DOI:10.19476/j.ysxb.1004.0609.2019.01.20
二氧化硫还原分解铁酸锌及锌浸渣工艺
郑宇,邓志敢,樊刚,魏昶,樊光,李兴彬,李存兄,李旻廷
(昆明理工大学 冶金与能源工程学院,昆明 650093)
摘 要:锌冶炼浸出渣中锌主要以铁酸锌的形式存在,针对锌浸渣中铁酸锌难于分解的问题,以铁酸锌作为研究对象,研究二氧化硫作用下铁酸锌中锌的溶出和Fe(Ⅲ)的还原行为。考察初始硫酸浓度、液固比、二氧化硫通入量、反应时间、反应温度对二氧化硫还原分解铁酸锌行为的影响。结果表明:最佳反应条件如下,初始硫酸浓度120 g/L、液固比11:1、二氧化硫通入量0.41×10-2 mol/g、反应时间120 min、反应温度105 ℃。在最佳反应条件下,对锌浸渣开展还原浸出实验,锌的浸出率能达到99%以上,Fe(Ⅲ)的还原率能达到98%。通过ICP-MS和XRD分析表明,锌浸渣中的铁酸锌完全分解,还原浸出渣的主要成分为锌和铅,分别以ZnS和PbSO4的形式存在。
关键词:铁酸锌;锌浸渣;二氧化硫;浸出
文章编号:1004-0609(2019)-01-0170-09 中图分类号:TF813 文献标志码:A
金属锌应用广泛,消费量大[1-2]。目前,锌生产的主流方法是“焙烧-浸出-电积”(RLE)工艺,全世界约85%的锌经RLE工艺产出[3]。
在RLE工艺的焙烧过程中,硫化锌精矿中含有的杂质铁在高温氧化条件下不可避免地与主金属锌生成铁酸锌(ZnFe2O4)[4-5],铁酸锌属于尖晶石型锌铁氧体,其晶格是一种复杂的面心立方结构,立方体的各个角及每个面的中心均为氧原子,铁原子与锌原子处于氧原子的间隙中,这种晶格结构具有相当大的稳定性,因此若只采用酸浸处理难以溶出[6-7]。
从锌浸渣中回收锌的主要工艺有烟化法、还原焙烧法、电热法、热酸浸出法等[8-9]。常规火法工艺处理锌浸渣对高沸点金属回收率低,产生的烟气和窑渣对环境污染严重,而热酸浸出法则存在有价金属铜、铟回收流程长、回收率低,锌、铟分离困难等问题[10]。近年来,针对难溶铁酸盐的分解问题,国内外学者进行了一定的研究[11-14],张燕娟等[15]利用机械活化的方法对铁酸盐的分解进行了研究,机械活化虽然强化了铁酸盐的浸出效果,但反应时间长、酸耗量较大[16]。
ELGERSMA等[17]研究表明,铁酸锌的溶解经过以下3个步骤:1) 水分子在铁酸锌固体表面羟基化形成配合物分子;2) 配合物分子在铁酸锌固体表面发生解离与扩散;3) 反应产物解离。在这3个步骤中,Fe(Ⅲ)由铁酸锌固体颗粒表面到溶液主体之间的传递过程是整个溶解过程的限制性环节。当溶液中含有大量Fe(Ⅲ)离子时,传递过程较慢;当溶液中含有大量Fe(Ⅱ)离子时,传递过程较快。
二氧化硫是RLE工艺焙烧过程中的副产物,其水合产物为亚硫酸,在酸性溶液中亚硫酸的还原性强于其氧化性[18],采用二氧化硫还原法处理铁酸锌在实现铁酸锌高效分解的同时能完成Fe(Ⅲ)向Fe(Ⅱ)转化。锌浸渣中铁酸锌的大量存在是造成总锌浸出率低的主要原因,还原分解铁酸锌,并使浸出液中的铁以Fe(Ⅱ)的形态存在,不仅能够提高总锌的回收率,而且能为后续锌、铟与铁的分离创造有利条件。
1 二氧化硫还原分解铁酸锌的热力学分析
利用SO2表现出来的还原性和ZnFe2O4中三价铁所表现出来的氧化性,设计的反应具有较高的热力学反应趋势。在SO2还原分解ZnFe2O4过程中,发生的主要反应为
ZnFe2O4+2H2SO4+SO2=ZnSO4+2FeSO4+2H2O (1)
在373.15K时,根据热力学数据[19],计算得到反应(1)的
为-42 kJ/mol,反应具有较大的热力学推动力,因此,利用SO2在高温条件下还原分解ZnFe2O4的工艺是可行的。
SO2还原分解ZnFe2O4涉及氧化还原,物种的氧化性强弱与反应体系pH存在密切关系[20]。就水溶液中发生的化学反应而言,绘制φ-pH图可以直观了解不同氧化还原电势和pH值条件下反应体系内各种形态化合物或离子的相互平衡情况,SO2在硫酸溶液中还原分解ZnFe2O4是气-液-固三相反应,因此,可以采用SO2-ZnFe2O4-H2O系的φ-pH优势区图对反应(1)进行描述和讨论。不同温度下SO2-ZnFe2O4-H2O系的φ-pH优势区图如图1所示。由图1可知,ZnFe2O4在酸性条件下的分解机制有两种。在非还原条件下,ZnFe2O4第一步反应分解成Fe2O3和Zn2+,第二步反应Fe2O3分解成Fe3+;在还原条件下,ZnFe2O4反应分解成Fe2O3和Zn2+后,Fe2O3被还原成Fe2+。当控制氧化还原电位在(B)区域内,ZnFe2O4中锌以Zn2+形态进入溶液,而铁以Fe2O3形态保留在渣中。当控制氧化还原电位在(D)、(E)、(F)区域内,ZnFe2O4中锌和铁分别以Zn2+和Fe2+的形态进入溶液。
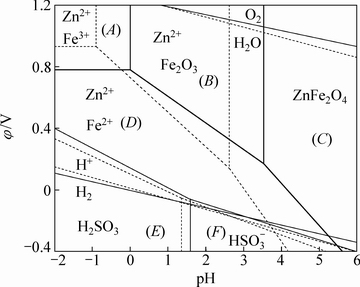
图1 SO2-ZnFe2O4-H2O系的φ-pH优势区图(25 ℃,实线;100 ℃,虚线)
Fig. 1 φ-pH predominance diagram of SO2-ZnFe2O4-H2O system (25 ℃, solid line; 100 ℃, dash line)
2 实验
2.1 实验原料铁酸锌的制备
鉴于锌浸出渣成分复杂,本文采用合成的铁酸锌进行实验,以减少干扰因素,有利于对铁酸锌发生的主要化学反应进行研究分析。以分析纯级ZnO和Fe2O3作为原料,在合成铁酸锌的过程中,主要发生的化学反应为
ZnO+Fe2O3=ZnFe2O4 (2)
具体的合成步骤如下:1) 将酸性氧化物Fe2O3和两性氧化物ZnO[21-22]按摩尔比1:1在酒精溶液中混合均匀,制成直径为0.3 cm左右的球形颗粒。2) 球形颗粒充分干燥后,在900 ℃条件下煅烧10 h,随炉冷却。3) 将冷却的球形颗粒充分破碎,在酒精溶液中再次混合均匀,制成直径为0.3 cm左右的球形颗粒。4) 球形颗粒充分干燥后,在1100 ℃条件下进行二次焙烧,时间为5 h,随炉冷却。5) 再次将合成的铁酸锌充分磨细,并在1:1(体积比)的盐酸溶液中浸泡除杂、水洗、干燥,得到ZnFe2O4固体。
合成铁酸锌粒径分布如图2所示。由图2可知,其粒径主要分布在85~100 μm范围内。分别选取85~90、90~95、95~100 μm这3个粒级的物料化验其成分,其主要化学成分如表1所示。不同粒级合成物料的锌、铁含量,与铁酸锌中锌、铁含量的理论值27.09%、46.33%误差都在0.5%以内,纯度较高,符合实验要求。
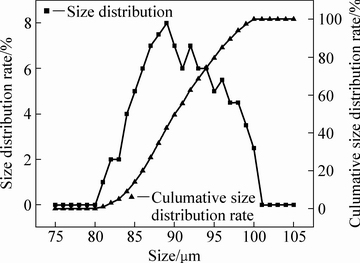
图2 铁酸锌粒径分布图
Fig. 2 Particle size distribution of zinc ferrite
表1 不同粒级铁酸锌样品的主要化学成分
Table 1 Typical chemical composition of each size fraction from zinc ferrite
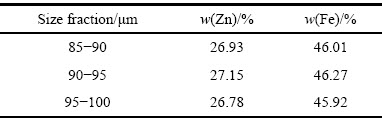
借助XRD和SEM对合成的铁酸锌进行晶相组成和微观形貌分析。铁酸锌的XRD谱如图3所示,铁酸锌的特征衍射峰尖锐,晶型良好;将检测到的XRD波形与标准卡片对比,探测到的主要物相为铁酸锌。合成铁酸锌的SEM检测分析结果如图4所示,组成铁酸锌的微粒尺寸保持在0.4~0.6 μm,呈不规则多边形状,表面光滑、团聚紧密。
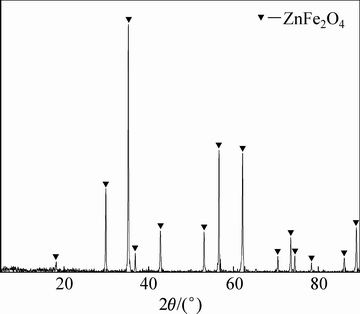
图3 合成铁酸锌的XRD谱
Fig. 3 XRD pattern of synthetic zinc ferrite
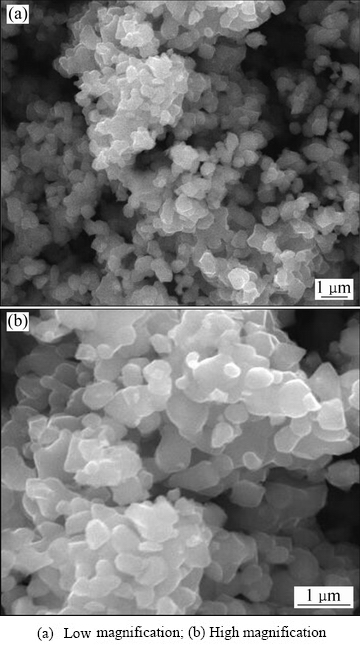
图4 合成铁酸锌的SEM像
Fig. 4 SEM images of synthetic zinc ferrite
2.2 实验设备与方法
用JE6001型电子天平(梅特勒-托利多仪器上海有限公司)称取一定量粒级在85~100 μm的铁酸锌,加入GSH-CS型磁力驱动高压釜(威海化工机械有限公司)内,然后加入一定量预定浓度的硫酸溶液,调成矿浆,加盖釜盖;安装好热电偶和测速器,用来测定高压釜内温度和搅拌转速,采用FDK型高压釜控制器(威海化工机械有限公司)调节实验所需温度和搅拌转速;当高压釜内温度达到实验所需温度时,将钢瓶装纯度为99.99%的二氧化硫气体(昆明梅塞尔气体产品有限公司)经减压器(上海减压器有限公司)进入缓冲瓶,然后通过LZB-2型玻璃转子流量计(淮安森菱仪表有限公司)控制流量,向高压釜内通入预定量的二氧化硫气体,反应开始。
从反应开始直至达到实验预设的时间后,停止加热,打开循环冷却水阀门,待温度降至室温,排出残留的气体,压力降到0后开启高压釜。通过2XZ-2型旋片式真空泵(浙江台州求精真空泵有限公司)将高压釜内的矿浆全部抽取出来,并进行固液分离。用量筒(上海垒固仪器有限公司)量好浸出液体积,并且用PHSJ-4F型实验室pH计(上海仪电科学仪器股份有限公司)测定溶液的pH值,然后将所得的浸出液密封保存,并送分析。将浸出渣置于DZF-6090型真空干燥箱(上海一恒科学仪器有限公司)中,在75 ℃下恒温12 h烘干,称量记录、分析。
2.3 分析检测与计算
采用重铬酸钾滴定法检测浸出液中Fe(Ⅱ)和Fe(Ⅲ)的浓度,采用EDTA滴定法检测浸出渣中锌、铁的含量;采用钨丝灯扫描电镜(SEM)对铁酸锌及其浸出渣进行宏观、微观形貌分析;浸出率和还原率分别采用式(3)和(4)进行计算。
锌的溶出率计算公式为
η={1-[c2m2/(c1m1)]}×100% (3)
铁的还原率计算公式为
γ=[F2V2/(c1m1)]×100% (4)
式中:η为溶出率,%;γ为还原率,%;c1为反应原料中锌的含量,%;m1为反应原料的质量,g;c2为渣中锌的含量,%;m2为渣的质量,g;F2为反应终点液体中Fe(Ⅱ)的含量,g/ml;V2为反应终点液体体积,mL。
3 结果与讨论
3.1 液固比对铁酸锌还原分解的影响
当体系温度为105 ℃、初始硫酸浓度为120 g/L、铁酸锌加入量为100 g,固定搅拌转速为500 r/min的情况下通入二氧化硫0.41 mol,反应4 h,不同液固比对铁酸锌还原分解率的影响如图5所示。由图5可知,随着液固比的增大,锌的溶出率和Fe(Ⅲ)的还原率显著提高。这是由于在初始硫酸浓度一定的情况下,当液固比较低时,虽然初始硫酸浓度相同,但是总的硫酸量较少,不利于锌、铁的浸出。随着液固比的增大,硫酸的量也相应增多,ZnFe2O4与H2SO4的混合液黏度也相应减小,改善了扩散条件,固液接触效率增大,使反应率提高。
当液固比为11:1时,铁酸锌的还原浸出率能达到95%。在液固比大于11:1的情况下,锌的溶出率和Fe(Ⅲ)的还原率几乎一致。这是由于当液固比大于11:1时,随着反应的进行,浸出液黏度没有明显增大,依然保持着较好的扩散条件,锌的溶出和Fe(Ⅲ)的还原呈现出一致性的趋势。在实际生产中,在液固比增大、处理相同物料的情况下,将使溶液处理量和残余终酸量增大,使生产成本提高,综合考虑取液固比为11:1更加符合生产要求。
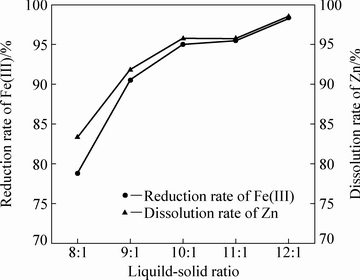
图5 液固比对铁酸锌还原分解的影响
Fig. 5 Effect of liquid-solid ratio on reductive decomposition of zinc ferrite
3.2 初始硫酸浓度对铁酸锌还原分解的影响
当体系温度为105 ℃、液固比为10:1、铁酸锌加入量为100 g、固定搅拌转速为500 r/min的情况下通入二氧化硫0.41 mol,反应4 h,不同初始硫酸浓度对铁酸锌还原分解率的影响如图6所示。由图6可知,随着初始硫酸浓度的增大,铁酸锌中锌的溶出率和Fe(Ⅲ)的还原率在整体上呈上升的趋势。当初始硫酸浓度低于110 g/L时,锌、铁的浸出率随着初始硫酸浓度的增加没有明显变化;但当初始硫酸浓度从110 g/L升高到120 g/L,锌、铁的浸出率急剧增高,这是由于随着初始硫酸浓度的增加,单位体积内硫酸的量增加,反应体系内的H+浓度保持在一个较高水平,使H+与ZnFe2O4的碰撞机会增加,促进反应(1)向右进行;当初始硫酸浓度达到120 g/L后,再继续增加初始硫酸浓度锌、铁的浸出率几乎不再增加。

图6 初始硫酸浓度对铁酸锌还原分解的影响
Fig. 6 Effect of initial acid concentration on reductive decomposition of zinc ferrite
3.3 二氧化硫通入量对铁酸锌还原分解的影响
当体系温度为105 ℃、初始硫酸浓度为120 g/L、液固比为10:1、铁酸锌加入量为100 g、固定搅拌转速为500 r/min、反应4 h条件下,不同二氧化硫通入量对铁酸锌还原分解率的影响如图7所示。
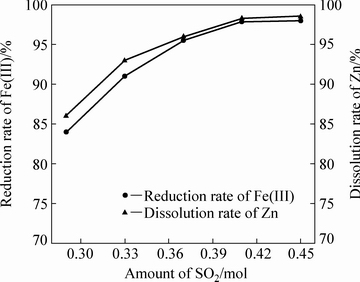
图7 二氧化硫通入量对铁酸锌还原分解的影响
Fig. 7 Effect of amount of SO2 on reductive decomposition of zinc ferrite
由图7可知,二氧化硫通入量对锌、铁的浸出率有较大的影响,二氧化硫通入量越大,化学反应的推动力越大,锌的溶出率和Fe(Ⅲ)的还原率也较高,当二氧化硫通入量为0.41 mol时,锌的溶出率和Fe(Ⅲ)的还原率能达到最大值。这是因为按照亨利定律,在反应温度恒定时,二氧化硫溶解量正比于气相分压,在一定的高压釜容积内,通入的气体量越大,高压釜内分压越大,二氧化硫溶解度越大。在反应温度为105 ℃的情况下,SO2在水中的溶解度能达到3.7 g/L,SO2溶解生成的H2SO3能使铁酸锌充分反应。但随着二氧化硫通入量继续增大,溶液中溶解的二氧化硫趋于饱和,因此,继续增加二氧化硫通入量对反应进行程度的促进作用较小,只需要将二氧化硫通入量保持在0.41 mol,就可以使反应进行程度保持在一个较高水平。
3.4 反应时间对铁酸锌还原分解的影响
当体系温度为105 ℃、初始硫酸浓度为120 g/L、液固比为10:1、铁酸锌加入量为100 g,固定搅拌转速为500 r/min,通入二氧化硫0.41 mol,不同反应时间对铁酸锌还原分解率的影响如图8所示。由图8可知,当反应时间为60 min时,铁酸锌中锌的溶出率和Fe(Ⅲ)的还原率分别为87%和79%,延长反应时间至120 min时,锌的溶出率和Fe(Ⅲ)的还原率都能达到95%左右,再继续延长反应时间,锌的溶出率和Fe(Ⅲ)的还原率增幅都明显减小,这是因为随着反应时间继续向后推进,溶液中H2SO4不断消耗,H+浓度降低,整个体系中固体反应物ZnFe2O4的量也不断减小,因此反应进行的推动力很小。
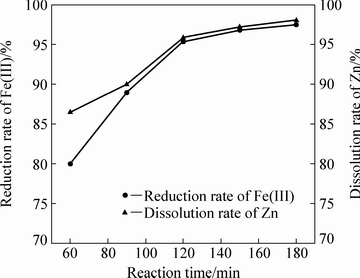
图8 反应时间对铁酸锌还原分解的影响
Fig. 8 Effect of reaction time on reductive decomposition of zinc ferrite
3.5 反应温度对铁酸锌还原分解的影响
当体系硫酸浓度为120 g/L、液固比为10:1、铁酸锌加入量为100 g,固定搅拌转速为500 r/min,通入二氧化硫0.41 mol,反应4 h,不同反应温度对铁酸锌还原分解率的影响如图9所示。
由图9可知,反应温度对于二氧化硫还原分解铁酸锌有较大的影响。随着反应温度从85 ℃升高到105 ℃,铁酸锌中锌的溶出率和Fe(Ⅲ)的还原率分别从88.74%和85.53%升高到95%左右。反应体系温度升高,分子热运动更加剧烈,反应体系内活性分子的比例增大,单位时间内参加反应的分子数量增多;阳启华等[20]研究表明,当压力一定时,二氧化硫溶解度随温度的升高,出现了下降趋势,所以温度升高到115 ℃,反应的浸出率增幅减缓。

图9 反应温度对铁酸锌还原分解的影响
Fig. 9 Effect of reaction temperature on reductive decomposition of zinc ferrite
3.6 二氧化硫还原浸出锌浸渣
通过以上5组试验,结果表明合成的高纯度铁酸锌在二氧化硫作用下被较大程度的还原分解。为了进一步探究二氧化硫对锌浸渣的作用效果,选取云南某锌冶炼厂的锌浸渣进一步开展了实验研究。
采用ICP-MS对该锌浸渣进行定性分析,化学成分结果如表2所示,主要金属元素为铁和锌。X射线衍射物相分析(XRD)结果如图10(a)所示,由XRD分析可知,该锌浸渣中晶相主要为铁酸锌、硅酸锌、硫化锌以及硫酸高铅,其中铁酸锌的衍射特征峰最为明显。
表2 锌浸渣化学组成
Table 2 Chemical composition of zinc leaching residue (mass fraction, %)
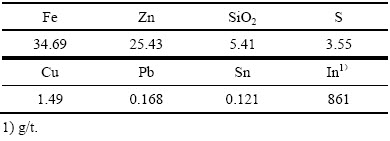
对该锌浸渣进行SEM-EDS分析,结果如图10(b)和图11所示。由图可知,组成这些矿物的颗粒比较单一,表明粗糙致密,呈多边形状。对该锌浸渣的多个颗粒进行元素定性分析,所选的3个颗粒中锌、铁、氧元素都出现了高强度的特征衍射峰,某些颗粒还出现了硅、铅、硫等元素的特征衍射峰。
固定搅拌转速500 r/min,温度105 ℃,初始硫酸浓度120 g/L,液固比11:1,反应时间120 min,取100 g粒径分布在85~100 μm的锌浸渣,在不通入二氧化硫和通入二氧化硫0.41 mol的条件下分别进行实验。
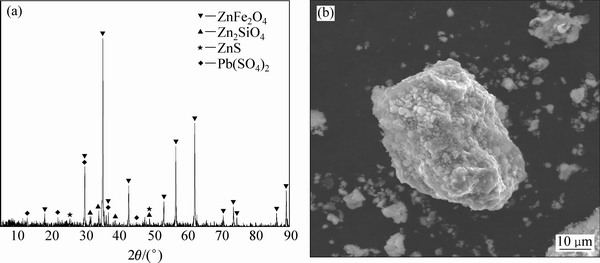
图10 锌浸渣的XRD谱及SEM像
Fig. 10 XRD pattern (a) and SEM image (b) of zinc leaching residue

图11 锌浸渣的SEM像及EDS谱
Fig. 11 SEM image (a) of zinc leaching residue and EDS spectrum in areas of positions 1 (b), 2 (c), 3 (d)
在不通入SO2的浸出试验中,锌的浸出率为63%,浸出液中Fe(Ⅲ)的含量占溶液中总铁含量的95%以上,浸出液固液分离困难;二氧化硫还原浸出试验结果表明,锌的浸出率能达到99%以上,Fe(Ⅲ)的还原率能达到98%,溶液中铁主要以Fe(Ⅱ)的形式存在,反应产物过滤性能良好。对两个反应的浸出渣采用ICP-MS进行定性分析,其主要化学成分如表3所示。
在不通入SO2的浸出试验中,浸出渣锌、铁含量较高;二氧化硫还原浸出渣中锌含量为9.55%,Pb含量为7.37%。浸出渣的XRD分析结果如图12所示,由热酸浸出渣XRD谱(无SO2)可知:在不通入二氧化硫的条件下浸出渣中硅酸锌等易溶矿物已经完全溶解,热酸浸出渣中含有较高的铁酸锌,以及部分硫酸铅。由还原浸出渣XRD谱(添加SO2)可知:还原浸出渣中的晶相主要是硫酸铅,以及少量的硫化锌,未见有铁酸锌物相的存在,表明铁酸锌已经完全溶解,还原浸出渣中的铅和锌是以难溶的硫酸铅和硫化锌形式存在。
表3 浸出渣的化学组成
Table 3 Chemical composition of leaching residue
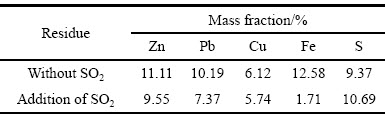
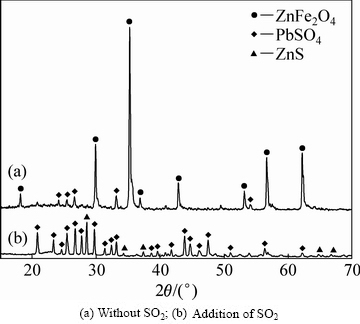
图12 浸出渣的XRD谱
Fig. 12 XRD pattern of leaching residue
4 结论
1) 二氧化硫还原浸出锌浸渣,在反应温度为105 ℃,初始硫酸浓度为120 g/L,液固比为11:1,反应时间为120 min,搅拌转速为500 r/min,二氧化硫通入量为0.41×10-2 mol/g的条件下锌的浸出率能达到99%以上,有价金属锌得到了较高程度的富集。
2) 二氧化硫还原浸出锌浸渣的过程中,有效实现了溶液中Fe(Ⅲ)向Fe(Ⅱ)的转变,Fe(Ⅲ)的还原率达 到98%。由于大量的Fe(Ⅲ)都还原为Fe(Ⅱ),能够有效缓解溶液中高浓度三价铁离子对铁酸锌溶解的抑制作用,不会由于Fe(Ⅲ)的浓度过高而降低H+活度,更有利于铁酸锌的还原分解。
3) 二氧化硫还原分解锌浸渣的浸出液中Fe(Ⅲ)含量低,为后续工段中铜、铟等有价金属的分离回收提供了有利条件。
REFERENCES
[1] 魏 昶, 李存兄. 锌提取冶金学[M]. 北京: 冶金工业出版社, 2013: 15.
WEI Chang. LI Cun-xiong. Zinc extraction metallurgy[M]. Beijing: Metallurgical Industry Press, 2013: 15.
[2] 王成彦, 陈永强. 中国铅锌冶金技术状况及发展趋势: 锌冶金[J]. 有色金属科学与工程, 2017, 8(1): 1-7.
WANG Cheng-yan, CHEN Yong-qiang. Lead and zinc metallurgy technology situation and development treads of China: zinc metallurgy[J]. Nonferrous Metals Science and Engineering. 2017, 8(1): 1-7.
[3] SOUZA A D, PIN P S, LEAO V A. Bioleaching and chemical leaching as an integrated process in the zinc industry[J]. Minerals Engineering, 2007, 20(6): 591-599.
[4] 彭海良. 常规湿法炼锌中铁酸锌的行为研究[J]. 湖南有色金属, 2004, 20(5): 20-22.
PENG Hai-liang. Study on the behavior of zinc ferrite in conventional hydrometallurgical zinc production process[J]. Hunan Nonferrous Metals, 2004, 20(5): 20-22.
[5] GRAYDON J W, KIRK D W. The mechanism of ferrite formation from iron sulfides during zinc roasting[J]. Metallurgical Transactions B, 1988, 19(5): 777-785.
[6] 窦明民. 锌冶金中铁酸锌生成及离解机理研究[J]. 云南冶金, 2003, 32(10): 63-65.
DOU Ming-min. Study on the formation and mechanism of zinc ferrite in zinc metallurgy[J]. Yunnan Metallurgy, 2003, 32(10): 63-65.
[7] 陈婷立. 纳米铁酸锌的制备及其性能的研究[D]. 苏州: 苏州大学, 2012: 1-2.
CHEN Ting-li. Study on synthesizing and characterizing of zinc ferrite nanoparticles[D]. Suzhou: Soochow University, 2012: 1-2.
[8] 许 冬, 阮胜寿, 贾 荣. 锌冶炼废渣中铟回收技术综述[J]. 材料研究与应用, 2009, 3(4): 231-233.
XU Dong, RUAN Sheng-shou, JIA Rong. Review on technology of recovery of indium from zinc smelting slags[J]. Materials Research and Application. 2009, 3(4): 231-233.
[9] 陈永海. 低品位氧化锌矿直接提锌工艺研究[D]. 长沙: 中南大学, 2005: 2-10.
CHEN Yong-hai. Direct extraction of zinc from low-grade zinc oxide ores[D]. Changsha: Central South University, 2005: 2-10.
[10] 张 帆. 湿法炼锌浸出渣与高铁锌精矿协同浸出机理与工艺研究[D]. 昆明: 昆明理工大学, 2017: 1-2.
ZHANG Fan. Study on mechanism and process of synergistic leaching of leaching residue from zinc hydrometallurgy with high iron and zinc concentrates[D]. Kunming: Kunming University of Science and Technology, 2017: 1-2.
[11] 韩俊伟, 刘 维, 覃文庆, 蔡 鑫, 罗虹霖, 王大伟. CO还原焙烧铁酸锌的选择性分解行为[J]. 中国有色金属学报, 2016, 26(6): 1324-1331.
HAN Jun-wei, LIU Wei, QIN Wen-qing, CAI Xin, LUO Hong-lin, WANG Da-wei. Selective decomposition behavior of zinc ferrite by reduction roasting with CO[J]. The Chinese Journal of Nonferrous Metals, 2016, 26(6): 1324-1331.
[12] POLSILAPA S, INTAKUEAN P, PROMBOOBPA A, The decomposition of zinc ferrite in electric arc furnace dust by carbon[J]. Key Engineering Materials, 2015, 4087(658): 156-160.
[13] 刘 洋, 谭 军, 尹周澜, 刘常青, 陈启元, 张平民, 廖 舟, 王心皞. 湿法炼锌沉铁渣和浸锌渣的焙烧预处理[J]. 中国有色金属学报, 2016, 26(1): 212-222.
LIU Yang, TAN Jun, YIN Zhou-lan, LIU Chang-qing, CHEN Qi-yuan, ZHANG Ping-min, LIAO Zhou, WANG Xin-hao. Roasting pretreatment of iron-sinking slag and zinc leaching residue in zinc hydrometallurgy[J]. The Chinese Journal of Nonferrous Metals, 2016, 26(1): 212-222.
[14] SENANAYAKE G, CHILDS J, AKERSTROM B D, PUGAEV D. Reductive acid leaching of laterite and metal oxides—A review with new data for Fe(Ni, Co)OOH and a limonitic ore[J]. Hydrometallurgy, 2011, 110(1/4): 13-32.
[15] 张燕娟, 黎铉海, 潘柳萍, 韦岩松. 机械活化对铟铁酸锌溶解动力学及物化性质的影响[J]. 中国有色金属学报, 2012, 22(1): 315-323.
ZHANG Yan-juan, LI Xuan-hai, PAN Liu-ping, WEI Yan-song. Influence of mechanical activation on dissolution kinetics and physicochemical properties of indium-bearing zinc ferrite[J]. The Chinese Journal of Nonferrous Metals, 2012, 22(1): 315-323.
[16] 张 纯, 闵小波, 张建强, 王 密, 李辕成. 锌冶炼中浸渣锌还原浸出机制与动力学[J]. 中国有色金属学报, 2016, 26(1): 197-203.
ZHANG Chun, MIN Xiao-bo, ZHANG Jian-qiang, WANG Mi, LI Yuan-cheng. Mechanisms and kinetics on reductive leaching of zinc from neutral leaching residue[J]. The Chinese Journal of Nonferrous Metals, 2016, 26(1): 197-203.
[17] ELGERSMA F, WITKAMP G J, ROSMALEN V G M. Kinetics and mechanism of reductive dissolution of zinc ferrite in H2O and D2O[J]. Hydrometallurgy, 1993, 33(1/2): 165-176.
[18] 韩效钊, 朱艳芳, 姚卫堂, 许民才. 软锰矿吸收SO2制备硫酸锰(Ⅰ)[J]. 矿冶工程, 2003, 23(2): 53-55.
HAN Xiao-zhao, ZHU Yan-fang, YAO Wei-tang, XU Min-cai. Preparation of manganese sulfate from pyrolusite by absorpting sulfur dioxide(Ⅰ)[J]. Mining and Metallurgical Engineering, 2003, 23(2): 53-55.
[19] 杨显万. 高温水溶液热力学数据计算手册[M]. 北京: 冶金工业出版社, 1983: 224-251, 527-673.
YANG Xian-wan. Handbook of thermodynamic data in aqueous solutions at high temperature[M]. Beijing: Metallurgical Industry Press, 1983: 224-251, 527-673.
[20] 阳启华, 张 昭. SO2浸出软锰矿过程中抑制连二硫酸锰生成的研究[J]. 湿法冶金, 2012, 31(3): 144-148.
YANG Qi-hua, ZHANG Zhao. Study on restrain generation of manganese dithionate in leaching of MnO2 With SO2[J]. Hydrometallurgy of China, 2012, 31(3): 144-148.
[21] 黄希祜. 钢铁冶金原理[M]. 北京: 冶金工业出版社, 2013: 295-296.
HUANG Xi-hu. Principles of iron and steel metallurgy[M]. Beijing: Metallurgical Industry Press, 2013: 295-296.
[22] 魏 昶, 王吉坤. 湿法炼锌理论与应用[M]. 昆明: 云南科技出版社, 2003: 31-32.
WEI Chang, WANG Ji-kun. Theory and application of zinc hydrometallurgy[M]. Kunming: Yunan Science and Technology Press, 2003: 31-32.
Reductive decomposition of zinc ferrite and zinc residues by sulfur dioxide
ZHENG Yu, DENG Zhi-gan, FAN Gang, WEI Chang, FAN Guang, LI Xing-bin, LI Cun-xiong, LI Min-ting
(Faculty of Metallurgical and Energy Engineering, Kunming University of Science and Technology, Kunming 650093, China)
Abstract: The zinc in zinc residues exists mainly as zinc ferrite, in order to solve the difficulty of decompose zinc ferrite in zinc residues, by taking a zinc ferrite as the research object, the dissolution of zinc and the reduction of Fe(Ⅲ) in zinc ferrite under the action of sulfur dioxide were investigated. The effects of initial sulfuric acid concentration, liquid solid ratio, sulfur dioxide content, reaction time and reaction temperature on the reductive decomposition of zinc ferrite were studied when sulfur dioxide was used as reductant. The results show that the optimal reaction condition are as follows: sulfuric acid concentration of 120 g/L, liquid-solid ratio of 11:1, SO2 intake of 0.41×10-2 mol/g , reaction time of 120 min and reaction temperature of 105 ℃. The leaching rate of zinc is as high as 99% and the reduction rate of Fe(Ⅲ) is 98% under the optimum reaction conditions. Furthermore, the zinc ferrite is fully decomposed, and the main compositions of the residue are ZnS and PbSO4, according to the ICP-MS and XRD analysis.
Key words: zinc ferrite; zinc residues; sulfur dioxide; leaching
Foundation item: Projects(51564030, 51664030, 51664029) supported by the National Natural Science Foundation of China; Project(2014CB643404) supported by the National Basic Research Program of China; Project(2016FB097) supported by Yunnan Applied Basic Research Program, China
Received date: 2017-11-06; Accepted date: 2018-01-02
Corresponding author: DENG Zhi-gan; Tel: +86-871-65188819; E-mail: dengzhigan83@163.com
(编辑 龙怀中)
基金项目:国家自然科学基金资助项目(51564030,51664030,51664029);国家重点基础研究发展计划资助项目(2014CB643404);云南省应用基础研究计划项目(2016FB097)
收稿日期:2017-11-06;修订日期:2018-01-02
通信作者:邓志敢,讲师,博士;电话:0871-65188819;E-mail:dengzhigan83@163.com