J. Cent. South Univ. Technol. (2007)02-0149-04
DOI: 10.1007/s11771-007-0030-3 
Phase composition, transition and structure stability of functionally graded cemented carbide with dual phase structure
ZHANG Li(张 立)1, CHEN Shu(陈 述)2, XIONG Xiang-jun(熊湘君)1, HE Yue-hui(贺跃辉)1,
HUANG Bai-yun(黄伯云)1, ZHANG Chuan-fu(张传福)3
(1. State Key Laboratory of Powder Metallurgy, Central South University, Changsha 410083, China;
2. Changsha Mining and Metallurgy Research Institute, Changsha 410012, China;
3. School of Metallurgical Science and Engineering, Central South University, Changsha 410083, China)
Abstract: The phase composition, phase transition and phase structure transformation of the wire-cut section of functionally graded WC-Co cemented carbide with dual phase structure were investigated by XRD phase analysis. It is shown that the composition of η phase in the core zone is Co3W3C (M6C type). The structure of cobalt based solid solution binder phase is fcc type. At the cooling stage of the sintering process, the phase transition of η phase, i.e. M6C→M12C and the martensitic phase transition of the cobalt based solid solution binder phase, i.e. fcc→hcp are suppressed, which facilitates the strengthening of the alloy. Because the instantaneous temperature of the discharge channel is as high as 10 000 ℃ during the wire cutting process, the processed surface is oxidized. Nevertheless, the oxide layer thickness is in micro grade. In the oxide film, η phase is decomposed into W2C and CoO, and cobalt based solid solution binder is selectively oxidized, while WC remains stable due to the existence of carbon containing liquid organic cutting medium.
Key words: cemented carbide; dual phase structure; functionally graded material; phase identification; fracture toughness testing
1 Introduction
Functionally graded materials (FGMs) have been successfully implemented in many applications due to their ability to tailor properties gradually and avoid stress concentrations resulted from the abrupt changes in properties between two dissimilar interfaces. As a family member of FGMs, functionally graded cemented carbide with dual phase structure, for short DP cemented carbide, is characterized by three zones structure, i.e. surface zone with low cobalt content, intermediate zone (cobalt-rich zone) with cobalt graded structure, both with WC+γ conventional structure where γ is cobalt based solid solution binder phase, i.e. Co (W, C), and core zone with WC+γ+η unconventional structure[1]. Because of its perfect combination of high wear resistance and high toughness, it has been successfully applied in the modern tools for rock drilling, mineral cutting, oil drilling and in tools for concrete and asphalt milling[1-6]. In recent years, Chinese researchers have made remarkable progress in the study of the mechanisms for the control of the grain size and distribution of η phase, the formation of graded structure, as well as the property characterization of DP cemented carbide[7-12]. As is known that martensitic phase transition of the cobalt based solid solution binder phase, i.e. fcc→hcp can take place during the cooling stage of the sintering process and there are many kinds of phase composition of η phase. The objective of this work is to investigate the composition, transition and structure stability of the phases in DP cemented carbide so as to shed more light upon the understanding of the strengthening mechanism.
2 Experimental
DP cemented carbide was prepared through two steps technique, i.e. the preparation of low carbon containing precursor with WC+γ+η unconventional structure by vacuum liquid phase sintering, followed by carburizing treatment. The basic composition of the alloy is WC-6%Co (mass fraction, the same in the following). The quarter of DP cemented carbide rock bit button, 25 mm in diameter and 34 mm in height, was cut out and then separated into two pieces in the direction of height by wire cutting. The section was used in the observation and analysis. The grinding of the wire-cut section was carried out on the equipment for metallurgical specimen preparation from the Struers Company, Denmark. Metal-bond diamond wheel of 181 μm in granularity was used for the grinding with running water as grinding medium. The grinding time is 2 min. The determination of the phase composition of the wire-cut section and the ground section was performed on Rigaku Dmax /2550VB X-ray diffraction (XRD) instrument with Cu Kα radiation (40 kV, 300 mA), scanning speed of 0.15(?)/s in the range of 10?-90?.
The specimen for microstructure observation was etched with Murakami’s reagent (10 g NaOH, 10 g potassium ferricyanide and 100 mL distilled water) at room temperature for 3-4 min.
3 Results
3.1 Microstructure
A typical DP cemented carbide structure with three zones is observed on the section, i.e. surface zone with low cobalt content, intermediate zone (cobalt-rich zone) with cobalt graded structure, both with WC+γ conventional structure, and core zone with WC+γ+η unconventional structure. The microstructures of the core zone with fine η phase and the surface zone with WC+γ conventional structure are presented in Figs.1 and 2.
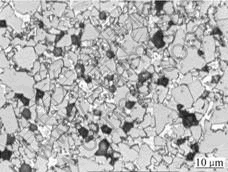
Fig.1 Microstructure of core zone with fine η phase(The black, bright and gray with multangular shape are η phase, γ phase and WC,respectively)

Fig.2 Microstructure of surface zone with WC and γ phases
3.2 Phase identification
The results of XRD phase analysis of the wire-cut section and the ground section are shown in Figs.3 and 4, and Tables 1 and 2. It is known from Fig.3 that there are WC, W2C, as well as CoO phases on the wire-cut section. Obviously, it is the result of surface oxidation. From Table 1 it is known that the content of CoO is as high as 20.2%-34.8%. Because of the existence of η phase in the alloy, the tungsten content in cobalt increases dramatically as indicated in Fig.5. It is known from Fig.5 that, for WC-25Co cemented carbide, when the carbon content in the alloy decreases from 4.52% to 4.25%, the tungsten content in cobalt increases dramatically from 2.6% to 20.2%. Therefore, the mass fraction of cobalt based solid solution binder phase increases remarkably, which is an important reason for the higher cobalt oxide mass fraction. Nevertheless, it should be mentioned that the error in analysis should also be taken into consideration.
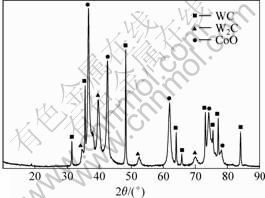
Fig.3 XRD pattern of wire-cut section
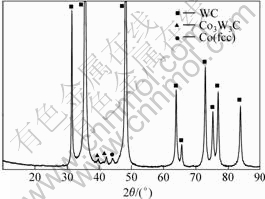
Fig.4 XRD pattern of ground section
From Fig.4 and Table 2, it is known that there are WC, γ with fcc structure, as well as η (Co3W3C) phases on the ground section, being in agreement with the microstructures shown in Figs.1 and 2.
Table 1 Comparative content of phases of wire-cut section by XRD analysis(mass fraction, %)
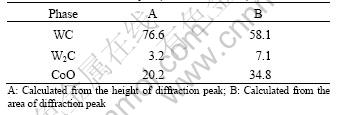
Table 2 Analysis and comparison of 2θ between XRD patterns of ground section and counterpart phase in PDF card,
not including WC phase
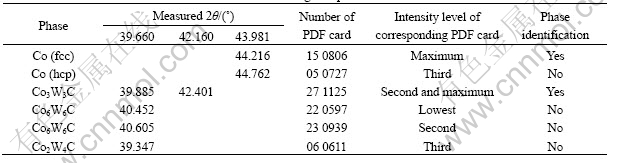
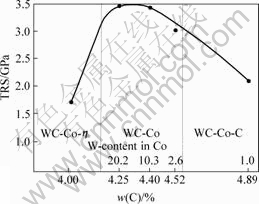
Fig.5 Transverse rupture strength (TRS) of WC-25Co cemented carbide as function of W content in binder and total carbon content [13]
4 Discussion
4.1 Phase transition in alloy
From the phase identification result of the ground section, it is known that the composition of η phase in the core zone is Co3W3C, belonging to M6C type (M=Co, W); the structure of the cobalt based solid solution binder phase is fcc type, thus the martensitic phase transition of the binder phase, i.e. fcc→hcp is suppressed. It can be deduced that the suppression of the martensitic phase transition is due to the dramatic increase in the solid solubility of tungsten in cobalt. Because of the much more glide system in fcc than that in hcp, the suppression of the martensitic phase transition must accompany with the strengthening of the alloy.
Fig.6 shows the vertical section phase diagram of WC-10Co cemented carbide. It is known that when the carbon content is relatively low, two types of η phase, i.e. M6C and M12C, with Gibbs free energy of formation,?f
of -77.2 and -130 kJ/mol [14], respectively may appear in the alloy. Nevertheless, it is shown that at the cooling stage of the sintering process, the phase transition of η phase, i.e. M6C→M12C is suppressed although M12C is more stable than M6C at room temperature. The high solid solubility of tungsten in cobalt may stabilize cobalt as the binder phase and thus prevent the recombination of cobalt and tungsten with M6C to form M12C. Obviously, the suppression of the transition from M6C to M12C facilitates the improvement of toughness because more cobalt can act as the binder and the toughness of WC-Co cemented carbide is in proportion to the mass fraction of cobalt as the binder phase.
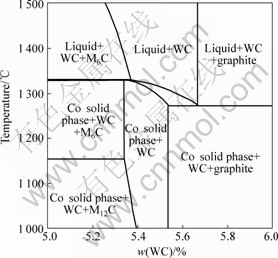
Fig.6 Vertical section phase diagram of WC-10Co cemented carbide [13]
4.2 Transformation of phase structure resulted from wire cutting
Wire cutting is one type of electrical discharge machining (EDM), which is performed by means of electric sparks. The sparks jump between two electrodes subjected to a given voltage which are submerged in an insulating liquid (dielectric fluid)[15]. This electric spark produces intense heat with temperature reaching 8 000 to 12 000 ℃ at the discharge channel, melting almost anything. For EDM, the spark is very carefully controlled and localized so that it only affects the surface of the material.
According to the physical principle of EDM, it is known that the existence of WC, W2C as well as CoO phases on the wire-cut section is a consequential result of surface oxidation reaction resulted from the extremely high temperature. It can be deduced from the phase identification results of the wire-cut section and the ground section that the following surface oxidation reaction may take place during the wire cutting process which is carried out in a carbon containing liquid dielectric:
2Co3W3C+C+3O2→3W2C+6CoO (1)
2Co(W, C)+O2→2Co(W, C)O (2)
2WC+C+2O2→W2C+2CO2 (3)
From Table 1 it is known that the content of W2C is as low as 3.2%-7.1%, therefore the possibility of reaction (3) is very small.
From the fact that the oxide layer can be easily removed through grinding within 2 min by diamond wheel of 181 μm, it can be deduced that the oxide layer thickness is in micro grade.
From the discussion above, it is involuntary to associate the change in the surface state resulted from wire cutting with the fracture toughness testing techniques. Single edge notched beam (SENB, usually made by wire cutting or diamond saw) method is one of the commonly used test techniques for fracture toughness assessment[16-17]. However, few attention is paid on the effect of the oxide film resulted from wire cutting on the test results. It is necessary to mention that even though the oxide film thickness is in micro grade, the change in surface state and thus surface properties must play a role in affecting the crack deflection and propagation, and thus the test veracity.
5 Conclusions
1) At the cooling stage of the sintering process, the phase transition of η phase, i.e. M6C→M12C and the martensitic phase transition of the cobalt based solid solution binder phase, i.e. fcc→hcp are suppressed, which facilitates the strengthening of the alloy.
2) During the wire cutting process, the processed surface is oxidized. Within the oxide film, η phase is decomposed into W2C and CoO, cobalt based solid solution binder phase is selectively oxidized and WC remains stable.
3) After being machined by wire cutting or other treatment which may cause the change in the surface properties, cemented carbide tools should be treated by proper means, e.g. reduction, grinding, so as to eliminate the effect of machining on the composition, structure and properties of the processed surface, and thus avoid the unconventional breakdown.
References
[1] BROOKES K J A. Rock tools lead the way in drilling[J]. Metal Powder Report, 1992, 47(12): 48-50.
[2] FISCHER UDO K R, HARTZELL ERIK T, AKERMAN JAN G. H. Cemented Carbide Body used Preferably for Rock Drilling and Mineral Cutting[P]. US patent: 4743515. 1988-5-10.
[3] FISCHER UDO K R, HARTZELL ERIK T, AKERMAN JAN G. H. Cemented Carbide Body with a Binder Phase Gradient and Method of Making the Same [P]. US patent: 4820482. 1989-4-11.
[4] HARTZELL ERIK T, AKERMAN JAN G H, FISCHER UDO K R. Cemented Carbide Body Used Preferably for Abrasive Rock Drilling and Mineral Cutting[P]. US patent: 5401461. 1995-3-28.
[5] AKERMAN JAN G. H, FISCHER UDO K R, HARTZELL ERIK T. Cemented Carbide Body with Extra Tough Behavior[P]. US patent: 5453241, 1995-9-26.
[6] FISCHER UDO K R, WALDENSTROM M, HARTZELL ERIK T. Cemented Carbide Body with Increased Wear Resistance[P]. US patent: 5856626. 1999-1-5.
[7] ZHANG Li, HUANG Bai-yun, WU En-xi. Research on dual phase cemented carbides[J]. Materials Review, 2000, 14 (12): 17-19.(in Chinese)
[8] YANG Jian-gao, WANG Hai-bin, LIU Yong, et al. Influence of carbon content on formation of gradient structure of cemented carbide for mining[J]. The Chinese Journal of Nonferrous Metals, 2004, 14(3): 424-428.(in Chinese)
[9] LIU Yong, WANG Hai-bin, YANG Jian-gao, et al. Formation mechanism of cobalt-gradient structure in WC-Co hard alloy[J]. Journal of Materials Science, 2004, 39: 4397-4399.
[10] LIU Yong, WANG Hai-bin, HE Yue-hui, et al. Investigation on the formation of grated structure in WC-Co hard alloy[C]// DANNINGER H, RATZI R. Euro PM2004 Conference proceedings. Vienna: European Powder Metallurgy Association, 2004: 461-466.
[11] LIU Yong, WANG Hai-bin, YANG Jian-gao, et al. Relationship between structure and properties of graded cemented carbide[J]. Materials Science and Engineering of Powder Metallurgy, 2005, 10(6): 356-360.(in Chinese)
[12] ZHANG Li, CHEN Shu, XIONG Xiang-jun, et al. Microstructure and Vickers hardness of functionally graded WC-Co cemented carbide with dual phase structure[J]. The Chinese Journal of Nonferrous Metals, 2005, 15(8): 1194-1199.(in Chinese)
[13] European Powder Metallurgy Association (EPMA). Powder Metallurgy of Hardmetals[M]. London: EPMA, 1995.
[14] JOHANSSON T, UHRENIUS B. Phase equilibria, isothermal reactions, and a thermodynamic study in the Co-W-C system at 1 150 ℃[J]. Metal Science, 1978, 12(2): 83-94.
[15] ZHANG Yuan-min. Practice Textbook for Technology of Metal[M]. Beijing: Higher Education Press, 2003.(in Chinese)
[16] FANG Z Z, GRIFFO A, WHITE B, et al. Fracture resistance super hard materials and hardmetals composite with functionally designed microstructure[J]. International Journal of Refractory Metals & Hard Materials, 2001, 19: 453-459.
[17] TORRES Y, CASELLAS D, ANGLADA M, et al. Fracture toughness evaluation of hardmetals: influence of testing procedure[J]. International Journal of Refractory Metals & Hard Materials, 2001, 19: 27-34.
Foundation item: Projects(50323008, 50574104) supported by the National Natural Science Foundation of China; Project (04JJ3084) supported by the Natural Science Foundation of Hunan Province, China
Received date: 2006-06-23; Accepted date: 2006-08-24
Corresponding author: ZHANG Li, PhD, Professor; Tel: +86-731-8876424; E-mail: zhangli@mail.csu.edu.cn
(Edited by YUAN Sai-qian)