J. Cent. South Univ. Technol. (2011) 18: 1377-1382
DOI: 10.1007/s11771-011-0849-5
Hexagonal hematite platelets synthesized from pyrite cinders by hydrothermal process
LIU Zhao-cheng(刘昭成), ZHENG Ya-jie(郑雅杰)
School of Metallurgical Science and Engineering, Central South University, Changsha 410083, China
? Central South University Press and Springer-Verlag Berlin Heidelberg 2011
Abstract: Well-crystallized hexagonal hematite (α-Fe2O3) platelets were synthesized by hydrothermal process, using a highly concentrated ferric hydroxide as precursor. The precursor was prepared by adding ammonia to the ferric sulfate solution which was obtained by leaching pyrite cinders with sulfuric acid. Structure and morphology of the synthesized products were investigated by X-ray diffraction, scanning electron microscope, transmission electron microscope and selected area electron diffraction. The results reveal that the reaction temperature has significant effects on the structure, size and shape of the synthesized hematite particles. Typical hexagonal hematite platelets, about 0.4-0.6 ?m in diameter and 0.1 ?m in thickness, were prepared at 230 °C for 0.5 h. Al3+, contained in the sulfuric acid leaching solution as an impurity, plays an extremely important role in the formation of hexagonal hematite. In addition, a possible mechanism about the formation of hexagonal hematite platelets was proposed.
Key words: hematite; α-Fe2O3; pyrite cinders; hydrothermal process; hexagonal platelets
1 Introduction
Hematite (α-Fe2O3), an n-type semiconductor (Eg= 2.1 eV), is the most thermodynamically stable phase of iron oxide. Now, α-Fe2O3 has been extensively investigated in pigments [1], heterogeneous catalysts [2], gas sensors [3], adsorbents [4], electrode materials [5] and magnetic recording media [6] because it possesses such outstanding characteristics as non-toxicity, chemical stability, durability, high resistance to corrosion and low cost.
It is well known that the characteristics of ultrafine materials deeply depend on their size and shape. Therefore, in order to control the size and shape, considerable efforts have been devoted to the fabrication process. α-Fe2O3 particles have different shapes, such as spheres [7], spindles [8], pores [9], tubes [10], wires [11], rods [12], cubes [13] and platelets [14]. Methods for preparing these α-Fe2O3 particles with different shapes include gel-sol, forced hydrolysis, and hydrothermal treatment. For example, SUGIMOTO and WANG [15] reported the preparation of monodisperse platelet-type hematite (α-Fe2O3) particles by gel-sol in a high alkaline medium. KANDORI et al [16] prepared disk-shaped hematite particles by forced hydrolysis using acidic FeCl3 solution with the presence of polyvinyl alcohol. DIAMANDESCU et al [17] obtained plate-like hematite from ferric hydroxide precursor in a strong alkaline medium via hydrothermal method. Among these methods, the hydrothermal approach has attracted much more attention than others due to its distinct advantages in particle size and shape control, mild synthetic conditions, less time consumption, high homogeneity and good crystallization.
Annually, millions of tons of pyrite cinders are produced as a by-product of sulphuric acid industry world wide. And pyrite cinders are mainly composed of iron oxides, especially hematite (α-Fe2O3). Pyrite cinders are fine powders (~75 μm) and contain hazardous heavy metals [18], possibly posing a serious threat to the surrounding area. And the hazardous heavy metals limit their usage in pig iron industry [19]. As a result, the search of new and cost-effective technologies for pyrite cinders treatment and disposal has become increasingly important in recent years. Considering the environmental protection, treatment costs and limited landfill/disposal sites, the most suitable method for pyrite cinders utilization is to recycle them as a secondary raw material. Methods for pyrite cinders reutilization have been reported, such as recycling as brick, paint and cement [20]. However, the approach of using pyrite cinders as iron source to prepare hematite (α-Fe2O3) platelets, to the best of our knowledge, has never been reported in previous literatures.
In this work, single-crystalline hexagonal α-Fe2O3 platelets were successfully synthesized by hydrothermal treatment, using a highly concentrated ferric hydroxide as precursor. The precursor was prepared by adding ammonia to the ferric sulfate solution, which was obtained by leaching pyrite cinders with sulfuric acid. And the effect of hydrothermal temperature on hematite phase transformation and hematite morphology was studied. Moreover, the probable formation mechanism of hexagonal α-Fe2O3 platelets was proposed.
2 Experimental
2.1 Materials and reagents
Analytical reagents H2SO4, H2O2 and NH3·H2O (Tianjin Kaitong Chemical Co.) were used without further purification. Ultrafine α-Fe2O3 particles (Hunan Three Ring Pigment Co.), spherical and about 0.3 ?m in diameter, were used as the seed crystal. Pyrite cinders were provided by Guangdong Pyrite Mine Corporation (Guangdong, China). Its chemical composition was examined by X-ray fluorescence spectroscopy (XRF), and its main compositions (mass fraction) were 58.15% Fe, 30.2% O, 5.545% Si, 1.951% S, 1.62% Al, 1.04% Ca, 0.368% Mg, 0.433% K, and 0.148% Zn.
The mixture of ferric and ferrous sulfate was prepared from pyrite cinders by sulfuric acid leaching [21]. First, 6.5 L 50% sulfuric acid solution was added to a 10 L three-necked flask. Then, 3 kg pyrite cinders were gradually added into the sulfuric acid solution under vigorous stirring, keeping at 115 °C for 4 h. After filtration, the solution was diluted to 9.0 L with deionized water. The diluted solution, using as the iron source for hematite preparation, was mainly a mixture of ferric sulfate and ferrous sulfate (see Table 1), containing other trace elements such as Al, Mg, Ca.
Table 1 Chemical compositions of acidic leaching solution of pyrite cinders (g/L)
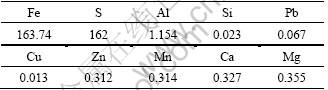
2.2 Synthesis of hexagonal α-Fe2O3 platelets
Typical procedure used to prepare hexagonal hematite platelets from pyrite cinders is summarized in Fig.1. Firstly, 175 mL hydrogen peroxide solution (30%, volume fraction) was dropped to the diluted ferric and ferrous sulfate solution under vigorous stirring, adjusting n(Fe(II))/n(Fe(III)) to 0.08. Then, 200 mL iron solution, whose total iron concentration was 2.5 mol/L, was taken out and ammonia solution (25%, volume fraction) was added until its pH reached 7. Subsequently, 2 g ultrafine hematite particles were added into the suspension, the total volume of which was 400 mL. At last, the suspension was transferred to a 500 mL autoclave, sealed and maintained at a set temperature for 0.5 h. Temperatures investigated were 140, 170, 200 and 230 °C, respectively. After the heating treatment, the reactor was cooled down to room temperature by an internal cooling coil. It was filtered and rinsed with deionized water, and finally dried at 105 °C for 12 h.
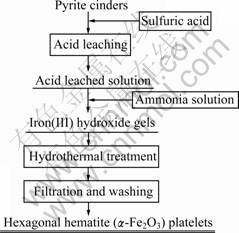
Fig.1 Flow sheet of preparation of hexagonal hematite platelets from pyrite cinders by hydrothermal method
2.3 Characterization
Ferrous and ferric ion concentrations were performed according to GB/T 1863—2008 (Chinese National Standard). Each analysis was repeated for three times and the mean values were used. Powder X-ray diffraction (XRD, Rigaku, D/max-rA) with Cu Kα (λ=1.540 562 ?) radiation was used to identify the obtained products. The scanning scale of 2θ was ranged from 10.0° to 70.0° with a step rate of 0.01 (°)/s. Particle size distribution of the obtained hematite platelets was determined using a Zetasizer Nano ZS (Malvern Instruments, Malvern, UK). The surface morphology was observed with a scanning electron microscope (SEM, JSM-6360LV, JEOL, Ltd., Tokyo, Japan). TEM patterns were recorded on a Hitachi Model H-800 transmission electron microscope at an accelerating voltage of 200 kV. Meanwhile, selected area electron diffraction (SAED) was further performed to identify the crystallinity.
3 Results and discussion
3.1 Crystal structure of α-Fe2O3 particles
Crystal structure of the resulting products was characterized by XRD. Figure 2 shows the XRD patterns of the products obtained at the reaction temperature ranging from 140 °C to 230 °C. All the XRD patterns except Fig.2(a) are well indexed to the rhombohedra phase, α-Fe2O3, with space group R-3c (167), and its cell parameters are a=5.036 ?, b=5.036 ?, c=13.749 ? (JCPDS file card, No. 33-0664). And these XRD peaks exactly match the (012), (104), (110), (006), (113), (202), (024), (116), (018), (214) and (300) crystal planes of α-Fe2O3 with a corundum crystal structure. No other diffraction peaks are found, indicating that α-Fe2O3 is successfully synthesized under the experimental conditions. The XRD pattern of Fig.2(a) indicates the coexistence of α-Fe2O3 and α-FeOOH phases in the product obtained at 140 °C and the peak intensity is comparably weakonfirmsngks exactly matched, which suggests that the phase transformation from ferric hydroxide gel to α-Fe2O3 or α-FeOOH is not completed in this condition. When the reaction temperature is increased to 170 °C (Fig.2(b)), α-Fe2O3 can be clearly identified, and α-FeOOH disappears, which indicates that the phase transformation from α-FeOOH to α-Fe2O3 is completed. Further elevating the reaction temperature, peak intensity of the α-Fe2O3 phase is also increased consecutively (Figs.2(c) and (d)). When the reaction temperature is increased to 230 °C (Fig.2(d)), the peaks of α-Fe2O3 become extraordinarily intensive and extremely sharp, suggesting that a well-crystallized and high-purity α-Fe2O3 is synthesized. Based on the above experimental results, it can be concluded that the increase of reaction temperature promotes the transformation of Fe(OH)3→ α-FeOOH→α-Fe2O3 and accelerates the rate of nucleation. This is because that the phase transition process of Fe(OH)3→α-FeOOH→ α-Fe2O3 belongs to an endothermic reaction [22]. Thus, elevating reaction temperature is conducive to these phase transitions.
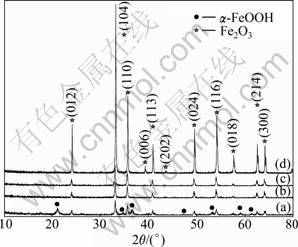
Fig.2 Evolution of XRD patterns of α-Fe2O3 particles synthesized at different temperatures for 0.5 h: (a) 140 °C; (b) 170 °C; (c) 200 °C; (d) 230 °C
3.2 Morphology evolutional process of α-Fe2O3 platelets
For a complete view of the formation process of the α-Fe2O3 platelets and of their growth mechanism, a detailed temperature-dependent morphology evolution study was conducted. The morphology and size of the products at different temperatures were examined by SEM, as shown in Fig.3. From Fig.3(a), some spherical α-Fe2O3 and rod-like α-FeOOH particles can be observed at 140 °C. Meanwhile, some aggregated irregular particles are also observed, which suggests that the crystallization is poor, consisting with the corresponding XRD patterns (Fig.2(a)). The sample prepared at 170 °C shows that its morphology is inhomogeneous and the particles agglomerate seriously, as can be seen from Fig.3(b). And this agglomeration is caused by high specific surface area of these fine particles. When reaction temperature is increased to 200 °C, considerable small platelet-type hematite particles are synthesized (Fig.3(c)). It is a signal for the formation of hexagonal platelet-type hematite particles. Further elevating the reaction temperature to 230 °C (Fig. 3(d)), almost all of the products are hexagonal platelet-type hematite particles, with 0.4-0.6 mm in diameter and ~0.1 mm in thickness. And there is no agglomeration among these hexagonal hematite platelets.
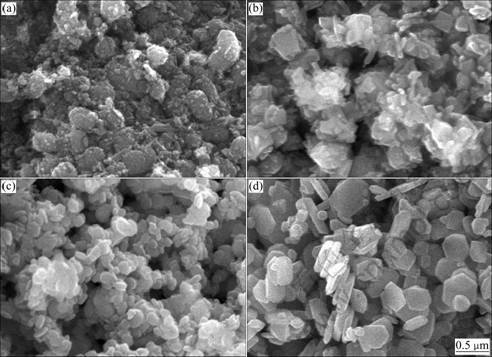
Fig.3 SEM images of products obtained at different temperatures for 0.5 h: (a) 140 °C; (b) 170 °C; (c) 200 °C; (d) 230 °C
Figure 4 shows the size distribution of the hexagonal hematite platelets obtained at 230 °C for 0.5 h. It also can be seen from Fig.4 that the size distribution of the synthesized hexagonal platelet-type hematite particles is very narrow (~0.56 ?m), which coincides with the SEM images, indicating that the hematite platelets obtained at 230 °C are uniform and in good crystallization.
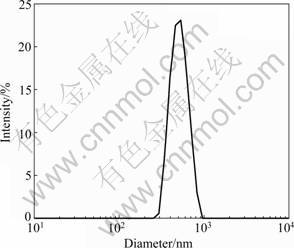
Fig.4 Particle size distribution of hexagonal hematite platelets synthesized at 230 °C for 0.5 h
Figure 5 shows typical TEM images of hexagonal hematite platelets obtained at 230 °C for 0.5 h, and the morphology and size are similar to those observed from the SEM images (Fig.3(d)). This further reveals that uniform hematite particles can be successfully prepared by this approach. Figure 5(b) shows a higher magnification TEM image and Fig.5(c) shows an individual hexagonal hematite platelet. Herein, the hematite particles with a regular hexagonal shape can be clearly observed. The strong spots of the SEAD pattern depicted in the inset of Fig.5(c) indicate that the obtained hematite platelets have a satisfied crystallinity. And it also illustrates that the platelet-type α-Fe2O3 particles are single crystals.
3.3 Formation mechanism of α-Fe2O3 platelets
The acidic leaching solution of pyrite cinders contains some other metal ions, where Al3+ in particular accounts for a relatively large proportion. It was reported that Al3+ incorporation played a very important role in modifying particles morphology during the hematite particles formation. CAO et al [23] pointed out that aluminum ion substitution had a significant effect on the modification of hematite morphology. They have prepared discoid hematite particles by catalytic phase transformation using co-precipitates of Fe3+ and Al3+ as precursor. SCHWERTMANN et al [24] also demonstrated that Al substitution promoted the anisotropic growth of hematite particles in the c crystal direction in the iron and aluminum nitrate system, although they found that increasing substitution actually retarded the crystal growth along the c axis. Nevertheless, the shape of the hexagonal hematite platelets in this work might be a result of the stronger adsorption of Al3+ to the {0001} face, thereby retarding the growth in this direction, and the growth rate on
and
plane is relatively fast. Thus, the formation of the hexagonal hematite platelets may be attributed to the preferred growth of some planes in the recrystallization process.
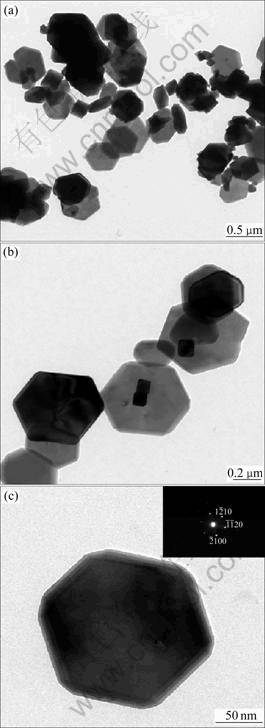
Fig.5 TEM images of hexagonal platelet-type α-Fe2O3 particles synthesized at 230 °C for 0.5 h: (a) Low magnification; (b) and (c) High magnification (inset in (c) SAED pattern of hexagonal α-Fe2O3 platelet)
In order to demonstrate the effect of Al3+ on the formation of α-Fe2O3 platelets, chemical compositions of the obtained hematite particles prepared at different temperatures were determined by XRF. The results were listed in Table 2. It is shown that Fe2O3 contents increase with the reaction temperature increasing and the contents of other impurity elements such as Si and S decrease gradually. It is possibly because the smaller hematite particles, formed at lower temperatures, can easily adsorb impurity elements due to their large specific surface area. However, Al content of the obtained products increases as the reaction temperature increases, which suggests that Al is incorporated into hematite crystals or adsorbed on their surface. It is no doubt that Al3+ of the acidic leached solution plays an important role during the hexagonal hematite platelets formation. The results of this experiment strongly support our previous analysis.
Table 2 Chemical composition of hematite particles synthesized at different temperatures (%)
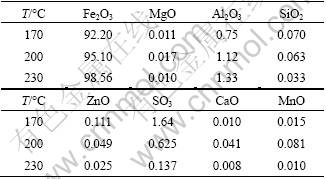
On the basis of the information gathered previously, the whole reaction of hexagonal hematite platelets formation by hydrothermal process can be proposed as follows:
Fe2O3+6H+→2Fe3++3H2O (1)
FeO+2H+→Fe2++H2O (2)
2Fe2++2H++H2O2→2Fe3++2H2O (3)
Fe3++3NH3·H2O→Fe(OH)3↓+
(4)
Fe(OH)3→α-FeOOH+H2O (5)
2α-FeOOH→α-Fe2O3+H2O (6)
First, n(Fe(II))/n(Fe(III)) of the acid leaching solution, obtained from pyrite cinders by sulfuric acid leaching, was adjusted to 0.08 by hydrogen peroxide solution. Fe2+ ions in the hydrothermal process could catalyze the phase transformation of Fe(OH)3 gel to α-Fe2O3 particles [25]. Then, the adjusted solution reacted with NH3·H2O to form Fe(OH)3 gel. Sequentially, the rod-like α-FeOOH was generated by the phase transition of Fe(OH)3 under hydrothermal conditions. By increasing the reaction temperature, α-FeOOH began to dissolve and it was converted to α-Fe2O3, and then the formed small α-Fe2O3 particles gathered and gradually grew into platelets due to the fact that the (0001) plane was protected by Al3+. In this process, an interesting phenomenon was observed that α-Fe2O3 platelets were formed by the oriented gathering of small α-Fe2O3 particles. This process differed from the transformation of α-FeOOH to α-Fe2O3 as reported in the literature [26], in which the α-FeOOH precursor underwent a topotactic transformation. In the present case, the α-Fe2O3 platelets did not retain the morphologies of the α-FeOOH precursor and it was more likely that α-FeOOH would transform to α-Fe2O3 via “dissolution/recrystallization” procedure.
4 Conclusions
1) Hexagonal hematite platelets have been successfully synthesized via hydrothermal methods using pyrite cinders as raw material. It is found that reaction temperature has a significant effect on the hematite crystal structure, size and shape. When the temperature is maintained at 140 °C for 0.5 h, the obtained product is poorly crystallized and both α-Fe2O3 and α-FeOOH phases exist. When reaction temperature increases to 170 °C, α-FeOOH is completely transformed to α-Fe2O3. Small α-Fe2O3 platelets are obtained at 200 °C. As the reaction temperature increases to 230 °C, typical hexagonal hematite platelets (0.4-0.6 ?m in diameter and ~0.1 ?m in thickness) are prepared.
2) Al3+ of the acid leached solution plays the role of shape-control agent for the synthesis of hexagonal hematite platelets. The shape of the hexagonal hematite platelets is mainly ascribed to the stronger adsorption of Al3+ to the {0001} face, retarding the growth in this direction, and the growth rate on
and
plane is relatively fast. XRF investigation also supports the above results.
3) The formation mechanism of hexagonal hematite platelets is proposed: Fe(OH)3 precursor is firstly transformed into α-FeOOH by hydrothermal process and then the obtained α-FeOOH is dissolved and converted to α-Fe2O3. At last, the small hematite particles obtained gather together and grow to hexagonal platelet-type α-Fe2O3 particles.
References
[1] CORNELL R M, SCHWERTMANN U. The iron oxide structure, properties, reactions, occurrences, and uses [M]. Weinhein: Wiley- VCH, 2003: 130-137.
[2] SARKAR A, SETH D, DOZIER A K, NEATHERY J K, HAMDEH H H, DAVIS B H. Fischer-Tropsch synthesis: Morphology, phase transformation and particle size growth of nano-scale particles [J]. Catal Lett, 2007, 117(1/2): 1-17.
[3] CHEN Jun, XU Li-na, LI Wen-yang, GOU Xing-long. α-Fe2O3 nanotubes in gas sensor and lithium-ion battery applications [J]. Adv Mater, 2005, 17(5): 582-586.
[4] ZHONG Liang-shu, HU Jin-song, LIANG Han-pu, CAO An-min, SONG Wei-guo, WAN Li-jun. Self-assembled 3D flowerlike iron oxide nanostructures and their application in water treatment [J]. Adv Mater, 2006, 18(18): 2426-2431.
[5] NULI Y, ZENG R, ZHANG P, GUO Z P, LIU H K. Controlled synthesis of α-Fe2O3 nanostructures and their size-dependent electrochemical properties for lithium-ion batteries [J]. J Power Sources, 2008, 184(2): 456-461.
[6] TADIC M, MARKOVIC D, SPASOJEVIC V, KUSIGERSKI V, REMSKAR M, PIRNAT J, JAGLICIC Z. Synthesis and magnetic properties of concentrated α-Fe2O3 nanoparticles in a silica matrix [J]. J Alloys Compd, 2007, 441(1/2): 291-296.
[7] WANG Dan-jun, LI Dong-sheng, GUO Li, FU Feng, QI Guang-cai, WANG Yao-yu. Synthesis and characterization of spherical hematite (α-Fe2O3) nanopowder by sonochemical hydrolysis method [J]. Chinese J Inorg Chem, 2006, 22(7): 1317-1320.
[8] LU Jian, CHEN Dai-rong, XIU Jiao-ling. Fabrication, characterization, and formation mechanism of hollow spindle-like hematite via a solvothermal process [J]. J Colloid Interface Sci, 2006, 303(2): 437-443.
[9] QIU Jin, YANG Ru, LI Min, JIANG Nan. Preparation and characterization of porous ultrafine Fe2O3 particles [J]. Mater Res Bull, 2005, 40(11): 1968-1975.
[10] JIA Chun-jiang, SUN Ling-dong, YAN Zheng-guang, YOU Li-ping, LUO Feng, HAN Xiao-dong, PANG Yu-cheng, ZHANG Ze, YAN Chun-hua. Single-crystalline iron oxide nanotubes [J]. Angew Chem Int Edit, 2005, 44(28): 4328-4333.
[11] SUBER L, IMPERATORI P, AUSANIO G, FABBRI F, HOFMEISTER H, Synthesis, morphology, and magnetic characterization of iron oxide nanowires and nanotubes [J]. J Phys Chem B, 2005, 109(15): 7103-7109.
[12] WU Chang-zheng, YIN Ping, ZHU Xi, OUYANG Chuan-zi, XIE Yi. Synthesis of hematite (α-Fe2O3) nanorods: Diameter-size and shape effects on their applications in magnetism, lithium ion battery, and gas sensors [J]. J Phys Chem B, 2006, 110(36): 17806-17812.
[13] HOU Bo, WU You-shi, WU Li-li, SHI Yuan-chang, ZOU Ke, GAI Hong-de. Hydrothermal synthesis of cubic ferric oxide particles [J]. Mater Lett, 2006, 60(25/26): 3188-3191.
[14] SUGIMOTO T, WAKI S, ITOH H, MURAMATSU A. Preparation of monodisperse platelet-type hematite particles from a highly condensed β-FeOOH suspension [J]. Colloids and Surfaces A, 1996, 109(11): 155-165.
[15] SUGIMOTO T, WANG Y. Mechanism of the shape and structure control of monodispersed α-Fe2O3 particles by sulfate ions [J]. J Colloid Interface Sci, 1998, 207(1): 137-149.
[16] KANDORI K, YAMAMOTO N, YASUKAWA A, ISHIKAWA T. Preparation and characterization of disk-shaped hematite particles by a forced hydrolysis reaction in the presence of polyvinyl alcohol [J]. Phys Chem Chem Phys, 2002, 4(1): 6116-6122.
[17] DIAMANDESCU L, D. MIHAILA-TARABASANU D, POPECSU- POGRION N, TOTOVINA A, BIBICU I. Hydrothermal synthesis and characterization of some polycrystalline α-iron oxides [J]. Ceram Int, 1999, 25(8): 689-692.
[18] GIUNTI M, BARONI D, BACCI E. Hazard assessment to workers of trace metal content in pyrite cinders [J]. Bull Environ Contam Toxicol, 2004, 72(2): 352-357.
[19] TUGRUL N, DERUN E M, PISKIN M. Utilization of pyrite ash wastes by pelletization process [J]. Powder Technol, 2007, 176(2): 72-76.
[20] AIP I, DEVECI H, YAZICI E Y, TURK T, SUNGUN Y H. Potential use of pyrite cinders as raw material in cement production: Results of industrial scale trial operations [J]. J Hazard Mater, 2009, 166(1): 144-149.
[21] ZHENG Ya-jie, CHEN Bai-zhen, GONG Zhu-qing, CHEN Wen-mi. A new method of preparing polymeric ferric sulfate from pyrite cinders [J]. Journal of Central South University: Science and Technology, 2001, 32(2): 142-145. (in Chinese)
[22] NAVROTSKY A, MAZEINA L, MAJZLAN J. Size-driven structural and thermodynamic complexity in iron oxides [J]. Science, 2008, 319(5870): 1635-1638.
[23] CAO Fu-Ling, WU Yu-Fei, LIU Hui, WEI Yu. Preparation and property of discoid aluminum-doped α-Fe2O3 particles [J]. Acta Chimica Sinica, 2008, 66(12): 1405-1410.
[24] SCHWERTMANN U, FITZPATRICK R W, TAYLOR R M, LEWIS D G. The influence of aluminum on the iron oxides: Part II. Preparation and properties of Al-substituted hematites [J]. Clays Clay Miner, 1979, 27(2): 105-112.
[25] LIU Hui, WEI Yu, SUN Yu-han. The formation of hematite from ferrihydrite using Fe(Ⅱ) as a catalyst [J]. J Mol Catal A Chem, 2005, 226(1): 135-140.
[26] JIA Bao-ping, GAO Lian, Sun Jing. Synthesis of single crystalline hematite polyhedral nanorods via a facile hydrothermal process [J]. J Am Ceram Soc, 2007, 90(4): 1315-1318.
(Edited by HE Yun-bin)
Foundation item: Project(2008A090300016) supported by the Key Science and Technology Item of Guangdong Province, China; Project(ZKJ2010022) supported by the Precious Apparatus Opening Center Foundation of Central South University, China
Received date: 2010-09-07; Accepted date: 2010-12-23
Corresponding author: ZHENG Ya-jie, Professor, PhD; Tel: +86-731-88836285; E-mail: zzyyjj01@yahoo.com.cn