
Effect of large deformation on microstructure of ZK60 alloy
LIN Jin-bao(林金保)1, 2, WANG Qu-dong(王渠东)1, CHEN Yong-jun(陈永军)1,
ZHANG Lu-jun(张陆军)1, DING Wen-jiang(丁文江)1
1. National Engineering Research Center of Light Alloy Net Forming, Shanghai Jiao Tong University,
Shanghai 200030, China;
2. School of Applied Science, Taiyuan University of Science and Technology, Taiyuan 030024, China
Received 28 July 2006; accepted 15 September 2006
Abstract: Microstructure evolution of ZK60 magnesium alloy deformed at 623 K by cyclic extrusion compression (CEC) large deformation method was investigated. ZK60 alloy was deformed in the range of accumulated true strain of 0.8-17. The microstructure of evolution was investigated by optical microscope (OM) and transmission electron microscopy (TEM). The results show that microstructure is obviously refined, and homogenous equiaxed microstructure is achieved in the entire range of the examined deformations by subjected to CEC deformation. By increasing the accumulated strain to 17, the grain size decreases into sub-micron regime with about several hundred nanometers. The mechanism of grain refinement in ZK60 alloy by CEC can be attributed to continuous dynamic recovery and recrystallization.
Key words: ZK60 magnesium alloy; cyclic extrusion and compression; continuous dynamic recovery and recrystallization; micros- tructure
1 Introduction
Mg alloys research has surged because of their good properties, such as low density, dimensional stability and high specific strength, which make them potential applications for automobiles and airplanes. However, as a consequence of their hexagonal close-packed (HCP) crystal structure, Mg alloys generally exhibit limited ductility and poor formability at ambient temperature. Grain refinement is an important means of improving the mechanical properties of magnesium alloys. According to the Hall-Petch relationship, yield stress depends on grain size. As grain size decrease, yield stress as well as ductility could rise. While large plastic deformations technologies provide feasibility for producing ultra-fine grain sizes in a sub-micrometer or nanometer range in bulk materials[1-3]. At present, several large plastic technologies are available, including equal-channel angular extrusion (ECAE), high-pressure torsion (HPT), accumulative roll-bonding (ARB) and cyclic extrusion and compression (CEC)[2].
An original method of CEC has been patented in Poland, which allows obtaining arbitrarily large plastic deformations[4-5]. This method combines the repetitive kneading effects of extrusion and compression to render the alloys a refined, dense and uniform microstructure in both grain and second phase distribution[6]. The CEC method has been successfully applied to refine the microstructures of Cu, Al alloys and other metals[4-6]. However, a little attention has been paid to the effect of CEC on the microstructures of magnesium alloys.
The present work was undertaken to examine the potential for grain refinement of ZK60 Mg alloy through CEC process. Emphases were placed on the microstructure evolution during CEC process of ZK60 alloy. As will be proved, CEC process is effective in decreasing grain size of ZK60 Mg alloy. Finally, the mechanism of grain refinement in ZK60 alloy by CEC was investigated.
2 Experimental
ZK60 alloy used in present study has a chemical composition of Mg 5.5% Zn 0.5%Zr. It was received as extruded rods with a diameter of 30 mm and then cut to pieces with a length of 42 mm. Before CEC processing the rod was annealed at 623 K for 1.5 h, and the CEC die was preheated to 623 K. CEC was carried out by pushing a sample from one cylindrical chamber with a diameter d0 to another one with equal dimensions, through a die with smaller diameter dm (Fig.1)[7]. The graphite was used as lubricant. All specimens were quenched in water immediately after deformation. The cumulated true strain after being subjected to n cycles of extrusion and compression is given by
In this study, the parameters d0=30 mm and dm=20 mm, make the strain 1.62 per cycle. We applied up to 10.5 cycles (10 cycles CEC and single extrusion) leaded to accumulated strains up to 17. The photo of specimen after CEC 1.5 cycles is shown in Fig.2.
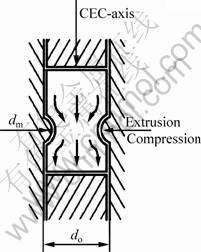
Fig. 1 Sketch of CEC deformation mode
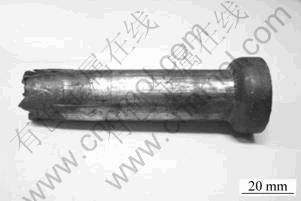
Fig. 2 Specimen photo of CECed ZK60 alloy at 623 K
The microstructure along CEC extrusion direction of CECed ZK60 alloy was studied by optical microscope (OM, LEICA MEF4M) and transmission electron microscopy (TEM, JEM-100).
3 Results and discussion
3.1 Microstructure observation
The optical microstructures of CECed ZK60 alloys with different cycles at 623 K are shown in Fig. 3. True grain size d was measured by the linear intercept method using a correction factor of 1.74[8]. Fig.3(a) shows the micrograph of the as-extruded materials (without CEC). It can be seen that the grain size distribution tends to be rather heterogeneous: the large grains (some coarser than 50 ?m) are accompanied with some fine recrystallized grains smaller than 5 ?m, and the average is about 15- 25 ?m.
Figs.3(b)-(d) show the micrographs of the alloy after CEC: (b) 1.5 cycles, (c) 4.5 cycles, (d) 10.5 cycles at 623 K. As shown in Fig.3(b), the homogeneous structure containing significantly refined equiaxed grains (about 3.5 ?m) is present in the alloy after only 1.5 cycles of CEC. Similar to other SPD methods, this fact confirms that grain refinement is most pronounced at the initial stage of CEC process but is not significant at large strains[9-11].
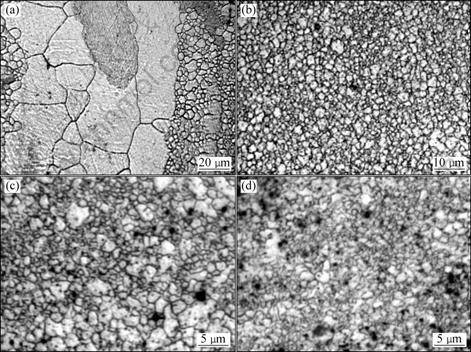
Fig. 3 Optical microstructures of ZK60 alloy prior to CEC (a), after CEC 1.5 cycles (b), after CEC 4.5 cycles (c) and after CEC 10.5 cycles (d)
After 4.5 cycles, the microstructure was further refined to an average grain size of about 1.8 ?m. Although some large grains (2-4 ?m) are still present, most grains were refined to the sub-micron scale (Fig.3(c)). Moreover, some ultra-fined grains (500-700 nm) were found by transmission electron microscopy (TEM) (Fig.4(a)). Deformation up to 10.5 cycles further refines the grains to an average size of small than 1?m and grain structures are homogenized and equiaxed which suggested that dynamic recrystallization took place during CEC process. And there are some nano-grains which are too small to be resolved by optical metallography technique. TEM observation gave an estimated grain size of between 0.5 and 0.7 μm, shown in Fig.4(b).
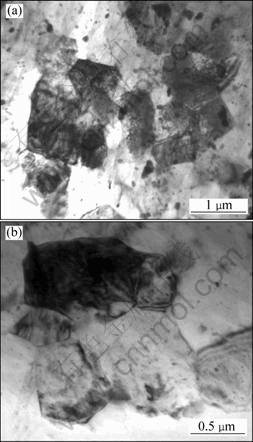
Fig. 4 TEM microstructures ZK60 alloy subjected to CEC (a) 4.5 cycles, (b)10.5 cycles
The TEM examination reveals that the structure of the CECed ZK60 alloy is characterized by a big fraction of high-angle grain boundaries (HAGBs) and equiaxed grains (Fig.4 and Fig.5). Moreover, the dislocation pile-ups can be visible in some grains of the CECed alloys (Fig.5). At the same time, sub-boundaries and low angle grain boundaries (LAGBs) are also discovered. This indicates that during the CEC process sliding dislocation form dislocation boundaries and subgrain boundaries in accordance with low energy dislocation structure (LED) theory[12].
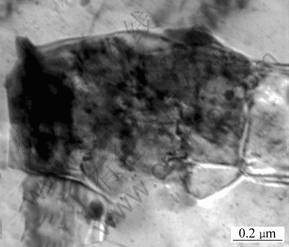
Fig.5 TEM image of subgrain structure and dislocation pile-ups of CECed ZK60 alloy
3.2 Discussion
The grain size as a function of the accumulated strain is shown in Fig.6. The final microstructure shows very fine equiaxed grains (about 700 nm) (Fig.4(b)). The significant reduction of the grain size proves that the current CEC process is effective in refining the micro- structure of ZK60 alloy.
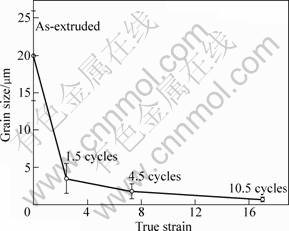
Fig. 6 Grain size as function of accumulated strain
Some investigations indicate that the formation of ultra-fine grains by CEC is generally connected with the formation of microband microstructure and the evolution of ultra-fine microstructure results in the intersection of the microbands whose width systematically decreases with increasing deformation [4, 13]. In present work, the homogeneous microstructure with equiaxed fine grains instead of the microband microstructure has been observed in all range of deformation, which suggests that there is a different mechanism of grain refinement for the CECed ZK60 alloy, which maybe related to dynamic recovery and recrystallization. Since dynamic recovery and recrystallization are easily activated in the grain boundaries with large strain concentration[10,14], the refined grains and tangled dislocations obviously render a large driving force for dynamic recovery and recrystallization. With given more deformation, dynamic recovery and recrystallization rapidly takes place and more fine grains are observed. So, with the increase of the accumulated true strain, the microstructures become more finely and homogeneously. Moreover, many dislocation boundaries and subgrain boundaries have been replaced by LAGBs and HAGBs in an equaixed structure thereby reducing the total surface energy of these boundaries[15]. Above results indicate that the structure of subgrain boundaries evolves into LAGBs and HAGBs which is a kind of dynamic recovery and recrystallization during CEC process. However, there is no any new recrystallization nucleus surround with the HAGBs observed by TEM, so it should be regarded as the continuous dynamic recovery and recrystalliza- tion[11,16].
Moreover, it has been shown that a strong hydrostatic compression pressure may lead to a stronger ‘fragmentation’ of the microstructure [4]. The resulting subgrain size is smaller than that resulting from conventional deformation modes which seems to be the consequence of the higher hydrostatic pressure of CEC.
4 Conclusions
1) CEC process is effective in refining the grain size of ZK60 alloy.
2) The homogeneous structure with the significantly refined equiaxed grains is present after CEC, and the average grain size is refined from 20.0 μm to 0.7 μm by 10.5 CEC cycles at 623 K.
3) During CEC, dislocations form dislocation boundaries, sub-boundaries and then evolve to low and high angle grain boundaries.
4) The main mechanism of formation of ultra-fine grains after large deformations is connected with the continuous dynamic recovery and recrystallization. Moreover, the higher hydrostatic pressure of CEC results in ultra-fined microstructure.
References
[1] Morris D G. Mechanical Behaviour of Nanostructured Materials Materials Science Fundations 2[M]. Switzerland: Trans Tech Publications, 1998.
[2] Valiev R Z, Islamgaliev R K, Alexandrov I V. Bulk nanostructured materials from severe plastic deformation[J]. Progress in Materials Science, 2000, 45: 103-189.
[3] MEYERS M A, MISHRA A, BENSON D J. Mechanical properties of nanocrystalline materials[J]. Progress in Materials Science, 2006, 51: 427-556.
[4] Richert M,Richert J, Zasadzin?ski J, hawrylkiewicz S, dlugopolski j. Effect of large deformations on the microstructure of aluminium alloys[J]. Materials Chemistry and Physics,2003, 81(2/3): 528-530.
[5] Richert J, Richert M. A new method for unlimited deformation of metals and alloys[J]. Aluminium (Germany), 1986, 62(8): 604-607.
[6] YEH J W, YUAN S Y, PENG C H. A reciprocating extrusion process for producing hypereutectic Al-20wt.% Si wrought alloys[J]. Mater Sci Eng A, 1998(252): 212-221.
[7] Richert M, Stu?we H P, Zehetbauer M J, Richert J, Pippan r, Motz ch, Schafler e. Work hardening and microstructure of AlMg5 after severe plastic deformation by cyclic extrusion and compression[J]. Mater Sci Eng A, 2003, 355: 180-185.
[8] Kim W J, Hong S I, Kim Y S, Min S H, Jeong H T, Lee J D. Texture development and its effect on mechanical properties of an AZ61 Mg alloy fabricated by equal channel angular pressing[J]. Acta Materialia, 2003, 51: 3293-3307.
[9] Dong Hyuk Shin, Kim I, Kim J, Park K T. Grain refinement mechanism during equal-channel angular pressing of a low-carbon steel[J].Acta Materialia, 2001, 49(7): 1285-1292.
[10] Yuan S Y, Yeh J W, Tsau C H. Improved microstructures and mechanical properties of 2024 aluminum alloy produced by a reciprocating extrusion method[J].Materials Transactions, JIM, 1999, 40(3): 233-241.
[11] JIN Li, LIN Dong-liang, MAO Da-li, ZENG Xiao-qin, CHEN Bin, DING Wen-jiang. Microstructure evolution of AZ31 Mg alloy during equal channel angular extrusion[J]. Mater Sci Eng A, 2006, A423: 247-252.
[12] Doris K W. High-strain disloca- tion patterning, texture formation and shear banding of wavy glide materials in the LEDS theory[J]. Scripta Materialia, 1997, 36: 173-181.
[13] Kurzydlowski K J, Richert M, Richert J, Zasadziński J, Su?-Ryszkowska M. Effect of non-conventional large deformations on the formation of nanostructure in materials[J]. Solid State Phenomena, 2004, 101/102: 31-36.
[14] Lee S W, Yeh J W, Liao Y S. Premium 7075 aluminium alloys produced by reciprocating extrusion[J]. Advanced Engineering Materials, 2004, 6 (12): 936-943.
[15] Richert M, Liu Q, Hansen N. Microstructural evolution over a large strain range in Aluminum deformed by cyclic-extrusion- compression[J]. Mater Sci and Eng A, 1999, A260: 275-283.
[16] Humphreys F J, Hatherly M. Recrystallization and Related Annealing Phenomena[M]. Great Britain: Galliard Publishing Ltd., Great Britain, 1995.
(Edited by YANG Hua)
Foundation item: Project (50674067) supported by the National Natural Science Foundation of China
Corresponding author: LIN Jin-bao; Tel: +86-21-62932508; E-mail: linjinbao@sjtu.edu.cn, linjinbao@sohu.com