J. Cent. South Univ. (2016) 23: 2397-2401
DOI: 10.1007/s11771-016-3298-3

Time-domain CFD computation and analysis of acoustic attenuation performance of water-filled silencers
LIU Chen(刘晨)1, JI Zhen-lin(季振林)2, CHENG Yin-zhong(程垠钟)1, LIU Sheng-lan(刘胜兰)1
1. Department of Power Engineering, China Ship Research and Development Academy, Beijing 100192, China;
2. School of Power and Energy Engineering, Harbin Engineering University, Harbin 150001, China
Central South University Press and Springer-Verlag Berlin Heidelberg 2016
Abstract: The multi-dimensional time-domain computational fluid dynamics (CFD) approach is extended to calculate the acoustic attenuation performance of water-filled piping silencers. Transmission loss predictions from the time-domain CFD approach and the frequency-domain finite element method (FEM) agree well with each other for the dual expansion chamber silencer, straight-through and cross-flow perforated tube silencers without flow. Then, the time-domain CFD approach is used to investigate the effect of flow on the acoustic attenuation characteristics of perforated tube silencers. The numerical predictions demonstrate that the mean flow increases the transmission loss, especially at higher frequencies, and shifts the transmission loss curve to lower frequencies.
Key words: water-filled silencer; acoustic attenuation performance; time-domain CFD approach; flow effect; perforated tube
1 Introduction
Silencers are widely used to attenuate the noise in pipes [1-2]. Frequency-domain finite element method (FEM) and boundary element method (BEM) are the common approaches for prediction of acoustic attenuation performance of silencers [3-6]. The advantages of these methods are the fast computation and convenient employment. However, the accuracy of these methods is not perfect enough if the influence of flow is included in the computations. Time-domain approach is an alternative method and may overcome this problem. More accurate results may be obtained by considering the effects of complex flow and medium viscosity on the sound attenuation in silencer computation, which is a great advantage of the time-domain approach.
The two-dimensional (2-D) axisymmetric CFD method was proposed by MIDDELBERG et al [7] to calculate the acoustic attenuation characteristics of circular expansion chamber mufflers, and their predictions agree well with the published experimental data [7]. BROATCH et al [8] studied a simple expansion chamber and a reversing chamber muffler by a 3-D time-domain approach based on the CFD simulation for the impulse test technique, and the transmission loss results of these silencers agree fairly well with the experiment measurements and FEM results without air flow. However, the calculated transmission loss at low Mach number mean flow (M=0.07) is not validated with experiment. Later, the 3-D time-domain CFD approach was extended to calculate the acoustic attenuation performance of perforated tube reactive silencers and resonators without and with air flow by JI et al [9] and LIU et al [10], and the predictions agree well with the available experimental data in the literature. LIU et al [11] employed the multi-dimensional CFD approach to calculate the transfer matrix of an exhaust muffler without and with gas flow, and the noise reduction derived from the transfer matrix and radiation impedance was compared with the measured results without gas flow to validate the accuracy of the CFD approach. Then, the effect of mean flow on the noise reduction was discussed. TORREGROSA et al [12] and PISCAGLIA et al [13] paid attention to the spurious reflections of non-reflecting boundary conditions (NRBCs) in a CFD commercial code, and developed new NRBCs for the 3-D time-domain analysis.
However, the aforementioned works have been focused on the predictions of acoustic attenuation characteristics of air-filled silencers. The noise in water- filled pipes is an important noise source in several special engineering practices and needs to be attenuated by using silencers. To the best knowledge of the authors, the related researches on the acoustic computation and analysis of time-domain approach for water-filled piping silencers are not available in the literature. The objectives of the present work are then 1) to extend the multi-dimensional time-domain CFD approach to predict the acoustic attenuation performance of water-filled silencers, and 2) to examine the influence of volume flow rate on the acoustic attenuation performance of perforated tube silencers.
2 Time-domain CFD approach
2.1 Principle and computational method
The model for transmission loss calculation by using the multi-dimensional time-domain CFD approach is shown in Fig. 1. The inlet and outlet of silencer are connected with long tubes, and two pressure monitoring points are placed in the appropriate locations of the upstream and downstream tubes. The pressure far field was used as the inlet and outlet boundary conditions in the CFD model of air-filled silencers to reduce the lengths of upstream and downstream tubes [11]. However, this boundary condition is not applicable in the present work, because the host medium is water. Then, an impulse signal (acoustic excitation) is imposed at the inlet of upstream tube, and the time histories of the pressures at the two monitoring points can be acquired through the unsteady CFD computation. After the interference signals caused by wave reflection are removed from the pressure signals at the two monitoring points, incident and transmitted sound pressures may be obtained subsequently. Finally, the incident and transmitted pressure signals in the time-domain are transformed into the frequency-domain by FFT, and the transmission loss of silencer could be determined by
(1)
where pin is the sound pressure of incident wave at the upstream monitoring point of silencer, ptr is the sound pressure of transmitted wave at the downstream monitoring point of silencer, Ai and Ao are the cross-sectional areas of the inlet and outlet of silencer, respectively [14].
It should be noted that the incident and transmitted pressure signals at the two monitoring points to be Fourier transformed are not contaminated by reflected waves. Therefore, the lengths of the upstream and downstream tubes and the locations of two monitoringpoints must be selected reasonably, so as to allow the reflected signals from the silencer and downstream tube termination to arrive at the monitoring points at a time after which the incident and transmitted signals have attenuated to the stable conditions. In order to acquire reasonable predictions, the lengths of inlet and outlet tubes should exceed forty times the length of the silencer after many tentative calculations. The choice for the locations of two monitoring points is determined from the method proposed by SINGH and KATRA [15].
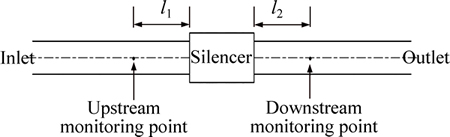
Fig. 1 Scheme for transmission loss calculation of a silencer
2.2 CFD computation
In the present work, the software Fluent is used as the computational tool, which is based on the finite volume method. The pressure-based implicit solver with the second order implicit time stepping is implemented. The pressure-velocity coupling scheme is PISO algorithm, and the second order scheme is chosen for the spatial discretization. Laminar model and realizable k-ε turbulence model are chosen for the stationary medium and mean flow, respectively.
The working medium in the calculations is water. The compressibility of water is simulated by the user- defined functions in software Fluent and other physical properties are determined by water temperature. The boundary conditions are set as follows.
1) The mass flow inlet boundary condition is used in the models. An impulse signal superimposed on a constant mass flow is imposed on the inlet of upstream pipe. The impulse is a half period of sinusoidal wave of a frequency of 12.8 kHz and mass flow amplitude of 35 g/(m2·s). After the impulse signal is completed, the pipe inlet remains the constant mass flow for the remainder of the solution.
2) The pressure outlet boundary condition is applied to the outlet of computational model.
3) The walls are considered as stationary, adiabatic and no-slip.
In the computations, the time step is 1 μs, and the corresponding sampling frequency is 1000 kHz, which is much higher than the maximum of the effective frequency in acoustic excitation signal, so that the sampling law is satisfied.
3 Results and analyses
For the sake of saving the time consuming for the time-domain CFD approach, the 2-D axisymmetric models are used for the calculation of dual expansion chamber silencer and the rotationally periodic boundary condition (3-D model) is used for the perforated tube silencers.
The double expansion chamber silencer consists of two expansion chambers with one inter-connecting tube (Fig. 2), and the dimensions are: D=400 mm for the inner diameter of chamber, l1=600 mm and l2=400 mm for the lengths of the first and second chambers, respectively, di=dc=do=200 mm for the inner diameters of inlet tube, inter-connecting tube and outlet tube, respectively, li= 200 mm for the extended length of the inlet tube into the first chamber, lc1=lc2=200 mm for the extended lengths of inter-connecting tube into the first and second chambers, respectively. The computational model is discretized with structured mesh of 6 mm.
The transmission loss predictions from the 2-D time-domain CFD approach and FEM are compared for the double expansion chamber silencer without flow (Fig. 3), and good agreement between them is observed.
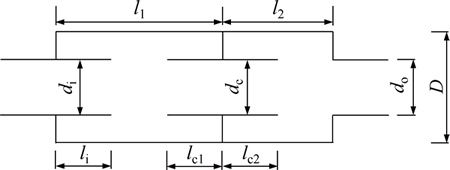
Fig. 2 Double expansion chamber silencer
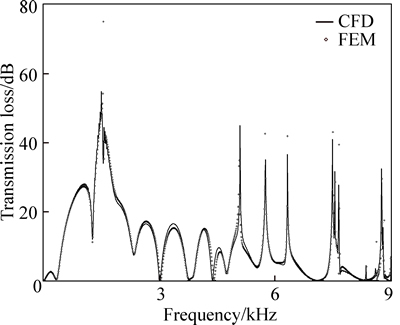
Fig. 3 Comparison of transmission loss results of double expansion chamber silencer (T=293 K, Q=0 m3/h)
The straight-through perforated tube silencer as shown in Fig. 4 is considered next. The dimensions of the silencer are as below: D=110 mm for the inner diameter of chamber, l=200 mm for the length of chamber, d=32 mm for the inner diameter of perforated tube, tw=2 mm for the thickness of perforated tube, dh=4 mm for the diameter of hole and porosity σ=4.7%. In the computational model, the inlet and outlet tubes are discretized with structured mesh of less than 2.5 mm, the silencer is discretized with unstructured mesh of less than 0.85 mm, and the region near the perforation is refined further.
Figure 5 compares the transmission loss predictions of the straight-through perforated tube silencer from the 3-D time-domain CFD approach and FEM for the case without flow (the perforations are directly built in CFDand FEM models.), and good agreement between them is observed in the frequency range of interest. The numerical predictions showed that the transmission loss of straight-through perforated tube silencer consists of dome attenuation at lower frequencies and axial resonances at higher frequencies.
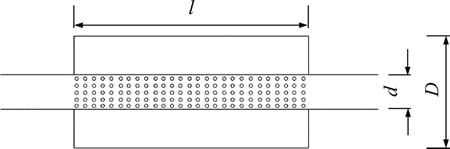
Fig. 4 Straight-through perforated tube silencer
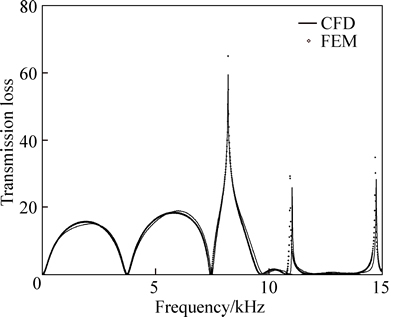
Fig. 5 Comparison of transmission loss results of straight- through perforated tube silencer (T=288 K, Q=0 m3/h)
The effect of volume flow rate on the transmission loss of straight-through perforated tube silencer is examined and depicted in Fig. 6. The volume flow increases the acoustic attenuation at most frequencies and slightly reduces the resonant peaks, which may be explained by the fact that the acoustic resistance of perforation increases as the flow velocity increasing.
The cross-flow perforated tube silencer as shown in Fig. 7 is studied in the last, and the dimensions are:D=110 mm for the inner diameter of chamber, l1=l2=100 mm for the lengths of inlet and outlet perforated tubes, respectively, d=32 mm for the inner diameter of perforated tube. The wall thickness of perforated tube is tw=2 mm, dh=8 mm for the hole diameter and porosity σ=10.7%. In the time-domain CFD computation, the inlet and outlet tubes are discretized with structured mesh of less than 2.2 mm, the silencer is discretized with unstructured mesh of less than 0.65 mm, and the region near the perforation is refined further.
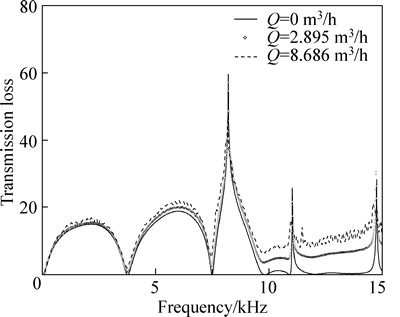
Fig. 6 Comparison of transmission loss results of straight- through perforated tube silencer with mean flow (T=288 K)
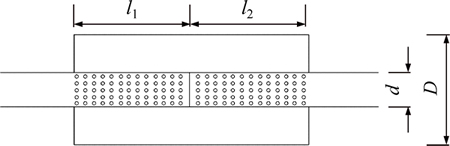
Fig. 7 Cross-flow perforated tube silencer
The transmission loss predictions of the cross-flow perforated tube silencer from the 3-D time-domain CFD approach and FEM for the case without flow are depicted in Fig. 8. When the frequency exceeds 9 kHz, there are small discrepancies between them. Although the perforations are directly simulated in the FEM model, the viscosity of water is not considered in the finite element calculation. As a result, the resonant peak of FEM prediction is higher than that of time-domain CFD result around 9.5 kHz. The difference in the trough at 10 kHz may also be attributed to the effect of water viscosity. In addition, the working medium is regarded as incompressible in the FEM model, and the sound speed is a constant. The differences between the sound speed in the time-domain CFD approach and FEM are responsible for the frequency shift in transmission loss curve. The comparison between Fig. 5 and Fig. 8 reveals that the cross-flow perforated tube silencer is more sensitive to the viscosity of medium than the straight-through perforated tube silencer, which may be related to the propagation path of sound wave.
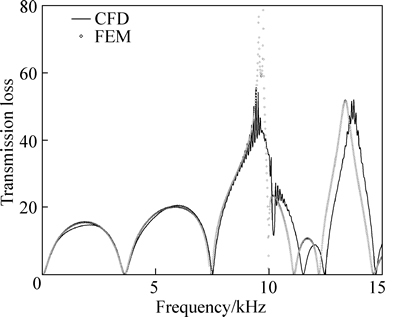
Fig. 8 Comparison of transmission loss results of cross-flow perforated tube silencer (T=288 K, Q=0 m3/h)
The influence of volume flow rate on the acoustic attenuation performance of cross-flow perforated tube silencer is similar to that of straight-through perforated tube silencer (Fig. 9). However, the transmission loss increases throughout the frequencies of interest as the volume flow increasing, which may be attributed to the facts that the acoustic resistance of perforation increases and the effective flow-path areas in the holes decrease as the volume flow increasing. The frequency shift in the transmission loss curve is due to the convective effect.
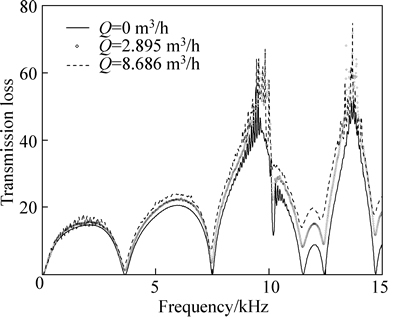
Fig. 9 Comparison of transmission loss results of cross-flow perforated tube silencer with mean flow (T=288 K)
4 Conclusions
1) The multi-dimensional time-domain CFD approach is extended to calculate the transmission loss of water-filled piping silencers, and the present time- domain CFD predictions agree well with the FEM results in the absence of flow.
2) The time-domain CFD method is used to examine the influence of volume flow rate on the acoustic attenuation characteristics of straight-through and cross-flow perforated tube silencers. The time- domain CFD predictions demonstrate that the volume flow increases the acoustic attenuation at most frequencies and shifts the transmission loss curve to lower frequency somewhat.
References
[1] REHMAN H, CHUNG H, JOUNG T, SUWONO A, JEONG H. CFD analysis of sound pressure in tank gun muzzle silencer [J]. Journal of Central South University of Technology, 2011, 18(6): 2015-2020.
[2] ZHANG Meng-hao, ZUO Shu-guang, XIANG Long-yang, HU Jia-jie. Transmission loss theoretical calculation and analysis of double-layer micro-perforated muffler [J]. Journal of Central South University: Science and Technology, 2015, 46(2): 505-510. (in Chinese)
[3] ROSS D F. A finite element analysis of perforated component acoustic systems [J]. Journal of Sound and Vibration, 1981, 79(1): 133-143.
[4] ZHAO Hai-jun, DENG Zhao-xiang, YANG Jie, PAN Fu-sheng. Comparison of numerical methods for calculating transmission loss in inserted ducts muffler and parameters analysis [J]. Chinese Internal Combustion Engine Engineering, 2008, 29(6): 65-69. (in Chinese)
[5] JI Z L, SELAMET A. Boundary element analysis of three-pass perforated duct mufflers [J]. Noise Control Engineering Journal, 2000, 48(5): 151-156.
[6] WU T W, CHENG C Y R, TAO Z. Boundary element analysis of packed silencers with protective cloth and embedded thin surfaces [J]. Journal of Sound and Vibration, 2003, 261(1): 1-15.
[7] MIDDELBERG J M, BARBER T J, LEONG S S, BYRNE K P, LEONARDI E. CFD analysis of the Acoustic and mean flow performance of simple expansion chamber mufflers [C]// Proceedings of the International Mechanical Engineering Congress and Exposition. New York, USA: American Society of Mechanical Engineers, 2004: 1-6.
[8] BROATCH A, MARGOT X, GIL A, DENIA F D. A CFD approach to the computation of the acoustic response of exhaust mufflers [J]. Journal of Computational Acoustics, 2005, 13(2): 301-316.
[9] JI Z L, XU H S, KANG Z X. Influence of mean flow on acoustic attenuation performance of straight-through perforated tube reactive silencers and resonators [J]. Noise Control Engineering Journal, 2010, 58(1): 12-17.
[10] LIU Chen, JI Zhen-lin, XU Hang-shou. Three-dimensional time- domain computation and analysis of acoustic attenuation performance of perforated tube silencers [J]. Journal of Mechanical Engineering, 2012, 48(10): 7-13. (in Chinese)
[11] LIU L Y, HAO Z Y, LIU C. CFD analysis of a transfer matrix of exhaust muffler with mean flow and prediction of exhaust noise [J]. Journal of Zhejiang University: Science A, 2012, 13(9): 709-716.
[12] TORREGROSA A J, FAJARDO P, GIL A, NAVARRO R. Development of nonreflecting boundary condition for application in 3D computational fluid dynamic codes [J]. Engineering Applications of Computational Fluid Mechanics, 2012, 6(3): 447-460.
[13] PISCAGLIA F, MONTORFANO A, ONORATI A. Development of a non-reflecting boundary condition for multidimensional nonlinear duct acoustic computation [J]. Journal of Sound and Vibration, 2013, 332(4): 922-935.
[14] MUNJAL M L. Acoustic of ducts and mufflers [M]. New York, USA: Wiley-Interscience, 1987: 42-150.
[15] SINGH R, KATRA T. Development of an impulse technique for measurement of muffler characteristics [J]. Journal of Sound and Vibration, 1978, 56(2): 279-298.
(Edited by DENG Lü-xiang)
Foundation item: Project(11174065) supported by the National Natural Science Foundation of China
Received date: 2015-06-01; Accepted date: 2015-08-09
Corresponding author: JI Zhen-lin, PhD, Professor; Tel: +86-451-82588822-318; E-mail: zhenlinji@yahoo.com