J. Cent. South Univ. (2012) 19: 1169-1174
DOI: 10.1007/s11771-012-1124-0
Thermo-plasticity of high-strength and high-ductility 7050 aluminum ingot
DENG Ying(邓英)1, YIN Zhi-min(尹志民)1, CONG Fu-guan(丛福官)2
1. School of Materials Science and Engineering, Central South University, Changsha 410083, China;
2. Northeast Light Alloy Co. Ltd, Harbin 150060, China
? Central South University Press and Springer-Verlag Berlin Heidelberg 2012
Abstract: Thermo-plasticity of homogenized 7050 aluminum ingot was investigated by instantaneous tensile tests conducted at different temperatures. The results show that, with the increase of testing temperatures, the strength decreases, and the plasticity increases firstly and then decreases in homogenized 7050 ingot. When the studied alloy is deformed between 380 ℃ and 420 ℃, the deformation resistance is lower and plasticity is better. And the actual heating temperature for ingot before hot extrusion should be controlled between 360 ℃ and 400 ℃. At low tensile temperatures, the deformation structure is mainly composed of dislocation substructure. With the increase of testing temperatures, transgranular fracture transforms into intergranular fracture progressively during deformation. At high tensile temperatures, the grain boundaries are weakened, deformation is concentrated at the grain boundaries and the re-orientation of equilibrium phases at grain boundaries appears.
Key words: 7050 alloys; tensile test; thermo-plasticity; microstructure; mechanical property
1 Introduction
7××× series aluminum alloys are widely used in the aircraft industry due to their high specific strength [1-4] and good hardenability [5-6]. One of the most important applications for 7050 aluminum alloy is to manufacture aircraft rivet. And its manufacturing procedure is as follows: homogenization → hot extrusion → drawing → intermediate annealing → drawing → solution and aging. In the view of higher content of alloying elements in 7050 alloy, it is easier for homogenized ingot to craze during its subsequent hot-working treatment. As a result, the research of hot-working characteristics for ingot after homogenization is meant to be of great practical significance. Currently, the research of hot-working characteristics in high-strength aluminum alloy is mainly focused on hot deformation behaviors. HU et al [7] recently showed that the fracture surface of the 7050 aluminum treated by solid solution transformed from ductile transgranular fracture into intergranular fracture with the increase of deformation temperature. LIN et al [8] studied on the hot deformation behaviors of homogenized Al-Zn-Mg-Cu-Cr aluminum alloy through hot compression experiments. It was revealed that the deformation structures gradually inclined to dynamic- recrystallization with the deformation temperature rising. CERRI [9] investigated the hot workability of 7012 and 7075 alloys by hot torsion tests, and found that the ductility of the extruded alloys was almost double that of the as-cast material, with the exception of the solution-treated material where, at low temperature, the ductility of the extruded alloy was lower. LIU et al [10] discovered that water-quenched 7050 alloy after homogenization exhibited higher flow stresses than furnace-cooled alloy, and the difference in the peak stress decreased with temperature increasing under hot compression. DENG et al [11] indicated that the main softening mechanism of homogenized 7050 aluminum alloy was dynamic recovery. The previous work provides a basis for designing practical hot working conditions. However, there is less report about the proper hot working conditions of homogenized 7050 ingot.
The present work aims to find proper hot extrusion temperature interval of homogenized 7050 ingot by instantaneous tensile test at elevated temperature and to investigate its microstructural evolution during deformation by X-ray diffractometry (XRD), scanning electron microscopy (SEM) and transmission electron microscopy (TEM).
2 Experimental
The nominal composition of 7050 aluminum ingot, in the form of semi-continuous cast billets, with 162 mm in diameter and 200 mm in height, is Al-5.87Zn-2.07Mg- 2.28Cu-0.11Zr-0.04Si-0.08Fe-0.10Mn-0.04Cr-0.05Ni-0.06Ti (mass fraction, %). Ingot was homogenized at 400 ℃ for 10 h and 470 ℃ for 48 h and then cooled to room temperature in air.
The experimental alloys were machined into the shape shown in Fig. 1. The thermo-plasticity of high-strength and high-ductility 7050 aluminum ingot was evaluated by means of instantaneous tensile test at elevated temperature. The instantaneous tensile tests were carried out on RWS50 electronic testing machine for creeping relaxation at temperatures of 28, 100, 200, 250, 300, 350, 370, 385, 400, 420, 450, 475 and 500 ℃, respectively and the tensile rate of 1 mm/min. The designing of tensile test condition is according to industrial hot working conditions. The tensile tests strictly followed the relevant provisions according to GB/T 4338—1995 “Tensile Test Method of Alloy at High Temperature”, and the result for one temperature was obtained from the average results of four samples tested under the same conditions. The alloys after test were quenched in absolute alcohol immediately to avoid oxidation. And the fracture analysis was performed on Quanta MK2-200 SEM. Samples for TEM analysis were selected near the fracture surfaces. The deformed structures were prepared by the conventional methods for the microstructural observations on a TECNAI G220 transmission electron microscope.
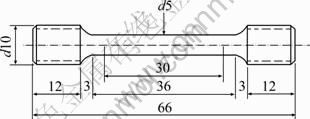
Fig. 1 Sample of instantaneous tensile test at elevated temperature (Unit: mm)
3 Results
3.1 Tensile properties
The tensile properties of homogenized 7050 ingot at different testing temperatures are shown in Fig. 2.
The results show that, with the increase of testing temperatures, the tensile strength decreases, and the elongation and area reduction firstly increase and then decrease. It can be seen that deformation resistance is low and plasticity is good at 380-420 ℃ in homogenized 7050 ingot. As a result, the temperatures for hot-working should be controlled in this temperature range. During the deformation between 450 and 500 ℃, the fractured cross-section of the specimen shrinks to a point. As a result, the deformation in this temperature range is equal to creep deformation, and the plasticity increases abruptly.
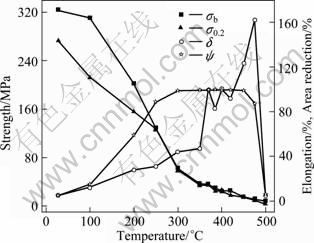
Fig. 2 Tensile properties of homogenized 7050 ingot deformed at different temperatures
3.2 Fracture surfaces
Figure 3 shows the morphologies of fracture surfaces of homogenized 7050 ingots after instantaneous tensile tests at different temperatures.
The fracture surface of the sample deformed at room temperature (28 ℃) exhibits a typical transgranular fracture, as shown in Fig. 3(a). With the increase of testing temperatures, the depth of dimples increases, and fracture surfaces gradually possess the characteristics of intergranular fracture, as shown in Figs. 3(b)–(d). The fracture surface of the sample after deformation at 500 ℃ shows a typical intergranular rock-candy-shaped fracture, and there are lots of small melting balls distributed on the fracture surface.
3.3 Result of SEM analysis for lateral side of deformed alloy
Figure 4 shows the SEM images for the lateral side of the homogenized 7050 samples deformed at different temperatures.
It can be seen that the grains of 7050 ingot are elongated laterally into fibrous tissue along the direction of tensile force. Due to different orientations of grains compared with tensile direction, each grain possesses different degrees of deformation, resulting in drawing the outline of grains on the lateral side of the sample after deformation. With the increase of testing temperatures, the grain boundaries are gradually weakened, leading to the fact that the outline of the deformed grains on the lateral side of the sample after deformation is gradually clear. Besides, by combining the results of Figs. 3 and 4, it can also be seen that deformation is concentrated at the grain boundaries, resulting in the same strength (σb=σ0.2) above 250 ℃ in Fig. 2.
3.4 Result of XRD analysis
XRD analysis was undertaken to identify the phases of homogenized 7050 ingot after instantaneous tensile tests at different temperatures. The XRD patterns are shown in Fig. 5.
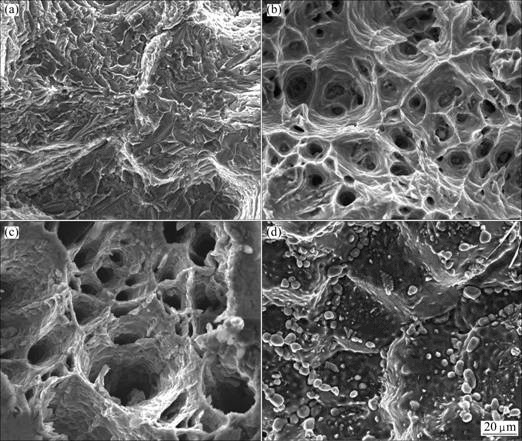
Fig. 3 Morphologies of fracture surfaces of homogenized 7050 ingot after instantaneous tensile test at different temperatures: (a) 28 ℃; (b) 250 ℃; (c) 400 ℃; (d) 500 ℃
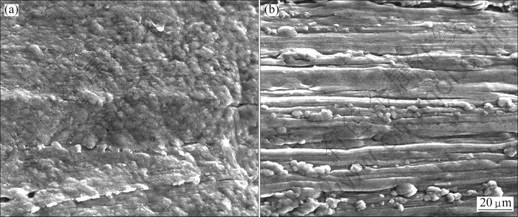
Fig. 4 SEM images of homogenized 7050 ingot after instantaneous tensile test at different temperatures: (a) 250 ℃; (b) 400 ℃
The phases in the homogenized 7050 ingot are α(Al) matrix, a lot of η (MgZn2) phases and a few of S (Al2CuMg) phases. With the increase of deformation temperatures, firstly, η (MgZn2) and S (Al2CuMg) phases largely precipitate, then gradually dissolve into matrix. η phases precipitate most at 250 ℃, while S phases have the maximum precipitation at 400 ℃. Finally, η and S phases all dissolve into matrix completely at 500 ℃.
3.5 Result of TEM analysis
Figure 6 shows TEM bright-field images of the microstructures of the studied alloy.
The results show that, the microstructure of homogenized 7050 ingot deformed at room temperature is mainly composed of dislocation substructures, and in addition to high dislocation density, there is a large number of small second phase particles. At 250 ℃, the microstructure is still composed of dislocation substructure, but the number and the size of second phase particles increase. Dislocation substructure still exists in the homogenized 7050 ingot after instantaneous tensile test at 400 ℃; in addition, second phase particles coarsen and strong slip lines can be seen in the grains (arrows in Fig. 6(d)). At 500 ℃, dislocation substructure disappears and the reorientation of equilibrium phases distributed at the grain boundaries appears owing to the sliding of grain boundaries (arrows in Figs. 6(e)-(f)), indicating that grain boundaries are weakened at high temperature and deformation is concentrated at the grain boundaries.
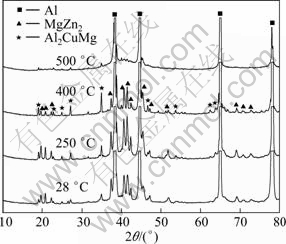
Fig. 5 X-ray diffraction patterns of homogenized 7050 ingot after instantaneous tensile tests at different temperatures
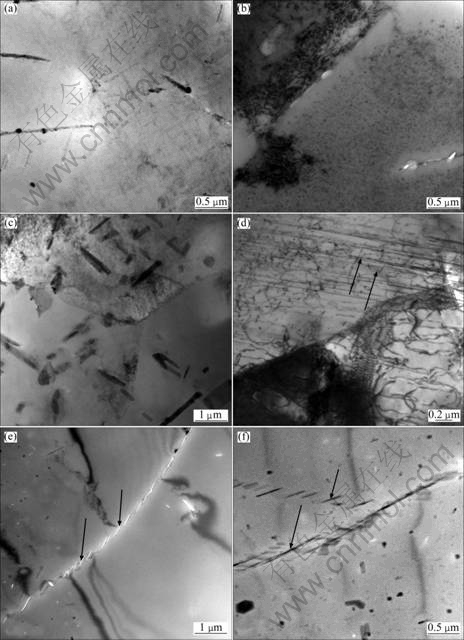
Fig. 6 TEM bright-field images of homogenized 7050 ingot after instantaneous tensile tests at different temperatures: (a) 28 ℃; (b) 250 ℃; (c)-(d) 400 ℃; (e)-(f) 500 ℃
4 Discussion
4.1 Effects of testing temperatures on microstructures and properties of ingot
LIU et al [12] pointed out that, the hot deformation of aluminum alloy is a competing process of dynamic softening and work hardening. At lower deformation temperatures, work hardening is the main deformation mechanism. High dislocation density and a large number of dispersed second phase particles in alloy lead to higher strength. With the increase of tensile testing temperatures, the decrease of dislocation density, brought by dynamic softening such as dynamic recovery and dynamic recrystallization, gradually offsets the effect of work hardening, leading to the gradual weakening of dislocation substructure. At the same time, second phase particles gradually coarsen. As a result, the strength of alloy gradually decreases. At 500 ℃, the dislocation substructure disappears and the reorientation of equilibrium phases distributed at grain boundaries appears owing to the sliding of grain boundaries, indicating that grain boundaries are weakened at high temperature and deformation is concentrated at grain boundaries. Therefore, the strength of alloy reaches its lowest value. The relationship between fracture surfaces and testing temperatures is determined. ZHONG and ZHAO [13] pointed out that the relative plasticity and the deformation hardening index of metal materials have direct impact on the way of aggregation and connection of microscopic holes. The greater the deformation hardening index is, the more difficult the internal constraints occur in materials. And it will generate more microscopic holes or the microscopic holes connecting with each other through shear brisement, thus leading to forming smaller and shallower dimples. Influenced by microstructure and relative plasticity of alloy, dimples would show a completely different shape and size. When 7050 ingot is stretched below 400 ℃, the fracture surfaces exhibit transgranular dimple fracture. With the increase of testing temperatures, the depth of dimples gradually increases, thus the elongation and area reduction gradually increase. When the tensile testing temperature is up to 500 ℃, the fracture surfaces transform from transgranular fracture into intergranular fracture, thus the elongation and area reduction decrease.
4.2 Proper temperature interval for hot-working in homogenized 7050 ingot
MENG et al [14] and HUANG et al [15] confirmed that flow stress is closely related to dislocation configuration during hot deformation of aluminum alloy. At lower deformation temperatures, to start dislocation needs higher energy. With the increase of deformation degree, it is easier to form dislocation tangles, which can effectively impede metal deformation. At the same time, there are a large number of fine second phase particles in the alloy, which can effectively impede the slipping and climbing of dislocation. Therefore, the deformation resistance is greater at lower testing temperatures. With increasing deformation temperature, due to the difference of thermal activation, dynamic recovery or recrystallization occurs, leading to the reduction of deformation resistance and the increase of thermo-plasticity. And the higher the deformation temperature is, the smaller the deformation resistance is. But when the deformation temperature is up to 500 ℃, grain boundaries are weakened, the sliding of grain boundaries occurs, and the deformation is concentrated at the grain boundaries. As a result, it is easy for ingot to occur intergranular fracture during hot-working. The results show that the deformation resistance is low and plasticity is good at 380-420 ℃ in homogenized 7050 ingot. As a result, the temperatures for hot-working should be controlled in this temperature range. However, to determine the temperature of hot extrusion, in addition to the heating temperature of ingot, it needs to be considered that there are about 20-30 ℃ temperature increases during extrusion in extrusion barrel for ingot. Therefore, the actual heating temperatures of ingot before hot extrusion should be controlled between 360 and 400 ℃.
5 Conclusions
1) With the increase of testing temperatures, the tensile strength decreases, and the elongation and area reduction increase firstly and then decrease in the homogenized 7050 ingot. When the studied alloy is deformed between 380 ℃ and 420 ℃, deformation resistance is low and plasticity is good. The actual heating temperature for homogenized 7050 aluminum ingot before hot extrusion should be controlled between 360 and 400 ℃.
2) At low deformation temperatures, the interaction between high dislocation density and second phase particles in the alloy leads to higher deformation resistance and lower plasticity. With the increase of tensile temperature, the decrease of dislocation density, brought by dynamic softening such as dynamic recovery and dynamic recrystallization, gradually offsets the effect of work hardening. At the same time, second phase particles gradually coarsen. As a result, the deformation resistance gradually decreases and the plasticity increases. At 500 ℃, second particles dissolve into matrix completely, grain boundaries are weakened and deformation is concentrated at grain boundaries. Therefore, the strength and the plasticity of studied alloys reach their lowest values.
References
[1] LIN Chih-kuang, YANG Sheng-tseng. Corrosion fatigue behavior of 7050 aluminum alloys in different tempers [J]. Engineering Fracture Mechanics, 1998, 59(6): 779-795.
[2] DESCHAMPS A, BRECHET Y. Influence of quench and heating rates on the ageing response of an Al-Zn-Mg-(Zr) alloy [J]. Materials Science and Engineering A, 1998, 251: 200-207.
[3] OU Bin-lung, YANG Ji-gang, WEI Mon-yu. Effect of homogenization and aging treatment on mechanical properties and stress-corrosion cracking of 7050 alloys [J]. Metallurgical and Materials Transactions A, 2007, 38: 1760-1773.
[4] PAGLIA C S, JATA K V, BUCHHEIT R G. A cast 7050 friction stir weld with scandium: Microstructure, corrosion and environmental assisted cracking [J]. Materials Science and Engineering A, 2006, 424: 196-204.
[5] STILLER K, WARREN P J, HANSEN V, ANGENETE J, GJ?NNES J. Investigation of precipitation in an Al-Zn-Mg alloy after two-step ageing treatment at 100 ℃ and 150 ℃ [J]. Materials Science and Engineering A, 1999, 270: 55-63.
[6] WILLIAMS J C, STARKE E A. Progress in structural materials for aerospace systems [J]. Acta Materialia, 2003, 51: 5775-5799.
[7] HU H E, ZHEN L, YANG L, SHAO W Z. ZHANG B Y. Deformation behavior and microstructure evolution of 7050 aluminum alloy during high temperature deformation [J]. Materials Science and Engineering A, 2008, 488: 64-71.
[8] LIN G Y, ZHANG Z F, ZHANG H, PENG D S, ZHOU J. Study on the hot deformation behaviors of Al-Zn-Mg-Cu-Cr aluminium alloy [J]. Acta Metallurgica Sinica: English Letters, 2008, 21: 109-115.
[9] CERRI E. Comparative hot workability of 7012 and 7075 alloys after different pretreatments [J]. Materials Science and Engineering A, 1995, 197: 181-198.
[10] LIU S D, YOU J H, ZHANG X M, DENG Y L, YUAN Y B. Influence of cooling rate after homogenization on the flow behavior of aluminum alloy 7050 under hot compression [J]. Materials Science and Engineering A, 2010, 527: 1200-1205.
[11] DENG Y, YIN Z M, HUANG J W. Hot deformation behavior and microstructural evolution of homogenized 7050 aluminum alloy during compression at elevated temperature [J]. Materials Science and Engineering A, 2011, 528: 1780-1786.
[12] LIU X Y, PAN Q L, HE Y B, LI W B, LIANG W J, YIN Z M. Flow behavior and microstructural evolution of Al-Cu-Mg-Ag alloy during hot compression deformation [J]. Materials Science and Engineering A, 2009, 500: 150-154.
[13] ZHONG Qun-peng, ZHAO Zi-hua. Fractography [M]. Beijing: Higher Education Press, 2006: 131-164. (in Chinese).
[14] MENG G, LI B L, LI H M, HUANG H, NIE Z R. Hot deformation behavior of an Al-5.7 wt.% Mg alloy with erbium [J]. Materials Science and Engineering A, 2010, 516: 131-137.
[15] HUANG X D, ZHANG H, HAN Y, WU W X, CHEN J H. Hot deformation behavior of 2026 aluminum alloy during compression at elevated temperature [J]. Materials Science and Engineering A, 2010, 527: 485-490.
(Edited by YANG Bing)
Foundation item: Project(JPPT-115-2-948) supported by the National Civilian Matched Program of China
Received date: 2011-03-28; Accepted date: 2011-05-06
Corresponding author: YIN Zhi-min, Professor, PhD; Tel: +86-731-88830262; E-mail: zmyin@163.com