Microstructures, mechanical and oxidation behaviors of C/C composites modified by NiAl alloy
Hua-chan FANG, Peng XIAO, Xiang XIONG, Guang-jun YU
State Key Laboratory of Powder Metallurgy, Central South University, Changsha 410083, China
Received 8 February 2015; accepted 10 November 2015
Abstract: Carbon/carbon composites modified by NiAl alloy were prepared using vacuum reactive melt infiltration methods with NiAl and titanium mixed powders as raw materials. The microstructures were investigated by scanning electron microscopy. The fracture behavior, infiltration and oxidation mechanism were further discussed. The results indicated that NiAl alloy exhibited good wettability on the C/C preform because a TiC reaction layer formed at the interface. Multi-layer (PyC/TiC/NiAl+TiC) coating evenly and compactly distributed on the surface of the carbon fiber in tubular form. The penetration depth of molten NiAl alloys depended on the reaction between the PyC and titanium. The impact fracture was inclined to along the interface between the NiAl permeability layer and C/C matrix. Al2TiO5 and TiO2 formed on the surface, while the interior multi-layer tubular structure partially remained after oxidation at 1773 K for 30 min.
Key words: carbon/carbon composites; interface; NiAl; multilayer structure; oxidation
1 Introduction
Carbon fiber reinforced carbon matrix composites (C/C) are expected to be applied as a potential high-temperature structural material for engineering and aerospace applications, due to their unique and excellent properties of high specific strength, high thermal conductivity and high specific stiffness at temperatures above 2273 K [1-3]. However, rapid oxidation above 673 K in an oxidizing environment restricts their high temperature applications [4]. Therefore, C/C composites need to be infiltrated with ultra-refractory materials such as metals and carbides/borides [5-8] to improve their anti-oxidation property at high temperature. Combined with the anti-ablation of ultra-high temperature ceramics and high ductility, thermal shock resistance of metallic materials to modify C/C composites may be an effective method for addressing this issue.
NiAl is recognized as a promising candidate for high temperature structural applications, due to its high melting point (1913 K), superplasticity (1073-1373 K, 480%) and excellent creep resistance at high temperature [9-11]. Using high temperature super- plasticity, high temperature oxidation resistance, and high temperature strength of NiAl intermetallic compound to improve the oxidation resistance of C/C composites has not been reported. However, it is very difficult to directly infiltrate NiAl to C/C composite because of the poor wetting [12]. Titanium possesses good wettability on the surface of C/C composites preform. RAN et al [13,14] prepared C/C-Cu composites through reactive melt infiltration (RMI) process using titanium as an active additive. It is revealed that the improvement of adding small amount of titanium for molten copper infiltration into the C/C composites preform results from the improvement of the chemical and physical adsorption characteristic of copper on the composites. The liquid copper alloy infiltrates into the preform under the capillary pressure. YU et al [12] also indicated that adding a small amount of Ti to NiAl may improve its wettability on carbon, and improve the interface bonding by forming a TiC layer. In the present research, using titanium as an active additive, a NiAl modified C/C composite was fabricated by vacuum reactive melt infiltration. The microstructures, fracture and oxidation behavior were obtained. The infiltration and oxidation mechanisms were investigated.
2 Experimental
NiAl (150 μm, 99.95% purity) and titanium (50 μm, 99% purity) powders were used as raw materials. The infiltrating agent was mixed according to the composition of 15% Ti and 85% NiAl (mass fraction). The porous C/C preforms with a density of 1.35 g/cm3 were embedded in the infiltrating agent in a crucible. They were placed in a vacuum furnace and heated at 2073 K for 1 h, then cooled to room temperature.
Phase analysis was conducted by X-ray powder diffraction using a D/Max2550 X-ray diffractometer (Rigaku, Japan) with Cu Kα radiation. Microstructural characterization was carried out using scanning election microscopy (SEM, NOVATM Nano SEM230 and JSM-6360LV) with energy-dispersive spectrometry (EDS). Electron probe microanalysis (EPMA, JEOLCO, JXA8530F) was performed to detect the distributions of the major elements in the composites.
The density of the composite was measured by the Archimedes water-immersion method using Sartorius cp224 s densitometer at room temperature. The open porosity was measured using air displacement method by filling the pores with kerosene under vacuum. Flexural strength was measured using a three-point bending test (Instron3369, UK) with a span of 40 mm. The crosshead speed was 2.00 mm/min. At least three specimens with dimensions of 55 mm × 5.0 mm × 3.0 mm were tested to obtain the average data. After three-point flexural tests, the fracture surfaces were observed by a scanning electron microscopy (SEM, JSM-6360LV).
The isothermal oxidation tests of the composites were carried out at 1773 K in air in an electrical resistance furnace. The samples after oxidation test for 30 min were analyzed by SEM and XRD with Cu Kα radiation.
3 Experimental
3.1 Microstructures
Surface SEM images and XRD patterns of the NiAl modified C/C composites are presented in Fig. 1. High densities of gray micron-sized particles are homogeneously distributed in the matrix surface. XRD pattern of the surface in Fig. 1(a) reveals that the phases of the composites mainly consist of NiAl, TiC and C, while the Ti phase is hardly detected. The composition of the white phases is determined by EDS to be 49.55 % Ni, 50.45 % Al. The composition of the gray large particles is 37.45 % C, 67.55 % Ti (mole fraction). Combining the EDS analysis and the results of XRD (Fig. 2(a)), it is obtained that the white phases and the gray large particles are determined as NiAl and TiC, respectively.
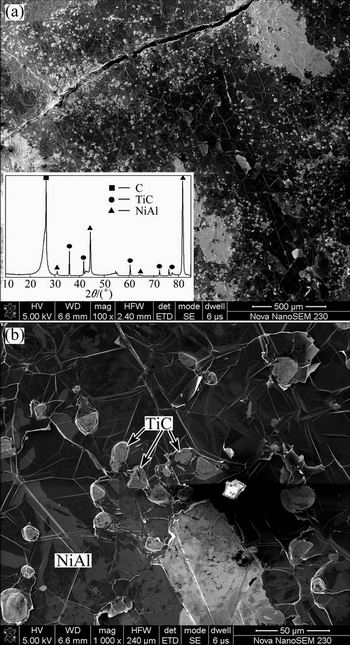
Fig. 1 Surface SEM images and XRD pattern of NiAl modified C/C composites
Cross-section SEM images of the composites are presented in Fig. 2. The metallic diffused layer of 0.8-0.9 mm in Fig. 2(a) shows that the inter-bundle and the inter-layer pores are not filled completely by the infiltrated NiAl metal. Combining the EDS analysis and the results of XRD (Fig. 2(a)), it is obtained that the white phases and the gray large particles are determined as NiAl and TiC, respectively. NiAl melts dispersed with micron-sized gray TiC particles are combined closely, while the interfaces between C/TiC and TiC/NiAl are perfectly bonded and free of pores and microcracks (Fig. 2(b)).
According to the EMPA results of the diffused layer in Fig. 3, Ni and Al elements are distributed around carbon fiber and Ti element, the distribution of Ni and Al is almost uniform. Titanium is mainly distributed around the carbon fiber and carbon matrix in the form of TiC layer or TiC particles. Combined with the XRD results shown in Fig. 1(a), it is inferred that the particles consist of TiC, surrounded by residual NiAl melt. TiC phases are resulted from the reaction between the PyC and titanium powder after reactive melt infiltration process. TiC distributes around PyC inside the pores in the C/C preform and NiAl locates in the middle of pores surrounded by TiC.
Fiber cross-sectional micrograph and element line scanning EDS analyses of the fiber in the diffused layer are displayed in Fig. 4(a). It can be seen from Fig. 4(a) that a tubular structure is enwrapped on the surface of carbon fiber. Element line scanning EDS analysis confirms that the Ti content close to the carbon fiber is apparently higher, while the concentrations of Ni and Al in the outer layer of the tubular structure is relatively higher. This indicates that the TiC reaction layer is formed in situ reaction with PyC during the vacuum reactive melt infiltration process. In general, multi-layer (PyC/TiC/NiAl+TiC) coating with a thickness of about 5 μm evenly and compactly distributes on the surface of the carbon fiber in tubular form (Fig. 4(b))
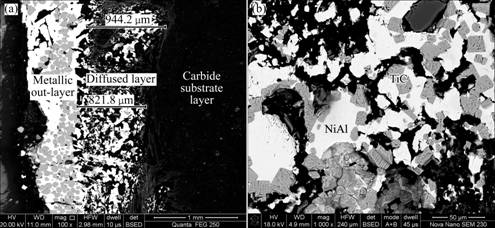
Fig. 2 Cross-section images of NiAl modified C/C composites
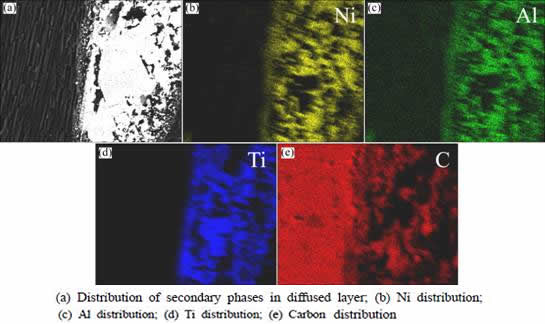
Fig. 3 SEM images of representative cross-section and corresponding elemental analysis results of NiAl modified C/C composites
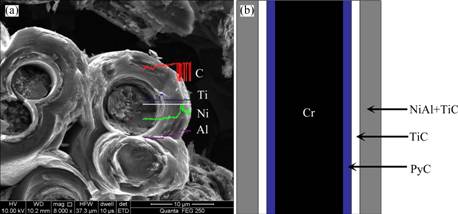
Fig. 4 SEM image of fiber cross-section and element line scanning EDS analyses (a) and schematic diagram (b) of fiber in diffused layer
3.2 Physical and mechanical properties
Typical load-displacement curves of the flexural strength test for the original and the NiAl modified C/C composites are given in Fig. 5. For the NiAl modified C/C composite, an increasing quasi-linear stress up to the maximum is followed by a smooth and gentle decline region, showing a typical pesudo-plastic fracture characteristic.
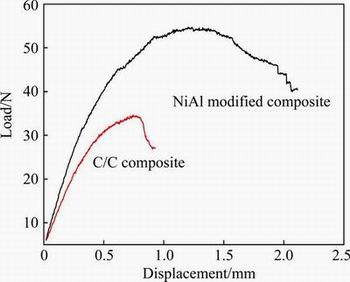
Fig. 5 Typical flexural load-displacement curves of original and NiAl modified C/C composites
Physical properties and flexural strength of the original and the NiAl modified C/C composites are summarized in Table 1. Compared with the original C/C composites showing a density of 1.35 g/cm3, an open porosity of 27% and a flexural strength of 40.5 MPa, the density increases to 2.47 g/cm3 and the final open porosity decreases to 15.1% after melt infiltration. This indicates that the molten NiAl alloy has been drawn into porous C/C preform to some extent. However, there is no significant difference in the flexural strength. It is inferred in Fig. 2(a) that the inter-bundles and inter-pores are not infiltrated with metallic melt. Great amount of inter-pores might be one of key reasons for their low flexural strength. Moreover, the interface reaction, damage of fiber, strong or weak interface bonding obviously influence the fabrication process and strength of the NiAl modified C/C composites.
Table 1 Density, open porosity and flexural strength of original and NiAl modified C/C composites
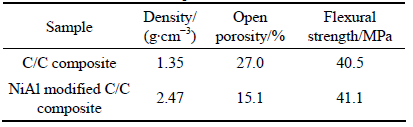
3.3 Fracture behavior
SEM images of fracture surfaces of the composites after the bending test are shown in Fig. 6. As revealed in Fig. 6(c), the fracture occurs at the interface between the NiAl diffused layer and C/C matrix. NiAl diffused layer with dispersive distribution of TiC particle entraining carbon fibers are split from the C/C matrix. The fracture surface in the diffused layer region contains quantities of multi-layered microstructures (Fig. 6(a)). NiAl and fibers are bonded well, with the continuous metal matrix surrounding the fiber very tightly, as confirmed by high-magnification SEM image (top-right corner in Fig. 6(b)). Most of the pulled-out fibers are shorter and their fracture surfaces are rough. Figure 6(d) shows that the fibers are coated in patches with finer particles. EDS analysis reveals that the particles are TiC. Presumably, they are generated in situ from the carbon fibers. High thermal conductivity of NiAl [15] and a strengthening interfacial bonding strength between NiAl/TiC and TiC/PyC can reduce the thermal stress. The multi-layered microstructures can absorb energy when fibers pull-out, which is beneficial to the improvement of strength and toughness.
3.4 Oxidation surface
The isothermal oxidation tests on the NiAl modified C/C composites were carried out in static air at 1773 K. Figure 7 shows the mass changes of the composites as a function of oxidation time. The mass loss of the composite increases almost linearly with oxidation time throughout the oxidation process. After oxidation for 10 min, the mass loss of the composite is about 2.85%. As the oxidation time increases to 30 min, the mass loss increases up to 8.68%. Some large size cracks can be found on the surface of the composites from Fig. 1(a) because of the higher thermal expansion coefficient (CTE) of NiAl than that of C/C substrate. After oxidation, oxygen can permeate into the C/C matrix and the oxidation occurs.
Surface morphology of the composite after isothermal oxidation test in Fig. 8 shows that obvious holes can be found on the surface after oxidation for 10 min. After 30 min of oxidation, many cracks appear, and the surface oxide layer lifts. Moreover, white oxide scale can be observed on the surface of the as-oxidized NiAl modified C/C composites.
Surface and inner substrate SEM images of the NiAl modified C/C composites after oxidation at 1773 K for 30 min are displayed in Fig. 9. According to the results of XRD pattern (bottom-right corner in Fig. 9(a)), Al2TiO5 phase and TiO2 phase can be observed on the surface after oxidation. The surface is relatively rough with some inherent defects such as microcracks and holes (Fig. 9(b)). In the inner substrate, carbon fibers become thinner and sharper because the erosion firstly occurs at the interface between fiber and multi-layered (TiC/NiAl+TiC) coating. The multi-layered metal coating is preserved in some degree (Fig. 9(c)). In the multi-layered cannular microstructures, the NiAl-TiC outer layer has been oxidized into Al2TiO5 (Area A in Fig. 9(d)), while closest to the fiber consists of partial oxidized NiAl-TiC (Area B in Fig. 9(d)).
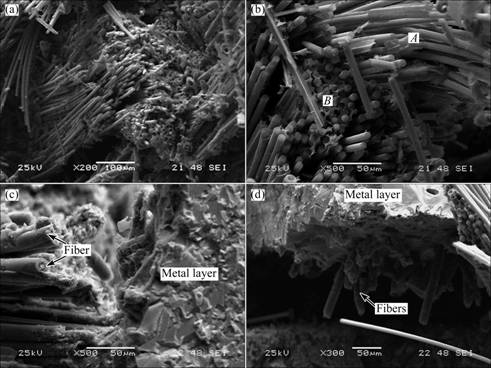
Fig. 6 SEM images of fracture surfaces of composites at different magnification after bending test showing continuous metal matrix surrounding fiber and (d) nano-sized TiC particles agglomerated together on carbon fiber
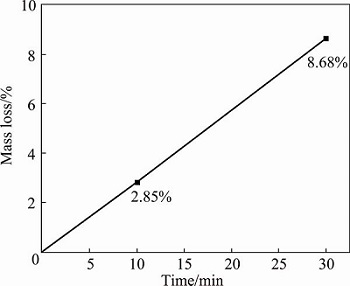
Fig. 7 Isothermal oxidation curve of NiAl modified C/C sample in static air at 1773 K
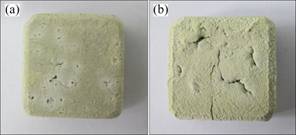
Fig. 8 Macro morphologies of NiAl modified C/C sample after oxidation at 1773 K for 10 min (a) and 30 min (b)
4 Discussion
4.1 Infiltration mechanism
The infiltrating process of NiAl and titanium mixed powders on C/C perform during the vacuum reactive melt infiltration process can be explained in Fig. 10. Firstly, molten titanium penetrates into C/C preform preferentially to form TiC, then the molten NiAl alloy infiltrates along the TiC reaction layer. Secondly, carbon atoms diffuse through the TiC layer and arrive at TiC/NiAl interface. Finally, TiC reaction terminates when titanium is exhausted, the infiltrating process stops. The factors affecting the infiltration of NiAl are as follows: 1) Inhomogeneous distribution of TiC; 2) Molten Ti is difficult to further diffusion when TiC interface layer formed and the TiC layer grows up slowly due to the lack of Ti (Ti diffuses slowly); 3) Theinter-layer pores are easily blocked due to the strong reaction between Ti and C. Hence, the death of NiAl diffused layer on C/C composite is 0.8-0.9 mm.
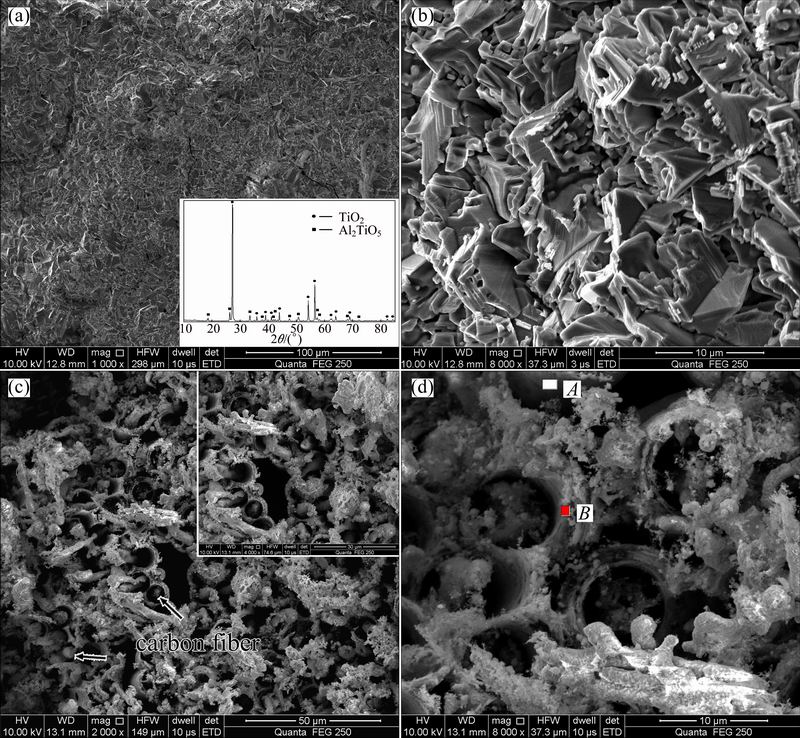
Fig. 9 SEM images of surface (a, b) and inner substrate (c, d) of NiAl modified C/C composite after oxidation at 1773 K for 30 min
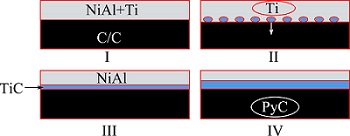
Fig. 10 Schematic illustrations showing wetting process and infiltration mechanism of C/C composites modified by NiAl alloy in vacuum reactive melt infiltration process (2073 K, 1 h)
4.2 Oxidation behavior
The possible reactions during the oxidation testing are as follows:
4NiAl+3O2→2Al2O3+4[Ni](1)
2TiC+3O2→2TiO2+2CO(2)
TiO2+Al2O2→2Al2TiO5(3)
Oxidation of NiAl does not result in the formation of NiO [16,17]. The free [Ni] atom moves to the inner matrix to form Ni-rich area (Eq. (1)). Al2O3 and TiO2 phases derive from the oxidation of NiAl and TiC (Eqs. (1) and (2)), and then TiO2 reacted with α-Al2O3 to produce Al2TiO5 at 1573 K (Eq. (3)). Al2TiO5 phase is the only thermodynamic stable compound for the Al2O3-TiO2 system [18]. Al2TiO5 phase possesses excellent thermal shock resistance, high melting point, and lower thermal expansion coefficient (average CTEAl2TiO5=1.0×10-6-1.5×10-6/K, at 298-1373 K), which is close to that of PyC (CTEC=0-2.2×10-6/K at 293-2273 K) [19]. Hence, it can effectively relieve the high thermal mismatch between NiAl, TiC and C when it exposed to high temperature.
5 Conclusions
1) Porous C/C preforms have been infiltrated with NiAl to a maximum depth of 0.8-0.9 mm by vacuum infiltrating process.
2) In situ formation of TiC reaction layer at the interface results in infiltration of the molten NiAl alloys. Multi-layered (PyC/TiC/NiAl+TiC) coating enwraps around the carbon fiber evenly and compactly.
3) Blocked holes, inhomogeneous distribution of TiC and a slowing growth of TiC layer inhibit the infiltration.
4) Fracture occurs at the interface between the NiAl diffused layer and C/C matrix.
5) Al2TiO5 and TiO2 are formed on the surface and the TiC/NiAl+TiC multi-layered metal coatings are partially preserved after oxidation at 1773 K.
References
[1] IMMARIGEON J P, HOLT R T, KOUL A K, ZHAO L, WALLACE W, BEDDOES J C. Lightweight materials for aircraft applications [J]. Materials Characterization, 1995, 35(1): 41-67.
[2] HUDA Z, EDI P. Materials selection in design of structures and engines of supersonic aircrafts: A review [J]. Materials Design, 2013, 46: 552-560.
[3] VIGNOLES G L, ASPA Y, QUINTARD M. Modelling of carbon-carbon composite ablation in rocket nozzles [J]. Composites Science and Technology, 2010, 70(9): 1303-1308.
[4] HUANG J F, YANG W D, CAO L Y. Preparation of a SiC/Cristobalite-AlPO4 multi-layer protective coating on carbon/carbon composites and resultant oxidation kinetics and mechanism [J]. Journal of Materials Science & Technology, 2010, 26(11): 1021-1026.
[5] REN X R, LI H J, FU Q G, LI K Z. Ultra-high temperature ceramic TaB2-TaC-SiC coating for oxidation protection of SiC-coated carbon/carbon composites [J]. Ceramics International, 2014, 40(7): 9419-9425.
[6] ZENG Y, XIONG X, LI G D, CHEN Z K, SUN W, WANG D N, WANG Y L. Effect of fiber architecture and density on the ablation behavior of carbon/carbon composites modified by Zr-Ti-C [J]. Carbon, 2013, 63: 92-100.
[7] LIU Chun-xuan, CHEN Jia-xun, SU Zhe-an, YANG Xin, CAO Liu-xu, HUANG Qi-zhong. Pyrolysis mechanism of ZrC precursor and fabrication of C/C-ZrC composites by precursor infiltration and pyrolysis [J]. Transactions of Nonferrous Metals Society of China, 2014, 24(6): 1779-1784.
[8] LI He-jun, YAO Xi-yuan, ZHANG Yu-lei, YAO Dong-jia, WANG Shao-long. Anti-oxidation properties of ZrB2 modified silicon-based multilayer coating for carbon/carbon composites at high temperatures [J]. Transactions of Nonferrous Metals Society of China, 2013, 23(7): 2094-2099.
[9] STOLOFF N S, LIU N S, DEEVI S C. Emerging applications of intermetallics [J]. Intermetallics, 2000, 8(9-11): 1313-1320.
[10] OU Tao-ping, CAO Guang-hui. Preparation processes of Ni-Al-based coatings and their oxidation resistance [J]. The Chinese Journal of Nonferrous Metals, 2012, 22(6): 1725-1730. (in Chinese)
[11] HU W, WEIRICH T, HALLSTEDT B, CHEN H, ZHONG Y, GOTTSTEIN G. Interface structure, chemistry and properties of NiAl composites fabricated from matrix-coated single-crystalline Al2O3 fibres (sapphire) with and without an hBN interlayer [J]. Acta Materialia, 2006, 54: 2473-2488.
[12] YU Guang-jun, XIAO Peng, FANG Hua-chan. Influence of adding Ti on molten NiAl intermetallic infiltration into C/C composites [J]. The Chinese Journal of Nonferrous Metals, 2013, 23(12): 3316-3322. (in Chinese)
[13] RAN Li-ping, ZHOU Wen-yan, ZHAO Jian-xin, YI Mao-zhong, YANG Lin. Mechanical properties of C/C-Cu composites fabricated by molten infiltration method [J]. The Chinese Journal of Nonferrous Metals, 2011, 21(7): 1607-1613. (in Chinese)
[14] YI Zhen-hua, YI Mao-zhong, RAN Li-ping, YANG Lin. Influence of adding Ti on molten copper infiltration into C/C composites[J]. The Chinese Journal of Nonferrous Metals, 2006, 16(7): 1214-1218. (in Chinese)
[15] GAO M X, PANA Y, OLIVEIR F J, BAPTISTA J L, VIEIRA J M. Interpenetrating microstructure and fracture mechanism of NiAl/TiC composites by pressureless melt infiltration [J]. Materials Letters, 2004, 58(11): 1761-1765.
[16] GRABKE H J. Oxidation of NiAl and FeAl [J]. Intermetallics, 1999, 7 (10): 1153-1158.
[17] ZHANG Guang-ye, ZHANG Hua, TANG Guo-ning, GUO Jian-ting, LIAO Yan-chun, LI Mao-hua. Oxidation behavior of NiAl and NiAl-based alloys [J]. Materials Review, 2006, 20(3): 71-75.
[18] ARENAS I B. Reactive sintering of aluminum titanate [J]. Sintering of Ceramics-New Emerging Techniques, 2012, 2: 501-526.
[19] BUESSUM W R, THIEKE N R, SARAKAUSKAS R V. Thermal expansion hysteresis of aluminum titanante [J]. Ceramics Age, 1952, 60: 38-40.
NiAl改性C/C复合材料的组织、力学性能和氧化行为
方华婵,肖 鹏,熊 翔,於广军
中南大学 粉末冶金国家重点实验室,长沙 410083
摘 要:以NiAl和钛的混合粉为原料,采用真空熔渗法制备了NiAl改性C/C复合材料,利用扫描电镜观察了复合材料的显微组织,分析了其断裂行为、渗透机制和氧化机制。结果表明:界面反应形成的TiC提高了NiAl对C/C多孔体的润湿性,且均匀致密的PyC/TiC/NiAl+TiC多层空间管状网络结构包覆在碳纤维表面,而NiAl合金的渗透深度则取决于热解碳与钛的反应。复合材料倾向于在NiAl渗透层和未渗透的C/C界面处断裂。经1773 K氧化30 min后的复合材料表面生成钛酸铝(Al2TiO5)和氧化钛(TiO2),内部的多层空间管状网络结构得以部分保留。
关键词:C/C复合材料;界面;NiAl;多层结构;氧化
(Edited by Yun-bin HE)
Foundation item: Project (2011CB605804) supported by the National Basic Research Development Program of China; Project (2015JJ3167) supported by the Natural Science Foundation of Hunan Province, China; Project (2013M531810) supported by the Postdoctoral Science Foundation of China
Corresponding author: Peng XIAO; Tel: +86-731-88830131; Fax: +86-731-88710855; E-mail: xiaopeng@csu.edu.cn
DOI: 10.1016/S1003-6326(16)64106-7