
Fabrication, microstructure and properties of electron beam-physical
vapor deposited TiAl sheet and TiAl/Nb laminated composites
HAN Jie-cai(韩杰才), ZHANG De-ming(章德铭), CHEN Gui-qing(陈贵清), MENG Song-he(孟松鹤), ZHANG Xing-hong(张幸红)
Center for Composite Materials, Harbin Institute of Technology, Harbin 150080, China
Received 10 April 2006; accepted 25 April 2006
Abstract: The TiAl-based alloys sheet with 150 mm×100 mm×0.4 mm and the TiAl/Nb laminated composites with 150 mm×100 mm×0.2 mm were fabricated by using electron beam-physical vapor deposition(EB-PVD) method, respectively. The microstructure and properties of the sheet were investigated by AFM, SEM and EDS. The results show that the TiAl based alloys sheet has a good surface quality, and its microstructure is columnar crystal. The component of the alloys indicates a regular and periodical gradient change which leads to the spontaneous delamination along the normal direction of substrate. In the TiAl/Nb laminated composites alternating overlaid by TiAl of 24 layers and Nb of 23 layers, the interface of each layer evenly distributed throughout the cross-section is transparent, and the interlayer spacing is about 8 μm. The component of TiAl layers also changes regularly along the normal direction of substrate, but no delamination phenomenon is found. The TiAl/Nb laminated composites have better ductility than the TiAl-based alloys sheet.
Key words: electron beam-physical vapor deposition; TiAl-based alloys sheet; TiAl/Nb laminated composites; fabrication; microstructure; property
1 Introduction
TiAl-based alloys are being considered the most promising lightmass high-temperature structural materials, and they are potential candidates to replace the Ti-based alloys and Ni-based superalloys for applications in both aerospace and automotive industries[1, 2]. Especially, the TiAl-based alloys sheet can be used as thermal protection system panel, exhaust nozzle, low-pressure turbine blades, etc; for these, 40% mass reductions are possible[3]. However, it is difficult to prepare the TiAl sheet because of their limited ductility at temperatures below 973 K. To overcome this drawback, using the Nb layers as the toughener seems to be a feasible method, and the research in correlative fields is becoming the focus of people’s attention[4].
The traditional rolling process is not suitable for the preparation of TiAl sheet and TiAl/Nb laminated composites, because of the limited dimension and thickness of the prepared sheet. Powder metallurgy technique is apt to induce non-metallic impurities in the prepared sheet that usually has poor density. As a new technology of sheet preparation, electron beam-physical vapor deposition (EB-PVD) can be used to prepare the brittle materials sheet and laminated composites with many advantages, such as higher deposition speed and thermal efficiency, purer and near-net shaped product[5]. EB-PVD process can be described as that using high-speed electron produced by electron gun under the vacuum environment bombards the target materials, which will melt, turn into vapor and then condense on the substrate surface. The extreme dimension of sheet fabricated by EB-PVD is d1 000 mm, and the sheet thickness is from 0.1 mm to 5 mm, which can satisfy the preparation requirements of different materials and different application environment for sheet.
In this study, the TiAl-based alloys sheet with 150 mm×100 mm×0.4 mm and the TiAl/Nb laminated composites with 150 mm×100 mm×0.2 mm were fabricated successfully by using EB-PVD method, respectively. And the microstructure and properties of the two kinds of sheets were investigated comparatively by AFM, SEM and EDS.
2 Experimental
The ingots of TiAl-based alloys used in this study were prepared by vacuum induction melting two times on water-cooled copper crucible. And the nominal composition of the ingots is Ti-47Al (molar fraction). High purity Nb ingots (99.8 %) were used. The experimental device is UE-204 type EB-PVD equipment with horizontal feed mode, as shown in Fig.1. To take off the ultimate sheet from the substrate conveniently, a ceramic stripper layer with about 20 μm should be deposited on the substrate before formal evaporation. The evaporation of TiAl-based alloys was continuous; but in the evaporation of TiAl/Nb laminated composites, the TiAl and Nb ingots were evaporated alternatingly with 3 min and 1 min respectively. The deposition conditions of TiAl and Nb are listed in Table 1. After evaporation, the substrate was removed to the load chamber, and then taken out from furnace when cooled to 423 K. At the room temperature, four sheets with dimension of 150 mm×100 mm were gained by mechanical stripping from the substrate surface.

Fig.1 Principle scheme of EB-PVD process
Table 1 Major technical parameters of experiment
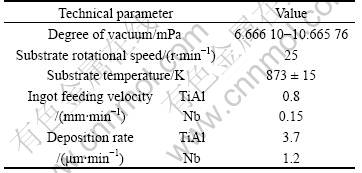
The macro-microscopic morphology on the surface of the TiAl-based alloys sheet fabricated by EB-PVD is shown in Fig.2. It can be seen that the grain size on the surface of the sheet is less than 2 μm, and the sheet has small surface roughness and good surface quality. The observed results on the surface of the TiAl/Nb laminated composites are similar to that of the TiAl-based alloys sheet. And these mean that it is feasible to prepare the TiAl-based alloys sheet and TiAl/Nb laminated composites by EB-PVD process. The morphology and composition on cross-section of specimens were analyzed by SEM equipped with EDS (Hitachi S-4700).
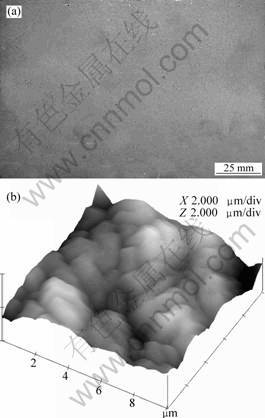
Fig.2 Macro-microscopic morphologies on surface of TiAl- based alloys sheet fabricated by EB-PVD: (a) Macrograph;(b) AFM micrograph
3 Results and discussion
Fig.3 shows the micrographs on cross-section of two kinds of specimens. As can be seen from Fig.3(a), there is spontaneous delamination alternating overlaid by Ti-rich area and Al-rich area inside the TiAl-based alloys sheet, the microstructure of which is columnar crystal. The formation of columnar crystal is related with the substrate temperature and deposition speed[9], and the delamination phenomenon is caused by the phase evolution derived from the composition fluctuation. It can be found from Fig.3(b) that inside the TiAl/Nb laminated composites, TiAl of 24 layers and Nb of 23 lays are evenly distributed throughout the cross-section. The interface between TiAl and Nb is transparent, and the interlayer spacing is about 8 μm, but no delamination phenomenon is found in the TiAl layers.
The linear distribution curves of elements on cross-section of specimens are shown in Fig.4. It can be seen that the Ti and Al contents in those two kinds of sheets show a regular gradient variation along the normal direction of substrate. Since having no gaseous TiAl, the TiAl-based alloys must be decomposed into Ti vapor and Al vapor and then condense on the substrate surface when evaporation. And SIEGFRIED et al[6] indicated that the substrate temperature can determine the sticking coefficient of vapor atoms on the substrate surface and affect their deposition rate. So the few difference of compositional variation of interlamination should be attributed to the little temperature fluctuation on the substrate surface.
The TiAl-based alloys sheet is composed of γ, α2 and τ phase, and the TiAl layers in the composites are composed of γ and τ phase. This phenomenon can be explained by that the evaporation of each TiAl layer in the composites is intermittent with little time, which makes the thickness of each TiAl layer much smaller than that of every layer in the TiAl-based alloys sheet. Thus, although the composition shows a gradient variation, the variation has not integrated periodicity and is not big enough to change the phases, which leads to the TiAl layers in the composites without α2 phase and delamination phenomenon.
The fracture morphology of TiAl-based alloys sheet is further proved that the microstructure of the alloys is columnar crystal whose pattern and dimension are uniform (see Fig.5(a)), which indicates that the delamination phenomenon has no effect on the growth of the columnar crystal. Furthermore, it can be found that the fractures of the alloys are the manner of brittle intergranular fracture, and this shows that the plasticity

Fig.3 Micrographs on cross-section of specimens: (a) TiAl; (b) TiAl/Nb
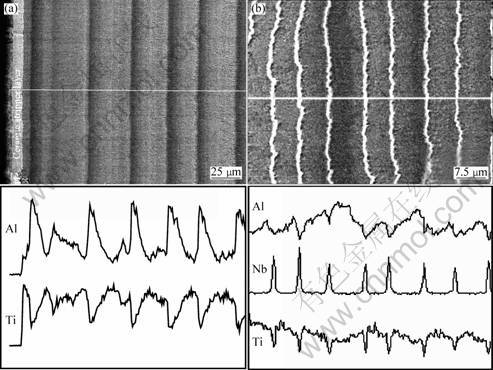
Fig.4 Linear distribution of elements on cross-section of specimens: (a) TiAl; (b) TiAl/Nb
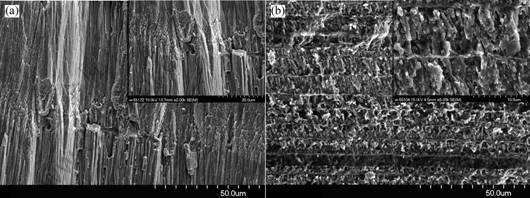
Fig.5 SEM fractographs of specimens: (a) TiAl; (b) TiAl/Nb
of as-deposited TiAl-based alloys sheet is poor at room temperature. The main reasons can be summed up as follows: essential brittleness of materials[7], higher porosity caused by SHADOW and KIRKENDALL Effect[8, 9], bigger internal stresses inner as-deposited sheet, and weaker combination of each columnar crystal.
The fracture morphology of TiAl/Nb laminated composites is much more complex than that of the TiAl-based alloys sheet, as shown in Fig.5(b). It can be seen that the Nb layers are transparent and continuous distributed, and are combined well with the TiAl layers. Further more, it can also be found that the micrographs of the columnar crystal in the TiAl layers are not very distinct, and the fractures of the composites are the mixed manner of brittle intergranular fracture with some ductile quasi-cleavage fracture, which indicates that the addition of Nb layers can improve the plasticity of TiAl-based alloys at room temperature effectively. This is because that during fracture process, the Nb layers cause crack deflection, crack propagation resistance and energy increase, consequently some plastic deformation occurs.
4 Conclusions
The TiAl-based alloys sheet with 150 mm × 100 mm × 0.4 mm and the TiAl/Nb laminated composites with 150 mm × 100 mm × 0.2 mm can be fabricated successfully by using EB-PVD method, respectively. The TiAl based alloys sheet has a good surface quality, the microstructure of which is columnar crystal. The regular and periodical gradient change of composition leads to the natural delamination alternating overlaid by Ti-rich area and Al-rich area inside the alloys. The TiAl/Nb laminated composites are alternating overlaid by TiAl of 24 layers and Nb of 23 layers which are evenly distributed throughout the cross-section. The interface of interlamination is transparent, and the interlayer spacing is about 8 μm. The fact of having no delamination phenomenon in the TiAl layers can be attributed to the intermittent evaporation with little time. Compared with the TiAl-based alloys sheet, since crack deflection caused by the Nb layers increases crack propagation energy during fracture process, the fractures of the TiAl/Nb laminated composites are diverted from the manner of brittle intergranular fracture to the mixed manner of brittle intergranular fracture with some ductile quasi-cleavage fracture.
References
[1] Dimiduk D M. Gamma titanium aluminide alloys—an assessment within the competition of aerospace structural materials[J]. Materials Science and Engineering, 1999, A263: 281-288.
[2] Edward A L. Gamma titanium aluminides as prospective structural materials[J]. Intermetallics, 2000, 8: 1339-1345.
[3] Austin C M. Current status of gamma Ti aluminides for aerospace applications[J]. Current Opinion in Solid State and Materials Science, 1999, 4: 239-242.
[4] LOu J, YE F, LI M, SOBOYEJO W O. Ductile layer toughening of brittle intermetallic composites[J]. J Mater Sci, 2002, 37: 3023-3034.
[5] Singh J, Wolfe D E. Nano and macro-structured component fabrication by electron beam-physical vapor deposition(EB-PVD)[J]. J Mater Sci, 2005, 40: 1-26.
[6] Siegfried S, Ullrich H, Siegfried P. Electron Beam Technology[M]. New York: Wiley-Interscience Publication, 1982.
[7] Wiezorek J M K, DeLuca P M, Fraser H L. Mechanisms of plasticity and fracture of partially lamellar titanium aluminum[J]. Intermetallics, 2000, 8: 99-113.
[8] Zhu X f, Williams S W, Lim L C, ZHANG S, WU Z Q. Micro-structure and internal stresses of physical vapor deposited film[J]. Physics, 1998, 27(1): 37-40.(in Chinese)
[9] Liu F X, HE Y H, LU Y, HUANG B Y, LI Z. Present status and future prospects for PM TiAl-based alloy sheet[J]. Rare Metal Materials and Engineering, 2005, 34(2): 169-173.(in Chinese)
(Edited by YANG You-ping)
Foundation item: Projects(90205034, 90405016) supported by the National Natural Science Foundation of China