with B (samples b and c) after heat treatment at 2 400 ℃ for 2 h. The (002) peak shifts toward a higher value (decrease in d002) with increasing the content of B, as shown in Fig.2 (samples b and c). The highest degree of graphitization, with d002 of 0.336 7 nm and Lc of 20 nm is achieved at B content of 2.49% (sample c). In the absence of B (sample a), very little carbon was graphitized after heat treatment at 2 400 ℃, as seen in Fig.2. These results indicate that the content of 2.49% B can effectively improve the graphitization of the PAN-based carbon fibers. The content of B is obtained by weighing the dried fibers before and after loading the additive.
Table 1 Microstructure parameters of graphitized PAN-based carbon fibers at graphitization temperature of 2 400 ℃
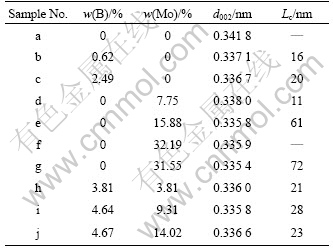
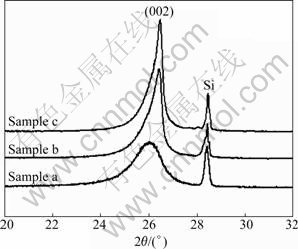
Fig.2 XRD patterns of PAN-based carbon fibers loaded with different mass fractions of B
The effect of Mo on catalytic graphitization was also investigated, as shown in Fig.3. The corresponding crystal parameters are listed in Table 1. With increasing the content of Mo from 7.75% to 15.88%, the interlayer spacing d002 decreases from 0.338 0 to 0.335 8 nm, and (002) peaks become sharper and more symmetrical as shown in Fig.3 (samples d and e). Further increasing the Mo content to 31.55%, the (002) peak shifts little but results in a decrease in the intensity of (002) peaks (samples f and g). Moreover, the high Mo content results in the appearance of a shoulder peak in the (002) peak (samples e, f and g), indicating the existence of disordered graphite structure with the ordered structure. A high content of Mo is unfavorable to the transformation from disorder carbon structure to graphite structure.
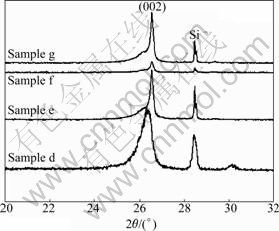
Fig.3 XRD patterns of PAN-based carbon fibers loaded with different mass fractions of Mo
The synergistic catalytic effects of Mo-B on the graphitization of the PAN-based carbon fibers were investigated, with the corresponding XRD patterns shown in Fig.4. As shown in Fig.4 (samples h and i), with increasing the content of Mo and B, the interlayer spacing d002 decreases from 0.336 0 to 0.335 8 nm, which is close to the hexagonal graphite interlayer spacing of 0.335 4 nm, and the crystallite size Lc (002) also increases from 21 to 28 nm. However, further enhancing the content of Mo to 14.02% results in a significant decrease in the intensity of the (002) peak as shown in Fig.4 (sample j). The Mo-B mixture shows much better catalytic effect in the graphitization of PAN-based fibers, and the highest graphite degree is achieved at 9.31%Mo-4.64%B. Compared with the (002) peak of the graphitized fibers using Mo (Fig.2) or B (Fig.3) as catalyst, the (002) peak profiles using Mo-B as catalysts (Fig. 4) are sharper and more symmetrical, with a smaller d002 of 0.335 8 nm and a larger Lc of 28 nm, suggesting a synergistic catalytic effect of Mo-B alloy.
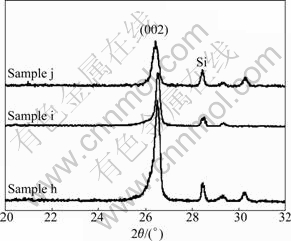
Fig.4 XRD patterns of PAN-based carbon fibers loaded with different contents of Mo and B
3.3 HRTEM image of PAN-carbon fibers
The HRTEM photograph of carbon fibers graphitized in the presence of Mo-B is shown in Fig.5, and the inset shows highly ordered stacking layers with d002 of 0.335 8 nm, indicating that graphitized crystallization is achieved in the Mo-B-loaded PAN- based carbon fibers after heat treatment at 2 400 ℃ for 2 h. These results are consistent with the values of interlayer spacing d002 and crystallite size Lc obtained from XRD patterns.
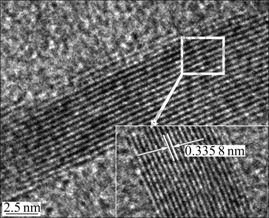
Fig.5 HRTEM image of PAN-based carbon fibers loaded with 9.31%Mo-4.64%B after heat treatment at 2 400 ℃
3.4 Raman studies
Raman spectroscopy is a powerful tool for characterizing the structures of various carbon materials. In general, carbons show mainly two Raman bands: G band of graphite at about 1 580 cm-1 related to the relative motion of sp2 bonded carbon atoms and D band at about 1 360 cm-1 corresponding to the defect-induced Raman band which is absent in the single crystal graphite. Both G and D bands are generally attributed to graphitic sp2 bonded carbon [18]. In addition to these two bands, a D′ band at around 1 620 cm-1 appears as a G-band shoulder corresponding to discontinuities in the hexagonal carbon layer. As shown in Fig.6, the intensity of G band becomes sharper, and D and D′ bands almost disappear with increase of Mo and B contents, indicating that PAN-carbon fibers with turbostratic structures are turned into perfect three-dimensional graphite. The intensity ratio of D band to G band (peak area) ID/IG changing from 0.433 to 0.342, is also an important parameter for characterizing the degree of graphitization. Based on above results, it is indicated that good catalytic graphitization can be obtained in the presence of 9.31%Mo-4.64%B.
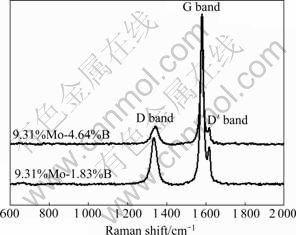
Fig.6 Raman spectra of PAN-based carbon fibers loaded with different contents of Mo and B
3.5 Mechanism of catalytic graphitization
To explore the catalytic mechanism of Mo-B dopants, the phase composition of Mo-B-doped PAN-based carbon fibers is determined with XRD as a function of different graphitization temperatures. As shown in Fig.7, in addition to graphite profile, the profiles of Mo2C and Mo2BC are also detected. However, no boron or boron carbide phase is detected. The reasons are discussed as follows. The radius of boron atom is 0.77 nm, which is very close to the radius of carbon atom (0.66 nm). Therefore, boron atom can enter the interstitial positions of the carbon lamellar structure to arrange the crystal lattice by replacing carbon atom and the diffusion speed of boron atom in carbon is quick through the lattice of the carbon [16]. In these processes, the extent of graphitization is enhanced. In the presence of Mo and B, Mo plays a significant effect and follows the well-known dissolution– precipitation mechanism [19], through the reaction of Mo with carbon to form carbides, such as Mo2BC and Mo2C, as indicated in Fig.7. The decomposition of the carbides forms graphite carbon and precipitates [5, 20].
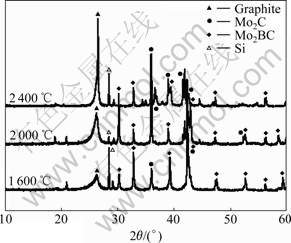
Fig.7 XRD patterns of 9.31%Mo-4.64%B loaded PAN-based carbon fibers heat-treated at different temperatures
4 Conclusions
(1) A novel method is applied to doped catalyst on PAN-based carbon fibers by immersing anodized carbon fibers in a uniformly dispersed Mo-B sol. By the proposed method, a uniform catalyst coating on the carbon fibers is achieved with a controllable composition of the dopants.
(2) In the presence of 9.31%Mo-4.64%B, the highest degree of graphitization and crystallization is observed with d002 of 0.335 8 nm and Lc (002) of 28 nm. The achieved graphitization degree in the presence of Mo-B is higher than that in the presence of single Mo or B, suggesting a synergistic catalytic effect.
(3) The catalytic mechanism of Mo follows the well-known dissolution–precipitation mechanism.
References
[1] INAGAKI M, MEYER R A. Stress graphitization [M]. New York: Chemistry and Physics of Carbon, 1999: 149-244.
[2] HU Xiao-bin, CHENG Gang, ZHAO Bin-yun, WANG Hui-ming, HU Ke-ao. Catalytic effect of dopants on microstructure and performance of MCMB derived carbon laminations [J]. Carbon, 2004, 42(2): 381-386.
[3] GARCIA-ROSALES C, ORDAS N, OYARZABAL E, ECHEBERRIA J, BALDEN M, LINDIG S. Improvement of the thermo-mechanical properties of fine grain graphite by doping with different carbides [J]. J Nucl Mater, 2002, 307/311(10): 1282-1288.
[4] QIU Hai-peng, SONG Yong-zhong, LIU Lang, ZHAI Geng-tai, SHI Jing-li. Thermal conductivity and microstructure of Ti-doped graphite [J]. Carbon, 2003, 41(5): 973-978.
[5] OYA A, OTANI S. Catalytic graphitization of carbons by various metals [J]. Carbon, 1979, 17(2): 131-137.
[6] LEE Y J, UCHIYAMA Y, RADOVIC L R. Effects of boron doping in low and high-surface-area carbon powders [J]. Carbon, 2004, 42(11): 2233-2244.
[7] PARK S H, JO S M, KIM D Y, LEE W S, KIM B C. Effects of iron catalyst on the formation of crystalline domain during carbonization of electrospun acrylic nanofiber [J]. Synth Met, 2005, 150(3): 265-270.
[8] TZENG S S. Catalytic graphitization of electroless Ni-P coated PAN-based carbon fibers [J]. Carbon, 2006, 44(10): 1986-1993.
[9] LI Fei, ZOU Xiao-ping, CHENG Jin, ZHANG Hong-dan, REN Peng-fei, WANG Mao-fa, ZHU Guang. Synthesis of carbon nanofibers by ethanol catalytic combustion technique [J]. Journal of Central South University of Technology, 2008, 15(1): 15-19.
[10] ZUO Jin-lü, ZHANG Hong-bo, HUANG Qi-zhong, XIAO Peng, XU Hui-juan. Influence of bulk density and graphitization degree on hardness of C/C composites [J]. Journal of Central South University of Technology, 2003, 34(3): 225-227. (in Chinese)
[11] WANG Hong-qiang, LI Xin-hai, GUO Hua-jun, ZHANG Bao, GUO Yong-xing. Electrochemical performance of Ag-coated mesocarbon microbeads [J]. Journal of Central South University of Technology, 2003, 34(6): 615-618. (in Chinese)
[12] RODRIGUEZ N M, BAKER R T K. Fundamental studies of the influence of boron on the graphite-oxygen reaction using in situ electron microscopy techniques [J]. J Mater Res, 1993, 8(8): 1886-1894.
[13] HOWE J Y, JONES L E. Influence of boron on structure and oxidation behavior of graphite fiber [J]. Carbon, 2004, 42(3): 461-467.
[14] WU X X, RADOVIC L R. Inhibition of catalytic oxidation of carbon/carbon composites by boron-doping [J]. Carbon, 2005, 43(8): 1768-1777.
[15] LEE Y J, RADOVIC L R. Oxidation inhibition effects of phosphorus and boron in different carbon fabrics [J]. Carbon, 2003, 41(10): 1987-1997.
[16] ZHOU Hai-hui, YU Qiang, PENG Qi-ling, WANG Hua, CHEN Jin-hua, KUANG Ya-fei. Catalytic graphitization of carbon fibers with electrodeposited Ni-B alloy coating [J]. Materials Chemistry and Physics, 2008, 110(2/3): 434-439.
[17] ZOU Lin-hua, HUANG Bai-yun, HUANG Yong, HUANG Qi-zhong, WANG Chang-an. An investigation of heterogeneity of the degree of graphitization in carbon-carbon composites [J]. Mater Chem Phys, 2003, 82(3): 654-662.
[18] WANG Y, SERRANO S, SANTIAGO-AVILES J J. Raman characterization of carbon nanofibers prepared using electrospinning [J]. Synth Met, 2003, 138(3/4): 423-427.
[19] FITZER E, KEGEL B. Reactions of carbon saturated vanadium carbide with disordered carbon (effects on catalytic graphitization) [J]. Carbon, 1968, 6(4): 433-436.
[20] QIU Hai-peng, HAN Li-jun, LIU Lang. Properties and microstructure of graphitized ZrC/C or SiC/C composites [J]. Carbon, 2005, 43(5): 1021-1025.
Foundation item: Project(2006CB600903) supported by the National Basic Research Program of China
Received date: 2009-06-02; Accepted date: 2009-10-29
Corresponding author: CAI Qing-yun, Professor; Tel: +86-731-88821848; E-mail: qycai0001@hnu.cn
(Edited by YANG You-ping)