文章编号:1004-0609(2011)10-2631-08
Al-Zn-Mg-Cu合金的淬火敏感性
熊柏青,李锡武,张永安,李志辉,朱宝宏,王 锋,刘红伟
(北京有色金属研究总院 有色金属材料制备加工国家重点实验室,北京 100088)
摘 要:采用分级淬火试验方法,结合对合金峰时效态硬度、淬火态电导率的测试,拟合得到新型Al-7.5Zn-1.7Mg-1.4Cu-0.12Zr合金的温度—时间—性能(TTP)曲线,并与传统的7B04和7150合金进行比较。结果表明:新型合金的TTP曲线鼻温大约在290 ℃,其孕育期约为4.5 s,与同等条件下制备的7150合金(320 ℃,2.6 s)和7B04合金(335 ℃,0.1 s)相比,其TTP曲线的鼻温最低,对应的孕育期最长,反映出新型合金过饱和固溶体的稳定性最高,具有最低的淬火敏感性。进一步的TEM分析表明,随着鼻温附近保温处理时间的延长,合金内部的淬火脱溶析出现象不断加剧。淬火诱导脱溶η相优先在(亚)晶界上形核析出,在晶内依附于已存在的Al3Zr弥散相粒子形核析出;时效后,在这些粗大η相周围形成一定宽度的无沉淀析出带。合金的成分及组织形态影响和决定着合金的淬火敏感性;新型合金淬火可以适当降低冷却速度以减小残余应力。
关键词:Al-Zn-Cu-Mg合金;淬火敏感性;TTP曲线;脱溶析出
中图分类号:TG111.5 文献标志码:A
Quench sensitivity of Al-Zn-Mg-Cu alloys
Xiong Bai-qing, Li Xi-wu, Zhang Yong-an, Li Zhi-hui, Zhu Bao-hong, WANG Feng, liu Hong-wei
(State Key Laboratory of Nonferrous Metals and Processes, General Research Institute for Nonferrous Metals,
Beijing 100088, China)
Abstract: The quench sensitivity of an Al-7.5Zn-1.7Mg-1.4Cu-0.12Zr alloy was determined by temperature-time- property (TTP) curve by an interrupted quench method with the measurement of the hardness as aged and electrical conductivity as quenched compared with traditional 7B04 alloy and 7150 alloy. The results indicate that the nose temperature of TTP curve and the corresponding incubation period of the novel alloy, 7150 alloy and 7B04 alloy are about (290 ℃, 4.5 s), (320 ℃, 2.6 s) and (335 ℃, 0.1 s), respectively, the nose temperature of the alloy is the lowest among three alloys and the critical time at the nose temperature is the longest for the alloy, which is obvious that the supersaturated solid solution of the alloy is the most stable, exhibiting the alloy has the lowest quench sensitivity. Further, TEM analysis results show that, with the prolongation of keeping time at the nose temperature, the quench-induced precipitation phenomenon becomes obvious. The quench-induced η precipitates nucleate and precipitate at grain and sub-grain boundaries by preference, and the quench-induced precipitates appear to nucleate mostly on the pre-existing Al3Zr dispersoids. After aging treatment, these η precipitates were surrounded by a precipitate-free zone. The composition and microstructure morphology of alloy play an important role in the quench sensitivity of the alloy quenched. For the novel alloy, appropriately decreasing the cooling rate may be helpful to relieve the residual stresses.
Key words: Al-Zn-Cu-Mg alloy; quench sensitivity; TTP curve; precipitation
7×××系(Al-Zn-Mg-Cu)合金具有较高的室温强度和良好的综合性能,是世界各国航空、航天、交通运输等领域不可或缺的结构材料[1-2]。经过80多年的发展,7×××系铝合金已先后成功开发出了7×75、7×50和7055等系列合金,得到了广泛的应用。随着新一代飞机的发展,上述7×××系高强铝合金由于存在淬火敏感性高的问题,都难以满足当今对超大厚度(150 mm以上)航空铝合金锻件、预拉伸板制品提出的紧迫需 求[3]。为此,美国铝业公司(Alcoa)于2003年在国际上率先推出具有高强韧性和低淬火敏感性的7085合金(Al-7.5Zn-1.5Mg-1.6Cu-0.12Zr),现已在空客A380等飞机中用于制造翼梁和翼肋等主承力结构件[4]。但研究表明,由于7085铝合金中主强化元素Mg的含量相对过低,制约了合金强度的进一步提高。为此,本研究在美铝7085合金的基础上,针对7085合金强度性能尚显不足的问题,通过适当提高合金中主强化元素Mg的含量,并进一步降低合金中淬火敏感性元素Cu的含量,探索研究一种新型的Al-7.5Zn-1.7Mg-1.4Cu- 0.12Zr合金。
7×××系铝合金是典型的时效强化合金,固溶淬火得到的α固溶体过饱和程度对合金时效强化效果具有决定性作用。在淬火过程中这种过饱和固溶体通常是很不稳定的,要想得到理想的过饱和程度就必须迅速冷却以避免发生脱溶析出。合金在淬火过程中过饱和α固溶体的稳定性及其发生脱溶析出的难易程度是合金(材料)的一种本征表现,称其为淬火敏感性。淬火敏感性的高低决定厚截面铝合金工件在特定淬火条件下被淬透的能力。在合金一定的情况下,确定合金淬火敏感性的高低,以选择适宜的淬火制度,既防止合金在淬火过程中发生脱溶析出、降低合金的力学性能,又有效控制和降低工件的残余应力,显得尤为重要。通过分级淬火方法测定合金的温度-时间-性能(TTP)曲线(又称为C曲线)是表征合金淬火敏感性的一种有效可行的方法,一些学者对部分铝合金的TTP曲线进行了研究[5-7],并就相关影响因素进行了分析[8-10],但该方面的研究结果仍非常有限,对于新型低淬火敏感性合金与传统高淬火敏感性合金的对比、特别是在同等条件下进行测试评价的研究工作难见相关报道。为此,本文作者采用分级淬火试验方法,结合对合金峰时效态硬度、淬火态电导率的测试,在同等测定条件下拟合得到了新型合金、传统的7B04合金和7150合金的TTP曲线,评价合金的淬火敏感性;利用TEM分析了新型合金在等温保温处理过程中发生淬火脱溶析出的行为特征,并初步探讨了决定合金淬火敏感性的影响因素,具有实际意义和理论价值。
1 实验
实验用新型合金的化学成分为:Al-7.5Zn-1.7Mg- 1.4Cu-0.12Zr、0.02Fe、0.01Si(质量分数,%)。合金铸锭经(440 ℃, 12 h)+(475 ℃, 24 h)的均匀化热处理后,热挤压成截面为102 mm×25 mm的板带。为了开展对比研究,本研究还在同等条件下制备了7150合金(Al-6.4Zn-2.3 Mg-2.3Cu-0.12Zr, Fe, Si<0.01%)和7B04合金(Al-6.2%Zn-2.6%Mg-1.6%Cu-0.16%Cr-0.31%Mn、0.15%Fe、0.05%Si(质量分数,%))挤压板带。为保证合金在分级淬火过程中温度的快速响应,采取2 mm× 20 mm×20 mm较小尺寸的试样。合金经470~475 ℃的固溶处理后,快速淬入温度190~430 ℃(共取9个点,相邻温度间隔30 ℃)的盐浴炉中进行等温处理,转移时间小于3 s,盐浴炉的温度波动为±3 ℃,保温一定时间(2~2 400 s)后立即淬入室温水中,之后立即测试合金的淬火态电导率,再经7×××系铝合金通用的 120 ℃、24 h峰值时效热处理后测试合金的硬度,由获得的等温处理过程中合金硬度的变化曲线绘制TTP曲线图。
合金的电导率测试参照GB/T 12966—2008采用7501型涡流电导仪进行。HV硬度测试参照GB/T 4340—2009在WOLPERT 430SVD型数显维氏硬度计上进行,加载力196 N。每个实验点测得至少5个以上的有效数据,取平均值。显微组织观察在JEM-2010高分辨透射电镜(TEM)上进行,工作电压200 kV。TEM样品用MTP-1双喷电解减薄仪制取,电解液为含25% HNO3的甲醇溶液,温度控制在-30~-20 ℃之间,电压为15~20 V。
2 结果与分析
2.1 分级淬火等温保温处理对合金峰时效态硬度和淬火态电导率的影响
完成固溶处理后,对样品不进行中间分级淬火保温处理而直接进行室温水淬处理,测得新型合金、7150和7B04合金淬火态电导率和峰时效态硬度值分别为20.7、18.2、18.0 MS/m和180、188、195 HV。
图1所示为新型合金、7B04合金和7150合金等温保温处理峰时效态硬度和淬火态电导率曲线。由图1可以看出,随着保温时间的延长,合金时效态的硬度总体上均呈下降趋势,淬火态电导率相应地呈上升趋势,而且硬度的下降速率和电导率的上升速率取决于保温温度。总体而言,新型合金受保温温度及时间的影响程度最小,7B04合金受影响程度最大,而且3种合金受影响程度大的保温温度点及时间也存在着明显的差异。对于新型合金,如图1(a)和(b)所示,峰时效态硬度下降速率和相应的电导率上升速率基本上随保温时间的延长单调增加,合金性能受影响程度最大的温度是280 ℃,其次是310 ℃和250 ℃;温度由280 ℃上升或下降,性能的变化幅度明显减小,当温度为400 ℃和430 ℃时,合金的性能在试验时间2 400 s内几乎没有变化,而且即使在受影响程度最大的280 ℃,合金的性能变化也是在保温10 s后才能明显区别。对于7B04合金,如图1(e)和(f)所示,与新型合金存在着明显的差异,合金性能受影响程度最大的温度是340 ℃,其次是310 ℃和370 ℃;温度在310 ℃及其以上时,峰时效态硬度下降速率和相应的电导率上升速率基本呈单调递减,而温度低于310 ℃则在保温的前 600 s内呈递增趋势,之后变为递减。即使在最高的430 ℃时,合金的性能也随保温时间发生变化;而且保温2 s后的性能已有明显的变化。对于7150合金,如图1(c)和(d)所示,性能变化规律与新型合金更接近一些,但合金性能受影响程度最大的温度是340 ℃,其次是310 ℃和280 ℃;温度由340 ℃上升或是下降,性能的变化幅度明显减小,温度为430 ℃时,合金性能在试验时间2 400 s内几乎没有变化。
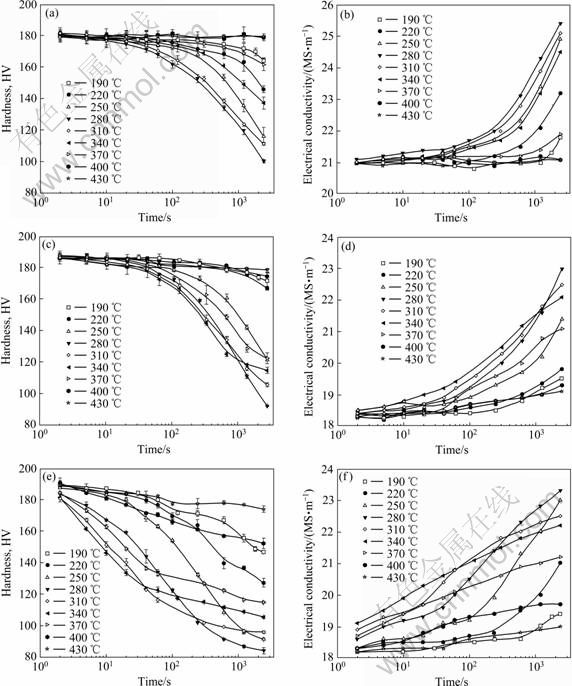
图1 分级淬火等温保温处理下合金的峰时效态硬度和淬火态电导率曲线
Fig.1 Hardness as aged and electrical conductivity as quenched with isothermal duration: (a), (b) Novel alloy; (c), (d) 7150 alloy; (e), (f) 7B04 alloy
2.2 合金的TTP曲线
EVANCHO和STALEY[6, 11]在研究铝合金连续冷却析出动力学时给出了TTP曲线(C曲线)的一般方程如下:
(1)
式中:k1为常数,等于淬火过程中为转变分数的自然对数;k2为与形核数目的倒数有关的常数,s;k3为与单位形核能有关的常数,J/mol;k4为与固溶相线温度有关的常数,K;k5为与扩散激活能有关的常数,J/mol;R为摩尔气体常数,8.314 J/(mol?K);T为热力学温度,K。显然C(T)是描述TTP曲线中某个温度下发生一定数量析出转变所需要的临界时间,s。根据合金峰时效后的硬度与等温保温温度和保温时间的关系进行拟合可以得到TTP曲线。采用方程(1)通过多次非线性回归拟合得到相应的系数,见表1。
表1 新型合金、7150合金和7B04合金TTP曲线的系数
Table 1 Coefficients for Vickers hardness TTP curves of novel alloy, 7150 alloy and 7B04 alloy
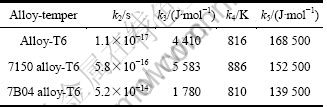
基于以上结果可以得到硬度最大值99.5% (99.5%HVmax)的TTP曲线,如图2所示。由图2可以看出,新型合金、7150合金和7B04合金的TTP曲线均呈“C”形,不同的是三者的C曲线鼻温范围及其孕育期均存在着明显的差异,新型合金的C曲线明显右下移。对于新型合金,C曲线鼻温大约在290 ℃,其孕育期约为4.5 s;对于7150合金,C曲线鼻温大约在320 ℃,其孕育期约为2.6 s;对于7B04合金,C曲线鼻温大约在335 ℃,其孕育期约为0.1 s。比较3种合金可以看出,新型合金C曲线的鼻温最低、对应的孕育期最长,7B04合金的鼻温最高、对应的孕育期最短;显然,在同样的淬火条件下,新型合金过饱和固溶体的稳定性最高,具有最低的淬火敏感性,这与之前研究3种合金淬透性的末端淬火实验结果是一致的[12]。
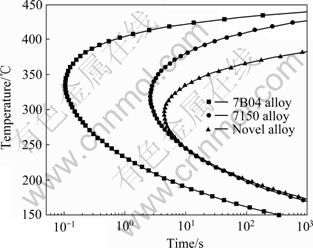
图2 新型合金、7150合金和7B04合金的TTP曲线 (99.5% HVmax)
Fig.2 TTP curves representing 99.5% of maximum attainable Vickers hardness for novel alloy, 7150 alloy and 7B04 alloy
2.3 等温保温处理过程中新型合金发生脱溶析出的行为特征
新型合金的鼻温大约为290 ℃,本研究选取其相邻温度(280 ℃)保温2 s、60 s和600 s的等温保温试样时效态组织进行TEM观察,对合金于鼻温条件下等温保温过程中新型合金发生脱溶析出的行为特征进行了分析。图3所示为新型合金在280 ℃等温保温2 s、100 s和600 s并水淬后峰时效态晶界和晶内的TEM形貌。由图3(a)和(b)可以看出,经过2 s等温保温后,合金的组织形貌与直接水淬后获得峰时效态组织形貌完全一致,晶内析出相尺寸为3~6 nm,晶界析出相比较窄,呈连续状分布,未出现明显的晶间无析出带(PFZ),晶内还有分布的Al3Zr弥散相粒子(见图3(b)中的箭头所示)。显然,合金在280 ℃等温保温2 s时未发生脱溶析出,这与由合金TTP曲线获得此温度下孕育期约为4.5 s相吻合。随着保温时间延长至60 s后(见图3(c)和(d)),晶内组织未见明显的变化,而晶界析出相却已显著粗化,呈层片状断续分布,并且形成宽度约150 nm的晶间无析出带,晶内还有分布的Al3Zr粒子(见图3(d)中的箭头所示);由选区电子衍射花样分析结果(见图4(a))可知,晶界上的脱溶析出相为含有Cu和Al、MgZn2结构的η相。当保温时间达到600 s后(见图3(e)和(f)),晶界析出相未见明显变化,晶间无析出带略有加宽,而晶内组织则出现了显著的变化,析出了大量粗大的η相(衍射花样见图4(b)),多为棒状,少量呈层片状,尺寸为100~400 nm,这些粗大粒子周围基本上看不到时效析出的弥散沉淀相,存在着一定宽度的无沉淀析出带。进一步可以发现,这些粗大的η相粒子中大都可以观察到球形的Al3Zr粒子(见图3(f)中的箭头所示),其能谱分析结果为84.44%Al、10.36%Zn、2.62%Cu、1.06%Mg和1.52%Zr(质量分数)。显然,在淬火前合金中存在的部分Al3Zr粒子成了在晶内优先脱溶析出的形核点。
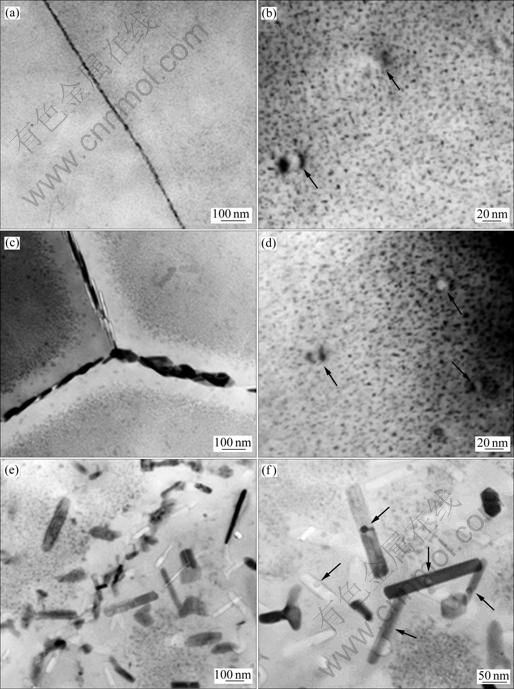
图3 280 ℃等温保温处理不同时间的新型合金峰时效态晶内晶界TEM像
Fig.3 TEM images of precipitates at grain boundary and inside grain of alloy under aging conditions after isothermal treatment for different times at 280 ℃: (a), (b) 2 s; (c), (d) 60 s; (e), (f) 600 s
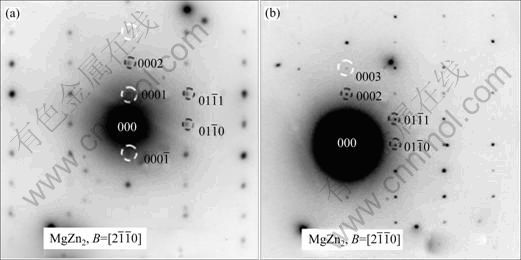
图4 280 ℃等温保温处理的新型合金峰时效态晶界和晶内析出相的衍射花样
Fig.4 SAED patterns of precipitates of alloy under aging conditions after isothermal treatment at 280 ℃: (a) Precipitates at grain boundary; (b) Precipitates inside grain
3 讨论
合金的淬火敏感性反映了合金在淬火过程中过饱和固溶体的稳定性,其稳定性越高,越能在较低的冷却速率条件下将过饱和形式固定到室温,淬火敏感性越低,淬透性越高。铝合金的淬火敏感性决定于过饱和α固溶体的转变动力学特性。过饱和α固溶体的脱溶过程是一个扩散过程,与钢相似,其脱溶速度和温度的关系也具有C曲线的特点,即由于过冷度与原子扩散速度这两个因素的相互制约[13],合金元素Zn、Mg和Cu在铝基体中的溶解度随温度降低而减小,过饱和固溶体在淬火过程中可能会发生脱溶析出第二相,但析出速度取决于温度。在高温区间,由于过饱和度小,脱溶析出的驱动力很小,第二相主要通过非均匀形核析出,虽然溶质原子扩散速度大,但形核率很小,脱溶析出速度很小;在低温区间,虽然过饱和度较大,析出驱动力大,但由于温度较低,溶质原子扩散速度小,第二相长大速度慢,故脱溶析出速度很小;只有在中温区间既有一定的驱动力,温度又较高、溶质原子扩散速度较大,因此,脱溶析出速度较大。从而使得脱溶析出速度在某一温度达到最大值,即鼻温,本研究中,新型合金、7150合金和7B04合金的TTP曲线(即C曲线)的鼻温分别为290 ℃、320 ℃和335 ℃左右(见图2)。而孕育期的长短表示过饱和α固溶体稳定性的高低,从而反映了合金淬火敏感性的低与高。从TTP曲线中可以看出,在鼻温处孕育期最短,过饱和α固溶体最不稳定,脱溶析出速度最快,合金的淬火敏感性最高;在高温和低温区孕育期较长,合金的淬火敏感性较低。而且,C曲线越往右移,孕育期越长,过饱和α固溶体越稳定,脱溶析出速度越慢,铝合金淬火敏感性越低;反之依然。7150合金和7B04合金的TTP曲线(即C曲线)的鼻温处所对应的孕育期分别为4.5 s、2.6 s和0.1 s左右(如图2所示),显然,新型合金具有相对较低的淬火敏感性。
大量的实验结果表明,合金的成分(包括合金元素总含量、成分配比以及杂质含量)和组织(第二相的种类、数量和分布以及(亚)晶界形态、组织的均匀性等)影响和决定着合金的淬火敏感性,合金的成分决定着合金基体过饱和固溶体的稳定性,(亚)晶界及晶内弥散相等第二相粒子等在淬火缓冷过程中容易成为非均质形核质点诱导脱溶析出的产生。Al-Zn-Mg-Cu合金中,(Zn+Mg+Cu)元素总含量及其配比、Cu含量、含Zr或Cr等弥散相、以及(亚)晶界形态等均会对合金的淬火敏感性产生影响。有研究表明[14-16],低的合金元素总含量、低的Cu含量、高的Zn/Mg比、用Zr替代Cr均能有效降低合金的淬火敏感性;特别是Cr的弥散相,由于其点阵常数与铝基体相差较大,与基体处于非共格状态,其周围畸变较大,容易成为淬火脱溶析出相的形核核心;高的Zn/Mg比会减小析出相的尺寸,增加析出相的密度。本研究工作新近结果进一步表明,主合金元素Zn、Mg、Cu的摩尔分数显著影响着合金过饱和固溶体的晶格常数,决定着合金过饱和固溶体的稳定性,其中,Cu元素原子引起的晶格畸变要明显大于Mg和Zn,Cu元素含量对Al-Zn-Mg-Cu合金的淬火敏感性影响最为显著(相关研究工作将另行报道)。从7B04、7150到新型合金,溶质原子总含量降低,Cu含量显著降低,合金固溶体晶格畸变降低,过饱和固溶体稳定性增加,而且用Zr替代了Cr、Zn/Mg比增加,新型合金淬火敏感性明显降低。新型合金具有低的淬火敏感性,正是其成分设计和组织控制良好结合的反映。因此,在厚截面大规格用7×××铝合金材料的成分设计、加工制备以及热处理工艺 中,可以通过成分调整和组织控制来最大可能地降低合金的淬火敏感性。
为了尽可能减小残余应力,应使合金工件从固溶热处理最高温度缓慢冷却至TTP曲线临界温度区域以上的某一温度,然后用快速冷却,只要使冷却时间少于产生析出所需的时间,就能尽量减少对合金性能的不利影响。如果已知实际淬火中可能的转变时间,则可以根据TTP曲线(见图2)判断对应的淬火敏感温度区间,从而来指导Al-Zn-Mg-Cu合金淬火工艺的制定:为保证合金的性能,合金固溶后淬火应在敏感温度区间内加快冷却速度快速通过,而在高于敏感温度区间,可以适当降低淬火速率减小热应力,这样在保证合金最终性能的同时,又可以减小残余应力,这可以通过冷速可调的淬火方式(如喷淋淬火等)来控制实现。不过,对于针对淬火敏感区间采取先慢后快的淬火方式,虽然实际上可以操作,但还应该考虑到在高温端较慢的冷却速率对空位过饱和度的影响,这会影响到合金时效过程中GP区的形成,对此还需要进一步的研究,需综合考虑来选择合金最适宜的淬火工艺。
4 结论
1) 通过TTP曲线的测定,新型合金TTP曲线鼻温大约在290 ℃,其孕育期约为4.5 s;较之同等条件下制备的7150合金(320 ℃,2.6 s)和7B04合金(335 ℃,0.1 s),新型合金C曲线的鼻温最低,且对应的孕育期最长,反映出新型合金过饱和固溶体的稳定性最高,具有最低的淬火敏感性。
2) 利用TEM分析研究新型合金在分级淬火等温保温过程中发生脱溶析出的行为特征发现,随着鼻温附近保温处理时间的延长,合金内部的淬火脱溶析出现象不断加剧。淬火诱导脱溶η相优先在(亚)晶界上形核析出,在晶内依附于已存在的Al3Zr弥散相粒子形核析出;时效后在这些粗大η相周围形成一定宽度的无沉淀析出带。
3) 合金的成分和组织特征影响和决定着合金的淬火敏感性;对于新型合金厚截面大规格工件,可以选择比7150和7B04合金较慢的淬火速度来保证其既获得合格、均匀的组织性能,又尽量降低残余应力。
REFERENCES
[1] WARNER T. Recently-developed aluminum solutions for aerospace applications[J]. Mater Sci Forum, 2006, 519/521(2): 1271-1278.
[2] MILLER W S, ZHUANG L, BOTTEMA J, WITTEBROOD A J, de SMET P, HASZLER A, VIEREGGE A. Recent development in aluminium alloys for the automotive industry[J]. Mater Sci Eng A,2000, 280(3): 37-49.
[3] JOHN L. Advanced aluminum and hybrid aerostructures for future aircraft[J]. Mater Sci Forum, 2006, 519/521: 1233-1238.
[4] CHAKRABARTI D J, LIU J, SAWTELL R R, VENEMA G B. New generation high strength high damage tolerance 7085 thick alloy product with low quench sensitivity[C]//Proceedings of ICAA 9. Melbourne: Institute of Materials Engineering Australasia Ltd, 2004: 969-974.
[5] BERNARDIN J D, MUDAWAR I. Validation of the quench factor technique in predicting hardness in heat treatable aluminum alloys[J]. Int J Heat Mass Transfer, 1995, 38(5): 863-873.
[6] STALEY J T. Quench factor analysis of aluminium alloys[J]. Mater Sci Technol, 1987, 3(11): 923-935.
[7] 张新明, 刘文军, 刘胜胆, 袁玉宝, 邓运来. 7050铝合金的TTP曲线[J]. 中国有色金属学报, 2009, 19(5): 861-868.
ZHANG Xin-ming, LIU Wen-jun, LIU Sheng-dan, YUAN Yu-bao, DENG Yong-lai. TTP curve of aluminum alloy 7050[J]. The Chinese Journal of Nonferrous Metals, 2009, 19(5): 861-868.
[8] DESCHAMPS A, BR?CHET Y. Influence of quench and heating rates on the ageing response of an Al-Zn-Mg-(Zr) alloy[J]. Mater Sci Eng A, 1998, 251(1/2): 200-207.
[9] ROBINSON J S, CUDD R L, TANNER D A. Quench sensitivity and tensile property inhomogeneity in 7010 forgings[J]. J Mater Proc Technol, 2001, 119(1/3): 261-267.
[10] LIU S D, ZHONG Q M, ZHANG Y, LIU W J, ZHANG X M, DENG Y L. Investigation of quench sensitivity of high strength Al-Zn-Mg-Cu alloys by time-temperature-properties diagrams[J]. Mater Design, 2010, 31(6): 3116-3120.
[11] EVANCHO J W, STALEY J T. Kinetics of precipitation in aluminum alloys during continuous cooling[J]. Metall Trans, 1974, 5(1): 43-47.
[12] 熊柏青, 李锡武, 张永安, 李志辉, 朱宝宏, 王 锋, 刘红伟. 新型高强韧低淬火敏感性Al-7.5Zn-1.65Mg-1.4Cu-0.12Zr合金[J]. 中国有色金属学报, 2009, 19(9): 1539-1547.
Xiong Bai-qing, Li Xi-wu, Zhang Yong-an, LI Zhi-hui, ZHU Bao-hong, WANG Feng, LIU Hong-wei. Novel Al-7.5Zn- 1.65Mg-1.4Cu-0.12Zr alloys with high strength high toughness and low quench sensitivity[J]. The Chinese Journal of Nonferrous Metals, 2009, 19(9): 1539-1547.
[13] MACKENZIES D S. Quench rate and aging effects in AlZnMgCu aluminum alloy[D]. Missouri: University of Missouri-Rolla, 2000: 4-26.
[14] LIM S T, YUN S J, NAM S W. Improved quench sensitivity in modified aluminum alloy 7175 for thick forging applications[J]. Mater Sci Eng A, 2004, 371(1/2): 82-90.
[15] DESCHAMPS A, BR?CHET Y. Nature and distribution of quench-induced precipitation in an Al-Zn-Mg-Cu alloy[J]. Sci Mater, 1998, 39(11): 1517-1522.
[16] CONSERVA M, FIORINI P. Interpretation of quench-sensitivity in Al-Zn-Mg-Cu alloys[J]. Metall Trans, 1973, 4(3): 857-862.
(编辑 李艳红)
基金项目:国际科技合作项目(2010DFB50340);国家自然科学基金资助项目(50904010);国家重点基础研究发展计划资助项目(2012CB619504)
收稿日期:2011-05-09;修订日期:2011-07-20
通信作者:熊柏青,教授,博士;电话:010-62055404;E-mail: xiongbq@grinm.com
熊柏青教授简介
熊柏青,1963年11月出生,教授,博士,博士生导师,现任北京有色金属研究总院副院长,兼任有色金属材料制备加工国家重点实验室主任。长期从事先进铝合金材料与制备加工技术研究,先后主持14项、参加31项国家级科研项目的研究工作,发表论文170余篇,其中110余篇被SCI、EI收录,获授权发明专利25项,出版著作2部,获部级科技进步一等奖1项、二等奖3项、三等奖1项。享受国务院政府特殊津贴专家、“新世纪百千万人才计划”国家级人选、国防科技创新团队带头人。“十五”863计划新材料领域主题专家组委员,“十一五”863计划军用材料重大项目总体专家组副组长,国防科工局科技委成员,中国材料研究学会常务理事,中国有色金属学会理事兼材料科学与工程分会主任。