J. Cent. South Univ. Technol. (2011) 18: 972-977
DOI: 10.1007/s11771-011-0789-0
Carbonaceous mesophase spherule/activated carbon composite as anode materials for super lithium ion capacitors
YANG Juan(杨娟), ZHOU Xiang-yang(周向阳), LI Jie(李劼), LOU Shi-ju(娄世菊)
School of Metallurgical Science and Engineering, Central South University, Changsha 410083, China
? Central South University Press and Springer-Verlag Berlin Heidelberg 2011
Abstract: A series of carbonaceous mesophase spherule/activated carbon composites were prepared as anode materials for super lithium ion capacitors using carbonaceous mesophase spherules as the core materials and pitch as the active carbon shell precursor. The structures of the composites were examined by scanning electron microscopy and X-ray diffractometry. The electrochemical performance was investigated in electric double layer capacitor and half-cell. The results show that, the composite exhibits good performance in both capacitor and battery with a high reversible capacity of 306.6 mA?h/g (0.2C) in the half-cell, along with a capacitance of 25.8 F/g in the capacitor when an optimum ratio of carbonaceous mesophase spherules to active carbon is adopted. The composite also shows a favorable rate performance and good cycle ability. A working model of this anode in super lithium ion capacitors was established.
Key words: super lithium ion capacitor; carbonaceous mesophase spherule; active carbon; compound anode
1 Introduction
Electric double layer capacitors (EDLCs) and lithium ion batteries (LIBs) are regarded as the most successful energy storage devices among those that can be found in the market. EDLCs can develop a long cycle-life, very high specific power but low energy density. In contrast, LIBs, which can deliver high energy density, suffer from their limited power output and poor cycle ability. This has led to the intense investigation of a new type of energy storage devices known as super lithium ion capacitors (SLICs) [1-3]. Both double-layer capacitance process and lithium ion intercalation- deintercalation process are involved in the electro- chemical process of SLICs. A SLIC can combine the energy storage capability of LIB and power storage behavior of EDLC and fill the gap between high-powered capacitor and high-energy battery, thus to satisfy the growing demands in many fields such as portable devices and hybrid electric vehicles.
As one of the key materials, the anode materials of SLIC should possess the characteristics of both anode of LIB and anode of EDLC. Graphitic carbons are widely used as the anode materials of LIB because of their high reversible discharge capacities and low stable discharge voltage platform [4-5]. On the other hand, activated carbons (ACs) are the only marketing anode materials of EDLCs because of their properties of stable electro- chemical performance, no contamination and long life [6-7]. A lot of work has been done concerning these two materials [8-10]. The voltage window was large and both energy density and power density were large when employing the composite of graphite and AC as the electrode materials. Yet in all these researches, the anode materials were limited to single carbonous materials of graphite or AC. Furthermore, they reported only their performance in capacitors without the performance in batteries.
When using the compounds of graphite and AC as the anode materials of SLIC, it is necessary to determine whether will the anode exhibit the characteristics of both anode of LIB and anode of EDLC. Recently, interests have been focused on a series of carbon compounds as the anode materials in our research group [11]. An anode material was prepared by ultrasonic blending, which exhibited a kind of double-characteristics. Although the capacities were not good enough (220 mA?h/g in LIB at 0.2C while 20 F/g in EDLC), the results still presented the prospect of this kind of compound materials. In this work, in-situ reaction techniques were employed to fabricate carbon composites which possess a shell-core structure using carbonaceous mesophase spherules (CMSs) as the core material and coal-tar pitch as the carbon source of AC shell. A model of the anode working mechanism was established thereafter.
2 Experimental
The shell-core structure carbon composite powders were fabricated as follows. CMS (particle size: 10 μm in diameter, tap density: 1.21 g/cm3, surface area: 1.0 m2/g) as core material and coal-tar pitch (softening point: 83 °C, volatile component content: 15%) as AC precursor were mixed in a certain ratio with ethanol solvent. The elemental powders were added into a saturated KOH solution and the solution was stirred for 30 min to ensure that the powders were mixed sufficiently. Pretreatment of the powders was then carried out in an air atmosphere by pelletizing and heating the mixture in an electric furnace. The almost dried particles were then carbonized at 800 °C in Ar for 2 h in order to wrap the CMS up with an AC coating through the in-situ reaction of pitch.
In order to investigate the component and structure, the powders prepared thereafter were thoroughly washed with hydrochloric acid and then water. The particle morphology and structure were examined by scanning electron microscopy (SEM). The phase components of the composite material were investigated by X-ray diffractometry (XRD). The tap-densities were obtained with a tap-density apparatus and the brunauer-emmett- teller (BET) surface area was measured by the analysis of N2 adsorption-desorption isotherms.
For the preparation of working electrodes, the composite powders (80%, mass fraction) were mixed with polyvinylidene fluoride (10%, mass fraction) and carbon black (10%, mass fraction) in N-methylpyrrolidone. The slurry thus obtained was coated onto aluminum (used in EDLC) and copper foil (used in half-cell) and roll-pressed in air. The electrodes were dried at 120 °C in vacuum.
As long as the electrolyte used for SLIC is still under R&D, the electrochemical performance is studied in capacitor and half-cell. Two-electrode-capacitor using 1 mol/L (C2H5)4NBF4 solution in acetonitrile (AN) as electrolyte and 2025 coin-type half-cell using 1 mol/L LiPF6 solution in a mixed solvent of ethylene carbonate (EC) and dimethyl carbonate (DMC) as electrolyte were built with the same working electrodes mentioned above in an Ar filled glove box. Galvanostatic charge and discharge tests of the composite electrodes were carried out on a 10 mA Land at 25 °C.
3 Results and discussion
3.1 Structure of carbon composites
For comparison, a sample was fabricated from pure pitch using the same method as the carbon composites; the obtained sample was designated as sample 0. Also for comparison, CMS was processed with the same heat treatment and named as T-CMS.
The SEM images of sample 0 and T-CMS are shown in Fig.1. Obviously, sample 0 shows an irregular particle shape with a median diameter of 100 μm. Many cavities (indicated by arrows in Fig.1(b)) can be seen clearly on the surface of the particles. It comes to a conclusion that the resultant of pitch undergoing such a process is AC [12].
A series of CMS/AC composites were prepared by processing the mixture of CMS and pitch in mass ratios of 1:1 (sample 1), 2:1 (sample 2), and 3:1 (sample 3). Figure 2 shows the SEM images of these composites before powdering. It can be seen that a kind of cross linked composites are obtained. From Fig.1(b) and Fig.2(b), many cavities can be found on the surface of sample 1 and sample 2 similar to the ones found in sample 0. Furthermore, from Fig.1(c) and Figs.2(a) and (c), it can be seen that T-CMS which undergoes the same heat treatment exhibits spherical shape and smooth surface while sample 1 and sample 2 exhibit cross linked structure and porous surface. As long as CMS does not react with the pitch, nor does it change at low temperature, it can be deduced that a layer of AC-shell has been in-situ produced on the CMS surface. From Fig.2(d), it can be seen that the CMS particles have spherical shape which almost maintains after treatment. However, these particles are embedded into the AC-matrix and almost covered by AC. This AC-matrix decreases as the pitch content decreases, thus forming thinner AC-shell (Fig.2(c)). The AC-shell also acts as a shell to protect the inner CMS core from the penetration of electrolyte and other big ions [13-14].
The XRD patterns of sample 0, sample 1 and sample 2 are illustrated in Fig.3. The followings can be obtained obviously from the figure: 1) For sample 1 and sample 2, there exist only the diffraction peaks at (002), (100) and (004) which stand for graphitic carbon. This means that the CMS/AC composites maintain the microstructure of graphitic carbon. 2) The almost diffused peaks are found in sample 0, which may be attributable to the completely disordered AC produced from pure pitch. 3) The (002) crystalline diffraction peak becomes broader and shorter with the increase of pitch content in precursor mixture, which means the increase of AC-shell thickness coated on the surface of CMS-core.
Table 1 lists the BET surface areas and tap-densities of the composite materials. With the decrease of pitch content in the precursor mixture, the BET surface area decreases while the tap-density increases, both of which are attributed to the diminished AC component in the composite. These two properties are important factors that affect the electrochemical properties discussed in detail later.
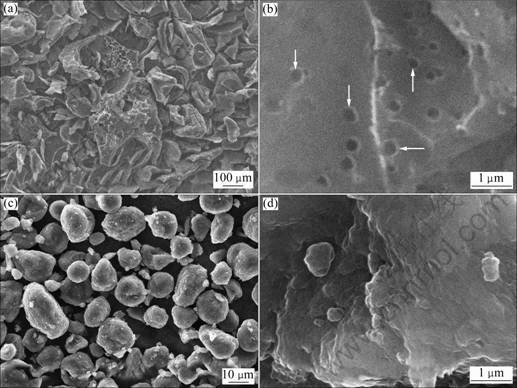
Fig.1 Different resolution SEM images of sample 0 ((a), (b)) and T-CMS ((c), (d))
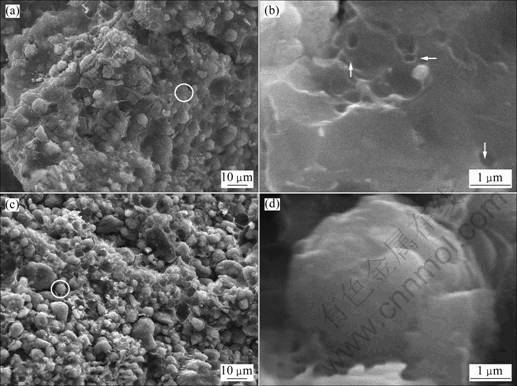
Fig.2 SEM images of composites before powdering: (a) Sample 1; (b) High resolution image of AC-matrix in sample 1; (c) Sample 2; (d) High resolution image of CMS particle covered by AC in sample 2
3.2 Electrochemical properties of carbon composites in EDLC
In order to investigate the electrochemical properties of the carbon composites thoroughly, both EDLC and half-cell are assembled with the same composite electrode. Figure 4 displays the charge- discharge curves of the composite electrodes in EDLC by constant-current mode. All the composites exhibit typical AC characteristics. Almost straight and symmetrical charge-discharge lines are obtained when constant current is applied. These curves confirm the conclusion obtained from the SEM images.
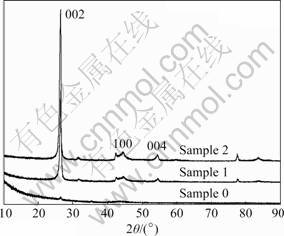
Fig.3 XRD patterns of sample 0, sample 1 and sample 2
Table 1 BET surface area and tap-density of composites
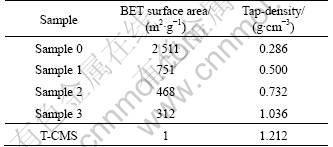
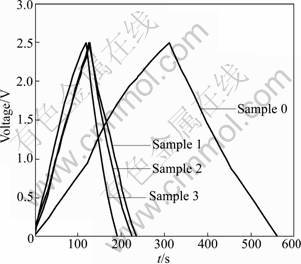
Fig.4 Charge-discharge curves of composites at current density of 0.5 A/g
Table 2 summaries the electric double layer capacitances, CEDLC, obtained from the slopes of the discharge curves at different constant currents (0.5- 10 A/g) and different terminate voltages (2.5-3.5 V). Large CEDLC of 138.3 F/g at 0.5 A/g is obtained for sample 0 with a BET surface area of 2 511 m2/g (Table 1). With the increase of CMS content, CEDLC drops to a much smaller value, which is caused by the smaller BET surface area and larger tap-density (Table 1). As summarized in Table 2, all the carbon composites exhibit very good rate capability. CEDLC at 5 A/g is almost the same as that at 0.5 A/g.
Table 2 Electric double layer capacitance, CEDLC of samples at different constant currents and different terminate voltages
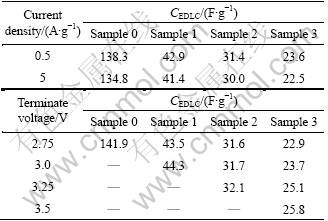
It can be speculated from Table 2 that CMS has an infection on the accessible terminate voltage of the composite due to its broad voltage window (0-4.2 V) [15]. In practice, EDLC based on AC is able to operate only up to 2.7 V [16]. With the increase of CMS content, the terminate voltage can be increased from 2.75 V (sample 0) to 3.5 V (sample 3). High terminate voltage is favorable to the increase of specific energy. This could be obtained from [17]:
(1)
where E is the specific energy, W?h/kg; C is the specific capacitance, F/g; U is the terminate voltage, V.
In Eq.(1), the specific energy is proportional to the specific capacitance, CEDLC, and proportional to the square of voltage. Therefore, although the CEDLC has little increase with the terminate voltage increasing, that is, 22.9 to 25.8 F/g for sample 3, the specific energy can be undoubtedly improved remarkably by the high terminate voltage itself.
3.3 Electrochemical properties of carbon composites in LIB
From the above results, we come to a conclusion that the composites have good electrochemical properties in EDLC. Still, as the anode material for SLIC, the composite should have good LIB characteristics. 2025 coin-type half-cells were fabricated using the same composite electrodes named sample 1, sample 2, sample 3, and a metallic lithium foil as the counter electrode. The cycling performance of the cell was evaluated in a constant-current mode at 0.2C (74.4 mA/g). The cut-off voltage was set between 0.01 and 2.0 V.
Table 3 and Fig.5 both show the charge (lithium insertion)-discharge (lithium extraction) performance of the composite materials in half-cell. Along with the increase of CMS, the discharge capacity in the first cycle increases and the coulombic efficiency increases gradually. This is because when the AC content is increased, the specific surface area becomes larger, leading to more consumption of lithium ion to form solid electrolyte interface (SEI) [18] on the electrode surface in the first cycle. This irreversible process results in larger irreversible capacity and smaller discharge capacity. T-CMS exhibits 321.2 mA?h/g with the initial coulombic efficiency of 67.2%. Clearly, the treatment with CMS declines the capacity and efficiency slightly. Sample 3 composite has a capacity as much as 306.6 mA?h/g still.
Table 3 Initial capacities and coulombic efficiencies of composites compared with T-CMS at 0.2C
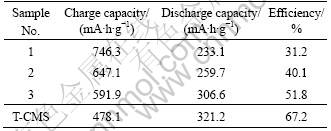
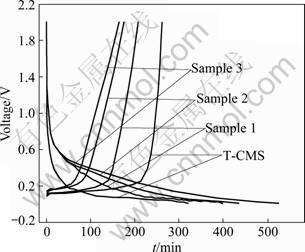
Fig.5 Galvanostatic charge-discharge curves of composites and T-CMS at 0.2C
Figure 5 shows the galvanostatic charge-discharge curves of the composites compared with T-CMS in the first cycle. Along with the increase of AC content, the time for lithium ions to insert electrode becomes longer in the initial charging process. This means that the AC-shell makes the intercalation of lithium ion more difficult. Some of the lithium ions are retained in the pores of AC making the deintercalation process slower. However, once the SEI is formed, no more lithium ions are consumed irreversibly and the efficiency comes up to more than 90% in the following cycles.
The reversible capacities, Ccell, of the composites and T-CMS, as a function of cycle number are presented in Fig.6. Among all the electrodes, sample 3 composite exhibits the highest capacity retention rate of about 94.0% after 20 cycles while T-CMS keeps about 72.0% capacity. This result indicates that the microstructure of AC-shell/CMS-core composite is very effective in buffering the damages from the electrolyte to CMS.
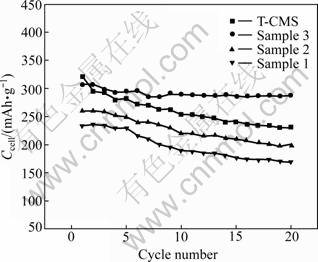
Fig.6 Discharge capacity vs cycle number plots of carbon composites compared with T-CMS
Sample 3 is found to have the best properties compared with sample 1 and sample 2, even CMS. This material exhibits large specific capacity, superior cyclability and high coulombic efficiency as LIB anode. Therefore, proper amount of AC-shell can enhance the performance of CMS in LIB while keeping good capacitance properties of AC in EDLC, which means that it is possible to combine the merits of EDLC and LIB by controlling the microcosmic structure and component of the composites.
4 Model
Through the performance investigation of the CMS/AC composite electrodes in both electrolytes, a working principle model of this anode suitable for SLIC is established. The diagram is shown in Fig.7. As the diagram shows, this model consists of three major parts: a negative electrode of CMS/AC composite; an ideal positive electrode which has the similar principle matching the negative electrode and probably comprises lithium ions, metallic oxide ions, such as
and an electrolyte, comprising lithium ions, (C2H5)4N+ and
The latter two are under R&D simultaneously in our research group [5, 19-20].
From the diagram, the charge-discharge process is displayed clearly. When small current is applied, the charge-discharge process is parallel to ordinary LIB. The AC-shell mainly acts as a protecting shell preventing solvation ions and big ions from infiltrating the CMS layer and destroying its structure. Because of the sufficient charging and discharging time, lithium ions could traverse the AC-shell and intercalate/deintercalate into/from CMS layer, which brings into full play of the capacity of CMS and obtains high energy density. On the other hand, when large current is applied, the charge- discharge process is parallel to EDLC. Positive ions (lithium ions, (C2H5)4N+) adsorb and congregate on the huge surface of AC-shell, forming electric double layer. The capacitance from electric double layer could offset the diminished capacity of CMS under large current. Thus, high power density could also be obtained.
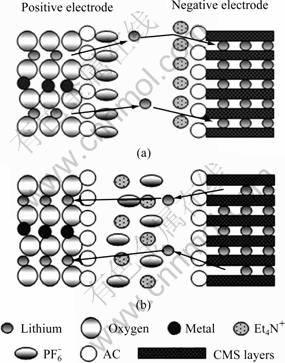
Fig.7 Diagram of working principle model in SLIC
5 Conclusions
1) The CMS/AC composite, as indicated by electrochemical tests analyses in EDLC and half-cell, combines the merits of EDLC and LIB.
2) The composite shows a high reversible capacity of 306.6 mAh/g (0.2C) in half-cell, along with a capacitance of 25.8 F/g in EDLC when a proper ratio of CMS to AC is adopted.
3) The composite also shows favorable rate performance and good cycle ability due to its unique core-shell structure.
References
[1] PASQUIER A D, PLITZ I, GURAL J, BADWAY F, AMATUCCI G G. Power-ion battery: Bridging the gap between Li-ion and supercapacitor chemistries [J]. J Power Sources, 2004, 136: 160-170.
[2] HONGYU W, MASAKI Y, ARJUN K T, HIROYOSHI N. From symmetric AC/AC to asymmetric AC/graphite, a progress in electrochemical capacitors [J]. J Power Sources, 2007, 169: 375-380.
[3] MATSUI K, TAKAHATA R, NOBUO A. Lithium ion capacitor: CN 1954397 [P]. 2007-04-25.
[4] AURBACH D, TELLER H, KOLTYPIN M. On the behavior of different types of graphite anodes [J]. J Power Sources, 2003, 119: 2-7.
[5] LI Fan-qun, LAI Yang-qing, ZHANG Zhi-an, GAO Hong-quan, YANG Juan. Electrochemical behaviors of Et4NBF4+LiPF6/ EC+PC+DMC electrolyte on graphite electrode [J]. Acta Phys Chim Sin, 2008, 24(7): 1302-1306.
[6] GAMBYA J, TABERNAA P L, SIMON P, FAUVARQUE J F, CHESNEAU M. Studies and characterisations of various activated carbons used for carbon/carbon super capacitors [J]. J Power Sources 2001, 101: 109-116.
[7] YANG Jing, LIU Ya-fei, CHEN Xiao-mei, HU Zhong-hua, ZHAO Guo-hua. Carbon electrode material with high densities of energy and power [J]. Acta Phys Chim Sin, 2008, 24(1): 13-19.
[8] KHOMENKO V, RAYMUNDO-PI?ERO E, B?GUIN F. High-energy density graphite/AC capacitor in organic electrolyte [J]. J Power Sources, 2008, 177: 643-651.
[9] HONGYU W, MASAKI Y. Graphite,a suitable positive electrode material for high-energy electrochemical capacitors [J]. Electrochem Commun, 2006, 8: 1481-1486.
[10] OSAMU H. Lithium ion capacitor [C]// 16th International Seminar on Double Layer: Capacitors & Hybrid Energy Storage Devices. Colombia, USA, 2006: 241-251.
[11] LI Jie, YANG Juan, HAO Xin, ZHANG Zhi-an, LAI Yan-qing, ZHOU Xiang-yang. Carbon composite as anode material electrode in super lithium ion capacitor [C]// TMS 2009 138th Annual Meeting & Exhibition. San Francisco, 2009: 391-398.
[12] DEYANG Q. Studies of the activated carbons used in double-layer supercapacitors [J]. J Power Sources, 2002, 109(2): 403-411.
[13] ZHOU Y F, XIE S, CHEN C H. Pyrolytic polyurea encapsulated natural graphite as anode material for lithium ion batteried [J]. Electrochimica Acta, 2005, 50: 4728-4735.
[14] HAN Y S, JUNG J H, LEE J Y. Investigation on the first-cycle charge loss of graphite anodes by coating of the pyrolytic carbon using tumbling CVD [J]. J Electrochem Soc, 2004, 151: A291-A295.
[15] LEROY S, MARTINEZ H, DEDRYV?RE R, LEMORDANT D, GONBEAU D. Influence of the lithium salt nature over the surface film formationon a graphite electrode in Li-ion batteries: An XPS study [J]. Appl Surf Sci, 2007, 253: 4895-4905.
[16] CONWAY B E. Eletrochemical supercapacitors: Scientific fundamentals and technological applications [M]. New York: Kluwer Academic Pubishers/Plenum Press, 1999: 131-132.
[17] LEWANDOWSKI A, GALINSKI M. Practical and theoretical limits for electrochemical double-layer capacitors [J]. J Power Sources, 2007, 173: 822-828.
[18] BRYNGELSSON H, STJERNDAHL M, GUSTAFSSON T, EDSTR?M K. How dynamic is the SEI [J]. J Power Sources, 2007, 174: 970-975.
[19] LI Jie, ZHANG Zhi-an, LAI Yan-qing, ZENG Tao. Super lithium ion capacitor: CN 200710035205.3 [P]. 2007-06-25.
[20] ZHANG Zhi-an, ZENG Tao, LI Jie, LAI Yan-qing. An electrolyte used in super lithium ion capacitor: CN 200710035206.8 [P]. 2007- 06-25.
(Edited by PENG Chao-qun)
Foundation item: Project(2007BAE12B00) supported by the National Key Technology R&D Program of China; Project(50974136) supported by the National Natural Science Foundation of China
Received date: 2010-05-20; Accepted date: 2010-07-09
Corresponding author: ZHOU Xiang-yang, Professor, PhD; Tel: +86-731-88836329; E-mail: yjjxgz@126.com