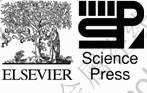
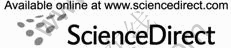
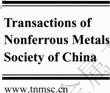
Trans. Nonferrous Met. Soc. China 22(2012) 1133-1139
Effect of composition and structure on specific resistivity of SiC fibers
WANG De-yin, SONG Yong-cai, LI Yong-qiang
State Key Laboratory of Novel Ceramic Fibers and Composites, National University of Defense Technology,
Changsha 410073, China
Received 13 May 2011; accepted 5 March 2012
Abstract: Four kinds of SiC fibers with different specific resistivities were prepared by the pyrolysis of cured polycarbosilane fiber. The results show that SiC fibers with different specific resistivities can be obtained by changing the curing and pyrolysis conditions. And the free carbon content and the ability to crystallize no longer affect the specific resistivities notably with the time when the fiber is covered with an excess carbon layer, and the fiber has a low specific resistivity. The excess carbon layer in the circular outer part is originated from the re-pyrolysis and deposition of hydrocarbon volatiles. The removal of the carbon by oxidative treatment may affect the surface property and also promote the magnitude of specific resistivity. The influence of the surface property on the specific resistivity can be considerable and should not be neglected.
Key words: silicon carbide fiber; excess carbon layer; specific resistivity
1 Introduction
Polymer-derived SiC fiber is highly valued because of its excellent heat-resistance, and used as reinforcement for PMC, MMC and CMC [1-4]. Not only is the heat-resistance attracting much attention, but the electrical properties of the fibers are also of great interest. SiC fibers are n-type semiconductors with a resistivity between 10-1 and 107 Ω·cm [5]. For example, the resistivities of NL-400 (HVR) and NL-500 (HVR) fibers commercialized by the Nippon Carbon company are 106-107 and 0.5-5.0 Ω·cm, respectively. The former- reinforced PMC can be used as structural materials for radar domes and aircrafts based on its excellent microwave permeability, and the latter can be used in the development of structural materials for microwave absorbers based on its excellent microwave absorption [6].
The electrical behavior of SiC fibers is closely dependent on their chemical and structural properties [7,8]. Generally, the magnitude of the specific resistivity is controlled by free carbon content and β-SiC crystals present in the fibers. In the present work, the specific resistivities of four fibers prepared from the pyrolysis of organosilicon precursors were studied in correlation with their chemical and structural properties, and found that the surface structure affects the specific resistivity notably.
2 Experimental
Continuous polycarbosilane green fibers were cured with atmospheric oxygen. Pyrolysis of the cured PCS fiber in flowing nitrogen gas was conducted continuously in a tube furnace at the temperature of 1300-1400 ℃ [9], and the ultimate product was named as SiC-1 fiber. The PCS fibers were cured with atmospheric oxygen, cyclohexene and γ-ray irradiation [10,11], respectively. Then the cured fibers were heated to 1300-1400 ℃ in flowing nitrogen at a rate of about 100 ℃/h, and the ultimate products were named as SiC-2, SiC-3 and SiC-4 fibers, respectively.
The bulk composition of fibers was determined by chemical analysis. Solid-state nuclear magnetic resonance (29Si NMR) of the SiC fibers was obtained on a Bruker AV300 spectrometer using stander Bruker double-resonance magic-angle sample spinning (MAS) probes. Using the two-terminal method to determine the electrical resistivity, both ends of a monofilament were attached with electro conductive resin to the electrode plates which were 25 mm (L) apart in distance, the specific resistivity was derived by: ρv=RS/L=Rπd2/(4L)= 10-9Rπd2, where R, S and d represent resistivity, cross-sectional area and diameter of SiC fibers, the value of resistivities was the average of about 20 measurements. The crystallinity of the SiC fibers was detected via X-ray diffraction, using diffractometer with Cu Kα radiation; Microstructural analysis was carried out using high-resolution transmission electron microscopy (HRTEM). Depth profiles of SiC fibers were measured by Auger electron spectroscope (AES) with a PHI-610/SAM analyzer.
3 Results and discussion
3.1 Composition
The composition and specific resistivities of the four SiC fibers are listed in Table 1.
Table 1 Chemical composition of four SiC fibers
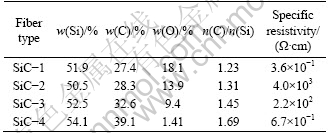
The specific resistivities of the four fibers are 3.6×10-1, 4.0×103, 2.2×102 and 6.7×10-1 Ω·cm, the mole ratios of C to Si of the four fibers are 1.23, 1.31, 1.45 and1.69, respectively. Generally, the magnitude of the specific resistivity is mainly controlled by free carbon phase present in the fibers; the more the free carbon content is, the higher the specific resistivity is [7]. The free carbon content cannot be demonstrated by the total carbon content and the mole ratio of C to Si for the silicon and the carbon have several kinds of tetrahedral environment besides SiC4 structure. Solid 29Si NMR can describe the tetrahedral environment of silicon atoms and evaluate the ratio between each entity. 29Si NMR spectra of the four fibers are shown in Fig. 1.
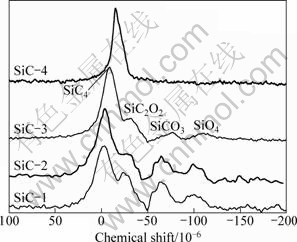
Fig. 1 29Si MAS NMR spectra of four SiC fibers
Four types of silicon environments are detected in the fibers with resonances centered around -15×10-6, -30×10-6, -72×10-6 and -107×10-6 which can be assigned to the presence of SiC4, SiO2C2, SiCO3 and SiO4 entities [12], respectively. The relative ratios of each entity are shown in Table 2.
Table 2 Area ratio of each entity for SiC fibers
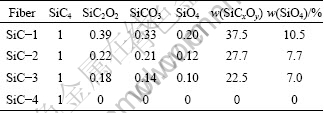
As shown in Table 2, the content of ternary amorphous silicon oxycarbide (SiCxOy) structure involved with SiC2O2 and SiCO3 in the SiC-1 fiber is 37.5% (mole fraction), higher than that of the SiC-2, SiC-3 or SiC-4 fiber which are 27.7%, 22.5% and 0. The same result can also be found in the fibers with the SiO4 structure, the content of SiO4 structure in SiC-1 fiber is 10.5%, higher than the SiC-2, SiC-3 or SiC-4 fiber which are 7.7%, 7.0% and 0, respectively.
The SiCxOy structure can be described by Si sites bonding with x carbon neighbors and y-oxygen neighbors, and corresponds to the chemical formula of SiCx/4Oy/2 when one carbon can bond with four Si atoms and one oxygen can bond with two Si atoms. The chemical formulas of the tetrahedral structures such as SiC4, SiC2O2, SiCO3 and SiO4 are SiC, SiC1/2O, Si1/4O3/2 and SiO2, respectively. The structure of the three SiC fibers can be described by (SiC)a/(SiC1/2O)b/(SiC1/4O3/2)c/ (SiO2)d/Cf, and can be integrated into SiCxOy/Cf concisely. The free carbon content can be figured out by the 29Si NMR spectra and the chemical analysis results.
Table 3 Free carbon content data of four SiC fibers
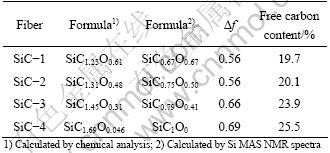
The difference of mole ratio of O to Si calculated by the 29Si NMR spectra and the chemical analysis results is acceptable and can be ignored. The 29Si NMR results subtracted from the chemical analysis results give the free carbon content. The free carbon contents of the four fibers are 19.7%, 20.1%, 23.9% and 25.5%, respectively.
As mentioned above, the magnitude of the specific resistivity is mainly controlled by the free carbon phase, and this can explain that the SiC-4 fiber which has a higher free carbon content possesses a low specific resistivity. The SiC-1 fiber and SiC-2 fiber exhibit nearly the same free carbon content, but the electrical resistivity of the SiC-1 fiber is 3.6×10-1 Ω·cm, nearly 3 or 4 orders of magnitude lower than that of the SiC-2 fiber or SiC-3 fiber which are 4.0×103 Ω·cm and 2.2×102 Ω·cm, respectively. This result indicates that the low electrical resistivity of the SiC-1 fiber is not originated from the free carbon content.
3.2 Crystallization
The XRD patterns of the fibers are shown in Fig. 2. The three intense peaks of the SiC-2 fiber, SiC-3 fiber and the SiC-4 fiber are at 2θ≈36.5°, 60° and 72°, which correspond to the diffraction lines from (111), (220) and (311) lattice planes of β-SiC crystals, respectively. Conversely, the SiC-1 fiber exhibits no tendency towards crystallinity, and only one peak indexed as the (111) reflection is observed.
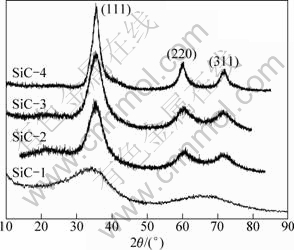
Fig. 2 XRD patterns of four SiC fibers
The inability to crystallize in SiC-1 fiber is ascribed to the presence of excess oxygen. In Si-C ceramic systems prepared by precursor route, the presence of hetero-atoms such as oxygen and nitrogen in the bulk Si-C matrix will depress and retard the progress of β-SiC crystallization [13,14]. It is unsurprisingly that the SiC-1 fiber with high oxygen content will keep being amorphous at 1300-1400 ℃. By contrast, The SiC-2, SiC-3 and SiC-4 fibers with a notable reduction in oxygen content show intense diffraction peaks of β-SiC crystal.
TEM images are in good agreement with the XRD results. The bright-field image (Fig. 3(a)) shows a very smooth microstructure and indicates that there is no polycrystalline microstructure in the SiC-1 fiber. Whereas, β-SiC crystal stacks can be found in Figs. 3(b)-(d), suggesting that β-SiC crystals do exist in the SiC-2, SiC-3 and SiC-4 fibers.
The specific resistivity of the pure β-SiC is 7×10-3 ?·cm [5]. Generally, the magnitude of specific resistivity of SiC fibers will decrease with the evolution of β-SiC crystals. The SiC-1 fiber which shows no tendency towards crystallinity should exhibit a higher electrical resistivity than the SiC-2 or SiC-3 fiber, but the result is quite different, indicating that the low specific resistivity of the SiC-1 fiber did not come from the crystallization.
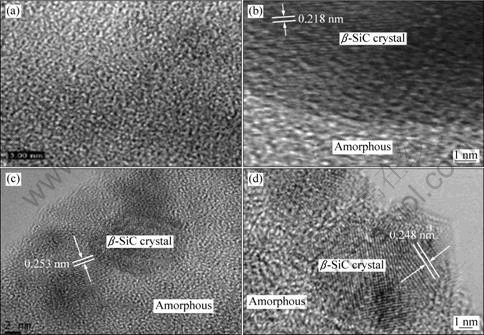
Fig. 3 HRTEM images of SiC fibers: (a) SiC-1; (b) SiC-2; (c) SiC-3; (d) SiC-4
3.3 Surface structure
The free carbon content and the ability to crystallize are not the chief factors in determining the reasons of great difference in electrical resistivity among the three fibers. Still, another concern arises in the surface structure. In order to investigate the surface property, AES was adopted and the depth profile results of the fibers are shown in Fig. 4.
According to the results of AES analysis, it is evident that a carbon-rich layer with a thickness about 50 nm exists in the circular outer part of the SiC-1 fiber. In this area, carbon content is more than 97% (mole fraction), and only carbon signal can be found in the survey scan result. Surface properties of SiC-2, SiC-3 and SiC-4 fibers are quite different. In the survey scan result, C, O and Si signals can be found simultaneously.
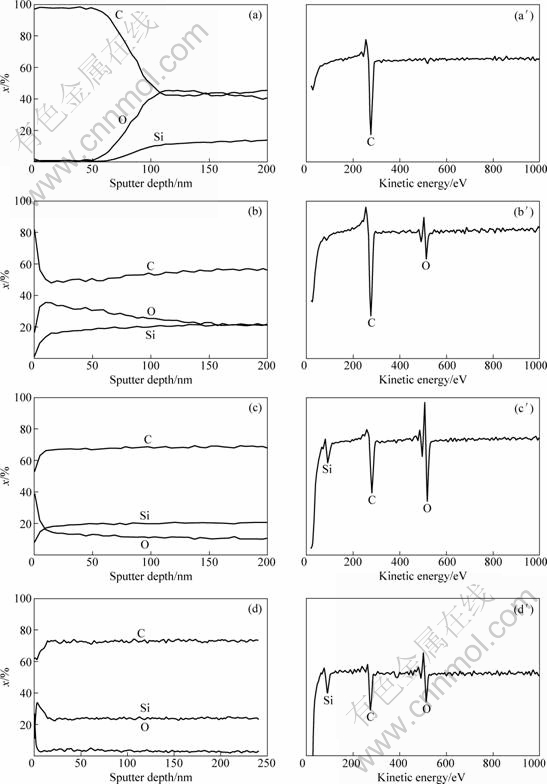
Fig. 4 AES depth profiles (a, b, c, d) and survey scans (a′, b′, c′, d′) of SiC fibers: (a), (a′) SiC-1; (b), (b′) SiC-2; (c), (c′) SiC-3; (d), (d′) SiC-4
Because of the low electrical resistivity of carbon which is about 10-6 Ω·cm, the SiC-1 fiber covered with the excess carbon layer has a very low electrical resistivity. The mass fraction of carbon layer can be evaluated by a simple model consisting of an exterior carbon sleeve and an interior column:
mc/mf=Vcρc/Vfρf≈πDdρc/[π(D/2)2ρf]=4dρc/(Dρf) (1)
where d and D represent the thickness of the excess carbon layer and the fiber diameter; ρc and ρf denote the densities of carbon and the bulk SiC fiber; the values of the four factors are 50 nm, 14 μm, 2.0 g/cm3 and 2.4 g/cm3, respectively. The mass fraction of the carbon layer calculated by equation above is only about 1.2%, but its influence on the specific resistance is considerable and should not be neglected.
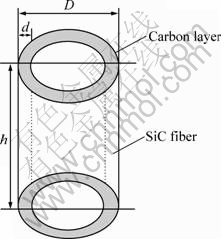
Fig. 5 Model of SiC-1 fiber with excess carbon layer in circular outer part
It is worth to note that the electric behavior is evidently controlled by the free carbon content and the SiC grain size, but the two factors will no longer affect the specific resistivity notably with the time when the fiber is covered with a carbon-rich superficial layer like that observed on the SiC-1 fiber.
A very easy way to confirm the importance of surface property is to burn the excess carbon layer in the open air, and measure the resistivity again. The bearable temperatures of normal carbon structure and SiCxOy in oxidative atmosphere are 400 ℃ and 700 ℃ [15,16], respectively. Therefore, to expose the SiC-1 fiber to the open air at 500-600 ℃ would be effective to remove the carbon layer. AES depth profiles and specific resistivity of the SiC-1 fiber after thermal exposure at 600 ℃ are shown in Figs. 6 and 7, respectively.
Removal of the carbon by oxidative treatment affects the surface property and also promotes the magnitude of specific resistivity. After thermal exposure to the open air, the content of C falls from 97% to 38% (mole fraction). Besides the C signal, O and Si signals can also be detected in the survey scan resulting from the content of 54% and 8% (mole fraction). The specific resistivity ranges from 3.6×10-1 ?·cm to 2.5×104 ?·cm.
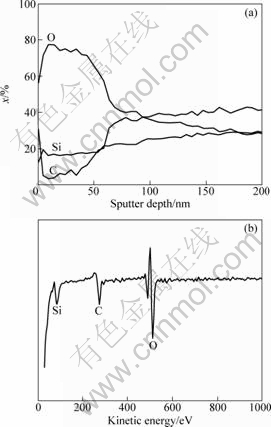
Fig. 6 AES depth profiles (a) and survey scan (b) of SiC-1 fiber after thermal exposure at 600 ℃
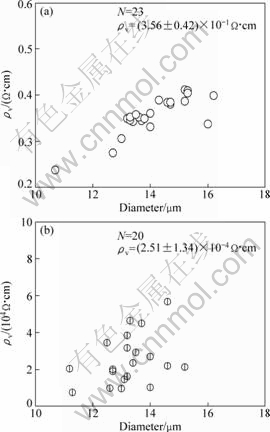
Fig. 7 Results of electrical resistivity (ρv) tests before (a) and after (b) thermal exposure to air (N is number of fiber)
3.4 Formation of carbon layer
Surface structure of SiC fibers is closely connected with the pyrolysis technological operation. The gas evolution of the cured polycarbosilane fiber during pyrolysis is shown in Fig. 8.
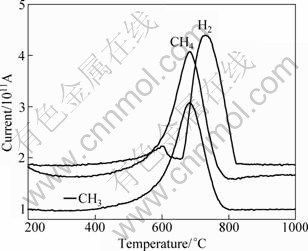
Fig. 8 Gas evolution during pyrolysis of cured polycarbosilane fiber
As shown above, m/z values of the three main gaseous products in evolution in the temperature ranging from 600 to 800 ℃ are 2, 16 and 15, and can be assigned to H2, CH4 and —CH3, respectively. The gaseous products result from the decomposition of the side chains such as Si—H and Si—CH3.
Manufacture of the SiC-1 fiber was conducted continuously in a tube furnace at the temperature of 1300-1400 ℃, the organic molecules of the cured PCS fiber will suffer from a huge thermal shock suddenly and convert into inorganic Si—C networks accompanied by gas evolution. The hydrocarbon volatiles, such as CH4 which can be regarded as carbon resource, will do re-pyrolysis and deposit on the SiC fiber at a high temperature in the tube furnace. It goes on without saying that the process is a chemical vapour deposition (CVD). Re-pyrolysis of hydrocarbon volatiles makes the SiC fiber carbon excess on the peripheral surface.
CH4(g)→C(s)+2H2(g) (2)
The starting temperature of deposition with assumption that graphite carbon and hydrogen are pyrolysis products of the CH4, neglecting the chemical kinetics, can be evaluated by the thermodynamic equation. The expression for the free energy of the pyrolysis is given by:



(3)
where
and Qf are the standard free energies in atmospheric pressure and quotient of fugacity, respectively;
,
and
,
represent the fugacities and fugacity parameters of H2 and CH4, respectively. The theoretical deposition temperature in the atmospheric pressure, implying that
=0, is 560 ℃. In practice, the value exhibits large deviation for two reasons: 1) the evolution of CH4 from the pyrolysis of the chains, such as Si—H and Si—CH3, starting at 550 ℃ [17] and the PCS fiber was started to decompose at the theoretical temperature; 2) Qf cannot be neglected when the pressures of CH4 and H2 are not within the atmospheric pressure. The practical deposition temperature will increase with the introduction of RTlnQf in Eq. (3). Despite of the two reasons, the deposition will happen at a high temperature of 1300-1400 ℃, the volatiles, such as CH4, will do re-pyrolysis and form an excess carbon layer on the SiC fibers.
In the cases of the SiC-2 fiber and SiC-3 fiber, the cured fibers sustain the increasing heat by a slow degree, and the organic-inorganic transition is relatively slow; hydrocarbon volatiles which can be regarded as carbon resources are almost blew away by the inert gas flow; the absence of sufficient carbon resource makes the deposition of carbon impossible. Therefore, the surfaces of the two fibers were not excess carbon, and the value of electrical resistivity was relatively high.
4 Conclusions
1) The electrical properties of several SiC fibers prepared from the pyrolysis of organosilicon precursors were studied in correlation with their chemical and structural properties. The excess carbon layer with a thickness of about 50 nm existing in the circular outer part is the main reason for the low electrical resistivity of SiC-1 fiber. And the surface structure can also affect the specific resistivity of SiC fiber, as well as the free carbon content and the crystallization.
2) Formation of the excess carbon layer is closely connected with the technological operation. The quick achievement of organic-inorganic transition is accompanied by vigorous CH4 liberation, and then- pyrolysis and deposition of CH4 will make SiC fiber carbon excess on the peripheral surface.
References
[1] LIU H T, CHENG H F, WANG J, TANG G P, CHE R C, MA Q S. Effects of the fiber surface characteristics on the interfacial microstructure and mechanical properties of the KD SiC fiber reinforced SiC matrix composites [J]. Mater Sci Eng A, 2009, 525(1-2): 121-127.
[2] LIU H T, CHENG H F, WANG J, CHE R C, TANG G P, MA Q S. Microstructural investigations of the pyrocarbon interphase in SiC fiber-reinforced SiC matrix composites [J]. Mater Lett, 2009, 63(23): 2029-2031.
[3] WANG H L, ZHOU X G, YU J S. Fabrication of SiCf/SiC composites by chemical vapor infiltration and vapor silicon infiltration [J]. Mater Lett, 2010, 64(15): 1691-1693.
[4] YU H J, ZHOU X G, WANG H L. 2D SiC/SiC composite for flow channel insert (FCI) application [J]. Fusion Eng Des, 2010, 85(7-9): 1693-1696.
[5] CHAUVET O, STOTO T, ZUPPIROLI L. Hopping conduction in a nanometer-size crystalline system: A SiC fiber [J]. Phys Rev B, 1992, 46(13): 8139-8146.
[6] ISHIKAWA T. Recent development of the SiC fiber Nicalon and its composites, including properties of the SiC fiber Hi-Nicalon for ultra-high temperature [J]. Compos Sci Technol, 1994, 51(2): 135-144.
[7] CHOLLON G, PAILLER R, CANET R, DELHAES P. Correlation between microstructure and electrical properties of SiC-based fibers derived from organosilicon precursors [J]. J Eur Ceram Soc, 1998, 18(6): 725-733.
[8] NARISAWA M, ITOI Y, OKAMURA K. Electrical resistivity of Si-Ti-C-O fibers after rapid heat treatment [J]. J Mater Sci, 1995, 30(13): 3401-3406.
[9] ZHENG Chun-man, LI Xiao-ding, WANG Hao, ZHU Bin. Thermal and curing kinetics of polycarbosilane fibers [J]. Transactions of Nonferrous Metals Society of China, 2006, 16(2): 44-48.
[10] LI W, SONG Y C, MAO X H. Mechanism of cyclohexene vapor curing polycarbosilane fibers [J]. J Mater Sci, 2006, 41(21): 7011-7018.
[11] MAO X H, SONG Y C, LI W. Mechanism of curing process for polycarbosilane fiber with cyclohexene vapor [J]. J Appl Polym Sci, 2007, 105(3): 1651-1657.
[12] LI X D, EDIRISINGHE M J. Evolution of the ceramic structure during thermal degradation of a Si-Al-C-O precursor [J]. Chem Mater, 2004, 16(6): 1111-1119.
[13] KURTENBACH D, MARTIN H P, M?LLER E, ROEWERB G, HOELL A. Crystallization of polymer derived silicon carbide materials [J]. J Eur Ceram Soc, 1998, 18(13): 1885-1891.
[14] MONTHIOUX M, DELVERDIER O. Thermal behavior of (Organosilicon) polymer-derived ceramics. Part V: Main facts and trends [J]. J Eur Ceram Soc, 1996, 16(7): 721-731.
[15] TAKEDA M, SAKAMOTO J H, IMAI Y, ICHIKAWA H. Thermal stability of the low-oxygen-content silicon carbide fiber Hi- NicalonTM [J]. Compos Sci Technol, 1999, 59(6): 813-819.
[16] SHIMOO T, OKAMURA K, MUTOH W. Oxidation behavior and mechanical properties of low-oxygen SiC fibers prepared by vacuum heat-treatment of electron-beam-cured poly(carbonsilane) precursor [J]. J Mater Sci, 2003, 38(8): 1653-1660.
[17] HASEGAWA Y, OKAMURA K. Synthesis of continuous silicon carbide fiber. III. Pyrolysis process of polycarbosilane and structure of the products [J]. J Mater Sci, 1983, 18(12): 3633-3648.
组成和结构对SiC纤维电阻率的影响
王得印,宋永才,李永强
国防科技大学 新型陶瓷纤维及复合材料重点实验室,长沙410073
摘 要:通过烧成制备电阻率不同的4种SiC纤维,并对纤维的元素组成、结晶性能和表面结构进行分析。结果表明:通过调整不熔化及烧成工艺参数可以获得电阻率量级不同的SiC纤维。当纤维表层具有一定厚度的高富碳层结构时,纤维的电阻率受整体自由碳含量与结晶性能的影响不显著,此时,纤维具有较低的电阻率。富碳层的产生与不熔化纤维烧成时分解产生的烃类小分子的重新裂解沉积有关。通过低温氧化除去纤维表面的富碳层可以使纤维的电阻率增大。表面结构对连续SiC纤维的电阻率有重要影响。
关键词:SiC纤维;富碳层;电阻率
(Edited by LI Xiang-qun)
Corresponding author: SONG Yong-cai; Tel: +86-731-84576442; E-mail: songyongcai@yahoo.com.cn
DOI: 10.1016/S1003-6326(11)61295-8