
Sphericizing metal powders by mechanical means
WANG Fu-xiang(王富祥), GAI Guo-sheng(盖国胜), YANG Yu-fen(杨玉芬)
Key Laboratory for Advanced Materials of Ministry of Education, Department of Materials Science and Engineering, Tsinghua University, Beijing 100084, China
Received 10 April 2006; accepted 25 April 2006
Abstract: A dry mechanical surface treatment was described, in which irregularly shaped metal powders were impacted and sphericized by using high speed airflow impact method particles composite system(PCS). The optimum technological parameters for the metal powders processed were determined according to the treatment effect under different conditions. The results show that the irregularly shaped metal powders are impacted into dense spherical particles, the bulk density and tap density of the metal powders increase noticeably. The combination property of metal powders is improved greatly.
Key words: metal powders; particles composite system; spherical particles; powder properties
1 Introduction
Powder is an important industry raw material. With the development of powder application, powder performance has been a major concern in particulate materials, which not only demands lower impurity content, finer particle diameter, and stricter size distribution, but also demands certain particle appearance. Particle appearance, which closely relates to particle property, exerts an important influence on many properties of particle swarm, for examples, specific surface area, fluidity, adhesive power, chemical activity, and so on. The spherical metal or alloy particles have good fluidity and isotropy, high bulk density, small friction coefficient, and great particle intensity[1-3], so they were widely used in porosint preparation, thermal spraying, powder metallurgy, injection molding technology, etc[4]. The porosint made of spherical tungsten powder has more homogeneous pore, and air permeability of the product can be controlled easily. The spherical metal or alloy particles, which have good fluidity, are convenient to thermal spraying. So the spraying layer is more symmetrical and homogeneous. In powder metallurgy, excellent size control of the pressed green compact made by spherical metal or alloy powders can be easily achieved repeatedly because of high green density and homogeneous shrinkage of the molding made of the spherical particles. So, preparing spherical metal or alloy particles is very important to enhance the industry value and economy value of the powder, and expand its application area.
2 Experimental
The raw powders used in the experiment were commercial normal electrolytic copper powders, which was produced by Gripm Advanced Materials Co. Ltd. The method used was a dry impact blending method particles composite system, which is the method used to form microparticles into spherical shapes by causing rotary impact as a result of a high-speed air flow in a ring-shaped impact chamber. Fig.1 presents schematic diagram of PCS basic functions. It was operated at rotation speed of 2 000-8 000 r/min at temperature range of 45-75 ℃. Raw electrolytic copper powders were put into the equipment in 200 g batches. The treatment time was 0–15 min, since it is understood that the properties of treated cement remain unchanged after more than 15 min of treatment[5,6]. Fig.2 shows the schematic diagram of the PCS apparatus.
Particle size distributions were measured by a laser scattering particle size distribution analyzer (BT-9300H, Dandong, China). About 0.1 g sample powder was put in 100 mL water and underwent dispersion treatment by an ultrasonic dispersion unit for about 5 min. Bulk density and tap density of electrolytic copper powders were measured by BT-1000 powder characteristic test apparatus. The size distribution and surface morphology of particles were observed by scanning electron microscopy (SEM).
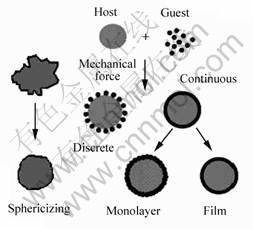
Fig.1 Schematic diagram of PCS basic functions
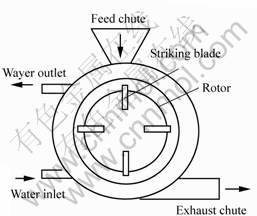
Fig.2 Schematic diagram of PCS apparatus
3 Results and discussion
Choosing appropriate matter (excellent plasticity) and suitable technological conditions (such as rotor speed, processing time, inventory rating.) is the key factor to improve particle properties. The technological parameters such as rotor speed, processing time, inventory rating, should be considered synthetically. In the appropriate PCS technological parameters, irregularly shaped particles were impacted into spherical particles gradually, and particles structure became more close-grained. So comparing size distribution change is the most simple and convenient means to determine the optimum PCS technological parameters.
3.1 Treatment effect under different PCS conditions
Rotor speed is the primary sources of energy, and is also the major factor to affect sphericizing availability. Fig.3 shows the relationship between particles median diameter and the PCS rotor speed when processing time is 10 min. The particles diameter decreases noticeably with increasing rotor speed, and the reason is that impact energy of PCS rotors is a linear relation with the square value of the PCS rotor speed. So, high rotor speed can get better effect. The rotor speed chose is 5 000 r/min in the experiment.
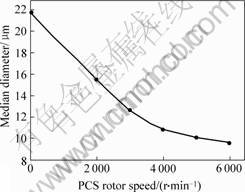
Fig.3 Relationship between median diameter and rotor speed
Processing time is also an important factor to affect sphericizing availability, and the length of processing time is relevant to the properties of raw material processed. Fig.4 shows the relationship between particles median diameter and the PCS processing time of when rotor speed is 5 000 r/min. The particle size decreases noticeably in the first 10 min; but after 15 min, the particles size almost remains the same. The appropriate processing time is about 15 min, since the particle properties almost remain the same after more than 15 min of treatment.
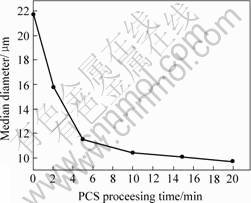
Fig.4 Relationship between median diameter and processing time
Inventory rating is a very important technological parameter. Except for the wallop of rotor, the clearance between the rotor and stator also affect the particle interaction. It’s very hard to evenly distribute particles if too much raw powders were put into the machine, but effectual collision between particles can’t work well if too little powders were put.
3.2 Treatment effect in appropriate technological parameters
Irregularly shaped electrolytic copper powders were processed under the technological conditions of rotor speed 5 000 r/min, processing time 15 min, inventory rating 150 g per batch, and argon atmosphere. The metal particles properties such as bulk density, tap density, size distribution, sphericity, and fluidity, etc, all improve evidently.
Purity of power prepared by the electrolytic process is high, and particle shape of electrolytic is dendritic. SEM photographs of the raw electrolytic copper particles are shown in Fig.5(a), and the average diameter of the Cu particles is about 25 μm. The dendritic particles become spherical gradually by continuous impacting, sphericity factor improves a lot, meanwhile the particles size also decreases obviously (Fig.5(b)).

Fig.5 SEM images of electrolytic copper powders: (a) Raw powders; (b) After processing
Table 1 lists the electrolytic copper powders change of size distribution (D10, D50 and D90) and specific surface area. After processing, irregularly shaped metal powders were impacted into dense spherical particles, and particles size decreased obviously, and Specific surface area increased noticeably under the appropriate process conditions.
Table 1 Size distribution and specific surface of electrolytic copper powders
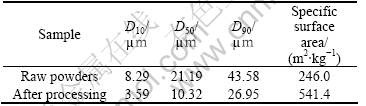
The bulk density, tap density, angle of repose, angle of spatula, and uniformity of electrolytic copper powders were measured by BT-1000 powder characteristic test apparatus, and degree of compression and slamp value were calculated according to the measuring results. Table 2 lists the detailed results. After processing, bulk density and tap density of the powders increases noticeably, and the angle of repose and angle of spatula decrease evidently. The fluidity of copper powders is raised, and the combination property of powders is improved greatly.
Table 2 Combination property of electrolytic copper powders
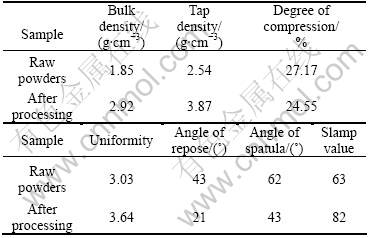
References
[1] TANAKA I, KOISHI M, SHINOHARA K. A study on the process for formation of spherical cement through an examination of the changes of powder properties and electrical charges of the cement and its constituent materials during surface modification [J]. Cement and Concrete Research, 2002 (32): 57-64.
[2] JIN Zong-lian, XU Hua-rui, ZHAO Bin, GU Hong-chen. Globose ultra fine metal silver powder prepared by spray pyrolysis process [J]. Shanghai Metals, 2001, 3: 37-40.
[3] TOE Y, FENG D, ZHANG Yi-wen, et al. Study on the production process of spherical Ni-based superalloy powder for special applications [J]. Powder Metallurgy Industry, 2003, 13(5):12-15.
[4] JIANG Wen-wei, PU Chong-en. Investigation of process for spherical tungsten powder by plasma atomization [J]. Cemented Carbide, 2000, 2: 85-88.
[5] TANAKA I, KOISHI M. Fabrication and characteristics of Fe3O4-polymer composite particles by hybridization [J]. Construction and Building Materials, 1999, 13: 285-292.
[6] GU Yuan. The technology and application of powder surface modification[J]. Chemical Industry and Engineering Progress, 1994, 1: 33-41.
(Edited by LONG Huai-zhong)
Foundation item: Project(50474003) supported by the National Natural Science Foundation of China
Corresponding author: GAI Guo-sheng; Tel.: +86-10-62772725; Fax: +86-10-62772135. E-mail: gaigs@mail.tsinghua.edu.cn