J. Cent. South Univ. (2016) 23: 362-369
DOI: 10.1007/s11771-016-3081-5

Optimal design of functionally graded PmPV/CNT nanocomposite cylindrical tube for purpose of torque transmission
Abolfazl Khalkhali, Sharif Khakshournia, Parvaneh Saberi
Automotive Simulation and Optimal Design Research Laboratory, School of Automotive Engineering, Iran University of Science & Technology, Tehran 16846-13114, Iran
Central South University Press and Springer-Verlag Berlin Heidelberg 2016
Abstract: Carbon nanotube (CNT)/polymer nanocomposites have vast application in industry because of their light mass and high strength. In this work, a cylindrical tube which is made up of functionally graded (FG) PmPV/CNT nanocomposite, is optimally designed for the purpose of torque transmission. The main confining parameters of a rotating shaft in torque transmission process are mass of the shaft, critical speed of rotation and critical buckling torque. It is required to solve a multi-objective optimization problem (MOP) to consider these three targets simultaneously in the process of design. The three-objective optimization problem for this case is defined and solved using a hybrid method of FEM and modified non-dominated sorting genetic algorithm (NSGA-II), by coupling two softwares, MATLAB and ABAQUS. Optimization process provides a set of non-dominated optimal design vectors. Then, two methods, nearest to ideal point (NIP) and technique for ordering preferences by similarity to ideal solution (TOPSIS), are employed to choose trade-off optimum design vectors. Optimum parameters that are obtained from this work are compared with the results of previous studies for similar cylindrical tubes made from composite or a hybrid of aluminum and composite that more than 20% improvement is observed in all of the objective functions.
Key words: nanocomposite; carbon nanotube (CNT); functionally graded materials (FGM); cylindrical tube; finite element method (FEM); modified NSGA-II technique for ordering preferences by similarity to ideal solution (TOPSIS); nearest to ideal point (NIP)
1 Introduction
Cylindrical tubes are commonly used as structural members (e.g., hollow structural sections), piping systems, members of offshore platforms, and also as drive shaft in automotive and aerospace industries [1]. To obtain better characteristics, application of functionally graded composite and nanocomposite materials was developed for cylindrical tubes. Functionally graded materials (FGMs) are a class of composites in which the material properties are graded but continuous along a particular direction. In other words, the volume fraction of constitutive materials vary uniformly and continuously along a given direction [2].
Carbon nanotubes (CNTs), were first discovered by Ijima [3] in 1991. Due to their remarkable structural, mechanical, thermal and electrical properties, CNTs are considered one of the most attractive reinforcements for functionally graded nanocomposites. Carbon nanotubes have unique mechanical properties, such as high stiffness and high axial strength besides large aspect ratios and small diameters. Therefore, they have widespread applications in light mass and high strength composites [3-8]. It has been demonstrated that with a small percentage of CNTs added in a polymer matrix material, the mechanical and electrical properties of these materials can be improved conspicuously.
In application of cylindrical tubes as drive shafts in vehicle and aerospace industries, the main function is torque transmission. Therefore, to have a high performance shaft, it is required to increase the critical buckling torque as much as possible. But there are some other confining parameters, such as geometry, mass of the shaft and critical speed of rotation which is directly proportional to the first natural torsion frequency. Many studies have been done on the composite cylindrical tubes to investigate these parameters. Loy et al [9] presented a study on the vibration of cylindrical tubes made of a functionally gradient material (FGM) composed of stainless steel and nickel. The purpose of that work was to investigate the natural frequencies, the influence of constituent volume fractions and the effects of configurations of the constituent materials on the natural frequencies.
It is observed that the natural frequency characteristics are similar to those obtained for homogeneous isotropic cylindrical tubes and those are affected by volume fraction and configuration of the reinforcement material. Pradhan et al [10] investigated the effects of boundary conditions and volume fractions on natural frequencies of the FG cylindrical tube. Shokrieh et al [11] presented an analysis on the torsional buckling of a composite drive shaft. They investigated the effect of different parameters, such as boundary conditions, fiber orientation angle and stacking sequence on the buckling torque. Moradi et al [12] carried out dynamic analysis of nanocomposite cylinders reinforced by single-walled carbon nanotubes (SWCNTs) subjected to an impact load by a mesh-free method free vibration and stress wave propagation analyses of carbon nanotube reinforced composite (CNTRC) cylinders were presented [12]. They investigated the effects of distribution and volume fraction of carbon nanotubes and cylinder thickness on the natural frequencies and stress wave propagation of CNTRC.
When the cylindrical tubes are used as the drive shafts of automotive, there are some different design parameters that should be considered, such as the first torsional natural frequency that is proportional to the critical speed, mass of the shaft and the critical buckling torque. To consider these three parameters simultaneously and obtain the best result, it is necessary to solve a multi-objective optimization problem (MOP). Genetic algorithm has a vast application in solving multi- objective optimization problems. NSGA-II, which was first presented by Deb et al [13], is a popular non-dominated sorting method based on genetic algorithm for MOPs that generates a set of non-dominated solutions (Pareto solutions). After obtaining the non-dominated points, it is desired to find some trade-off optimum points compromising objective functions. For this purpose, multi-criterion decision making (MCDM) approach should be applied. Some of the methods that can be used in this approach are the nearest to ideal point (NIP) method or technique for ordering preferences by similarity to ideal solution (TOPSIS). To improve NSGA-II, JAMALI proposed modified NSGA-II [14]. This method is employed successfully in many recent studies [15-16].
In this work, the optimized designing of nanocomposite cylindrical tube reinforced by CNTs for the purpose of torque transmission is done. This problem is solved by a hybrid method of FEM, modified NSGA II and MCDM, needing a coupling between the finite element software; ABAQUS and the programming language; MATLAB it has been shown that for a PmPV/cylindrical tube with different distribution of CNTs, the FG-V pattern has the best results in torque transmission [8]. Therefore, a cylindrical tube, which is made of functionally graded PmPV/CNT nanocomposite with FG-V pattern, is subjected to a torsional load and fixed at one end. The material properties are assumed to be graded in the thickness direction and estimated by the RVE model proposed by Hernandz-Perez and AVILES [18]. Three parameters are considered objective functions, mass of the shaft, critical buckling torque and critical speed of rotation. A finite element model of the problem is generated in ABAQUS, and optimization code is written in MATLAB software. By creating a coupling between ABAQUS and MATLAB, the three-objective optimization problem is solved using modified NSGA-II algorithm. Then, two methods, NIP and TOPSIS, are employed to choose trade-off optimum design vectors.
2 Material properties of functionally graded CNTRC cylindrical tube
The CNT reinforced composite (CNTRC) cylindrical tube which is considered in this study is made from a mixture of CNTs (along the longitudinal direction) and an isotropic polymer matrix. Several methods have been developed to predict the effective material properties of polymer/carbon nanotube composites, e.g., representative volume element (RVE) method [18], extended rule of mixture [19] and molecular dynamics [20]. The RVE model proposed by Hernandez- Perez and AVILES [18] is used to estimate the elastic properties such as elastic modulus, shear modulus and Poisson ratios along longitudinal and transverse directions. Since in this simulation the influence of interphase is taken into account, the RVE includes three phases, the matrix, the filler and the interphase, which is a virtual material that is considered to model the atomic bonds between the matrix and filler atoms. The effective mechanical properties of CNTRCs are obtained as follows [18]:
(1)

(2)
(3)
(4)
(5)
where Ez and Er are the elastic modulus along longitudinal and radius directions, respectively; urz and urθ are the Poisson ratios; Grθ is the shear modulus; L is length of the RVE; R and ri are outer and inner radiuses of the RVE, respectively; and J is the polar moment of inertia of the RVE’s section. In the above equations, the unknown parameters are: ΔL, ΔRI, ΔRII and α which are respectively the variation of RVE’s length and radius and the RVE’s twist angle. These parameters are determined from the finite element model of RVE which is created in the commercial FEM software, ABAQUS. The model is subjected to three different loadings, I-tension, II-pressure and III-torsion according to fig. 1. Finite element model of the RVE under pressure P0 carried out in ABAQUS is shown in fig. 2. To ensure that the deflections are in the elastic regions, very small values of torque and stresses according to table 1, are applied to the RVE’s model in the three mentioned loading cases. Substitution of the unknowns which are determined from the FEM model into eqs. (1) to (5), leads to finding the elastic properties of CNRTs.
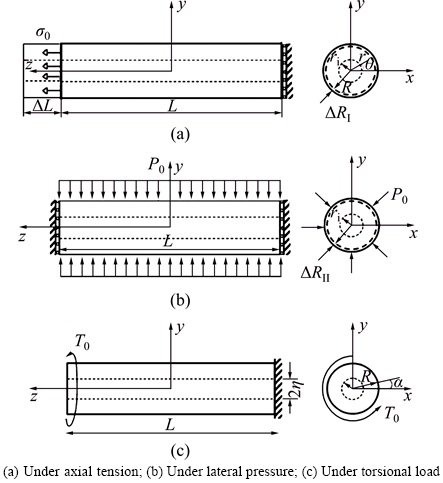
Fig. 1 Different loading cases applied to RVE:
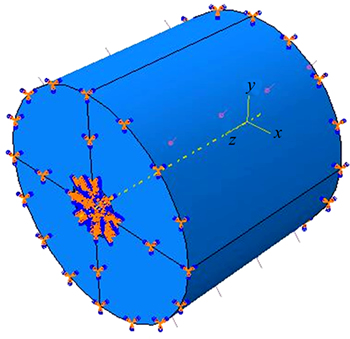
Fig. 2 Finite element model of RVE under pressure P0
Table 1 values of torque and stresses applied to RVE model
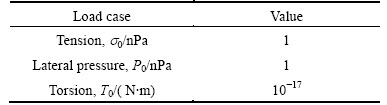
The profile of CNT’s distribution in the polymer matrix has an important effect on the elastic properties of CNTRC. For functionally graded fiber reinforced composites, three linear patterns can be commonly considered for the distribution of CNT reinforcements, FG-V, FG-Λ, and FG-X. Among these profiles, FG-V leads to the best values of weight and torsional strength for the cylindrical tube [17]. Therefore, FG-V pattern is assumed for profile of CNTs’ distribution in the cylindrical tube. Figure 3 shows the quality of distribution for this pattern through the thickness of the cylindrical tube, where ri and ro are the inner and outer radii, respectively, and
is the average volume traction of CNT in the nanocomposite. The volume fraction of CNT for such pattern is calculated as follows [17]:
(6)
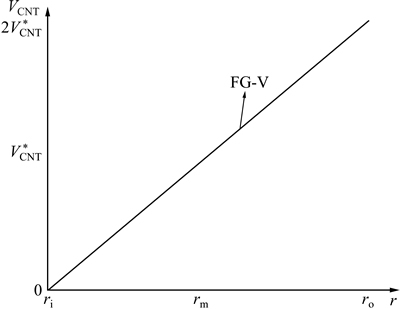
Fig. 3 Volume fraction of CNT for FG-V distribution pattern as a function of radius
3 Simulation of functionally graded CNTRC cylindrical tube under torque transmission
3.1 Finite element model
In order to have an acceptable comparison between the results of this simulation and previous studies, the dimensions of the cylindrical tube are considered according to Ref. [21]. The cylindrical tube has a length of 1.73 m and average diameter of 50.3 mm. The properties of matrix material which is PmPV polymer are: E=2.1 GPa, ρ=1150 kg/m3 and υ=0.34. Furthermore, the filler material is carbon nanotube with following properties: E=1 TPa, ρ=1400 kg/m3 and υ=0.3. Finite element model of the cylindrical tube is created in ABAQUS software and S4R which is an element with 4 nodes and 6 DOFs for each node is chosen as the element type. This element is typically used in shell analyses. Figure 4 shows the finite element model of the cylindrical tube.
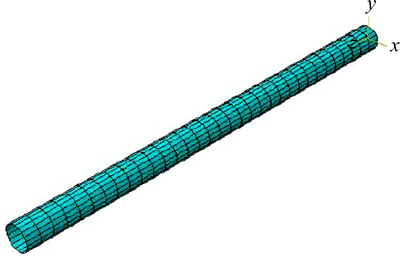
Fig. 4 Finite element model of nanocomposite cylindrical tube
3.2 Modal analysis
The critical speed that a drive shaft can tolerate is proportional to its first torsional natural frequency. Hence, it is desired to increase the first torsional natural frequency of a shaft in torque transmission. By considering the cylindrical tube as a cantilever beam, the first torsional natural frequency is computed by [22]
(7)
where fn, g, Ex, W, L and I are respectively first torsional natural frequency of the shaft, gravity acceleration, elastic modulus in axial direction, mass of the shaft per length, length of the shaft and the second moment of inertia, respectively. I, for a thin walled cylinder, is obtained by [22]
(8)
where r and t are average radius and thickness of the cylinder, respectively. To investigate effects of CNT volume fraction (V*) on the first torsional natural frequency of the cylindrical tube, a parametric study is carried out using FEM model. Figure 5 depicts the results of this parametric study, which shows that the first torsional natural frequency increases with the increase in the volume fraction of CNTs.
3.3 Critical buckling torque
Due to the long length of the cylendrical tube, it is more important to investigate occurrence of buckling under torsional loading. The value of critical buckling torque for an orthotropic cylindrical tube, can be obtained by [22]
(9)
where Tcr, Ex, Eh, t and r are the critical buckling torque, elastic modulus in longitudinal direction, average elastic modulus in radial direction, thickness and radius of the shaft, respectively. As it is obvious, the elastic modulus in radial direction has an important role in the value of critical buckling torque in a cylindrical shell. The changes in critical buckling torque to CNT volume fraction (V*) are extracted using FEM model and shown in fig. 5. This figure shows that the critical buckling torque also increases with the increase in the volume fraction of CNTs.
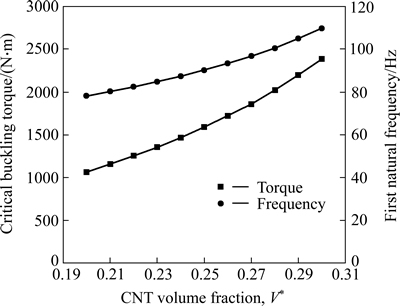
Fig. 5 Critical buckling torque and first torsional natural frequency of drive shaft versus average CNT volume fraction
4 Multi-objective optimization
4.1 non-dominated sorting genetic algorithm
Multi-objective optimization is an integral part of optimization activities and has a powerful practical importance, since almost all real-world optimization problems are ideally suited to be modeled using multiple conflicting objectives. The non-dominated sorting GA or NSGA-II procedure [13] is outlined in the following steps, for finding multiple Pareto-optimal solutions in a multi-objective optimization problem:
Step 1: The parent population Pt and offspring population Qt are combined to create
where t denotes the generation number. The combined population Rt is sorted according to non-constrain- dominance and the different fronts are ranked, Fi=1, 2, … etc. [23]
Step 2: New population Pt+1=Φ and a contour i=1 is set. Until |Pt+1|+|Fi|
and i=i+1.
Step 3: The crowding-sort (Fit+1|) solutions are included by using the crowding distance values in the sorted Fi to Pt+1.
Step 4: Offspring population Qt+1 from Pt+1 is created by using the crowded tournament selection, crossover and mutation operators.
NSGA-II algorithm which is a Pareto-based approach has a wide range usage in multi-objective problems [24-25]. But the density scale which is used in this algorithm for distribution of design vectors and preventing population accumulation has deficiencies in solving multi-objective problems with more than two objective functions. In this work, we’ve used modified NSGA-II algorithm which is applicable for optimization problems with infinite objective functions. The Pareto front obtained by modified NSGA-II optimization algorithm, prepares a set of non-dominated design points. It is necessary to employ some methods to choose the trade-off optimal design point through the Pareto front. In this work, nearest to ideal point (NIP) method and technique for order performance by similarity to ideal solution (TOPSIS) method are used [26].
4.2 Formulation of optimization problem
To achieve an optimum design for the cylindrical tube, a multi-objective optimization problem is solved using modified NSGA-II algorithm by considering three conflicting objective functions, mass of the shaft, critical buckling torque and first torsional natural frequency which is directly proportional to the critical speed of rotation of the cylindrical shell. The design parameters which vary through the optimization process are: average volume fraction of CNTs
the shafts thickness (t) and average radius of the shaft (rm). In this process, the finite element method and modified NSGA-II algorithm are used simultaneously. For this purpose, two software MATLAB and ABAQUS are coupled together during the run time. Modified NSGA-II has been written in MATLAB and the value of objective functions are computed by PYTHON code in ABAQUS. In each generation, design vectors are produced by modified NSGA-II code and are sent to ABAQUS. Then, after calculating the value of objective functions for each design vector in ABAQUS, the obtained values will be returned to MATLAB and the optimization process will be continued. Finally, the non-dominated optimum values of objective functions and the corresponding designing vectors can be obtained. The preceding algorithm is shown in fig. 6. Three constraints are considered for this problem, a constraint for mass of the shaft, another for critical buckling load and another one for first torsional natural frequency. If each of the constraints is reversed, by using penalty function method, tiny values will be assigned to critical buckling torque and first torsional natural frequency but the mass will get an extreme large value. The conditions and constraints of the optimization problem are summarized as follows:
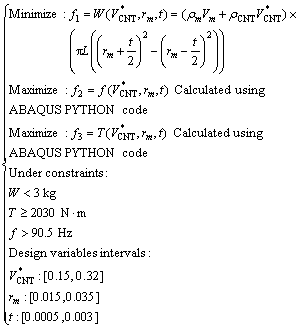
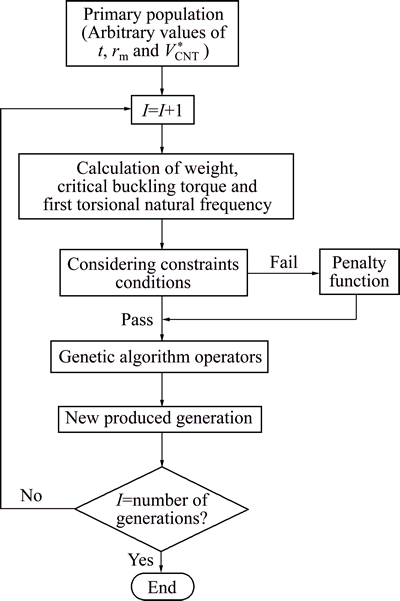
Fig. 6 flowchart of multi-optimization process for CNTRC
5 Results and discussions
5.1 Non-dominated optimum points obtained by optimization process
A multi-objective optimization of CNTRC cylindrical tube is performed for three objective functions with the goal of maximizing the first fundamental torsional frequency f, maximizing the critical buckling torque T and minimizing weight of the shaft W. A population of 50 individuals with a crossover probability (Pc) of 0.7 and mutation probability (Pm) of 0.07 have been used in 500 generation for all the objective functions. By solving the tri-objective optimization problem, non-dominated optimum points are obtained as shown in different planes in figs. 7 to 9.
5.2 Finding trade-off optimum design point
To find the trade-off optimum design point from non-dominated optimum points obtained in the previous section, NIP and TOPSIS methods are applied. The details of these methods can be found in previous publications [26]. In TOPSIS 1, the weight coefficient for all three objective functions, is considered equal to 1/3. In TOPSIS 2, the weight coefficient for weight of the shaft is equal to 1/2 and for the natural frequency and the critical buckling torque is considered equal to 1/4. It is obvious that in the second case, to find the optimum point, minimizing the mass, is the first preference comparing to maximizing other objective functions. The optimum design points which are obtained by each of NIP, TOPSIS 1 and TOPSIS 2 methods and also optimum points of single objective optimization for mass (SOW), first torsional natural frequency (SOF) and critical buckling torque (SOT) are listed in tables 2. In table 3, the values of mass, first torsional natural frequency and critical buckling torque which are obtained from mentioned optimization methods for a CNTRC cylindrical tube, are compared with the values obtained by Badieh et al [21] and Khalkhali et al [22] for a hybrid of aluminum and composite drive shafts. According to this table, results of natural frequency and critical buckling torque for an optimized CNTRC shaft, are improved evidently. This comparison is also shown in figs. 7 to 9.
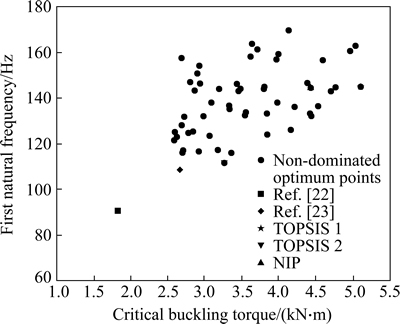
Fig. 7 Non-dominated optimum points in plane of critical buckling torque and first torsional natural frequency
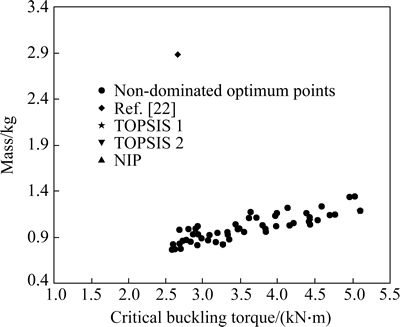
Fig. 8 Non-dominated optimum points in plane of critical buckling torque and weight
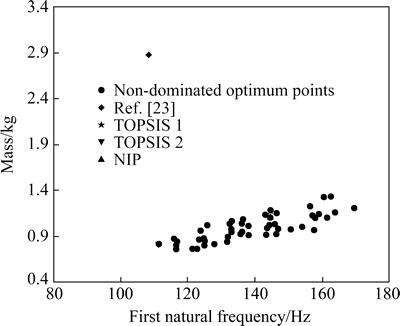
Fig. 9 Non-dominated optimum points in plane of first torsional natural frequency and weight
Figure 10 depicts the relation between first torsional natural frequency and radius of the shaft in optimal case
which shows that there is a linear relation between them. According to this figure and passing a line through its points, the natural frequency of the optimum cylindrical tube can be estimated by
f=4536.9rm+8.3844 (10)
Moreover, according to fig. 10, for any radius in interval 25 mm to 35 mm, there is an optimum design for the cylindrical tube.
Table 2 Trade-off optimum design points for CNTRC cylindrical tube by different methods
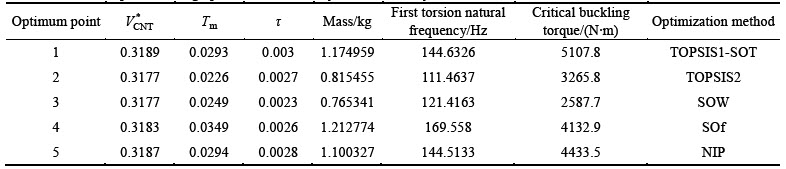
Table 3 values of mass, first torsional natural frequency and critical buckling torque for cylindrical tube
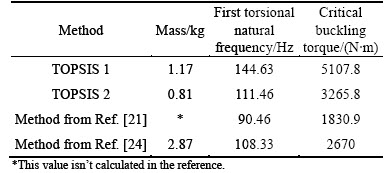
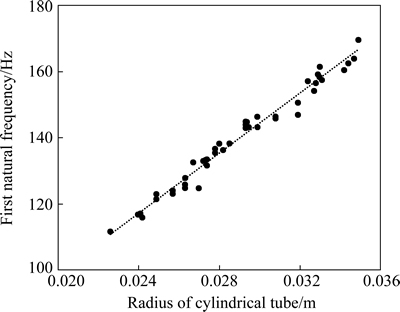
Fig. 10 changes of first torsional natural frequency to radius of cylindrical tube corresponding to non-dominated optimum points of figures 6 to 8
As another achievement, fig. 11 shows that there is a direct relation between the critical buckling torque and the thickness of the shaft. Increasing the thickness has a clear effect on increase of the critical buckling torque. By passing an exponential function through the points of this figure, the critical buckling torque of the optimum cylindrical tube can be estimated by following equation:
T=386.16e857t (11)
In addition, according to fig. 11, it can be concluded that the optimum thickness for designing the cylindrical tube is between 2.2 mm and 3 mm.
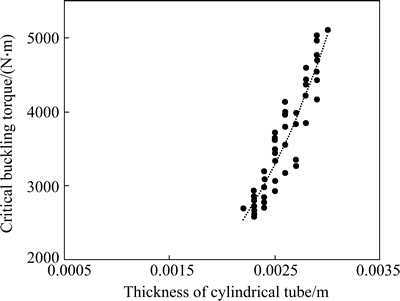
Fig. 11 changes of critical buckling torque to thickness of cylindrical tube corresponding to non-dominated optimum points of figs. 6 to 8
6 Conclusions
1) The results show that adding CNTs into Pm/PV polymer with FG-V pattern has an evident effect on improvement of mechanical properties of the cylindrical tube compared to composite one. The results of optimization included a set of non-dominant design points.
2) The optimum design points are found by methods such as TOPSIS and NIP. The minimum value for mass of the shaft is obtained from TOPSIS 2. The maximum values for first torsional natural frequency and critical buckling torque are obtained by TOPSIS 1. Dependent on the kind of application and the importance of each objective function, designer can choose properties of the cylindrical tube, based on each of these optimized cases.
3) The relation between objective functions and design variables is also investigated. Increasing the volume fraction of CNTs causes an increase in the value of all three objective functions. The natural frequency has a linear relation with mean radius of the shaft and the value of critical buckling torque is strongly under the effect of thickness changes.
References
[1] Salahifar R, Mohareb M. Analysis of circular cylindrical tubes under harmonic forces [J]. Thin walled structures, 2010, 48: 528-539.
[2] Malekzade P, Heydarpour Y. Free vibration analysis of rotating functionally graded cylindrical tubes in thermal environment [J]. Composite structures, 2012, 94: 2971-2981.
[3] Ijima S. Helical microtubules of graphitic carbon [J]. Nature, 1991, 354: 56-58.
[4] Joshi U A, Satish s C, Harsha S P. Effect of carbon nanotube orientation on the mechanical properties of nanocomposites [J]. Composites Part B: Engineering, 2012, 43: 2063-2071.
[5] Tai Le-minh, Huang Shyh-chour. Modeling and analysis the effect of helical carbon nanotube morphology on the mechanical properties of nanocomposites using hexagonal representative volume element [J]. Applied Mechanics and Materials, 2014, 577: .
[6] Nima, Nouri, et al. Fabrication and mechanical property prediction of carbon nanotube reinforced aluminum nanocomposites [J]. Materials & Design, 2012, 34: 1-14.
[7] Ping Z, Lei Z X, Liew K M. Static and free vibration analyses of carbon nanotube-reinforced composite plates using finite element method with first order shear deformation plate theory [J]. Composite Structures, 2012, 94: 1450-1460.
[8] Sadollah E, Rafii-Tabar H. Influence of hydrogen functionalization on mechanical properties of graphene and CNT reinforced in chitosan biological polymer: Multi-scale computational modeling [J]. Computational Materials Science, 2015, 101: 189-193.
[9] Loy C T, Lam K Y, Reddy J N. Vibration of functionally graded cylindrical tube [J]. International Journal of mechanical science, 1999, 41: 309-324.
[10] Pradhan S C, Loy C T, Lam K M, Reddy J N. Vibration characteristics of functionally graded cylindrical tubes under various boundary conditions [J]. 2000, 61: 111-129.
[11] Shokrieh M, Hasani A, Lessard L B. Shear buckling of a composite drive shaft under torsion [J]. Composite structures, 2004, 64(10): 63-69.
[12] Moradi R, Foroutan M, Pourasghar A. Dynamic analysis of functionally graded nanocomposite cylinders reinforced by carbon nanotubes by a meshfree method [J]. Materials and design, 2013, 44: 256-266.
[13] Deb K, Agrawal S, Pratap A, Meyarivan T. A fast and elitist multi-objective genetic algorithm: NSGA-II [J]. IEEE Trans on Evolutionary Computation, 2002, 61: 182-197.
[14] Jamali A, Nariman-zadeh N, Darvizeh A, Masoumi A, Hamrang S. Multi-objective evolutionary optimization of polynomial neural networks for modeling and prediction of explosive cutting process [J]. Intemation Journal of engineering applications of artificial intelligence, 2009, 22: 676-687.
[15] Khalkhali A, Nariman-zadeh N, Darvizeh A, Masoumi A, Notghi B. Reliability-based robust multi-objective crashworthiness optimization of s-shaped box beams with parametric uncertainties [J]. Int Journal of crashworthiness, 2010, 15: 443-456.
[16] Khalkhali A, Safikhani H. Pareto based multi-objective optimization of cyclone vortex finder using CFD, GMDH type neural networks and genetic algorithm [J]. Engineering optimization, 2012, 44: .
[17] Khakshournia S H. Multi-objective optimization of carbon nanotube reinforced nanocomposite shaft [D]. Tehran, Iran: Automotive Engineering School, Iran University of Science and Technology, 2013.
[18] Hernandez-Perez A, Aviles F. Modeling the influence of interphase on the elastic properties of carbon nanotube composites [J]. Computational materials and science, 2010, 47: 926-933.
[19] Zhu P, Lei Z, Liew K. Static and free vibration analysis of carbon nanotube-reinforced composite plates using finite element method with first order shear deformation plate theory [J]. Composite structures, 2010, 94: 1450-1460.
[20] Han Y, Elliotte J. Molecular dynamics simulations of the elastic properties of polymer/carbon nanotube composites [J]. Computational material science, 2007, 39: 315-325.
[21] Badieh M A, Mahdi E, Hamouda A M S. An investigation into hybrid carbon/glass fiber reinforced epoxy composite automotive drive shaft [J]. Materials and Designs, 2011, 32: 1485-1500.
[22] Khalkhali A, Nikghalb E, Norouzian M. Multi-objective optimization of hybrid carbon/glass fiber reinforced epoxy composite automotive drive shaft [J]. International Journal of Engineering, 2015, 28(4): 583-592.
[23] Pelletier J L, Senthil S. Multi-objective optimization of fiber reinforced composite laminates for strength, stiffnrss and minimal mass [J]. Computer & Structures, 2006, 184: 2065-2080.
[24] Khalkhali A, Farajpoor M, Safikhani H. Modeling and Multi-objective optimization of forward-curved blades centrifugal fans using CFD and neural networks [J]. Transactions of Canadian society for mechanical engineering, 2011, 35(1).
[25] Nariman-Zadeh N, Salehpour M, Jamali A, Haghloo E. Pareto optimization of a five-degree of freedom vehicle vibration model using a multi-objective uniform-diversity genetic algorithm (MUGA) [j]. Engineering applications of artificial intelligence, 2011, 23: 543-551.
[26] Khalkhali A, Khakshournia S, Nariman-zadeh N. A hybrid method of FEM, modified NSGA II and TOPSIS for structural optimization of sandwich panels with corrugated core [J]. Journal of Sandwich Structures & materials, 2014, 16: 583-592.
(Edited by DENG Lü-xiang)
Received date: 2015-03-18; Accepted date: 2015-07-25
Corresponding author: Abolfazl Khalkhali; Tel: +98-2177491225; E-mail: ab_khalkhali@iust.ac.ir