
J. Cent. South Univ. (2021) 28: 89-99
DOI: https://doi.org/10.1007/s11771-021-4588-y

Kinetic model research on drying characteristics of artificial magnetite green pellet
ZHANG Han-quan(张汉泉)1, LIU Cheng-xin(刘承鑫)1, LU Man-man(路漫漫)2, YU Hong(余洪)1
1. Xingfa School of Mining Engineering, Wuhan Institute of Technology, Wuhan 430205, China;
2. School of Minerals Processing and Bioengineering, Central South University, Changsha 410083, China
Central South University Press and Springer-Verlag GmbH Germany, part of Springer Nature 2021
Abstract: In this study, the effects of drying temperature, hot airflow speed and diameter of green pellet on drying rate of artificial magnetite pellet were deeply investigated to clarify the drying characteristics of artificial magnetite green pellet. The results show that the drying process of artificial magnetite green pellet has three stages, accelerated drying stage, constant drying stage and decelerated drying stage. And drying temperature and hot airflow speed both have significant reciprocal effects on moisture ratio and drying rate of green pellet during the drying process. However, the diameter of green pellet has little effect on drying process of green pellet. Then the drying fitting models of Correction Henderson and Pabis, Lewis, Correction Page (III), Wang and Singh are used to describe the drying kinetics of artificial magnetite green pellet. The fitting results indicate that the drying process of artificial magnetite pellet can be described by Correction Page (III) model accurately. Finally, the contrast experiments demonstrate that the fitting model can well describe the actual drying process.
Key words: magnetic roasting; artificial magnetite; pellet; drying rate; drying kinetics
Cite this article as: ZHANG Han-quan, LIU Cheng-xin, LU Man-man, YU Hong. Kinetic model research on drying characteristics of artificial magnetite green pellet [J]. Journal of Central South University, 2021, 28(1): 89-99. DOI: https://doi.org/10.1007/s11771-021-4588-y.
1 Introduction
Iron ore pellet is a kind of high-quality burden for ironmaking using blast furnace [1, 2]. Nowadays, the pellet has gradually become the main raw materials of blast furnace with the short of high-grade natural iron ore [3-5]. With the growing scarcity of natural magnetite, the artificial magnetite concentrate has become one of the main raw materials for iron ore pellet [6]. The artificial magnetite concentrate is obtained from reduction roasting-magnetic separating process [7]. This process uses refractory iron ores with weak magnetism as raw materials. After reduction roasting-magnetic separating process, the high-grade iron concentrate obtained is used as raw materials for pellet production [8]. Compared with natural magnetite, the artificial magnetite has poorer crystallinity, and the artificial magnetite concentrate has more inclusion with incomplete crystal structure [9, 10]. In contrast to natural magnetite, the artificial magnetite has strong hydrophobicity, low electronegativity, large specific surface area and rough surface [11]. The big differences of surface hydrophilicity between artificial magnetite and natural magnetite lead that the green pellet of artificial magnetite and natural magnetite have quite different drying characteristics in drying process [12].
It is known that the drying process is very important for pellet industrial production, especially in grate-rotary kiln technology [13]. In our previous researches, it was found that the mechanical strength of artificial magnetite green pellet is much higher than that of natural magnetite green pellet. However, the high moisture content of the artificial magnetite green pellet leads to the fact that the artificial magnetite green pellet is easier to crack in drying process compared to natural magnetite green pellet [6]. So, the drying process of artificial magnetite pellet is more complicated compared to the natural magnetite pellet. The previous literatures mainly focused on the pelletizing process and the drying characteristics of natural iron ore pellet [14, 15]. The quantitative and modelling discussions on drying kinetics of artificial magnetite green pellet have seldom been published.
In this study, one typical artificial magnetite concentrate was used as the pelletizing raw material. The drying characteristics of artificial magnetite green pellet were investigated via measuring dehydration rate. In addition, four classic drying kinetics models were used to describe the drying characteristics of artificial magnetite green pellet. Finally, the moisture ratios calculated by model equation and obtained from experiments were compared to evaluate the accuracy of the model equation.
2 Materials and methods
2.1 Materials
2.1.1 Artificial magnetite concentrate
The artificial magnetite concentrate used in this work was obtained from reduction roasting- magnetic separation technology. The major chemical composition of artificial magnetite concentrate is listed in Table 1. It shows that the iron grade of the artificial magnetite concentrate is as high as 61.32 wt%. The physical properties of artificial magnetite showed in Table 2 indicate that more than 88% of the concentrate has a particle size less than 75 μm. The specific surface area is measured as 3155 cm2/g using Blaine method (National Standard GB/T 8074-2008). The balling index shows that this iron ore concentrate has an excellent ballability.
2.1.2 Pellet binder
Bentonite is a traditional binder utilized for pelletizing production due to its high water holding capacity, high binding strength, and low cost [16]. Chemical composition and physical properties of bentonite used in this study are listed in Tables 3 and 4. Its high methylene blue absorption capacity and swelling value indicate that this bentonite was suitable for pelletizing.
2.2 Methods
2.2.1 Pelletizing
The green pellet was prepared in φ800 mm disk-balling machine with the side height of 130 mm. In batch experiment, about 4 kg of artificial magnetite concentrate was mixed with 2.0 wt% bentonite binder. The total pelletizing time was 18 min including 2 min for initial nucleation, 12 min for growing and 4 min for compacting. During pelletizing, the moisture ratio of each batch was controlled manually at 17.0%±0.5%.
Table 1 Chemical composition of artificial magnetite concentrate (wt%)

Table 2 Physical properties of magnetite concentrate

Table 3 Chemical analysis of bentonite/(wt%)

Table 4 Physical properties of bentonite

2.2.2 Drying process
Drying tests were conducted in a non-standard equipment which was designed and assembled by our group, as shown in Figure 1. The equipment includes air blower, dryer, rotameter, shaft furnace, heat transfer medium, sample stage, thermocouple and thermobalance. The air passes through the quicklime desiccant to ensure that the air does not contain moisture, then enters the shaft furnace and is heated by the heat transfer medium. The hot air is used to dry the green pellet, and the thermocouple is used to measure the temperature of hot air. The weight changes of green pellet on the sample stage during drying process are measured by thermobalance. In drying process, the drying moisture ratio (MR) and the drying rate (DR) were calculated by measuring the change of weight of green pellet using thermobalance. The relationships between MR, DR and time (t) were shown in M-t and DR-t curves. The effects of drying temperature, hot airflow speed and diameter of the green pellet were described by MR-t and DR-t curves. The moisture content, drying moisture ratio and drying rate of green pellet were calculated according to the following equation:
(1)
where M is the moisture ratio of the pellet, %; m and m∞ are the moisture weight and dry weight of pellet, g, respectively. So, at any time t, the moisture ratio of the pellet can be expressed as:
(2)
where Mt is the moisture content of the pellet at time t, %; mt is the dry weight of pellet at time t, g.
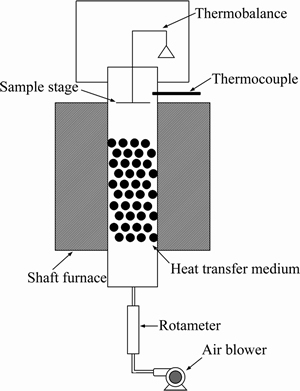
Figure 1 Schematic of equipment for drying test
When the drying time is t, the drying moisture ratio can be expressed as:
(3)
where MR is the moisture ratio; Mo and Me are the moisture ratio of the pellet at initial state and equilibrium state of drying, respectively.
When drying process reaches equilibrium, Me almost approaches zero. Equation (3) can be simplified to Eq. (4):
(4)
The drying rate of pellet in the drying process can be defined as:
(5)
where DR is the drying rate; Mt1 and Mt2 are the moisture ratio of the pellet at t1 and at t2 in drying process, (g·(g·min)-1), respectively.
3 Results and discussion
3.1 Drying characteristics of green pellet
3.1.1 Effect of drying temperature
For green pellet drying, the temperature of hot air flow is the most important factor. If the temperature is too high, the moisture in green pellet evaporates quickly, and the inner vapor pressure will make pellet burst. On the other hand, if the temperature is too low, the moisture in green pellet can’t be evaporated timely, thus reducing production efficiency and deteriorating the oxidation process subsequently. In this research, five temperature conditions of hot air flow were adopted to investigate the effects of drying temperature on drying process of artificial magnetite green pellet. The hot air flow speed and pellet diameter were controlled at 1.1884 m/s and 12.5 mm, respectively. The M-t and D-t curves at various drying temperatures are shown in Figure 2.
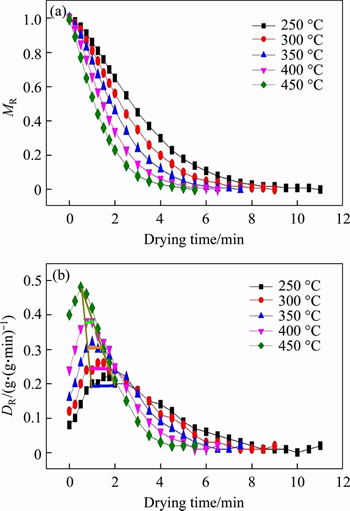
Figure 2 MR-t (a) and DR-t (b) curves of green pellet drying at different drying temperatures
The MR-t and DR-t curves displayed in Figure 2 illustrate that there are three stages in the green pellet drying process, i.e., accelerated drying stage, constant drying stage and decelerated drying stage. The MR of green pellet drying declined rapidly in the first 1 min. Then, the water evaporation rate of green pellet kept a constant in the next 1 min. After 2 min, the MR of green pellet drying declined slowly until it no longer changed.
As shown in Figure 2(a), as the drying temperature increased from 250 to 450 °C, the total drying time reduced sharply from 11 to 5.5 min. This was because the higher temperature exacerbated the evaporation of water, so that the drying rate increases significantly. It was found from Figure 2(b) that, the accelerated drying stage time of green pellet at different drying temperatures was all about 1 min and the increasing temperature had very little effect on reducing the accelerated drying stage time. On the contrary, the higher temperature was helpful for shorting constant drying stage and decelerated stage time of green pellet.
The main reasons of this phenomenon were that in accelerated drying stage, temperature of the surface of green pellet started to increase, causing the evaporation of water on the surface of green pellet. This process was controlled by water evaporation rate. The setting temperatures in the experiments were far beyond the boiling point of water, and increasing the temperature had little effect on the evaporation rate of water. Thus, increasing temperature had little help for shorting the accelerated drying stage time. In constant drying stage and decelerated stage, the water in the surface layer of green pellet had been evaporated completely. The moisture inside the green pellet began to migrate to the outside and evaporate off the surface layer of green pellet. In this process, the drying rate depended on the moisture migrating rate. The high drying temperature could increase the temperature inside the green pellet, thus promoting the outward migration of moisture. So, the higher drying temperature could shorten the constant drying stage and decelerate stage time.
3.1.2 Effect of hot airflow speed
The hot airflow speed is also an important factor for green pellet drying. Too high hot airflow speed can’t increase the drying rate. On the contrary, it will increase the energy consumption and cause the dust pollution. In this experiment, the drying temperature and pellet diameter are controlled at 350 °C and 12.5 mm, respectively. The MR-t and DR-t curves at various hot airflow speed are depicted in Figure 3.
The results exhibited in Figure 3 demonstrated that increasing hot airflow speed could significantly reduce drying time, but its positive help for declining the drying time is weaker than raising the drying temperature. As the hot airflow speed increased from 0.7356 to 2.0938 m/s, the total drying time reduced only from 8.5 to 6 min. On the other hand, increasing hot airflow speed could extend the accelerated drying stage time. This was because the higher airflow speed could decline the vapor pressure on the surface of green pellet, thus accelerating the drying process. It was shown that the time of drying rate to reach a stable value was extended with the increasing hot airflow speed in accelerated drying stage, but the end of the stable value was not extend. Under the condition of high hot airflow speed, the vapor pressure on the surface of green pellet was very low. So, the water vapor on the surface of green pellet diffused fast to air, thus increasing the initial drying rate.
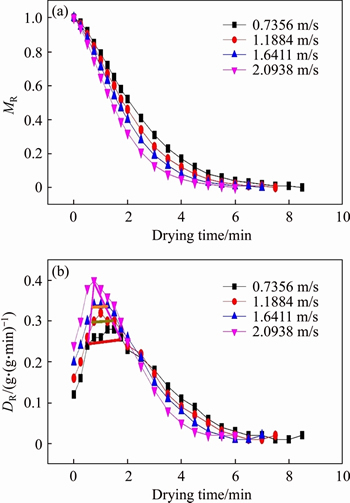
Figure 3 MR-t (a) and DR-t (b) curves of green pellet drying at different hot airflow speeds
3.1.3 Effects of green pellet diameter
The results of the above investigation indicated that in constant drying stage and decelerated stage, the drying rate depended on the moisture migrating rate. So, the diameter of green pellet was also an influencing factor of drying process, especially in constant drying stage and decelerated stage. In this experiment, drying temperature and hot airflow speed were controlled at 350 °C and 1.1884 m/s, respectively. The results of effect of green pellet diameter are displayed in Figure 4.
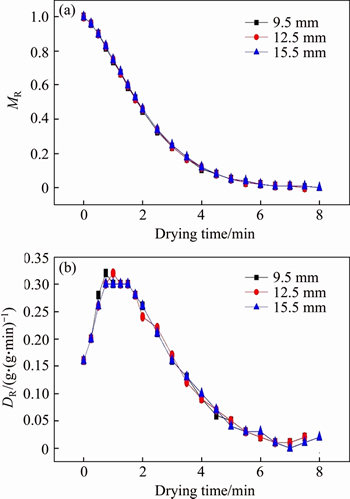
Figure 4 MR-t (a) and DR-t (b) curves of green pellet drying at different green pellet diameters
It was seen from Figure 4 that the total drying time declined from 8 to 6.5 min with the decreasing of green pellet diameter because the reduction of green pellet diameter helped the water inside of the green pellet to migrate to the outside quickly. However, the changes of green pellet diameter had no effect on the drying speed. This result manifested that the drying temperature and hot airflow speed were the crucial factors for drying process of green pellet.
3.2 Drying kinetics
Today, modelling has been widely used in drying investigation fields [17-20]. The kinetic characteristics of green pellet during drying were investigated by ascertaining the parameters of these model equations using fitting methods. In this study, four models, Correction Henderson and Pabis [21], Lewis [22], Correction Page (III) [23], and Wang and Singh, [24] were adopted to describe the drying characteristics of artificial magnetite green pellet. The drying model investigation adopted orthogonal test method.
method was used in orthogonal tests. The equations of models adopted are listed in Table 5. The conditions of drying temperature, hot airflow speed and green pellet diameter and the fitting results of different drying models are showed in Table 6.
It was seen that from Table 6, Correction Page (III) could describe the drying process of artificial magnetite green pellet accurately compared to the other three drying models. The data obtained under different conditions was inserted into Correction Page (III) model. The parameters calculated by Correction Page (III) model were shown in Table 7.
The results shown in Tables 6 and 7 manifested that the Correction Page (III) model could well explain the drying process of artificial magnetite green pellet, thus it was an ideal drying kinetic model for artificial magnetite green pellet.
The effects of drying temperature, hot airflow speed and pellet diameter on the parameter of Correction Page (III) model were investigated, and the results are showed in Figures 5-7.
As shown in Figure 5, the parameter a was mainly influenced by drying temperature. The hot airflow speed and green pellet diameter could hardly affect it. Software SPSS 22.0 was used to fit the parameter a, and the result was presented as follows:
a=0.9997+2.0105×10-11T3+9.9810×10-27T9
R2=0.996 (6)
The results displayed in Figure 6 illustrate that the parameter k was mainly affected by drying temperature, and secondly by the hot airflow speed. The green pellet diameter had almost no effect on it. The fitting result was also fitted using Software SPSS22.0 as follows:
Table 5 Equations of drying models for artificial magnetite green pellet

Table 6 Analysis results of various drying models for artificial magnetite green pellet
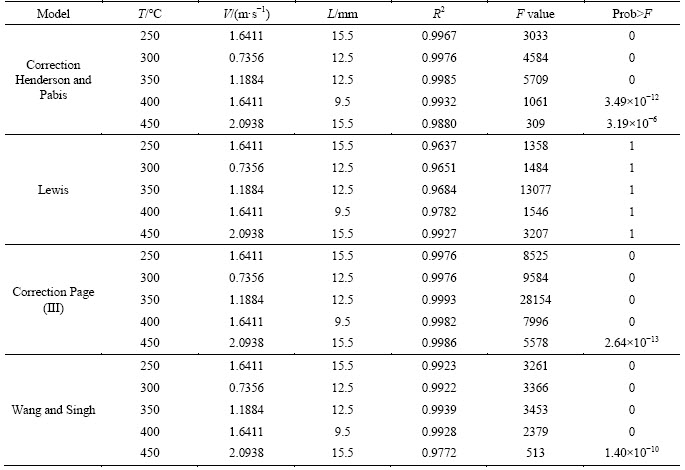
Table 7 Parameter values of different effect factors
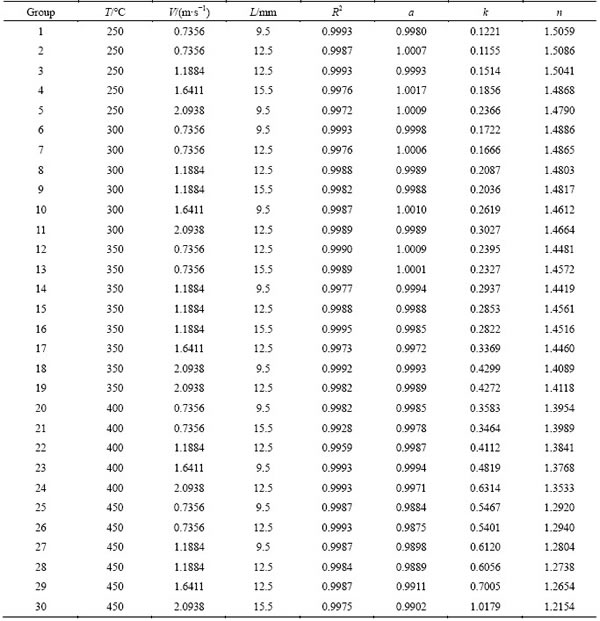
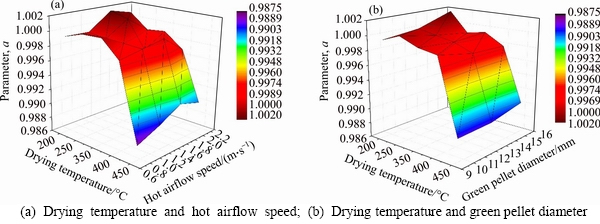
Figure 5 Effect of different factors on parameter a:
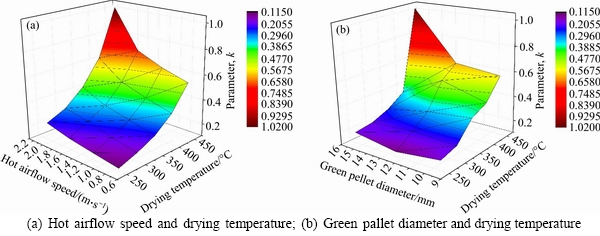
Figure 6 Effect of different factors on parameter k:
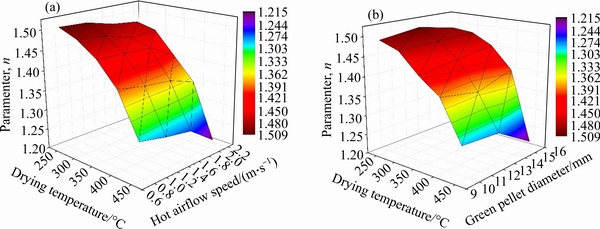
Figure 7 Effect of different factors on parameter n: Drying temperature and hot airflow speed; (b) Drying temperature and green pallet diameter
k=0.021+3.0105×10-9T3+2.0010×10-25T9+
3.3222×10-4TV-1.7475×10-13T4V4+
6.1720×10-22T7V7+3.5318×10-4V3+
4.4055×10-6V9-8.0117×10-6L3+
2.0013×10-13L9, R2=0.997 (7)
Similarly, the parameter n was also mainly influenced by drying temperature and hot airflow speed. The diameter had no effect on it. The result fitted by Software SPSS22.0 is as follows:
n=1.53+1.1008×10-9T3+1.601×10-25T9+
7.0686×10-5TV-7.4895×10-14T4V4+
1.4989×10-22T7V7+1.7659×10-4V3+
3.0838×10-6V9-3.0012×10-6L3+
2.0001×10-14L9, R2=0.992 (8)
So, the drying kinetic equation could be expressed as:
MR=(0.9997+2.0105×10-11T3+9.9810×
10-27T9)·exp(-(0.021+3.0105×10-9T3+
2.0010×10-25T9+3.3222×10-4TV-1.7475×
10-13T4V4+6.1720×10-22T7V7+3.5318×10-4V3+
4.4055×10-6V9-8.0117×10-6L3+2.0013×
10-13L9)t^(1.53+1.1008×10-9T3+1.601×
10-25T9+7.0686×10-5TV-7.4895×10-14T4V4+
1.4989×10-22T7V7+1.7659×10-4V3+
3.0838×10-6V9-3.0012×10-6L3+
2.0001×10-14L9)) (9)
where MR is the moisture rate; t is the drying time; T is the drying temperature; V is the hot airflow speed; L is the green pellet diameter.
3.3 Model verification
In order to evaluate the accuracy of the model equation, the actual drying verification tests were conducted. The test conditions and results are listed in Table 8 and Figure 8, respectively.
The results exhibited in Figure 8 indicate that the accuracy of the fitting model equation was very high for describing the drying process of artificial magnetite green pellet. What’s more, Figure 8 also illustrated that the higher the drying temperature is, the closer the calculated value is to the experimental value. It was suggested that the drying kinetic model was more accurate under high drying temperature.
Table 8 Conditions of three additional test
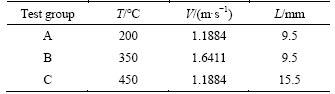

Figure 8 Comparison of calculated and experimental MR-t curve
4 Conclusions
1) The drying process of artificial magnetite green pellet consisted of three stages, accelerated drying stage, constant drying stage and decelerated drying stage. The drying temperature and hot airflow speed had significant effects on the moisture ratio and drying rate of green pellet. However, the green pellet diameter could scarcely affect it. The optimal drying conditions were 450 °C of hot airflow temperature and 2 m/s of hot airflow speed. The diameter of green pellet could hardly affect the drying process.
2) In the accelerated drying stage, the control part was evaporation rate of water on the surface of green pellet. On the other hand, in the constant drying stage and decelerated drying stage, the control part was moisture migrating rate. In these two stages, increasing drying temperature had more effects on drying process than increasing the hot airflow speed. Based on the above results, it was recommended to adopt the drying system which has high hot airflow speed in the preliminary stage and high drying temperature in the middle and later stage.
3) The drying test results were fitted by four kinetic models. The fitting relative coefficient (R2) showed that the drying process of artificial magnetite green pellet conformed to the Correction Page (III) model. The subsequent verification tests indicated that the fitting equation based on Correction Page (III) model could describe the drying process well. The drying kinetic equation could be written as:
MR=a·exp(-ktn)
where
a=0.9997+2.0105×10-11T3+9.9810×10-27T9;
k=0.021+3.0105×10-9T3+2.0010×10-25T9+
3.3222×10-4TV-1.7475×10-13T4V4+
6.1720×10-22T7V7+3.5318×10-4V3+4.4055×
10-6V9-8.0117×10-6L3+2.0013×10-13L9;
n=1.53+1.1008×10-9T3+1.601×10-25T9+7.0686×
10-5TV-7.4895×10-14T4V4+1.4989×10-22T7V7+
1.7659×10-4V3+3.0838×10-6V9-3.0012×
10-6L3+2.0001×10-14L9.
Contributors
The overarching research goals were developed by ZHANG Han-quan, LIU Cheng-xin, and LU Man-man. ZHANG Han-quan contributed to the conception of the study. LIU Cheng-xin and LU Man-man designed and performed the experiments. LIU Cheng-xin and YU Hong performed the data analysis and wrote the manuscript. All authors replied to reviewers’comments and revised the final version.
Conflict of interest
ZHANG Han-quan, LIU Cheng-xin, LU Man-man and YU Hong declare that they have no conflict of interest.
References
[1] ZHOU You-lian, KAWATRA S K. Pelletization using humic substance-based binder [J]. Mineral Processing and Extractive Metallurgy Review, 2017, 38(2): 83-91. DOI: 10.1080/08827508.2016.1262859.
[2] PAL J, GHORAI S, NANDI B, CHAKRABORTY T, DAS G, VENUGOPALAN T. Effect of pyroxenite and olivine minerals as source of MgO in hematite pellet on improvement of metallurgical properties [J]. Journal of Central South University, 2015, 22(9): 3302-3310. DOI: 10.1007/s11771-015-2870-6.
[3] COPELAND C R, CLAREMBOUX V, KAWATRA S K. A comparison of pellet quality from straight-grate and grate-kiln furnaces [J]. Mineral Processing and Extractive Metallurgy Review, 2018, 40(3): 218-223. DOI: 10.1080/08827508.2018.1536050.
[4] LONG Hong-ming, WANG Hong-tao, DI Zhan-xia, CHUN Tie-jun, LIU Zheng-gen. Influences of hydrogen-enriched atmosphere under coke oven gas injection on reduction swelling behaviors of oxidized pellet [J]. Journal of Central South University, 2016, 23(8): 1890-1898. DOI: 10.1007/ s11771-016-3244-4.
[5] de MORAES S L, RIBEIRO T R. Brazilian iron ore and production of pellet [J]. Mineral Processing and Extractive Metallurgy Review, 2019, 40(1): 16-23. DOI: 10.1080/ 08827508.2018.1481056.
[6] ZHANG Han-quan, LU Man-man, FU Jin-tao. Oxidation and roasting characteristics of artificial magnetite pellet [J]. Journal of Central South University, 2016, 23(11): 2999-3005. DOI: 10.1007/s11771-016-3363-y.
[7] LUO Li-qun, HUANG Hong, YU Yong-fu. Characterization and technology of fast reducing roasting for fine iron materials [J]. Journal of Central South University, 2012, 19(8): 2272-2278. DOI: 10.1007/s11771-012-1271-3.
[8] ZHANG Yuan-bo, DU Ming-hui, LIU Bing-bing, SU Zi-jian, LI Guang-hui, JIANG Tao. Separation and recovery of iron and manganese from high-iron manganese oxide ores by reduction roasting and magnetic separation technique [J]. Separation Science and Technology, 2017, 52(7): 1321-1332. DOI: 10.1080/01496395.2017.1284864.
[9] JANG K O, NUNNA R M, HAPUGODA S, NGUYEN A V, BRUCKARD W J. Chemical and mineral transformation of a low grade goethite ore by dehydroxylation, reduction roasting and magnetic separation [J]. Minerals Engineering, 2014, 60: 14-22. DOI: 10.1016/j.mineng.2014.01.021.
[10] GUO Hong-wei, BAI Jun-li, ZHANG Jian-liang, LI Hong-ge. Mechanism of strength improvement of magnetite pellet by adding boron-bearing iron concentrate [J]. Journal of Iron and Steel Research, International, 2014, 21: 9-15. DOI: 10.1016/S1006-706X(14)60002-9.
[11] LUO Li-qun, ZHANG Han-quan. Process mineralogy and characteristic associations of iron and phosphorous-based minerals on oolitic hematite [J]. Journal of Central South University, 2017, 24(9): 1959-1967. DOI: 10.1007/s11771- 017-3604-8.
[12] YANG Cong-cong, ZHU De-qing, PAN jian, ZHOU Bin-zhi, XUN Hu. Oxidation and induration characteristics of pellet made from western Australian ultrafine magnetite concentrates and its utilization strategy [J]. Journal of Iron and Steel Research, International, 2016, 23: 924-932. DOI: 10.1016/S1006-706X(16)30140-6.
[13] HALT J A, KAWATRA S K. Iron ore pellet dustiness part II: Effects of firing route and abrasion resistance on fines and dust generation [J]. Mineral Processing and Extractive Metallurgy Review, 2015, 36(5): 340-347. DOI: 10.1080/ 08827508.2014.978317.
[14] RAJSHEKAR Y, PAL J, VENUGOPALAN T. Mill scale as a potential additive to improve the quality of hematite ore pellet [J]. Mineral Processing and Extractive Metallurgy Review, 2018, 39(3): 202-210. DOI: 10.1080/08827508. 2017.1415205.
[15] FAN Xiao-hui, YANG Gui-ming, CHEN Xu-ling, HE Xiang-ning, HUANG Xiao-xian, GUO Lu. Effect of carboxymethyl cellulose on the drying dynamics and thermal cracking performance of iron ore green pellets [J]. Powder Technology, 2014, 267: 11-17. DOI: 10.1016/j.powtec.2014. 07.011.
[16] ZHANG Yuan-bo, LU Man-man, ZHOU You-lian, SU Zi-jian, LIU Bing-bing, LI Guang-hui, JIANG Tao. Interfacial interaction between humic acid and vanadium, titanium-bearing magnetite (VTM) particles [J]. Mineral Processing and Extractive Metallurgy Review, 2020, 41(2): 75-84. DOI: 10.1080/08827508.2018.1538986.
[17] RAMACHANDRAN R P, BOURASSA J, PALIWAL J, CENKOWSKI S. Effect of temperature and velocity of superheated steam on initial condensation of distillers’ spent grain pellets during drying [J]. Drying Technology, 2017, 35(2): 182-192. DOI: 10.1080/07373937.2016.1166123.
[18] ATHAYDE M, COTA M, COVCEVICH M. Iron ore pellet drying assisted by microwave: A kinetic evaluation [J]. Mineral Processing and Extractive Metallurgy Review, 2018, 39(4): 266-275. DOI: 10.1080/08827508.2017.1423295.
[19] LJUNG A L, LUNDSTROM T S, MARJAVAARA B D, TANO K. Influence of air humidity on drying of individual iron ore pellets [J]. Drying Technology, 2011, 29(9): 1101- 1111. DOI: 10.1080/07373937.2011.571355.
[20] LJUNG A L, FRISHFELDS V, LUNDSTROM T S, MARJAVAARA B D. Discrete and continuous modeling of heat and mass transport in drying of a bed of iron ore pellets [J]. Drying Technology, 2012, 30(7): 760-773. DOI: 10.1080/07373937.2012.662 567.
[21] ERGUN K, CALISKAN G, DIRIM S N. Determination of the drying and rehydration kinetics of freeze dried kiwi (Actinidia deliciosa) slices [J]. Heat and Mass Transfer, 2016, 52(12): 2697-2705. DOI: 10.1007/s00231-016-1773-x.
[22] LEWIS W K. The rate of drying of solid materials [J]. The Journal of Industrial and Engineering Chemistry, 1921, 5: 427-432. https://pubs.acs.org/doi/pdf/10.1021/ie50137a021?casa_token=BQq4thzr7o8AAAAA:0k1QfVlo_xP5t1J0um2xPk7zItY-wc3C-5pjfYPkRFaD4lEZ754Wqn7alV4ATJOfc1Xuerezxql1it-6.
[23] DANISH M, JING H, PIN Z, ZIYANG L, PANSHENG Q. A new drying kinetic model for sewage sludge drying in presence of CaO and NaClO [J]. Applied Thermal Engineering, 2016, 106: 141-152. DOI: 10.1016/ j.applthermaleng.2016.05.191.
[24] BABALIS S J, PAPANICOLAOU E, KYRIAKIS N, BELESSIOTIS V G. Evaluation of thin-layer drying models for describing drying kinetics of FIGS (Ficus carica) [J]. Journal of Food Engineering, 2006, 75(2): 205-214. DOI: 10.1016/j.jfoodeng.2005.04.008.
(Edited by ZHENG Yu-tong)
中文导读
人工磁铁精矿生球干燥的动力学模型
摘要:本文研究了干燥温度、热风流速以及生球直径对人工磁铁精矿生球干燥速度的影响,明确了人工磁铁精矿生球的干燥特性。结果表明,生球的干燥过程存在三个阶段,即加速干燥段、恒定干燥段和减速干燥段。在干燥过程中,干燥温度和热风流速对生球含水率和干燥速率变化有显著影响,而生球直径对生球干燥过程影响不大。随后,采用修正Henderson、Pabis、Lewis、修正Page(III)、Wang和Singh的干燥拟合模型来描述人工磁铁矿生球的干燥动力学。模型拟合结果表明,人工磁铁精矿生球的干燥过程符合Page(III)模型。最后,将实际实验数据与模型拟合数据进行对比,结果表明该拟合模型方程可以较好地描述实际生球干燥过程。
关键词:磁化焙烧;人工磁铁矿;球团;干燥速率;干燥动力学
Foundation item: Projects(51974204, 51474161) supported by the National Natural Science Foundation of China
Received date: 2019-09-19; Accepted date: 2020-08-09
Corresponding author: LU Man-man, PhD Candidate; Tel: +87-27-87193799; E-mail: lmmcsu@163.com; ORCID: https://orcid.org/ 0000-0001-8888-2893