
Flow stress of 2197 Al-Li alloy during hot compression deformation
WEI Xiu-yu(魏修宇), ZHENG Zi-qiao(郑子樵), FU Xin(付欣), CHEN Qiu-ni(陈秋妮)
School of Materials Science and Engineering, Central South University, Changsha 410083, China
Received 15 July 2007; accepted 10 September 2007
Abstract: The flow stress behavior of 2197 Al-Li alloy during hot compression deformation was studied in the strain rate range from 0.01 to 10 s-1 and the temperature range from 360 to 510 ℃ by isothermal compression test on a Gleeble-1500 thermal-mechanical simulator. The results show that the flow stress of 2197 Al-Li alloy decreases with the increase of deformation temperature and increases with the increase of strain rate. The peak flow stress during high temperature deformation can be represented by Z parameter in a hyperbolic sine function. The analytical expression of peak flow stress was fitted with the hot deformation activation energy of 260.6 kJ/mol.
Key words: 2197 Al-Li alloy; hot compression deformation; flow stress; Z parameter
1 Introduction
The ongoing thrust within the aerospace industry towards reducing structural airframe mass has resulted in the development of several generations of Al-Li alloys since the 1980s. Compared with conventional aluminum alloys, Al-Li alloy has lower density, higher values of specific strength and modulus, and improved fatigue crack growth rate resistance, therefore is considered one of the most efficient mass-saving structural material for aerospace application [1]. 2197 alloy is a third generation Al-Li alloy registered in 1993 and has been successfully used as bulkheads in F-16 fighter aircraft[2-4].
As it is known, the flow stress behavior and microstructure evolution during practical deformation are the most basic parameters to characterize plastic deformation properties and mechanical properties of metals and alloys. In recent years, investigations on this subject are very active[5-8]. In this study, the flow stress behavior of 2197 Al-Li alloy during hot compression deformation was studied in the strain rate range from 0.01 to 10 s-1 and the temperature range from 350 to 510 ℃ by isothermal compression test on a Gleeble-1500 thermal-mechanical simulator, associated structural changes were studied by transmission electron microscopy(TEM), and the flow stress equation was established through monadic linear regression.
2 Experimental
Industrial scale DC cast 2197 alloy ingot, with chemical composition of 2.87%Cu, 1.48%Li, 0.32%Mn, 0.24%Mg, 0.11%Zr (mass fraction), were used in this investigation. The alloy ingot was homogenized at 510 ℃ for 8 h followed by 530 ℃ for 24 h in salt bath. Cylindrical compression specimens of 15 mm in height and 8 mm in diameter were machined from the homogenized ingot. Concentric annular grooves of 0.2 mm deep were machined at both end faces of the cylinders to retain the lubricant during compression test. Graphite lubricant mixed with machine oil was used in order to minimize the friction between the sample and anvils. Prior to compression, each sample was soaked 3 min at the test temperature to equalize the thermal gradients within the samples. The high-temperature compression tests were carried out on a computer- controlled Gleeble 1500 machine at 350-510 ℃ under various true strain rates of 0.001-10 s-1.
3 Results and discussion
3.1 Stress—strain curves of 2197 alloy
A series of typical true stress—strain curves obtained during hot-compression of 2197 alloy at various temperatures and strain rates are depicted in Fig.1. The results show that at the same strain rates, the higher the deformation temperatures are, the lower the stresses are. At the same deformation temperatures, the flow stress increases with increasing strain rate, which indicates that the alloy has positive strain rate sensitivity under those conditions. At low strain rate and high deformation temperature, the flow stress decreases after a peak value, showing dynamic recrystallization characteristics. And the steady-state flow characteristics exist on other deformation conditions, showing dynamic recovery.
3.2 TEM microstructure
The TEM micrographs of 2197 alloy under different deformation conditions are shown in Fig.2. It can be seen that at low deformation temperature, the microstructure is typically fibrous structure (Fig.2(a)). Dynamic recovery can hardly happen under this condition. With deformation temperature increasing, the number of dislocations decreases and subgrains formed by dynamic recovery become more and more obvious (Fig.2(b)). In Fig.2(c) it can be seen that a moving grain boundary toward the joint of other two grain boundaries to form grains with 120? angles, which shows that dynamic recrystallization has occurred. When deformed at 510 ℃, the alloy recrystallized obviously (Fig.2(d)).
Fig.1 Typical stress—strain curves for 2197 Al-Li alloy at different strain rates: (a)
=0.001 s-1; (b)
=0.01 s-1; (c)
=0.1 s-1; (d)
=1 s-1; (e)
=10 s-1
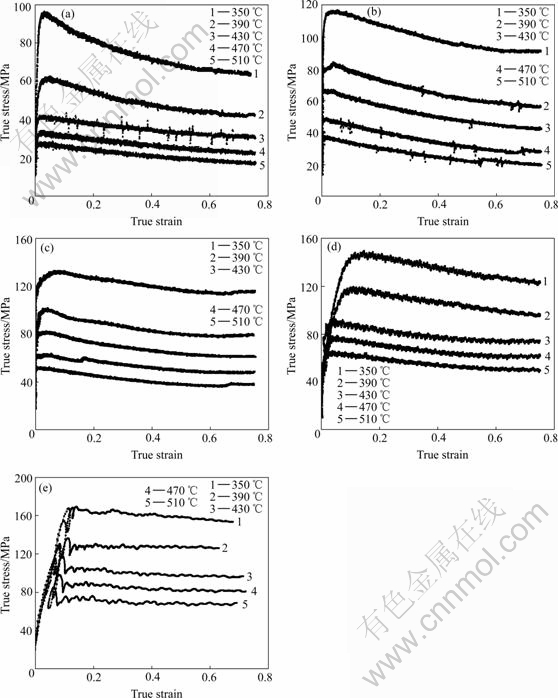
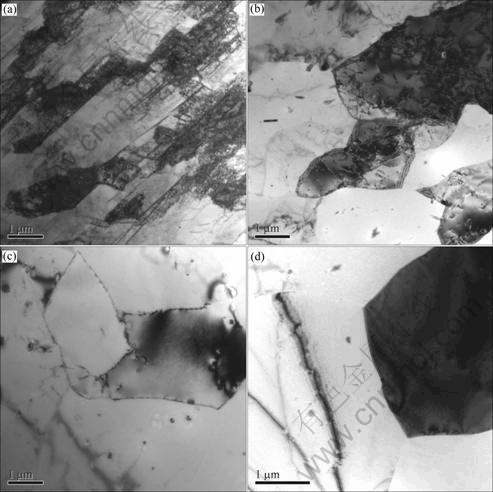
Fig.2 TEM micrographs of 2197 Al-Li alloy under different deformation temperatures and strain rates: (a) 350 ℃, 0.1 s-1; (b) 430 ℃, 0.1 s-1; (c) 470 ℃, 0.1 s-1; (d) 510 ℃, 0.1 s-1
3.3 Flow stress equation
The high temperature deformation process was controlled by thermal activation. The relationship between the maximum stress, strain rate and temperature can be described by the Arrhenius equation[9-11]:
(1)
where A, α, n are constants independent on temperature; α is stress level parameter; R is gas constant; n is stress exponent; T is thermodynamic temperature; σ means peak stress or steady state flow stress.
Eqn.(1) is appropriate for all stress levels. For low stress level and high stress level, Eqn.(1) can be written as
(2)
(3)
where α=β/n1. Moreover, the relationship between true stress and true strain can be expressed by Z parameter:
(4)
From Eqn.(4), one can obtain[12-13]
(5)
According to the definition of hyperbolic sine function sinh(ασ)=(eασ-e-ασ)/2,
(6)
Combining Eqn.(5) with Eqn.(6), the flow stress can be expressed by a function including Zener-Hollomon parameter:
(7)
Changing Eqns.(2) and (3) into logarithmic form, the following equations can be obtained:
(8)
(9)
The relationships between strain rate and flow stress of 2197 alloy are shown in Fig.3. According to Eqns.(8) and (9), it can be found that n1 and β can be determined by averaging slopes of five lines in Fig.3(a)(
—ln σ curves) and Fig.3(b) (
—σ curves) respectively, then n1=10.975 3, β=0.136 9, so α=β/n1=0.012 6 MPa-1.
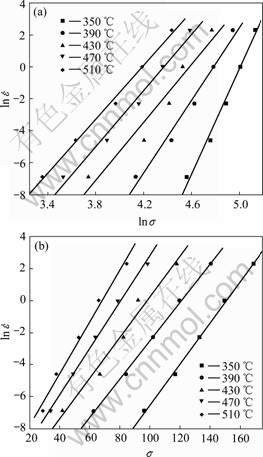
Fig.3 Relationships between flow stress and strain rate: (a)
—ln σ; (b)
—σ
When the temperature is kept constant, Eqn.(1) can be expressed as follows:
(10)
Fig.4 illustrates the relationship between
and
which shows that
is linear with
Therefore the relationship between the stress and strain rate of 2197 Al-Li alloy fits hyperbolic sine relation.
When the strain rate is constant, Eqn.(4) can be changed into
(11)
where B and C are constants. Fig.5 shows that Eqn.(11) can express the relationship of flow stress and deformation temperature correctly because
is also linear with 1/T.
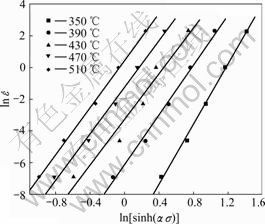
Fig.4 Relationships between true strain and flow stress
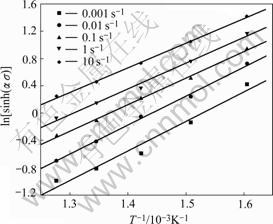
Fig.5 Relationships between flow stress and temperature
Through partial derivative transformation of Eqn.(1), Q can be expressed as
(12)
According to Eqn.(12), Fig.4 and Fig.5, the activation energy Q can be obtained to be 260.6 kJ/mol. Through logarithmic transformation, Eqn.(4) can be changed into the form as
(13)
Substituting the related data into Eqn.(13), the ln Z—
curve is plotted as shown in Fig.6. By linear regression analysis, the stress exponent and material constant can be deduced as follows: n=7.78, A=6.11×1017 s-1.
By substituting all the parameters in Eqn.(1) with experimental and calculated data, the following stress—strain equation of 2197 Al-Li alloy is obtained:
(14)
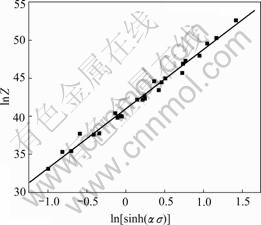
Fig.6 Relationship between flow stress and Zener-Hollomon parameter
The peak flow stress can be expressed by Z parameter:
(15)
where 
4 Conclusions
1) In the strain rate range from 0.001 to 10 s-1 and the temperature range from 350 to 510 ℃, the flow stress of 2197 Al-Li alloy decreases with the increase of deformation temperature and increases with the increase of strain rate.
2) The flow stress of 2197 Al-Li alloy during hot deformation can be expressed by a Zener-Hollomon parameter in the hyperbolic-sine function. The calculated constants are: Q=260.6 kJ/mol, α=0.012 6 MPa-1, n=7.78, A=6.11×1017 s-1. The relationship among flow stress, strain rate and temperature of 2197 alloy during plastic deformation can be expressed as

References
[1] STARKE E A Jr, SANDER T H Jr, PALMER I G. New approaches to alloy development in the Al-Li system [J]. JOM, 1981, 33(8): 24-33.
[2] WILLIAMS J C, STARKE E A Jr. Progress in structural materials for aerospace systems [J]. Acta Materialia, 2003, 51: 5775-5799.
[3] BALMUTH E S, CHELLMAN D J. Alloy design for overcoming the limitations of Al-Li alloy plate [C]// Proceedings of the 4th International Conference on Aluminum Alloys. USA: The Georgia Institute of Technology, School of Mater Sci and Eng, 1994: 282-289.
[4] HUANG Lan-ping, ZHENG Zi-qiao, HUANG Yong-ping. Microstructure and properties of 2197 Al-Li alloy [J]. The Chinese Journal of Nonferrous Metals, 2004, 14(12): 2066-2072. (in Chinese)
[5] CAVALIERE P. Hot and warm forming of 2618 aluminium alloy [J]. J Light Met, 2002, 4(2): 247-252.
[6] HAN Dong-feng, ZHENG Zi-qiao, JIANG Na, LI Jin-feng. Flow stress of high strength weldable 2195 aluminum-lithium alloy during hot compression deformation [J]. The Chinese Journal of Nonferrous Metals, 2004, 14(12): 2090-2095. (in Chinese)
[7] KAIBYSHEV R, MUSIN F, AVTOKRATOVA E, MOTOHASHI Y. Deformation behavior of modified 5083 aluminum alloy [J]. Materials Science and Engineering A, 2005, 392: 373-379.
[8] ZHANG Hui, LI Luo-xing, YUAN Deng, PENG Da-shu. Hot deformation behavior of the new Al-Mg-Si-Cu aluminum alloy during compression at elevated temperatures [J]. Materials Characterization, 2007, 58(2): 168-173.
[9] SHEPPARD T, JACKSON A. Constitutive equations for use in prediction of flow stress during extrusion of aluminum alloys [J]. Mater Sci Technol, 1997, 13: 203-206.
[10] MCQUEEN H J, RYAN N D. Constitutive analysis in hot working [J]. Materials Science and Engineering A, 2002, 322(1/2): 43-63.
[11] SHEN Jian , LI De-feng. The flow stress of an Al-Li alloy during plastic deformation at elevated temperatures [J]. Rare Metal Materials and Engineering, 1997, 26(5): 26-29. (in Chinese)
[12] LIN Qi-quan, ZHANG Hui, PENG Da-shu, et al. Flow stress behavior of 5182 aluminum alloy under hot compression deformation [J]. Natural Science Journal of Xiangtan University, 2002, 23(3): 84-88. (in Chinese)
[13] SHEN Jian. Behavior of flow stress of 2091 Al-Li alloy during hot compression [J]. Chinese Journal of Rare Metals, 1998, 22(1): 47-50. (in Chinese)
Foundation item: Project(MKPT-2004-19ZD) supported by the National Defense Science, Technology and Industry Committee of China
Corresponding author: WEI Xiu-yu; Tel: +86-731-8830270; E-mail: s-maloy@mail.csu.edu.cn, weixiuyu79@126.com
(Edited by PENG Chao-qun)