J. Cent. South Univ. Technol. (2008) 15: 743-747
DOI: 10.1007/s11771-008-0137-1
Effect of CaO doping on corrosion resistance of Cu/(NiFe2O4-10NiO) cermet inert anode for aluminum electrolysis
LAI Yan-qing(赖延清), HUANG Li-feng(黄礼峰), TIAN Zhong-liang(田忠良),
WANG Jia-wei(王家伟), ZHANG Gang(张 刚), ZHANG Yong(张 勇)
(School of Metallurgical Science and Engineering, Central South University, Changsha 410083, China)
Abstract: The CaO-doped Cu/(NiFe2O4-10NiO) cermet inert anodes were prepared by the cold isostatic pressing-sintering process, and their corrosion resistance to Na3AlF6-K3AlF6-Al2O3 melt was studied. The results show that the relative density of 5Cu/(NiFe2O4-10NiO) cermet sintered at 1 200 ℃ increases from 82.83% to 97.63% when 2% CaO (mass fraction) is added. During the electrolysis, the relative density of cermet inert anode descends owing to the chemical dissolution of additive CaO at ceramic grain boundary, which accelerates the penetration of electrolyte. Thus, the corrosion resistance to melts of Cu/(NiFe2O4-10NiO) cermet inert anode is reduced. To improve the corrosion resistance of the cermet inert anode, the content of CaO doped should be decreased and the technology of cleaning the ceramic grain boundary should be applied.
Key words: aluminum electrolysis; Cu/(NiFe2O4-10NiO) cermet; CaO; inert anode; corrosion resistance
1 Introduction
The implementation of inert anode in aluminum reduction can decrease carbon consumption, emit oxygen and reduce the environmental pollution. And it has become a research focus. The inert anode materials for aluminum electrolysis need not only good corrosion resistance to the molten salts and thermal stability at high temperature, but also high electrical conductivity and good mechanical performance[1].
Recent studies in this field are mainly concentrated on alloy and cermet material. NiFe2O4-based cermets have been regarded as a promising inert anode for aluminum electrolysis[2-4]. LAI et al[2-3] and XI et al[4] studied their electrolysis corrosion behaviour and the electrical conductivity at high temperature, and thought the corrosion performance and the electrical conductivity must be improved. To increase the relative density and improve the mechanical property during preparation, some oxides such as CaO, ZnO, TiO2 and MnO2 were used as additives[5-6].
The results in Refs.[7-8] show that the addition of CaO can improve the mechanical properties of NiFe2O4- based cermet. But the corrosion resistance to the melts has not been studied. In this work, Cu/(NiFe2O4-10NiO) cermet inert anodes with addition of different contents of CaO were prepared by the cold isostatic pressing- sintering process, and the corrosion resistance to Na3AlF6-K3AlF6-Al2O3 melts was studied.
2 Experimental
2.1 Preparation of samples
The raw materials, Cu powder, Fe2O3, NiO and CaO were reagent grade. Cu/(NiFe2O4-10NiO) cermet inert anodes were prepared by cold isostatic pressing-sintering process. A proper amount of NiO and Fe2O3 were mixed using a ball mill and then calcined to obtain NiFe2O4-10NiO ceramic powder. Then the calcined ceramic powder was mixed again with a proper amount of Cu powder and addition of CaO by ball milling in the media containing organic dispersant. Finally, the mixed ceramic-metal powder was dried and isostatically pressed into some cylindrical blocks (d 20 mm×40 mm) at the pressure of 200 MPa[9]. The cylindrical blocks were sintered under certain temperature and atmosphere of effectively controlled oxygen partial pressure to the desired cermet samples[10].
2.2 Electrolysis tests
The electrolyte was made up of reagent grade Na3AlF6, K3AlF6 and Al2O3, technical grade AlF3. The mole ratio of (NaF+KF) to AlF3 was 1.7, and the primary crystal temperature was 890 ℃. All compositions were dried at 120 ℃ for 48 h to remove the water before use. In order to eliminate the effect of relative density on the corrosion resistant of material in the electrolytic tests, the relative densities of the samples were beyond 95%.
A sketch of the experimental cell is shown in Fig.1. The cell consisted of a graphite crucible and an alumina crucible with a hole at the bottom. A certain content of metallic aluminum was added to obtain the steady cathodic surface area before experiment, and the bottom of the alumina crucible was covered with liquid metal aluminum. During testing, the temperature was measured with Pt/Pt-10%Rh thermocouple and controlled by TCE-II programmable temperature controller, and the current and the cell voltage were supplied and monitored by a multi-purpose Potentiostat/Galvanostat (273A/10, Perkin-Elmer Instruments). Though Al2O3 was consumed incessantly and its concentration in the bath decreased, alumina sleeve would dissolve into the electrolyte and supply the consumption of Al2O3. So, Al2O3 was not added throughout the testing.
After testing, the anode was raised out of the melt while maintaining polarization state in order to avoid the metal in electrolyte being deoxidized and corroded.
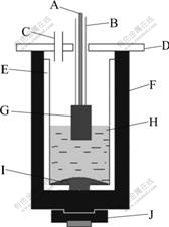
Fig.1 Sketchmap of experimental electrolysis cell: A— Stainless steel anode rod; B—Al2O3 sleeve; C—Bath withdrawing tube; D—Al2O3 board; E—Al2O3 crucible; F— Graphite crucible; G—Inert anode; H—Electrolyte; I—Metal aluminum(cathode); J—Cathodic steel pallet
2.3 Performance detection
Relative density and porosity of Cu/(NiFe2O4- 10NiO) cermet samples were tested with the paraffin method (ASTM Archimedes method C373-88 (1999))[11]. The impurity contents of samples were analyzed with X-ray fluorescense (XRF) spectroscope, and its analytical error was about 10% for the measured values below 1×10-4, 5% for the values between 1×10-4 and 1×10-3 and 3% above for the values 1×10-3[12]. The microstructures of the anodes were analyzed with JSM- 6360LV scanning electron microscope and EDX- GENESIS energy dispersive spectrometer.
3 Results and discussion
3.1 Effect of CaO content on relative density of cermets
The relative densities of the CaO-doped Cu/ (NiFe2O4-10NiO) cermet inert anodes sintered at different temperatures are listed in Table 1. The data show that the relative density of Cu/(NiFe2O4-10NiO) cermet inert anodes sintered at 1 200 ℃ increases with increasing content of CaO-doped. The relative density of Cu/(NiFe2O4-10NiO) doped with 2%(mass fraction) CaO is 97.63%, which is close to that of CaO-undoped material sinter at 1 250 ℃ (96.70%). For the 2.0%CaO- Cu/(NiFe2O4-10NiO) cermet, when the mass fraction of metal Cu increases from 5% to 17%, the relative densities are approximate, being 97.63% and 95.05% respectively. Therefore, CaO is a good sintering agent for Cu/(NiFe2O4-10NiO) cermet. It can decrease sintering temperature and prevent the metal Cu from outflowing while the relative density is equivalent.
Based on the thermodynamics calculation, it can be concluded that CaO can react with Fe2O3 at about 1 000 ℃ to generate Ca2Fe2O5 which is in liquid phase below 1 200 ℃[13-14]. So the CaO-doped sample achieves densification by means of dissolution and separation of this liquid phase, which is used as transferred carrier to accelerate mass mobility and viscous flow. Although the metal Cu is in liquid phase at the sintering temperature, its wettability with the oxide ceramic is poor, thus leading to the spill glomeration, which is harmful to improving the relative density of the materials.
3.2 Effect of CaO content on impurity concentration in bath
Fig.2 shows the concentration change of Fe, Ni, Cu and Ca vs time for the cermet inert anodes IA-1, IA-3 and IA-4. For the 5Cu/(NiFe2O4-10NiO) cermet inert anode, it takes about 6 h for the concentration of impurity to reach steady-state, and the concentrations of impurities of Fe, Ni, Cu and Ca are 146.3×10-6, 34.3×10-6, 67.7×10-6 and 193.5×10-6 respectively after testing. Compared with the results mentioned by DEYOUNG (bath ratio is 1.1, 6.5% Al2O3, 1 000 ℃)[15], the concentrations of impurities Ni and Fe in this work are far less than their solubilities (90×10-6 for impurity Ni, 580×10-6 for impurity Fe). But the concentration of impurities in electrolyte is very unstable for the cermet inert anode doped with 2% CaO. After testing, the concentrations of impurities in bath for inert anodes IA-3 and IA-4 are respectively: Fe 331.5×10-6 and 184.7×10-6; Ni 207.1×10-6 and 94.4×10-6; Cu 174.2×10-6 and 1 337.9×10-6; Ca 503.2×10-6 and 649.8×10-6, which are more than those of the inert anode IA-1.
Table 1 Relative densities of Cu/(NiFe2O4-10NiO) cermets

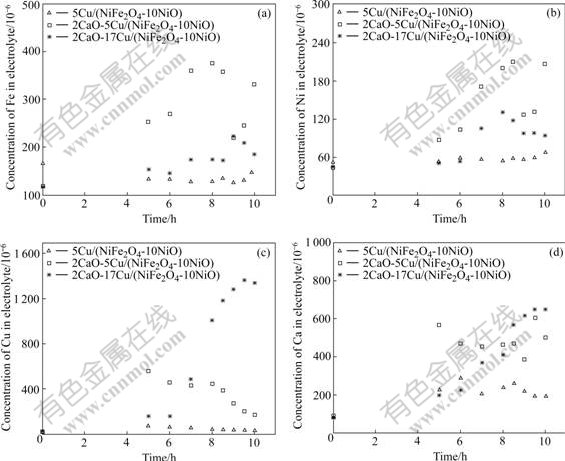
Fig.2 Concentration of impurities as function of time in electrolyte: (a) Fe; (b) Ni; (c) Cu; (d) Ca
Therefore, from the concentration of impurities in the bath during electrolysis, it indicates that the addition of CaO as doping agent to Cu/(NiFe2O4-10NiO) cermet inert anode will decrease their corrosion resistance to the melts.
3.3 Morphological analysis of cermet inert anodes after electrolysis
The ceramic inert anodes after electrolysis are shown in Fig.3. It can be seen that some parts of inert anodes IA-3 and IA-4 (besides anode IA-1) swell from the anode substrate and there is khaki matter on the surface, which is approved to be some phases such as NiFe2O4 and NiF2, AlF3 by XRD.

Fig.3 Surface shapes of different inert anodes after electrolysis: (a) IA-1; (b) IA-3; (c) IA-4
The SEM images and EDS patterns of the cermet inert anodes after electrolysis are shown in Figs.4 and 5, respectively. From Fig.4(a) and Fig.5(a), the metallic phase Cu for 5Cu/(NiFe2O4-10NiO) cermet inert anode corrodes evenly in ceramic phase, and the electrolyte does not penetrate into the inert anode, which exhibits good corrosion resistance to the molten cryolite. However, from Figs.4(b), (c) and Fig.5(b), it is very obvious that the metallic phase Cu leaks seriously for the cermet inert anodes IA-3 and IA-4, which are doped with 2% CaO. There is clear corrosive layer on the surface of the inert anodes studied, and the electrolyte penetrates into the inert anode, which shows poor corrosion resistance to the melt.
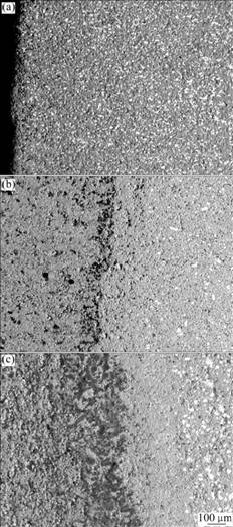
Fig.4 SEM images of different inert anodes after electrolysis: (a) IA-1; (b) IA-3; (c) IA-4
Therefore, from the surface shapes and microstructure of inert anodes after electrolysis, it indicates that the addition of CaO to Cu/(NiFe2O4-10NiO) cermet inert anode is not favorable for improving the corrosion resistance.
The results in Ref.[13] indicate that CaO added to
Cu/(NiFe2O4-10NiO) might exist in both ceramic matrix and the grain boundary. For the former, there is a possible reaction during electrolysis:
6CaO(s)+4AlF3(s)=6CaF2(s)+3O2(g)+4Al(l) (1)
Although the additive CaO is advantageous to improving the relative density of Cu/(NiFe2O4-10NiO), lots of holes and pores are left because of the reaction of CaO with electrolyte existing at the grain boundary during electrolysis. Thus, the relative density of the cermet inert anode decreases rapidly, which aggravates the corrosion of electrolyte penetration and makes the inert anode swell. So, while making full use of the function of doping agent, the measures must be taken to reduce the content of CaO and clean the ceramic grain boundary, which can avoid CaO or its reaction product concentrating at the grain boundary, and restrains the negative effect of CaO on the corrosion resistance of cermet inert anodes.
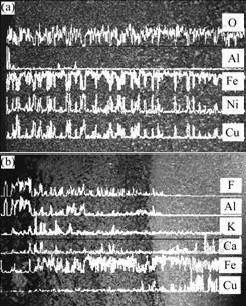
Fig.5 EDS patterns of different inert anodes after electrolysis: (a) IA-1; (b) IA-3
4 Conclusions
1) The addition of CaO to 5Cu/(NiFe2O4-10NiO) cermet is advantageous to improving the relative density because of the forming of low melting point compound Ca2Fe2O5. The relative density will increase from 82.83% to 97.63% if 2.0% CaO is added to 5Cu/ (NiFe2O4-10NiO) cermet at 1 200 ℃.
2) During electrolysis, the concentration of Cu/ (NiFe2O4-10NiO) inert anode constituents in electrolyte increases with increasing CaO content. In melt Na3AlF6-K3AlF6-Al2O3 at 900 ℃, the concentrations of Fe, Ni, Cu and Ca are 146.3×10-6, 34.3×10-6, 67.7×10-6 and 193.5×10-6 respectively for 5Cu/(NiFe2O4- 10NiO) cermet inert anode after electrolysis for 10 h. However, the corresponding values are 331.5×10-6, 207.1×10-6, 174.2×10-6 and 503.2×10-6 respectively for the inert anode doped with 2% CaO.
3) CaO or Ca2Fe2O5 existing at the grain boundary of cermet induces anode constituents running-off and lots of holes are formed. The electrolyte penetration accelerates, inert anodes swell and the corrosion resistance decreases. The measures that can reduce the CaO dosage and clean the ceramic grain boundary must be taken to exert the function of CaO sintering agent and improve the corrosion resistance.
References
[1] LIU Ye-xiang. Advance on the research and development of inert anode and wettable cathode in the aluminum electrolysis [J]. Light Metals, 2001(5): 26-29. (in Chinese)
[2] LAI Yan-qing, QIN Qing-wei, DUAN Hua-nan, LI Jie, LIU Ye-xiang. Materials fabrication and corrosion behavior of NiFe2O4 cermet inert anode [J]. Journal of Central South University of Technology: Natural Science, 2004, 35(6): 885-890. (in Chinese)
[3] TIAN Zhong-liang, LAI Yan-qing, LI Jie, LIU Ye-xiang. Electrical conductivity of Cu/(10NiO-NiFe2O4) cermet inert anode for aluminum electrolysis [J]. Journal of Central South University of Technology, 2007, 14(5): 643-646.
[4] XI Jin-hui, YAO Guang-chun, LIU Yi-han, ZHANG Xiao-ming. Electrolysis corrosion behaviour of NiFe2O4-based cermet inert anode [J]. The Chinese Journal of Process Engineering, 2006, 6(5): 758-762. (in Chinese)
[5] JOHNSON D W, VOGEL E M, GHATE B B. Recent progress on mechanical properties of ferrites [C]// Proceedings of the Third International Conference on Ferrite. Tokyo: Reidel Publishing Company, 1980: 285-291.
[6] GHOSH A, DAS S K, BISWAS J R, TRIPATHI H S, BANERJEE G. The effect of ZnO addition on the densification and properties of magnesium aluminate spinel [J]. Ceramics International, 2000, 26(6): 605-608.
[7] LI Jie, ZHANG Gang, LAI Yan-qing, ZHANG Yong, TIAN Zhong-liang. Densification and sintering dynamics of 10NiO-NiFe2O4 doped CaO [J]. Journal of Central South University of Technology, 2007, 14(5): 629-632.
[8] LAI Yan-qing, ZHANG Yong, ZHANG Gang, LI Jie, HE Yue-hui, HUANG Bai-yun, LIU Ye-xiang. Effect of CaO doping on densification of NiFe2O4-10NiO composite ceramics [J]. The Chinese Journal of Nonferrous Metals, 2006, 16(8): 1355-1360. (in Chinese)
[9] LAI Yan-qing, SUN Xiao-gang, LI Jie, DUAN Hua-nan, LI Xin-zheng, ZHANG Gang, TIAN Zhong-liang. Densification of Ni-NiFe2O4 cermets for aluminum electrolysis [J]. Trans Nonferrous Met Soc China, 2004, 14(3): 666-670.
[10] ZHANG Gang, LI Jie, LAI Yan-qing, SUN Xiao-gang. Effect of sintering atmosphere on the relative density and conductive properties of Ni-Fe spinel ceramics [J]. Journal of Functional Materials, 2006, 36(11): 1709-1711. (in Chinese)
[11] QING Qing-wei, LAI Yan-qing, XIAO Jin, LI Jie, LIU Ye-xiang. Preliminary testing of NiFe2O4-NiO as ceramic matrix of cermet inert anode in aluminum electrolysis [J]. Trans Nonferrous Met Soc China, 2003, 13(5): 1208-1212.
[12] OLSEN E, THONSTAD J. Nickel ferrite as inert anodes in aluminium electrolysis (I): Material fabrication and preliminary testing [J]. Journal of Applied Electrochemistry, 1999, 29: 293-299.
[13] ZHANG Gang, LI Jie, LAI Yan-qing, ZHANG Yong, TIAN Zhong-liang. Effect of CaO addition on the densification and conductivity of 10NiO-NiFe2O4 composite ceramics [J]. Journal of Materials and Metallurgy, 2007, 6(3): 214-219. (in Chinese)
[14] JUNZO T, TOYOHIKO I. Effect of additives on magnetization of ferrites [C]// HIROSHI W F. Proceedings of the Third International Conference on Ferrites. Tokyo: Reidel Publishing Company, 1980: 178-181.
[15] DEYOUNG D H. Solubilities of oxides for inert anodes in cryolite-based melts [C]// Light Metals. Warrendale: TMS, 1986: 299-307.
Foundation item: Project(2005CB623703) supported by the Major State Basic Research and Development Program of China; Project(2008AA030503) supported by Hi-Tech Research and Development Program of China
Received date: 2008-07-08; Accepted date: 2008-09-12
Corresponding author: LAI Yan-qing, Professor, PhD; Tel: +86-731-8876454; E-mail: 13975808172@126.com
(Edited by CHEN Wei-ping)