
Effects of microalloying on grain refinement behaviors and hardness properties of wedge-shaped Al-Mg-Mn castings
LIU En-ke(刘恩克), YANG Fu-bao(杨福宝), XU Jun(徐骏), SHI Li-kai(石力开)
National Engineering and Technology Research Center for Nonferrous Metal Matrix Composites,
General Research Institute for Nonferrous Metals, Beijing 100088, China
Received 15 July 2007; accepted 10 September 2007
Abstract: The effects of microalloying elements Ti, Sc, Zr and Er on grain refinement behaviors and hardness properties of wedge-shaped Al-Mg-Mn alloy castings were investigated. The results indicate that alloys containing Sc and Zr can remarkably reduce the grain sizes of Al-Mg-Mn castings. Combination of Sc, Zr and Er can completely eliminate the columnar dendritic grains and further obtain refined grains with nondendritic sub-structure; the whole wedge-shaped cross-section of the casting consequently exhibits more homogeneous cast structures instead of the typical tri-crystal region structures. Large amounts of Al3Sc-based intermetallic compound particles, such as Al3(Sc1-x, Zrx), Al3(Sc1-x, Tix), Al3(Sc1-x-y, Zrx, Tiy) and Al3(Sc1-x-y, Zrx, Ery) are present in the microalloyed alloys, resulting from their numerously forming in high-temperature melt before solidification. These phases have the same L12-type crystal structure to Al3Sc phase as well as smaller misfits with the primary α(Al) grains, which leads to more efficient epitaxial growth for α(Al) grains on all crystal planes of these composite phases. The experimental alloys have been hardened in different levels and, show the low susceptibilities of hardness change with varying cooling rate. The high hardness of the castings are caused by grain-refined strengthening and solid solution strengthening.
Key words: Al-Mg-Mn alloy; filler metal; wedge-shaped casting; grain-refined strengthening; solid solution strengthening
1 Introduction
A refined, equiaxed and homogeneous microstructure may give aluminum alloy casting excellent mechanical property, low hot cracking, good weldability and high corrosion resistance[1]. The Al-Mg series alloys have good integrated properties but their medium strength cannot give enough satisfaction for some applications, especially as the filler metals for industrial welding. It is necessary to develop new filler metals with both higher strength and better ductility, as well as lower hot cracking and stress corrosion susceptibilities. An important method to synchronously solve these issues may be the grain refinement of the alloys[2-3]. In this paper, we principally target the grain refinement behaviors under microalloying of the castings, also since the solidification behaviors will have great influence on the quality of welds.
There are many conventional refiners based on Al-Ti, Al-Ti-B, Al-Ti-C and Al-Zr systems for aluminum alloys[4-6]. It has been reported by DRITS et al[7] that Sc is the most efficient refiner in aluminum alloy refinement. When Sc element is alloyed with aluminum, a Al3Sc phase will form in Al-Sc system, and it has a cubic L12-type crystal structure with a lattice parameter of 0.410 4 nm, which leads to a quite small misfit with b.c.c α(Al) (aAl=0.404 nm, δa=1.58%). This enables α(Al) grains to epitaxially grow on all the Al3Sc crystal planes conveniently to finally form a refined, equiaxed cast microstructure. However, to obtain this remarkable grain-refining effect, the content of Sc should exceed the eutectic composition (0.55%) to produce primary Al3Sc phase particles. The subsequent studies[8-9] revealed that joint addition of Sc and Zr can improve both the grain refinement effect and thermal stability of the aluminum alloys such as Al-Mg, Al-Zn-Mg, and Al-Mg-Li systems. Zr can replace partial Sc atoms of Al3Sc to form Al3(Sc1-x, Zrx) composite phase, which not only has the same crystal structure as Al3Sc but further reduces the α(Al)/Al3Sc misfit. The more significant matter was that adding Zr with proper content into the Sc-containing alloys would lower the critical concentration for grain refinement effect of Sc that works with hypereutectic composition[10]. HARADA et al[11] have reported that the lattice parameter of Al3(Sc1-x, Zrx) decreases linearly with increasing Zr content, when x reaches 0.5 the α(Al)/Al3(Sc1-x, Zrx) misfit reduces to 1.04% while the tetragonal D023 phase with Al3Zr composition begins to appear in the studied alloys. ELAGIN et al[8] have reported that Ti can also dissolve in L12-type Al3Sc phase with the maximal substitution up to 50% of Sc, which decreases the lattice parameter of the Al3(Sc1-x, Tix) phase.
In recent years, Er has been studied in aluminum alloy refinement to substitute the expensive Sc[12-13].
Just as Al3Sc phase, Al3Er phase also has the L12-type crystal structure. Although the lattice parameter a is 0.4215 nm and the α(Al)/Al3Er misfit is larger than that of α(Al)/Al3Sc, the cost of Er is much lower than Sc. This is why it is adopted in this work.
This article includes a brief review above of the grain refinement of Sc, Er and the joint alloying, followed by a description of the cast structures and a discussion of the mechanisms for the grain refinement and hardness of the alloys.
2 Experimental
The starting materials used in the preparation of the experimental alloys are high purity Al (99.99%), high purity Mg (99.99%), high purity Zn (99.9%) and Al-10%Mn, Al-4.77%Zr, Al-5.5%Ti, Al-2.12%Sc, Al-10%Er master alloys (All compositions are given in mass fraction if not mentioned otherwise). The alloys were melted in a vacuum induction furnace. The furnace with starting materials was preheated to 400 ℃ and then charged in argon gas with the pressure of 0.08 MPa. The molten melt was cooled down to 730 ℃ and poured into a wedge-shaped copper mould to produce a casting, as shown in Fig.1. The chemical compositions determined by inductively coupled plasma atomic emission spectrometry (ICP-AES) are listed in Table 1. The samples were taken from the wedge tip 75 mm away along the centre line of each wedge-shaped casting. These specimens were polished and etched with standard Keller’s reagent (2 mL HF, 3 mL HCl, 5 mL HNO3 and 190 mL distilled water) combined with H3PO4 solution (10%, volume fraction). Microstructural characterization was performed by optical and scanning electron microscopy (SEM, S-4800, Hitachi Inc). Microchemical information was obtained by energy dispersive X-ray spectroscopy analysis(EDXS) and line-scan attached to SEM. And phase structures were analyzed by X-ray diffraction analysis (XRD, X′Pert PRO MPD, PANalytical Inc) using Cu Kα radiation.
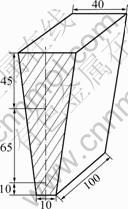
Fig.1 Schematic diagram of wedge-shaped casting (All dimensions given in mm)
The grain sizes were measured using Micro-image Analysis and Process System (MIAPS, Metal version) from the specimen center and along the through-thickness direction, respectively. And the macrohardness of the castings was measured along the center line on polished wedge cross-section using a Brinell’s machine (HD-1875) at room temperature. The Brinell ball a the diameter of 2.5 mm, load of 625 N and 20 s holding period for the load were adopted in this work.
3 Results and discussion
3.1 Cast structures and grain refinement of experi- mental alloys
Optical micrographs of the specimens are shown in Fig.2. The four alloys were refined in different levels, especially for alloys No.2 and No.4 added Sc and Zr, their mean grain sizes being about 52 and 43 μm (Figs.2(b) and (d)). From Figs.2(a) and (c), it is observed that joint addition of Sc and Ti could lead to about 120 and 100 μm mean grain sizes, respectively, and Er element could further refine the grains. Dramatically,there is no dendritic substructure inside the refined cast grains of alloy No.4 (Fig.2(d)), while typical dendritic sub- structures inside the refined cast grains of all the other alloys are there. The refined cast grains of alloy No.4 are highly regular and the grain boundaries are fine and straight compared with the other alloys, which means little segregation or enrichment of other phases along the grain boundaries.
Table 1 Chemical compositions of experimental alloys (mass fraction, %)


Fig.2 Optical micrographs of structural evolution of as-cast Al-Mg-Mn alloys with different alloying elements: (a) Alloy No.1, 0.058%Ti+0.18%Sc; (b) Alloy No.2, 0.068%Ti+0.16%Sc+0.10%Zr; (c) Alloy No.3, 0.060%Ti+0.19%Sc+0.37%Er; (d) Alloy No.4, 0.058%Ti+ 0.18%Sc+0.10%Zr+0.18%Er
In alloys No.1, 2 and 3, the columnar dendritic grains were found at two sides of the center line of each wedge-shaped casting, forming a V-shaped macrostruc- ture. These columnar dendritic grains usually nucleate near the mould wall and grow into interior of casting along the heat transfer direction during alloy solidification. Fig.3 shows the grain sizes of transverse cross-sections of wedge-shaped castings for alloys No.2 and 4. From Fig.3, we can quantificationally see that alloy No.2 still remains the refined grain region, columnar grain region and equiaxed grain region, corresponding to the typical tri-crystal region structures. In alloy No.4, in contrast, there is a complete absence of columnar dendritic grain, leaving much more homogeneous spherical grains throughout the whole cross-section with thin refined grain region at edges of castings due to the high cooling rate. The grain sizes in the three regions of alloy No.2 vary tempestuously, whereas the grains of alloy No.4 basically maintain a well-proportioned size.
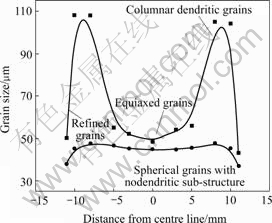
Fig.3 Variations of grain size in transverse cross-sections of wedge-shaped castings for alloys No.2 and 4
3.2 Formation of composite particles for grain- refining during solidification
From Section 3.1, it is seen that joint microalloying of lower Sc with Ti, Zr, and Er could result in refined, uniform cast structures in different levels. Multifarious intermetallic compound particles are present inside some grains or at the grain boundaries. These particles are highly faceted, in the forms of triangle, square, star, pentagon, regular hexagon, etc. At the same time, it is apparent that all of them basically have a core-shell structure. In Fig.4, EDXS line-scan displays the element distribution of the core-shell structure found in alloy No.2. The particle is exceptionally rich in Sc, Zr and Ti in contrast to the matrix. As a whole, the intensities of Sc and Zr in the shell are higher than those in the core and the intensity of Mg in the shell is lower, while the intensity of Ti keeps the same in both the shell and core. Compared with Sc, the intensity of Zr is always low, close to the half intensity of Sc. Moreover, given careful observation, the sharp lack of the three elements in the core/shell interfaces could be discovered from the line-scan curve. Fig.5 shows the EDXS analysis of the core area framed in Fig.4 and the chemical composition of the core is listed in Table 2. It is observed that the atom ratio of (Zr+Ti) to Sc is less than 1?1 and the richment of Mg atoms in the core relative to the shell was further confirmed. In the alloys, we have still found these particles are all the Al3Sc-based particles in which Ti, Zr, Er or one or two of them is dissolved. And it is gratifying that, in almost all of the particles, the total compositions (in mole fraction) of other alloying elements together always come near but don’t exceed the composition of Sc. These results suggest that Sc atoms in Al3Sc phase are jointly replaced by Zr, Ti or Er atoms with scale of no more than 50%, which means the lower misfits of the particles with α(Al) grains. The X-ray diffraction analysis was applied to identify the phase structures of these particles (Fig.6). Due to the low volume fraction (fineness and deconcentration) of these phases, their Bragg peaks are very weak. In Fig.6, Al3(Sc, X) (X=Ti, Zr, Er or one or two of them) phases labeled are the Al3Sc-based substitutional solid solutions[10]. The information of these Al3(Sc, X) phases are unavailable in X-ray diffraction analysis database, and the known information about them is that their misfits with α(Al) are lower than that of Al3Sc phase[11, 14]. In the X-ray diffraction analysis, a phase Al0.968Sc0.032 is found instead of Al3Sc, and this phase has the lattice parameter of 0.406 5 nm, much closer to the α(Al) (0.404 nm) than Al3Sc (0.410 4 nm). However, the existence of Al0.968Sc0.032 phase in the alloys is impossible when the Ti, Zr and Er are present. In addition, the microchemical compositions of the particles found in the alloys indicate that almost all of the particles contain second or third element besides Al and Sc. In some particles that only contain Al and Sc, the concentration of Sc is much higher than that in Al0.968Sc0.032 phase. Therefore, the Bragg peaks are identified as the information of Al3(Sc, X) phases instead of Al3Sc phase, and it can be further supposed that the X-ray diffraction patterns of Al3(Sc, X) phases evolve with increasing alloying element concentrations. Al3Er and Al3(Er1-x, Tix) phases in alloys No.3 and 4 are also found by X-ray diffraction analysis, which also contribute to the nucleation of α(Al) grains.
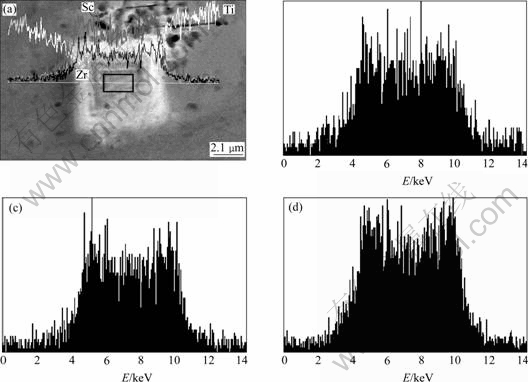
Fig.4 EDXS line-scan of element distribution for particle with core-shell structure: (a) SEM micrograph; (b) Ti element distribution; (c) Zr element distribution; (d) Sc element distribution
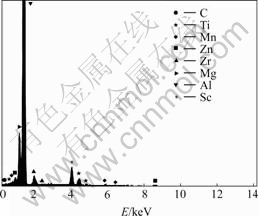
Fig.5 EDXS analysis of core area framed in Fig.4
Table 2 Chemical composition of core area
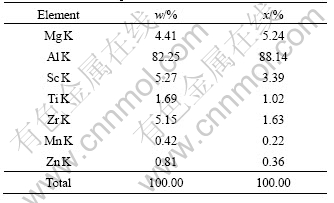

Fig.6 XRD patterns of specimens taken from wedge tip 75 mm away, corresponding to ones of Fig.2: (a) Alloy No.2, 0.068%Ti+0.16%Sc+0.10%Zr; (b) Alloy No.4, 0.058%Ti+ 0.18%Sc+0.10%Zr+0.18%Er
We can thus believe that these primary intermetallic compound particles play an essential role of grain refinement. When jointly adding of Sc with other elements with the lower concentrations of them, as expected, the Al3(Sc, X) intermetallic compound particles formed at higher temperature as the first phases in the melt. A mass of tiny and more coherent dispersoids offered enough nuclei of heterogeneous nucleation of α(Al) grains during solidification. The α(Al) grains grew outwards and came into collision with each other before the planar and spherical solid/liquid interfaces of the small initial grains lost their stability, thus the uniform grains with nondendritic sub-structure formed[15]. Simultaneously, the substitution would allow Sc to form more Al3(Sc, X) particles, which may be the reason why joint additions would reduce the critical concentration for grain-refinement effect of Sc used alone.
We can also observe Al3Mg2, (Al,Zn)49Mg32 and Al6Mn phases in the alloys. Furthermore, a new phase Al20Ti2Er aggregating at grain boundaries in alloys No.3 and 4 were found. These phases will be discussed in our further work.
3.3 Hardness properties and strengthening analysis
Fig.7 shows the Brinell hardness of the experimental alloys. We can clearly see that the hardness increases with decreasing grain size for different castings, and increases with the minishing distance from the wedge tip for each casting. Note that each hardness at 75 mm away from the tip corresponds to the grain structure of specimens shown in Fig.2. The wedge copper mould offered increasing cooling rate from top to tip of the wedge, and the grains were sequentially refined to an increasing extent. Grain refinement can prolifically manifold the grain boundaries, which act as obstacles to the continuous motion in the matrix of dislocations and prevent the propagating of micro-cracks[2], eventually heightening the hardness of the castings. This is the typical grain-refined strengthening. The grain size dependence of yield strength can be described by the Hall-Petch relation, σs=σ0+Kd -0.5 (K is a constant and d is the mean grain size). In grain deforming process, resistance of plastic yield is related to the maximum slip band length, while the maximum slip band length is determined by the grain size. Small grain size would thus offer high resistance of plastic yield, which generally corresponds to the hardness of alloys. From Fig.7, it is still observed that the hardness varies unsharply from top to tip of the wedge. This can be attributed to a large number of grains nucleating in the whole melt after poured into the wedge mould, while the rapid solidification contributes little to grain refinement under the circumstances.
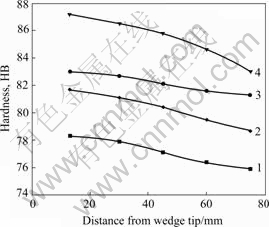
Fig.7 Plot of Brinell hardness vs distance from wedge tip for experimental alloys
The grain refinement also weakens the micro- segregation of the Mg and other elements at the grain boundaries[16], including the disappearance of Al3Mg2 phase (Figs.2(d) and 6(b)). The solute redistribution still occurs at the solute boundary layer when the small grains grow, but the microsegregation could be fainter relative to the large, irregular, unrefined grains with dendritic substructures. This should enable more Mg atoms to dissolve in α(Al) solid solution and sequentially result in the solution strengthening for the castings[17].
The solution strengthening can improve the strength, while the grain-refined strengthening is regarded as the unique method of giving great contribution to the improvements in both strength and ductility of materials.
4 Conclusions
1) The joint microalloying of Sc, Ti, Zr and Er can significantly refine the grains of Al-Mg-Mn alloy, leading to very uniform cast structures for the wedge-shaped castings. The refinement effect of Sc and Zr combination (with Ti) is more prominent than that of Sc and Er combination (with Ti), while the combination of Sc, Zr and Er (with Ti) can completely eliminate the columnar dendritic grains and obtain refined spherical grains with nondendritic sub-structure.
2) The microalloying elements Ti, Zr, and Er can dissolve into the Al3Sc phase to form Al3Sc-based substitutional solid solutions Al3(Sc, X) particles in the melt and further lower the misfits of Al3Sc phase with α(Al) matrix. These fine, more coherent particles are the excellent nuclei of heterogeneous nucleation for α(Al) grains.
3) The hardness of the refined Al-Mg-Mn castings are improved in different levels, and the hardening mechanisms are grain-refinement strengthening and solid solution strengthening, all mainly caused by grain refining. In addition, the castings have the low susceptibilities of hardness change along the centre line of each casting, corresponding to varying cooling rate.
References
[1] FLEMINGS M C. Solidification processing [M]. New York: McGrawHill, 1974.
[2] EASTON M, GRANDFIELD J, STJOHN D, RINDERER B. The effect of grain refinement and cooling rate on the hot tearing of wrought aluminium alloys [J]. Materials Science Forum, 2006, 519/521: 1675-1680.
[3] LATHABAI S, LLOYD P G. The effect of scandium on the microstructure, mechanical properties and weldability of a cast Al-Mg alloy [J]. Acta Materialia, 2002, 50(17): 4275-4292.
[4] JOHNSSON M, BACKERUD L, SIGWORTH G K. Study of the mechanism of grain-refinement of aluminum after additions of Ti-containing and B-containing master alloys [J]. Metallurgical Transactions A, 1993, 24(2): 481-491.
[5] KASHYAP K T, CHANDRASHEKAR T. Effects and mechanisms of grain refinement in aluminium alloys [J]. Bulletin of Materials Science, 2001, 24(4): 345-353.
[6] MURTY B S, KORI S A, CHAKRABORTY M. Grain refinement of aluminium and its alloys by heterogeneous nucleation and alloying [J]. International Materials Reviews, 2002, 47(1): 3-29.
[7] DRITS M E, TURKINA N I, KANADAR E S. Rare-earth metals in nonferrous alloys [N]. Nauka, Moscow, 1975. (in Russian)
[8] ELAGIN V I, ZAKHAROV V V, ROSTOVA T D. Scandium-alloyed aluminum alloys [J]. Metallovedenie I Termicheskaya Obrabotka Metallov, 1992: 24-28.
[9] ZAKHAROV V V. Stability of the solid solution of scandium in aluminum [J]. Metal Science and Heat Treatment, 1997, 39(2): 61-66.
[10] DAVYDOV V G, ELAGIN V I, ZAKHAROV V V, ROSTOVAL D. Alloying aluminum alloys with scandium and zirconium additives [J]. Metal Science and Heat Treatment, 1996, 38(8): 347-352.
[11] HARADA Y, DUNAND D C. Microstructure of Al3Sc with ternary transition-metal additions [J]. Materials Science and Engineering A, 2002, 329/331: 686-695.
[12] GUO Fu-xue, NIE Zuo-ren, JIN Tou-nan, YANG Jun-jun, FU Jing-bo, YIN Zhi-min. Effects of trace erbium on casting microstructure of LF-3 Al-alloy[J]. Journal of the Chinese Rare Earth Society, 2002, 20(2): 143-145.
[13] YU Sheng-wen, WANG Wei, YANG. Jun-jun, ZOU Jing-xia, NIE Zuo-ren. Thermodynamic calculation and precipitation behavior of Al3Er phase in Al-5Mg-Er alloy [J]. Journal of the Chinese Rare Earth Society, 2006, 24(4): 470-474.
[14] CLOUET E, LAE L, EPICIER T, LEFEBVRE W, NASTAR M, DESCHAMPS A. Complex precipitation pathways in multicomponent alloys [J]. Nature Materials, 2006, 5(6): 482-488.
[15] MARTINEZ R A, KARMA A, FLEMINGS M C. Spheroidal particle stability in semisolid processing [J]. Metallurgical and Materials Transactions A, 2006, 37(9): 2807-2815.
[16] NORMAN A F, PRANGNELL P B, MEWEN R S. The solidification behaviour of dilute aluminium-scandium alloys [J]. Acta Materialia, 1998, 46(16): 5715-5732.
[17] RYEN ?, NIJS O, SJ?LANDER E, HOLMEDAL B, EKSTR?M H, NES E. Strengthening mechanism in solid solution Aluminum alloys [J]. Metallurgical and Materials Transactions A, 2006, 37(6).
Corresponding author: LIU En-ke; Tel: +86-10-82241229; E-mail: encke@126.com
(Edited by PENG Chao-qun)